铸钢托轮铸造工艺模拟
铸钢齿轮熔模铸造工艺设计
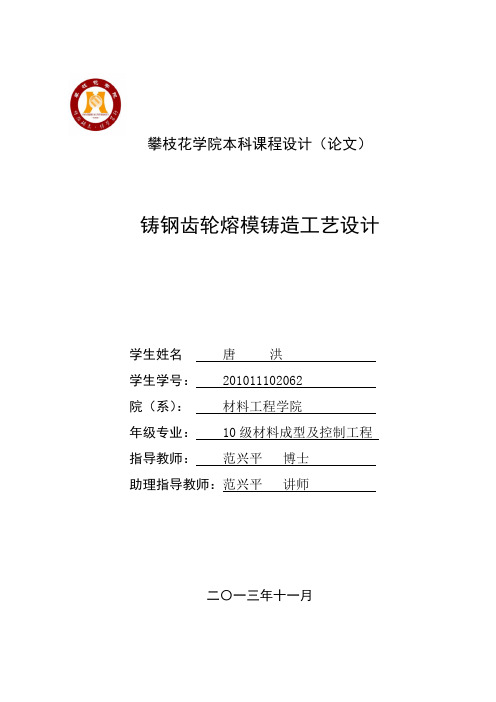
攀枝花学院本科课程设计(论文)铸钢齿轮熔模铸造工艺设计学生姓名唐洪学生学号: ************ 院(系):材料工程学院年级专业: 10级材料成型及控制工程指导教师:范兴平博士助理指导教师:范兴平讲师二〇一三年十一月攀枝花学院本科学生课程设计任务书课程设计(论文)指导教师成绩评定表摘要熔模铸造在我国具有悠久的历史。
它是一种少切削或无切削的铸造工艺,铸造行业中的一项优异的工艺技术,是一种无分型面的特种铸造方法。
熔模铸造是用一种易形成模样的材质如石蜡等做成零件的模型,然后在表面涂一层耐火材料和型砂形成一个模壳,经过脱蜡后对壳进行焙烧使壳具有一定的强度,然后进行浇注,经冷却落砂后生产出产品。
本课程设计主要是对齿轮的熔模铸造进行了设计,对齿轮的材料进行了分析,和在铸造中遇到的一系列问题,并一一进行处理。
在模料的选择中进行了分析并列举了制模的操作步骤等。
关键字:熔模铸造,齿轮,工艺设计目录摘要 (Ⅰ)1.零件分析 (1)1.1齿轮的形状分析 (1)1.2 齿轮材质分析 (1)2.选择基准面…………………………………………………………………………3.制模工部设计………………………………………………………………………3.1模料选择……………………………………………………………………………3.2制模设备与工艺…………………………………………………………………… 3.2.1制模设备………………………………………………………………………3.2.2蜡膏制备………………………………………………………………………3.2.3制模工艺………………………………………………………………………3.2.4压型制造………………………………………………………………………3.3蜡模修整………………………………………………………………………………4.制壳工部设计…………………………………………………………………………4.1 耐火材料选择………………………………………………………………………4.2涂料的配置及操作程序…………………………………………………………… 4.3 制壳………………………………………………………………………………4.4 脱蜡和型壳焙烧…………………………………………………………………5.熔炼工部设计…………………………………………………………………………5.1 熔炼操作步骤………………………………………………………………………6.浇注工部设计……………………………………………………………………………7.落纱清理及质检工部设计………………………………………………………………8.铸件表面处理方案的选择………………………………………………………………9.结束语……………………………………………………………………………………10.参考文献…………………………………………………………………………………1 零件分析1.1齿轮形状分析齿轮的外圆直径为φ258.26mm,宽为60mm,轮毂上有均匀分布的六个直径为φ40mm的孔,齿轮中心孔的直径为50mm。
