切削加工
机械加工工艺基础之切削加工

机械加工工艺基础之切削加工简介切削加工是制造业中常见的一种金属加工方法,通过使用切削工具将工件上的材料去除,使其形状和尺寸得到精确控制。
切削加工具有广泛的应用领域,包括航空航天、汽车制造、机械制造等。
本文将介绍切削加工的基本概念、常用切削工具以及切削加工的一些相关工艺。
切削加工的基本概念切削加工主要依靠切削工具对工件进行切削,切削工具与工件相对运动,通过切削削刃与工件接触,切削下来工件上的材料,从而改变工件的形状和尺寸。
切削加工的基本概念包括切削速度、进给速度和切削深度。
•切削速度(Cutting speed):切削速度是指切削工具相对于工件表面移动的速度,通常以每分钟切削轴转数(RPM)表示。
切削速度的选择取决于材料和切削工具的性质。
•进给速度(Feed rate):进给速度是指每刀具转一圈时工件上与切削工具的相对运动速度,通常以每分钟进给量表示。
进给速度的选择取决于切削类型和切削工具的性质。
•切削深度(Depth of cut):切削深度是指工件上切削削刃切入工件的距离,也称切削量。
切削深度的选择会影响加工表面的质量和切削力的大小。
常用切削工具切削工具是切削加工的核心部分,常用的切削工具有刀具、钻头和铣刀等。
刀具刀具是切削加工中最常用的工具,常见的刀具包括车刀、铣刀、钻头等。
刀具通常由高速钢(HSS)或硬质合金制成。
刀具的设计和选择会影响切削过程的效率和加工质量。
钻头钻头是用于钻孔的切削工具,通常由硬质合金制成。
钻头的种类繁多,包括中心钻、旋刃钻、麻花钻等。
钻头的直径和结构会影响钻孔的大小和质量。
铣刀铣刀是通过刀具的旋转来对工件进行切削的工具。
铣刀可以分为面铣刀、立铣刀和滚刀等多种类型,根据不同的加工需求选择合适的铣刀。
切削加工的工艺切削加工的工艺包括切削类型、切削参数和切削润滑剂的选择。
切削类型常见的切削类型包括纵向切削、横向切削和竖向切削。
•纵向切削:也称为平面切削,刀具与工件表面垂直运动,沿工件表面切削材料。
切削加工基本知识

1 切削加工基本知识1.1 概述切削加工是利用切削工具从毛坯或半成品上切除掉多余的材料,以获得形状、尺寸以及表面粗糙度等各方面都符合图纸要求的机械零件。
切削加工是机械制造过程中的重要环节,零件的加工,特别是精度和表面质量要求较高的零件都必须经过切削加工。
切削加工分为机械加工和钳工。
机械加工是由工人操作机床对工件进行切削加工,钳工一般由工人手持工具对工件进行切削加工。
零件的加工制造一般是在常温状态下进行的,不需要加热,故称为冷加工。
切削加工是冷加工的主要方式,冲压加工和特种加工也属于冷加工。
1. 2切削运动分析及切削用量1.2.1零件典型表面的种类及形成零件都是由一个表面(如球面)或多个不同性质的典型表面组成的。
因此,我们可以将各种各样的零件简化为数量有限的几个不同性质的典型表面的组合。
绝大多数的零件由以下两大类表面组成:1.2.1.1基本表面(1)回转体表面是以直线为母线,以圆为运动轨迹,且母线与回转轴线在同一平面内(互相平行或相交)作旋转运动所形成的表面,如内、外圆柱面,内、外圆锥面。
若母线为折线或曲线,则形成回转体成形表面。
这类表面一般在车床、钻床、镗床、磨床等机床上加工。
