电镀工艺流程介绍
各种电镀生产工艺流程
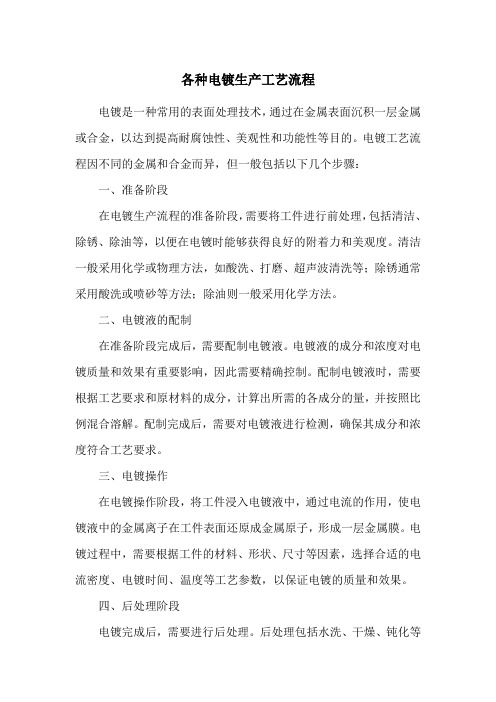
各种电镀生产工艺流程电镀是一种常用的表面处理技术,通过在金属表面沉积一层金属或合金,以达到提高耐腐蚀性、美观性和功能性等目的。
电镀工艺流程因不同的金属和合金而异,但一般包括以下几个步骤:一、准备阶段在电镀生产流程的准备阶段,需要将工件进行前处理,包括清洁、除锈、除油等,以便在电镀时能够获得良好的附着力和美观度。
清洁一般采用化学或物理方法,如酸洗、打磨、超声波清洗等;除锈通常采用酸洗或喷砂等方法;除油则一般采用化学方法。
二、电镀液的配制在准备阶段完成后,需要配制电镀液。
电镀液的成分和浓度对电镀质量和效果有重要影响,因此需要精确控制。
配制电镀液时,需要根据工艺要求和原材料的成分,计算出所需的各成分的量,并按照比例混合溶解。
配制完成后,需要对电镀液进行检测,确保其成分和浓度符合工艺要求。
三、电镀操作在电镀操作阶段,将工件浸入电镀液中,通过电流的作用,使电镀液中的金属离子在工件表面还原成金属原子,形成一层金属膜。
电镀过程中,需要根据工件的材料、形状、尺寸等因素,选择合适的电流密度、电镀时间、温度等工艺参数,以保证电镀的质量和效果。
四、后处理阶段电镀完成后,需要进行后处理。
后处理包括水洗、干燥、钝化等步骤。
水洗是为了去除工件表面的残留物和杂质;干燥可以通过自然晾干或烘干等方法使工件表面的水份蒸发;钝化是为了提高工件表面的耐腐蚀性和抗氧化的能力。
后处理的质量对电镀产品的质量和性能也有很大的影响。
五、检测与包装最后,需要对电镀产品进行检测和包装。
检测包括外观检测、镀层厚度检测、附着力检测等,以确保产品质量符合要求。
包装是为了保护产品在运输和存储过程中的安全和美观度。
包装一般采用防震、防潮、防尘等材料,根据不同的产品需求进行定制。
六、废水处理与环保措施在电镀生产过程中,会产生大量的废水,其中含有重金属离子和有害物质。
为了保护环境和人类健康,需要对废水进行处理。
废水处理方法包括化学沉淀法、吸附法、离子交换法等,根据废水的成分和浓度选择合适的方法进行处理。
电镀工艺流程
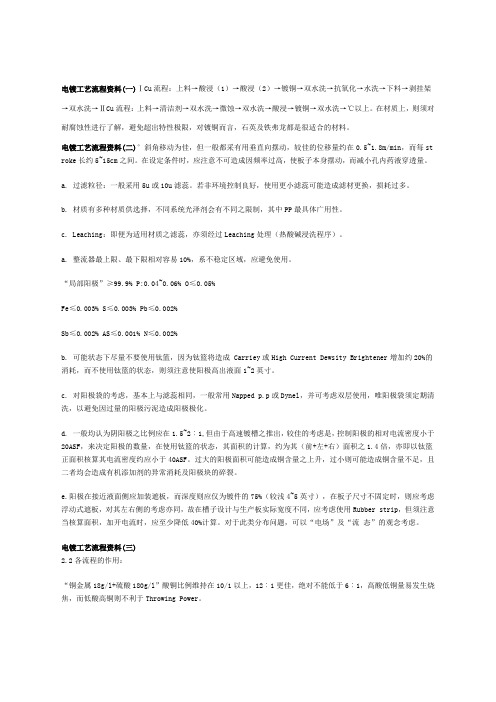
电镀工艺流程资料(一)ⅠCu流程:上料→酸浸(1)→酸浸(2)→镀铜→双水洗→抗氧化→水洗→下料→剥挂架→双水洗→ⅡCu流程:上料→清洁剂→双水洗→微蚀→双水洗→酸浸→镀铜→双水洗→℃以上。
在材质上,则须对耐腐蚀性进行了解,避免超出特性极限,对镀铜而言,石英及铁弗龙都是很适合的材料。
