VDA6.3最新整理检查表
过程审核VDA6.3检查表

过程审核VDA6.3检查表P2-过程要素最低要求2.1是否建立项目管理及项目组织机构?具有项目管理流程。
详细规定跨职能项目组织机构,并定义联络窗口。
确定项目负责人及小组成员的职责和权限。
项目小组成员有资质来执行项目任务。
项目组织机构能满足顾客要求。
供方被纳入项目管理。
2.2是否为落实项目而规划了所有必要的资源,这些资源是否已经到位,并且体现了变更情况?资源规划应在项目合同的基础上考虑到顾客要求。
制定并落实项目成员规划。
必须考虑员工的工作负荷。
当发生变更(时间、开发规模,等等)时,对资源规划开展复核,必要时加以调整。
这既适用于由顾客发起的变更,也适用于内部变更以及由供方发起的变更。
在资源规划中,要特别留意关键路径。
针对人员和设备(例如测试和实验室设备等)方面必要的项目预算,进行了规划并审批通过。
项目组织机构(与顾客接口)的变更必须进行通报。
P2-过程要素最低要求2.3是否编制项目计划,并与顾客协调一致?项目计划满足顾客的具体要求。
所有内部里程碑以及顾客里程碑都被完整地纳入项目计划。
在项目计划中所定义的里程碑时刻开展评审,以确认所有计划的事项都得到实施,相对应的成熟度等级得到落实。
产品如有特殊的法规方面的认证/批准要求,那么该认证/批准程序要包括在项目策划中。
要确保内部对于项目计划变更的联络沟通。
对于影响到顾客的项目计划变更,要同顾客协商沟通并达成一致。
关键路径产生于项目计划,并顾及到关键的零件范围。
项目计划必须包括具体的项目质量事项。
可从项目计划生成出单独文件(质量管理计划)。
这些计划必须考虑原型件和试生产。
项目计划必须包括涉及采购的具体事项。
可从项目计划生成出单独的详细计划。
2.4是否进行项目质量策划,并对其符合性进行监控?项目质量策划满足顾客特定要求。
产品和过程保证的措施是项目质量策划的内容之一。
产品和过程的验证/确认要求要包含在策划事项中。
策划也考虑到关键零部件和关键供应方(内外部供方)。
定期监控策划的符合性和目标的达成情况。
最新VDA6.3过程审核检查表及评分标准
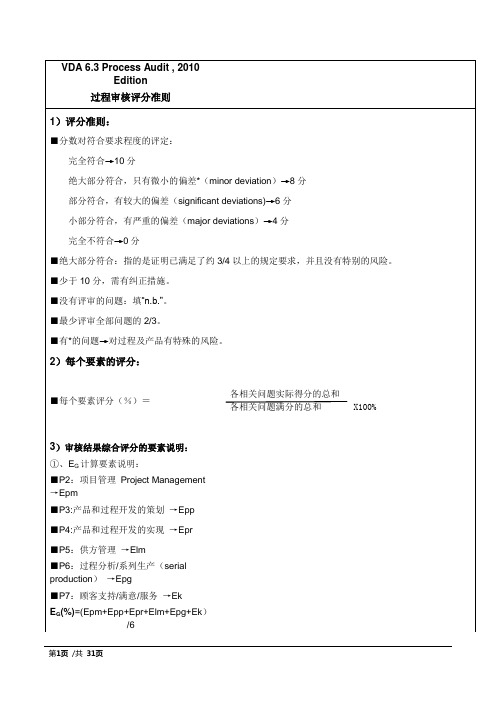
■项目计划=>关键路径则(critical path)
■质量管理计划(QM plan) :项目计划的组成部分。
P2.4
项目组织是否在项目进程中提供了可靠的变更管理?考虑要点,如:
■变更管理需要满足特定的顾客要求。
■变更的可行性检验(manufacturing feasibility check)
EG(%)=(Epm+Epp+Epr+Elm+Epg+Ek)/6
②、过程分析/管理—乌龟图(P6:生产)各要素说明:
■Eu1:输入
■Eu1:工作内容
■Eu3:支持过程
■Eu4:材料、资源
■Eu5:效率
■Eu6:输出/结果
■Eu7:零件运输(Transport/Parts Handling)
