Commercial Polymer Blends 8
PMM Ultra Blend 高性能矿物改性沥青乳胶封面剂说明书

PRODUCT DESCRIPTION & BENEFITS Polymer-Modified MasterSeal (PMM) Ultra Blend Pavement Sealer is a high performance mineralreinforced asphalt emulsion sealcoat hot blended with flexible, high strength polymers and specially selected surfactants for superior adhesion, flexibility and durabil ity. PMM Ultra Blend is a higher solids, faster dryingpavement sealer designed to beautify and protect asphalt pavement. PMM Ultra Blend is a ready to apply material that is factory blended with aggregate. PMM Ultra Blend meets ASTM D8099/D8099M-17 for Asphalt Emulsion Pavement Sealer .RECOMMENDED USESPMM Ultra Blend is ideal for protecting and beautifying all types of pavement surfaces including parking lots, shopping malls, airports, driveways, roadways and more.ESTIMATING MATERIAL REQUIREMENTS One gallon of PMM Ultra Blend will cover approximately 70 - 82 square feet per gallon per coat (7.75 – 9.1 square yards per gallon per coat).APPLICATION RATEApply PMM Ultra Blend at a rate of 70 – 82 square feet per gallon per coat (7.75 – 9.1 square yards per gallon per coat). Application rates may vary due to pavement porosity and method of application.SURFACE PREPARATIONSSurface must be clean and free from loose material and dirt. Cracks should be filled with SealMaster Cold or Hot-Applied Crack Filling Materials. Oil stains should be cleaned and primed with SealMaster Oil Spot Primer.APPLICATION EQUIPMENTPMM Ultra Blend shall be applied by mechanical squeegee/brush equipment or spray equipmentcapable of spraying coatings with sand. Equipment shall have continuous agitation or mixing capabilities to maintain homogeneous consistency of mixed material throughout the application process. T ruck mount or self-propelled squeegee/brush equipment shall have at least 2 squeegee or brush devices (one behind the other) to assure adequate distribution and penetration of PMM Ultra Blend into bituminous pavement. HandFactory Blended with AggregateSMT-154REVISED 04/21/18POL YMER-MODIFIED MASTERSEAL (PMM)UL TRA BLEND PAVEMENT SEALERPhone: REVISED 04/21/18squeegees and brushes shall be acceptable in areas where practicality prohibits the use of mechanized equipment.MIXING PROCEDURESMix PMM Ultra Blend thoroughly before applying. If needed, a small amount of water may be added to facilitate application.APPLICATION PROCEDURESFor optimum performance and durability apply a minimum of two coats of PMM Ultra Blend. A third coat may be applied to high traffic areas such as parking lot entrances, exits and drive lanes for added durability. Allow each coat to dry thoroughly before applying successive coats. Allow final coat to dry for 24 hours prior to opening to vehicle traffic.APPLICATION WEATHER CONDITIONSPMM Ultra Blend shall not be applied when temperature is expected to drop below 50° F during application and for a period of at least 24 hours after application. Do not apply if rain is imminent or forecast within 12 hours.LINE STRIPING AND TRAFFIC MARKINGS Use SealMaster T raffic Paints for line striping and traffic markings.PACKAGING AND AVAILABILITYPMM Ultra Blend is available for plant pick up or bulk tanker load quantities. PMM Ultra Blend is supported by a national network of SealMaster manufacturing and distribution facilities along with a national network of qualified applicators.WARRANTY AND DISCLAIMERThe statements made on this technical data sheet are believed to be true and accurate and are intended to provide a guide for approved application practices. A s workmanship, weather, construction, condition of pavement, tools utilized, and other variables affecting results are all beyond our control, the manufacturer warrants only that the material conforms to product specifications and any liability to the buyer or user of this product is limited to the replacement value of the product only. The manufacturer expressly disclaims any implied warranties of merchantability or fitness for a particular purpose.Factory Blended with AggregatePOL YMER-MODIFIED (PMM) MASTERSEALUL TRA BLEND PAVEMENT SEALERSMT-154。
polymer blends

What are polymer blends? It is "multicomponent polymer". Since most of the multicomponent polymers are of multiple phases, It is also called "multiphase polymer". To emphasis the importance the chemical and/or physical interactions of the polymer chains at a molecular level, it is also been referred to as "polymer alloy".A common polymer blend involves two or more homopolymers mixed together. However, some block copolymers also show phase separation behavior just like polymer blend does. To obtain optimum property of polymers, a blend should have a synergistic property enhancement from all component polymers. For example, high impact polystyrene (HIPS) is polystyrene toughened with SBR (styrene-butadiene rubber). With the use of special techniques, the rubber particles can be totally dispersed in PS matrix. Also, there are PS chains infused in rubber particles forming "cellular structure". With this phase structure, a satisfied toughening effect is achieved with addition of only 5-10% rubber. Another example of toughening PS is to blend styrene-acrylonitrile randomcopolymer and polystyrene-grafted rubber. This product is called ABS. Clearly, there is tremendous change in product properties, as being showed in the plot (a plot comparing the tensile properties of PS, HIPS and ABS):That tells us why the research on polymer blends is catching so much attention in academics as well as in industry. You may be impressed more by looking at a review on this research area (see how polymer scientists get excited about it) . The phase morphology of polymer blends determines their properties and it can be evaluated by many characterization techniques . The phase structure information also includes the interface of phases. To understand the mechanism for forming these structures, we haveto learn a little about the thermal dynamics of polymer blends . Which has been the subject of interests to the polymer physicists for a long time. The first systematic description of polymer systems are made by P. J. Flory. In his bible book "Principles of Polymer Chemistry", he states that two high polymers are mutually compatible with one another only if their free energy of interaction is favorable, i.e., negative . In deed, in a great majority of cases, the mixing of a pair of polymers is endothermic. So the compatibility is really an exception. However, more and more compatible systems have been reported thereafter. People realized that the segmental interactions among the polymers is crucial for understanding these phenomena. Some of the interactions are purposely introduced into the systems to enhance the compatibility. As you touring around this。
玻纤增强pa66复合材料的力学性能

图130%GF-PA66复合材料的力学性能第一作者简介:殷文英(1993—),女,硕士,山东科技大学,研究方向:复合材料及注塑成型。
殷文英,张慧,陈志远(山东科技大学,山东泰安271000)摘要:以30%的玻纤增强尼龙66,通过注塑工艺注塑成标准件,研究了玻纤增强尼龙66复合材料的力学性能,结果表明:玻纤增强PA66的拉伸强度、弯曲强度、冲击强度的平均值分别为154.34Mpa、224.25Mpa、59.27KJ/m 2,力学性能有明显的提升。
