主要工艺参数作用及选择
研磨加工中的研磨工艺参数选择
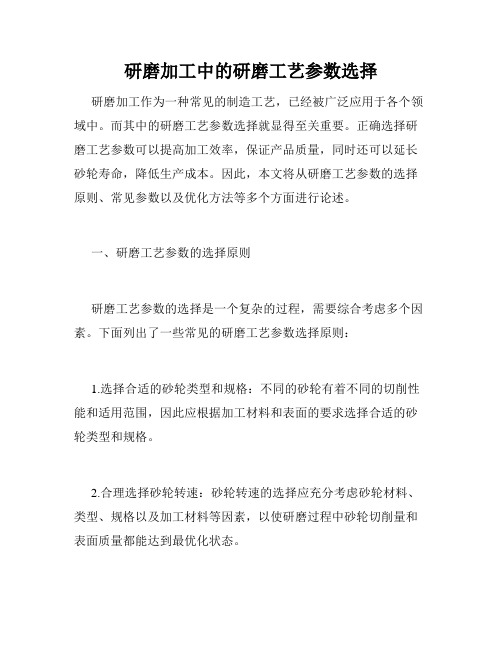
研磨加工中的研磨工艺参数选择研磨加工作为一种常见的制造工艺,已经被广泛应用于各个领域中。
而其中的研磨工艺参数选择就显得至关重要。
正确选择研磨工艺参数可以提高加工效率,保证产品质量,同时还可以延长砂轮寿命,降低生产成本。
因此,本文将从研磨工艺参数的选择原则、常见参数以及优化方法等多个方面进行论述。
一、研磨工艺参数的选择原则研磨工艺参数的选择是一个复杂的过程,需要综合考虑多个因素。
下面列出了一些常见的研磨工艺参数选择原则:1.选择合适的砂轮类型和规格:不同的砂轮有着不同的切削性能和适用范围,因此应根据加工材料和表面的要求选择合适的砂轮类型和规格。
2.合理选择砂轮转速:砂轮转速的选择应充分考虑砂轮材料、类型、规格以及加工材料等因素,以使研磨过程中砂轮切削量和表面质量都能达到最优化状态。
3.控制研磨深度:在控制研磨深度时,应考虑研磨加工的材料、硬度和粘结情况,以及加工后表面的粗糙度要求等因素。
4.合理选择工艺水平:研磨加工时,工艺水平的选择要符合实际情况和加工要求,以保证加工效率和表面质量。
二、研磨工艺参数的常见参数在实际生产中,研磨工艺参数主要包括砂轮种类、规格、转速、进给速度、深度和冷却液等。
下面分别介绍这些参数的选择原则和作用。
1.砂轮种类与规格:砂轮材料的选择应考虑研磨材料和表面质量要求。
常见的砂轮包括氧化铝砂轮、碳化硅砂轮、氮化硼砂轮等。
而砂轮规格的选择则应考虑砂轮的切削能力和性价比等因素。
2.砂轮转速:砂轮的转速是影响研磨深度、表面质量和砂轮寿命等关键参数之一。
砂轮转速过高会导致表面张力集中,砂轮易热软化、断裂等问题,而转速过低则会降低研磨效率。
因此,在选择砂轮转速时应综合考虑砂轮类型、规格、硬度、加工材料、表面质量等因素。
3.进给速度:进给速度的选择应根据研磨深度和表面光洁度等要求进行调整,以保障加工效率和表面质量。
4.研磨深度:研磨深度是研磨加工中一个关键的参数,合理的研磨深度不仅可以保证加工表面质量,还可以降低表面残余应力、改善材料组织等。
压铸原理及工艺参数选择
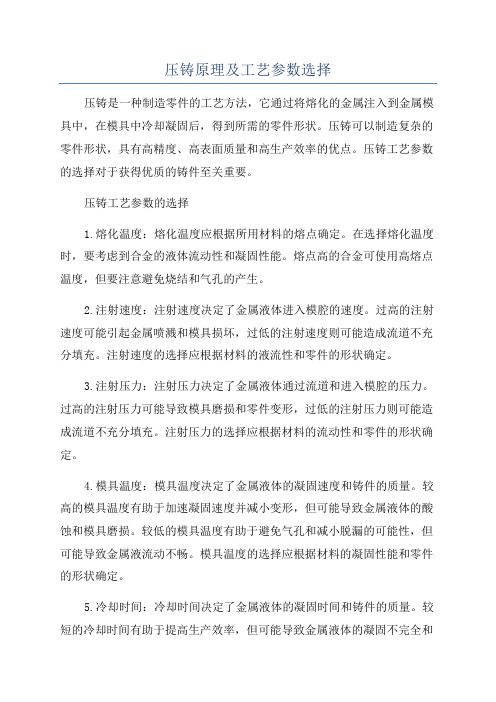
压铸原理及工艺参数选择压铸是一种制造零件的工艺方法,它通过将熔化的金属注入到金属模具中,在模具中冷却凝固后,得到所需的零件形状。
压铸可以制造复杂的零件形状,具有高精度、高表面质量和高生产效率的优点。
压铸工艺参数的选择对于获得优质的铸件至关重要。
压铸工艺参数的选择1.熔化温度:熔化温度应根据所用材料的熔点确定。
在选择熔化温度时,要考虑到合金的液体流动性和凝固性能。
熔点高的合金可使用高熔点温度,但要注意避免烧结和气孔的产生。
2.注射速度:注射速度决定了金属液体进入模腔的速度。
过高的注射速度可能引起金属喷溅和模具损坏,过低的注射速度则可能造成流道不充分填充。
注射速度的选择应根据材料的液流性和零件的形状确定。
3.注射压力:注射压力决定了金属液体通过流道和进入模腔的压力。
