对气压烧结碳化硅晶须增韧氧化铝基陶瓷刀具材料的研究
氧化锆增韧氧化铝陶瓷的研究进展

氧化铝陶瓷具有优良的化学稳定性、机械性能以及电性能,在陶瓷材料中属于应用十分广泛的类型,但是其断裂韧性仅在2.5MPa ·m 1/2~4.5MPa ·m 1/2,所以其应用范围的拓展受到严重限制,由此,提升氧化铝陶瓷的断裂韧性成为行业内的研究重点之一。
当前可以应用于其中的方法较多,主要包括引入第二相、加入Al 2O 3籽晶和形成缺陷分布三种方式,从整体上来看,应用价值最高的方式为氧化锆增韧,即采用机械混合法、溶胶-凝胶法等方式,将氧化锆复合于氧化铝粉体中,再进行相应的处理,可以获取氧化铝陶瓷,使氧化锆晶粒可填充与氧化铝晶界处,从而起到提升氧化铝陶瓷断裂韧性的作用,也就可以进一步提升氧化锆增韧氧化铝陶瓷的使用效果和使用价值。
氧化锆增韧氧化铝陶瓷也可被称为ZTA 陶瓷,其熔点高、硬度高,并且耐酸碱腐蚀,同时具有韧性较强的优势,属于高温结构陶瓷中具有较大应用潜力的一类。
其中的氧化锆含量在10%~20%之间时,可以起到抑制晶体生长氧化铝酸性的作用,也就可以起到提升材料硬度的作用。
特别是若氧化锆含量处于12%~14%之间时,ZTA 陶瓷的硬度和强度均能上升至最大值,如果氧化锆粉末含量为20%,并且其呈高度分散状态,经过热压烧结处理以后,ZTA陶瓷的机械性能将达到最好状态。
对陶瓷断裂韧性产生影响的因素可以通过公式(1)进行体现:(1)在公式(1)当中,为陶瓷材料断裂韧性,其与弹性模量E、泊松比v 以及断裂表面能均具有密切关联性,弹性模量以及泊松比均属于非显微结构敏感参数,所以需要借助提升断裂表面能的方式提升材料断裂韧性。
而能够影响陶瓷材料表面的因素较多,主要包括热力学自由表面能、内应力与裂纹、气孔、塑性形变、相变、晶粒尺寸等多个方面。
从断裂力学的视角来看,可以采用增加自由表面能的方式,促使新生表面形成,同时也可起到缩减晶粒尺寸、缩减气孔率的作用,还可应用适当的应力促进相变,并形成微裂纹,从而起到提升陶瓷材料断裂韧性的作用。
陶瓷基复合材料

陶瓷基复合材料论文2015年5月5日摘要:陶瓷基复合材料主要以高性能陶瓷为基体.通过加入颗粒、晶须、连续纤维和层状材料等增强体而形成的复合材料。
如碳化硅、氮化硅、氧化铝等,具有耐高温、耐腐蚀、高强度、重量轻和价格低等优点。
陶瓷基复合材料的研究还处于较初级阶段,我国对陶瓷基复合材料的研究则刚刚起步不久。
关键词:陶瓷基复合材料基体增强体强韧化机理制备技术前言:陶瓷基复合材料是以陶瓷为基体与各种纤维复合的一类复合材料。
陶瓷基体可为氮化硅、碳化硅等高温结构陶瓷。
这些先进陶瓷具有耐高温、高强度和刚度、相对重量较轻、抗腐蚀等优异性能,而其致命的弱点是具有脆性,处于应力状态时,会产生裂纹,甚至断裂导致材料失效。
而采用高强度、高弹性的纤维与基体复合,则是提高陶瓷韧性和可靠性的一个有效的方法。
纤维能阻止裂纹的扩展,从而得到有优良韧性的纤维增强陶瓷基复合材料。
陶瓷基复合材料具有优异的耐高温性能,主要用作高温及耐磨制品。
其最高使用温度主要取决于基体特征。
正文一、陶瓷基复合材料基本概述陶瓷基复合材料的基体为陶瓷。
如碳化硅、氮化硅、氧化铝等,具有耐高温、耐腐蚀、高强度、重量轻和价格低等优点。
化学键往往是介于离子键与共价键之间的混合键。
陶瓷基复合材料中的增强体通常也称为增韧体。
从几何尺寸上可分为纤维(长、短纤维)、晶须和颗粒三类。
碳纤维主要用在把强度、刚度、重量和抗化学性作为设计参数的构件;其它常用纤维是玻璃纤维和硼纤维。