关键词:玻璃纤维;PA66;力学性能中图分类号:O631.2文献标识码:A 文章编号:1671-1602(2019)19-0128-011引言聚酰胺-66(PA-66)具有较高的拉伸强度、弯曲强度、压缩强度等优异的力学性能被广泛应用于汽车、化工、电器等行业。
近几年,随着社会的快速发展,单一的材料已经不能够满足市场的需求,拓展应用的空间,复合型的高抗冲增强材料成为一种新的研究课题。
尼龙材料具有吸湿性大、耐酸性差[1]、干态和低温冲击强度低以及吸水后易变形,影响了制品的尺寸稳定性,影响尺寸精度。
所以,使其应用范围受到了一定的限制。
为了改进上述缺点,扩大其应用领域,并更好的满足对使用性能的要求,人们采用多种方法对PA66进行改性[2],以改进PA66塑料的冲击性、热变形性、力学性能、成型加工性能及耐化学腐蚀性能。
杨其等[3]研究了玻纤增强PA66,结果表明,当玻璃纤维质量分数达30%时,纤维对PA66增强效果最佳,复合材料的拉伸强度达112.13MPa。
刘义等[4]对玻纤增强PA66的研究表明,其冲击强度和拉伸强度随玻纤配比的增大而逐渐提高,MFR则逐渐减小。
2实验2.1实验材料GF:短切原丝,单纤维直径分别为6μm,巨石集团有限公司;PA66:德国巴斯夫有限公司。
2.2实验设备注塑机:宁波市北仑区海普塑料机械有限公司电子万能试验机:美特斯工业系统(中国)有限公司摆锤式冲击试验机:济南恒旭试验机技术有限公司扫描电子显微镜:德国蔡司公司3结果与讨论3.1玻纤增强PA66的力学性能分析从图1中可以看出玻纤增强PA66的拉伸强度、弯曲强度、冲击强度的平均值分别为154.34Mpa、224.25Mpa、59.27KJ/m 2。
论芳纶纤维研究进展及制定其相关标准的重要性

Discussion on the Progress of Aramid Fiber Research and the Importance of Establishing Relevant Standards
Wang Zhaolei , Li Yupeng, Zhu Wei, Han Yejing (Tianjin Textile Fiber Inspection Institute)
目前,我国有 60 余所企业、高校及科研机构从 事与芳纶及其产品相关的研究生产工作,分布在山 东、广东、上海、四川等全国各地,例如山东烟台 泰和新材料股份有限公司、广东彩艳股份有限公司 及中蓝晨光化工研究院等在行业内较为知名。
4 应用领域
芳纶由于其综合性能突出,是高性能纤维中发 展最为迅速且重要的成员之一,其优异且全面的性 能使得其以多种形式形态应用于诸多方面,尤其在 高新科技领域日益扮演着重要角色。 4.1 建筑、橡胶、增强补强材料
所以为统一芳纶纤维在行业内的技术要求,急 需制定相关国家标准,以满足市场需求,便于管理 约束,并为实施售后服务、扩大竞争创造条件。制 定相关国家标准不仅可以规范社会生产活动、规范 市场行为,让遍布各地的企业在技术上保持高度的 统一,且为衡量产品质量好坏提供了主要依据。惟 有通过制定并提供统一完善的技术标准,方可使得 先进的科技成果转化为生产力,从而产生更好的经 济效益和社会效益。
聚合物共混和合金介绍

AAN023 Introduction to Polymer Blends and Alloys*A. Franck, TA Instruments GermanyKeywords: blends, alloys, compatibilization, glass transition, mixing enthalpy, synergy, miscibilitySCOPEFrom 1970 to 1980, the demand for plastics inthe United States increased from 20 to 50 billionpounds. The success of plastics is due to the broadspectrum of applications, attributable to a wide rangeof properties which made plastic replace metals,glass, ceramics, paper, natural fibers, packaging,consumer products, piping, furniture, etc...The important properties of plastics are lightweight, breakage resistance, ability to consolidatefunctional parts, relatively inexpensive, easyautomated production, lower costs of manu/facturing,..With the accomplishment of substituting allpossible traditional materials, slower economic andpopulation growth in the developed regions of the word and polymer down grading (due to environ/ mental protection, reinstitution of older values) becoming a significant trend, the polymer growth rates slowed down. Intercompetition among polymers in addition has increased and the development risk of new polymers often outweighs the potential commercial reward.These factors favored the relative inexpensive route of combining two or more commercial available polymers through alloying or blending in order to create product differentiation for new applications.The blending technology turned out to be an excellent tool for tailoring a polymer compound for specific applications requirements, often at much lower production costs then the current available Figure 1: Concentration diagramm of blend & alloys.(A)1(B))(φPφΒmaterial. Alloys and blends developments are market driven and demand an on going dialogue between supplier and customer. The continuous modification and adjustment of blends and alloys for new applications requires an extensive understanding of the relation of material structure, processing and end-use performance. Material testing instruments including Rheometers, dynamic mechanical ana/ lyzers, etc...are a fundamental need o insure this developmentALLOYS AND BLEND TECHNOLOGY In order to mix two components and obtain a product, which doesn’t undergo complete phase separation during processing or end use, a minimum thermodynamic compatibility is necessary. Beyond this level of compatibility, greater attractive forces___________________* Reference: Advances in Polymer blends and Alloys Technology Volume 1; Chapter 1 by S.Y. KienzleTabel 1: Crystalline and amorphous properties and polymersbetween the constituents serve to enhance the properties of the final product.In general for two component mixture, any property can be described by the following equation:P=P 1c 1+P 2c 2+IP 1P 2P i is the property value, c i the concentration and I the interaction coefficient. For I>0, the resultant polymer has better properties then the arithmetic average of the property.For I=0, the properties are additiveFor I<=, the resultant polymer has properties,worse than the arithmetic average of the components.Alloys are synergistic polymer combinations (I>0), if the components are thermodynamically compatible, or strong intermolecular forces make the mixture behave as a single phase material with one single transition (TG). f.ex: PS modified PEO(Noryl) or PS modified PPE (Prevex). For theseblends, PS reduces the melt viscosity sufficiently to allow easy processing and largely retaining strength(modulus), impact resistance, hydrolytic stability of the PEO or PPE.Blends show less intense thermodynamic compatibility and therefore exhibit discrete polymerphases with multiple glass transitions. In general,the properties of blends reflect the weighted arithmetic average of the properties of the consti/tuents (I=0). f.ex: PC/ABS blends. Specific gravity,coefficient of thermal expansion, flexural modulus,etc... are arithmetic averages.BLEND/ALLOY PREPARATIONThere are different ways to mix polymers, meltblending, solution blending, latex or dispersion blending.The melt blending using an extruder is pre-dominately used method to prepare patibilizing agents may be incorporated in the same time in order to enhance the synergism (compounds with functional groups that mate with the dissimilar polymers) to prevent phase separation and to enhance the physical and mechanical properties; for example: block co-polymers.SELECTING POLYMER COMBINATIONS Polymer components, which make the blend, aregenerally selected to complement each other in one or more of the following properties, costs,processability, mechanical properties, warpage,chemical resistance, thermal performance Blends are typically viewed as cost savings: -the more expensive polymer is combined with the less expensive product to provide adequate performance at a significant reduced price (ABS/PC, ABS/Polysulfone, PES/PEEK). In addition, the development of a synergistic property profile (I>0)is the goal.V ery often crystalline and amorphous polymers are blended to achieve a specific property range.Crystalline polymers have excellent chemical resistance, good mechanical properties (especially with reinforcements), low viscosity whereasamorphous polymers provide good dimensional stability (no warpage) and excellent impact strength.Crystallinepolymers Amorphous polymers properties • chemical resistance• dimensional stability and • sharp melting point warpage resistance • low viscosity melt • clarity• good flexural and heat • good impact strengthdistorsion properties with • No property changes at high temperatures reinforcements • melting range polymersPP ABS Nylon PCPBTpoly sulfone poly acrylateThe combination typically results in a product of good dimensional stability, easy