(2)平面是以直线为母线,以另一直线为轨迹作平移运动时所形成的表面。
若母线为折线或曲线,则形成纵向成形表面,如燕尾槽、齿条。
这类表面一般在铣床、刨床、插床和磨床等机床上完成。
1.2.1.2型面这是以曲线为母线,运动轨迹也为曲线或圆,作旋转或平移时所形成的表面,如各种造型模具的型腔、气轮机叶片。
这类表面一般在数控铣床、加工中心、电火花机床等机床上完成的。
1.2.2切削运动切削加工是靠切削运动实现的。
所谓切削运动是指刀具与工件之间的相对运动。
切削运动按其在切削加工中的作用,可分为主运动和进给运动。
1.2.1.1主运动主运动是由机床或人力提供的主要运动,它促使刀具和工件之间产生相对运动,从而使刀具前面接近工件。
在切削加工中主运动必须有,但只能有一个。
第1篇切削加工的理论基础
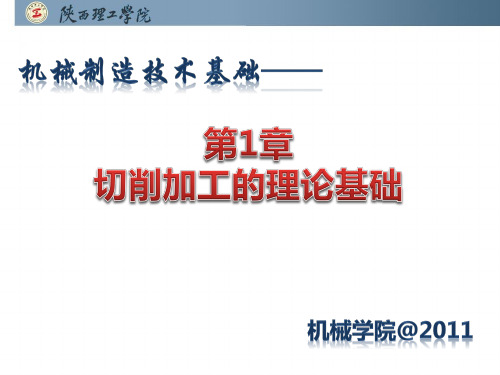
第1章 切削加工的理论基础
机械制造技术基础
1.2.1 切屑的形成
挤压与切削 正挤压:
金属材料受挤压时,最大剪应力方向与作用力方向约 成45°
偏挤压:
金属材料一部分受挤压时,OB线以下金属由于母体阻 碍,不能沿AB线滑移,而只能沿OM线滑移s
机械制造技术基础
刀具 O
切屑根部金相照片
1.2.2 切削层的变形及其影响因素
变形区的划分
第一变形区
机械制造技术基础
第二变形区
第三变形区
1.2.2 切削层的变形及其影响因素
第一变形区的变形特征:
切削层金属沿滑移线的剪切 滑移变形及随之产生的加工 硬化。
第一变形区的实际厚度为 0.02~0.2mm,切削速度越 大,厚度越小。故第一变形 区可看成是一个剪切面。
剪切面与切削速度之间的夹 角成为剪切角,体现变形的 难易程度。
机械制造技术基础
1.2.2 切削层的变形及其影响因素
机械制造技术基础
第二变形区的变形特征:
切屑底层金属受摩擦挤压后的塑性变形及晶粒纤维化。
受力:
挤压
摩擦
滑移与晶粒的伸长
1.2.2 切削层的变形及其影响因素
前刀面内的摩擦(内摩擦与外摩擦) 区域划分: 粘结区lf1: 剪切滑移,内摩擦 滑动区lf2: 滑动摩擦,外摩擦
切屑长度压缩比(Λl)
l
LD Lch
h
hch hD
OM
sin(90 OM sin
o)
cos( o ) sin
表示切屑变形程度的方法
机械制造技术基础
第5章 切削加工的基础知识

(1) 钨钴类 其代号为 YG,相当于 ISO 标准的 K 类。 (2) 钨钛钴类 其代号为 YT,相当于 ISO 标准的 P 类。 (3) 钨钛钽(铌)钴类 其代号为 YW,相当于 ISO 标准的 M 类。YW 类合金兼有 YG 类 和 YT 类合金的大部分优良性能,故被称为通用合金。
图 5.6 车刀的主要角度及辅助平面
1—正交平面 2—正交平面图形平移 3—翻倒
1—切削平面 2—基面 3—正交平面
(1) 前角 γ o 前刀面与基面的夹角,在正交平面中测量。其作用是使切削刃锋利,便 于切削。但前角也不能太大,否则会削弱刀头的强度,容易磨损甚至崩坏。加工塑性材料 时,前角应选大些,加工脆性材料时,前角要选小些。另外粗加工时前角选较小值,精加 工时前角选较大值。前角取值范围为-5°~25°。
1. 高速工具钢