电镀工艺流程资料(二)°斜角移动为佳,但一般都采有用垂直向摆动,较佳的位移量约在0.5~1.8m/min,而每st roke长约5~15cm之间。
在设定条件时,应注意不可造成因频率过高,使板子本身摆动,而减小孔内药液穿透量。
a. 过滤粒径:一般采用5u或10u滤蕊。
若非环境控制良好,使用更小滤蕊可能造成滤材更换,损耗过多。
b. 材质有多种材质供选择,不同系统光泽剂会有不同之限制,其中PP最具体广用性。
c. Leaching:即便为适用材质之滤蕊,亦须经过Leaching处理(热酸碱浸洗程序)。
a. 整流器最上限、最下限相对容易10%,系不稳定区域,应避免使用。
“局部阳极”≥99.9% P:0.04~0.06% O≤0.05%Fe≤0.003% S≤0.003% Pb≤0.002%Sb≤0.002% AS≤0.001% N≤0.002%b. 可能状态下尽量不要使用钛篮,因为钛篮将造成 Carriey或High Current Dewsity Brightener增加约20%的消耗,而不使用钛篮的状态,则须注意使阳极高出液面1~2英寸。
c. 对阳极袋的考虑,基本上与滤蕊相同,一般常用Napped p.p或Dynel,并可考虑双层使用,唯阳极袋须定期清洗,以避免因过量的阳极污泥造成阳极极化。
d. 一般均认为阴阳极之比例应在1.5~2︰1,但由于高速镀槽之推出,较佳的考虑是,控制阳极的相对电流密度小于20ASF,来决定阳极的数量,在使用钛篮的状态,其面积的计算,约为其(前+左+右)面积之1.4倍,亦即以钛篮正面积核算其电流密度约应小于40ASF。
电镀工艺流程简介
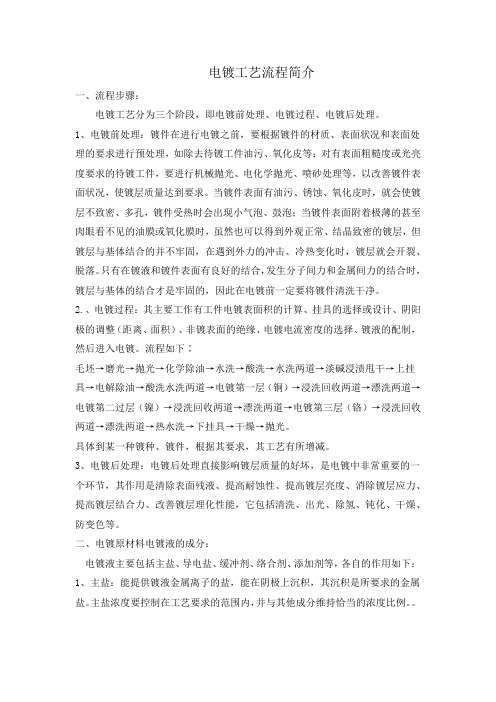
电镀工艺流程简介一、流程步骤:电镀工艺分为三个阶段,即电镀前处理、电镀过程、电镀后处理。
1、电镀前处理:镀件在进行电镀之前,要根据镀件的材质、表面状况和表面处理的要求进行预处理,如除去待镀工件油污、氧化皮等;对有表面粗糙度或光亮度要求的待镀工件,要进行机械抛光、电化学抛光、喷砂处理等,以改善镀件表面状况,使镀层质量达到要求。
当镀件表面有油污、锈蚀、氧化皮时,就会使镀层不致密、多孔,镀件受热时会出现小气泡、鼓泡;当镀件表面附着极薄的甚至肉眼看不见的油膜或氧化膜时,虽然也可以得到外观正常、结晶致密的镀层,但镀层与基体结合的并不牢固,在遇到外力的冲击、冷热变化时,镀层就会开裂、脱落。
只有在镀液和镀件表面有良好的结合,发生分子间力和金属间力的结合时,镀层与基体的结合才是牢固的,因此在电镀前一定要将镀件清洗干净。
