炼钢机械: 连铸机械
炼钢连铸工艺流程介绍
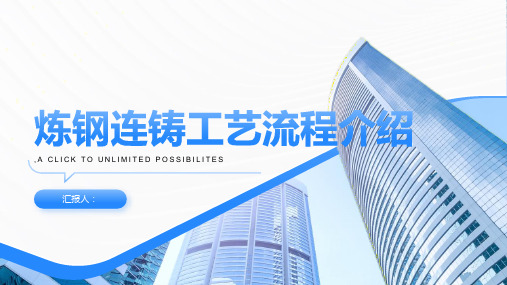
主要方法:采 用脱硫、脱磷、
脱碳等方法
设备:铁水预 处理设备,如 脱硫罐、脱磷
罐等
效果:提高铁 水质量,降低 钢中杂质含量, 提高钢的力学 性能和耐腐蚀
性
转炉炼钢原理:利用高温熔融的钢水与氧气反应,生成铁水与钢渣
转炉炼钢设备:包括转炉、氧枪、钢包等 转炉炼钢过程:将铁水倒入转炉,加入氧气进行反应,生成铁水与钢渣, 然后进行钢渣分离和钢水精炼 转炉炼钢优点:生产效率高,产品质量好,成本低,环保性能好
连铸机的维护:定期检查、维护和 保养,确保连铸机的正常运行
提高生产效率:采用先进的自动化技术,提高生产效率,降低生产成本 节能减排:采用节能环保技术,减少能源消耗,降低环境污染 提高产品质量:采用先进的工艺技术,提高产品质量,满足市场需求 智能化发展:采用先进的智能化技术,实现生产过程的智能化控制,提高生产效率和产品质量
工艺流程:钢液在炉外精炼 设备中进行脱硫、脱氧、脱
碳等处理
优点:提高钢液质量,减少 杂质,降低成本,提高生产
效率
连铸工艺:将钢水连续铸造成钢坯 的工艺
关键技术:连铸机的设计、控制和 维护
连铸机的类型:立式连铸机、卧式 连铸机等
连铸机的工作原理:钢水通过连铸 机,冷却凝固成钢坯
连铸机的控制:温度、速度、压力 等参数的控制
切割速度:根据铸坯尺寸和材质选择合适的 切割速度
切割温度:控制切割温度在1000℃左右, 防止铸坯过热或过冷影响切割质量
切割后处理:切割后对铸坯进行冷却、打 磨等处理,保证铸坯表面光滑、无毛刺
切割质量控制:定期对切割设备进行维护和 校准,确保切割质量稳定可靠。
目的:去除铁 水中的杂质和 气体,提高铁
电炉炼钢原理: 利用电弧热能 熔化废钢和铁 水,生产出钢
钢铁生产工艺的设备

钢铁生产工艺的设备
钢铁生产工艺的设备主要包括以下几种:
1. 炼铁设备:
炼铁是指将铁矿石还原为铁的过程。
常用的炼铁设备有高炉、直接还原炉(如电炉、燃煤直接还原炉)、轧中直接还原炉等。
其中,高炉是最常用的炼铁设备,通过高温煅烧将铁矿石还原为铁水。
2. 炼钢设备:
炼钢是将铁水中的杂质除去,调整合金成分,得到所需钢种的过程。
常用的炼钢设备有转炉、电炉、LF炉等。
其中,转炉
是最常用的炼钢设备之一,通过氧气吹吐将铁水中的碳等杂质氧化除去,同时加入适量合金元素进行调质。
3. 连铸设备:
连铸是将炼钢得到的钢水连续铸造成板坯、方坯或其他断面形状的过程。
常用的连铸设备有铸机、结晶器、铸坯切割装置等。
连铸设备的主要作用是快速冷却和凝固钢水,使其形成坯料。
4. 轧钢设备:
轧钢是将钢坯进行压延加工,制备成所需的钢材形状的过程。
常用的轧钢设备有热轧机组、冷轧机组、轧机等。
热轧机组主要用于压延高温的钢坯,冷轧机组则用于压延低温的钢坯。
此外,钢铁生产还需要其他辅助设备,如原料处理设备、焦化设备、除尘设备、冷却设备、能源提供设备等,以保证生产过
程的顺利进行。
总的来说,钢铁生产工艺的设备是极为复杂的,各种设备在整个生产过程中相互配合,共同完成钢铁的制备。
这些设备的运行稳定性以及技术水平的高低,直接关系到钢铁生产的效率和质量。
