计算机模拟在头部链轮体铸造工艺设计中的应用
集成计算材料工程及其在铸件开发过程中的应用

集成计算材料工程及其在铸件开发过程中的应用
集成计算材料工程是结合材料科学、计算机科学和工程学的交叉
学科,旨在通过计算机模拟和仿真,预测、优化和设计新材料的性能,以满足工程应用的需求。
在铸件开发过程中,集成计算材料工程为材料选择、铸造工艺优
化和性能预测等方面提供了有效的工具和方法。
具体应用包括以下几
个方面:
1. 材料选择:通过集成计算材料工程,可以预测不同材料的力
学性能、热学性能、耐蚀性等特性,帮助工程师选择最适合特定应用
的材料。
例如,通过计算材料的晶体结构、原子间相互作用和缺陷行
为等因素,可以预测材料的力学强度、韧性和耐磨性。
2. 铸造工艺优化:铸造工艺对于铸件的质量和性能具有重要影响。
集成计算材料工程可以模拟铸造过程中的液态流动、凝固行为和
相变过程等,提供优化铸造工艺的指导。
通过优化铸造参数和结构设计,可以减少铸件缺陷(如气孔、夹杂物和热裂纹)的产生,提高铸
件的质量和性能。
3. 性能预测:通过集成计算材料工程,可以预测铸件的力学性能、磨损性能、疲劳寿命等。
这有助于工程师评估铸件的可靠性和寿命,指导制定合理的使用和维护方案。
例如,通过计算材料的微观结
构和应力分布,可以预测铸件的疲劳寿命和断裂行为。
综上所述,集成计算材料工程在铸件开发过程中的应用可以提高
铸件的质量和性能,减少开发时间和成本,促进材料工程的发展和进步。
带轮铸造工艺设计及数值模拟
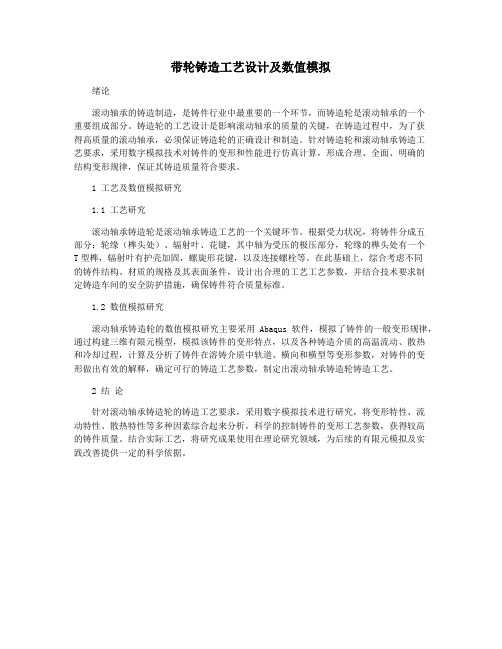
带轮铸造工艺设计及数值模拟绪论滚动轴承的铸造制造,是铸件行业中最重要的一个环节,而铸造轮是滚动轴承的一个重要组成部分。
铸造轮的工艺设计是影响滚动轴承的质量的关键,在铸造过程中,为了获得高质量的滚动轴承,必须保证铸造轮的正确设计和制造。
针对铸造轮和滚动轴承铸造工艺要求,采用数字模拟技术对铸件的变形和性能进行仿真计算,形成合理、全面、明确的结构变形规律,保证其铸造质量符合要求。
1 工艺及数值模拟研究1.1 工艺研究滚动轴承铸造轮是滚动轴承铸造工艺的一个关键环节。
根据受力状况,将铸件分成五部分:轮缘(榫头处)、辐射叶、花键,其中轴为受压的极压部分,轮缘的榫头处有一个T型榫,辐射叶有护壳加固,螺旋形花键,以及连接螺栓等。
在此基础上,综合考虑不同的铸件结构、材质的规格及其表面条件,设计出合理的工艺工艺参数,并结合技术要求制定铸造车间的安全防护措施,确保铸件符合质量标准。
1.2 数值模拟研究滚动轴承铸造轮的数值模拟研究主要采用Abaqus软件,模拟了铸件的一般变形规律,通过构建三维有限元模型,模拟该铸件的变形特点,以及各种铸造介质的高温流动、散热和冷却过程,计算及分析了铸件在溶铸介质中轨道、横向和横型等变形参数,对铸件的变形做出有效的解释,确定可行的铸造工艺参数,制定出滚动轴承铸造轮铸造工艺。