2.、电镀过程:其主要工作有工件电镀表面积的计算、挂具的选择或设计、阴阳极的调整(距离、面积)、非镀表面的绝缘、电镀电流密度的选择、镀液的配制,然后进入电镀。
流程如下∶毛坯→磨光→抛光→化学除油→水洗→酸洗→水洗两道→淡碱浸渍甩干→上挂具→电解除油→酸洗水洗两道→电镀第一层(铜)→浸洗回收两道→漂洗两道→电镀第二过层(镍)→浸洗回收两道→漂洗两道→电镀第三层(铬)→浸洗回收两道→漂洗两道→热水洗→下挂具→干燥→抛光。
具体到某一种镀种、镀件,根据其要求,其工艺有所增减。
3、电镀后处理:电镀后处理直接影响镀层质量的好坏,是电镀中非常重要的一个环节,其作用是清除表面残液、提高耐蚀性、提高镀层亮度、消除镀层应力、提高镀层结合力、改善镀层理化性能,它包括清洗、出光、除氢、钝化、干燥、防变色等。
二、电镀原材料电镀液的成分:电镀液主要包括主盐、导电盐、缓冲剂、络合剂、添加剂等,各自的作用如下:1、主盐:能提供镀液金属离子的盐,能在阴极上沉积,其沉积是所要求的金属盐。
主盐浓度要控制在工艺要求的范围内,并与其他成分维持恰当的浓度比例。
电镀的一般工艺流程
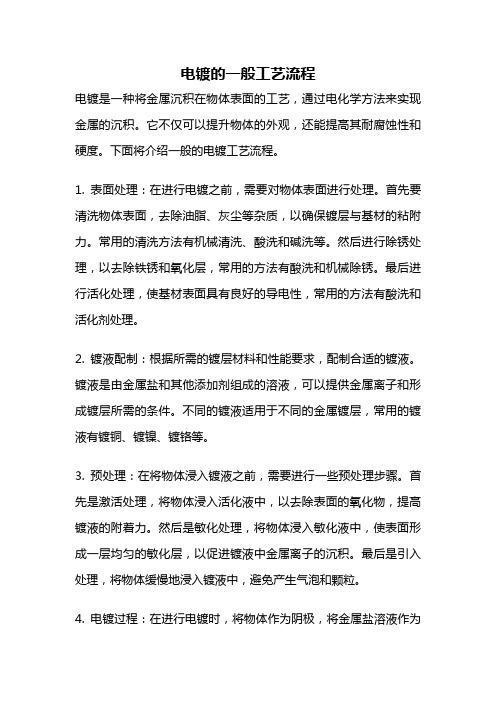
电镀的一般工艺流程电镀是一种将金属沉积在物体表面的工艺,通过电化学方法来实现金属的沉积。
它不仅可以提升物体的外观,还能提高其耐腐蚀性和硬度。
下面将介绍一般的电镀工艺流程。
1. 表面处理:在进行电镀之前,需要对物体表面进行处理。
首先要清洗物体表面,去除油脂、灰尘等杂质,以确保镀层与基材的粘附力。
常用的清洗方法有机械清洗、酸洗和碱洗等。
然后进行除锈处理,以去除铁锈和氧化层,常用的方法有酸洗和机械除锈。
最后进行活化处理,使基材表面具有良好的导电性,常用的方法有酸洗和活化剂处理。
2. 镀液配制:根据所需的镀层材料和性能要求,配制合适的镀液。
镀液是由金属盐和其他添加剂组成的溶液,可以提供金属离子和形成镀层所需的条件。
不同的镀液适用于不同的金属镀层,常用的镀液有镀铜、镀镍、镀铬等。
3. 预处理:在将物体浸入镀液之前,需要进行一些预处理步骤。
首先是激活处理,将物体浸入活化液中,以去除表面的氧化物,提高镀液的附着力。
然后是敏化处理,将物体浸入敏化液中,使表面形成一层均匀的敏化层,以促进镀液中金属离子的沉积。
最后是引入处理,将物体缓慢地浸入镀液中,避免产生气泡和颗粒。
4. 电镀过程:在进行电镀时,将物体作为阴极,将金属盐溶液作为阳极,通过外加电流的作用,使金属离子从阳极迁移到阴极上,形成金属镀层。
电镀过程中需要控制镀液的温度、电流密度和时间等参数,以获得理想的镀层厚度和质量。
5. 后处理:在完成电镀后,还需要进行一些后处理步骤。