4)审核结果的综合评分Overall Assessment:
VDA 6.3 Process Audit , 2010 Ed分数对符合要求程度的评定:
完全符合→10分
绝大部分符合,只有微小的偏差*(minor deviation)→8分
部分符合,有较大的偏差(significant deviations)→6分
小部分符合,有严重的偏差(major deviations)→4分
:记录
■定义的过程[记录所有变更]
■说明变更(highlight)
■和顾客协商沟通、评价
■影响到产品质量的变更=>风险评价
■供方(关键群体)参与
■对变更停止的时间点:明确的定义、遵守
■如果不能遵守,则在顾客和供方之间必须以书面形式加以记录。
■SOP之前的变更时间段:不会影响到产品质量。
VDA6.3过程审核检查表(带示例_自动计算符合率)
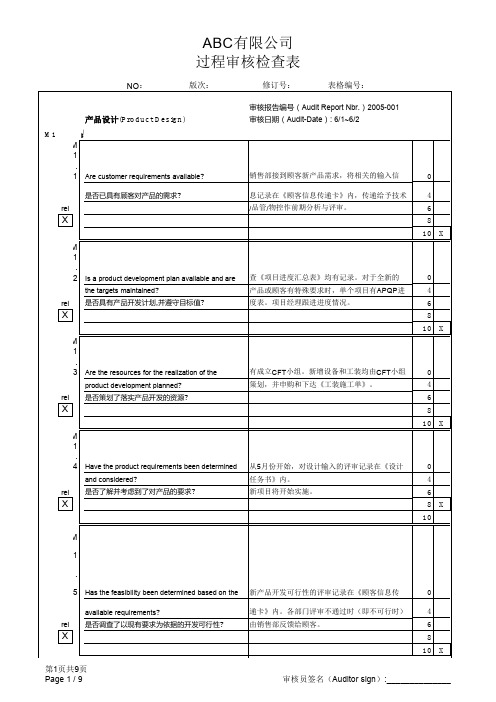
0 4 6 8 10 X 0 4 6 8 10 X
Is a process development plan available and
are the targets maintained? rel 是否已具有过程开发计划,是否遒守目标值?
已根据产品族系列做了相应的P-FMEA。 PCB板系列接插件产品目前还没有做P-FMEA。
0 4 6 X 8 10
X
第3页共6页 Page 3 / 6
审核员签名(Auditor sign):______________
ABC有限公司 过程审核检查表
NO: 版次: 修订号: 表格编号:
审核报告编号(Audit Report Nbr.)2005-001
0 4 6 X 8 10
X
M4.2 Is a quality plan prepared?
是否制定了质量计划? rel
X
M4.3 Are the required releases/qualification records
available at the respective times? rel 是否已具备各阶段所要求的认可/合格证明?
0 4 6 X 8 0 4 6 8 10 X
X
M2.2 Is the design FMEQA updated in the project
process and are established measures realized? rel 设计D-FMEA是否在项目过程中补充更新?已确 定的措施是否已落实?
X
M4.6 Are the required resources available?
rel
VDA6.3检查表

实际审核记录
问题点பைடு நூலகம்
审核人:
年
月
日
7.2是否保证了对顾客的服务?
7.3对顾客的抱怨是否快速反应并确保产品供应? 7.4在与质量要求有偏差时是否进行缺陷分析并实 施改进措施?
7.5执行各种任务的员工是否具备所需的素质?