2 结论针对滚动轴承铸造轮的铸造工艺要求,采用数字模拟技术进行研究,将变形特性、流动特性、散热特性等多种因素综合起来分析,科学的控制铸件的变形工艺参数,获得较高的铸件质量。
结合实际工艺,将研究成果使用在理论研究领域,为后续的有限元模拟及实践改善提供一定的科学依据。
CAE仿真指导铸造关键工艺参数优化设计
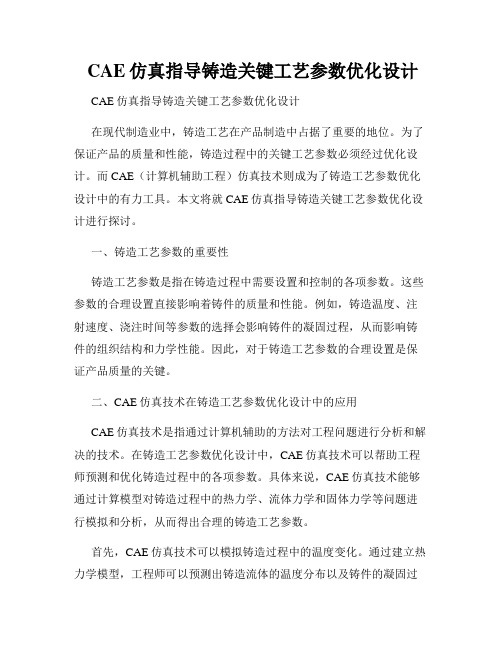
CAE仿真指导铸造关键工艺参数优化设计CAE仿真指导铸造关键工艺参数优化设计在现代制造业中,铸造工艺在产品制造中占据了重要的地位。
为了保证产品的质量和性能,铸造过程中的关键工艺参数必须经过优化设计。
而CAE(计算机辅助工程)仿真技术则成为了铸造工艺参数优化设计中的有力工具。
本文将就CAE仿真指导铸造关键工艺参数优化设计进行探讨。
一、铸造工艺参数的重要性铸造工艺参数是指在铸造过程中需要设置和控制的各项参数。
这些参数的合理设置直接影响着铸件的质量和性能。
例如,铸造温度、注射速度、浇注时间等参数的选择会影响铸件的凝固过程,从而影响铸件的组织结构和力学性能。
因此,对于铸造工艺参数的合理设置是保证产品质量的关键。
二、CAE仿真技术在铸造工艺参数优化设计中的应用CAE仿真技术是指通过计算机辅助的方法对工程问题进行分析和解决的技术。
在铸造工艺参数优化设计中,CAE仿真技术可以帮助工程师预测和优化铸造过程中的各项参数。
具体来说,CAE仿真技术能够通过计算模型对铸造过程中的热力学、流体力学和固体力学等问题进行模拟和分析,从而得出合理的铸造工艺参数。
首先,CAE仿真技术可以模拟铸造过程中的温度变化。
通过建立热力学模型,工程师可以预测出铸造流体的温度分布以及铸件的凝固过程。
根据模拟结果,工程师可以调整铸造温度和凝固时间等参数,以实现理想的凝固结构和性能。
其次,CAE仿真技术可以模拟铸造过程中的流体流动情况。
通过建立流体力学模型,工程师可以预测出浇注过程中的金属液流动速度和压力分布。
根据模拟结果,工程师可以调整注射速度和浇注时间等参数,以优化铸造工艺,避免产生缺陷,提高铸件的质量。
此外,CAE仿真技术还可以对铸件的固态变形进行模拟和分析。
通过建立固体力学模型,工程师可以预测出铸件在凝固和冷却过程中的应力和变形情况。
根据模拟结果,工程师可以调整铸造温度和冷却速率等参数,以减少应力集中和变形产生,提高铸件的整体性能。
三、CAE仿真技术的优势和挑战CAE仿真技术在铸造工艺参数优化设计中具有许多优势。
有限元模拟技术在主体锻造工艺设计中的应用
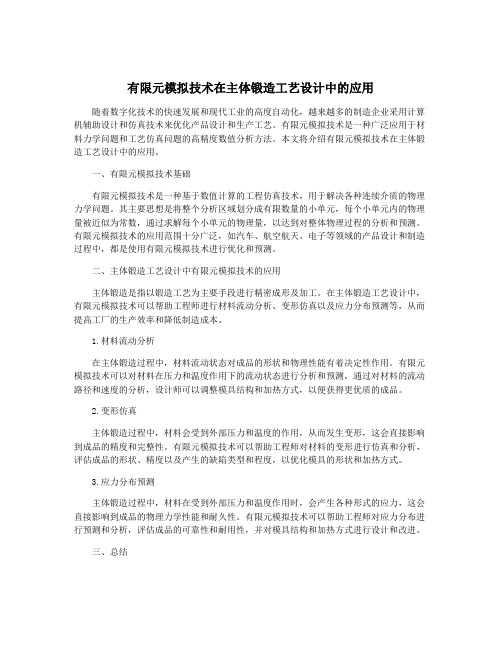
有限元模拟技术在主体锻造工艺设计中的应用随着数字化技术的快速发展和现代工业的高度自动化,越来越多的制造企业采用计算机辅助设计和仿真技术来优化产品设计和生产工艺。
有限元模拟技术是一种广泛应用于材料力学问题和工艺仿真问题的高精度数值分析方法。
本文将介绍有限元模拟技术在主体锻造工艺设计中的应用。
