汽车座椅安全带固定点强度试验系统研究
基于LS-DYNA的汽车安全带固定点强度分析
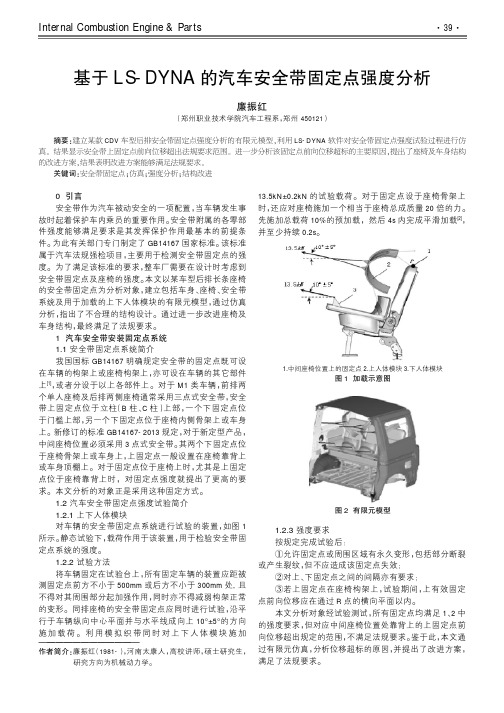
Internal Combustion Engine &Parts0引言安全带作为汽车被动安全的一项配置,当车辆发生事故时起着保护车内乘员的重要作用。
安全带附属的各零部件强度能够满足要求是其发挥保护作用最基本的前提条件。
为此有关部门专门制定了GB14167国家标准。
该标准属于汽车法规强检项目,主要用于检测安全带固定点的强度。
为了满足该标准的要求,整车厂需要在设计时考虑到安全带固定点及座椅的强度。
本文以某车型后排长条座椅的安全带固定点为分析对象,建立包括车身、座椅、安全带系统及用于加载的上下人体模块的有限元模型,通过仿真分析,指出了不合理的结构设计。
通过进一步改进座椅及车身结构,最终满足了法规要求。
1汽车安全带安装固定点系统1.1安全带固定点系统简介我国国标GB14167明确规定安全带的固定点既可设在车辆的构架上或座椅构架上,亦可设在车辆的其它部件上[1],或者分设于以上各部件上。
对于M1类车辆,前排两个单人座椅及后排两侧座椅通常采用三点式安全带,安全带上固定点位于立柱(B 柱、C 柱)上部,一个下固定点位于门槛上部,另一个下固定点位于座椅内侧骨架上或车身上。
新修订的标准GB14167-2013规定,对于新定型产品,中间座椅位置必须采用3点式安全带。
其两个下固定点位于座椅骨架上或车身上,上固定点一般设置在座椅靠背上或车身顶棚上。
对于固定点位于座椅上时,尤其是上固定点位于座椅靠背上时,对固定点强度就提出了更高的要求。
本文分析的对象正是采用这种固定方式。
1.2汽车安全带固定点强度试验简介1.2.1上下人体模块对车辆的安全带固定点系统进行试验的装置,如图1所示。
静态试验下,载荷作用于该装置,用于检验安全带固定点系统的强度。
1.2.2试验方法将车辆固定在试验台上,所有固定车辆的装置应距被测固定点前方不小于500mm 或后方不小于300mm 处,且不得对其周围部分起加强作用,同时亦不得减弱构架正常的变形。
驾驶员座椅安全带固定点强度分析报告

安全带锚固点坐标
X
Y
1517.6
-597.3
1459.4
-624.8计位置
Z 993.9
59 216.5
变形图(动画)
变形图(动画)
变形图(动画)
变形图(动画)
变形图(动画)
变形图(动画)
变形图(动画)
变形图(动画)
变形图(动画)
120%加载力保持阶段(时间从 0.16s-0.22s), 三条链的位移曲线基本保持水平,这说明座椅 不再变形,座椅能承受120%加载力。
应力/应变图_左前连杆支架(厚度4.0mm)
材料: S550MC 屈服强度:551.4MPa 极限应力:690MPa 极限应变:13.6%
应力/应变图_左前连杆支架(厚度4.0mm)
材料: S550MC 屈服强度:551.4MPa 极限应力:690MPa 极限应变:13.6%
应力/应变图_左后连杆齿支架(厚度4.0mm)
材料: 16MnCr5 屈服强度:1187MPa 极限应力:1373MPa 极限应变:10.0%
应力/应变图_右前连杆支架(厚度 2.5mm)
材料: ZSTE420 屈服强度:420MPa 极限应力:556.8MPa 极限应变:14.8%
应力/应变图_左前连杆支架(厚度 2.5mm)
材料: QSTE460 屈服强度:460MPa 极限应力:592.8MPa 极限应变:13.1%
材料: QSTE460 屈服强度:460MPa 极限应力:592.8MPa 极限应变:13.1%
应力/应变图_右内滑轨(厚度 1.8mm)
内滑轨存在拉断的风险!