纤维增强陶瓷基复合材料是改善陶瓷材料韧性的重要手段。
目前常用的晶须是SiC和A12O3,常用的基体则为A12O3,ZrO2,SiO2,Si3N4以及莫来石等。
晶须具有长径比,含量较高时,桥架效应使致密化困难,引起了密度的下降导致性能下降。
颗粒代替晶须在原料的混合均匀化及烧结致密化方面均比晶须增强陶瓷基复合材料要容易。
常用的颗粒也是SiC、Si3N4和A12O3等。
陶瓷基复合材料发展迟滞,发展过程中也遇到了比其它复合材料更大的困难。
国内外碳化硅陶瓷材料研究与应用进展
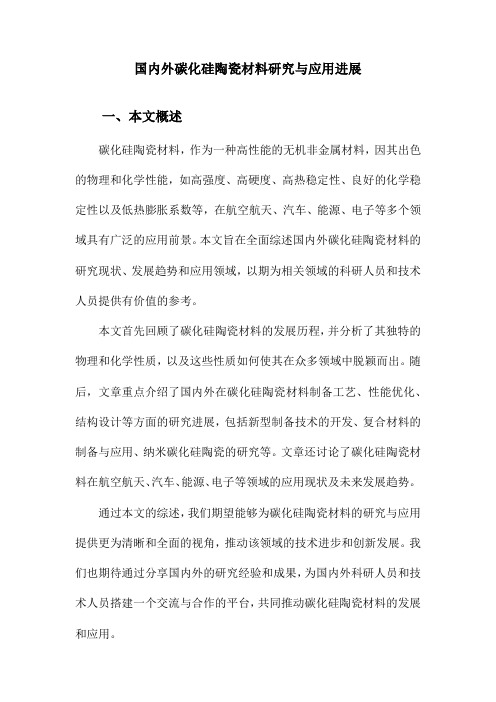
国内外碳化硅陶瓷材料研究与应用进展一、本文概述碳化硅陶瓷材料,作为一种高性能的无机非金属材料,因其出色的物理和化学性能,如高强度、高硬度、高热稳定性、良好的化学稳定性以及低热膨胀系数等,在航空航天、汽车、能源、电子等多个领域具有广泛的应用前景。
本文旨在全面综述国内外碳化硅陶瓷材料的研究现状、发展趋势和应用领域,以期为相关领域的科研人员和技术人员提供有价值的参考。
本文首先回顾了碳化硅陶瓷材料的发展历程,并分析了其独特的物理和化学性质,以及这些性质如何使其在众多领域中脱颖而出。
随后,文章重点介绍了国内外在碳化硅陶瓷材料制备工艺、性能优化、结构设计等方面的研究进展,包括新型制备技术的开发、复合材料的制备与应用、纳米碳化硅陶瓷的研究等。
文章还讨论了碳化硅陶瓷材料在航空航天、汽车、能源、电子等领域的应用现状及未来发展趋势。
通过本文的综述,我们期望能够为碳化硅陶瓷材料的研究与应用提供更为清晰和全面的视角,推动该领域的技术进步和创新发展。
我们也期待通过分享国内外的研究经验和成果,为国内外科研人员和技术人员搭建一个交流与合作的平台,共同推动碳化硅陶瓷材料的发展和应用。
二、碳化硅陶瓷材料的制备技术碳化硅陶瓷材料的制备技术是决定其性能和应用领域的关键因素。
经过多年的研究和发展,目前碳化硅陶瓷的主要制备技术包括反应烧结法、无压烧结法、热压烧结法、气相沉积法等。
反应烧结法:反应烧结法是一种通过碳和硅粉在高温下反应生成碳化硅的方法。
这种方法工艺简单,成本较低,但制备的碳化硅陶瓷材料致密度和性能相对较低,主要用于制备大尺寸、低成本的碳化硅制品。
无压烧结法:无压烧结法是在常压下,通过高温使碳化硅粉末颗粒之间发生固相反应,实现烧结致密化。
这种方法制备的碳化硅陶瓷材料具有较高的致密度和优良的力学性能,但烧结温度较高,时间较长。
热压烧结法:热压烧结法是在加压和高温条件下,使碳化硅粉末颗粒之间发生固相反应,实现快速烧结致密化。
这种方法制备的碳化硅陶瓷材料具有极高的致密度和优异的力学性能,但设备成本高,生产效率较低。
现代技术陶瓷发展论文

现代技术陶瓷发展论文陶瓷材料一般分为传统陶瓷和现代技术陶瓷两大类。
传统陶瓷是指用天然硅酸盐粉末(如黏土、高岭土等)为原料生产的产品。
因为原料的成分混杂和产品的性能波动大,仅用于餐具、日用容器、工艺品以及普通建筑材料(如地砖、水泥等),而不适用于工业用途。
现代技术陶瓷是根据所要求的产品性能,通过严格的成份和生产工艺控制而制造出来的高性能材料,主要用于高温和腐蚀介质环境,是现代材料科学发展最活跃的领域之一。
下面对现代技术陶瓷3个主要领域:结构陶瓷、陶瓷基复合材料和功能陶瓷作一简单介绍。