审核人:
年
月
日
内 部 过 程 审 核 提 问 表
共 4 页
第
页 实际审核记录 问题点
检查项目
1.1是否已具有顾客对产品的要求? 1.2是否具有产品开发计划?是否能遵守目标值? 1.3是否规划了用于落实产品开发的开发能力? 1.4是否调查了解了对产品的要求求并在工作中对 其进行了考虑? 1.5是否调查了以现有要求为依据的开发可行性? 1.6是否已计划/已具备项目开展所需的人员与技 术的必要条件?
2.1是否已进行了设计FMEA并确定了改进措施?
2.2设计FMEA是否在项目过程中补充更新?已确定 的措施是否已落实?
2.3是否制订了质量计划? 2.4是否已获得各阶段所要求的认可/合格证明? 2.5是否已具备所要求的产品开发能力?
3.1是否具备了对产品的要求?
3.2 是否具备了对过程开发的计划?是否遵守目标值? 3.3是否已策划了落实批量生产时能力? 3.4是否调查了解了对生产过程的要求并对此进行了 考虑? 3.5是否已计划/已具备完成项目所需的人员与技 术的必要条件? 3.7是否已做了过程FMEA并确定了改进措施?
共 4 页 检查项目
6.1人员/要素
第
页
实际审核记录 问题点
6.1.1是否对员工委以监控产品质量/过程质量的职 责和权限? 6.1.2是否对员工委以负责生产设备/生产环境的职 责和权限? 6.1.3员工是否适合完成所交付的任务并保持其素 质? 6.1.4是否有包括顶岗规定的人员配置计划? 6.1.5是否有效地使用了提高员工工作积极性的方 法? 6.2生产设备/工装 6.2.1生产设备/工装模具是否能保证满足产品特定 的质量要求? 6.2.2在批量生产中使用的检测、试验设备是否能 有效地监控质量要求? 6.2.3生产工位、检验工位是否符合要求? 6.2.4生产文件和检验文件中是否标出所有的重要 技术要求并坚持执行? 6.2.5对产品调整/更换是否必备的辅助器具? 6.2.6是否进行批量生产起始认可,并记录调整参 数及偏差情况? 6.2.7要求的纠正措施是否按时并检查其有效性? 6.3运输/搬运/储存/包装 6.3.1产品数量/生产批次的大小是否按需求而定? 是否有目的地运往下道工序? 6.3.2产品/零件是否按要求储存?运输器具/包装 方法按产品/零件的特性而定?
VDA6.3最新检查表(评分矩阵+要素说明+评审提问表)

- 时间表 - 变更管理过程描述 - 变更表单 - 变更历史 - 变更评价 - 变更许可
- 顾客 - 供方 - 内部专业部门 - VDA第1卷 - VDA第4卷,第3部分 - VDA手册:新零件开发成熟度保障
- 时间表 - 变更管理过程描述 - 责权的确定 - 变更表单 - 变更历史 - 变更评价 - 变更认可
- 顾客 - 供方 - 内部专业部门 - VDA第1卷 - VDA第2卷 - VDA第4卷 - VDA第4卷,第3部分 - VDA第4卷,产品和过程FMEA - VDA手册:新零件开发成熟度保障
P2.6 项目是否有质量管理计划?是否对其执行情况进行了定期监察以确保其符合性? 在项目计划中必须包含有一份质量管理计划。该表将涉及所有与质量管 理策划有关的事项。 - 项目计划 应根据顾客要求/合同编制质量管理计划,其中既要包含内部、同时也要 - 顾客的里程碑 包含外部产品质量保障规范。 - 设计质量管理策划的顾客要求 针对质量管理计划的编制和管理,定义并任命了相关负责的人员。 - 顾客技术规范 质量管理计划考虑到了总体项目的时间安排。 - 在质量管理计划中考虑到了关键的零部件部分 质量管理计划中包含有关键的供方群体。 - 根据具体的过程技术/产品组,共同实现了计划的评审(状 在质量管理计划中,针对验证和确认,考虑到了所有相关的产品和过程 态) 技术规范。 针对质量管理计划的实现情况,定期对目标的遵守以及实现开展监控。 P2.7 是否建立了事态升级程序,及其是否得到了有效的实施?* 对于项目中的不符合情况,一旦影响到总体的时间表,那么,就必须有 一套事态升级模型(风险管理)可供使用。 为项目描述并建立了一道事态升级过程。在其中考虑到了具体的顾客要 - 根据具体的风险,约定事态升级的时间范围 - 在事态升级过程中定义了联系人/决策者 求。 - 定义了事态升级标准以及联络沟通途径 确定了事态升级的标准。规定了责权关系以及权限。 - 包括措施在内的里程碑评价纪录 通过相应的记录,证明措施(事态升级)的有效性。 如果发现过程技术,供方以及交货国家在存在特殊的风险,那么,同样 应该在事态升级管理中这类情况考虑在内。
VDA6.3检查要求与证据清单(VDA6.3检查表)

5
离及标识?