一、有限元模拟技术基础有限元模拟技术是一种基于数值计算的工程仿真技术,用于解决各种连续介质的物理力学问题。
其主要思想是将整个分析区域划分成有限数量的小单元,每个小单元内的物理量被近似为常数,通过求解每个小单元的物理量,以达到对整体物理过程的分析和预测。
有限元模拟技术的应用范围十分广泛,如汽车、航空航天、电子等领域的产品设计和制造过程中,都是使用有限元模拟技术进行优化和预测。
二、主体锻造工艺设计中有限元模拟技术的应用主体锻造是指以锻造工艺为主要手段进行精密成形及加工。
在主体锻造工艺设计中,有限元模拟技术可以帮助工程师进行材料流动分析、变形仿真以及应力分布预测等,从而提高工厂的生产效率和降低制造成本。
1.材料流动分析在主体锻造过程中,材料流动状态对成品的形状和物理性能有着决定性作用。
有限元模拟技术可以对材料在压力和温度作用下的流动状态进行分析和预测,通过对材料的流动路径和速度的分析,设计师可以调整模具结构和加热方式,以便获得更优质的成品。
2.变形仿真主体锻造过程中,材料会受到外部压力和温度的作用,从而发生变形,这会直接影响到成品的精度和完整性。
有限元模拟技术可以帮助工程师对材料的变形进行仿真和分析,评估成品的形状、精度以及产生的缺陷类型和程度,以优化模具的形状和加热方式。
3.应力分布预测主体锻造过程中,材料在受到外部压力和温度作用时,会产生各种形式的应力,这会直接影响到成品的物理力学性能和耐久性。
有限元模拟技术可以帮助工程师对应力分布进行预测和分析,评估成品的可靠性和耐用性,并对模具结构和加热方式进行设计和改进。
三、总结随着数字化技术和自动化技术的不断发展,主体锻造工艺设计中的有限元模拟技术将得到更广泛的应用。
利用计算机模拟技术解决铸件质量问题

利用计算机模拟技术解决铸件质量问题[目的]运用计算机模拟技术,通过对铸件工艺技术参数的分析计算与动态模拟演示,预测出铸件在生产中可能出现的问题与缺陷。
针对具体问题与缺陷,对设计工艺参数进行优化与调整,从而及时有效的控制了铸件质量,避免和减少铸件缺陷。
[过程和方法]首先用Expert软件对UG系统输出的实体数值进行几何剖析与网格划分,再将待铸工件的浇冒系统,化学成份,浇注温度,造型材料,铸型条件等相关工艺参数进行输入、计算,模拟出铸件的动态充型过程、动态凝固过程和温度场显示,最后对计算与演示结果进行评估。
结合理论分析、优化和调整铸件的工艺设计参数、模具结构,最终使铸件在计算机模拟过程中达到完美无缺陷,再付诸实施。
[结果]极大的减少生产资源的浪费和缩短了生产周期,无需投入就可创造更多的经济效益。
[结论]通过实践证明:运用计算机模拟技术,可以有效地预测铸件缺陷、优化铸造工艺,使铸件的生产过程更加趋于科学化、合理化,这一新技术切实可行,可以大力推广使用。
标签:铸件缺陷;计算机模拟;Expert软件;UG系统;预测;优化TB1 前言随着现代高科技的迅猛发展,企业科技更新已成为不可逆转的发展趋势,计算机模拟技术是一项先进技术,涉及数学、流体力学、材料科学、计算机科学、计算机图形学……,需要综合多学科知识;其理论性很强、应用性很广,它随着指导理论的发展而发展,必将在装备制造领域中发挥出重要的作用。