一、结构陶瓷同金属材料相比,陶瓷的最大优点是优异的高温机械性能、耐化学腐蚀、耐高温氧化、耐磨损、比重小(约为金属的1/3),因而在许多场合逐渐取代昂贵的超高合金钢或被应用到金属材料根本无法胜任的场合,如发动机气缸套、轴瓦、密封圈、陶瓷切削刀具等。
结构陶瓷可分为三大类:氧化物陶瓷、非氧化物陶瓷和玻璃陶瓷。
1、氧化物陶瓷主要包括氧化铝、氧化锆、莫来石和钛酸铝。
氧化物陶瓷最突出优点是不存在氧化问题,原料价格低廉,生产工艺简单。
氧化铝和氧化锆具有优异的室温机械性能,高硬度和耐化学腐蚀性,主要缺点是在1000℃以上高温蠕变速率高,机械性能显著降低。
氧化铝和氧化锆主要应用于陶瓷切削刀具、陶瓷磨料球、高温炉管、密封圈和玻璃熔化池内衬等。
莫来石室温强度属中等水平,但它在1400℃仍能保持这一强度水平,并且高温蠕变速率极低,因此被认为是陶瓷发动机的主要候选材料之一。
上述三种氧化物也可制成泡沫或纤维状用于高温保温材料。
钛酸铝陶瓷体内存在广泛的微裂纹,因而具有极低的热膨胀系数和热传导率。
它的主要缺点是强度低,无法单独作为受力元件,所以一般用它加工内衬用作保温、耐热冲击元件,并已在陶瓷发动机上得到应用。
2、非氧化物陶瓷主要包括碳化硅、氮化硅和赛龙(SIALON)。
同氧化物陶瓷不同,非氧化物陶瓷原子间主要是以共价键结合在一起,因而具有较高的硬度、模量、蠕变抗力,并且能把这些性能的大部分保持到高温,这是氧化物陶瓷无法比拟的。
氧化铝陶瓷刀具的研究与应用

高速加工技术论文氧化铝陶瓷刀具的研究与应用院系:燕山大学机械工程学院班级:11硕研机制系组长:明组员:指导老师:时间:2011年12月01日氧化铝陶瓷刀具的研究与应用摘要:作为先进制造技术,高速切削技术能大幅度地提高加工品质和加工效率,并能降低加工成本。
高速切削已经成为切削加工的主要发展方向。
为真正实现切削加工的高速化,不仅要研究开发与高速切削相适应的材料,还要不断改进刀具结构,并对刀具的动平衡和可靠性进行分析。
目前,国际上现已发展的陶瓷刀具主要是氧化铝基(Al2O3) 和氮化硅基( Si3N4) 两大系列。
陶瓷刀具具有很高的硬度、耐磨性能及良好的高温性能,与金属的亲合力小,并且化学稳定性好。
因此,陶瓷刀具可以加工传统刀具难以加工的高硬材料,实现以车代磨。
关键词:高速加工、氧化铝陶瓷刀具、高硬度、高耐磨性、抗高温1、陶瓷刀具的材料及选择陶瓷材料比硬质合金更适合于高速切削,陶瓷材料与金属亲合力小,热扩散磨损就很小。
另外,陶瓷的高温硬度优于硬质合金,在1200 ℃~1400℃时仍能达到HRA80,相当于硬质合金400℃以下的硬度。
氧化铝陶瓷硬度高、耐磨性好,但韧性不足,抗热振能力差,易于发生刃口早期破损。
通过加入ZrO2形成的相变增韧复合陶瓷Al2O3一ZrO2,和由具有高横向断裂强度的SiC晶须组成的晶须强化陶瓷Al2O3一SiC以及Al2O3一SiC+金属等Al2O3基陶瓷断裂韧性和强度有较大的提高,强了耐冲击和断续切削的能力,如Al2O3一ZrO2,能以1000m/mi的切削速度铣削硬度小于HRC38的钢件和HB300的铸铁件。
氮化硅(Si3N4)陶瓷具有较高的强度、韧性和抗热振能力,刀具耐用度显著提高,尤其提高了断续切削的可靠性。
通过在Si3N4基体添加YO、Al2O3和TiC(N)等形成的氮化硅系陶瓷,具有良好的烧结工艺性并能保持优良的切削性能。
近期开发的XE10是一种高强韧性的纤维状的高纯度高密度Si3N4陶瓷, 断裂韧性达7.0MPa²M1\2,热传导率比其它陶瓷高,2倍,抗热冲击性强,在铸铁的有冷却液高速断续切削中获得较高的刀具寿命。