首先是冲洗,将镀层表面的残留镀液和杂质冲洗掉,以防止镀层腐蚀或变色。
然后是烘干,将物体放入烘干设备中,使其完全干燥。
最后是抛光,通过机械或化学方法,对镀层进行抛光处理,以获得光滑、亮丽的表面。
电镀的一般工艺流程包括表面处理、镀液配制、预处理、电镀过程和后处理。
每个步骤都非常重要,需要严格控制各项参数,以确保获得理想的镀层效果。
电镀工艺的应用广泛,可以用于改善产品的外观和性能,延长其使用寿命。
电镀工艺流程
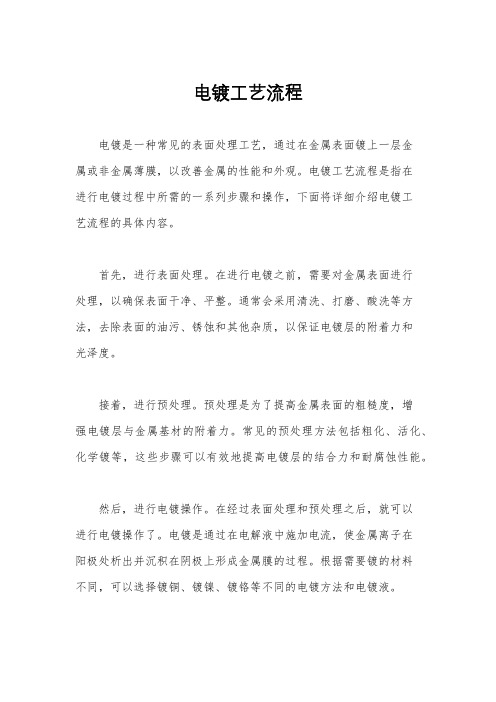
电镀工艺流程电镀是一种常见的表面处理工艺,通过在金属表面镀上一层金属或非金属薄膜,以改善金属的性能和外观。
电镀工艺流程是指在进行电镀过程中所需的一系列步骤和操作,下面将详细介绍电镀工艺流程的具体内容。
首先,进行表面处理。
在进行电镀之前,需要对金属表面进行处理,以确保表面干净、平整。
通常会采用清洗、打磨、酸洗等方法,去除表面的油污、锈蚀和其他杂质,以保证电镀层的附着力和光泽度。
接着,进行预处理。
预处理是为了提高金属表面的粗糙度,增强电镀层与金属基材的附着力。
常见的预处理方法包括粗化、活化、化学镀等,这些步骤可以有效地提高电镀层的结合力和耐腐蚀性能。
然后,进行电镀操作。
在经过表面处理和预处理之后,就可以进行电镀操作了。
电镀是通过在电解液中施加电流,使金属离子在阳极处析出并沉积在阴极上形成金属膜的过程。
根据需要镀的材料不同,可以选择镀铜、镀镍、镀铬等不同的电镀方法和电镀液。
紧接着,进行后处理。
电镀完成后,还需要进行后处理工序,以提高电镀层的光泽度和耐腐蚀性能。
后处理通常包括清洗、烘干、抛光、封孔等步骤,这些工序可以使电镀层更加光滑均匀,提高其外观和质量。
最后,进行检验和包装。
在完成电镀工艺流程后,需要对成品进行检验,确保电镀层的厚度、硬度、附着力等性能符合要求。
通过检验合格后,再进行包装,以保护电镀层不受外界环境的影响,确保产品的质量和美观。
总的来说,电镀工艺流程是一个复杂而严谨的过程,需要经过多道工序和严格的操作要求。
只有严格按照工艺流程进行操作,并且在每个环节都严格把关,才能确保电镀层的质量和性能达到要求。
希望通过本文的介绍,能够对电镀工艺流程有一个更加深入的了解,为实际工作提供一定的参考和帮助。
电镀工艺流程
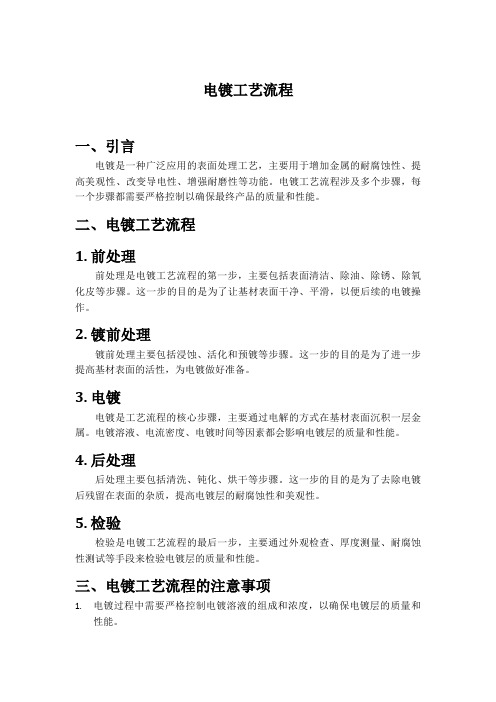
电镀工艺流程一、引言电镀是一种广泛应用的表面处理工艺,主要用于增加金属的耐腐蚀性、提高美观性、改变导电性、增强耐磨性等功能。
电镀工艺流程涉及多个步骤,每一个步骤都需要严格控制以确保最终产品的质量和性能。