隔离存放区域
不合格品处理规定
生产 物料箱等
P6.2. 是否对报废,返工和调整件进行了隔
5
离及标识?
不合格品处理规定
生产
不合格品处理记录
产品存放区域管理,
生产 区域标识,
P6.2. 6
是否确保了物料/零件的流向,以防止 混料/错料的产生?
产品状态标识管理, 流程卡, 多余物料存放
P6.4. 生产设施/工装的维护及保养是否受
1
控?
关键设备备件, 模具/工装维护保养,
点检表, 技术 备品备件计划
岗前培训与考核(技能/安全/ 质量工具/产品/过程),
生产 看现场实际操作,
P6.3. 员工是否适合完成下达任务,并且资 特殊岗位能力
2
格是否保持更新?*(人能干吗)
变更(人员岗位变更;产品/ 生产 绩效考核;
过程变更)培训
管理 特殊岗位培训记录要求保留15年
人力资源管理流程(培训/考核
人力资源管理流程(培训/考核/
生产用水/电/气/汽,设备/工 装/模具/检具的验收,备件计
技术
验收报告 CMK(设备过程能力指数)
P4.5
基于要求,是否在不同阶段具有所需 的能力证明和放行(批准)?*
各阶段评审
各阶段评估/评审报告, 技术 里程碑评审,
各阶段管理者承诺
三阶段CP(原则上样件CP就是DVP
P4.6
是否在不同阶段应用了控制计划,并 由此编制出了生产,测试和检验文件?
生产 样件(审核时可现场再验证一
2
对设置数据进行了采集?
模具/工装验证
生产 紧急放行
紧急放行的要求(首件检验结果 生产
VDA6.3过程审核检查表

受审核部门/产品:
体系审核
√ 过程审核
保管编号:
标准 条款
主要内 容
检查 方法
检查记录
评 分
是否对员工委以监控产品质量/过程质量的职责和权限
是否对员工委以负责生产设备/生产环境的职责和权限
员工是否适合于完成所交付的任务并保持其素质
是否有包括顶岗规定的人员配置计划
是否有效地使用了提高员工工作积极性的方法
拟制
日期
批准
日期
FR171004
审核检查表
受审核部门/产品:
体系审核
√ 过程审核
保管编号:
标准 条款
主要内 容
检查 方法
检查记录
评 分
分要素 运输/搬运/储存/包装
产品数量/生产批次的大小是否按需求而定是否有目的地运往下道工序
产品/零件是否按要求储存运输器具/包装方法是否按产品/零件的特性 而定
废品、返修件和调整件以及车间内的剩余料是否坚持分别储存并标识
是否已做了过程 P-FMEA,并确定了改进措施
要素
4
过程开发的落实
过程 P-FMEA 是否在项目过程中补充更新已确定的措施是否已落实
是否制订了质量计划
是否已具备各阶段所要求的认可/合格证明
是否为了进行批量生产认可而进行在批量生产条件下的试生产
生产文件和检验文件是否具备且齐全
拟制
日期
受审核部门/产品:
整个物流是否能确保不混批、不混料并保证可追溯性
模具/工具,工装,检验、测量和实验设备是否按要求存放
分要素 缺陷分析/纠正措施/持续改进(KVP)
是否完整地记录质量数据/过程数据,并具有可评定性
是否用统计技术分析质量数据/过程数据,并由此制订改进措施
VDA6.3最新检查表(评分矩阵+要素说明+评审提问表)

潜力 分析** x x x x x x x
物流和 零件搬运
PV x
基本因素*** ZI KO
RI x
x x xຫໍສະໝຸດ x xx x x x
x
x
x x x
x x x
x
x
x x x x x x x x x x x x x