是指含有钨、铬、钒等元素的高合金工具钢,热处理后硬度可达 62HRC~65HRC。当 切削温度为 500℃~600℃时,高速工具钢能保持其良好的切削性能。这种材料用于各种刀
·98·
第 5 章 切削加工的基础知识
·99·
具,尤其是各种复杂刀具的制造,如钻头、铣刀、拉刀、齿轮刀具、丝锥、板牙、铰刀等。
f
z=
f z
单位时间进给量称为进给速度 vf,单位为 mm/s 或 mm/min。进给量越大,生产率一般
越高,但是,零件表面的加工质量也越低。
切削加工基本知识
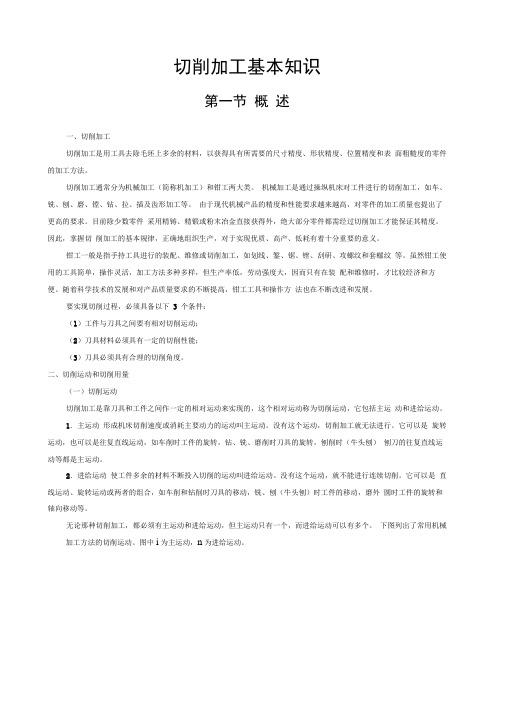
切削加工基本知识第一节概述一、切削加工切削加工是用工具去除毛坯上多余的材料,以获得具有所需要的尺寸精度、形状精度、位置精度和表面粗糙度的零件的加工方法。
切削加工通常分为机械加工(简称机加工)和钳工两大类。
机械加工是通过操纵机床对工件进行的切削加工,如车、铣、刨、磨、镗、钻、拉、插及齿形加工等。
由于现代机械产品的精度和性能要求越来越高,对零件的加工质量也提出了更高的要求。
目前除少数零件采用精铸、精锻或粉末冶金直接获得外,绝大部分零件都需经过切削加工才能保证其精度。
因此,掌握切削加工的基本规律,正确地组织生产,对于实现优质、高产、低耗有着十分重要的意义。
钳工一般是指手持工具进行的装配、维修或切削加工,如划线、錾、锯、锉、刮研、攻螺纹和套螺纹等。
虽然钳工使用的工具简单,操作灵活,加工方法多种多样,但生产率低,劳动强度大,因而只有在装配和维修时,才比较经济和方便。
随着科学技术的发展和对产品质量要求的不断提高,钳工工具和操作方法也在不断改进和发展。
要实现切削过程,必须具备以下3 个条件:(1)工件与刀具之间要有相对切削运动;(2)刀具材料必须具有一定的切削性能;(3)刀具必须具有合理的切削角度。
二、切削运动和切削用量(一)切削运动切削加工是靠刀具和工件之间作一定的相对运动来实现的,这个相对运动称为切削运动,它包括主运动和进给运动。
1.主运动形成机床切削速度或消耗主要动力的运动叫主运动。
没有这个运动,切削加工就无法进行。
它可以是旋转运动,也可以是往复直线运动,如车削时工件的旋转,钻、铣、磨削时刀具的旋转,刨削时(牛头刨)刨刀的往复直线运动等都是主运动。
2.进给运动使工件多余的材料不断投入切削的运动叫进给运动。
没有这个运动,就不能进行连续切削。
它可以是直线运动、旋转运动或两者的组合,如车削和钻削时刀具的移动,铣、刨(牛头刨)时工件的移动,磨外圆时工件的旋转和轴向移动等。
无论那种切削加工,都必须有主运动和进给运动,但主运动只有一个,而进给运动可以有多个。
切削加工知识点总结

切削加工知识点总结一、切削加工概述切削加工是指用刀具在工件上进行物质去除的一种加工方法,是制造业中最常见、最重要的加工方式之一。
切削加工分为传统切削加工和非传统切削加工两大类。
传统切削加工以车、铣、钻、镗、磨为代表,主要依靠刀具对工件进行物质去除。
非传统切削加工包括激光切割、电火花加工、超声波加工、高压水射流切割等,主要依靠其他能量对工件进行物质去除。
本文将主要介绍传统切削加工的相关知识点。
二、刀具1. 刀具的分类刀具可按照不同标准进行分类,如按形状分为转动刀具和平动刀具;按用途分为车刀、铣刀、钻头、切削刀片等;按加工工件的特点分为粗加工刀具和精加工刀具等。
