废乳化液处理
废乳化液处理工艺流程

废乳化液处理工艺流程
《废乳化液处理工艺流程》
废乳化液是指在工业生产过程中产生的含有乳化剂和油脂的废水。
处理废乳化液是环境保护和资源再利用的重要环节。
下面介绍一种常见的废乳化液处理工艺流程。
首先,废乳化液进入处理装置,经过初步的固液分离。
通过重力沉降或机械过滤,大部分固体颗粒被分离出来,液体部分则进入处理设备。
接着,废乳化液经过调节PH值,利用添加化学药剂的方法去除其中的油脂。
通常采用的方法有沉淀法、机械分离法和溶剂萃取法。
通过这一步骤,废乳化液中的油脂被有效去除,环境污染降低。
然后,处理后的液体经过生化处理。
通过加入特定的微生物菌种,对废乳化液中的有机物进行生物降解,将污染物质转化为无害的较简单的化合物,从而净化废水。
最后,经过生化处理的液体通过净化设备,如活性炭吸附、超滤膜过滤等,去除残留的微量污染物,使废乳化液得到彻底净化。
经过以上处理工艺流程,废乳化液得到了有效处理,达到了排放标准,同时也可对废水中的有用物质进行回收利用,提高资
源利用效率。
这一处理工艺流程在废乳化液处理领域得到了广泛应用,对环境保护和可持续发展产生了积极影响。
废乳化液处理方法

废乳化液处理方法
乳化液在机械加工、金属轧制等行业中被广泛应用,但使用后产生的废乳化液如果不妥善处理,会对环境造成严重污染。
那废乳化液该怎么处理呢?
处理废乳化液,一般可以采用物理化学法。
首先要进行破乳,这就好比是把一团乱麻解开,让油和水分离。
可以通过添加破乳剂来实现,就像给这团乱麻找到了一把快刀。
在添加破乳剂时一定要注意剂量哦,多了少了都不行,这可是个技术活!然后进行沉淀,让分离出来的物质慢慢沉淀下去,这就像是让它们安静地“睡”在容器底部。
接着进行过滤,把沉淀后的杂质过滤掉,让水变得更清澈。
哎呀,可别小看这些步骤,每一步都要精心操作,稍有不慎就可能前功尽弃呀!
在这个过程中,安全性和稳定性可太重要啦!就像走钢丝一样,稍有偏差就可能出大问题。
处理过程中要防止化学药剂的泄漏,那可不得了,会造成很大危害呢!还要保证设备的正常运行,不能关键时刻掉链子呀!所以操作人员一定要高度重视,打起十二分的精神来。
这种处理方法的应用场景那可多了去了!无论是大型工厂还是小型作坊,只要有废乳化液产生,都可以用这个方法。
它的优势也很明显呀,处理效果好,能把废乳化液处理得干干净净,让环境不再受到污染。
而且操作相对简单,成本也不是很高,多好呀!
就拿某个机械加工厂来说吧,之前他们对废乳化液的处理很头疼,不知道该怎么办。
后来采用了这种物理化学法,哇塞,效果那叫一个显著!不仅解决了污染问题,还为企业节省了不少成本呢。
你说这是不是很棒?