过高的注射压力可能导致模具磨损和零件变形,过低的注射压力则可能造成流道不充分填充。
注射压力的选择应根据材料的流动性和零件的形状确定。
4.模具温度:模具温度决定了金属液体的凝固速度和铸件的质量。
较高的模具温度有助于加速凝固速度并减小变形,但可能导致金属液体的酸蚀和模具磨损。
较低的模具温度有助于避免气孔和减小脱漏的可能性,但可能导致金属液流动不畅。
模具温度的选择应根据材料的凝固性能和零件的形状确定。
5.冷却时间:冷却时间决定了金属液体的凝固时间和铸件的质量。
较短的冷却时间有助于提高生产效率,但可能导致金属液体的凝固不完全和热裂纹的产生。
较长的冷却时间有助于提高铸件的密度和表面质量,但可能导致产量降低。
冷却时间的选择应根据材料的凝固性能和零件的形状确定。
总结压铸是一种高效、高精度的制造方法,工艺参数的选择对于获得优质的铸件至关重要。
在选择工艺参数时,要综合考虑材料的性质、零件的形状和制造要求,以及设备和模具的性能。
通过合理选择工艺参数,可以提高铸件的质量和生产效率,降低生产成本。
焊接工艺参数选择

焊接工艺参数的选择手工电弧焊的焊接工艺参数主要条直径、焊接电流、电弧电压、焊接层数、电源种类及极性等。
1.焊条直径焊条直径的选择主要取决于焊件厚度、接头形式、焊缝位置和焊接层次等因素。
在一般情况下,可根据表6-4按焊件厚度选择焊条直径,并倾向于选择较大直径的焊条。
另外,在平焊时,直径可大一些;立焊时,所用焊条直径不超过5mm;横焊和仰焊时,所用直径不超过4mm;开坡口多层焊接时,为了防止产生未焊透的缺陷,第一层焊缝宜采用直径为3.2mm的焊条。
表6-4 焊条直径与焊件厚度的关系mm焊件厚度≤23~45~12>12焊条直径23.24~5≥152.焊接电流焊接电流的过大或过小都会影响焊接质量,所以其选择应根据焊条的类型、直径、焊件的厚度、接头形式、焊缝空间位置等因素来考虑,其中焊条直径和焊缝空间位置最为关键。
在一般钢结构的焊接中,焊接电流大小与焊条直径关系可用以下经验公式进行试选:I=10d2 (6-1) 式中I ——焊接电流(A);d ——焊条直径(mm)。
另外,立焊时,电流应比平焊时小15%~20%;横焊和仰焊时,电流应比平焊电流小10%~15%。
3.电弧电压根据电源特性,由焊接电流决定相应的电弧电压。
此外,电弧电压还与电弧长有关。
电弧长则电弧电压高,电弧短则电弧电压低。
一般要求电弧长小于或等于焊条直径,即短弧焊。
在使用酸性焊条焊接时,为了预热部位或降低熔池温度,有时也将电弧稍微拉长进行焊接,即所谓的长弧焊。
4.焊接层数焊接层数应视焊件的厚度而定。
除薄板外,一般都采用多层焊。
焊接层数过少,每层焊缝的厚度过大,对焊缝金属的塑性有不利的影响。
施工中每层焊缝的厚度不应大于4~5mm。
5.电源种类及极性直流电源由于电弧稳定,飞溅小,焊接质量好,一般用在重要的焊接结构或厚板大刚度结构上。
其他情况下,应首先考虑交流电焊机。
根据焊条的形式和焊接特点的不同,利用电弧中的阳极温度比阴极高的特点,选用不同的极性来焊接各种不同的构件。