2. 刀具的结构刀具由切削部分和刀柄组成,其中切削部分又包括主切削刃和辅切削刃。
刀柄用于连接和固定刀具,同时也需要具有足够的刚度和强度。
3. 刀具材料刀具的材料选择非常重要,一般需具备较高的硬度、耐磨性和热稳定性。
常用的刀具材料包括高速钢、硬质合金、陶瓷、立方氮化硅和金刚石等。
三、切削原理1. 切削力切削力是指刀具在切削过程中对工件所施加的力,其大小和方向受刀具的切削角度、进给量、转速、材料性能等因素影响。
合理控制切削力对降低切削振动、提高表面质量和延长刀具寿命非常重要。
2. 切屑形成在切削过程中,金属材料被刀具切除后形成的薄膜状物质称为切屑。
切屑的形成方式及类型取决于刀具的切削角度、刀具材料、工件材料和切削参数等。
合理的切削参数可以调整切屑的形成方式,在一定程度上影响切削效率和工件表面质量。
3. 切削温度切削过程中,由于切削热的激发,会导致刀具和工件的温度升高。
合理的切削冷却和润滑能有效地降低切削温度,并有效地减小材料变形、提高表面质量、延长工具寿命。
四、切削参数1. 主切削角主切削角是刀具主要切削刃与工件表面法线之间的夹角。
刀具的主切削角大小影响着切削加工的效率、刀具寿命以及工件的表面质量,不同的材料和加工情况需要选用不同的主切削角。
2. 副切削角副切削角是刀具次要切削刃与工件表面的法线之间的夹角。
机械制造基础之切削加工

第六章切削加工
第一节 切削加工概述 一、切削加工的分类、特点、应用及发展方向 1.切削加工的分类 切削加工是利用切削刀具从工件毛坯上切除多余的
材料,以获得具有一定形状、尺寸、精度和表面 粗糙度的零件的加工方法。 目前,机械零件除了少数是利用精密铸造、精密锻 造、粉末冶金等无屑加工方法获得,大多数零件 还是靠切削加工的方法来完成。因此,切削加工 在机械制造中占有重要的地位。
2
• 切削加工可分为机械加工和钳工两部分。
(1)机械加工又称(机加工、冷加工),是通过人工操纵机床 设备来实现的。
主要有车削、钻削、镗削、铣削、刨削、磨削及齿轮加工等。
所用的机床分别为车床、钻床、镗床、铣床、刨床、磨床及齿 轮加工机床等。
(2)钳工是在平台上手持工具 来进行切削加工。
主要加工有画线、錾切、锯割、锉削、刮削、钻孔、扩孔、铰 孔、攻螺纹、套丝、机械装配和设备修理等。
对于有些加工工艺过程,例如钻孔和绞孔,机械加工和钳工并 没有明显的界限,两者均可进行。
目前,随着加工技术的发展和自动化程度的提高,钳工中的某 些工种已逐渐实现机械化和自动化,而且这种替代将会愈来 愈多。但在机器装配和修理等工艺过程中,钳工比机械加工 更为灵活、方便和经济,并容易保证产品的质量,所以钳工 加工具有独特的价值,是切削加工中不可缺少的一部分。
例如卧式车床的卡盘和尾架,钻床、刨床、铣床和平面磨床的工 作台等。
(4)刀具安装装置 用来安装刀具。
例如车床、刨床的刀架,钻床、立式铣床的主轴,卧式铣床的刀 轴,磨床磨头的砂轮轴等。
(5)支承件 用来支承和连接机床的各零部件,是机床的基础构件, 例如各类机床的床身、立柱、底座、横梁等。
(6)动力源 为机床运动提供动力,即电动机。
第5章 切削加工基础知识