为了提高钢铁生产的效率和节约能源,目前还在不断研发改进设备技术,以适应市场需求和环境保护要求。
连铸机械的常见故障与维修措施
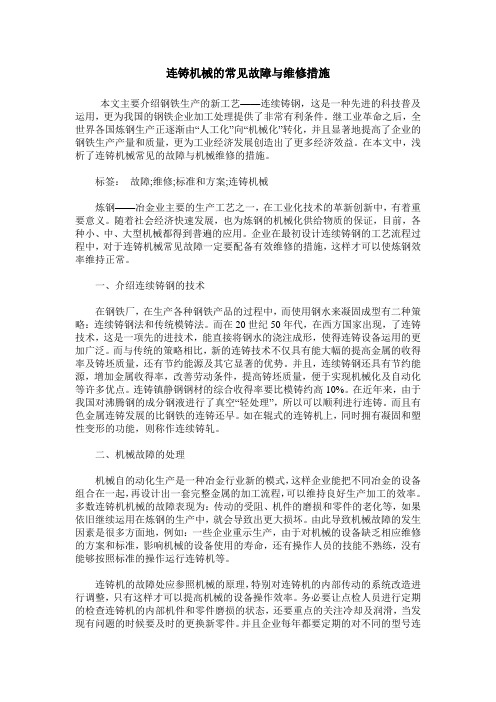
连铸机械的常见故障与维修措施本文主要介绍钢铁生产的新工艺——连续铸钢,这是一种先进的科技普及运用,更为我国的钢铁企业加工处理提供了非常有利条件。
继工业革命之后,全世界各国炼钢生产正逐渐由“人工化”向“机械化”转化,并且显著地提高了企业的钢铁生产产量和质量,更为工业经济发展创造出了更多经济效益。
在本文中,浅析了连铸机械常见的故障与机械维修的措施。
标签:故障;维修;标准和方案;连铸机械炼钢——冶金业主要的生产工艺之一,在工业化技术的革新创新中,有着重要意义。
随着社会经济快速发展,也为炼钢的机械化供给物质的保证,目前,各种小、中、大型机械都得到普遍的应用。
企业在最初设计连续铸钢的工艺流程过程中,对于连铸机械常见故障一定要配备有效维修的措施,这样才可以使炼钢效率维持正常。
一、介绍连续铸钢的技术在钢铁厂,在生产各种钢铁产品的过程中,而使用钢水来凝固成型有二种策略:连续铸钢法和传统模铸法。
而在20世纪50年代,在西方国家出现,了连铸技术,这是一项先的进技术,能直接将钢水的浇注成形,使得连铸设备运用的更加广泛。
而与传统的策略相比,新的连铸技术不仅具有能大幅的提高金属的收得率及铸坯质量,还有节约能源及其它显著的优势。
并且,连续铸钢还具有节约能源,增加金属收得率,改善劳动条件,提高铸坯质量,便于实现机械化及自动化等许多优点。
连铸镇静钢钢材的综合收得率要比模铸约高10%。
在近年来,由于我国对沸腾钢的成分钢液进行了真空“轻处理”,所以可以顺利进行连铸。
而且有色金属连铸发展的比钢铁的连铸还早。
如在辊式的连铸机上,同时拥有凝固和塑性变形的功能,则称作连续铸轧。
二、机械故障的处理机械自的动化生产是一种冶金行业新的模式,这样企业能把不同冶金的设备组合在一起,再设计出一套完整金属的加工流程,可以维持良好生产加工的效率。
多数连铸机机械的故障表现为:传动的受阻、机件的磨损和零件的老化等,如果依旧继续运用在炼钢的生产中,就会导致出更大损坏。
连铸机械的常见故障与维修措施

连铸机械的常见故障与维修措施【内容摘要】连续铸钢是钢铁生产中的新工艺,这种先进科技的普及运用为我国钢铁企业的加工处理创造了有利的条件。
工业科技革命自后,世界各国的炼钢生产逐渐有“机械化”代替“人工化”,显著提高了企业钢铁生产的产量、质量,为工业经济的发展创造了更多的经济效益。
本文分析了“连铸机”常见的故障机维修措施。
【关键词】连铸机械;故障;维修;标准和方案炼钢是冶金业的主要生产工艺,在工业化技术改革创新中有着重要的意义。
社会经济的快速发展为炼钢机械化提供了物质保证,各种大、中、小型机械得到了普遍运用。
企业在制定连续铸钢工艺流程期间,也要对连铸机械的常见故障配备有效的维修措施,以维持正常的炼钢效率。
一、连续铸钢技术介绍在钢铁厂生产各类钢铁产品过程中,使用钢水凝固成型有两种方法:传统的模铸法和连续铸钢法。
而在二十世纪五十年代在欧美国家出现的连铸技术是一项把钢水直接浇注成形的先进技术,连铸机设备的运用更加广泛,如图1。