x
x
x x x x x x x
x x x x
x x x x x
x
x x
x x
x x x x x x
x x x x
x x
x
x x x
x
x x x x
x x x
x
x x
x x
6.5.3* 6.5.4* 6.6 6.6.1* 6.6.2 6.6.3 6.6.4 P7 7.1* 7.2 7.3* 7.4 7.5 7.6
当与产品和过程的要求有偏差时,是否进行了原因分析,并检查了纠 正措施的有效性? 是否定期进行了过程和产品审核? 过程应该产出什么?(过程结果/输出) 在产品和过程方面,是否符合了顾客要求? 数量/生产批次数是否满足要求,并且被以适当的方式提供给下道过 程步骤? 是否用适宜的方式对产品/零件进行了仓储,所使用的运输设备/包装 方式是否与产品/零件的特殊特性相适应? 是否对必要的记录/放行进行了管理,并且进行了适宜的存档? 顾客支持/顾客满意/服务 顾客在质量管理体系,产品(交付时)和过程方面的要求是否得到了 满足? 是否确保了顾客支持? 是否确保了零件供给? 若与质量要求有偏差,是否进行了失效分析,并有效地实施了纠正措 施? 是否具有能够有效地开展缺陷零件分析的过程? 人员资质是否能满足不同的任务,并定义了其职责?
x x
x x
x x x
- 1、下载文档前请自行甄别文档内容的完整性,平台不提供额外的编辑、内容补充、找答案等附加服务。
- 2、"仅部分预览"的文档,不可在线预览部分如存在完整性等问题,可反馈申请退款(可完整预览的文档不适用该条件!)。
- 3、如文档侵犯您的权益,请联系客服反馈,我们会尽快为您处理(人工客服工作时间:9:00-18:30)。
x
查:岗位说明书/或岗位职责 、人员能力评价记录
P6 过程分析/生产
6.1 什么输入过程?(过程输入)
是否在开发和批量生产之间进
6.1.1 行了项目交接?并确保了可靠 x
x
的量产启动?
是否能在正确的时间、正确的
6.1.2 地点(库位、工位)获得所需
x
数量/生产批次数的原材料?
是否对原材料进行了适宜的仓 6.1.3 储,运输设备/包装方式是否 x x
顾客在质量管理体系,产品 7.1 (交付时)和过程方面的要求 x
是否得到了满足?
查顾客要求(合同、各项协 x 议),查交付业绩统计是否满
足顾客要求
7.2
是否对顾客关怀提供了必要的 保障?
x
7.3* 是否确保了零件供给?
x
针对投诉,是否进行了失效分
7.4* 析,并有效地实施了纠正措
x
施?
x xx xx
x
查:生产计划、领料计划的一 致性,文件规定的发料要求
查:仓库储存条件,库位、温 度、湿度、防尘、通风、标识 、先进先出等
x
查:物料标识规定、标识状态
查:设计变更管理,包括顾客
x
提出的变更落实(通知单、文 件收发记录等)、变更后的具
体实施时间及标识
x
查:检验标准并与批产控制计 划比对,核对检验记录
6.2.2*
查:新项目在生产过程所需的 人员配置(操作人员、质量控 制人员)及培训和能力评价
x
查:基础设施的配置及能力验 证记录
查:试产阶段的PPK分析报告
、产能评价报告、测量系统分
x
析报告、过程参数确认报告; 查:批产阶段的合格率统计分
析报告、CPK分析报告等。并
将结果与设计目标核对
x
查:试产CP、批产CP、试产 SOP、批产SOP、检验标准等
x
5.4*
对于外包产品和服务,是否获 得了所需的批准/放行?