铝合金轮毂铸造工艺设计与仿真分析

铝合金轮毂铸造工艺设计与仿真分析摘要:以某轮毂为基准,采用 UG 软件对轮毂模具进行设计。
以 A356.0-T6 铝合金作为轮毂轻量化材料,应用有限元技术,建立轮毂的挤压铸造模型,对铝合金轮毂压铸充型工艺进行数值模拟,并验证了铝合金轮毂铸造工艺设计的合理性。
关键词:有限元技术;铝合金轮毂;铸造工艺;模具0 引言铝合金因其密度小,强度高,可塑性好,导热性能好和易加工性而被广泛应用于航空、航天、机械制造、船舶等一类有色金属结构材料中。
采用铝合金制造的轮毂重量较钢轮毂轻得多,且具有能耗低,散热快,坚固耐用且寿命较长等特点,适合现代行业发展的要求,但是铝合金轮毂的铸造也存在着成形难以控制,铸造缺陷较多等问题,严重限制其在轮毂上的应用。
随着计算机技术在产品设计和制造中的应用与发展,新产品的开发和制造能力得到显著提高,建立工程计算模型并通过铸造数值模拟软件对铸造工艺进行模拟分析,设计合理铸造工艺参数,可有效地降低铸造缺陷产生概率、缩短产品开发周期、提高产品设计质量、降低产品生产成本。
1 轮毂结构及其模具设计1.1 轮毂材料及结构A356.0-T6 铝合金是典型的 Al-Si-Mg 系合金,具有良好的铸造性能,并且强度、屈服强度与可塑性等综合力学性能都很好,可满足轮毂尺寸精度与外观设计等要求,比其他型号的铸造铝合金更适合轻合金轮毂的制造要求。
如表 1 与表 2 所示分别表述了 A356.0-T6 铝合金的组成元素及含量、热熔融性能与物理机械性能。
1.2 轮毂模具设计由于轮毂中有沉孔和凹坑的存在,使铸型分型面无法与铸件完全相交,很可能引起模具体积块分割失败,如果采用传统的分型面方法,需要对分型面上沉孔和凹坑作修补才能达到分型面闭合的目的。
本文则采用侧面影像曲线方法来提取零件的最大轮廓线,在创建形成轮辐及风孔的上下箱分型面时,需要在轮毂三维模型内部创建一个与轮毂轮圈壁相切的辅助曲面,以确保上下箱开合时不会发生干涉,同时在设计该曲面时还要考虑拔模斜度的影响,否则模具的分离会失败。
端盖铸造模拟课程设计

端盖铸造模拟课程设计一、课程目标知识目标:1. 学生能理解端盖铸造的基本概念,掌握铸造过程中金属流动、冷却、凝固等基本原理。
2. 学生能掌握端盖铸造工艺参数对铸件质量的影响,如浇注系统设计、模具温度、浇注速度等。
3. 学生能了解并描述端盖铸造过程中可能出现的缺陷类型及其产生原因。
技能目标:1. 学生能运用计算机软件进行端盖铸造模拟,分析铸造过程可能出现的问题,并提出改进方案。
2. 学生能运用所学知识,设计合理的端盖铸造工艺参数,提高铸件质量。
情感态度价值观目标:1. 学生通过课程学习,培养对铸造工艺的热爱,增强对制造行业的认同感。
2. 学生能够认识到团队合作的重要性,培养协同解决问题的能力。
3. 学生能够关注铸造行业的发展,关注环境保护和资源利用,树立绿色生产的理念。
课程性质分析:本课程为实践性较强的课程,旨在通过端盖铸造模拟,让学生更好地理解铸造原理,掌握铸造工艺,提高解决实际问题的能力。