所以呀,处理废乳化液就得用这种物理化学法,效果好,又安全可靠。
还等什么呢,赶紧行动起来吧!让我们一起为保护环境出一份力!。
废乳化液处理

废乳化液处理简介废乳化液是工业生产过程中产生的废水之一,其处理对于环境保护和资源利用具有重要意义。
废乳化液是指在乳化液生产、使用过程中所产生的废水,其中含有残余的乳化剂、含油物质以及其他污染物。
正确处理废乳化液可以减少对水环境的污染,同时回收其中的有价值物质,实现资源的循环利用。
本文将介绍废乳化液处理的方法及步骤,并针对不同处理工艺进行了详细的阐述。
废乳化液的处理方法废乳化液的处理方法主要包括物理处理、化学处理和生物处理三种方式。
具体选择何种处理方法,需根据废乳化液的污染特征和处理要求来确定。
物理处理物理处理主要是通过对废乳化液进行分离、过滤等操作,将废乳化液中的含油物质与其他污染物分离出来,达到净化液体的目的。
常用的物理处理方法包括: - 沉淀处理:通过重力或离心力将固体颗粒从废乳化液中沉淀出来,常见的沉淀设备有沉砂池、沉淀池等。
- 过滤处理:将废乳化液通过过滤装置,通过滤网、滤芯等将悬浮固体颗粒和油分分离出来,常用的过滤设备有滤袋、滤板等。
化学处理主要是针对废乳化液中的特定污染物采用化学方法进行处理,以达到降解或转化有害物质的目的。
常用的化学处理方法包括: - 氧化处理:将废乳化液中的有机物通过氧化剂进行氧化反应,使其转化为无毒、易降解的物质。
常见的氧化剂有过硫酸盐、高锰酸钾等。
- 沉淀处理:通过加入沉淀剂,使废乳化液中的悬浮颗粒形成沉淀,从而达到固液分离的目的。
常见的沉淀剂有氢氧化钙、氯化铁等。
生物处理生物处理利用微生物的作用,将废乳化液中的有机污染物降解为无害物质。
常用的生物处理方法包括: - 好氧处理:将废乳化液与空气进行接触,利用好氧微生物降解有机物。
好氧处理能够有效降解废乳化液中的有机物,但对于乳化剂的降解能力较弱。
- 厌氧处理:将废乳化液在缺氧或无氧条件下进行处理,利用厌氧微生物将有机物降解为甲烷等无害物质。
废乳化液处理的步骤废乳化液处理的具体步骤可以根据处理方法的选择来确定,一般包括以下几个步骤:废液预处理废液预处理主要是对废乳化液进行初步的处理,去除其中的大颗粒悬浮物、大量油脂等杂质。
废乳化液处理工艺与设备的改进

的 。在 机 床 切 削 使用 的 乳 化 液 中 为 了 提 高 乳 化 液 的 防 锈 性 , 加 入 了 亚 硝 酸钠 等 成 分 。 还 基于本文所研究废水 的特殊性 , 采用原 工艺 , 若 则 存 在 处 理 效 率 较 低 且 成 本过 高 的 问题 , 因此 需 要 研究 适 用 的处 理 工 艺 , 以使 排 放水 的指 标 能 符 合 公 司 内部 的 污
备 在操 作 过 程 中更安 全 , 备 运 作 的 成本 降低 , 来 更 大 的 经 济 效 益 。 设 带
关 键 词 : 化 液 ; 凝 剂 ; 收 乳 絮 回
中图分类号 :682 0 4 .
文献标识码 : A
文 章 编 号 : 6 49 4 ( 0 2 0 — 1 60 1 7 — 9 4 2 1 ) 70 6 — 2
