电镜
透射电镜的成像特点及应用
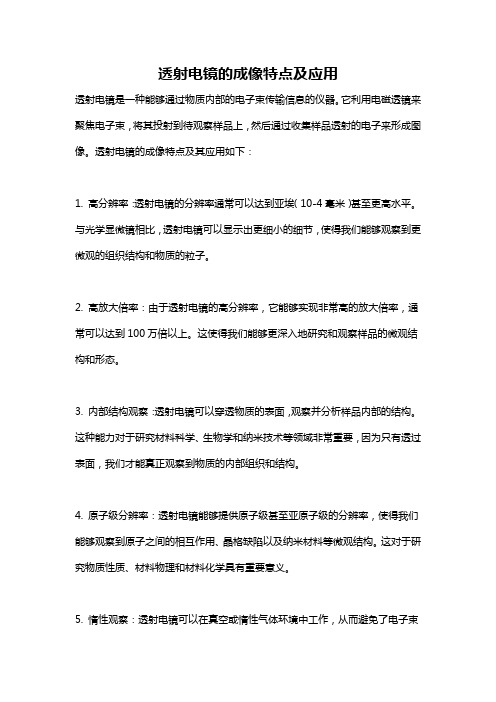
透射电镜的成像特点及应用透射电镜是一种能够通过物质内部的电子束传输信息的仪器。
它利用电磁透镜来聚焦电子束,将其投射到待观察样品上,然后通过收集样品透射的电子来形成图像。
透射电镜的成像特点及其应用如下:1. 高分辨率:透射电镜的分辨率通常可以达到亚埃(10-4毫米)甚至更高水平。
与光学显微镜相比,透射电镜可以显示出更细小的细节,使得我们能够观察到更微观的组织结构和物质的粒子。
2. 高放大倍率:由于透射电镜的高分辨率,它能够实现非常高的放大倍率,通常可以达到100万倍以上。
这使得我们能够更深入地研究和观察样品的微观结构和形态。
3. 内部结构观察:透射电镜可以穿透物质的表面,观察并分析样品内部的结构。
这种能力对于研究材料科学、生物学和纳米技术等领域非常重要,因为只有透过表面,我们才能真正观察到物质的内部组织和结构。
4. 原子级分辨率:透射电镜能够提供原子级甚至亚原子级的分辨率,使得我们能够观察到原子之间的相互作用、晶格缺陷以及纳米材料等微观结构。
这对于研究物质性质、材料物理和材料化学具有重要意义。
5. 惰性观察:透射电镜可以在真空或惰性气体环境中工作,从而避免了电子束与空气中的气体分子发生相互作用,保持样品的原始性质。
这对于观察和研究空气中不稳定的物质或易受氧化的物质非常重要。
透射电镜的应用范围非常广泛,以下是一些典型的应用领域:1. 材料科学:透射电镜可以观察和研究材料的晶体结构、相互作用和缺陷等特性。
它在材料科学领域的应用包括纳米材料研究、金属合金的结构分析、材料的电子结构分析等。
2. 生物学:透射电镜在生物学研究中广泛用于观察和分析生物细胞、组织和病毒等的结构和形态。
它可以帮助我们研究细胞的超微结构、蛋白质的空间结构、细胞分裂过程等。
3. 纳米技术:透射电镜对于纳米技术的研究和应用至关重要。
它可以观察和研究纳米材料的结构、性质和相互作用,从而帮助我们设计和制造具有特殊性能的纳米材料和纳米器件。
4. 矿物学和地球科学:透射电镜在矿物学和地球科学中有着广泛的应用。
透射电镜的工作原理
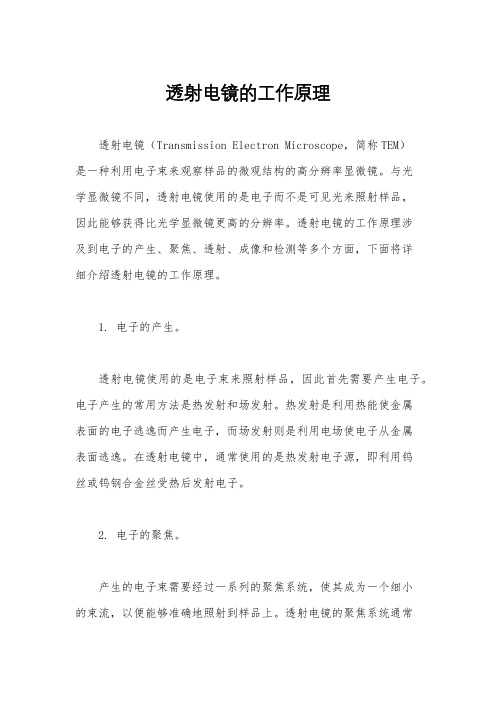
透射电镜的工作原理透射电镜(Transmission Electron Microscope,简称TEM)是一种利用电子束来观察样品的微观结构的高分辨率显微镜。
与光学显微镜不同,透射电镜使用的是电子而不是可见光来照射样品,因此能够获得比光学显微镜更高的分辨率。
透射电镜的工作原理涉及到电子的产生、聚焦、透射、成像和检测等多个方面,下面将详细介绍透射电镜的工作原理。
1. 电子的产生。
透射电镜使用的是电子束来照射样品,因此首先需要产生电子。
电子产生的常用方法是热发射和场发射。
热发射是利用热能使金属表面的电子逃逸而产生电子,而场发射则是利用电场使电子从金属表面逃逸。
在透射电镜中,通常使用的是热发射电子源,即利用钨丝或钨钢合金丝受热后发射电子。
2. 电子的聚焦。
产生的电子束需要经过一系列的聚焦系统,使其成为一个细小的束流,以便能够准确地照射到样品上。
透射电镜的聚焦系统通常包括电子透镜和磁透镜。
电子透镜利用电场来聚焦电子束,而磁透镜则利用磁场来聚焦电子束。
通过合理设计和调节,可以使电子束聚焦到非常小的尺寸,从而获得高分辨率的成像能力。
3. 电子的透射。
经过聚焦系统聚焦后的电子束将照射到样品上,这时的电子束被称为透射电子束。
透射电子束穿过样品时,会与样品中的原子和分子发生相互作用,产生散射和吸收。
透射电镜通过检测透射电子束的变化来获取样品的结构信息。
4. 成像。
透射电镜的成像原理是利用透射电子束与样品相互作用后产生的信号来获取样品的结构信息。
透射电镜通常采用透射电子显微镜来观察样品。
透射电子显微镜通过探测透射电子束的强度和位置来获得样品的结构信息,然后将这些信息转换成图像显示出来。
5. 检测。
透射电镜的检测系统通常包括电子探测器和图像处理系统。
电子探测器用于探测透射电子束的强度和位置,然后将这些信息传输给图像处理系统。
图像处理系统将探测到的信息转换成图像,并进行增强和处理,最终显示在显示屏上供用户观察。
总结来说,透射电镜的工作原理涉及到电子的产生、聚焦、透射、成像和检测等多个方面。
透射电镜的基本原理

透射电镜的基本原理透射电镜(Transmission Electron Microscope,TEM)是一种使用电子束而非光线进行成像的仪器。
它使用高能电子束将样品穿透,然后收集透射的电子,并通过电子透射图像来获得样品的高分辨率图像。
以下是透射电镜的基本原理。
1.电子源:透射电镜中的电子通常是通过热发射或场发射从钨丝或钨尖中提取出来的。
电子源通常位于电镜的顶部,并通过加热或外加电场使电子发射。
2.加速器和减速器:电子源中产生的电子通过一个加速器进行加速,以达到高能水平。
这样可以使电子具有足够的能量穿透样品。
在穿过样品后,电子被进一步减速,以改变电子束的相对能量。
3.样品:样品通常是非晶态或晶态材料,厚度通常在几纳米到几十纳米之间。
样品先被制备成极薄切片,并被放置在透明的钢网上,并通过透射底座固定在电镜中。
4.磁透镜系统:磁透镜系统用于聚焦和定向电子束。
它可以通过控制磁铁中的磁场来控制电子束的聚焦和导向。
电镜通常包含一个物镜透镜和一个对焦透镜。
物镜透镜具有更大的聚焦能力,用于将电子束聚焦到样品上,而对焦透镜用于微调焦距。
5.透射:电子束穿过样品时会与样品中的原子和电子发生相互作用。
其中一个主要的相互作用是电子与样品中的原子核和电子发生库仑散射。
这些相互作用会使电子的能量损失,并改变电子的路径。
透射电子图像是根据这些散射事件的位置和能量损失来重建的。
6.探测器:透射电子通过样品后,会被收集并转换为可视图像。
光学系统使用透射电子图像来放大和重构样品。
最常用的探测器是闪烁屏幕和摄像机。
闪烁屏幕会发出光,而摄像机则将光转换为电信号,并将其转化为可视化的图像。
7.后处理:获得的透射电子图像可以通过计算机后处理进行增强和处理。
这些处理包括调整对比度,增强细节以及从二维图像中提取出三维信息。
透射电镜的原理允许它在纳米尺度下观察物质的结构和形貌。
与传统的光学显微镜相比,透射电镜具有更高的分辨率和更大的深度解析力。
扫描电镜工作原理
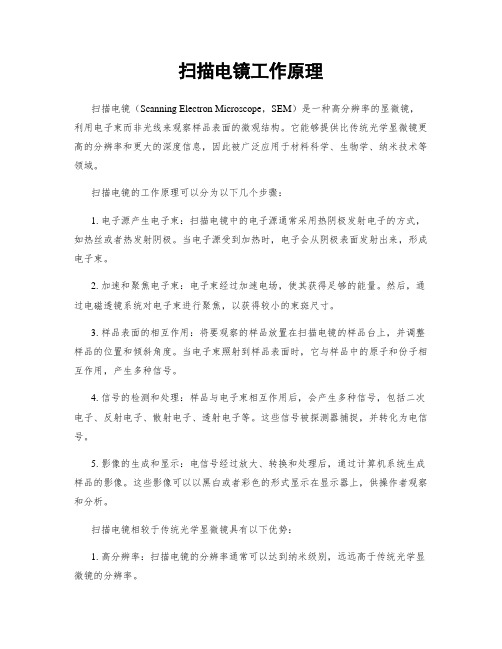
扫描电镜工作原理扫描电镜(Scanning Electron Microscope,SEM)是一种高分辨率的显微镜,利用电子束而非光线来观察样品表面的微观结构。
它能够提供比传统光学显微镜更高的分辨率和更大的深度信息,因此被广泛应用于材料科学、生物学、纳米技术等领域。
扫描电镜的工作原理可以分为以下几个步骤:1. 电子源产生电子束:扫描电镜中的电子源通常采用热阴极发射电子的方式,如热丝或者热发射阴极。
当电子源受到加热时,电子会从阴极表面发射出来,形成电子束。
2. 加速和聚焦电子束:电子束经过加速电场,使其获得足够的能量。
然后,通过电磁透镜系统对电子束进行聚焦,以获得较小的束斑尺寸。
3. 样品表面的相互作用:将要观察的样品放置在扫描电镜的样品台上,并调整样品的位置和倾斜角度。
当电子束照射到样品表面时,它与样品中的原子和份子相互作用,产生多种信号。
4. 信号的检测和处理:样品与电子束相互作用后,会产生多种信号,包括二次电子、反射电子、散射电子、透射电子等。
这些信号被探测器捕捉,并转化为电信号。
5. 影像的生成和显示:电信号经过放大、转换和处理后,通过计算机系统生成样品的影像。
这些影像可以以黑白或者彩色的形式显示在显示器上,供操作者观察和分析。
扫描电镜相较于传统光学显微镜具有以下优势:1. 高分辨率:扫描电镜的分辨率通常可以达到纳米级别,远远高于传统光学显微镜的分辨率。
2. 大深度信息:扫描电镜可以提供样品表面的三维形貌信息,使观察者能够更全面地了解样品的结构。
3. 高放大倍数:扫描电镜可以实现高倍数的放大,使细微结构和纳米级粒子能够清晰可见。
4. 可观察多种样品:扫描电镜适合于观察各种不同性质的样品,包括金属、陶瓷、生物组织、纤维材料等。
5. 光学显微镜无法观察的细节:扫描电镜能够观察到光学显微镜无法分辨的细节,如纳米级的表面形貌、弱小的缺陷和晶体结构等。
然而,扫描电镜也存在一些限制和挑战:1. 样品制备要求高:扫描电镜对样品的制备要求较高,需要进行表面处理、金属涂覆或者冷冻等步骤,以确保样品的导电性和稳定性。
电镜结构及成像范文

电镜结构及成像范文电子显微镜(Electron Microscope,简称EM)是一种利用电子束代替光束进行成像的显微技术。
相比传统光学显微镜,电子显微镜具有更高的分辨率和放大倍数,能够观察到更微小的结构。
它广泛应用于物理学、生物学、材料科学等领域。
电子显微镜由三个主要部分组成:光学部分、电子源和检测器。
首先,光学部分主要包括电子束射出器、透镜系统和投影透镜。
电子束射出器是产生电子束的部分,通常使用热阴极发射电子。
透镜系统由一系列电磁透镜组成,用于聚焦电子束并控制其聚焦程度。
投影透镜用于调整样品到成像平面的投影比例。
电子源是电子显微镜的关键部分,通常有两种类型:热发射电子源和场发射电子源。
热发射电子源通过加热金属阴极产生电子束,运行稳定可靠;场发射电子源则是通过强电场作用,使电子轻易地从阴极表面激发出。
检测器是用于接收电子束与样品相互作用后产生的信号的部分。
常见的检测器有底片或荧光屏。
底片是一种吸收电子束能量并转化成可见像的材料,荧光屏则是一种能够发射荧光的材料,通过观察荧光图案得到样品的成像。
在电镜成像过程中,首先电子束从电子源射出,然后经过透镜系统进行聚焦。
接下来,电子束通过样品,经过与样品相互作用后,会出射出不同类型的信号。
这些信号通常包括二次电子、透射电子、荧光和散射电子。
二次电子是从样品表面反射出的电子,能够提供样品形貌信息,信号强度与样品表面的形貌特征有关。
透射电子是穿透样品的电子,通过透射电子可以观察到样品内部的细微结构。
荧光是指样品吸收电子束能量后发射的可见光或荧光,通常用于观察含有荧光标记的样品。
散射电子是与样品原子和电子相互作用后发射出的电子,可以提供信息,例如化学成分和晶体结构等。
最后,这些信号由检测器接收并转化为电信号,并通过信号处理系统进行处理和放大。
处理后的信号通过显示器或相机显示出来,形成样品的显微图像。
电子显微镜因其高分辨率和放大倍数,成为研究微观世界的重要工具。
扫描电镜sem
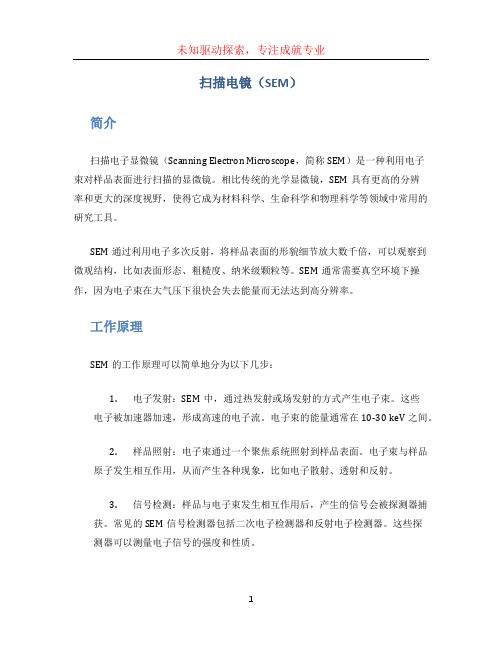
扫描电镜(SEM)简介扫描电子显微镜(Scanning Electron Microscope,简称SEM)是一种利用电子束对样品表面进行扫描的显微镜。
相比传统的光学显微镜,SEM具有更高的分辨率和更大的深度视野,使得它成为材料科学、生命科学和物理科学等领域中常用的研究工具。