2 Expert模拟分析系统铸造,是一门理论性和工艺性都极强的学科,而且其生产过程很封闭,人们经常称之为“黑箱子”工程,因此在生产中对铸件质量的控制是十分困难的。
在过去,铸件的浇冒口工艺设计与工艺参数的制定,必须要有足够经验的技术人员方能完成。
尽管看上去设计很合理,但在实践过程中还是会出现预想不到的缺陷,而且出现缺陷时往往找不到关键原因之所在,须经过多次反复实践与调整才能最终形成合理的铸造工艺方案。
工厂生产的铸件是千差万别的,几何尺寸变化万千,每个铸件都这样反复多次试验,势必造成巨大浪费。
利用计算机模拟技术优化设计轮毂加工工艺

利用计算机模拟技术优化设计轮毂加工工艺随着科技的不断发展,计算机模拟技术被广泛应用于各个领域,其中包括制造业。
利用计算机模拟技术优化设计轮毂加工工艺,可以提高生产效率、降低成本、优化产品质量等方面带来诸多好处。
一、利用计算机模拟技术分析轮毂加工工艺在传统的轮毂加工工艺中,往往需要花费大量的时间和精力进行试错。
而利用计算机模拟技术,可以通过建立模型,进行虚拟仿真,从而模拟和分析轮毂加工的每一个流程和细节,帮助设计师和工程师准确地了解整个加工流程,减少制造中出现的错误和问题。
通过对模型进行不同的参数调节,还可以得出最佳加工方案和生产线配置。
二、优化轮毂加工工艺设计计算机模拟技术的运用极大程度上提高了加工工艺的设计效率和准确性。
可以通过模拟和分析加工过程中轮毂各个部位的情况,得出最佳的加工参数和刀具选择。
同时还可以对产品的表面光洁度、精度等多个方面进行仿真模拟,从而得到最佳的工艺方案。
这使得加工过程更加高效、精确,避免了设计误差甚至可能对产品造成的损坏。
三、利用计算机模拟技术优化生产线配置在制造业中,生产线配置对于产品的制造效率和质量具有至关重要的作用。
利用计算机模拟技术,可以仿真模拟不同加工线的工作流程,从而确定最优生产线的配置方案。
在模拟过程中,可以对整个生产过程进行调整或模型参数的优化,以使生产线运转更为优化和高效。
四、带来的好处优化设计轮毂加工工艺,减少工序,大幅提高生产效率,降低制造成本;大大缩短了产品的开发周期,提升了产品质量和精度。
同时,通过计算机模拟,避免了进行一系列实际测试所耗费的时间、人力和物力。
这样,设计师和工程师能够把更多的时间和精力放在真正创造、提高和改善产品的创新上。
综上所述,利用计算机模拟技术优化设计轮毂加工工艺,不仅可以提高生产效率和质量,降低成本,还能使制造过程更为高效和精确。
随着科技的不断发展,这一技术也将被广泛应用于制造业以及其他各行各业。
计算机辅助技术在铸造机械设计中的应用
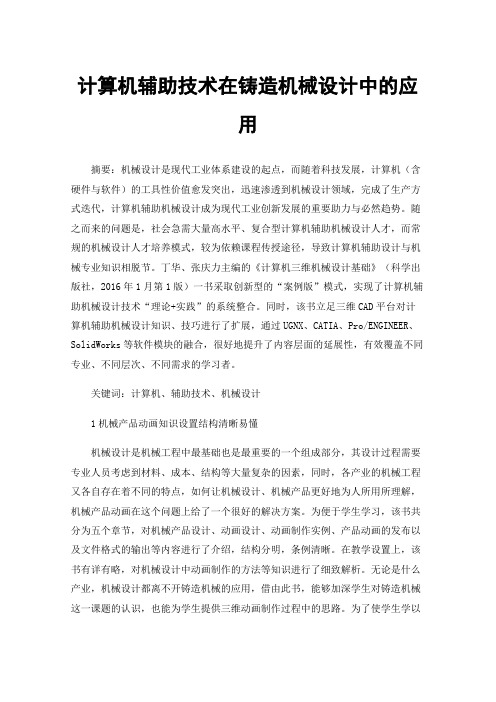
计算机辅助技术在铸造机械设计中的应用摘要:机械设计是现代工业体系建设的起点,而随着科技发展,计算机(含硬件与软件)的工具性价值愈发突出,迅速渗透到机械设计领域,完成了生产方式迭代,计算机辅助机械设计成为现代工业创新发展的重要助力与必然趋势。