processing,chemical resistance and mechanical properties tailored to the specific need. f.ex: Nylon/PPO, PBT/polyacrylate, PBT/PC. Typical applicationsare automotive body panels.The combination of elastomers with a polymer represents another important group of alloys/blends.The application is for impact resistance performance parts. The polymer gives the necessary stiffness,thermal resistance and strength. The rubber provides the impact modification. f.ex: PP/EPDM. An important application is in car bumpers.PHASE BEHAVIOR*A prime consideration in any polymer mixture is the degree of homogeneity of the blend. Immiscible blends form multiple phases for all ratios of composition, the composition of each phase being essentially those of the individual component.Miscible materials mix completely at all blend ratios forming a single phase. Partially miscible systems are very frequent. These blends are miscible at a selective composition and phase separation occurs at other compositions.The thermodynamic driving force for mixing is minimization of the free energy of the system ∆G mix =∆H mix -T ∆S. Thus if the free energy is positive,the system will be immiscible. If the free energy of mixing is negative at any composition, some degree of dissolution will occur and the system will be atleast partially miscible. For the system to be miscible, the second partial derivative on compo-sition of the free energy must be positive. That means,that the plot of the free energy vs. composition must be negative for all compositions and concave upward at all compositions (Figure 2). Blends, which are miscible at one set of conditions, may undergo phase separation if conditions are changing. As such,variations in temperature, pressure and/or shear stress can induce phase separation.Partially miscible systems exhibit local maxims and minims at constant temperature and pressure.The overall composition and the exact shape of the free energy diagram determines whether such asystem is present as a single phase or multiple mixed phases.The kinetics of the phase separation and the morphology of the resulting blend depends upon the stability of the homogeneous mixture at the given condition. If the mixing composition is near a local minimum in the free energy of mixing, the compo-0 1∆(A)(B)RTG mix φΒTypical blends/alloysAmoco PSO/ABS; PSO/PolyesterBorg Warner PPE/PS; ABS/PC; ABS/Nylpn;Celanese, PBT/PET; Nylon/Elastomers; PBT/Hoechst Elastomers DOW PC/ABS Dupont Nylon/Elastomer; PET/Elastomer;PBT/PETGE PPO/PS; PC/ABS; PPO/Nylon;PBT/PET; PC/PolyesterICI PEEK/PES BAYER ABS/NyloTabel 2: Typical blends/Alloys Figure 2.: Free energy of mixing______________________*M.E. Stewart, Eastman Kodak, Kingsport, Tennesee & D.R. Paul University of Texas,AustinFigure 3: Tg’s of binary inniscible, partially, and miscible blendsr.sition is metastable and will separate by a nucleation and growth mechanism. When the new composition condition is near a local maximum in the free energy diagram, then the blend is unstable and will spontaneously phase separate. The equilibrium compositions of the phases at equilibrium are given by the points of tangency of the free energy diagram. The relative contribution of the combinatorial entropy of mixing for polymers, due to the much larger size of the molecules, is small - thus the driving force for mixing is only the enthalpy ∆H mix . As such even relatively weak repulsion forces (non-polar molecules) (∆H mix >0) are sufficient to oppose mixing.The glass transition of polymer blends is strongly affected by the degree of phase separation at segmental level. The determination of the glass transition temperature(s) of a blend is a straight-forward method to access the degree of mixing of a blend. (Figure 3) Generally, the presence of a single,composition- dependent Tg at a temperature between the Tg’s of the component polymers is accepted as evidence of miscibility. Conversely, two-phase blends exhibit two Tg’s. If the polymers are completely immiscible, the Tg’s of the blend will equal the Tg’s of the component polymers. If there is partial miscibility, however, the exact positions of the Tg’s in a two-phase blend will depend upon the relative amount of each component in each phase.MORPHOLOGY AND COMPATIBILIZATIONMiscibility refers to mixing in the amorphous phase and doesn’t preclude crystallization of the blend components. In the absence of crystallinity,miscible blends consist of a single amorphous phase.Because of the lack of structure, miscible amorphous blends are transparent. Transparency therefore is often used as evidence of miscibility. However this is not a proof, as immiscible blends can also be transparent if the dispersed phase refractive index matches that of the matrix.Immiscible and partially miscible blends are more common, than miscible blends. The properties of these blends are highly dependent upon its phase behavior and morphology . When separate phases are present and the proper morphology is obtained, it is possible to combine the desirable attributes of each polymer into a single material. Phase separated blends, thus offer the potential to retain the desirable properties of both components. However the properties related to ductility and toughness, are often less attractive in the blend than in either of the components. This is due to a large extent to the extreme dependence of these properties on the morphology. Toughness requires a homogeneously dispersed phase of spherical particles. High interfacial tension opposes particle breakdown,during melt mixing for example, and causes coalescence. Consequently, the dispersion of the components in many immiscible blends is very rge interfacial energies produce sharp phase boundaries, which results in poor adhesion between phases. This reduces stress transfer between phases.In order to overcome these problems, production of block or graft copolymers has become an important technique to increase adhesion between phases andto control (stabilize) the dispersion of the dispersed phase. The general term for this process is compatibilization and the production of copolymersgAgBgAgBgAgBl o g M o d u l u spart. misciblein situ during the melt mixing process is known as reactive compatibilization. The goal of most compatibilization schemes is to increase the properties of the blends while retaining the two-phase nature and not to promote miscibility of the blend.MARKET FOR BLENDS A ND ALLOYS -LOOKOUT IN THE FUTUREIncreased inter-polymer competition with resultant losses in market share and margins force the polymer suppliers to focus their attention on providing polymer systems that offer unique competitive advantage to their customers. With the development and commercialization of -8 years (compared to 15 to 20 years for new polymers) the blend market is very dynamic. Suppliers are continually developing new alloys and blend to satisfy the changing applications and needs with better engineered products and lower cost products.Alloys and blends represent inexpensive routes to satisfy both end use material requirements and suppliers desires for competitive product differen-tiation. Despite the recession in polymers, the continuous development effort of thesuppliers in a growing market for blends creates a need for advanced material testing instruments to characterize the specific mechanical and other physical properties of blends in the product development environment.。