SEM通过利用电子多次反射,将样品表面的形貌细节放大数千倍,可以观察到微观结构,比如表面形态、粗糙度、纳米级颗粒等。
SEM通常需要真空环境下操作,因为电子束在大气压下很快会失去能量而无法达到高分辨率。
工作原理SEM的工作原理可以简单地分为以下几步:1.电子发射:SEM中,通过热发射或场发射的方式产生电子束。
这些电子被加速器加速,形成高速的电子流。
电子束的能量通常在10-30 keV之间。
2.样品照射:电子束通过一个聚焦系统照射到样品表面。
电子束与样品原子发生相互作用,从而产生各种现象,比如电子散射、透射和反射。
3.信号检测:样品与电子束发生相互作用后,产生的信号会被探测器捕获。
常见的SEM信号检测器包括二次电子检测器和反射电子检测器。
这些探测器可以测量电子信号的强度和性质。
4.信号处理和图像生成:SEM通过对探测到的信号进行处理和放大,生成图像。
这些图像可以显示出样品表面的微观结构和形貌。
应用领域SEM在许多科学领域中都有广泛的应用。
以下是一些常见的应用领域:材料科学SEM可以用于研究材料的结构和形态。
它可以观察微观缺陷、晶体结构、纳米颗粒等材料细节。
这对于材料工程师来说非常重要,可以帮助他们改进材料的性能和开发新的材料。
生命科学SEM可以用于观察生物样品的微观结构。
比如,它可以观察细胞的形态、细胞器的分布和细胞表面的纹理。
这对于生物学家来说非常重要,可以帮助他们了解生物体的结构和功能。
纳米科学SEM在纳米科学领域中也有广泛的应用。
通过SEM可以对纳米材料进行表面形貌和结构的观察。
它可以显示出纳米结构的细节,帮助科学家研究纳米颗粒的组装、层析和相互作用等现象。
透射电镜的原理

透射电镜的原理
透射电镜是一种常用的电子显微镜技术,用于观察和研究物质的微观结构。
其原理基于电子的波粒二象性和物质对电子的散射效应。
透射电镜的工作原理可以概括为以下几个步骤:
1. 电子源:透射电镜使用的电子源一般为热阴极或冷阴极。
电子发射后,通过加速电压和电子透镜系统,使电子获得足够的能量和聚焦程度。
2. 样品:待观察的样品被制备成非晶态或薄片状,并放置在样品台上。
样品的厚度通常在纳米到亚微米级别,以保证电子的穿透性。
3. 散射:通过透射电镜的电子束,电子与样品内的原子或分子发生相互作用。
根据样品的组成和结构,电子会被散射并改变方向。
4. 对比度增强:经过样品后,电子束进入投影镜筒。
在此过程中,通过调节投影镜筒中的电子透镜,可以调整电子束的聚焦度和强度。
5. 形成显影:电子束通过样品后,穿过投影镜筒的屏幕或探测器。
探测器接收到散射电子并转化为电子信号,经过放大和处理后,形成最终的图像。
透射电镜的原理是基于电子的波性和散射现象,利用电子的穿透性观察物质的微观结构。
通过控制电子束的聚焦度和强度,结合样品的散射特性,透射电镜可以提供高分辨率和高对比度的图像,用于研究各种材料的微观结构和性质。
电镜使用方法说明书
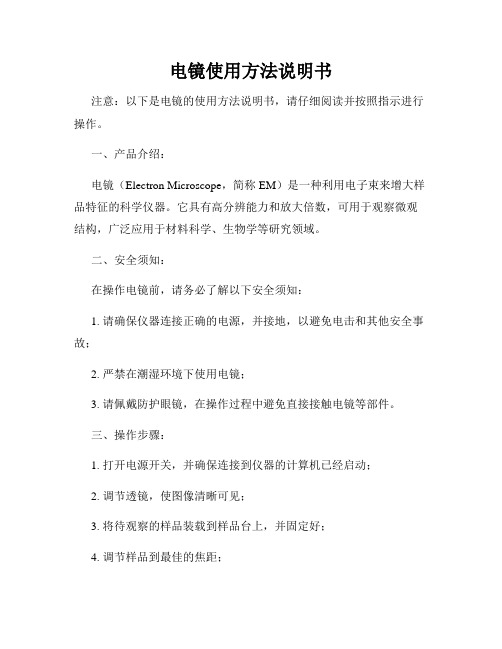
电镜使用方法说明书注意:以下是电镜的使用方法说明书,请仔细阅读并按照指示进行操作。
一、产品介绍:电镜(Electron Microscope,简称EM)是一种利用电子束来增大样品特征的科学仪器。
它具有高分辨能力和放大倍数,可用于观察微观结构,广泛应用于材料科学、生物学等研究领域。
二、安全须知:在操作电镜前,请务必了解以下安全须知:1. 请确保仪器连接正确的电源,并接地,以避免电击和其他安全事故;2. 严禁在潮湿环境下使用电镜;3. 请佩戴防护眼镜,在操作过程中避免直接接触电镜等部件。
三、操作步骤:1. 打开电源开关,并确保连接到仪器的计算机已经启动;2. 调节透镜,使图像清晰可见;3. 将待观察的样品装载到样品台上,并固定好;4. 调节样品到最佳的焦距;5. 使用电镜软件进行图像采集和处理,可以根据需要更换不同的放大倍数;6. 观察完毕后,将样品从样品台上取下,并关闭电镜和计算机。
四、常见问题与解决方法:1. 图像模糊:请检查透镜是否调节到最佳焦距,或者更换更高品质的样品;2. 电源无法启动:请检查电源是否连接正常,并确保电源开关处于打开状态;3. 电脑无法识别电镜设备:请检查连接电脑的USB线缆是否插紧,并重启计算机。
五、维护与保养:1. 在使用完电镜后,切记关闭电源开关,并将电镜与计算机断开连接;2. 定期清理电镜表面的灰尘和污渍,可以使用干净的软布擦拭,避免使用化学溶剂;3. 若电镜出现故障,请及时联系专业人员进行维修。
六、附录:本使用方法说明书仅适用于常规电子显微镜的操作,若使用其他型号或有特殊要求,请参考相应的使用手册。
感谢您使用本电镜,希望本说明书能够帮助您顺利操作电镜,获取到准确的观察结果。
如有任何疑问或需要进一步帮助,请随时联系我们的客服。
祝您工作顺利!。
- 1、下载文档前请自行甄别文档内容的完整性,平台不提供额外的编辑、内容补充、找答案等附加服务。
- 2、"仅部分预览"的文档,不可在线预览部分如存在完整性等问题,可反馈申请退款(可完整预览的文档不适用该条件!)。
- 3、如文档侵犯您的权益,请联系客服反馈,我们会尽快为您处理(人工客服工作时间:9:00-18:30)。
Journal of Alloys and Compounds 494 (2010) 340–346Contents lists available at ScienceDirectJournal of Alloys andCompoundsj o u r n a l h o m e p a g e :w w w.e l s e v i e r.c o m /l o c a t e /j a l l c omInfluence of thermal treatment on catalytic performance of Pd/(Ce,Zr)O x –Al 2O 3three-way catalystsBo Zhao a ,b ,Chunqing Yang a ,Qiuyan Wang a ,Guangfeng Li a ,Renxian Zhou a ,∗a Institute of Catalysis,Zhejiang University,Hangzhou 310028,PR ChinabSchool of Pharmaceutical and Chemical Engineering,Taizhou University,Taizhou 317000,PR Chinaa r t i c l e i n f o Article history:Received 25August 2009Received in revised form 7January 2010Accepted 9January 2010Available online 18 January 2010Keywords:Sol–gelSupercritical drying Three-way catalysts CZA mixed oxidesa b s t r a c tCeO 2–ZrO 2–Al 2O 3(CZA)mixed oxides were synthesized using sol–gel and supercritical drying methods,and their physicochemical properties were characterized by BET surface area (BET),X-ray diffraction (XRD),H 2-temperature-programmed reduction (H 2-TPR)and O 2-temperature-programmed desorption (O 2-TPD)techniques.The catalytic performances of Pd/CZA catalysts with different thermal treatment were also investigated.The results indicate that catalytic activities are affected by thermal treatment of support or catalyst and Pd/CZA catalysts exhibit good thermal stability.H 2-TPR results show that the effect of thermal treatment on the dispersion state of PdO is different between catalyst and support after calcination.However,O 2-TPD results show that the influence of thermal treatment on the desorption performance of oxygen is similar in both cases.Desorption of surface oxygen is closely related to surface area of the support.During the calcination of the supports or the catalysts at high temperature,the surface oxygen desorption capacity and the mobility of lattice oxygen decrease due to the sintering of supports,which is harmful to the dispersion of active species,corresponding to the decrease of three-way catalytic activities.Crown Copyright © 2010 Published by Elsevier B.V. All rights reserved.1.IntroductionThree-way catalysts (TWCs)are today’s most successful exhaust after-treatment system for gasoline engines.With a warmed up catalyst and at steady-state conditions conversions of more than 95%are reached for the three pollutants CO,NO and HC [1].In recent years,typical TWC formulations have included