与传统方法相比,连铸技术具有大幅提高金属收得率和铸坯质量,节约能源等显著优势。
并且,连续铸钢具有增加金属收得率,节约能源,提高铸坯质量,改善劳动条件,便于实现机械化、自动化等优点。
连铸镇静钢的钢材综合收得率比模铸的约高10%。
近年来,我国对沸腾钢成分的钢液进行真空“轻处理”,可以顺利地进行连铸。
有色金属的连铸发展比钢铁连铸为早。
如在辊式连铸机上,兼有凝固和塑性变形,则称连续铸轧。
图1连铸机械的组成二、机械故障的处理机械自动化生产是冶金行业的新模式,企业可以把不同的冶金设备组合起来,设计一套完整的金属加工流程,维持了良好的生产加工效率。
连铸机机械故障多数表现为:机件磨损、传动受阻、零件老化等等,若依旧运用于炼钢生产会导致更大的损坏。
导致机械故障发生的因素是多方面的,如:企业注重生产,对机械设备缺乏相应的维修标准和方案,影响了机械设备的使用寿命;操作人员技能缺乏,未能按照标准操作连铸机等等。
炼钢作业部连铸机械点检员(液压)岗位规范
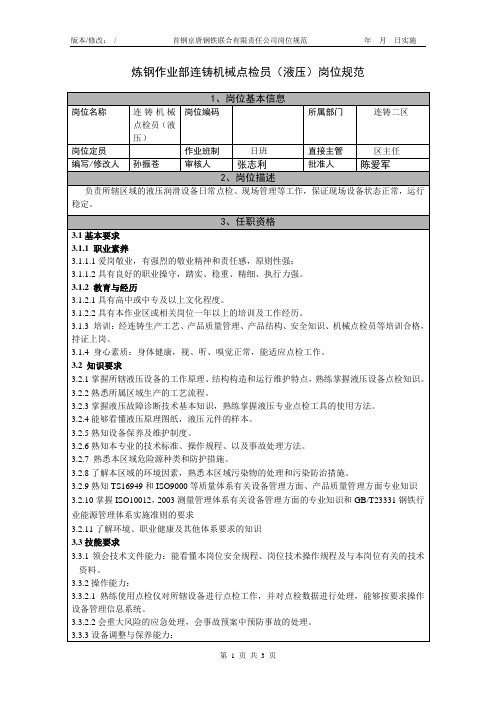
版本/修改: /
首钢京唐钢铁联合有限责任公司岗位规范
年
月
日实施
3.2.3.1 熟悉设备维护保养制度,能够发现并消除设备存在的一般缺陷。 3.2.3.2 能够判断设备是否处理故障状态,并能正确处理。 3.3.3.3 能够按文明生产相关要求进行设备调整和保养。 3.3.4 文字水平与语言表达能力: 3.3.4.1 能按要求填写设备运行记录、操作记录。 3.3.4.2 联系工作口齿清楚,语言表达流畅、准确。 3.3.5 合理化建议与技术革新能力:能对本岗位设备、操作等方面的改进提出合理的想法和建 议。
3、任职资格
3.1 基本要求 3.1.1 职业素养 3.1.1.1 爱岗敬业,有强烈的敬业精神和责任感,原则性强; 3.1.1.2 具有良好的职业操守,踏实、稳重、精细、执行力强。 3.1.2 教育与经历 3.1.2.1 具有高中或中专及以上文化程度。 3.1.2.2 具有本作业区或相关岗位一年以上的培训及工作经历。 3.1.3 培训:经连铸生产工艺、产品质量管理、产品结构、安全知识、机械点检员等培训合格, 持证上岗。 3.1.4 身心素质:身体健康,视、听、嗅觉正常,能适应点检工作。 3.2 知识要求 3.2.1 掌握所辖液压设备的工作原理、 结构构造和运行维护特点, 熟练掌握液压设备点检知识。 3.2.2 熟悉所属区域生产的工艺流程。 3.2.3 掌握液压故障诊断技术基本知识,熟练掌握液压专业点检工具的使用方法。 3.2.4 能够看懂液压原理图纸,液压元件的样本。 3.2.5 熟知设备保养及维护制度。 3.2.6 熟知本专业的技术标准、操作规程、以及事故处理方法。 3.2.7 熟悉本区域危险源种类和防护措施。 3.2.8 了解本区域的环境因素,熟悉本区域污染物的处理和污染防治措施。 3.2.9 熟知 TS16949 和 ISO9000 等质量体系有关设备管理方面、产品质量管理方面专业知识 3.2.10 掌握 ISO10012, 2003 测量管理体系有关设备管理方面的专业知识和 GB/T23331 钢铁行 业能源管理体系实施准则的要求 3.2.11 了解环境、职业健康及其他体系要求的知识 3.3 技能要求 3.3.1 领会技术文件能力:能看懂本岗位安全规程、岗位技术操作规程及与本岗位有关的技术 资料。 3.3.2 操作能力: 3.3.2.1 熟练使用点检仪对所辖设备进行点检工作,并对点检数据进行处理,能够按要求操作 设备管理信息系统。 3.3.2.2 会重大风险的应急处理,会事故预案中预防事故的处理。 3.3.3 设备调整与保养能力:
连铸机械的常见故障与维修措施

连铸机械的常见故障与维修措施摘要:连铸技术的在当前冶金业中逐渐被普及,连铸机械的应用大大提高了企业炼钢的质量和产量,起到了非常明显和至关重要的作用,它将逐渐替代炼钢中的人工操作,形成具有系统化、自动化的生产线作业流程。
但连铸设备的故障也是困扰炼钢企业的一大问题。
笔者系统的分析了连铸机械的多种常见故障,并提出了有效的解决措施。
关键词:连铸机械;设备;故障;维修引言炼钢业中的连铸技术与设备在迅猛发展,在实际炼钢生产中起到了不可估量的重要作用。
但连铸机的故障也是制约生产效率和质量的重要因素,甚至影响到炼钢工艺水平的提高。
在实际炼钢生产中不断出现机械故障、电气故障等,这就需要工作人员在使用连铸设备时掌握一定的排除故障能力和有效的维护方案,不能能够降低设备故障率,还能增加连铸机的使用寿命,提高连铸工艺水平,为炼钢企业增加更多的经济效益。
1.连铸技术的应用连铸技术是现代冶金业中的一项先进的、重要的技术,能够直接将钢水浇筑成型,应用十分广泛,经过多年的总结和延伸,技术也较为成熟。
其原理为:首先将钢坯熔融,然后将钢水持续浇灌到结晶器中,形成凝固的逐渐,再用设备将刚刚初凝的逐渐从结晶器另一端拉出来看,通过控制拉伸的力度、口径等技术手段获得需要的铸件。
连铸技术的发展引燃了炼钢业的一场革命,与传统的冶炼技术不同的是,新的连铸技术不但能大幅度提高成铸率和毛坯质量,而且还有改善工作条件、提高生产效率、节能环保的优势。
连铸技术的快速发展有效促进炼钢技术的提升,例如:冶炼时间与连铸技术的浇筑周期必须同期同步并按一定节拍运行,因而将炼钢过程中的冶金功能大部分转移到铁水处理工序和二次冶金的工序过程中。
提高了炼钢生产的效率和节奏。
连铸技术就似整个炼钢过程中的节拍器,它的持续、有节奏运行,牵动钢包转移、钢水浇灌、转炉连铸等多个工序的效率同步提升,大大提高了整体炼钢过程的效率、质量,增加了炼钢企业的经济效益。
2.电气故障与维修电气故障是制约连铸设备正常生产的一个重要因素,如:变压器故障、供电回路故障、PLC故障等,主要体现在机电一体化的自动化电气设备系统故障,制定有效的维修与维护措施是保障连铸设备正常运转的必要条件。
炼钢机械_连铸冷却及拉矫

14铸坯导向、冷却及拉矫装置铸坯从结晶器下口被拉出时,表层仅凝结一层10~25mm的坯壳,为使中心部位仍为未凝固的钢液,为了顺利拉坯和加快钢液凝固及矫直,需设置铸坯的导向、冷却及拉矫装置。
铸坯的导向、冷却及拉矫装置的作用是:(1)对初凝铸坯进行直接喷水冷却,促使快速凝固,称为二次冷却。
‘(2)对薄壳液芯的铸坯和引锭杆起支承导向作用,使其按正确轨道运行,防止铸坯鼓肚变形和裂纹。
(3)把弧形铸坯矫直,并在开浇前把引锭杆送入结晶器下口。
小方坯连铸机由于铸坯的断面小,冷却快,在钢水静压力作用下不易产生鼓肚变形,而且铸坯在完全凝固状态下矫直,故二冷支导及拉矫装置的结构都比较简单。