x
5.5*
是否确保了外包产品和服务的 质量?
x
5.6
是否对进厂的货物进行了适宜 的储存?
x
针对各具体的任务,相关的人 5.7 员是否具备资质,是否定义了
责权关系?
x
查:试产记录
x
x
查:达产评审记录,关注设计 目标的达成结果、PPAP批准。
x
生?
xx
x
查:各类标识的规定并与现场 核对
询问操作人员物料搬运的要求 并现场核实
6.3 哪些功能为过程提供支持?(过程支持 / 人力资源)
6.3.1*
员工是否能胜任被委派的工 作?
x
x
x
查:员工技能评定记录,如岗 位素质矩阵等
6.3.2
员工是否清楚被委以的产品和 过程质量监控的职责和权限?
x
x 查:岗位说明书
检查了纠正措施的有效性?
6.5.4
是否定期进行了过程和产品审 核?
x
6.6 过程应该产出什么?(过程结果/输出)
产量/生产批量是否是根据需
6.6.1 要确定的,并且有目的地运往
x
下道工序?
是否用适宜的方式对产品/零
6.6.2
件进行了仓储,所使用的运输 设备/包装方式是否与产品/零
x
x
件的特殊特性相适应?
施?
x
x
查:产品特殊特性清单、设计 输入评审记录
x
查:可制造性评审记录及评审 人签字。
查:设计开发计划,包括:工
x
装开发计划、专用检具开发计
划、供方开发计划等
x
查:相关计划及与计划有关的 内容。
x
查:产品和过程开发所需资源 的策划情况。
x xx
查:D/PFMEA所提出采取的措 施及验证和落实,核对CP、 SOP的文件
查半成品库/成品库/车间储存 处:储存条件,库位、温度、 湿度、防尘、通风、标识、先 进先出等。
查各项纪录的审批要求并核 对,询问存档规定并核对。
查客户方质量技术协议与生产 包装要求的一致性。 查公司内部包装的有效性(现 场查看包装有无破损、包装内 产品有无变形等)。
P7 顾客支持/顾客满意/服务
6.3.3 是否有人力资源安排计划?
x
6.4 通过哪些资源实现此过程?(物质资源)
6.4.1*
使用的生产设备是否可以满足 顾客对产品的特定要求?
x
6.4.2
生产设施/工装的维护及保养 是否受控?
x
通过使用的测试、检验和测量 6.4.3* 设备,是否能有效地监察质量 x
要求?
6.4.4
生产工位和测试/检验区域/工 位是否满足要求?
x
x
权限?
查:项目组(或多方论证小 x 组)名单,各成员的任务及责
任明确,人员资格要求明确。
是否为项目开发而策划并落实 2.2 了所需的资源,并且通报了变 x
更情况?
查:项目开发所需的资源配置 x x 清单,包括:软件、资金预算
、潜在供方等。
2.3
是否具备项目计划,并与顾客 进行了协商确定?
x
xx
查:项目开发计划,核对时间 进度与顾客要求的一致性
与原材料的特殊特性相适应?
必要的标识/记录/批准是否存
6.1.4 在,并且适当地体现在来料
x
上?
在系列生产过程中,是否对产 6.1.5* 品或者过程变更进行了跟进并
文件化?