学生特点分析:学生处于高年级阶段,具备一定的学科基础和动手能力,对实践性课程有较高的兴趣。
教学要求:1. 教师应注重理论联系实际,引导学生运用所学知识解决实际问题。
2. 教师应鼓励学生积极参与讨论,培养学生的创新意识和团队协作能力。
3. 教学过程中,关注学生的学习进度,及时调整教学策略,确保课程目标的实现。
二、教学内容1. 端盖铸造基本原理:包括金属流动、冷却、凝固等基本过程,铸件收缩、应力与变形等内容,对应教材第3章。
2. 端盖铸造工艺参数:浇注系统设计、模具温度、浇注速度等参数对铸件质量的影响,对应教材第4章。
3. 端盖铸造缺陷分析:介绍常见缺陷类型(如气孔、夹渣、裂纹等)及其产生原因,对应教材第5章。
4. 铸造模拟软件应用:教授学生使用计算机软件进行端盖铸造模拟,分析铸造过程可能出现的问题,并提出改进方案,对应教材第6章。
5. 端盖铸造工艺设计:指导学生运用所学知识,设计合理的端盖铸造工艺参数,提高铸件质量,对应教材第7章。
铸造模拟软件MAGMA操作教程
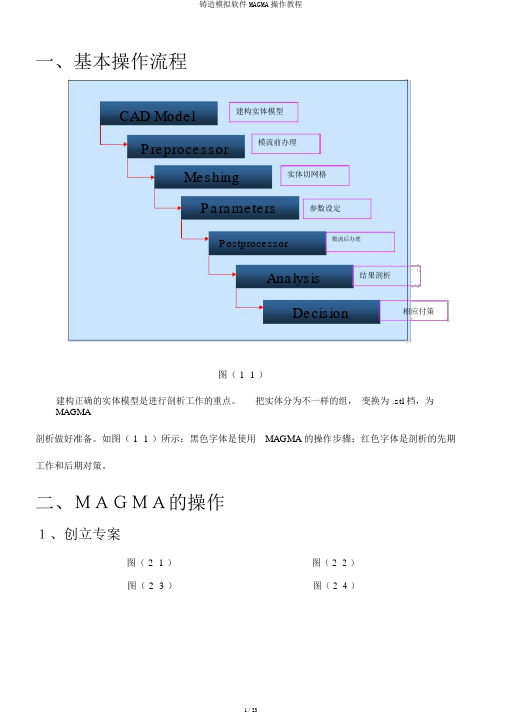
一、基本操作流程CAD Model建构实体模型Preprocessor模流前办理MeshingParameters 实体切网格参数设定Postprocessor模流后办理AnalysisDecision 结果剖析相应付策图( 1_1 )建构正确的实体模型是进行剖析工作的重点。
把实体分为不一样的组,变换为 .stl 档,为MAGMA剖析做好准备。
如图( 1_1 )所示:黑色字体是使用MAGMA 的操作步骤;红色字体是剖析的先期工作和后期对策。
二、MAGMA的操作1、创立专案图( 2_1 )图( 2_2 )图( 2_3 )图( 2_4 )专案名称.stl 档图( 2_5 )说明:图( 2_1)翻开桌面图标project 菜单create project 出现新对话框图( 2_2)选择 Iron casting 铸铁模组选择结果寄存路径( MAGMAsoft下)取分析方案名称回车键OK 出现新对话框图(2_3)默认系统选择直接按红框所标的键,直到图(2_4),按OK键结束创立专案操作。
如图( 2_5 )的路径,把成立好的 .stl 档存在 CMD 文件夹下。
2、前办理2-1 、材质群组介绍Z 轴正向Inlet 1、砂模( sandm)2、灌口( inlet)3、浇道( gating)4、浇道( gating)Gating CoreGatingFeederIngate5、冒口( feeder)6、冒口( feeder)7、入水口( ingate)8、入水口( ingate)9、砂芯( core)10、冷铁(chill)11、铸件(cast)chill图( 2_6 )在载入时必定要保证重力方向向上,如图(2_6 )所示。
一般在实体建模时便给出正确的重力方向。
假如方向错误也可在MAGMA 内改正。
(见后边说明)砂模能够在建构实体时绘出,也能够在MAGMA 内绘制出。
后边有进一步说明。