化纤纺丝 英文书籍

化纤纺丝英文书籍在化纤纺丝方面,有一些英文书籍可以提供深入的了解和学习。
以下是一些值得推荐的书籍:1. "Man-Made Fibres" by J. Gordon Cook 这本书是关于化学纤维制造和应用的经典著作,涵盖了纺丝技术、纤维结构、性能和应用等方面。
2. "Handbook of Textile Fibres" by J. Gordon Cook 这本手册提供了对各种纤维的详细描述,包括化学纤维、天然纤维和特种纤维,对纤维的物理和化学特性进行了全面的介绍。
3. "Polymer Science and Technology for Engineers and Scientists" by A. A. Brentin 这本书涵盖了化学纤维的制备、性能和应用,结合了化学和工程的知识,适合工程师和科学家阅读。
4. "Polymer Fibre Interactions" by Stephen Z. D. Cheng这本书主要探讨了聚合物纤维的相互作用和结构,对纤维的形成、力学性能和表面特性等方面进行了深入的研究。
5. "Textile Fibre Composites in Civil Engineering" by Thanasis Triantafillou 这本书介绍了纺织纤维在土木工程中的应用,包括增强混凝土、纤维增强材料和纤维增强土等方面。
6. "Polymer Blends and Composites" by A. K. Haghi 这本书涵盖了聚合物混合物和复合材料的制备、性能和应用,对纤维增强复合材料的制备技术和性能进行了详细介绍。
这些书籍涵盖了化纤纺丝的不同方面,从纤维的制备、结构到性能和应用等,可以帮助你深入了解和学习化纤纺丝的知识。
Polymer Blends

Encyclopedia of Polymer Sceince and TechnologyCopyright c 2005John Wiley&Sons,Inc.All rights reserved.POL YMER BLENDSPolymer BlendsMixing of two or more different polymers together makes it possible to achieve var-ious property combinations of thefinal material—usually in a more cost-effective way than in the case of synthesis of new polymers.Therefore,great attention has been paid to the investigation of these systems,as well as to the development of specific materials.Recently,the problem of polymer blends has also become im-portant for recycling industrial and/or municipal plastics scrap.A considerable amount of information has been collected during more than three decades,sum-marized in dozens of monographs(see General References).Basic problems associated with the equilibrium and interfacial behavior of polymers,compatibilization of immiscible components,phase structure develop-ment,and the methods of its investigation are described herein.Special attention is paid to mechanical properties of heterogeneous blends and their prediction. Commercially important types of polymer blends as well as the recycling of com-mingled plastic waste are briefly discussed.Equilibrium Phase BehaviorMixing of two amorphous polymers can produce either a homogeneous mixture at the molecular level or a heterogeneous phase-separated blend.Demixing of poly-mer chains produces two totally separated phases,and hence leads to macrophase separation in polymer blends.Some specific types of organized structures may be formed in block copolymers due to microphase separation of block chains within one block copolymer molecule.Two terms for blends are commonly used in literature—miscible blend and compatible blend.The terminology recommended by Utracki(1)will be used in this article.By the miscible polymer blend,we mean a blend of two or more amorphous polymers homogeneous down to the molecular level and fulfilling the thermody-namic conditions for a miscible multicomponent system.An immiscible polymer blend is the blend that does not comply with the thermodynamic conditions of phase stability.The term compatible polymer blend indicates a commercially at-tractive polymer mixture that is visibly homogeneous,frequently with improved physical properties compared with the constituent polymers.12POLYMER BLENDSEquilibrium phase behavior of polymer blends complies with the general thermodynamic rules(2–6)G mix= H mix−T S mix<0(1) andµ i =µii=1,2,...,n(2)where G mix, H mix,and S mix are the Gibbs energy,enthalpy,and entropy of mixing of a system consisting of i components,respectively,µi andµi are the chemical potentials of the component i in the phaseµ andµ .The condition given in equation1is necessary but it is not sufficient.Equation2must be also fulfilled.Generally for a compressible polymer blend the following requirement must be satisfied(5–7):∂2 G mix∂viT,P=∂2 G mix∂viV+∂V∂PT,v i∂2 G mix∂v i∂V>0(3)where v i is the volume fraction of component i,V molar volume of blend,P and T are pressure and temperature of the system.If we consider an incompressible system with V mix=0,the application of equation3to the simple Flory–Huggins relationship for G mix(4)leads to the condition of these stability1 N1v1+1N2v2−2χ12≥0(4)where N1,N2are the numbers of segments of polymer1or2,andχ12is theinteraction parameter between polymers1and2.The entropy contribution(thefirst and second terms on the left-hand side of equation4supporting miscibility ofpolymers is practically zero(N1,N2 1).In this case,the miscibility is controlled by the enthalpy of mixing(interaction parameterχ12).For nonpolar polymerswithout strong interactions,the temperature dependence ofχ12(Fig.1,curve1)is given asχ12=A+BT(5)where A and B are positive constants characterizing enthalpy and entropy parts of interaction parameterχ12,respectively.Its positive value indicates a very poor miscibility of high molecular weight nonpolar polymers.Relationships describing the compressibility of polymer blends are based on the equations-of-state theories(5,6,8–16).These relationships include contribu-tions to the entropy and enthalpy of mixing resulting from volume changes during mixing.The temperature dependence of free-volume interaction is schematically presented as curve2in Fig.1.This value plays a decisive role in determining phase behavior of a polymer blend at high temperature range.POL YMER BLENDS3Fig.1.Schematic temperature dependence of interaction parameters resulting from dif-ferent types of interactions in a polymer blend.(1-dispersive interactions,2-free-volume interactions,3-specific interactions,A-sum of1+2,B-sum of1+2+3).From the equation4it follows that the negative value of parameterχ12isnecessary to obtain a stable homogeneous polymer blend.The negative value of χ12is characteristic of systems with specific interactions such as dipole–dipole or hydrogen bond interactions(1,5,6,17).A schematic representation of the temper-ature dependence of a specific interaction parameter,according(13),is given inFigure1,curve3.The critical value of interaction parameterχc for“symmetric”polymer blendsof polymers1and2(N1=N2=N,N-number of segments in polymer chain)isχc =2/N.Whenχ12value crosses the critical value,a polymer blend separates into two macrophases.The character of the temperature dependence ofχ12determines the shape of the phase diagram(Fig.1).Figure2shows schematic binodal and spinodal curves corresponding to the different types of interaction parameters presented in Figure1.Binodal curves(Fig.2,curves1–4),defining the two-phase region,are calculated from equation2(2,4–6,18).A spinodal curve is obtained by solving of equation4.The spinodal curve defines the region of absolute instability of the polymer blend.The point common to the binodal and spinodal curves is the critical point.The position of the critical point of a blend of monodisperse poly-mers