材料: S650MC 屈服强度:650MPa 极限应力:700MPa 极限应变:10.0%
汽车安全带固定点强度试验系统研制

量精度 :1 满量程误差) ± %( 。
作 动 器可 以实 现双 向控制 。 以手 控进 退 。 可 亦可 在 计算 机 控制下 具 备低压 步进 。 压 自动加 载 能力 ; 高
可 以任 意设 定作 动 器工作 的数 量 、 加载 力大 小 、 加载
时间 和保持 时 间 保 证六 个作 动器 必须 同时 到达各
自设定 值 . 验加 载 时 间在 3 0 试 10S可调 。 持 时 间 保
在 0 1 0s 调 。系统 测 控软 件 能实 施对 系 统 中的 ~ 0 可
响应 存在 延迟 . 载 中存 在较 大 的力波 动 , 节过 程 加 调
较 长 . 容易超 出测 量范 围而使试 验数 据不 准 确 。 且 针对 以上 问题 .设 计开 发 出计算 机控 制 六通 道 电液 伺 服汽 车安全 带 固定点 强度试 验试 验 系统 该
汽车座椅安全带固定点强度分析
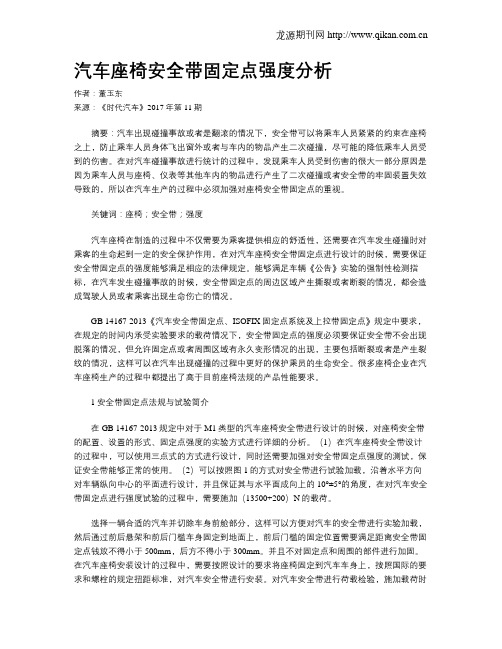
汽车座椅安全带固定点强度分析作者:董玉东来源:《时代汽车》2017年第11期摘要:汽车出现碰撞事故或者是翻滚的情况下,安全带可以将乘车人员紧紧的约束在座椅之上,防止乘车人员身体飞出窗外或者与车内的物品产生二次碰撞,尽可能的降低乘车人员受到的伤害。
在对汽车碰撞事故进行统计的过程中,发现乘车人员受到伤害的很大一部分原因是因为乘车人员与座椅、仪表等其他车内的物品进行产生了二次碰撞或者安全带的牢固装置失效导致的,所以在汽车生产的过程中必须加强对座椅安全带固定点的重视。
关键词:座椅;安全带;强度汽车座椅在制造的过程中不仅需要为乘客提供相应的舒适性,还需要在汽车发生碰撞时对乘客的生命起到一定的安全保护作用,在对汽车座椅安全带固定点进行设计的时候,需要保证安全带固定点的强度能够满足相应的法律规定。
能够满足车辆《公告》实验的强制性检测指标,在汽车发生碰撞事故的时候,安全带固定点的周边区域产生撕裂或者断裂的情况,都会造成驾驶人员或者乘客出现生命伤亡的情况。
GB 14167-2013《汽车安全带固定点、ISOFIX固定点系统及上拉带固定点》规定中要求,在规定的时间内承受实验要求的载荷情况下,安全带固定点的强度必须要保证安全带不会出现脱落的情况,但允许固定点或者周围区域有永久变形情况的出现,主要包括断裂或者是产生裂纹的情况,这样可以在汽车出现碰撞的过程中更好的保护乘员的生命安全。
很多座椅企业在汽车座椅生产的过程中都提出了高于目前座椅法规的产品性能要求。
1安全带固定点法规与试验简介在GB 14167-2013规定中对于M1类型的汽车座椅安全带进行设计的时候,对座椅安全带的配置、设置的形式、固定点强度的实验方式进行详细的分析。
(1)在汽车座椅安全带设计的过程中,可以使用三点式的方式进行设计,同时还需要加强对安全带固定点强度的测试,保证安全带能够正常的使用。
(2)可以按照图1的方式对安全带进行试验加载,沿着水平方向对车辆纵向中心的平面进行设计,并且保证其与水平面成向上的10°±5°的角度,在对汽车安全带固定点进行强度试验的过程中,需要施加(13500+200)N的载荷。
汽车座椅安全带固定点强度分析

汽车座椅安全带固定点强度分析摘要:汽车座椅靠背有支撑乘员背部的作用,在舒适性评价中有很高的占比,由于靠背远离固定点,且靠背与固定点之间存在多个调节机构,如高调四连杆、靠背调角器、水平调节滑轨等,导致靠背受到震动易产生晃动,对于不同座椅,产生晃动的震动波形也不同。