铰孔加工中的工艺参数
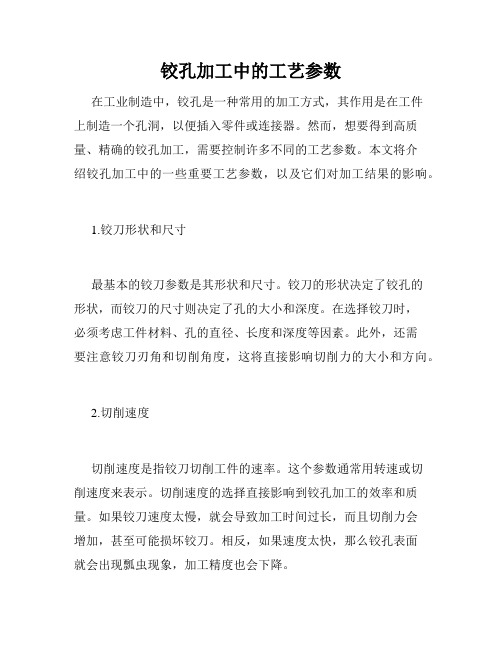
铰孔加工中的工艺参数在工业制造中,铰孔是一种常用的加工方式,其作用是在工件上制造一个孔洞,以便插入零件或连接器。
然而,想要得到高质量、精确的铰孔加工,需要控制许多不同的工艺参数。
本文将介绍铰孔加工中的一些重要工艺参数,以及它们对加工结果的影响。
1.铰刀形状和尺寸最基本的铰刀参数是其形状和尺寸。
铰刀的形状决定了铰孔的形状,而铰刀的尺寸则决定了孔的大小和深度。
在选择铰刀时,必须考虑工件材料、孔的直径、长度和深度等因素。
此外,还需要注意铰刀刃角和切削角度,这将直接影响切削力的大小和方向。
2.切削速度切削速度是指铰刀切削工件的速率。
这个参数通常用转速或切削速度来表示。
切削速度的选择直接影响到铰孔加工的效率和质量。
如果铰刀速度太慢,就会导致加工时间过长,而且切削力会增加,甚至可能损坏铰刀。
相反,如果速度太快,那么铰孔表面就会出现瓢虫现象,加工精度也会下降。
3.进给速度进给速度决定了铰刀在加工过程中每分钟进给的距离。
进给速度与切削速度一样重要,它对加工质量和效率都有影响。
如果进给速度太低,就会导致加工过程中铰孔表面不平滑,甚至出现切削刃痕。
另一方面,如果进给速度过高,则会导致铰刀磨损加速,加工过程中会产生过多的热量,甚至会损坏工件。
4.铰孔深度铰孔深度是铰孔加工的另一个重要参数。
在选择铰刀时,需要根据加工要求确定所需的孔深度,并确保铰孔的深度符合工程要求。
如果铰孔深度过浅,就会导致安装的零件不牢固,而深度过深则会加大工件成本和加工难度。
5.预冲长度预冲长度是指在实际切削铰孔之前,铰刀先在工件上移动的长度。
预冲长度的主要作用是使铰孔与工件表面完全接触,这有利于减少切削刃痕和杂散毛刺等不良现象。
预冲长度的选择应当依据工件材料、孔的直径和深度来确定,并参考铰刀的切削特性和工艺细节。
6.冷却液在铰孔加工过程中,冷却液的选择和使用也是至关重要的工艺参数。
冷却液通过冷却切削区域,降低加工温度,减少摩擦和磨损,并清洗切屑和切屑。
机械加工工艺参数

机械加工工艺参数机械加工是制造业中常用的一种加工方法,通过对原材料进行切削、磨削、铣削、钻削等工艺过程,使其获得所需的形状和尺寸。
而机械加工工艺参数对于加工过程的控制和结果的质量具有重要影响。
本文将介绍机械加工工艺参数的概念、分类以及在加工过程中的应用。
一、机械加工工艺参数的概念机械加工工艺参数是指在机械加工过程中,用于描述和控制加工操作的各项指标和参数。
这些参数包括加工速度、切削速度、进给量、切削深度等。
通过调整这些参数的数值,可以控制加工过程中的切削力、加工精度、加工效率等关键指标,从而达到所需的加工目标。
二、机械加工工艺参数的分类根据其影响的环节和作用特点,机械加工工艺参数可以分为以下几类:1. 切削参数:切削参数主要包括切削速度、进给速度、切削深度和切削宽度等。
切削速度是指刀具在单位时间内与工件接触的长度,通常以米/分钟或米/秒为单位。