随之而来的问题是,社会急需大量高水平、复合型计算机辅助机械设计人才,而常规的机械设计人才培养模式,较为依赖课程传授途径,导致计算机辅助设计与机械专业知识相脱节。
丁华、张庆力主编的《计算机三维机械设计基础》(科学出版社,2016年1月第1版)一书采取创新型的“案例版”模式,实现了计算机辅助机械设计技术“理论+实践”的系统整合。
同时,该书立足三维CAD平台对计算机辅助机械设计知识、技巧进行了扩展,通过UGNX、CATIA、Pro/ENGINEER、SolidWorks等软件模块的融合,很好地提升了内容层面的延展性,有效覆盖不同专业、不同层次、不同需求的学习者。
关键词:计算机、辅助技术、机械设计1机械产品动画知识设置结构清晰易懂机械设计是机械工程中最基础也是最重要的一个组成部分,其设计过程需要专业人员考虑到材料、成本、结构等大量复杂的因素,同时,各产业的机械工程又各自存在着不同的特点,如何让机械设计、机械产品更好地为人所用所理解,机械产品动画在这个问题上给了一个很好的解决方案。
为便于学生学习,该书共分为五个章节,对机械产品设计、动画设计、动画制作实例、产品动画的发布以及文件格式的输出等内容进行了介绍,结构分明,条例清晰。
在教学设置上,该书有详有略,对机械设计中动画制作的方法等知识进行了细致解析。
无论是什么产业,机械设计都离不开铸造机械的应用,借由此书,能够加深学生对铸造机械这一课题的认识,也能为学生提供三维动画制作过程中的思路。
为了使学生学以致用,方便其利用动画制作进行项目汇报、改进或者评判产品设计,该书列举了一系列动画制作运用实例,便于在实际操作时的理解和运用。
2构建多模块知识体系,夯实计算机三维机械设计基础计算机辅助设计是一种设计工作开展形式,可用的工具不止一种。
2.第5章 计算机技术在铸造技术中的应用

第5章 计算机技术在铸造技术中的应用 5.1铸件凝固过程数值模拟 5.1.1 概述 在铸造生产中,铸件凝固过程是最重要的过程之一,大部分铸造缺陷产生于这一过程。凝固过程的数值模拟对优化铸造工艺,预测和控制铸件质量和各种铸造缺陷以及提高生产效率都非常重要。凝固过程数值模拟可以实现下述目的: (1)预知凝固时间以便预测生产率。 (2)预知开箱时间。 (3)预测缩孔和缩松。 (4)预知铸型的表面温度以及内部的温度分布,以便预测金属型表面熔接情况,方便金属型设计。 (5)控制凝固条件。 (6)为预测铸应力,微观及宏观偏析,铸件性能等提供必要的依据和分析计算的基础数据。 铸件凝固过程数值模拟开始于60年代,丹麦FORSUND把有限差分法第一次用于铸件凝固过程的传热计算。之后美国HENZEL和KEUERIAN应用瞬态传热通用程序对汽轮机内缸体铸件进行数值计算,得出了温度场,计算结果与实测结果相当接近。这些尝试的成功,使研究者认识到用计算数值模拟技术研究铸件的凝固过程具有巨大的潜力和广阔的前景。