二、电镀工艺流程1. 前处理前处理是电镀工艺流程的第一步,主要包括表面清洁、除油、除锈、除氧化皮等步骤。
这一步的目的是为了让基材表面干净、平滑,以便后续的电镀操作。
2. 镀前处理镀前处理主要包括浸蚀、活化和预镀等步骤。
这一步的目的是为了进一步提高基材表面的活性,为电镀做好准备。
3. 电镀电镀是工艺流程的核心步骤,主要通过电解的方式在基材表面沉积一层金属。
电镀溶液、电流密度、电镀时间等因素都会影响电镀层的质量和性能。
4. 后处理后处理主要包括清洗、钝化、烘干等步骤。
这一步的目的是为了去除电镀后残留在表面的杂质,提高电镀层的耐腐蚀性和美观性。
5. 检验检验是电镀工艺流程的最后一步,主要通过外观检查、厚度测量、耐腐蚀性测试等手段来检验电镀层的质量和性能。
三、电镀工艺流程的注意事项1.电镀过程中需要严格控制电镀溶液的组成和浓度,以确保电镀层的质量和性能。
2.电镀过程中需要控制电流密度和电镀时间,以避免电镀层出现缺陷。
3.在进行电镀操作前,需要对基材进行充分的前处理和镀前处理,以确保基材表面的活性和清洁度。
4.电镀后需要进行后处理,以去除表面的杂质和提高电镀层的耐腐蚀性。
5.在整个电镀工艺流程中,需要注意安全操作,避免发生意外事故。
四、结论电镀工艺流程是一个复杂而精细的过程,需要严格控制各个步骤的参数和操作,以确保最终产品的质量和性能。
通过合理的前处理、镀前处理、电镀、后处理和检验,可以得到高质量的电镀层,提高产品的使用寿命和美观性。
在实际应用中,还需要根据具体的产品要求和电镀材料,灵活调整和优化电镀工艺流程。
电镀的工艺流程
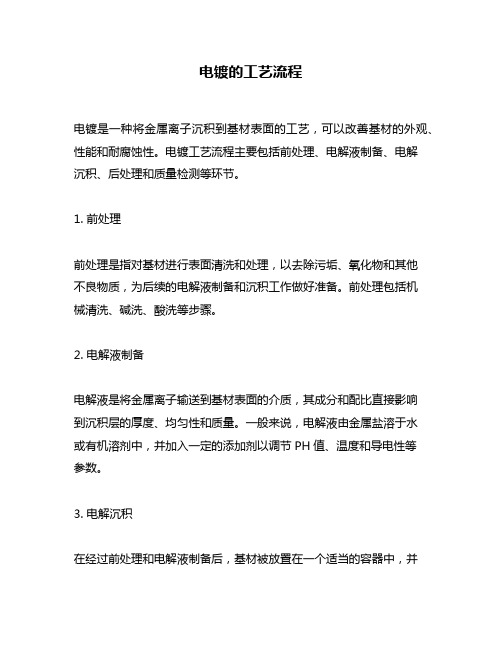
电镀的工艺流程
电镀是一种将金属离子沉积到基材表面的工艺,可以改善基材的外观、性能和耐腐蚀性。
电镀工艺流程主要包括前处理、电解液制备、电解
沉积、后处理和质量检测等环节。
1. 前处理
前处理是指对基材进行表面清洗和处理,以去除污垢、氧化物和其他
不良物质,为后续的电解液制备和沉积工作做好准备。
前处理包括机
械清洗、碱洗、酸洗等步骤。
2. 电解液制备
电解液是将金属离子输送到基材表面的介质,其成分和配比直接影响
到沉积层的厚度、均匀性和质量。
一般来说,电解液由金属盐溶于水
或有机溶剂中,并加入一定的添加剂以调节PH值、温度和导电性等
参数。
3. 电解沉积
在经过前处理和电解液制备后,基材被放置在一个适当的容器中,并
与正极相连。
随着电流通过,金属离子从电解液中沉积到基材表面,形成金属镀层。
电解沉积的过程需要控制电流密度、时间和温度等参数,以确保沉积层的均匀性和质量。