大方坯及板坯连铸机铸坯的断面尺寸大,在钢水静压力作用下,初凝坯壳容易产生鼓肚变形,而且在高生产率时,铸坯可能在液芯状态下矫直,因此在铸坯导向装置上需设置密排夹持辊,在拉矫装置上采用多辊多点矫直或连续矫直,结构较为复杂。
4.1 铸坯导向冷却及拉矫装置的构造14。
1.1小方坯连铸机图14—1是德马克小方坯连铸机的铸坯导向装置的结构图。
它只设少数夹辊和侧导辊,这是由于小方坯在浇铸过程中不易产生鼓肚的原因。
夹辊支架用三段无缝钢管制成,I a段和I段用螺栓联接成一体,由上部和中部两点吊挂,下部承托在基础上。
Ⅱ段的两端都支承在基础上。
导向装置上有四对夹辊,五对侧导辊,十二个导板和十四个喷水环,都安装在弧形无缝钢管架上,管内通水冷却,防止受热变形。
导向夹辊用铸铁制作,下导辊的上表面与铸坯的下表面留有20mm的间隙,因此,夹辊仅在铸坯发生大的变形时起作用。
为了适应浇铸不同厚度的铸坯,用垫片来调节夹辊的辊缝。
十二块导向板与铸坯下表面的间隙为5mm。
在图14—1的右上方还表示了供水总管、喷水环管及导向装置支架的安装位置。
在喷水环管上有四个喷嘴向铸坯喷水。
供水总管与导向支架间用可调的支架联结,当变更铸坯断面时,可调节环管的高度,使铸坯表面和四个喷嘴的距离相同。
连铸机安全技术条件说明书

GB ×××××—××××
目次
前言..................................................................................................................................................................... IV 引言....................................................................................................................................................................... V 1 范围................................................................................................................................................................... 1 2 规范性引用文件...............................................................................................................................................1 3 术语和定义.............................................................................................................