2-2、OVERLAY 原理1.CAST 1.INGATE排序2.INGATE 2.GATINGCAST3.GATING CAST 3.CASTCAVITY INSERTCAVITY INSERTINGATEINGATEGATINGGATING图( 2_7 )图(2_8)在建构实体时有一些地区重合。
重力倾斜铸造的模拟分析报告
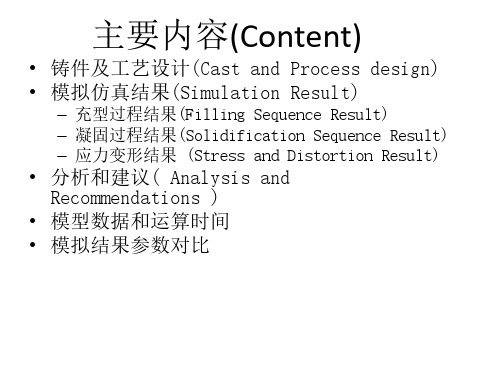
铸件充型初始位置
铸件充型终止位置
可以根据客户实际情况进行旋转速度设定,该 速度可以随时间的变化旋转角度的不同来控制。
2.模拟仿真结果(Simulation Result)
▶充型顺序结果(Overall Filling Pattern )
充型时间约为9秒 (The pouring time is about 9s)
变形量分布
3.分析和建议( Analysis and Recommendations )
▶缺陷
缺陷类型
具Hale Waihona Puke 描述原因缩松铸件的热节点处易产 生缩松
4. 数值模型和运算时间
▶充型和凝固耦合运算求 解
AnyCasting的充型和凝固耦合运算用了有限差分的网格 模型,通过真实模流(Real Flow)的求解技术,运用多 孔介质法和网格切割法,充分保证了网格模型与几何模
800 J/Kg*K (98℃) 0.63W/m*K (200℃)
1. 铸件及工艺设计(Cast and Process design)
▶模具设计方案(Mold Design)
浇口杯
(Pouring Basi n)
冒口 ( Riser)
重力方 向
砂芯(Core)
铸件(Cast) 模具(Mold)
图1. 模具设计方案
▶模具材料(Mold Material) : H13
热物属性(Property)
参考值 (Reference Value)
密度(Density)
7682Kg/m^3 (200℃)
比热 (Specific Heat)
522 J/Kg*K (200℃)
热传导系数 (Thermal Conductivity)
铸造实验报告书
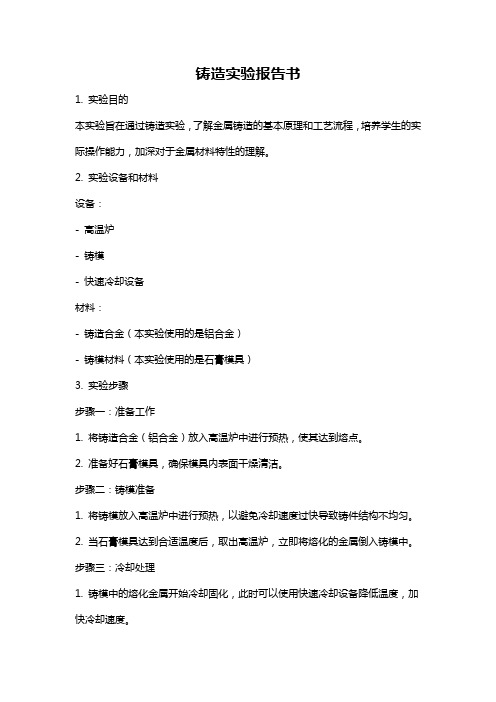
铸造实验报告书1. 实验目的本实验旨在通过铸造实验,了解金属铸造的基本原理和工艺流程,培养学生的实际操作能力,加深对于金属材料特性的理解。
2. 实验设备和材料设备:- 高温炉- 铸模- 快速冷却设备材料:- 铸造合金(本实验使用的是铝合金)- 铸模材料(本实验使用的是石膏模具)3. 实验步骤步骤一:准备工作1. 将铸造合金(铝合金)放入高温炉中进行预热,使其达到熔点。
2. 准备好石膏模具,确保模具内表面干燥清洁。
步骤二:铸模准备1. 将铸模放入高温炉中进行预热,以避免冷却速度过快导致铸件结构不均匀。
2. 当石膏模具达到合适温度后,取出高温炉,立即将熔化的金属倒入铸模中。
步骤三:冷却处理1. 铸模中的熔化金属开始冷却固化,此时可以使用快速冷却设备降低温度,加快冷却速度。
2. 等待足够时间,直到铸件冷却完全固化为止。
4. 实验结果与讨论经过以上实验步骤,我们成功完成了一次铸造实验,并获得了如图所示的铸件。
经过观察,铸件整体形状良好,表面呈现光滑平整的状态。