4. 后处理
后处理是指对电镀件进行清洗、干燥和加工等步骤,以去除残留的电解液和其他污垢,并对沉积层进行必要的加工和修整。
后处理包括水洗、烘干、抛光、喷漆等步骤。
5. 质量检测
质量检测是电镀工艺流程中非常重要的一环,其目的是检验沉积层的厚度、均匀性、附着力、硬度和耐腐蚀性等参数是否符合要求。
常用的质量检测方法包括厚度计测量、显微镜观察、耐腐蚀试验等。
综上所述,电镀工艺流程是一个复杂而精细的过程,需要严格控制每个环节并进行有效管理。
只有这样才能保证电镀件的质量和稳定性,并满足不同客户对于外观和性能要求。
电镀的工艺流程
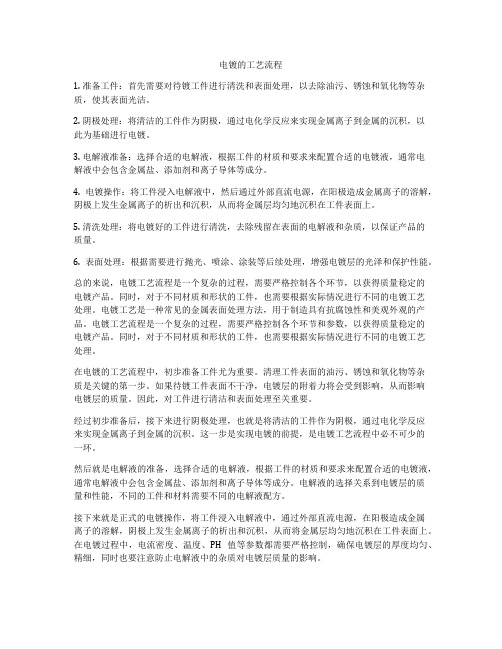
电镀的工艺流程1. 准备工件:首先需要对待镀工件进行清洗和表面处理,以去除油污、锈蚀和氧化物等杂质,使其表面光洁。
2. 阴极处理:将清洁的工件作为阴极,通过电化学反应来实现金属离子到金属的沉积,以此为基础进行电镀。
3. 电解液准备:选择合适的电解液,根据工件的材质和要求来配置合适的电镀液,通常电解液中会包含金属盐、添加剂和离子导体等成分。
4. 电镀操作:将工件浸入电解液中,然后通过外部直流电源,在阳极造成金属离子的溶解,阴极上发生金属离子的析出和沉积,从而将金属层均匀地沉积在工件表面上。
5. 清洗处理:将电镀好的工件进行清洗,去除残留在表面的电解液和杂质,以保证产品的质量。
6. 表面处理:根据需要进行抛光、喷涂、涂装等后续处理,增强电镀层的光泽和保护性能。
总的来说,电镀工艺流程是一个复杂的过程,需要严格控制各个环节,以获得质量稳定的电镀产品。
同时,对于不同材质和形状的工件,也需要根据实际情况进行不同的电镀工艺处理。
电镀工艺是一种常见的金属表面处理方法,用于制造具有抗腐蚀性和美观外观的产品。
电镀工艺流程是一个复杂的过程,需要严格控制各个环节和参数,以获得质量稳定的电镀产品。
同时,对于不同材质和形状的工件,也需要根据实际情况进行不同的电镀工艺处理。
在电镀的工艺流程中,初步准备工件尤为重要。
清理工件表面的油污、锈蚀和氧化物等杂质是关键的第一步。
如果待镀工件表面不干净,电镀层的附着力将会受到影响,从而影响电镀层的质量。
因此,对工件进行清洁和表面处理至关重要。
经过初步准备后,接下来进行阴极处理,也就是将清洁的工件作为阴极,通过电化学反应来实现金属离子到金属的沉积。
这一步是实现电镀的前提,是电镀工艺流程中必不可少的一环。
然后就是电解液的准备,选择合适的电解液,根据工件的材质和要求来配置合适的电镀液,通常电解液中会包含金属盐、添加剂和离子导体等成分。