Pd as the active metal,fluorite-type oxides,such as ceria–zirconia,as pro-moters and alumina as support as well as other minor components mainly present in order to enhance thermal stability [2–4].In mod-ern TWC formulations,the promotion by ceria has been extended to other structurally related oxide systems in order to increase or maintain the durability of the TWC while enhancing the oxygen-storage capacity (OSC)properties of the catalyst [5,6].In this sense,Ce–Zr mixed oxide systems have attracted much attention as they provide greater OSC after thermal sintering,potentially increasing the useful lifetime of the catalytic system [7–9].Concerning the active metal,the use of Pd as the only active metal component in TWC has received considerable attention [5,10].Part of this interest has been purely economic,resulting from the high cost and scarcity of Rh.On the other hand,recently,Pd has been widely used in TWC∗Corresponding author.Tel.:+8657188273290;fax:+8657188273283.E-mail address:zhourenxian@ (R.Zhou).for its good performance of HC oxidation and durability at high temperatures [11].Automotive emission standards are becoming increasingly stringent which requires continuous improvements in the exhaust after-treatment systems [12].Among them,achievement of lower light-off temperature during the cold-start phase is of the highest relevance,considering that more than 50%of the total emission is produced during that period [13].Most studies available in the literature have concentrated on improving the light-off behavior [14]and it is necessary to place the TWC closer to the engine in order to obtain its light-off activity immediately after the start up of the engine.Therefore,the catalyst must be able to have better thermal stability [15].Thus,the development of new-generation TWC requires that the oxygen-storage component exhibits better thermal stability and higher OSC.However,for the CeO 2–ZrO 2(CZ)compounds,the thermal stability of texture is not good enough,for example,after calcinations at 1273K,the specific surface area is lower than 10m 2g −1,which cannot meet the requirement of TWC [16].The “diffusion barrier concept”was presented through intro-ducing Al 2O 3into CeO 2–ZrO 2solid solution on a nanometer scale by Morikawa et al.[17].Recently,the effects of Al 2O 3addition on the thermal stability and reduction behavior of mixed oxides have also been reported in literatures [13,16].The CeO 2–ZrO 2–Al 2O 3(CZA)materials are hopeful to simultaneously maintain high-surface area of Al 2O 3and good OSC of CZ oxygen-storage materials [18].Fur-thermore,the catalyst containing CZA could significantly reduce0925-8388/$–see front matter.Crown Copyright © 2010 Published by Elsevier B.V. All rights reserved.doi:10.1016/j.jallcom.2010.01.031B.Zhao et al./Journal of Alloys and Compounds494 (2010) 340–346341the NO x emission[19].So investigation of CZA mixed oxide is significant to enhance performance of TWC.Moreover,these mate-rials would eventually help to decrease the cold-start emissions mainly by permitting the catalyst to be located closer to the engine [20–23].The chemical and structural characteristics of CZA mainly depend on the preparation method.The main preparation methods include sol–gel[24],coprecipitation[12]and impregnation[25,26]. However,further research should be done to improve the thermal stability of CZA mixed oxide.Therefore,there is currently a great deal of interest in prepar-ing CZA effectively.In this paper,high-surface area of CZA mixed oxides were synthesized using sol–gel and supercritical drying methods.TWC supported on CZA were prepared and the catalytic performances of0.5wt%Pd/CZA were also investigated.Reactant mixture simulated to the actual automotive exhaust was adopted to evaluate the catalytic performance of the catalysts.The redox properties of the materials were studied by means of temperature-programmed reduction(H2-TPR)and temperature-programmed desorption(O2-TPD)experiments.2.Experimental2.1.Catalyst preparationCZA mixed oxide was prepared by sol–gel methods combined with super-critical drying techniques.The solution of aqueous NH3was slowly dropped into quantitative mixed aqueous solutions of Ce(NO3)3,ZrO(NO3)2and Al(NO3)3under continuous stirring and the pH value was controlled to be9.5.The molar ratio of Ce:Zr was3:1and the content of CeO2–ZrO2in CZA was18wt%.After aging at room temperature for12h,the precipitate wasfiltered and washed with deionized water. Then the precipitate was dried under supercritical condition in alcohol(250◦C, 7.5MPa)for3h.Then the samples were calcined at500,800,900,1000and1100◦C, respectively,for4h