于是世界上许多国家都相继开展了铸件凝固过程数据模拟以及与之相关的研究工作。 5.1.2 数学模型的建立和程序设计 液态金属浇入铸型,它在型腔内的冷却凝固过程是一个通过铸型向环境散热的过程。在这个过程中,铸件和铸型内部温度分布要随时间变化。从传热方式看,这一散热过程是按导热,对流及辐射三种方式综合进行的。显然,对流和辐射的热流主要发生在边界上。当液态金属充满型腔后,如果不考虑铸件凝固过程中液态金属中发生的对流现象,铸件凝固过程基本上看成是一个不稳定导热过程。因此铸件凝固过程的数学模型正是根据不稳定导热偏微分方程建立的。但还必须考虑铸件凝固过程中的潜热释放。 基于分析和计算模型开发相应的程序,即可实现铸造凝固过程温度场的计算。 5.1.3 温度场的数值模拟 在热模拟中,温度场的数值模拟是最基本的,以三维温度场为主要内容的铸件凝固过程模拟技术已进入实用阶段,日本许多铸造厂采用此项技术。英国的Solstar系统由三维造型,网格自动剖分,有限差分传热计算,缩孔缩松预测,热物性数据库及图形处理等模块组成。 5.1.4 铸件充型过程的数值模拟 铸件充型过程的数值模拟是通过计算金属液充型过程中的流体流动得出的。充型过程的数值模拟可以分析在给定工艺条件下,金属液在浇注系统中以及在型内的流动情况。包括:流量的分布、流速的分布以及由此导致的铸件温度场分布。 充型过程数值模拟一方面分析金属液在浇冒口系统和型腔中的流动状态,优化浇冒口设计并仿真浇道中的吸气,以消除流股分离和避免氧化,减轻金属液对铸型的侵蚀和冲击;另一方面,分析充型过程中金属液及铸型温度变化,预测冷隔和浇不足等铸造缺陷。 充型过程数值模拟技术由于所涉及的控制方程多而复杂,计算量大而且迭代结果易发散,加上自由表面边界问题的特殊处理要求使其难度软件可对中等复杂铸件进行三维流场分析,获得比较符合实际情况的初始温度场分布。 铸造充型过程数值模拟技术主要有三种方法: (1)SIMPLE法,即压力连接方程半隐式方法(Semi- Implicit Method for Pressure Linked Equation); (2)SMAC法,即简化标示粒子法(Simplifed Marker and Cell); (3)SOL A- VOF法,即解法 (Solu-tion Algorithm)及体积函数法 (Volume of Fluid)。 5.1.5 应力场的数值模拟 铸件热应力的数值模拟是通过对铸件凝固过程中热应力场的计算、冷却过程中残余热应力的计算来预测热裂纹敏感区和热裂纹的。应力场分析可预测铸件热裂及变形等缺陷。 由于三维应力场模拟涉及弹性-塑性-蠕变理论及高温下的力学性能和热物性参数等,研究的难度大。现在研究多着重于建立专门用于铸造过程的三维应力场分析软件包,有些研究是利用国外的通用有限元软件对部分铸件的应力场进行模拟分析,这对优化铸造工艺和提高铸模寿命发挥了重要作用。应力场模拟分析正向实用化发展,但迄今为止还没有一种科学方法准确测量金属铸件各个部位的热应力或残余应力。 