coincides with the maximum(UCST-upper critical solution temperature) or minimum(LCST-lower critical solution temperature)of a binodal curve(18) (Fig.2).If only dispersive interactions among polymer molecules are effective in a blend(Fig.1,curve1),partial miscibility can be expected at low temperatures. Above the UCST,the polymer blend is homogeneous(Fig.2curve1)(4–6).Values4POLYMER BLENDSFig.2.Possible types of phase diagrams corresponding to interactions in Figure1(————binodal curves,———-spinodal curves,UCST—upper critical solution temperature, LCST—lower critical solution temperature).of interaction parameters of nonpolar polymers can be found in literature(1,5,6) or estimated from the solubility parameters,δ1andδ2,of the neat componentsχ≈(δ1−δ2)2(6) Theχparameter of disperse interactions is always positive,and miscibility is driven only by combinatorial entropy of mixing.In general,nonpolar polymers are rarely miscible with each other.Considerable data relevant to interaction energies obtained by different techniques can be found in the literature(5,6,19,20).The area below the spinodal curve is the region of absolute instability of a polymer blend.The phase separation in this region is controlled by a spin-odal mechanism.The region between spinodal and binodal curves is called the metastable region.Phase separation in this region is controlled by a nucleation mechanism.Phase structure at an initial stage of phase decomposition depends on the type of decomposition mechanisms.The characteristic trait of the spinodal decom-position in an absolutely unstable region is phase separation in the whole volume of a blend.Initially,the resulting structure is veryfine,but gradually gets coarse (5,21),and thefinal stage of separation is full macrophase separation.If the phase separation takes place in the metastable region,the decomposition of a blendPOL YMER BLENDS5 depends on the formation of a nucleus of a new phase.The resulting structure at the initial stage is grainy.The critical sizes of existing nuclei increase by Ostwald ripening mechanism(16)—small grains dissolve and large grains grow due to the dependence of the concentration gradient of dissolved molecules of the nucleating component,which are in turn dependent on grain radius.At thefinal stage,when the separation isfinished,the full phase-separated structure is again obtained(5).In unstable region,appearingfluctuations increase.Thefluctuations can be considered as a set of sinusoidal waves with a constant length(6,16).The am-plitude of thefluctuations appearing in the initial stage of the phase separation increases with time,as described by Kwei and Wang in Reference6.The phase structure of the system is co-continuous for a broad range of blend compositions. At the end of the process,separated phases are identical to the blend components. Theories describing various stages of spinodal decomposition(using various ap-proximations)have been developed(16).Scattering methods have been used for many experimental studies of phase structure decomposition in polymer blends. The initial,intermediate,and late stages of phase structure separation,differing in the time dependence of the domain size of individual phases were identified. The individual stages of the phase structure development are described by dif-ferent time dependences of the phase domain size.The development of spatial concentrationfluctuation is generally described by Ginsburg–Landau equation, considering chemical potential as a function of the order parameter,contribution of the random forces,and the hydrodynamic interaction between polymer molecules (16).Similar equations also describe polymer dissolution if,due to a change in thermodynamics parameters,an immiscible blend passes to a miscible one.The phase separation is affected by the presence of a copolymer and by a shearflow (16).A more detailed description of the kinetics of phase decomposition in polymer blends can be found in Reference16.If we have a system with free-volume or specific interactions,an increase in temperature causes phase separation at LCST.In real systems,where sev-eral types of interactions are effective,phase behavior with two regions of partial miscibility of components with UCST and LCST(Fig.2,binodals1and2)or hourglass-shaped binodal and spinodal curves(Fig.2,binodal3)can be expected (5,6,9,13–16).In some cases,a closed loop of immiscibility with LCST and UCST (Fig.2,binodal4)or a closed loop and region of partial immiscibility at high temperatures with LCST(Fig.2,binodals2and4)are observed.This pattern of phase behavior is caused by a diminishing intensity of specific interactions with increasing temperature.Whether polymers are miscible or not depends on a delicate balance of inter-actions among all components in a system(6).Any favorable gain in the energy of mixing is accompanied by an unfavorable noncombinatorial entropy effect(22,23).The effective value of the interaction parameterχeff of a multicomponent polymer blend is controlled by its composition.Blends containing statistical copolymers of A and B monomers can be used as ing the meanfield-theory leads to the following relation forχeffχeff=ij>iχijv Ai−v B jv Bi−v A j(7)6POLYMER BLENDSwhereχij is the interaction parameter between segments i and j.For the identical type of segments,its value is zero.It follows from equation7that at a proper composition of copolymers,the value ofχij can be negative,and the resulting blend is homogeneous.The former discussion deals with liquid–liquid phase behavior;however,one or both components of the blend can sometimes crystallize.For a polymer pair that is miscible in the melt,cooling well below the melting point of pure crystallizable component leads to a pure crystalline phase of that component.Far below the melting point,the free energy of crystallization is considerably larger than that of mixing.Because polymers never become100%crystalline,the pure crystals coexist with a mixed amorphous phase consisting of the material that did not crystallize(6,7).The morphology of heterogeneous polymer blends is controlled by interfacial tension.The interfacial tension,σ,is intrinsically positive and can be defined as the change in the Gibbs free energy when the interfacial area A is reversibly increased at constant temperature and pressure at closed system(24).