氧化锆增韧氧化铝陶瓷的研究现状

19中国粉体工业 2021 No.2氧化锆增韧氧化铝陶瓷的研究现状国运之/文【摘要】由于氧化铝陶瓷具有耐磨、耐高温、耐酸碱、硬度高等特点,而且还具有优异的电性能和化学稳定性,故而氧化铝陶瓷材料也成为了一种应用最为广泛的陶瓷材料之一。
然而,由于氧化铝陶瓷存在断裂韧度差、脆性大的缺点,使其应用范围受到一定的限制。
而氧化锆具有好的断裂韧性,其可以通过相变增韧来提高材料的力学性能,于是研究者们提出用氧化锆增韧氧化铝陶瓷的思路,多年来也进行了实践并得到了广泛的应用。
【关键词】氧化锆;氧化铝陶瓷;增韧;ZTA;制备方法1.ZTA 陶瓷粉体的制备方法Al 2O 3陶瓷以其高强度、高硬度、高耐磨、抗氧化及抗热震等优异性能,在机械、电子、化工等领域得到广泛应用[1]。
纯Al 2O 3陶瓷的高温性能好,但韧性不足,抗冲击能力差,切削时易发生轻微崩刃,通过在Al 2O 3基体中添加增韧材料,可明显改善这一现象[2]。
在ZTA 陶瓷中,Al 2O 3基体上均匀弥散分布着ZrO 2粒子,随着温度的变化,ZrO 2粒子发生相变,这种相变属于马氏体相变,会相应的产生体积膨胀和切应变,导致张应力和微裂纹的形成。
某些小尺寸的ZrO 2粒子在张应力的作用下产生微裂纹,这些裂纹局限在小尺寸晶粒中,其萌生和扩展等都会消耗外应力场的能量,进而提高Al 2O 3陶瓷的韧性和强度[3,4]。
ZTA 陶瓷的制备工艺主要包括ZrO 2/Al 2O 3复合粉体的制备、坯体成型及烧结等工序。
要制备性能优异的氧化锆增韧氧化铝陶瓷,获得优质的ZrO 2/Al 2O 3复合粉体是重要前提[5]。
氧化锆增韧氧化铝陶瓷复合粉体的2.氧化锆增韧氧化铝陶瓷成型粉体的成型可分为干法成型和湿法成型。
干法成型又包括传统干压成型、等静压成型等[5]。
传统干压成型可使粉体成为一个较低密度素坯,也可压碎粉体间的软团聚,而等静压成型(常用的是冷等静压),它是以液体作为压力传递介质,素坯可以更加均匀的受压,冷等静压成型主要是为了使素坯获得更大的致密度,从而将坯体在高压下再次成型以得到密度高、气孔小、均匀性好的坯体。
碳化硅晶须氧化铝

碳化硅晶须氧化铝
碳化硅晶须氧化铝是一种新型的复合材料,由碳化硅晶须和氧化铝组成。
碳化硅晶须是一种具有高强度和高硬度的材料,而氧化铝则具有优异的导热性能和耐高温性能。
将这两种材料相结合,可以充分发挥各自的优势,提高材料的性能。
碳化硅晶须氧化铝在许多领域都有广泛的应用。
首先,在机械制造领域,碳化硅晶须氧化铝可以用于制造高速切削工具和陶瓷刀片。
由于碳化硅晶须具有高硬度和高强度,可以有效地提高切削效率和切削质量。
而氧化铝具有良好的导热性能,可以有效地降低切削温度,延长刀具的使用寿命。
碳化硅晶须氧化铝还可以应用于电子领域。
由于碳化硅晶须具有优异的导热性能,可以用于制造高功率电子器件的散热器。
同时,碳化硅晶须还具有良好的耐高温性能,可以在高温环境下稳定工作。
而氧化铝则可以提供良好的绝缘性能,保护电子器件的安全运行。
碳化硅晶须氧化铝还可以用于制造陶瓷复合材料。
由于碳化硅晶须具有高强度和高硬度,可以增加陶瓷材料的强度和硬度,提高抗压性能。
而氧化铝则可以填充陶瓷材料中的孔隙,提高材料的致密性和耐磨性。
碳化硅晶须氧化铝是一种具有广泛应用前景的新型复合材料。
它在机械制造、电子和陶瓷等领域都有重要的应用,可以提高材料的性
能和使用寿命。