in air.These as-prepared mixed oxides were denoted as CZA5, CZA8,CZA9,CZA10and CZA11,respectively.CZ-free alumina was also prepared by a similar procedure and was calcined at500or1100◦C for4h.The Pd-only three-way catalysts with different CZA mixed oxides as supports were prepared by incipient impregnation method with aqueous solutions of H2PdCl4 as metal precursors(Sinopharm Chemical Reagent Co.,Ltd.).Pd nominal loading was0.5wt%.The impregnated samples were reduced with hydrazine hydrate,and washed with a large amount of deionized water until no Cl−ions was detected in thefiltered solution.The catalysts were dried at110◦C for12h and then calcined at 500◦C for2h.These as-prepared fresh catalysts,denoted as Pd/CZA-5,were further calcined at800,900,1000and1100◦C,respectively,for4h in air.The obtained aged catalysts were then denoted as Pd/CZA-8,Pd/CZA-9,Pd/CZA-10and Pd/CZA-11.Pd/Al2O3catalysts were also prepared by a similar procedure and were calcined at500and1100◦C for2h,respectively.The obtained catalysts were denoted as Pd/Al2O3-5and Pd/Al2O3-11.2.2.Characterization techniques2.2.1.BET surface areaSpecific surface area of the samples was measured by N2adsorption using an OMNISORP100CX apparatus.Prior to adsorption measurements,samples were degassed at200◦C for2h under vacuum,and N2adsorption was carried out at the liquid nitrogen temperature.2.2.2.X-ray powder diffraction(XRD)The powder X-ray diffraction experiment was recorded on a Rigaku D/Max-IIIB diffractometer employing monochromatic Cu K␣radiation.The X-ray tube was operated at45kV and40mA.2.2.3.Transmission electron microscopy(TEM)The size of the metallic particles on the supported Pd catalysts was checked with transmission electron microscopy using a JEM-2010apparatus operated at200kV. For the TEM analysis,the samples were grounded in a mortar and then deposited on a Cu grid covered with a perforated carbon membrane.2.2.4.Temperature-programmed reduction(H2-TPR)Hydrogen temperature-programmed reduction(H2-TPR)experiments were car-ried out in aflowing system to observe the reducibility of the sample.Typically0.05g of sample was employed.The standard pretreatment consisted of heating the sam-ple in air from room temperature to300◦C,holding at that temperature for0.5h. After cooling to−20◦C in the same atmosphere,the sample was heated underflow-ing H2(5%in Ar,40ml min−1)at a rate of10◦C min−1.The outlet gases were analyzed on-line by a gas chromatograph(GC,KX100)with a thermal conductivity detector (TCD),and the effluent H2O formed during H2-TPR was adsorbed with a5A molec-ular sieve,the latter not influencing the transient response of the TCD.Based on the amount of H2consumption observed over a standard CuO sample in similar TPR procedures,the amount of H2consumption for the samples were obtained.2.2.5.Temperature-programmed desorption(O2-TPD)Temperature-programmed desorption(O2-TPD)experiments were employed to investigate the O2desorption with temperature.The sample(0.10g)wasfirst pretreated inflowing O2(5%in He)at300◦C for1h in a quartzfixed-bed micro-reactor.After cooling to room temperature in the same atmosphere,the sample was purged inflowing He(40ml min−1)for30min.After that,the sample was heated at a rate of20◦C min−1to1000◦C.The outlet gases were analyzed on-line by a gas chromatograph(GC,KX100)with TCD.2.2.6.Catalytic testsThe three-way catalytic activity was evaluated in thefixed-bed reactor with the simulated exhaust gas containing CO(6800ppm),HC(C3H8,C3H6)(3300ppm),NO (1000ppm),NO2(300ppm),O2(1.75%)and Ar(balance)and theirflow rates were controlled by massflow controllers before entering the blender.The concentration of CO,NO,NO2and total HC(C3H6and C3H8)were analyzed by a Bruker EQ55FTIR spectrometer coupled with a multiple reflection transmission cell(Infrared Analysis Inc.).The space velocity was48,000h−1and0.2ml of catalysts(40–60mesh)were loaded in the reactor.The curves about the relationship between conversion and temperature were obtained.3.Results and discussionThe BET surface area of the CZ-free alumina calcined at500◦C is 300m2g−1.In contrast,the CZA support calcined at500◦C has large surface area and the BET value is362m2g−1.On the other hand,the CZA sample prepared by sol–gel and supercritical drying methods presents higher surface area in comparison with material obtained by microemulsion(about180m2g−1)method[27].Surface areas of CZA supports decrease obviously with increasing calcination tem-perature.The value of BET specific surface area is213m2g−1for CZA8,which is higher than that of CZA materials calcined at700◦C and prepared by coimpregnation(about120m2g−1)and