进给速度是指切削过程中刀具与工件之间的相对运动速度,以毫米/转或毫米/分钟为单位。
切削深度和切削宽度则是指刀具在切削过程中对工件的切削厚度和宽度。
2. 配合参数:配合参数主要包括间隙、间距、配合角等。
在机械加工过程中,不同零件之间可能需要进行配合,而配合参数则用于描述和控制零件之间的配合关系。
例如,两个轴承的配合对于机械设备的正常运转至关重要。
3. 热处理参数:热处理参数主要包括加热温度、保温时间、冷却速度等。
在一些特殊材料或工件的加工过程中,往往需要对工件进行热处理以改变其性能和组织结构。
而热处理参数则决定了热处理的效果和结果。
三、机械加工工艺参数的应用机械加工工艺参数的合理选择和应用对于加工结果的质量和效率具有重要影响。
以下是机械加工工艺参数在实际应用中的一些注意事项:1. 需要根据具体加工材料和工件的特点来选择和调整工艺参数。
不同材料和工件对于工艺参数的要求有所不同,需要根据实际情况进行调整。
2. 在选择工艺参数时,需要综合考虑加工结果的质量和加工效率的要求。
波峰焊的主要工艺参数及对工艺参数的调整
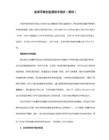
焊接时间=焊点与波峰的接触长度/传输速度
焊点与波峰的接触长度可以用一块带有刻度的耐高温玻璃测试板走一次波峰进行测量。
传输速度是影响产量的因素。在保证焊接质量的前提下,通过合理的综合调整各工艺参数,可以实现尽可能的提高产量的目的。
PCB类型
元器件
预热温度(℃)
中面板
纯THC或THC与SMD混装
90—100
双面板
纯THC
90—110
双面板
THC与SMD
100—110
多层板
纯THC
110—125
多层板
THC与SMD混装
110一130
波峰温度一般为250 ±5℃(必须测量打上来的实际波峰温度)。由于热量是温度和时间的函数,在一定温度下焊点和元件受热的热量随时间的增加而增加。波峰焊的焊接时间通过调整传送带的速度来控制,传送带的速度要根据不同型号波峰焊机的长度、预热温度、焊接温度等因素统筹考虑进行调整。以每个焊点,接触波峰的时间来表示焊接时间,—般焊接时间为3-4秒钟。
四、印制板爬坡角度和波峰高度
印制板爬坡角度为3—7℃。是通过调整波峰焊机传 输装置的倾斜角度来实现的。
适当的爬坡角度有利于排除残留在焊点和元件周 围由焊剂产生的气体,当THC与SMD混装时,由于通孔比较少,应适当加大印制板爬坡角度。通过调节倾斜角度还可以调整PCB与波峰的接触时间,倾斜角度越大,每个焊点接触波峰的时间越短,焊接时间就短;倾斜角度越小,每个焊点接触波峰的时间越长,焊接时间就长。适当加大印制板爬坡角度还有利于焊点与焊料波的剥离。当焊点离开波峰时,如果焊点与焊料波的剥离速度太慢,容易造成桥接。适当的波峰高度使焊料波对焊点增加压力和流速有利于焊料润湿金属表面、流入小孔,波峰高度一般控制在印制板厚度的2/3处。
压力容器制造工艺流程及主要工艺参数
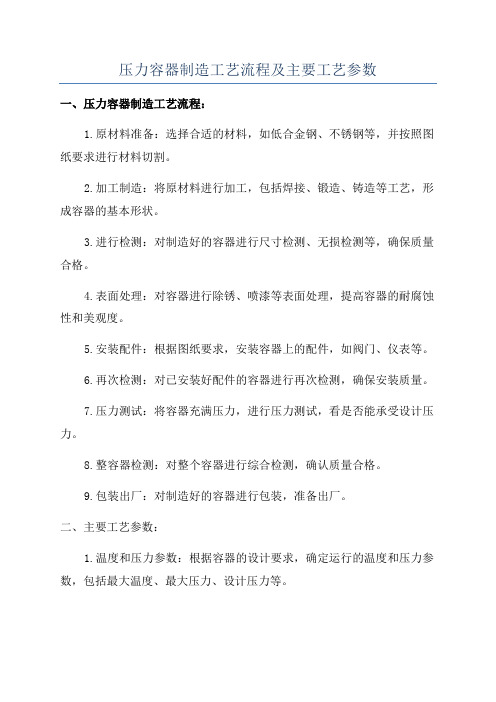