随着技术的不断进步,碳化硅晶须氧化铝将会有更广阔的发展空间,为各个行业带来更多的创新和突破。
氧化锆增韧氧化铝复合陶瓷制备及性能研究
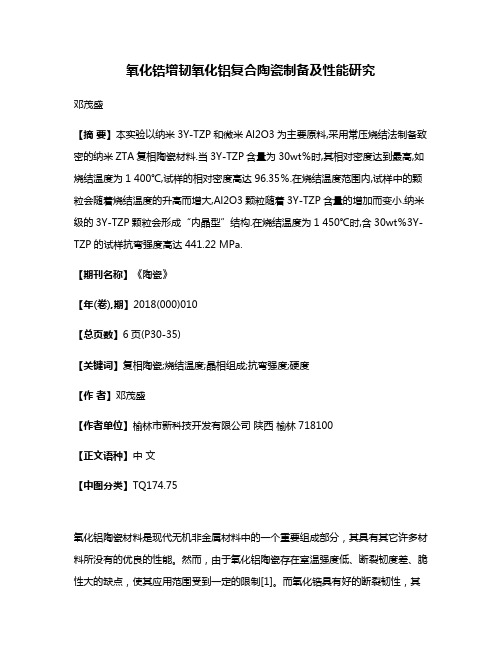
氧化锆增韧氧化铝复合陶瓷制备及性能研究邓茂盛【摘要】本实验以纳米3Y-TZP和微米Al2O3为主要原料,采用常压烧结法制备致密的纳米ZTA复相陶瓷材料.当3Y-TZP含量为30wt%时,其相对密度达到最高,如烧结温度为1 400℃,试样的相对密度高达96.35%.在烧结温度范围内,试样中的颗粒会随着烧结温度的升高而增大,Al2O3颗粒随着3Y-TZP含量的增加而变小.纳米级的3Y-TZP颗粒会形成“内晶型”结构.在烧结温度为1 450℃时,含30wt%3Y-TZP的试样抗弯强度高达441.22 MPa.【期刊名称】《陶瓷》【年(卷),期】2018(000)010【总页数】6页(P30-35)【关键词】复相陶瓷;烧结温度;晶相组成;抗弯强度;硬度【作者】邓茂盛【作者单位】榆林市新科技开发有限公司陕西榆林718100【正文语种】中文【中图分类】TQ174.75氧化铝陶瓷材料是现代无机非金属材料中的一个重要组成部分,其具有其它许多材料所没有的优良的性能。
然而,由于氧化铝陶瓷存在室温强度低、断裂韧度差、脆性大的缺点,使其应用范围受到一定的限制[1]。
而氧化锆具有好的断裂韧性,其可以通过相变增韧来提高材料的力学性能,人们根据此原因研制出氧化锆增韧氧化铝复合陶瓷[2]。
近年来,纳米复合材料的研究成为材料科学领域的一个热点,尤其是以氧化铝为基体的陶瓷[3]。
ZTA复相纳米陶瓷逐渐发展起来,利用相变增韧和第二相纳米颗粒增韧的叠加作用来改善Al2O3力学性能,被广泛应用于各项领域。
本研究是以纳米3Y-TZP和微米Al2O3为原料,采用液相烧结方式制备3Y-TZP/Al2O3复相陶瓷。
在最佳烧结条件下,研究不同含量的纳米3Y-TZP对3Y-TZP/Al2O3复相陶瓷的致密化、相组成、显微结构以及力学性能的影响,并对其复相陶瓷的增韧机理进行探讨。
1 实验内容1.1 实验原料实验所用的原料如表1所示。
表1 实验所用的原料表名称化学式生产厂家纯度八水氧氯化锆ZrOCl2·8H2O国药集团化学试剂有限公司分析纯,纯度≥99.0%六水硝酸钇Y(NO3)3·6H2O国药集团化学试剂有限公司分析纯,纯度≥99.0%二氧化钛TiO2国药集团化学试剂有限公司化学纯,纯度≥98.0%二氧化锰MnO2天津市福晨化学试剂厂分析纯,纯度≥85.0%氧化铝Al2O3浙江省乐清市超微细化工有限公司—无水乙醇C2H5OH国药集团化学试剂有限公司分析纯,纯度≥99.7%氨水NH3·H2O天津市福晨化学试剂厂分析纯,氨含量25%~28%聚乙二醇1000H(OCH2CH2)nOH国药集团化学试剂有限公司化学纯PVA[C2H4OCH]n自制5g/100ml去离子水H2O自制—1.2 试样的配方样品的编号采用以下方式:以组份中的质量百分比进行编号。
- 1、下载文档前请自行甄别文档内容的完整性,平台不提供额外的编辑、内容补充、找答案等附加服务。
- 2、"仅部分预览"的文档,不可在线预览部分如存在完整性等问题,可反馈申请退款(可完整预览的文档不适用该条件!)。
- 3、如文档侵犯您的权益,请联系客服反馈,我们会尽快为您处理(人工客服工作时间:9:00-18:30)。