sol–gel (about170m2g−1)methods[24].The values of BET specific sur-face area are133,121m2g−1for CZA9and CZA10,respectively. Moreover,the CZA11sample exhibits surface area of97m2g−1after calcination at1100◦C for4h,which is obviously higher than that of CZ-free alumina(35m2g−1)calcined at1100◦C.These results indicate that CZA mixed oxide prepared by sol–gel and supercritical drying methods shows higher heat resistance.Fig.1shows the XRD patterns of CZA mixed oxides calcined at different temperature.From Fig.1,it can be seen that the cubic and tetragonal phases of Ce x Zr1−x O2solid solutions are observed for all the samples and no pure CeO2diffraction peaks aredetected.Fig.1.XRD patterns of CZA pretreated at different temperature:(a)CZA5;(b)CZA8;(c)CZA9;(d)CZA10;(e)CZA11.342 B.Zhao et al./Journal of Alloys and Compounds494 (2010) 340–346Fig.2.TEM photographs of catalysts:(A)Pd/Al 2O 3-5;(B)Pd/Al 2O 3-11;(C)Pd/CZA-5;(D)Pd/CZA-11.The Ce x Zr 1−x O 2solid solutions show mainly the cubic phase due to high Ce content,which also occurs in CeO 2–ZrO 2/Al 2O 3speci-mens prepared by coimpregnation via organic precursors [24].The cell parameter of CZA5,CZA8,CZA9,CZA10and CZA11is 0.53601,0.53251,0.53103,0.53086and 0.53215nm,respectively,which is smaller than pure CZ and CeO 2(0.54nm)[27,28].It may be attribute to the fact that the ion radius of Al 3+(0.057nm)is smaller than that of Ce 4+(0.097nm)/Ce 3+(0.114nm)and Zr 4+(0.084nm).Incorpora-tion Al 3+into the CZ lattice by replacing of Ce 4+/Ce 3+or Zr 4+leads to the shrinkage of the lattice parameter.Moreover,with increasing the incorporation of Al 3+,the lattice parameter becomes smaller.Significant sharpening of the XRD patterns is normally observed with the increase of calcination temperature,which is due to the growth and sintering of the crystallites.Especially for the sample calcined at 1100◦C,the peaks of CZA solid solution become sharper and more intense,corresponding to an increase in the crystalline particle size and a decrease of the BET area of the supports.The major problem with CeO 2is the loss of OSC due to sintering of the particles and forming of CeAlO 3with ␥-Al 2O 3when the exhaust temperature exceeds 850◦C [29].However,in contrast with the results of Kozlov et al.[24]reported,no CeAlO 3diffraction peaks are detected during calcination of the mixed oxides at high tem-perature in our research.Moreover,it is interesting to note that ␥-Al 2O 3phase was transformed into ␦-Al 2O 3after CZA calcined at temperature higher than 800◦C.The results show that the pres-ence of ceria–zirconia mixed oxide inhibits the transformation of ␥-alumina into the low-surface-area ␣-phase,which is typical at this temperature [30].On the basis of these results a conclusion can be drawn that the interaction between CZ and Al 2O 3in the CZA mixed oxides is stronger,which is the main reason for big surface areas and high thermal stability of CZA mixed oxides.Fig.2shows TEM pictures of Pd/Al 2O 3and Pd/CZA catalysts calcined at 500and 1100◦C.For the catalysts calcined at 500◦C,PdO x particles exhibit well-dispersed state and shows small parti-cle size on the surface of supports.The average particle size of Pd on Pd/Al 2O 3-5and Pd/CZA-5is 6.0and 5.0nm,respectively.The micrograph shows that the CZA mixed oxides exhibit small sphere while free Al 2O 3exhibit filiform.The sintering of Pd particles and supports occurs obviously after calcined at 1100◦C for all catalysts.From Fig.2(B),it can be seen that for Pd/Al 2O 3-11catalyst seri-ous sintering and encapsulation phenomena of Pd particles occur due to significant agglomeration of support.On the opposite,for the Pd/CZA-11catalyst,PdO x particles still exhibit good dispersed state and no encapsulation phenomena exist.The average parti-cle size of Pd on Pd/Al 2O 3-11and Pd/CZA-11is 34.0and 19.5nm,respectively.That indicates that the addition of CZ would inhibit the sintering of PdO x particles in Pd/CZA catalyst and thus improve the thermal stability of the supported Pd catalyst because of the increased thermal stability of its support,which is in agreement with the BET and XRD results.Results obtained from the light-off tests under simulated exhaust gas over Pd/CZA catalysts are shown in Fig.3(catalyst was calcined at different temperature)and Fig.4(CZA support was calcined at different temperature).The light-off (T 50)and full-conversion (T 90)temperature of CO,HC,NO and NO 2over different Pd/CZA catalysts are shown in Table 1.T 50(corresponding to the temperature at which 50%conversion of a given compound is com-pleted)and T 90(corresponding to the temperature at which 90%conversion