压力容器制造工艺流程及主要工艺参数一、压力容器制造工艺流程:1.原材料准备:选择合适的材料,如低合金钢、不锈钢等,并按照图纸要求进行材料切割。
2.加工制造:将原材料进行加工,包括焊接、锻造、铸造等工艺,形成容器的基本形状。
3.进行检测:对制造好的容器进行尺寸检测、无损检测等,确保质量合格。
4.表面处理:对容器进行除锈、喷漆等表面处理,提高容器的耐腐蚀性和美观度。
5.安装配件:根据图纸要求,安装容器上的配件,如阀门、仪表等。
6.再次检测:对已安装好配件的容器进行再次检测,确保安装质量。
7.压力测试:将容器充满压力,进行压力测试,看是否能承受设计压力。
8.整容器检测:对整个容器进行综合检测,确认质量合格。
9.包装出厂:对制造好的容器进行包装,准备出厂。
二、主要工艺参数:1.温度和压力参数:根据容器的设计要求,确定运行的温度和压力参数,包括最大温度、最大压力、设计压力等。
2.材料选择:根据容器的使用环境和介质特性,选择合适的材料,如低合金钢、不锈钢等。
3.容器尺寸:根据容器的设计要求,确定容器的尺寸,包括直径、高度、壁厚等。
4.焊接工艺参数:根据容器的材料和设计要求,确定焊接工艺参数,包括焊接电流、焊接电压、焊接速度等。
5.表面处理要求:根据容器的使用环境和要求,确定表面处理要求,包括除锈等。
6.配件安装要求:根据图纸要求,确定配件安装的位置、尺寸和固定方式等。
7.检测标准:确定容器的检测标准,包括尺寸检测标准、无损检测标准等。
以上是压力容器制造的工艺流程及主要工艺参数的简要介绍。
在实际制造过程中,还需要根据具体的项目和要求进行详细设计和操作,以确保压力容器的质量和安全性。
制造工艺中的工艺参数优化

制造工艺中的工艺参数优化制造工艺在各个行业中都扮演着重要的角色,它不仅关乎产品的质量和稳定性,还关系到生产效率和成本控制。
而在制造工艺中,工艺参数的选择和优化是至关重要的一环。
本文将重点探讨制造工艺中的工艺参数优化方法和相关应用。
一、工艺参数的含义和作用工艺参数是指在制造过程中可以被控制和调整的各项变量。
它们可能涉及到原材料的选择、加工条件的控制、设备参数的设定等等。
工艺参数的选择和优化将直接影响产品的质量、成本和生产效率。
因此,合理设置和优化工艺参数可以提高产品的品质,降低生产成本,提升生产效率。
二、工艺参数优化的方法工艺参数优化需要遵循一定的科学方法和步骤,下面将介绍几种常见的工艺参数优化方法。
1. 数据分析法数据分析法是一种基于实验数据的优化方法。
通过收集实际生产过程中的数据,进行统计和分析,找出工艺参数和产品性能之间的关联规律,并进行参数调整和优化。
这种方法的优点是简单易行,但需要大量的实验数据支持。
2. 数值模拟法数值模拟法是一种基于数学模型和计算机仿真的优化方法。
通过建立适当的模型和算法,模拟工艺过程中的各个环节,分析不同工艺参数对产品性能的影响,并进行参数优化。
这种方法的优点是准确性高,可以进行多种条件下的优化分析,但需要具备一定的计算机模拟和编程能力。
3. 试错法试错法是一种通过不断尝试和调整工艺参数,来找到最佳参数组合的优化方法。