入 S R处 理 系统 , 过 该 系 统处 理 后 达 标 排 放 。 B 经 2 1 1 试 验 材 料 . .
水综合处理系统 。
问 , 拌 停 止 后 , 浴 冷却 至 室温 , 察 絮 凝 现 象 。然 后 搅 水 观
再 将 溶 液 用 滤 纸 过 滤 , 滤 出 液测 定 水 质 指 标 。 取 通过该试验表明 , 用 投加 药剂之 前进行 加热 , 采 加
热 的温 度 控 制 在 4 ℃左 右 即 可 , 择 P 5 选 AC 和 稀 硫 酸 进
通 过 破 乳 剂 比例 试 验 、 乳 剂 用 量 试 验 、 拌 时 间 破 搅
试 验 和破 乳 温 度 试 验 等 确 定 出破 乳 试 验 最 佳 条 件 为 :
L : Y9— 3 3: , 用 量 分 别 为 2 0 / Y8 L . 1其 . g m。和 0 6 / . g
废乳化液处理
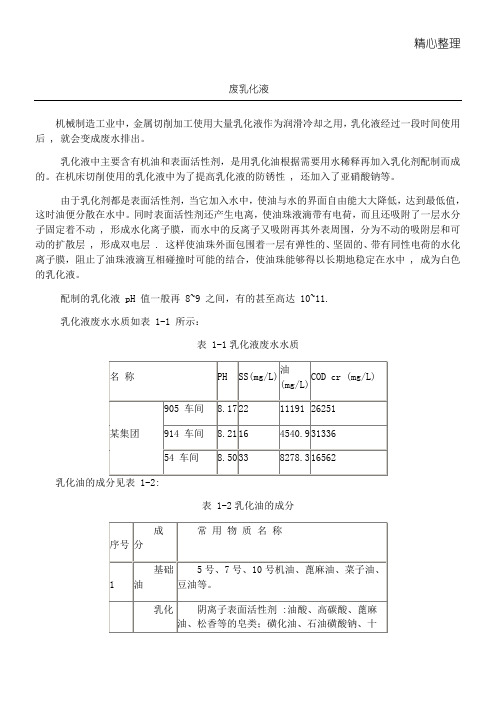
精心整理废乳化液机械制造工业中,金属切削加工使用大量乳化液作为润滑冷却之用,乳化液经过一段时间使用后 , 就会变成废水排出。
乳化液中主要含有机油和表面活性剂,是用乳化油根据需要用水稀释再加入乳化剂配制而成的。
在机床切削使用的乳化液中为了提高乳化液的防锈性 , 还加入了亚硝酸钠等。
2.2.1 乳化液废水处理原理根据乳化液的性质,进行乳化液废水的处理需经过二个步骤:破乳剂油; (2) 水质净化去除表面活性剂等物质。
破乳方法种类较多,有盐析法、乳酸法、凝聚法、顶替法、高压电法、吸附法等等。
一般常用的采用盐析凝聚混合法,现介绍如下在乳化液中加入电解质,电解质的离子在乳化液中发生强烈的水化作用即争水作用,使乳化液中的自由水分子减少了 , 对油珠产生脱水作用,从而破坏了乳化液油珠的水化层,中和了油珠的电性,破坏了它的双电层结构,因而油珠失去了稳定性,产生凝聚现象 ( 电解质一般分为二、三价的钙、镁、铝等盐类 ) ,其反应式如下:2C 17 H 33 COONa + 2MgCl 2 -→ (C 17 H 33 COO) 2 Mg+2NaCl油酸皂镁皂2C 17 H 33 (OSO 3 Na) COONa+2CaCl 2 -→ (C 17 H 32 ) 2 (OSO 3 ) 2Ca (COO) 2 +4NaCl磺化蓖麻油2-2 所示:2.2 处理工艺流程选择及设备图 2-1 原乳化液处理机处理工艺流程图上述处理工艺流程中存在以下问题 :a. 由于乳化液中油、SS、COD含量较高,一级气浮只能除去大部分油、SS、COD,残留的部分只能靠石英砂滤罐、两级活性炭吸附来保证出水达标,因此石英砂滤罐及两级活性炭滤罐负荷较重,造成经常反冲和活性炭很快饱和失去吸附作用需要更换的情况发生。
b.气浮设备进气未设自控装置,靠人工调整,很难达到良好的气浮效果,工人操作难度大。
a.采用两极气浮处理,能将SS、油在气浮处理阶段内完成达标,去除绝大部分CODcr值(COD值在70~170mg/L范围内),残留的少量CODcr值只需一级活性炭滤罐处理,就能达到国家排放标准。
HW09油水烃混合物或乳化液处理案例(危废、有机、案例、环评.