5.1.6 铸件微观组织模拟 铸件微观组织数值模拟是计算铸件凝固过程中的成核、生长等,以及凝固后铸件的微观组织和可能具备的性能。铸件微观组织模拟经过了定性模拟、半定量模拟和定量模拟阶段,由定点形核到随机形核。这一研究存在的问题是很难建立一个相当完善的数学模型来精确计算形核数,枝晶生长速度及组织转变等。瑞士 M Rappaz教授与美国 Stefanescu教授在 1985年前后同时进行该项目的研究。他们从宏观温度场入手,分别对铝合金及镍基合金和铁的晶粒数,晶粒尺寸分布及二次臂距进行估算。铸件微观组织模拟研究今后将向定向凝固及单晶方面发展,同时在计算精度、计算速度等方面有很多工作要做。 5.1.7 低压铸造工艺模拟 低压铸造适合于生产内部质量要求较高、尺寸精度要求较高的铝镁合金铸件。充型速度可控,使得充型平稳,可有效控制卷气和夹渣,防止合金氧化,适合于易氧化的铸件。且铸件在压力下凝固,辅以合理的冷却系统,有利于补缩,易于获得无缺陷铸件。 低压铸造工艺可分为开放式和封闭式。开放式指模具型腔直接与空气接触,因此充型后没有增压、保压凝固过程。封闭式指型腔通过透气孔与大气相连,充型后可进行增压、保压。由于封闭式可以根据铸件的结构与凝固特点制定增压、保压规范,获得更高的内部质量,因此是常见的低压铸造工艺。
- 1、下载文档前请自行甄别文档内容的完整性,平台不提供额外的编辑、内容补充、找答案等附加服务。
- 2、"仅部分预览"的文档,不可在线预览部分如存在完整性等问题,可反馈申请退款(可完整预览的文档不适用该条件!)。
- 3、如文档侵犯您的权益,请联系客服反馈,我们会尽快为您处理(人工客服工作时间:9:00-18:30)。
m et r ing1塑圈 n 参磊 工热 工 垫 型 w w w.重a|wo k箜 0.COr 加 丝 堡 箜 笙 95
圜
属。
血
分微小的的缩松 ,同时冒 口的尺寸过大 ,浪费了大量金
4 .工艺方案Ⅲ及模拟结果
通过 Ve at i C s模拟软件对工艺方案 Ⅱ进行浇注系统 w 的设计 ,直浇道尺寸 ¥ 0 mm× 10 m× 0 m 10 6 3 m 9 0 m;横浇
固过程 中,冒1 5内金属 的温度始终处于铸件的最 高状态 , 补缩通道畅通 ,冒1 5是最后凝 固部位 ,实现 了从铸 件到
( )工艺方案 Ⅲ 3 是在工艺方案 Ⅱ的基础上 , 上浇 加 注系统 ,适当降低 冒口高度 。模拟结果显 示,工艺 Ⅲ 实
警■■■■ 得 位置凝 固时 间 t 4 1S = 5 1 ,取此 处体 积为 8 e 0 r ,计算 a
出轮辐 与轮缘 连接 处 冒口模 数 M = . e 6 5 m,冒口直径 d = 4 mm,冒口高度 / =15 = 2 m 2 39 4 2 .d 5 4 m,为完成对铸 件的圆满补缩 ,铸件圆周需均 布 4个这 样的 冒 口,工艺 方案 I 模型如图 4所示 。
图5 工艺方案 I 缺陷分布
3 工艺方案 Ⅱ及模拟结果 .