σ=∂G∂AT,P(8)In a multicomponent system,the tendency to minimize the system Gibbs free energy leads to migration of the minor component on the interface.The re-sulting increase in concentration of this component at the interface(compared to its concentration in the bulk)(24)decreases the interfacial tension,as follows from equation9∂σ2=−RTN2VN1(9)where c2is the molar concentration of the component2, N2is the excess number of molecules of the component2on the interface,N1is the number of molecules of the component1,and V is volume of the system.Therefore low energy additives can greatly reduce the interfacial tension between polymers,and hence are ex-pected to increase the degree of dispersion in blends.Block and graft copolymers are the most effective interfacial agents.They show considerable surface activity of the low energy components,and their emulsifying property depends on their structure.CompatibilizationAs it follows from thermodynamics,the blends of immiscible polymers obtained by simple mixing show a strong separation tendency,leading to a coarse struc-ture and low interfacial adhesion.Thefinal material then shows poor mechanical properties.On the other hand,the immiscibility or limited miscibility of polymers enables formation of a wide range structures,some of which,if stabilized,can impart excellent end-use properties to thefinal material.To obtain such a stabi-lized structure,it is necessary to ensure a proper phase dispersion by decreasing interfacial tension to suppress phase separation and improve adhesion.This canPOL YMER BLENDS7 be achieved by modification of the interface by the formation of bonds(physical or chemical)between the polymers.This procedure is known as compatibilization, and the active component creating the bonding as the compatibilizer(1,6,7).Two general methods are used for compatibilization of immiscible polymers:(i)incor-poration of suitable block or graft copolymers,or(ii)reactive compatibilization.Incorporation of Copolymers(Nonreactive Compatibilization). Block or graft copolymers with segments that are miscible with their respective polymer components show a tendency to be localized at the interface between immiscible blend phases.The copolymers anchor their segments in the relevant polymer,reducing interfacial tension and stabilizing dispersion against coales-cence(24–52).Random copolymers,sometimes also used as compatibilizers,re-duce interfacial tension,but their ability to stabilize the phase structure is limited (53).Finer morphology and higher adhesion of the blend lead to improved mechan-ical properties.The morphology of the resulting two-phase(multiphase)material, and consequently its properties,depend on a number of factors,such as copoly-mer architecture(type,number,and molecular parameters of segments),blend composition,blending conditions,and the like(25,38,39).Creton and co-workers (54)have reviewed the molecular criteria for copolymers linking two immiscible homopolymers that must be fulfilled to achieve a good stress-transfer ability of the interface.In Figure3,the conformation of different block,graft,or random copolymers at the interface is schematically drawn.Fig.3.Possible localization of A-B copolymer at the A/B interface.Schematic of connecting chains at an interface,a-diblock copolymers,b-end-grafted chains,c-triblock copolymers,d-multiply grafted chain,and e-random copolymer.8POLYMER BLENDSBesides copolymers synthesized specially for compatibilization of immiscible polymers,commercial products(typically used as impact modifiers)are utilized as compatibilizers in research as well as in practice.Typical examples are styrene-butadiene block copolymers and their styrene-hydrogenated butadiene analogues used for compatibilization of styrene polymers(PS,HIPS,SAN,ABS),with poly-olefins(49),or ethylene–propylene copolymers for compatibilization of various polyolefins(50).Mechanical properties that are sensitive to stress transfer(impact strength, tensile strength,elongation)are usually considered as criteria of compatibilization efficiency because they indirectly characterize interface adhesion(1,7,45).Mor-phological characteristics,such as particle size of the dispersed phase,structure homogeneity,character of interfacial layer,existence of micelles,or mesophases, also give evidence on the compatibilization efficiency(25,29,40–44).This process,however,inherently bears two practical limitations.Blending of an immiscible polymer pair requires a specific block or graft copolymer.Conse-quently,a specific synthetic procedure is necessary to obtain the desired copolymer. This can be costly,and sometimes there is no feasible technology at manufacturer’s disposal.Moreover,the amount of the copolymer to be added is often significantly higher than that for saturation of the interface.A part of the copolymer may be trapped in the bulk phase during blending and never reach the interface.This fact can negatively affect the blend morphology and may lead to a higher compat-ibilizer consumption.During more than three decades,much information on nonreactive compat-ibilization has been obtained and successfully applied in the development of new multiphase materials.Moreover,the prove efficiency of block or graft copolymers in the controlling of the phase structure development has led to new,more effec-tive approaches to producing these copolymers directly during the blending.This process is known as reactive compatibilization.Reactive Compatibilization.Reactive compatibilization is the process that allows generating graft or block copolymers acting as compatibilizers in situ during melt blending(46,55).These copolymers are formed by reactions at the interfaces between suitably functionalized polymers,and they link the im-miscible phases by covalent or ionic bonds.In this process,the copolymers are formed directly at the interfaces,where they act like preformed copolymers,ie, they reduce the size of the dispersed phase and improve adhesion.For this rea-son,the problem with transport of the compatibilizer to interface is not rele-vant and structure control is easier than in the case of adding preformed copoly-mers.In order to achieve efficient compatibilization of polymer blends,the reac-tions between the functional groups should be selective and fast,and the mixing conditions should minimize the limitation of mass transfer in the course of the reaction.There are several types of reactive compatibilization.If the mixed polymers contain reactive groups,the reaction is straightforward.The polymers without reactive groups have to be functionalized or a miscible polymer containing proper reactive groups is added to the respective component.Therefore,reactive groups such as anhydride,hydroxy,amine,or carboxy are incorporated,into one or both of the polymers to be compatibilized.Maleic anhydride-grafted polymers,such as PP,PE,EPR,EPDM,SEBS,or ABS(46,55),which can react with polymersPOL YMER BLENDS9 containing amino group can serve as examples:Reactive compatibilization of polymers through copolymer formation is also possible with the help of low molecular weight compounds(56),eg by combination of a peroxide with an oligomer coagent for preparation of PE/PP blends(57)or bis-maleic imide for PE/PBT(58).Special cases of reactive compatibilization can be considered radical-initiated reactions of monomers forming homopolymers and grafts on the chains of dissolved polymers.This process is used for manufacture of such important polymers as HIPS or ABS(59).Preparation and Phase Structure DevelopmentMethods of Blend Preparation.Most polymer pairs are immiscible,and therefore,their blends are not formed spontaneously.Moreover,the phase struc-ture of polymer blends is not equilibrium and depends on the