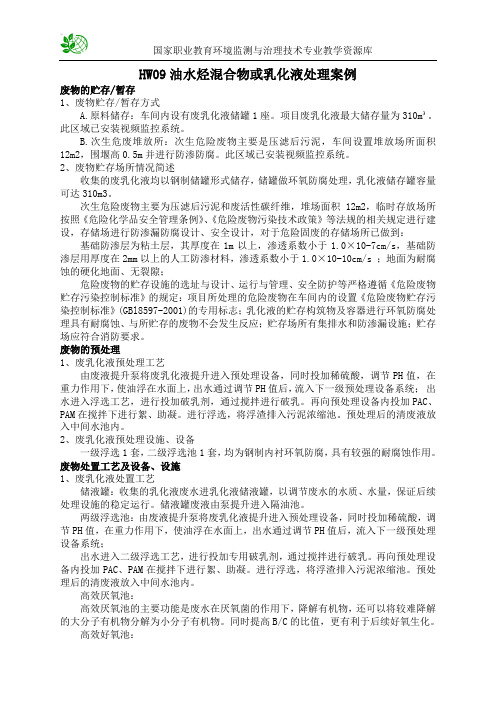
HW09油水烃混合物或乳化液处理案例废物的贮存/暂存1、废物贮存/暂存方式A.原料储存:车间内设有废乳化液储罐1座。
项目废乳化液最大储存量为310m³。
此区域已安装视频监控系统。
B.次生危废堆放所:次生危险废物主要是压滤后污泥,车间设置堆放场所面积12m2,围堰高0.5m并进行防渗防腐。
此区域已安装视频监控系统。
2、废物贮存场所情况简述收集的废乳化液均以钢制储罐形式储存,储罐做环氧防腐处理,乳化液储存罐容量可达310m3。
次生危险废物主要为压滤后污泥和废活性碳纤维,堆场面积12m2,临时存放场所按照《危险化学品安全管理条例》、《危险废物污染技术政策》等法规的相关规定进行建设,存储场进行防渗漏防腐设计、安全设计,对于危险固废的存储场所已做到:基础防渗层为粘土层,其厚度在1m以上,渗透系数小于1.0×10-7cm/s,基础防渗层用厚度在2mm以上的人工防渗材料,渗透系数小于1.0×10-10cm/s ;地面为耐腐蚀的硬化地面、无裂隙;危险废物的贮存设施的选址与设计、运行与管理、安全防护等严格遵循《危险废物贮存污染控制标准》的规定:项目所处理的危险废物在车间内的设置《危险废物贮存污染控制标准》(GBl8597-2001)的专用标志;乳化液的贮存构筑物及容器进行环氧防腐处理具有耐腐蚀、与所贮存的废物不会发生反应;贮存场所有集排水和防渗漏设施;贮存场应符合消防要求。
废物的预处理1、废乳化液预处理工艺由废液提升泵将废乳化液提升进入预处理设备,同时投加稀硫酸,调节PH值,在重力作用下,使油浮在水面上,出水通过调节PH值后,流入下一级预处理设备系统;出水进入浮选工艺,进行投加破乳剂,通过搅拌进行破乳。
再向预处理设备内投加PAC、PAM在搅拌下进行絮、助凝。
进行浮选,将浮渣排入污泥浓缩池。
预处理后的清废液放入中间水池内。
2、废乳化液预处理设施、设备一级浮选1套,二级浮选池1套,均为钢制内衬环氧防腐,具有较强的耐腐蚀作用。
废乳化液利用处置技术概述
2 . 2 各 种 处 置 方 法优 缺 点 比较
各 种废 乳化液的处理方法不 同, 决定 了其 在设 备 、 构 筑物 、 处
厂废水 、 来港油轮 压舱水 、 油 脂厂 含油废 水 、 内燃 机 的含油 废水 、 理 废 水 效 果 以及 处 理 费 用 等 方 面 也 有 所 不 同 。 各 种 废 乳 化 液 的 处理方法 比较结 果见 表 1 。 油 田采 油 废 水 等 。
第4 1 卷 第 1 7期 2 0 1 5 年 6 月
山 西 建 筑
SHANXI ARCH I TECTURE
Vo 1 . 41 No. 1 7
J u n . 2 0 1 5
・2 0 3・
文章编号 : 1 0 0 9 — 6 8 2 5 ( 2 0 1 5 ) 1 7 — 0 2 0 3 — 0 3
方式 、 耐火等级 、 防火分 区等 , 按照火灾 危险性分 类合理 确定煤 库 [ 3 ] 孙 胜 旺. 煤储 运 工 艺设 计及 运 行 [ J ] . 安徽化工, 2 0 1 4 , 4 0
1 . 3 废 乳 化液 的危 害
从 表 1中可 以看 出 , 废 乳 化液 的各种 处 理 方法 都 有其 局 限
在实际处理过程 中只能根据废 乳化液 的成 分 、 油存在 的形式 、 包括 乳化液在内的含油废水对生态 环境 的影 响主要 体现 在 : 性, 回收利 用的深度 以及 排放方式等 , 选 用合理 的处理方法 或者按 照 1 ) 危害人体健康: 可引起人类头痛、 恶心、 呕吐、 呼 吸 困难 等。 待处理废乳化液 的成 分和性质选用若干种处理方法 。 2 ) 恶化水体 , 危害水生生物 : 浮油 浮于水 面形成 油膜 , 隔绝空气 与
机械加工废水处理中废乳化液如何回收处理
机械加工废水处理中废乳化液如何回收处理废乳化液的回收处理废乳化液中含有大量矿物油料(例如配制一吨乳化油需用机械油600~800kg)及表面活性剂,过去由于对它的危害性认识不足,所以都采用直接排放。
随着工业的迅速发展,这种含油污水的排放量与日俱增。
据不完全统计,中国大陆仅机械工业废乳化液的日排放量已逾2亿吨。