针对靠背晃动问题综合考虑可行性、工艺性及成本等因素,选取高调四连杆作为研究对象,解决该问题,并提供一种该问题的解决思路。
关键词:汽车座椅;安全带;固定点;强度分析引言汽车座椅是汽车安全件的重要组成部分之一,它不仅可以给乘员提供支撑,还具有保护乘员避免或减少伤害的作用。
汽车座椅安全带固定点试验是车辆《公告》强制性试验项目。
在车辆发生碰撞事故时,如果安全带固定点强度不满足法规要求,则安全带固定点周围区域的撕裂或断裂是会造成人员伤亡。
为使座椅在整车碰撞过程中起到更好的保护作用,许多座椅企业会设计高于法规标准要求的性能产品。
一、汽车座椅概述乘坐汽车的舒适性分静态和动态两个场景。
静态舒适性主要取决于座椅的设计是否符合“人体工程学”。
简单来说,运用“人体工程学”提升座椅的舒适性可以总结为三个要点:座椅设计参考人体测量学数据;座椅具有可调节性,满足不同体型人群需求;座椅的位置与空间相协调。
此外,座椅不宜过软,过软的座椅不仅会对尾椎造成过大压力,导致损伤脊椎健康,还会压迫腿部,不利于血液循环。
以荣获J.D.Power2021大型MPV座椅质量第一的广汽传祺M8的座椅为例,安道拓基于人体工程学设计了高度贴合人体的座椅造型,使得人体与座椅之间的接触面积最大化,并采用多密度多硬度的泡沫给予乘坐者最有力的支撑。
同样在各系细分市场摘得座椅质量冠亚军的福特福克斯和小鹏G3i的座椅亦是如此。
安道拓不仅使得座椅兼具包裹性和支撑性,同时还配备电动腰托,使得不同身形的人群都能调节到最适合自己的支撑点。
蔚来赫赫有名的“女王副驾”同样来自安道拓。
“女王副驾”的座椅配备腿托和脚托,可以说是从上到下都提供舒适的包裹性。
汽车座椅安全带固定点强度分析

t o c k s o f d u mmy .A c c o r d i n g t o t h e GB 1 4 1 6 7 — 2 01 3, t h e t e s t c o n d i t i o n s o f t h e 1 o a d i n g t i me a n d l o a d o f t h e s e a t a r e s e t ,a n d t h e
・
机械研究与应用 ・2 0 1 6 年 第6 期( 第2 9 卷, 总
d o i : 1 0 . 1 6 5 7 6 / j . c n k i . 1 0 0 7 - 4 4 1 4 . 2 0 1 6 . 0 6 . 0 1 8
汽 车 座 椅 安 全 带 固定 点 强 度 分 析
—
DYNA s o f t w a r e .T h e a n a l y s i s r e s u l t s a r e u s e d t o p u t f o r w rd a t h e i mp r o v e me n t s c h e me,a n d C AE a n a l y s i s o f t h e i mp r o v e d
CA E a n a l y s i s o f t h e s e a t s fe a t y b e f o r e t h e p h y s i c a l e x p e r i me n t o f t h e c a r .Ba s e d o n t h e i f n i t e e l e me n t a n a l y s i s t h e o y ,t r h e i f n i t e
关于汽车安全带的固定点强度分析