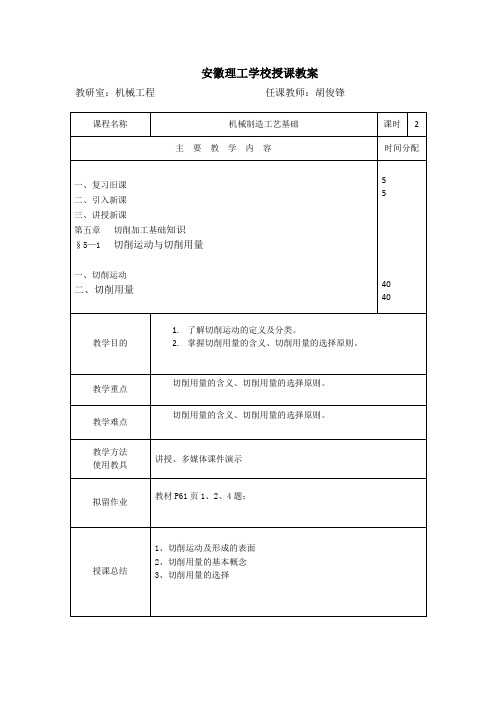
安徽理工学校授课教案教研室:机械工程任课教师:胡俊锋第五章 切削加工基础知识§5-1 切削运动与切削用量(一)切削运动及形成的表面1. 切削运动的定义及分类在切削过程中,工件和刀具之间的相对运动叫切削运动。
切削运动分主运动和进给运动两类:(1) 主运动:直接切除工件上的被切削层,使之转变为切屑,形成工件新表面的运动叫做主运动。
(2) 进给运动:使新的切削层不断投入切削的运动叫做进给运动。
进给运动又分为横向进给运动和纵向进给运动。
2. 切削时工件上形成的三个表面(1)已加工表面:已切去多余金属而形成的新表面。
(2)待加工表面:即将被切去金属层的表面。
(3)加工表面:刀刃正在切削的表面。
(二)切削用量的基本概念1.切削用量的定义切削用量是表示主运动及进给运动大小的参数,它包括切削深度、进给量和切削速度。
(见图1-2)(1)切削深度(吃刀深度)p a 单位:mm工件上已加工表面和等加工表面间的垂直距离叫切削深度。
车削外圆切削深度的计算公式: p a =2mw d d 式中p a :切削深度 w d :工件待加工表面直径 m d :工件已加工表面的直径。
(2)进给量(走刀量)ƒ 单位:mm/r进给量是指在主运动的一个循环内,刀具与工件沿进给运动方向的相对位移。
(3)切削速度v 单位:m/min 在进行切削加工时,刀具切削刃上某点相对待加工表面在主运动方向上的瞬时速度叫切削速度。
切削速度的计算公式为v=1000nd w 式中:v:切削速度 ,m/min w d :工件待加工表面的直径,mm n :车床的主轴转速,r/mim 。
例 车削的工件直径w d =50mm ,车床主轴的转速n=600r/min ,求切削速度v?解:根据公式可得: v=1000 n d w =10006005014.3X X =94(m/min ) (三)切削用量的选择合理的选择切削用量将对提高工件加工表面质量、刀具耐用度、生产效率和降低成本有利。
- 1、下载文档前请自行甄别文档内容的完整性,平台不提供额外的编辑、内容补充、找答案等附加服务。
- 2、"仅部分预览"的文档,不可在线预览部分如存在完整性等问题,可反馈申请退款(可完整预览的文档不适用该条件!)。
- 3、如文档侵犯您的权益,请联系客服反馈,我们会尽快为您处理(人工客服工作时间:9:00-18:30)。
車削(Turning)是切削加工方法中應用最為廣泛的一種,尤其是所得到加工面的表面粗糙度範圍最廣,粗糙度之Ra值從 到 都可產生。使用的工具機為車床(Lathe),在金屬材料製造業中被稱為「金工之王」或「工具機之母」。主要的加工方式是將具圓形截面工件的一端夾持於車床主軸的夾頭上,另一端則可用或不用尾座的頂針支撐住。工件隨同主軸做旋轉運動,以固定在刀架上的單鋒刀具做直線移動,將工件製成產品時不要部份的材料去除。
上述之加工程序適用於圓形之通孔或不通孔(未貫穿工件材料之孔,又稱為盲孔)的加工。若工件是薄板材且為通孔加工時,可使用薄板加工法中的沖孔(Punching),其生產效率極高,但模具的費用很高,必須是產量有一定規模時才合乎經濟效益。