- 1、下载文档前请自行甄别文档内容的完整性,平台不提供额外的编辑、内容补充、找答案等附加服务。
- 2、"仅部分预览"的文档,不可在线预览部分如存在完整性等问题,可反馈申请退款(可完整预览的文档不适用该条件!)。
- 3、如文档侵犯您的权益,请联系客服反馈,我们会尽快为您处理(人工客服工作时间:9:00-18:30)。
• 主体设备:盛钢桶及承载设备、中间包及转运设备、
•
结晶器及振动装置、二冷及支导设备(顶弯设备)、
•
拉矫机、引锭链的脱钩、存放、输送装置、切割设备
• 辅助设备:输送辊道、精整设备、推钢机、翻钢机、火焰清理机、
•
渣运机、打印机
• 工艺性设备:钢包吹氩(氮)装置、脱气装置、中间包修砌及烘烤设备
•
保护渣输送设备、结晶器润滑及冷却装置
• 1.钢水处理方面
炉外精炼、加钙、吹氩(氮)
• 搅拌真空脱气及保护浇注
• 2.连铸的钢种不断扩大
• 各种钢种包括特殊钢
• 3.不断提高钢高
采用一机多流、多炉连浇,
提高拉速
• (二) 连铸机机型与发展
•
各种机型图例介绍 P197
5.坯型大型化 简化规格,按需切分, 6.组合浇注连铸
• 自动控制及仪表装置:结晶器液面检测与显示装置、测温、测压、测速、称
•
重、测长装置、二冷辊缝检测装置、控制计算机
四、连铸生产工厂设备
• 3.重点设备介绍
• 3.1浇注设备
•
请同学分析组成结构及作用
• 介绍盛钢桶回转台结构
•
P303~305
•
介绍中间包结构
•
P306~310
四、连铸生产工厂设备
• 3.2结晶器及振动装置
•
动飞剪首次切断连铸坯
• 1959:第三台 立式 唐山钢厂 北设总院
• 1960:试验弧形连铸机成功 北京钢铁学院
• 1963:第一台 弧形 重庆 工业生产
•
1964.6.24 1700弧形 R=6m 拉矫辊辊身1700
•
1200~1500*180板坯 3流250*180方坯 1500液剪
三、连铸机主要参数
•
G——盛钢桶容量,t
•
T——一桶钢水允许浇注的时间 T=(lgG-0.2)/0.3f
•
f——铸坯质量系数 取10~16,质量高取小值
•
A——铸坯断面积
•
V——拉坯速度
•
r——铸坯密度
• 小时产量: Q=60zAVcr (t/h)
•
z——铸机流数 A——铸坯断面积m2
•
Vc——平均拉速 m/min,取(0.8~0.9)倍的工作拉速
•
即成为冶金长度。
•
Le= (H/2K)2 V
•
H——铸坯厚度 K—— 凝固系数 V—— 拉速
三、连铸机主要参数
• 4.拉坯速度
• 铸机每分钟拉出铸坯的长度 m/min
• 铸机每分钟浇注出的铸坯质量t/min
• 拉速主要受限于钢水的凝固速度(影响铸坯出结晶器的厚度),拉
速大,坯壳薄,钢水静压力作用易撑破坯壳而拉漏钢和引起铸坯内部 疏松也和缩孔。
第三章 连铸机械
• 一、连铸工艺过程
• 1.定义:
• 将钢水连续不断地浇注到水冷结晶器内,凝固成一定坯壳厚度的钢坯
连续地从结晶器内拉出,这种钢水连铸和钢坯连拉的过程的生产工艺 即成为连续铸钢。
• 2.连铸工艺过程
•
以弧形连铸机为例介绍(介绍连铸机立面图)P183
• 钢包——回转台——中间罐——结晶器及振动器
• 1.弧形连铸机性能参数:
• 铸坯形状与尺寸、拉速、弯曲半径、流数、冶金长度、生产率
• 2.铸坯断面