6.2 是否所有生产过程均受控?(过程管理)
6.2.1
生产控制计划里的要求是否完 整,并且得到有效实施?
x
x
查:达产评审及项目开发总结 报告
x
查岗位职责、相关人员的能力 评价等。
备注: 1)标注 为红色“*”的审核项为必审必答项,评分≤4分时,审核结果降级。 2)未带“*”项,评分为0分时,降级。
查顾客要求的服务项目(合同 、各项协议等),查服务人员 的技能、月度报告等。
按照顾客订单查发货记录,关 注交付及时率。查应急预案 (停电或限电、劳动率短缺、 火灾、物料采购不及时、批量 退货等)
查:顾客投诉/退货的分析、 8D报告、可能涉及的工程变更 等。
7.5
人员资质是否能满足不同的任 务,并定义了其职责?
查:供方清单,和对所有供方 的评审和批准记录
x x
查:发给供方的资料与顾客要 求的和对,确保顾客要求已明 确告知供方。
查:与供方签订的所有协议, 包括技术协议、质量协议。关 注对供方的质量目标要求, 如:退货PPM、三包周期等
x 查:供方提交的PPAP资料。
x
查:供方样品试验报告、进货 检查报告的
查:仓库储存条件,库位、温 x 度、湿度、防尘、通风、标识
是否对必要的记录/放行进行 6.6.3 了管理,并且进行了适宜的存
档?
6.6.4*
成品的交付方面是否满足顾客 要求?
x
x
如发现目标未实现,查原因分 析、改进措施及实施结果。
查:过程审核/产品审核的年 x 度计划、实施记录等,关注不
符合项的改进结果。
x x x
查生产计划的编制要求、领料 /发料的规定、搬运作业指导 书等,观察实际结果并与规定 的要求比较。
2.4
是否在项目中实施先期质量策 划,并对其符合性进行监控?
x
项目所涉及的采购事项是否得 2.5* 以实施,并对其符合性加以监 x
控?
项项目组织机构是否可以在项
2.6*
目进行过程中提供可靠的变更 管理?
x
x x
x
查:新项目的质量控制计划及 跟踪评审记录
x
查:变更的评审、措施等涉及 的人员。
查:设计变更管理,包括顾客
x
x
x
查:生产车间的定岗计划及多 能工评定记录
查:设备履历、工装履历等。 查:工装验收记录并与工装设 计文件比较。包括易损件/部 位的更换/维修周期的规定及 实施。
查:设备保养规程、保养计划 、保养记录、维修记录; 查:工装管理规定、保养记录 、精度检查记录。关注易损零 件/易损部位的定期更新记录 。
和过程的特定要求?
基于所确定的产品和过程要
3.2*
求,是否以多功能小组的形 式,对制造可行性进行了评
x
审?
3.3
是否为产品和过程开发编制了 相关的详细计划?
顾客支持/顾客满意/顾客服务 3.4 方面的事项是否具有相应计
划?
3.5
是否对产品和过程开发所需的 资源进行策划?
P4 产品和过程开发的实现
4.1*
提出的变更落实(通知单、文
x
件收发记录等)、设计验证提 出的变更(通知单、文件收发
记录等)。关注变更后的具体
实施时间及标
审核记录
2.7
是否建立了事态升级程序,及 其是否得到了有效的实施?
x
查:设计开发的应急预案,如 x x 进度不能满足顾客要求时的紧
急预案。
P3 产品和过程开发的策划
针对产品和过程的具体要求是 3.1 否已明确?是否已经具有产品 x
是否在量产条件下开展了效能
4.6
测试,以便获得批量生产批准 /放行?
为了确保批量生产的开始,是
4.7* 否对项目导入生产进行了控
x
制?
P5 供方管理
5.1
是否只选择获得批准/放行且 具备质量能力的供方?
x
5.2
是否在供应链上考虑到了顾客 要求?
x
5.3
是否与供方就交付绩效约定了 目标协议,并加以了落实?
6.5 过程实现的效果如何?(有效性、效率、减少浪费)
6.5.1
是否为产品和过程设定了目标 要求?
x
xx
问操作人员/班组长/车间管理 者过程目标有哪些?如:合格 率、废品率、工作节拍等。