通过实际操作和观察,逐步调整工艺参数的取值范围,找到最佳结果。
这种方法的优点是直观、实用,但需要较长的试验周期和大量的实验成本。
三、工艺参数优化的应用案例工艺参数优化方法在实际生产中有着广泛的应用。
以下是几个具体案例:1. 制造业中的材料选择在金属制造工艺中,不同材料的选择将直接影响产品的强度和韧性。
通过合理选择和优化材料的成分、工艺参数等,可以提高产品的品质和降低生产成本。
2. 电子制造中的工艺控制在电子制造工艺中,工艺参数的优化对产品的稳定性和可靠性至关重要。
- 1、下载文档前请自行甄别文档内容的完整性,平台不提供额外的编辑、内容补充、找答案等附加服务。
- 2、"仅部分预览"的文档,不可在线预览部分如存在完整性等问题,可反馈申请退款(可完整预览的文档不适用该条件!)。
- 3、如文档侵犯您的权益,请联系客服反馈,我们会尽快为您处理(人工客服工作时间:9:00-18:30)。
主要工艺参数作用及选择、均匀作用
.
(一)给棉刺辊部分
给棉刺辊部分各机构示意,其主要作用是喂棉、开松、除杂和排除短绒。
1.刺辊分梳作用及影响因素刺辊的分梳属于握持分梳武汉工作服,它与锡林部分的分梳不同,实质
维之f司得到混和。
在罗拉梳理机上,当锡林上一部分纤维转移到工作辊上时,由于工作辊表面速度比锡林慢.
先前分布在锡林较大面积上的纤维,转移凝聚到工作辊针面上,从而起到混和纤维的作用。
而
当工作辊上纤维层通过剥取辊的作用返回锡林时,又和锡林带到此处的纤维发生混和。
影响这
种混和作用的因素是_T作辊抓取纤维的能力,抓取得越多则混和作用越好。
还应指出,在罗拉
梳理机上,为了使前后喂人得纤维混和得更好,同一锡林上各工作辊的速度要有差异。
这是因
为如图4—12所示,当锡林带着纤维进入工作辊形武汉劳保服.的作用区时,其上的一部分纤维4被工作辊
肜-带走,余下的纤维日通过工作辊职时,其中一部分纤维c被工作辊哦带走,余下的纤维为
D。
若锡林上各工作辊直径及各剥取辊直径和速度相同,而各工作辊的速度也相同,那么,纤维
A和c回到锡林上时,正好重合,从而降低了均匀混和的效果。
因此,一般由喂入到输出的第一
个T作辊转速较高,随后逐个降低。
这样,未被充分梳理的纤维在第一工作辊针面上的负荷减
少,有利于分梳工作做得更完善。
若将正常运转的梳理机突然停喂。
可以发现输出的纤维网并不立即中
断,而是逐渐变细。
一般金属针布梳理时这种现象将持续几秒钟,弹性针布则更长些。
将变细的条子切断称重,便可得到如图4—13所示的曲线空白文化衫。
如果在条子变细的过程中恢
复喂给,条子也不会立即恢复到正常重量,而是逐渐变重,如图4—13所示的曲线7__6。
可
见在机台停止喂给和恢复喂给过程中,条子并不按图4一13所示的曲线1_2--3—4-5“
那样变化,而是按曲线l—2q-_6变化。
这表明在停止喂给时,针齿放出纤维,放出量为闭合曲线2—3—4-_7所围的面积。
在恢复喂给后,针齿吸收纤维,吸收量为闭合曲线5_-7__6 所围的面积。
这种针齿吸放纤维,缓和喂人量波动对输出量不匀影响的作用,称为梳理机的均匀作用。
广告衫。