拉削(Broaching)則可用於工件之外表面和各種形狀內孔的加工,使用立式或臥式的拉床(Broaching machine)以推或拉的方式移動拉刀或工件,使其產生相對運動達成切削作用,拉床的種類本書將於第八章中加以說明。拉刀是指由一系列尺寸漸增的連續切齒所構成的條形刀具,在完成一次加工操作過程後即可得到所要的產品,如圖7.5和圖7.6所示。拉削加工的優點有高生產效率、加工面精度高、刀具壽命較長和適用於自動化生產。缺點有拉削不適合做大量材料的切除、機器的剛性及工件的夾持要能承受拉削的作用力因而增加設備成本、拉刀構造複雜、拉削之孔徑不可小於10㎜但也不可大於80㎜和拉刀的製作費用高故不適合於小量生產。
說明。
鑽頭是切削刀具的一種,構成的部份有鑽柄(Shank),鑽身(Body)和鑽尖(Drill point),如圖7.4所示。鑽柄可為直柄或錐度柄,由鑽頭夾頭或套筒夾持裝入鑽床主軸內,用以帶動鑽頭。鑽身則是由鑽槽(Flute),鑽邊(Margin)和鑽腹(Web)所組成。鑽槽是用來排除切屑及使切削液得以流到鑽尖切削區。最常見的型式為兩個螺旋槽之鑽頭,稱之為蔴花鑽頭(Twist drill),也有單槽、三槽或四槽的鑽頭。鑽尖則包含鏨刃(Chisel edge)和鑽唇(Lip)。鏨刃又稱為靜點(Dead point)為兩鑽唇交接點,位置需在鑽軸中心上。鑽唇則為鑽頭之刀刃口(Cutting edge),有兩片,其夾角以 為標準角度。對於深孔鑽削則需注意克服排屑、冷卻及行程導引等問題,因而有直槽式深孔鑽頭,又稱為槍管鑽頭(Gun drill)的出現。對於在薄金屬板上鑽孔,則可使用圓鋸式鑽頭或翼形刀具(Fly cutter)。
製孔方法中的車床鑽孔已敘述於前。此外,可使用銑削之端銑刀銑製圓孔,將於第7.5節中敘述。而插床之插刀切削加工則可用於製造方孔、多邊形孔或不通孔,並將於第7.6節中敘述。
遇到小孔徑的深孔,夾持困難的工件,或難切削材料的孔加工時,可使用非傳統加工方法中的雷射、電子束、水噴射、磨料噴射、放電、放電線切割、超音波、電漿、化學蝕刻、電化學等進行各類型的製孔操作,本書將於第十一章中加以說明。有時也可使用氧乙炔氣或電弧切割方法,甚至以人工剪裁方式對薄板材進行孔的加工。當以鑄造或粉末冶金(本書將於第十一章中加以介紹)方法製造產品時,可利用砂心等預留空出孔的位置及大小,也是常見的加工過程。
車床的操作方式有手動、半自動和全自動。車床的種類有普通車床(又稱機力車床)、枱式車床、六角車床(又稱轉塔車床)、立式車床、自動車床、靠模車床、和電腦數值控制車床等,本書將於第八章中加以說明。
7.3 鑽削
使用鑽床(Drilling machine)上的鑽頭(Drill)在工件材料上鑽削出內孔,是目前最普遍也是最主要的製孔方法。加工過程是先將工件固定夾持在工作枱上,鑽頭則裝置在鑽床主軸上並隨之旋轉,並且同時沿著主軸軸向做進給移動,因而在工件上製作圓孔。車床和鑽床之鑽孔方式不同,在車床上鑽孔是工件隨著主軸旋轉,鑽頭固定在尾座上做進給移動而得。鑽孔加工一般分為鑽孔、深孔鑽孔和小孔鑽孔等。鑽孔加工是屬於半封閉式的切削過程,施加的切削液不容易到達切削區,而切屑也不容易自切削區排出,故常會發生切屑刮傷已完成加工的內孔壁或堵塞住孔,也常會出現鑽頭折斷的現象,鑽削的工作包含鑽孔、搪孔、鉸孔、鑽錐坑、鑽柱坑、切魚眼孔和攻螺紋等,鑚床的種類本書將於第八章中加以