含油污水造成的环境污染日益严重,严重地影响了水生动植物的生长、农业灌溉和人们的生活用水。
此外,废乳化液中的表面活性剂(乳化剂)由于其作用是使矿物油料高度分散在水中,所以更难清除,而且不少乳化剂有增加致癌物的作用,其危害性比分散的油污更为严重。
因此,未经处理的废乳化液不得任意排放。
废乳化液的回收处理,既符合环保要求,又可节约能源,降低生产成本。
废乳化液的回收处理工艺废乳化液回收处理的工艺过程大致为:废乳化液的集中→去除杂质→破乳→取油→水质净化→取水样化验→废水排放或供再循环使用。
废乳化液处理的关键工艺是要使油水分离,即破乳。
也就是要将乳化液中的油滴,从水的包围中分离出来,并使油滴相互聚集,然后借助于重力分离作用,使油、水分离开来。
废乳化液的破乳方法废乳化液的破乳方法,主要有酸化法和聚化法两种。
酸化法就是往废乳化液中加入酸(如盐酸或硫酸)。
所加入的酸可利用工业废酸。
由于在目前的乳化液配方中,多数选用阴离子型乳化剂(如石油磺酸钠、磺化蓖麻油),所以遇到酸就会破坏,乳化生成相应的有机酸,使油水分离,而酸中氢离子的引入,也有助于破乳的过程。
酸的用量是待处理乳化液重量的0.2%,浓度为37%;如果采用废酸时,则酸的用量应适当加大。
聚化法就是在废乳化液中添加盐类电解质(如0.4%氯化钙)和凝聚剂(如0.2%明矾),以达到乳化液破乳的目的。
酸化法的优点是油质较好,成本低廉,水质也好,水质中含油量一般在20mg/L以下,化学耗氧量(COD)值也比其它破乳方法低;其缺点是沉渣较多。
聚化法的优点是投药量少,一般工厂均有条件使用,但油质较差。
乳化液处置方法
乳化液处置方法乳化液是一种由两种不相溶的液体组成的混合物,其中一种液体以微小颗粒的形式分散在另一种液体中。
乳化液常见于食品、化妆品、医药等领域,但在使用过程中也会产生一些废弃物。
本文将介绍乳化液的处置方法,以减少对环境的影响。
对于已使用过的乳化液,我们可以通过回收和再利用的方式进行处理。
回收乳化液有两种主要方法:物理处理和化学处理。
物理处理是指通过物理手段,如离心、过滤、蒸发等,将乳化液中的固体颗粒或污染物分离出来,得到清洁的液体。
化学处理则是通过添加化学药品,如沉淀剂、消泡剂等,使乳化液中的固体或污染物沉淀下来,从而实现分离和净化。
如果乳化液无法回收利用,我们需要进行正确的废弃处理。
首先,应将乳化液储存在密封的容器中,以防止泄漏和污染环境。
然后,我们可以选择将废弃的乳化液交给专业的废物处理公司进行处理。
这些公司通常会采用高温燃烧、化学中和、微生物降解等方法,将乳化液进行处理,以减少对环境和人体的危害。
对于乳化液的生产过程中产生的废水和废气,我们也需要进行相应的处理。
废水可以通过物理化学方法进行处理,如沉淀、过滤、蒸发等,以去除其中的污染物,并达到排放标准。
废气则需要进行适当的处理,如利用吸附剂、催化剂等进行净化,以降低对大气的污染。
乳化液的包装废弃物也需要得到妥善处理。
包装废弃物应分类收集,并送往专门的回收站点进行处理和回收利用。
这样不仅可以减少资源浪费,还能降低对环境的影响。
总结起来,乳化液的处置方法包括回收利用和废弃处理两种方式。
回收利用可以通过物理处理和化学处理来实现,废弃处理则需要依靠专业的废物处理公司进行处理。
此外,乳化液生产过程中产生的废水、废气和包装废弃物也需要得到相应的处理。
通过正确的处置方法,可以最大程度地减少对环境的影响,实现资源的有效利用。
废乳化液处理工艺
废乳化液处理工艺
嘿,朋友们!今天咱来聊聊废乳化液处理工艺这档子事儿。
你说这废乳化液啊,就像是家里那堆乱糟糟不知道怎么收拾的杂物。
咱得想法子把它给搞定,让它不再是个麻烦。
先来说说物理处理法吧。
这就好比是咱用筛子筛东西,把大的杂质给筛出来。
通过过滤啊、离心啊这些手段,把那些能看得见的脏东西给分离出来。
这办法简单直接,能解决一部分问题呢。
再讲讲化学处理法,这可有点像变魔术啦!加些化学药剂进去,让废乳化液发生奇妙的化学反应,把里面不好的东西转化掉或者沉淀下来。
就好像魔术师挥一挥魔法棒,一切就变得不一样了。
还有生物处理法呢!这就像是请了一群勤劳的小生物来帮忙打扫。
让微生物们大显身手,把那些有机物给分解掉,多神奇呀!