然而,我们也发现了一些潜在问题,例如:1. 铸件表面出现微小气孔,可能是由于石膏模具的气体释放不彻底导致的。
2. 铸件的某些部位出现缺陷,可能是由于熔化金属的流动性不佳导致的。
针对这些问题,我们可以进一步优化实验流程,改进铸造工艺,以获得更加理想的铸件。
5. 实验结论通过本次铸造实验,我们深入了解了金属铸造的基本原理和工艺流程,通过实际操作也体会到了其中的挑战和困难。
在实验中,我们成功获得了铝合金铸件,对于铸造技术的应用和发展有了更深入的认识。
然而,在铸造过程中也遇到了一些问题和挑战,这也提示我们仍有许多工作需要进一步完善和改进。
我们应该不断学习和探索,提高实际操作技能,以逐步提升铸造工艺的质量。
6. 参考文献暂无以上是本次铸造实验的实验报告书,谢谢阅读!。
手工铸造实验报告总结(3篇)
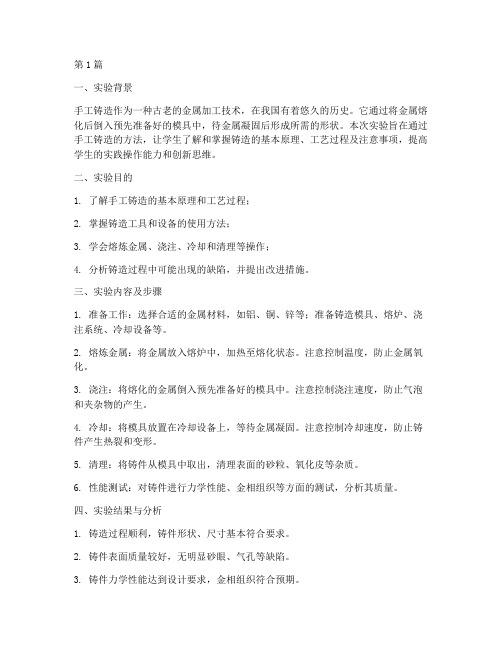
第1篇一、实验背景手工铸造作为一种古老的金属加工技术,在我国有着悠久的历史。
它通过将金属熔化后倒入预先准备好的模具中,待金属凝固后形成所需的形状。
本次实验旨在通过手工铸造的方法,让学生了解和掌握铸造的基本原理、工艺过程及注意事项,提高学生的实践操作能力和创新思维。
二、实验目的1. 了解手工铸造的基本原理和工艺过程;2. 掌握铸造工具和设备的使用方法;3. 学会熔炼金属、浇注、冷却和清理等操作;4. 分析铸造过程中可能出现的缺陷,并提出改进措施。
三、实验内容及步骤1. 准备工作:选择合适的金属材料,如铝、铜、锌等;准备铸造模具、熔炉、浇注系统、冷却设备等。
2. 熔炼金属:将金属放入熔炉中,加热至熔化状态。
注意控制温度,防止金属氧化。
3. 浇注:将熔化的金属倒入预先准备好的模具中。
注意控制浇注速度,防止气泡和夹杂物的产生。
4. 冷却:将模具放置在冷却设备上,等待金属凝固。
注意控制冷却速度,防止铸件产生热裂和变形。
5. 清理:将铸件从模具中取出,清理表面的砂粒、氧化皮等杂质。
6. 性能测试:对铸件进行力学性能、金相组织等方面的测试,分析其质量。
四、实验结果与分析1. 铸造过程顺利,铸件形状、尺寸基本符合要求。
2. 铸件表面质量较好,无明显砂眼、气孔等缺陷。
3. 铸件力学性能达到设计要求,金相组织符合预期。
4. 部分铸件出现轻微的热裂现象,经分析,可能是冷却速度过快或模具设计不合理所致。
五、实验总结1. 手工铸造是一种重要的金属加工方法,具有操作简便、成本低廉等优点。
2. 在实验过程中,要严格遵守操作规程,确保实验安全。
3. 熔炼金属时,要注意控制温度,防止金属氧化。
4. 浇注过程中,要控制浇注速度,避免气泡和夹杂物的产生。
5. 冷却过程中,要控制冷却速度,防止铸件产生热裂和变形。
6. 铸造模具的设计对铸件质量有很大影响,要充分考虑模具的刚度和强度。
7. 通过本次实验,使学生掌握了手工铸造的基本原理和工艺过程,提高了实践操作能力。
压力铸造生产虚拟仿真综合实验实验报告

压力铸造生产虚拟仿真综合实验实验报告
压力铸造是一种重要的金属成型工艺,广泛应用于汽车、航空、机械等行业。