文章编号:1000-2278(2001)03-0152-05对气压烧结碳化硅晶须增韧氧化铝基陶瓷刀具材料的研究金 健(重庆渝伦高技术陶瓷有限公司)摘 要本文介绍了用气压烧结S iC W 增韧Al 2O 3基陶瓷刀具的工艺,对气压烧结机理进行了分析,指出了气压法烧结S iC W 增韧Al 2O 3基陶瓷刀具材料在产业化生产中的优势与不足。
关键词 晶须增韧,复合陶瓷材料,气压烧结中图法分类号:T Q174.75+8 文献标识码:ARESEARCH ON GAS PRESSURE SINTERING OF SiC WREINFORCE D Al 2O 3CERAMIC INSERTSJin Jian(Chongqing Y u Lun High T echnology Ceramic MFG.C o.Ltd )AbstractThe process of gas pressure sintering (G PS )to produce SiC W reinforced Al 2O 3ceramic inserts is introduced.The mecha 2nism of G PS is analyzed.The advantage and disadvantage of G PS in production of SiC W reinforced Al 2O 3ceramic inserts are discussed.K eyw ords whisker reinforced ,ceramic com posites ,gas pressure sintering1 前 言尽管晶须增韧陶瓷刀具已进入商品化生产阶段,但国内外主要采用热压烧结后经切割加工的方法来制备,其制造成本较高,且难以达到产业化的规模。
我公司用气压法烧结的SiC W 增韧Al 2O 3基陶瓷刀具材料,其力学性能指标已达到或接近热压法生产的同类制品水平,在切削钛合金等难加工材料方面,已显示出比普通Al 2O 3-T iC N 、Si 3N 4基陶瓷刀具更为优越的切削加工性能。
目前国内外尚未见有类似的研究报道。
2 实验研究2.1 原材料Y 2O 3和T i (C N )粉:从德国H.C.Starck 公司购进,粉末平均粒径<0.5μm ;最大粒径<1μm 。
Al 2O 3粉:从美国C ondea Uista 公司购进,α-Al 2O 3>99%,粉末平均粒径<0.5μm ,0.7μm 以上<5%,比表面积:12-15m 2/g 。
收稿日期:2001-08-20作者简介:金 健,重庆渝伦高技术陶瓷有限公司,400041第22卷第3期2001年9月 陶瓷学报JOURNA L OF CERAMICSV ol.22,N o.3Sep.2001 SiC晶须:国内购买,其中β-SiC W≥92%;晶须直径率≥75%;晶须直径分布:≤0.4μm占10.8%,0.4-1μm占66%,1-1.2μm占23.2%。
晶须长度分布:≤10μm占10%,10-20μm占15%,20-30μm占28%,30 -50μm占46%。
SiC颗粒,游离C,Si等杂质约占2. 3%。
2.2 工艺过程本文所采用的工艺技术为气压烧结法(G PS),其主要工艺流程为:原料混合压制成型真空排胶高温气压烧结。
2.3 设备及检测仪器本文研究过程中使用了以下工艺和检测设备:PT A-1012型600W超声波清洗设备;QM-ISP行星式球磨机;M-18振动磨;VS D-12真空干燥器;DORST TPA15粉末压机;DB-1真空素烧窑;G PS-1500高温烧结窑;11AD-20平面打磨机;250PA-C NC 周边打磨机;250FS N-C NC韧口打磨机;样品抛光机;维氏硬度仪;PME-3光学显微镜;HHT-003激光衍射粒度分析仪;电子拉力机;X-ray衍射仪;扫描电镜等。