那咱在处理的时候可得注意啦,不能马虎。
就好像做饭一样,调料放多了或者放少了,味道可就差远了。
得掌握好火候,把握好各种方法的使用时机和条件。
咱想想看,如果不处理好这些废乳化液,那岂不是跟家里垃圾乱扔一样,多脏多乱呀!那对环境的影响可就大了去了。
这环境就像是咱的大院子,得干干净净、舒舒服服的才行呀。
而且,处理好了废乳化液,还能变废为宝呢!就像把旧衣服改成漂亮的小物件一样,多有意思。
这不是一举两得的好事嘛!
所以呀,大家可别小瞧了这废乳化液处理工艺,它可关系到我们的生活环境和未来呢!咱都得重视起来,认真对待,让我们的世界更加美好,不是吗?咱可不能让这些废乳化液随意捣乱,得把它们治理得服服帖帖的。
大家说是不是这个理儿呢?总之,废乳化液处理工艺很重要,我们得行动起来,为了我们的环境,为了我们的未来!。
- 1、下载文档前请自行甄别文档内容的完整性,平台不提供额外的编辑、内容补充、找答案等附加服务。
- 2、"仅部分预览"的文档,不可在线预览部分如存在完整性等问题,可反馈申请退款(可完整预览的文档不适用该条件!)。
- 3、如文档侵犯您的权益,请联系客服反馈,我们会尽快为您处理(人工客服工作时间:9:00-18:30)。
混凝剂法:1号高效破乳剂
投量大,没破乳。
投量大,没破乳。
搅拌后马上出现矾花,破乳效果好。
搅拌后马上出现矾花,破乳效果好。
酸析法:先加硫酸将样品pH值调到2,然后加碱调至7,投加1号高效破乳剂.
(1)pH值调到7后,无矾花产生;(2)加破乳剂搅拌后,产生矾花;(3)破乳效果好。
(1)pH值调到7后,无矾花产生;(2)加破乳剂搅拌后,产生矾花;(3)破乳效果好.
结论
酸析法破乳
酸析法破乳
混凝剂法
混凝剂法
处理工艺流程选择及设备
图2-1原乳化液处理机处理工艺流程图
上述处理工艺流程中存在以下问题:
a.由于乳化液中油、SS、COD含量较高,一级气浮只能除去大部分油、SS、COD,残留的部分只能靠石英砂滤罐、两级活性炭吸附来保证出水达标,因此石英砂滤罐及两级活性炭滤罐负荷较重,造成经常反冲和活性炭很快饱和失去吸附作用需要更换的情况发生。
3
防锈剂
碱类:碳酸钠、三乙醇胺、苯乙醇胺等。水溶性缓蚀剂:亚硝酸钠、苯甲酸钠、磷酸三钠、硼砂、水玻璃等。油溶性缓蚀剂:石油磺酸钡、环烷酸锌、羊毛脂等。
4
防霉杀菌剂
苯酚、四氯酚、已基汞硫代水杨酸钠等。
5
稳定剂
三乙醇胺、乙醇、异丙醇等。
6
助溶剂
少量水与乙醇的混合物。
7
极压添加剂
氯化石腊、氯化硬脂酸等.酸性磷酸脂、磷酸三甲酚脂等、硫化脂肪油、硫化油酸、烷基硫化物等、二聚酸乙二脂单脂等.