process of their preparation.Five different methods are used for the preparation of polymer blends (60,61):melt mixing,solution blending,latex mixing,partial block or graft copoly-merization,and preparation of interpenetrating polymer networks.It should be mentioned that due to high viscosity of polymer melts,one of these methods is re-quired for size reduction of the components(to the order ofµm),even for miscible blends.Melt mixing is the most widespread method of polymer blend preparation in practice.The blend components are mixed in the molten state in extruders or batch mixers.Advantages of the method are well-defined components and universality of mixing devices—the same extruders or batch mixers can be used for a wide range of polymer blends.Disadvantages of the method are high energy consumption and possible unfavorable chemical changes of blend components.Evolution of the phase structure in polymer blends during melt mixing and rules for prediction of the structure of the formed phases are discussed in the next section.During several past years,novel solid state processing methods,such as shear pulverization or cryogenic mechanical alloying,have been developed to pro-vide efficient mixing of polymer blends(62).The polymers are disintegrated in pulverizers at cryogenic temperatures,and nanoscale blend morphologies are achieved.Since the blends are prepared as solid powders,they must be conse-quently processed in the melt for concrete manufacture.Mechanochemistry of this process makes it possible to obtain block or graft copolymers acting as com-patibilizers.In spite of these advantageous results,this procedure has not been used so far in industrial practice because of large energy consumption.Solution blending is frequently used for preparation of polymer blends on a laboratory scale.The blend components are dissolved in a common solvent and intensively stirred.The blend is separated by precipitation or evaporation of the10POL YMER BLENDSsolvent.The phase structure formed in the process is a function of blend compo-sition,interaction parameters of the blend components,type of the solvent,and history of its separation.Advantages of the process are rapid mixing of the system without large energy consumption and the potential to avoid unfavorable chem-ical reactions.On the other hand,the method is limited by the necessity tofind a common solvent for the blend components,and in particular,to remove huge amounts of organic(frequently toxic)solvent.Therefore,in industry,the method is used only for preparation of thin membranes,surface layers,and paints.A blend with heterogeneities on the order of10µm can be prepared by mixing of latexes without using organic solvents or large energy consumption.Significant energy is needed only for removing water and eventually achievement offiner dispersion by melt mixing.The whole energetic balance of the process is usually better than that for melt mixing.The necessity to have all components in latex form limits the use of the process.Because this is not the case for most synthetic polymers,the application of the process in industrial practice is limited.In partial block or graft copolymerization,homopolymers are the primary product.But,an amount of a copolymer sufficient for achieving good adhesion between immiscible phases is formed(59).In most cases,materials with better properties are prepared by this procedure than those formed by pure melt mix-ing of the corresponding homopolymers.The disadvantage of this process is the complicated and expensive startup of the production in comparison with other methods,eg,melt mixing.Another procedure for synthesis of polymer blends is by formation of in-terpenetrating polymer networks.A network of one polymer is swollen with the other monomer or prepolymer;after that,the monomer or prepolymer is crosslinked(63).In contrast to the preceding methods used for thermoplastics and uncrosslinked elastomers,blends of reactoplastics are prepared by this method.Phase Structure Development in Molten State.Starting Period of Melt Mixing.Most polymer blends are prepared by melt mixing and processed in the molten state.Therefore,the phase structure of a blend is formed during meltflow and is petrified by solidification.Formation of the phase structure at the initial stage of the mixing was intensively studied by Macosko’s group(64–68).It was found that sheets of minor phase are formed after the start of mixing.Quite rapidly,holes are formed in these sheets that coalesce.Further,the sheets transform tofibers or co-continuous structures,which can pass(depending on blend composition and properties of the components)to a dispersed structure (see Figs.4a–4e).If the softening or melting transition temperature of the minor phase is lower than that of the major phase,switching of phase continuity occurs at this stage of mixing(67).It was found that the reduction of characteristic size of phase domains from millimeters(characteristic size of polymer pellets)to micrometers is rapid.This reduction has been achieved during thefirst2min in batch mixers and in thefirst mixing zones in extruders.T ype of Phase Structure.For application of polymer blends,type andfine-ness of their phase structure are important.In blends of immiscible polymers1 and2with low content of2,particles of component2are dispersed in the matrix of component1.With rising fraction of2,partially continuous structure of2appears. With further increase in the amount of2,fully co-continuous structure is formed (see Fig.5).After that,phase inversion occurs,where2forms the matrix and1Fig.4.(a)Scheme of initial morphology development.(b)Holes and lace structure ob-served in ribbons at1.0min mixing.(c)Broken lace structure and small spherical particles at1.0min mixing.(d)Morphology of the dispersed phase particles at1.5min mixing.(e) Morphology of the dispersed phase particles at7min.mixing.Reproduced with permission from Reference64.the dispersed phase(69,70).Dependencies of continuity indexes or percentages of continuity(the continuous fraction of a component,determined as a fraction of the component that can be dissolved with a selective solvent)on volume fraction of component2are schematically shown on Figure15.In contrast to low molecularweight emulsions,where phase inversion occurs in one point or in a very narrowposition range of co-continuous structure.Full line continuity index of phase 2,broken line continuity index of phase1.v cr1,v cr2,v f1a v f2are volume fractions of phase 1or2at which partial or full co-continuity of the related phase start.v PI designate phase inversion composition.Reproduced with permission from Reference69.interval of composition,co-continuous range for polymer blends is frequently quite wide.Phase inversion points calculated as the center of the interval with full co-continuity of both the components and of the interval between critical volume fractions,v cr1and v cr2for starting continuity of components1and2,need not be the same.The interval of volume fractions of the components in which the blend structure is co-continuous depends on rheological properties of the components, interfacial tension,and mixing conditions.There have been several attempts to formulate a rule for prediction of the phase inversion point from the knowledge of viscosity of the components(69,71–74).They qualitatively describe the experi-mentally verified tendency of a less viscous component to be continuous down to low volume fractions.However,all fail in quantitative evaluation of a substantial portion of experimental data(69).The proposed rules for prediction of the phase inversion from the knowledge of elastic properties of the components(75–77)con-tain unknown parameters or have limited validity.Utracki and Lyngaae-Jørgensen(78)proposed a theory based on the as-sumption that the critical volume fractions relate to the percolation thresholdsof droplets,and phase inversion appears at the composition at which the blend。