3 结果及讨论3.1 配方设计及优化晶须增韧陶瓷基复合材料的界面状态直接决定了其增韧机理,界面的组成、结构和结合状态对制品的性能有重大影响,因而在配方设计时,考虑引入适量的烧结助剂,以及添加第三相颗粒。
试验研究用配方的组表1 试验配方的原料配比(wt%)T able1 Batch ratio of experimental formula配方号组成及配比AS1086%Al2O3+10%S iC w+4%Y2O3AS2076%Al2O3+20%S iC w+4%Y2O3AS3066%Al2O3+30%S iC w+4%Y2O3ATS1060.2%Al2O3+19%S iC w+25.8%T iC N+4%Y2O3 ATS2053.2%Al2O3+20%S iC w+22.8%T iC N+4%Y2O3 ATS3046.2%Al2O3+30%S iC w+19.8%T iC N+4%Y2O3AS M74%Al2O3+20%S iC w+3%T iC N+3%M oATS M51.8%Al2O3+30%S iC w+22.2%T iC N+3%Y2O3+3%M o AS182%Al2O3+15%S iC w+2%Y2O3+1%T iO2ATS170%Al2O3+10%S iC w+1%Y2O3+1%T iO2+2%T iC N成如表1所示。
通过以上配方进行初步的实验及优化,发现晶须含量低于15wt%的材料,其增韧效果不明显,K IC约在5.5-6.5MPa.m1/2;当晶须含量高于30wt%时,其材料的烧结密度低,制品的相对密度低于93%,难以作为刀具制品使用。
本文对具有代表性的AS30及AST20两种配方进行了较深入的研究。
3.2 生产工艺技术的研究主要探讨了配料、压制和排胶与高温气压烧结工艺。
晶须在基体中的分散均匀程度直接影响到材料的致密化,如何克服晶须自身的团聚而导致局部成份的不均匀是分散工艺需要解决的主要任务。
通过对气压烧结后材料的相对密度及显微结构的观察,确定了较为有效的备料工艺。
成型时需要根据各种配方的特点来确定合适的压力参数,以尽量提高成型相对密度。
随着晶须含量的增加,成型制品的相对密度呈减少态势,这与晶须在坯体中的架桥效应及SiC w弹性模量较基体材料大有关(见表2)。
表2 粉料压制结果及坯体的相对密度T able2 P owder pressing result and relative density样品ATS10ATS20AS20AS30预置压坯相对密度%65.062.56360压坯弹性后效% 3.28 3.53 3.72 3.95坯体相对密度60.258.357.156.0图1 坯体排胶工艺曲线Fig.1 Binder rem oval technology curve 排胶工艺是为了使成型粘结剂在坯体内得到彻底清除,并不会因此引起产品的开裂,在真空状态下(≤15Pa)其升温制度如图1所示。
气压烧结过程可分为三个阶段:1200℃以下产品在真空状况下的加热;1200-1800℃区间内,填充约0. 5MPa的氩气保护气体;当烧结温度达到设定的最高烧结温度前开始加入8MPa的Ar气体,烧结按设定的程序完成后,烧结窑炉自动断电,停止加热,并随炉温自然冷却至室温。