传统的压力铸造生产过程需要大量的实验和试验,而且成本高、周期长、效率低。
为了提高压力铸造生产的效率和质量,压力铸造生产虚拟仿真技术应运而生。
本次实验采用了压力铸造生产虚拟仿真技术,通过建立压力铸造模型,进行了一系列仿真实验。
我们建立了压力铸造模型。
根据实际生产情况,我们采用了SOLIDWORKS软件建立了一个三维模型。
该模型可以模拟铸件的结构和几何形状,并可以进行参数化设计和优化。
同时,我们还建立了模具和注塑机模型,可以对模具和注塑机进行设计和优化。
我们对压力铸造过程进行了仿真实验。
在仿真实验中,我们可以对铸件的填充、凝固和收缩进行模拟,同时可以对模具和注塑机的运动进行模拟。
通过仿真实验,我们可以优化模具和注塑机的设计,提高铸件的质量和生产效率。
我们对压力铸造生产的各个环节进行了优化和改进。
通过实验,我们发现在压力铸造过程中,填充速度和温度是影响铸件质量的关键因素。
因此,在实际生产中,我们可以通过调整填充速度和温度来控制铸件的质量。
同时,我们还可以通过优化模具和注塑机的设计,
降低生产成本,提高生产效率。
压力铸造生产虚拟仿真技术是一种非常有效的生产工具,可以帮助企业提高生产效率和质量。
通过本次实验,我们深入了解了压力铸造生产虚拟仿真技术的原理和应用,对于今后的生产实践具有重要的参考价值。
- 1、下载文档前请自行甄别文档内容的完整性,平台不提供额外的编辑、内容补充、找答案等附加服务。
- 2、"仅部分预览"的文档,不可在线预览部分如存在完整性等问题,可反馈申请退款(可完整预览的文档不适用该条件!)。
- 3、如文档侵犯您的权益,请联系客服反馈,我们会尽快为您处理(人工客服工作时间:9:00-18:30)。
图 5 初始方案铸件缺陷分布图
3 改进后的工艺模拟
3.1 工艺改进 为使铸件凝固温度场分布合理并将最后凝固区
转移到冒口中,因此,在不影响铸件使用的情况下, 对铸造工艺进行以下两方面的改进:改用保温冒口, 从而增大冒口的模数,改变其凝固时间,使铸件的凝 固温度场重新分布;在冒口下设置锥形补贴,增加冒 口的补缩范围且便于机加工去除。 3.2 数值模拟及结果分析
2000,24, (12):21~27 5 荣科,姜希尚,谢明师. 铸造手册-铸造工艺第5卷[M]. 机械工业出版
社,2000:47~408 6 叶荣茂. 铸造工艺手册简明手册(哈尔滨工业大学)[M]. 机械工业出
版社,1997:1~235 7 杨国杰,张振斌,张武城. 铸造工程师手册[M]. 机械工业出版社,1997:
艺出品率较低,经济效益差[2]。为此,本文根据该铸 件结构和材料特点、技术要求等,采用现代设计理论 对铸钢托轮进行合理的铸造工艺设计,并利用Z-Cast 软件对铸件的凝固过程进行数值模拟,提出改进的措 施,达到优化铸造工艺方案的目的[3,4]。
2 初始方案的模拟计算
2.1 初始方案的确定 结合铸件的尺寸和结构特点,确定加工余量、拔
373~620 8 王文清,李魁盛. 铸造工艺学[M]. 北京:机械工业出版社,2002:2~
5 9 米国发,赵恒涛,等. Al-Si合金(A357)重力铸造充型及凝固过程模拟[J].