of a given compound is completed)are used to evalu-ate the activities of different catalysts.From Fig.3and Table 1we can see that the catalytic activities for both oxidation and reduction reactions decrease with the increasing of calcination temperature.B.Zhao et al./Journal of Alloys and Compounds494 (2010) 340–346343Fig.3.Three-way conversion as a function of reaction temperature over the Pd/CZA catalysts(catalysts calcined at different temperature).Fig.4.Three-way conversion as a function of reaction temperature over the Pd/CZA catalysts(supports calcined at different temperature).344 B.Zhao et al./Journal of Alloys and Compounds494 (2010) 340–346Table1Light-off(T50)and full-conversion(T90)temperature of CO,HC,NO and NO2over different Pd/CZA catalysts.Catalysts T50(◦C)T90(◦C)CO HC NO NO2CO HC NO NO2Pd/CZA-5171300352230191337358348 Pd/CZA-8174303354235200340363354 Pd/CZA-9182305357264204350364358 Pd/CZA-10191310360281219348368358 Pd/CZA-11205310359287218350368362 Pd/CZA5171300352230191337358348 Pd/CZA8178321363265202373368355 Pd/CZA9184326368274215383374372 Pd/CZA10195340373290222397378390 Pd/CZA11204350374305226411378399For CO conversion,the T50and T90increase more obviously com-pared with those of HC and NO.Moreover,the catalyst calcined at 1100◦C still present acceptable catalytic activity,which indicates that Pd/CZA catalysts exhibit better thermal stability.From Fig.4and Table1,it is worth pointing out that light-off activities of the catalysts are significantly affected by the calcina-tion temperature of the support.The catalytic activities decrease obviously with increasing calcination temperature of the supports. Compared with the catalyst supported on CZA calcined at500◦C, the T90for different reactants increases clearly in the range of 20–80◦C over the catalyst supported on CZA calcined at1100◦C. The data indicate that high temperature calcination of the support results in the decrease of catalytic activity due to sintering.Fur-thermore,the dispersion of active species is deteriorated with the decreasing of BET surface area of the support[31].Fig.5shows the H2-TPR profiles of the Pd/CZA catalysts calcined at different temperature.The H2consumption and peak tempera-ture maxima are listed in Table2.From Fig.5it can be seen that three positive peaks of hydrogen consumption at about40,70and 105◦C are found in all catalysts.These peaks are designated by␣,and␥.According to the previous work in our research group,we suggest that the peaks␣is ascribed to the reduction of the PdO dispersed on alumina-rich grains and the peakis ascribed to the reduction of the PdO species dispersed on Ce–Zr-rich grains[32]. For the peak␥,it is suggested that the stable PdO species are present on the Pd/CZA catalysts due to the strong interaction between PdO and ZrO2[33].The negative peak results from the decomposition of palladium hydride which is also seen in the reduction of bulk PdO [34].Palladium oxide is reduced to palladium metal on exposure to H2andthis metal absorbs hydrogen,forming the hydride phase, which decomposes near80◦C[35,36].In addition,from Table2 it can be seen that the peak␣shifts to higher temperature with increasing calcination temperature of the catalysts.On the other hand,H2consumption decreases.It is interesting to note that the trend of the peak␣with temperature increasing is similar to that of decreasing of their catalytic activities.This suggests that the cat-alytic activity may be related to the reducibility of␣-PdO species, and the higher the reducibility of the PdO species,the higher the catalytic activities.From Fig.5we can also see that for the catalyst Fig.5.TPR profiles of the catalysts calcined at different temperature:(A)Pd/CZA-5;(B)Pd/CZA-8;(C)Pd/CZA-9;(D)Pd/CZA-10;(E)Pd/CZA-11.calcined at1100◦C,the H2consumption of-PdO species increases obviously.But for the catalyst calcined below1100◦C,the changes for the H2consumption and reduction temperature of-PdO and ␥-PdO species are not obvious,indicating that strong interaction exists between PdO species and support.These results indicate that the essential change of dispersion state of surface PdO species can not be seen during calcination of the catalysts.Moreover,the Pd/CZA catalysts exhibit high heat resistance.H2-TPR profiles of the Pd/CZA catalysts with supports calcined at different temperature are shown in Fig.6.The influence of sup-ports calcination temperature on the reduction performance of the Pd/CZA catalysts is significant.Although all catalysts exhibit three peaks of hydrogen consumption and a negative peak of pal-ladium hydride decomposition,great changes have happened for