研究表明:(1)气压烧结温度对坯体致密化有较大的影响,不同配方有相应的理想烧结温度范围。
(2)SiC w含量增加,给气压烧结致密化带来明显的抑制作用,除自身重排困难外,还会形成网状架桥结构,抑制着基体颗粒的重排与坯体的收缩。
(3)高压气体的加入,以对应配方最佳烧结温度前20-30℃时效果较好,可形成数量少且尺寸小的晶体,过早加入,则不利于制品致密度的提高,增大了开口气孔收缩、封闭和排除的阻力。
(4)在同等条件下,带孔制品如S NG A1204比实心制品S NG N1204更能获得高致密度的烧结体。
3.4 样品的力学性能表3列出了热压和气压烧结后材料的断裂韧性和显微硬度。
由于晶须的分布不同,其力学性能也是呈现各向异性的变化。
热压晶须增韧陶瓷材料中的晶须分布具有明显的空间取向,在垂直于热压方向的面呈二维随机分布,而在平行于热压方向的面内却很少存在,导致热压材料正面与侧面的力学性能差异较大,如表3所示。
而气压烧结后的材料在各个方向上材料的力学性能呈现各向同性。
3.5 气压烧结机理分析气压法烧结陶瓷坯体的驱动力来自两方面:首先是烧结前的坯体系统表面能总是处于较高的状态,在烧结过程中,系统将自发地转变为热力学更稳定的低表面能状态。
其次是系统的外在驱动力,它包括对系统的加热和加压。
为了便于具体讨论晶须增韧陶瓷材料在气压烧结过程中的有关情况,我们将气压烧结过表3 气压和热压烧结材料的力学性能对比T able3 C om paris on of mechanical properties between gas-pressed and hot-pressed sintered materials 项 目AT AS10AS20AS30ATS10ATS20ATS30气压K IC(MPa.m1/2) 5.50 6.507.007.50 6.25 6.707.00烧结H v(G Pa)20.5019.2021.0019.0020.0020.4520.70热压烧结K IC(MPa.m1/2) 4.75 5.50 6.60 6.70 6.40 6.807.00H v(G Pa)20.7020.0020.4220.6020.7021.0821.30表4 热压AS30及ATS30配方不同面上的力学性能T able4 Mechanical properties on different sur faces of hot-pressed AS30and ATS30SS 样品AS30ATS30测试面热压正面热压侧面热压正面热压侧面H v(G Pa)20.8018.5021.3018.90K IC(MPa.m1/2) 6.85 6.207.09 6.51程分为初、中、后期,这样划分只是根据不同烧结时期的主要特点近似描述它们发生的次序。
烧结初期气压炉内所加Ar 较少,通常在0.5MPa 以内,因此可认为坯体在此阶段的烧结发生类似于常压下的液相烧结的初期阶段。
对于含SiC w 的坯体,粉料颗粒在液相作用下相对移动时,晶须的架桥作用随着坯体收缩变得越来越严重,使粉体颗粒的重排受到阻碍或减慢直至停止。
这种现象随晶须所占的体积分数的增加而加剧。
烧结中期的特点是坯体在溶解———沉淀等传质机制下得到进一步致密化。
Al 2O 3或T iC N 不仅能被液相润湿而且能溶解于液相,并通过液相向周围扩散。
SiC w 不溶于液相,因此不会通过溶解———沉淀来传质,以纤维状存在的架桥仍会对基体溶解———沉淀产生的收缩起阻碍作用,进而影响到制品的致密化进程。