• 板、方、矩、圆、六角、八角、工字
• 确定原则:满足轧制或锻压坯料压缩比
•
普钢:Min:4~6 特钢:Min:7~10
•
板坯宽厚比:1.2~1.4
•
断面越大越好
• 3.冶金长度
•
当坯壳厚度为成坯断面厚度一半时铸坯全部凝固,液芯的长度
• 气隙是钢水向结晶器传热,影响凝固的主要障碍,消除办法:结晶器 • 带倒锥度,减小气隙形成
3.2结晶器及振动装置
• (4)影响结晶器传热的因素
• 结晶器内腔面积、结晶器的导热系数、
•
液心矫直时弧形半径
•
多点顶弯矫直时弧形半径
• **固相矫直时内弧表面受拉,外弧表面受压
• 弧形半径:R ≥ 0.5H/[ε]l
•
R» (25~33.3)H
• [ε]l ——铸坯许用延伸率 一般1.5~2%
• H——铸坯厚度
三、连铸机主要参数
• 6.铸机流数与生产能力
• 流数: z=G /TAVr
一机能生产多种坯型 7.实现连铸连轧
采取短流程钢材生产工艺 8.改进连铸机结构 简化整体布局,优化主要装置
二、连铸发展概况
• (三)我国连铸技术与设备的发展
• 1957:第一台 立式 上海 试验研究
• 1958:第二台 立式 重庆 工业生产
•
北京钢铁学院与重钢三厂
•
浇注170*250 矩形坯 ,500t摆
• (1)结晶器应满足的性能
•
*导热性好,促使铸坯快速凝固,形成足
•
够强度的坯壳
•
*刚性好,不易变形,保证铸坯形状规则
• *工作面耐磨、抗热疲劳性好、寿命长
• *重量轻,振动惯性小
•
*结构简单,拆装、调整方便,易制造与维护
• (2)结晶器的传热原理
•
介绍P312图13-1
3.2结晶器及振动装置
• (3)结晶器中钢水热量的释放
•
• ——二冷段(弧形段/扇形段)——拉矫机——切割——堆码
• 钢水——结晶——二冷——拉矫——切割
一、连铸工艺过程
• 3.连铸的优越性
•
低投入,高产出,高效益
• 简化钢坯生产过程,节省投资
• 节省能源,降低生产成本
• 提高金属收得率,降低金属损耗
• 提高钢坯质量,降低废品率
二、连铸发展概况
• (一)连铸技术主要发展
•
r——铸坯密度 t/m3
• 年产量:Y=8760C1C2C3C4Q (t)
• 8760=365*24——年日历小时 C1——日历作业率 C2——日浇注率
•
C3——成坯率 C4——钢坯合格率
四、连铸生产工厂设备
• 1.工厂布置
• 介绍典型连铸生产线的实例
•
车间平面布置
•
请同学介绍实习所见
• 2.组成设备
•
具体表现为:铸坯断面大小与形状、钢种铸
•
机类型、钢温
•
一般拉速与断面周长成正比,与铸坯断面积成反比。
•
V=l’ K2/δ 2
• l‘——结晶器有效长度 = l - 0.1(m)l —— 结晶器长度
• K——凝固系数 δ——结晶器出口的结壳厚度
三、连铸机主要参数
• 5.铸机弧形半径
• 考虑因素:固相矫直时弧形半径
• —— 钢水冷却到液相线释放的热量,据实验,每公斤钢水每降10C释放
0.84KJ热量
• —— 钢液在液相线凝固时释放热量
•
277.2KJ/Kg
• ——凝固的坯壳从结晶温度冷却到出结晶
热量
器时的温度,每下降10C,释放
•
0.67J/Kg
• 结论:钢水在结晶器中是单向传热,途径与热量比例为:
钢水——坯壳26%——气隙71%——结晶器壁1%——冷却水界面2%