加药系统:Φ×H=580×930(mm),V有效=;配有两台加药泵CDL2-20及搅拌机,N=
二级气浮系统:Φ×H=×(m),Q=2m3/h接触室上升流速Vc=10mm/S,气浮分离速度Vs=S,分离室停留时间10min,R=30﹪,水
压力~,设出水调节装置;
溶气泵:32FPD15Z,Q=h,P=;
a.采用两极气浮处理,能将SS、油在气浮处理阶段内完成达标,去除绝大部分CODcr值(COD值在70~170mg/L范围内),残留的少量CODcr值只需一级活性炭滤罐处理,就能达到国家排放标准。因此,活性炭使用时间长(可达一年),并不经常反冲(半个月一次)。
b.省去了一级石英砂滤罐,使处理工艺流程简便。
c.原水泵采用潜水泵,保证泵能随时启动。
d.气浮器1、气浮器2均采用自动控制,不需人工管理,能达到最佳气浮效果,电磁阀采用不锈钢材料,专利产品,使气浮效果更好。
该设备于1996年5月起分别用在重庆某(集团)股份有限公司发动机车间乳化液废水处理、905车间乳化液处理、914车间乳化液处理、54车间乳化液处理,效果良好,见表2-3.
b.气浮设备进气未设自控装置,靠人工调整,很难达到良好的气浮效果,工人操作难度大。
c.三个滤罐需经常反冲洗,阀门多,操作繁杂,很难掌握,出水不能保证。
针对上述问题,我们设计了一种新型乳化液处理机,采用了新的处理工艺,解决了上述存在的问题,其处理工艺流程图如图2-2所示:
图2-2新型乳化液处理机处理工艺流程图
表2-3乳化液废水处理效果(监测数据)
名称
PH值
SS(mg/L)
油(mg/L)
CODcr(mg/L)
原水
发动机车间
905车间
914车间
54车间
630
22
16
33
70
11191
830
26251
31336
16562
出水
发动机车间
905车间
914车间
54车间
13
12
8
国标
6~9
70
10
100
备注
采用的JR-2型系列一体化乳化液废水处理机、1号高效破乳絮凝剂
﹪~1﹪
清晰透明,含油量15~50mg/L,耗氧量2000mg/L。
絮状沉渣很少
粘胶状及絮状
投药量少,一般工厂适用;油质较差,粘厚、水分多,再生困难。
混合法
综合盐析法和凝聚法的任何一种药剂
投盐﹪~﹪
凝聚剂﹪~﹪
清晰透明,含油量20~40mg/L,耗氧量2000mg/L。
絮状沉渣很少
稀糊状
投药量中等,破乳能力强,适应性广,对难于破乳的乳化液尤为适宜。
序号
成分
常用物质名称
1
基础油
5号、7号、10号机油、蓖麻油、菜子油、豆油等。
2
乳化剂
阴离子表面活性剂:油酸、高碳酸、蓖麻油、松香等的皂类;磺化油、石油磺酸钠、十二烷基苯磺酸钠等磺酸盐与硫酸脂类;高级醇磷酸酯二钠盐等磷酸脂类。非离子型表面活性剂:聚氧乙脂肪醇醚、司本(失水山梨醇与脂肪酸的脂类,如月桂酸脂、油酸脂等)、吐温(聚氧乙烯化的司本)等。两性表面活性剂:6503、6501清洗剂等。
四种破乳方法比较见表2-1:
表2-1四种破乳方法比较
方法
药剂名称
投药量
处理后水质
沉渣
油质
优缺点
盐析法
氯化钙
氯化镁
硫酸钙
硫酸镁
氯化钠
二价药为﹪~﹪
一价药为3﹪~5﹪
清晰透明,含油量20~40mg/L耗氧量2000mg/L。
絮状沉渣很少
棕黄色,清亮
油质好,便于再生,投药量最高,水中含盐量最大。
凝聚法
聚合氯化铝明矾
废乳化液处理
废乳化液
机械制造工业中,金属切削加工使用大量乳化液作为润滑冷却之用,乳化液经过一段时间使用后,就会变成废水排出。
乳化液中主要含有机油和表面活性剂,是用乳化油根据需要用水稀释再加入乳化剂配制而成的。在机床切削使用的乳化液中为了提高乳化液的防锈性,还加入了亚硝酸钠等。