工艺方案 I 改进的要点是 :? 肖除相邻两 冒 V之 间轮 I
缘区域 ,以及轮毂与 冒口结合 区域 的孤 立液相 区,延长
冒口的补缩距离 ,使热节 完全转移到 冒 口内,实现铸件
2 .工艺方案 I 及模拟结果
根据铸件凝 固结果 ,运用 Ve at i C s模拟软件进行 冒 w 口的设计。铸件 总体积 I 9 e , 4 m ,体收缩率 5 8 ,轮 =5 .% 毂处凝 固时间 t=8 1s 73 ,取轮毂区域体积为 10 m ,计 0e
工艺方案 Ⅲ模 拟 的缺 陷预测 如图 1 0所示 。可 以看 出,缩孔 、缩松缺陷出现在 冒口及浇 注系统内,整 个凝
( )工艺方案 Ⅱ在轮 毂部位加 上适 当尺寸 的补贴 , 2 同时在工艺方案 I中轮缘 区域 出现缺 陷的铸件下部设置
适当尺寸 的冷铁 ,有效地延长 了冒 口的补缩距离 ,缩孔 、
件底部散热快 ,已明显凝 固;t 90 时 ,铸 件轮缘 区 =10 s
图 1 工艺方案 Ⅲ缺陷分布 0
经机加工 ,没有发现缩孔 、缩松等缺陷 , 铸件组织致密 ,
力学性能达到了使用要求 。
域的钢液即将分割为 6部分 ,且 由 6个柱形 冒口分别进 行补缩 ,浇注系统 已完全凝 固;t 3 0 s ,轮辐处 的 = 60 时
18 % ,铸 型初始温度 2 % 。对铸 件进行凝 固模拟 ,其 50 5
结果见 图 3 。
金属 液 ( %)
10 0
与 冒口结合 区域在凝 固后 期产生 了孤立 液相 区,导致缩 孔 、缩松缺 陷,需进行工艺改进。
金属 液 ( %)
】0 0
图 3 铸件凝 固模拟结果
从 图 3可以看 出,缩孔 、缩 松缺 陷 出现 在轮毂 、轮 辐与轮缘连接处 ,以及 两轮辐之 间的轮缘 区域。根据铸 件结构和模 拟结果 ,需在铸 件浇注位置 时的顶 面设置适 当尺寸 的冒E ,对凝 固过程 中产生 的收缩进 行补足 ,使 l 缩孔 、缩松转移到冒口内。
懈
一 ■ ■ _
三、结语
导致缩孔 、缩松缺陷。
缩松被成功转移到 了冒 L中。 I
( )工艺方案 I中铸件圆周采用 6个柱形 冒1 1 3,轮
毂处采用一个柱形 冒 E进 行补缩 ,由于 补缩距离 过小, l
补缩瓶颈断裂 ,铸件内出现 7部分孤立液相 区,并 向冒
口根部延伸 ;t 520 =1 0 s时,此 时处 于最 后凝 固 阶段 , 铸件 已经完全凝固,冒口
金属 液 ( %)
10 0
图8 工艺方案Ⅲ三维模型
对工艺方案 Ⅲ进行 凝 固模 拟,其 过程如 图 9所 示。 其中深色显示的部位 表示 钢液仍处于液态或半液态 ,没
有完全凝固,浅色 区域 表示 已经完 全凝 固。可 以看 出, 当凝固过程进行 到 t 60 时 ,浇注系统开始凝 固,同 =0s 时 由于冷铁的激冷作用 ,降低 了激冷 区的铸 件模 数 ,铸
( )t6 O a =Os
道对 称 分 布 ,截 面尺 寸 为 q rn  ̄Om ;内浇 道 3个 ,截 面 尺
寸为 , O m;为节 约金属 ,将 轮缘 处 的冒 I尺 寸 改为 k m 6 : I
 ̄ 5 m 3 0 m,将轮毂处 的冒口尺寸改 为 6 9 m b 0 mX 5 m 3 40 m X 60 m。工艺方案 Ⅲ模型如 图 8 0m 所示。
算得 出轮 毂 处 冒 口模 数 M =9 1m,冒 口直径 d .e 。=
到 冒口的顺序凝 固,为此 在相 邻两 冒口之 间的铸件底 部
各设置一块 厚度为 9 r 的冷 铁 ,在轮毂部位 添加适 当 0m a
尺寸的补贴,其他参数不变,工艺方案Ⅱ 模型如图6 所示。
4 8 m,冒口高度 H =15 7 2 m。轮缘与轮辐热节 8m .d = 3m
图 6 工艺 Ⅱ 三维模型
工艺方案 Ⅱ模拟 的缺陷预测如 图 7所示。可以看出 ,
改进工艺后 ,有效地 延长 了冒口的补缩距 离 ,工艺方案
I中出现 的缩孔 、缩 松已基本消除 ,只是在 轮缘有 两部
金属液 ( %)
10 0
7 5
图4 工艺方案 I 三维模 型
工艺方 案 I 模拟的缺 陷预测如 图 5所示 ,从 中可 以 看 出,缩孑 、缩松大部分 已经转移 到 了冒 口中 ,冒口有 L 足够大的补缩能力。但 是 ,由于补缩距离过 小 ,补缩通 道过早地被 阻断 ,造成两 冒 口之间 的轮缘 区域 以及 轮毂