河南理工大学学报(自然科学版),2007,26(5):479~483 10 吴玉娟,侯峻玲,于宝义,等. 高压开关罐体低压铸造凝固数值模拟
a 凝固 50%时的温度分布
b 凝固 100%时的温度分布
图 3 凝固过程温度场模拟 图 4 为铸件各部分凝固时间的模拟结果。深颜色 显示的部位表示铝合金仍处于液态或半固态,没有完 全凝固;浅灰色表示已经完全凝固。当 t=1133s 时铸 件的外围、浇注系统及冒口均开始凝固。当 t=5213s 和 t=14053s 时,可以看出由于冒口的补缩距离和模数 太小,导致铸件最后凝固区并没有转移到冒口中,而
2.2 凝固过程数值模拟及结果分析 采用 Pro/E 软件建立铸件和浇注系统的几何实体
造型,并将几何实体存储为 STL 格式,作为下一步网 格剖分的基础。图 1 为铸件、浇注系统、冒口及出气 孔的三维造型。
采用韩国生产技术研究院、韩国 Cubictek 有限 公司和沈阳铸造研究所合作开发的 Z-Cast 铸造工艺 数值模拟分析系统对该铸钢托轮的铸造工艺进行模 拟。该系统的流动分析模块采用 SOLA-VOF 算法并 引入体积函数处理自由表面,该方法具有收敛性好、 计算时间短、节省内存单元、可以非常方便地处理充 型过程中的自由表面等,该系统在换热计算和流量修 正等方面进行了改进;凝固分析模块采用有限差 (FDM)方法,用温度回复法计算潜热,提高了计算 速度[9,10]。图 2 为铸件实体模型剖分并将网格消隐后 显示出的铸件外形,采用等步长的方法进行剖分,剖 分的总单元数为 10080000。
制造技术研究
2009 年 2 月第 1 期
R2178 21-2A 型铸钢托轮铸造工艺模拟及优化
米国发 董翠粉 赵大为 (河南理工大学材料科学与工程学院,焦作 454000)
摘要 利用 Z-Cast 软件对铸钢托轮凝固过程的温度场和时间分布进行模拟,依据模拟 分析结果对原工艺加以改进。通过采用添加保温冒口方法,改变铸件不合理的凝固顺序, 使铸件在整体上形成了有利于补缩的凝固顺序;在不影响铸件使用性能的前提下添加补贴, 建立补缩通道,有效地对最后凝固区域进行了补缩。通过改进工艺,最终消除了关键部位 的缩孔缺陷,获得了优质的大型铸钢托轮件。
关键词 大型托轮铸钢件 数值模拟 凝固 工艺优化
Simulation and Optimization of Casting Process for R2178 21-2A Large-scale Cast-steel Riding Wheel
Mi Guofa Dong Cuifen Zhao Dawei (College of Material Science and Engineering, Henan Polytechnic University, Jiaozuo 454000)
Abstract The numerical simulation software Z-Cast is used to simulate the temperature and the time distribution during the solidification process of cast-steel riding wheel. According to the results of simulation, the original casting technique is ing of the insulated riser is a valid way to change the solidification order, then a favorable order of solidification is formed, which is of great use of feeding. In order to create feeding channels effectively, the pads are added without any influence on the performance. By doing so the final solidifying zone could be fed effectively. The actual casting technique is modified based on the analysis and solution mentioned above synthetically. The shrinkage on the key position of casting is eliminated and high quality large-scale cast-steel riding wheel is obtained.