the dispersion state of PdO species in Fig.6compared with those in Fig.5.In addition,it can be seen that the trend of the peak␣-PdO with temperature increasing and the decreasing amount of H2con-sumption is similar to that of their catalytic activities decreasing. From Fig.6,wefind that the peak temperature for-PdO slightly changes but the amount of H2consumption increases obviously.In particular,for the supports calcined at1000or1100◦C,their TPR profiles exhibit two peaks of hydrogen consumption at60–100◦C, which indicates that a new dispersion state of PdO species appears. From Fig.6we can also see that the decomposition peak of pal-ladium hydride obviously shifts to higher temperature and shows less intense negative peak with the increasing of calcination tem-perature of the supports.Decreased intensity of the hydride peak suggests that less Pd was reduced on initial exposure to H2for the catalyst with support calcined at higher temperature,and conse-quently less hydride was formed.This,along with the increasedTable2H2consumption and temperature of TPR peaks for the catalysts calcined at different temperature.Catalysts␣PeakPeak␥PeakH2consumption (mol/g cat)Peak temperature(◦C)H2consumption(mol/g cat)Peak temperature(◦C)H2consumption(mol/g cat)Peak temperature(◦C)Pd/CZA-559.1±0.582710.8±0.0945 5.6±0.3698 Pd/CZA-858.6±0.6146 1.1±0.676212.1±0.21103 Pd/CZA-956.7±0.57480.89±0.5862.514.8±0.37102 Pd/CZA-1053.2±0.2550 1.0±0.5562.514.9±0.35103 Pd/CZA-1151.9±0.4954 5.4±0.117015.4±0.35106B.Zhao et al./Journal of Alloys and Compounds494 (2010) 340–346345Fig.6.TPR profiles of the catalysts(supports calcined at different temperature):(A) CZA5;(B)CZA8;(C)CZA9;(D)CZA10;(E)CZA11.temperature of PdO reduction,is consistent with a stronger inter-action between the metal and the support for the catalyst calcined at higher temperature of its support[37,38].At the same time, the results further show that the dispersion state of active species changes during calcination of the support due to the sintering and the decreasing of the BET surface area of CZA.Fig.7shows the O2-TPD profiles of the Pd/CZA catalysts cal-cined at different temperature.The TPD profiles of all catalysts display four peaks of oxygen desorption at about150,415,675 and975◦C,respectively.The peaks at about150and415◦C are ascribed to desorption of surface oxygen species.The peak at about 675◦C is due to decomposition of PdO species and the peak at about 975◦C is attributed to desorption of support bulk lattice oxygen [39].It is well known that the introduction of ZrO2into CeO2cre-ates a certain amount of oxygen vacancies(V o)via the formation of[Ce3+–V o–Ce3+]clusters[40].Fig.7indicates that the support of Pd/CZA-5can release a lot of oxygen.This is possibly due to the oxygen mobility increases with an increasing of V o concentration in support[41].From Fig.7,we can also see that oxygen desorp-tion area decreases obviously with the increasing of calcination temperature of the catalyst,especially for the desorption peaks at150and415◦C.This suggests that desorption of surface oxygenisFig.7.O2-TPD profiles of the catalysts calcined at different temperature:(A) Pd/CZA-5;(B)Pd/CZA-8;(C)Pd/CZA-9;(D)Pd/CZA-10;(E)Pd/CZA-11.Fig.8.O2-TPD profiles of the catalysts(supports calcined at different temperature): (A)CZA5;(B)CZA8;(C)CZA9;(D)CZA10;(E)CZA11.closely related to the surface area of support.With the decreasing of support surface area,desorption of surface oxygen is deteriorated. Furthermore,with the particle size increasing during high temper-ature calcination of the catalysts,the interaction between PdO and supports is enhanced,which results in decreased decomposition of PdO species.O2-TPD profiles of the Pd/CZA catalysts with supports calcined at different temperature are shown in Fig.8.From Fig.8,it can bee seen that the peak areas of desorption at different temperature decrease obviously with the increasing of calcination temperature of CZA, which is similar to that of Fig.7.These results indicate that physic-ochemical properties of the supports,such as surface area,particle size,structure and stability play a key role in catalytic performance of catalysts.During calcination of the supports or the catalysts at high temperature,the surface oxygen desorption capacity and the mobility of lattice oxygen decrease due to supports sintering,which is harmful to the dispersion of active species,as a result,three-way catalytic activities decrease correspondingly.4.ConclusionsThe catalytic activities are affected by thermal treatment of sup-port or catalyst.Moreover,Pd/CZA catalysts in our research exhibit good thermal