溶胶凝胶法制备二硫化钼干凝胶复合电极和电化学性能表征
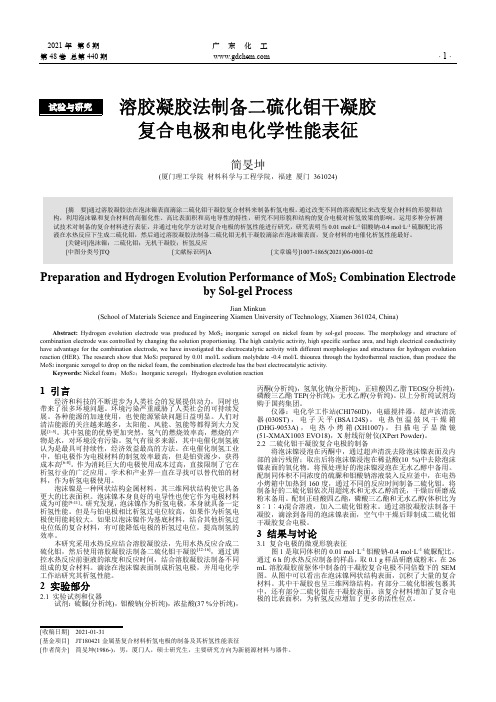
2021年第6期广东化工第48卷总第440期 · 1 ·溶胶凝胶法制备二硫化钼干凝胶复合电极和电化学性能表征简旻坤(厦门理工学院材料科学与工程学院,福建厦门361024)[摘要]通过溶胶凝胶法在泡沫镍表面滴涂二硫化钼干凝胶复合材料来制备析氢电极。
通过改变不同的溶液配比来改变复合材料的形貌和结构,利用泡沫镍和复合材料的高催化性、高比表面积和高电导性的特性,研究不同形貌和结构的复合电极对析氢效果的影响。
运用多种分析测试技术对制备的复合材料进行表征,并通过电化学方法对复合电极的析氢性能进行研究,研究表明当0.01 mol·L-1钼酸钠-0.4 mol·L-1硫脲配比溶液在水热反应下生成二硫化钼,然后通过溶胶凝胶法制备二硫化钼无机干凝胶滴涂在泡沫镍表面,复合材料的电催化析氢性能最好。
[关键词]泡沫镍;二硫化钼;无机干凝胶;析氢反应[中图分类号]TQ [文献标识码]A [文章编号]1007-1865(2021)06-0001-02Preparation and Hydrogen Evolution Performance of MoS2 Combination Electrodeby Sol-gel ProcessJian Minkun(School of Materials Science and Engineering Xiamen University of Technology, Xiamen 361024, China) Abstract:Hydrogen evolution electrode was produced by MoS2inorganic xerogel on nickel foam by sol-gel process. The morphology and structure of combination electrode was controlled by changing the solution proportioning. The high catalytic activity, high specific surface area, and high electrical conductivity have advantage for the combination electrode, we have investigated the electrocatalytic activity with different morphologies and structures for hydrogen evolution reaction (HER). The research show that MoS2 prepared by 0.01 mol/L sodium molybdate -0.4 mol/L thiourea through the hydrothermal reaction, than produce the MoS2 inorganic xerogel to drop on the nickel foam, the combination electrode has the best electrocatalytic activity.Keywords: Nickel foam;MoS2;Inorganic xerogel;Hydrogen evolution reaction1 引言经济和科技的不断进步为人类社会的发展提供动力,同时也带来了很多环境问题。
- 1、下载文档前请自行甄别文档内容的完整性,平台不提供额外的编辑、内容补充、找答案等附加服务。
- 2、"仅部分预览"的文档,不可在线预览部分如存在完整性等问题,可反馈申请退款(可完整预览的文档不适用该条件!)。
- 3、如文档侵犯您的权益,请联系客服反馈,我们会尽快为您处理(人工客服工作时间:9:00-18:30)。
Figure 7.1 In immiscible blends the onset of phase cocontinuity coincides with the percolation threshold [<f>c = 0.156 and 0.019, respectively, for shear (3D) and extension, (ID)]; experimentally, fac = 0.19 ± 0.09 (Lyngaae-J0rgensen and Utracki, 1991).
Phase inversion concentration versus viscosity ratio. Literature data (Utracki, 1991c).
log
Figure 7.2 Experimental invesion concentration <fei versus viscosity ratio A dependence for mechanically prepared thermoplastics blends. The solid line represents Equation 7.1; the values: [T?] = 1.9 and (f>m = 0.84 were used (Utracki, 199Ic).
generation of anisometric structures, (3) shear coalescence, (4) interlayer slip and (5) encapsulation. These are discussed below (Utracki, 1995). A fundamental study of morphology development was published recently (Kozlowski, 1994,1995). Flow may also cause mechano-chemical degradation that generates reactive components, e.g., radicals, peroxides, acids, etc. frflns-esterification and ester-amide exchange reactions are well documented (their rates depend on the total interphasial area that in turn depends on flow). The reactions are responsible for generation of compatibilizers that tend to increase the interphasial area, may affect the phase equilibrium and the regularity of the main chain, and thus the extent of dispersion and blend crystallinity. The miscibility of polymer blends is another area of industrial importance. There is also evidence that during processing, the imposed hydrostatic and shear stresses can change the lower critical solubility temperature (LCST) by at least 600C. This may result in formation (inside the processing unit) of a singlephase polymer blend that, emerging into a low pressure and stress domain, decomposes by the spinodal decomposition mechanism into two-phase blends having a cocontinuous morphology whose degree of dispersion can be controlled by quenching (Inoue, 1993). It should be stressed that the relationship between morphology and flow behavior is reciprocal - flow affects the structure, but variation in the structure engenders changes in the rheological response of the blend. Plochocki (1978,1982,1983) defined the particular rheological composition (PRC) most frequently reported for polyalkene blends. At PRC, the TJ = rj((/)) function reaches a local maximum or iiunimum. The existence of the maximum is related to a change of the dispersed phase, either from spherical to fibrillar, or passes through the phase cocontinuity (phase inversion concentration), whereas that of the minimum is related to a reciprocal change and/ or to variation of the specific volume. 7.2.1 Flow-induced dispersion
7
Morphology
7.1 EQUILIBRIUM MORPHOLOGY AND PHASE INVERSION Before discussing the performance of polymer blends, it is important to review the basic elements of blend morphology. When concentration of the dispersed phase is increased, the morphology changes from dispersion of nearly spherical drops to progressively interconnected drops, then rods, fibers and sheets. At the phase inversion concentration, <fr, the distinction between the disperse and matrix phases vanishes - the morphology becomes cocontinuous. It is important to recognize that the phase cocontinuity is one of many aspects of blend morphology. Since the morphology is strongly affected by large strains' flow, it is natural to expected that the method of specimen preparation influences the cocontinuity. Both the phase inversion concentration and the stability of the cocontinuous phase structure depend on the strain and thermal history. For a three-dimensional (3D) case, percolation theory predicts that 0perc = 0.156, while for ID </>perc = 0.019. In accord with this theory, the transition from drop dispersion to cocontinuous structures occurs at an average volume fraction, ^onset = 0.19 ± 0.09 (Lyngaae-J0rgensen and Utracki, 1991). In Figure 7.1, variation of phase cocontinuity in blends of high density polyethylene with polystyrene, HDPE/PS, is shown. The data (obtained by selective extraction of the matrix phase) indicate that the onset of phase cocontinuity occurred at <f)\c = 0.16 and 02c = 0.15 whereas fa = 0.64. The cocontinuity contributes to synergism of properties, e.g., advantageous combination of high modulus and high impact strength in commercial blends. Recently, assuming validity of an emulsion model, the following relation was derived (Utracki, 199Ic):