藉由配合不同型式的刀具,車削可執行的工作有切削工件之外徑、外形、端面、錐度、階級、凹槽、切斷、鑽孔、搪孔、鉸孔、外螺紋、內螺紋、壓花、繞彈簧及成型面等,圖7.3顯示其中的部份工作。
有關車刀的材質、幾何形狀和刀具型式等已在第六章中詳述過。車刀的形狀及種類可依其應用的場合分為左手車刀、右手車刀和圓鼻車刀,或是分為外徑車刀、內孔車刀、切槽車刀、切斷車刀、牙刀、倒角車刀、搪孔車刀、成型車刀和壓花刀等。
第七章 切削加工
一般稱為傳統切削加工,是指使用工具機(Machine tools)產生的機械力,經由刀具對工件材料進行切削作用而成形的加工方法。刀具的型式包含單鋒刀具、多鋒刀具和磨輪。有時依工件的外形分為圓形工件加工和非圓形工件加工。傳統切削加工常見的有車削(Turning),鑽削(Drilling),銑削(Milling),鉋削(Planning)和磨削(Grinding)等五種,相關的刀具與工件之運動方式有直線運動和旋轉運動,如圖7.1所示。近年來的發展顯示刨削已被其它加工方法所取代,車削、鑽削、銑削和鉋削所產生的平均切屑厚度約為0.025㎜到2.5㎜之間,磨削則為0.0025到0.25之間。切削過程中必須適時視實際狀況選用最佳組合的切削參數為三個切削條件,即切削速度(Cutting speed),進給(Feed)和切削深度(Depth of cut)。
鑽削的切削速度(V,m/min)和車削的定義類似,即 ,其中 鑽頭直徑 , 主軸每分鐘旋轉數(rpm或rev/min)。最常見的双刃鑽頭之進給(f,mm/rev)是指鑽頭轉一圈時,同時向工件內部的移動距離,故每刃的進給為(1/2)f進給率 (mm/min)等於 。鑽削的材料移除率 可表為 。
7.4 製孔方法
將圓盤鋸片改成使用磨料圓盤做為刀具時,是利用其高速旋轉所產生的摩擦能並轉換成熱能,促使材料軟化,然後配合進給壓力進行鋸切作用。此時,需注意熱影響區造成的不良副作用,和工件材料黏附在鋸片上的問題。此法適用於硬的鐵系金屬和強化塑膠的鋸切等。
3.連續式鋸切
將具有撓性的長鋸片,利用熔接方式接合成環形鋸條,放置於兩個以上的轉輪之外,做單向轉動的連續式鋸切。鋸條只有一小部份顯露在帶鋸機(Bandsawing machine)令外殼外面,藉由控制鋸片張力和導引裝置可進行往復式鋸切及圓盤鋸切所無法達成的曲線鋸切,用途非常廣泛。使用帶鋸機進行輪廓及曲面等之成形切削,具有快速、安全、簡易、省材料、省能源及低成本的優點,使用上的限制很少,適用於許多不同材料與各種形狀、大小尺寸工件的鋸切加工。
7.5 銑削
銑削(Milling)加工是指將銑刀固定在工具機主軸上並一起做旋轉運動,同時夾持固定在工作枱上的工件或主軸上的銑刀做直線進給運動的切削方法,它是機械製造中常用的加工方法之一。銑削主要是用來加工各種平面、曲面、垂直面、角度、溝槽、成型面、齒輪及切斷等。銑刀是一種圓形刀具,由刀體和許多刀齒(Tooth)所組成,刀齒的型式有直線形和螺旋形。銑刀的構造有整體型刀具和在刀齒處嵌入或鎖上捨棄式刀片作為刀刃等。有關銑刀各部份名稱,如圖7.7所示。銑刀的刀齒數依銑刀的直徑和型式可自端銑刀的二齒到鋸割銑刀的超過八十齒等而有不同的數目。