stability.H2-TPR results show that strong interaction exists between PdO species and the support.Moreover,different effect on the dispersion state of PdO can be seen between calci-nation of catalyst and support.The essential change of dispersion state of surface PdO species cannot be seen during calcination of the catalyst but significant influence can be seen on the samples with supports calcined at different temperature.The amount of H2consumption of the peak␣-PdO decreases obviously with the increasing of calcination temperature of the supports.But for the peak-PdO the trend is opposite.O2-TPD results indicate that the treatment temperature of catalysts or supports has almost the same effect on the desorption behavior of surface and bulk oxygen, depending mainly on the anti-sintering performance of supports. During the calcination of the supports or the catalysts at high tem-perature,the surface oxygen desorption capacity and the mobility of lattice oxygen decrease due to the sintering of supports,which is harmful to the dispersion of active species,corresponding to the decrease of three-way catalytic activities.AcknowledgementsWe gratefully acknowledge thefinancial supports from Nature Science Foundation of Zhejiang Province(No.Z504032)and the346 B.Zhao et al./Journal of Alloys and Compounds494 (2010) 340–346Ministry of Science and Technology of China(Nos.2006AA060306, 2009AA064804).References[1]R.Möller,M.Votsmeier,C.Onder,L.Guzzella,J.Gieshoff,Appl.Catal.B91(2009)30–38.[2]A.I.Juez,A.B.Hungría,A.Martínez-Arias,J.A.Anderson,M.Fernández-García,Catal.Today143(2009)195–202.[3]M.Ozawa,M.Hattori,T.Yamaguchi,J.Alloys Compd.451(2008)621–623.[4]M.W.Zhao,M.Q.Shen,X.M.Wen,J.Wang,J.Alloys Compd.457(2008)578–586.[5]A.Kubacka,A.Martínez-Arias,M.Fernández-García,M.A.Newton,Catal.Today145(2009)288–293.[6]L.P.R.Profeti,E.A.Ticianelli,E.M.Assaf,Int.J.Hydrogen Energy34(2009)5049–5060.[7]osiripojana,D.Chadwick,S.Assabumrungrat,Chem.Eng.J.138(2008)264–273.[8]I.Atribak,A.Bueno-López,A.García-García,J.Mol.Catal.A300(2009)103–110.[9]S.Damyanova,B.Pawelec,K.Arishtirova,M.V.M.Huerta,J.L.G.Fierro,Appl.Catal.A337(2008)86–96.[10]J.Q.Wang,M.Q.Shen,Y.An,J.Wang,mun.10(2008)103–107.[11]M.Zhao,S.H.Chen,X.Y.Zhang,M.C.Gong,Y.Q.Chen,J.Rare Earths27(2009)728–732.[12]C.C.Chuang,H.I.Hsiang,J.S.Hwang,T.S.Wang,J.Alloys Compd.470(2009)387–392.[13]A.Martínez-Arias,M.Fernández-García,A.B.Hungría,Catal.Today126(2007)90–95.[14]H.Santos,M.Costa,Chem.Eng.J.148(2009)173–183.[15]J.Kaˇs par,P.Fornasiero,M.Graziani,Catal.Today50(1999)285–298.[16]Z.L.Wei,H.M.Li,M.C.Gong,J.Alloys Compd.455(2008)322–326.[17]A.Morikawa,T.Suzuki,T.Kanazawa,K.kikuta,A.Suda,H.Shinio,Appl.Catal.B78(2008)210–221.[18]X.Y.Zhang,E.Y.Long,Y.L.Li,J.X.Guo,L.J.Zhang,M.C.Gong,M.H.Wang,Y.Q.Chen,J.Nat.Gas Chem.18(2009)139–144.[19]A.Iglesias-Juez,A.Martínez-Arias,M.Fernández-García,J.Catal.221(2004)148–161.[20]J.Wang,J.Wen,M.Q.Shen,J.Phys.Chem.C112(2008)5113–5122.[21]E.Rogemond,N.Essayem,R.Frety,V.Perrichon,M.Primet,F.Mathis,J.Catal.166(1997)229–235.[22]G.P.Osorio,S.F.Moyado,V.Petranovskii,A.Simakov,Catal.Lett.110(2006)53–60.[23]H.S.Gandhi,G.W.Graham,R.W.McCabe,J.Catal.216(2003)433–442.[24]A.I.Kozlov,D.H.Kim,A.Yezerets,P.Andersen,H.H.Kung,M.C.Kung,J.Catal.209(2002)417–426.[25]S.Suhonen,M.Valden,M.Hietikko,itinen,A.Savimäki,M.Härkönen,J.Appl.Catal.A218(2001)151–160.[26]M.H.Yao,R.J.Baird,F.W.Kunz,T.E.Hoost,J.Catal.166(1997)67–74.[27]M.Fernández-García,A.Martínez-Arias,A.Iglesias-Juez,C.Belver,A.B.Hungría,J.C.Conesa,J.Soria,J.Catal.194(2000)385–392.[28]E.Aneggi,M.Boaro,C.de Leitenburg,G.Dolcetti,A.Trovarelli,Catal.Today112(2006)94–98.[29]J.Z.Shyu,W.H.Weber,S.H.Gabdhi,J.Phys.Chem.92(1998)4964–4970.[30]B.H.Yue,R.X.Zhou,Y.J.Wang,X.M.Zheng,Appl.Catal.A295(2005)31–39.[31]A.Martínez-Arias,M.Fernández-García, A.B.Hungría, A.Iglesias-Juez,K.Duncan,R.Smith,J.A.Anderson,J.C.Conesa,J.Soria,J.Catal.204(2001) 238–248.[32]B.H.Yue,R.X.Zhou,Y.J.Wang,X.M.Zheng,Appl.Surf.Sci.252(2006)5820–5828.[33]K.Narui,K.Furuta,H.Yata,A.Nishida,Y.Kohtoku,T.Matsuzaki,Catal.Today45(1998)173–178.[34]H.W.Jen,G.W.Graham,W.Chun,R.W.McCabe,J.P.Cuif,S.E.Deutsch,O.Touret,Catal.Today50(1999)309–328.[35]A.B.Gaspar,L.C.Dieguez,Appl.Catal.A201(2000)241–251.[36]V.H.Sandoval,C.E.Gigola,Appl.Catal.A148(1996)81–96.[37]R.A.Daley,S.Y.Christou,A.M.Efstathiou,J.A.Anderson,Appl.Catal.B60(2005)117–127.[38]M.Q.Shen,M.Yang,J.Wang,J.Wen,M.W.Zhao,W.L.Wang,J.Phys.Chem.C113(2009)3212–3221.[39]R.X.Zhou,Y.J.Ding,X.Y.Jiang,X.M.Zheng,J.Chin.Mol.Catal.10(1996)226–230.[40]R.D.Monte,P.Fornasiero,M.Graziani,J.Kaˇs par,J Alloys Compd.275–277(1998)877–885.[41]H.He,H.X.Dai,K.W.Wong,C.T.Au,Appl.Catal.A251(2003)61–74.。