由于乳化剂都是表面活性剂,当它加入水中,使油与水的界面自由能大大降低,达到最低值,这时油便分散在水中。同时表面活性剂还产生电离,使油珠液滴带有电荷,而且还吸附了一层水分子固定着不动,形成水化离子膜,而水中的反离子又吸附再其外表周围,分为不动的吸附层和可动的扩散层,形成双电层.这样使油珠外面包围着一层有弹性的、坚固的、带有同性电荷的水化离子膜,阻止了油珠液滴互相碰撞时可能的结合,使油珠能够得以长期地稳定在水中,成为白色的乳化液。
活性炭过滤系统:Φ×H=×(m),配有过滤泵CDL2-20;
设备外形尺寸:L×B×H=4400×2200×2100(㎜),Q=2m3/h装机容量:。
3.结论
采用JR型系列一体化乳化液废水处理机和1号高效破乳絮凝剂处理乳化液废水是可行的,并且由于处理效果好,设备自动化,运行成本低,确保出水水质达标等,具有极大的推广应用价值。
配制的乳化液pH值一般再8~9之间,有的甚至高达10~11.
乳化液废水水质如表1-1所示:
表1-1乳化液废水水质
名称
PH
SS(mg/L)
油(mg/L)
CODcr(mg/L)
某集团
905车间
22
111911336
54车间
33
16562
乳化油的成分见表1-2:
表1-2乳化油的成分
8
消泡剂
乙醇和其他低级醇、聚醚型表面活性剂.
9
软水剂
无水碳酸钠、氢氧化钠等.
2.乳化液废水的处理
乳化液废水处理原理
根据乳化液的性质,进行乳化液废水的处理需经过二个步骤:
破乳剂油;(2)水质净化去除表面活性剂等物质。
破乳方法种类较多,有盐析法、乳酸法、凝聚法、顶替法、高压电法、吸附法等等。一般常用的采用盐析凝聚混合法,现介绍如下
油酸皂镁皂
2C17H33(OSO3Na)COONa+2CaCl2-→(C17H32)2(OSO3)2Ca(COO)2+4NaCl
磺化蓖麻油
2R-SO3Na+CaCl2-→[R-SO3]2Ca+2NaCl(R为烷基)
石油酸钠石油磺酸钙
加入混凝剂,则加快起到油水分离的目的。
在实际使用中,应注意调整水的pH值,将pH值调整为较好。
运行费用如表2-4所示:
表2-4乳化液废水运行费用表
废水量(m3/h)
电耗
药耗
合计(元)
运行费(元/m3)
耗量(KW)
金额(元)
耗量
金额(元)
JR-2型乳化液处理机:由反应箱、二级气浮系统、二级活性炭过滤系统、加药系统、电控系统、楼梯六个部分组成。
反应箱:A×B×L=1500×1000×800(mm),V有效=,t=,内设搅拌机,N=;
破乳方法及破乳剂、絮凝剂对不同的乳化液废水是不同的,用户在处理该类废水时应先优选破乳剂及絮凝剂做小样实验,为正确选用处理设备、设施打下基础。
酸化法
废硫酸废盐酸和石灰
约为废水6﹪
清澈透明,含油量20mg/L以下,耗氧量低于其他方法。
约为10﹪左右
棕红色,清亮.
水质好,含油量低,还可以废治废,但沉渣多。
我们经过多次实验筛选,配制出高效破乳絮凝剂,在工程实践中被广泛应用,见表2-2所示:
表2-2破乳试验结果表
试验方法
精工3号
美孚切削油
日石EC-50
在乳化液中加入电解质,电解质的离子在乳化液中发生强烈的水化作用即争水作用,使乳化液中的自由水分子减少了,对油珠产生脱水作用,从而破坏了乳化液油珠的水化层,中和了油珠的电性,破坏了它的双电层结构,因而油珠失去了稳定性,产生凝聚现象(电解质一般分为二、三价的钙、镁、铝等盐类),其反应式如下:
2C17H33COONa+2MgCl2-→(C17H33COO)2Mg+2NaCl