Key words large-scale cast-steel riding wheel numerical simulation solidification technology optimization
1 引言
托轮是回转窑的关键部件,主要起支撑作用,在 水泥和冶金矿山机械中得到广泛应用。由于托轮在工 作条件下需承受高温、高压和高度疲劳及高冲击应 力,因此对其内部质量和机械性能的要求较高[1]。由 于R2178 21-2A型托轮属铸钢厚大件,体收缩率大, 最大轮廓尺寸为Ф1700mm,最大壁厚可达860mm, 最小壁厚为150mm。在焦作矿山机械厂的实际生产中 常在热节区出现缩孔(松)和裂纹等缺陷,且铸造工
作者简介:米国发(1966-),教授,铸造专业;研究方向:凝固技术与合金铸造。 收稿日期:2008-09-09
18
制造技术研究
航天制造技术
模斜度、收缩率等参数;同时为确保铸件充型平稳, 避免浇不足等缺陷,本文采用底注式浇注系统[5~8]。 考虑到铸件机械性能和组织致密度要求高,需使铸件 顺序凝固,同时保证其厚大部位处得到充分补缩,避 免内部出现缩孔、缩松等缺陷。因而本文采用侧面外 冷铁,并在凝固温度较高的热节处设置冒口,为减少 铸件不必要的加工和修整,冒口采用位于在铸件上侧 且与铸件中心孔同轴的环形明冒口。如图 1 所示。
铸件表面质量好;对铸件的关键部位进行加工没有出 现上述缺陷,且铸件的致密性良好,机械性满足了使 用要求。改进后的工艺符合生产要求。
图 8 改进方案铸件缺陷分布图
a t=2172s
b t=16077s
c t=24332s
d t= 40409s
图 7 改进方案凝固时间分布图 从图 8 可以看出,在改进后方案模拟结果中,托 轮铸钢件的最终缺陷集中在冒口区,消除了其内部缩 孔、缩松等缺陷,表明改进后的方案是合理可行的。 改进工艺后进行生产实验,浇注工艺合理可行,
c t=14053s
a 凝固 50%时的温度分布
d t=20173s
图 4 凝固Байду номын сангаас间分布图
20
b 凝固 100%时的温度分布
图 6 凝固过程温度场模拟
制造技术研究
航天制造技术
图 7 为改进方案后铸件各部分凝固时间的模拟结 果。铸件各部分的凝固时间分布和温度场分布的模拟 过程相一致。铸件实现了顺序凝固,且将最后凝固区 引向冒口(t=40409s 时),铸件各部分均得到充分补 缩,确保了铸件的质量。
铁的激冷作用下,铸件与冷铁接触的部位的温度相 对较低,内部温度较高,铸件表面的温度比其内部 温度下降的要快,铸件由外向内顺序凝固。但是由 于冒口区温度也随之下降,因此把铸件的最后凝固 区引到铸件内部的厚大部位处,因而易形成缩孔 (松)等缺陷[11,12]。
图2 有限差分网格
图1 铸件、浇注系统、冒口及 出气孔的三维造型
参考文献
1 曹挺立. 大型托轮铸造工艺方案的改进[J]. 机械工人,2006,(12) 2 王纪敏. 大型铸钢托轮的铸造[J]. 河北科技大学学报,2000,20(3):1~
3 3 赵恒涛,米国发,等. 铸造充型及凝固过程模拟研究概况. 航天制造技
术,2007,(2):28~33 4 弓兴隆. 计算机数值模拟技术在铸件生产中的应用[J]. 航天制造技术,
19
制造技术研究
是向铸件内部推移。最终在铸件内部形成孤立的液相 区,形成缩孔和缩松等缺陷,如图 4d,当 t=20173s 时。从图中可以看出铸件各部分的凝固时间和温度场 的模拟基本相似。且在图 5 中铸件缺陷分布图中得到 了验证。
2009 年 2 月第 1 期
a t=1133s b t= 5213s
改进方案后铸件凝固过程温度场分布如图 6 所 示。分析图 6 可知,铸件表面由于温度较低,优先凝 固,在保温冒口的作用下,铸件底部的温度也明显低 于冒口区。铸件由外到内,由下到上逐次凝固,将铸 件最终凝固高温区引向冒口。同时,补贴的使用增加 了冒口的补缩范围,可确保铸件得到充分的补缩。因 而,铸件凝固过程的温度分布较初始方案更为合理。