电解液的选择关系到电镀层的质量和性能,不同的工件和材料需要不同的电解液配方。
- 1、下载文档前请自行甄别文档内容的完整性,平台不提供额外的编辑、内容补充、找答案等附加服务。
- 2、"仅部分预览"的文档,不可在线预览部分如存在完整性等问题,可反馈申请退款(可完整预览的文档不适用该条件!)。
- 3、如文档侵犯您的权益,请联系客服反馈,我们会尽快为您处理(人工客服工作时间:9:00-18:30)。
电镀工艺流程介绍
环型电镀自动线工艺流程Enthone Plating On Plastic Process
塑料镀多层镍-铬体系
7. CUPROSTAR 1541 光亮酸铜
非常光亮的酸铜镀层,整平性好并伸延性佳,与镍结合力强。
适合用于对整平性要求高的工艺。
添加剂稳定,不会因停工时令添加剂分解减少额外补充。
8. UDYLITE BTL 不含硫半光亮镍
延展力及整平力极佳的半光亮镍镀层,并且取得非常好的CASS试验结果。
独立的添加剂可调整电位差、整平性及柔软度。
BTL工艺具有连续的生产能力,无需定期进行纯化处理。
BTL添加剂及溶液与光亮镍镀液是兼容的,在BTL及以后的光亮镍过程无需水洗。
9. ELPELYT LS-1 光亮镍
高亮度的光亮镍镀层,整平性好。
最大优点在于其极佳的覆盖能力以及低应力,适合用于塑料电镀。
10. DUR NI 618 微孔镍
极微细的固体微孔镍,可产生极高及均匀的微孔数。
DUR NI 618已经国内主要塑料电镀厂家所采用,结果显示其微孔分布较其它的微孔镍较均匀,有利于提高抗腐蚀能力的要求。
固体溶解度高,操作容易。
开缸量及添加量较低,相对可大大降低运作成本。
另配套调整电位差的添加剂,可保证光亮镍及微孔镍之间的电位差达至合格水平。
配套霍尔曼测试仪(Fuhrmann Test Kit),可即时测定CASS结果。
霍尔曼测试已经是克莱斯勒以及大众汽车公司认可的测试方法,用家可在生产线上即时知道产品的质量,无需等数天的CASS 试验过程。
DUR NI 618微孔大小分布图
11. ANKOR NFDS 铬前活化
作为镀光亮铬之前的阴极电解活化,可替代铬酸的化学活化剂。
尽管所需的电流密度低,但能完
全防止由于光镍镀层钝化而出现白雾和污渍。
12. ANKOR 1120H 光亮铬
混合酸型铬电镀液,应用于装饰性光亮铬镀层。
电流密度范围宽及具有极佳的覆盖能力。
ANKOR 1120H 适用于300g/L及200g/L铬酸配方。
铬酸浓度高,能增强导电性及抗杂质污染的能力。
与一般的铬电镀液相比,高浓度配方的ANKOR 1120H镀液,会对镀液成份产生稳定作用。