关于汽车安全带的固定点强度分析摘要:为了进行汽车安全带固定点强度分析,运用有限元分析软件Hypermesh建立白车身、座椅、安全带、人体模块有限元模型。
采用LS-DYNA的显式积分法进行求解,按照国家标准设置规定的载荷,分析结构通过标准的可能性。
验证了运用有限元显式积分分析汽车安全带固定点强度的方法。
关键词:汽车;安全带;固定点;强度引言GB14167-2013《汽车安全带固定点、ISOFIX固定点系统及上拉带固定点》规定中要求,在规定的时间内承受试验要求的载荷情况下,安全带固定点的强度必须要保证安全带不会出现脱落的情况,但允许固定点或者周围区域产生永久变形或者裂纹,且规定安全带上固定点在受力方向的位移不得超过一定的范围。
本文基于此,以国内某车型为例,对安全带固定点的强度进行CAE分析,期望这些分析总结能为汽车车身正向开发提供参考依据。
1 安全带固定点实体模型安全带固定点强度分析的第一步是建立合理的几何模型,表面上理解似乎建立与此相应的整车结构模型要好一些,但不尽然.本研究中基于:①模型复杂、工作量大(计算机时、建模)、周期长;②边界、载荷考虑因素多反倒不利于分析等,采用局部结构几何模型对微型货车安全带固定点强度进行了优化设计分析,大大减轻了建模和计算的工作量。
在考虑与安全带固定点强度相关的驾驶室有关部件和结构之后,用CAD软件UG (Unigraphic)建立了分析腰带固定点强度的几何模型。
其中:驾驶室后围-横梁几何模型由后围、上横梁板、下横梁板以及上、下横梁之间的加强板4个部件所组成.这些部件之间都是以焊接的方式相连接的。
2 有限元模型的建立想要对安全带固定点强度进行分析,首先要创建合理的有限元模型。
由于考虑到整车结构太大,计算机的配置有限,在仿真的过程中应适当的减小分析模型。
白车身的有限元模型采用壳单元建立,与座椅模型、安全带系统组件、上下人体模块进行装配,白车身模型不带挡风玻璃和侧围玻璃。
汽车座椅及安全带固定点强度电液伺服加载试验台的研制

目l试验台整体外观
2试验台机械部分设计
2ห้องสมุดไป่ตู้
l机械台槊
本试验台机械部分包括机体台架、3绀垂直升降 平台.液压伺服缸平衡机构、试骗用各种横板、模块和
工鼗.
试验台架m型钢组成.满足试验的最大力强度要 求,台架不发生断裂、屈服等现象.同时要有足够刚度 能够满足试验要求。试验台构架上驻有3个水平横 梁,每个横粱上装3个液压伺服缸.液压缸后铰座通过 重载滑动轴承与横梁连接。3组升降机可控制3个横 粱的上下位置调整。通过横粱重载滑动轴承可“左右 调整伺服油缸位置。采川弹链平衡器既能有散甲衡伺 服油缸位置,叉不会产生多余f扰,J,还方便伺服油缸
液压与气动
2011年第1期
汽车座椅及安全带固定点强度电液伺服加载 试验台的研制
王燕波1,李军2,韩志富1,邓涛1,曾 思3,姜玉峰1。滕怀海1,张建国1,张巍1
ser、,o
DeVelopment of electrohydmulic automobile
sea,t
stren甜h
test
system for
E
g
蝴於
o”巍””50
闰ll多通道力加载试验曲线
5
6结论
本试验台功能集成,使用方便灵活,加载精度高, 使用范围广。各项性能指标好于最初研发预期指标。 本试验台能完成汽车座椅系统和安全带固定点强度的 各类试验,满足试验性能要求和功能要求.在一年来的 使用过程中.运行平稳,效果良好。本试验台完全能替
圈8变增益力伺服控制方块闺
代国外同类设备。
参考立髓
g矧二…。\
500l/
0 10 20 30 40
l黜}/\ l||||[/、li器f八 l—m¨/\