2.圓盤鋸切
使用圓周上有鋸齒的圓形鋸片作為鋸切刀具,當工件挾持固定後,鋸片以直式、橫式或傾斜方式朝工件進刀,執行切斷操作。使用的工具機稱為圓鋸機(Circular sawing machine),又稱為冷鋸機(Cold sawing machine)。此法的優點為可得到高生產效率、高精度、不需毛邊去除製程、刀具成本很低、操作簡單、可切任何材料及尺寸的工件。雖然機器成本較高,但上述的加工效益可以很快地抵銷此項成本。
鑽削加工是最常見的製孔方法。但它是屬於粗加工,對於內孔壁表面之光滑度,或形狀及尺寸之精度要求較高的孔,則需再進行搪孔(Boring)及鉸孔(Reaming)等後續加工,甚至使用內部研磨(Internal grinding)、搪磨(Honing)或拋光(Polishing)等超精密加工。
搪孔是利用單刃或多刃搪孔刀具,將已存在工件中之內孔壁上的材料進一步去除,使孔徑擴大的一種精密加工方法。搪孔刀可裝置在鑽床、車床或銑床上執行搪孔工作,但對於大型或特殊形狀的工件,則必須在搪床(Boring machine)上加工,才可得到較精確的尺寸,加工效率也較高。通常工件是固定的,搪孔刀做旋轉運動和進給運動。此外,搪床也可做車平面、車端面、車凹槽、車螺紋等工作。常見的搪床有臥式、立式和工模搪床等,本書將於第八章中加以說明。
其中, 切削速度
工件外徑
主軸每分鐘旋轉數(rpm或rev/min)
進給(f,mm/rev)是指工件每旋轉一圈,車刀在工件軸向或徑向的移動距離。切削深度(㎜)則是指車刀在工件徑向上,自未被切削面到被切削面間的進入距離。在車外徑時,工件每旋轉一圈其直徑會減小兩個切削深度的大小量。進給率(Feed rate)以 表示,單位為(mm/min),車削中進給率和進給關係為 。材料移除率以 表示,單位為 ,且 。因此可知上述任何一個切削條件的值增加時,都可提高材料移除率,但也都會減少刀具壽命。其中,切削速度對刀具壽命的影響最大,而切削深度的影響則為最小。
在木材工業方面有各類型的木材鋸切加工機器被大量使用,金屬工業的鉗工方面有手工鋸切使用的手弓鋸。至於利用動力操作的金屬材料鋸切作業主要的型式有裝置到弓鋸機(Hacksawing machine)的鋸架上,利用等速旋轉的曲柄帶動鋸架進行往復式運動,故又稱為往復式鋸床。加工過程的一半是切削行程,另一半則為沒有鋸切作用的回程行程,故加工效率較差,適用於產量不是很高的小型工廠。此法的優點為機具投資成本較低、操作簡單、刀具成本低、可以鋸切不同種類的材料、大斷面尺寸和任何長度的工件。缺點為切削過程是間歇性的作用,切削速度不斷的改變,無法做連續式的快速切斷操作。
7.1 鋸切
鋸切(Sawing)通常是大多數零件製造過程中的第一個加工道次,來自一次加工所得的線材、棒材、管材、型材、板材等,往往需先將材料切成所要求的長度以利後續之二次加工,尤其在大量生產與切斷非對稱形狀工件的操作上,以使用鋸切的方法最為常見,原因是它具有簡便、快速和具經濟性等優點。利用直條形、連續式帶狀或圓盤形之鋸片上的一連串小切齒當作切削刀具,每一個小切齒都會移除一部份的工件材料形成和拉削或鉋削相類似的切屑。鋸片上之鋸齒為交錯式的排列,用以提供排屑所需的空隙。鋸片的寬度一般較狹窄,故鋸切浪費的工件材料很少。