BGA焊盘设计的工艺性要求
BGA NSMD SMD

BGA NSMD/SMD于表贴封装元件的焊盘结构有两种(见图):阻焊层限定(Solder-Mask Defined,SMD)。
阻焊层开口小于金属焊盘。
电路板设计者定义形状代码、位置和焊盘的额定尺寸;焊盘开口的实际尺寸是由阻焊层制作者控制的。
阻焊层一般为LPI (可成像液体感光胶)的。
非阻焊层限定(Non-Solder-Mask Defined,NSMD)。
金属焊盘小于阻焊层开口。
在表层布线电路板的NSMD焊盘上,印刷电路导线的一部分将会受到焊锡的浸润。
焊盘的选择:阻焊层限定(SMD)与非阻焊层限定(NSMD)电路板设计者必需考虑到功率、接地和信号走向的要求在NSMD与SMD焊盘之间选择一种。
特殊的微过孔设计可能避免了表面走线,但是需要更先进的制板技术。
一旦选定,UCSP焊盘类型就不能混合使用。
焊盘和与其连接的导线的布局应该对称以防止偏离中心的浸润力。
选择UCSP焊盘类型时一些需要考虑的因素如下:蚀刻铜导线的过程能够得到更好的控制,与使用SMD焊盘时的阻焊层蚀刻相比,NSMD是更好的选择。
SMD焊盘可能使阻焊层交叠的地方产生压力的集中,这将导致压力过大时焊点破裂。
根据PCB上铜导线及其它空地的制作规则,NSMD焊盘可以给PCB上的布线提供更多的空间。
与SMD焊盘相比,NSMD更大的阻焊层开口为UCSP元件的贴放提供了更大的工作窗口。
SMD焊盘能够使用更宽的铜导线,在与电源和地层的连接中具有更低的电感。
Maxim在温度循环测试中使用NSMD设计。
一般地,假设NSMD PCB设计中的基底铜箔厚度为1/2或1 oz. NSMD圆形铜焊盘的直径为11 +0/-3 mils,其阻焊层开口为14 +1/-2 mils。
为了防止焊料流失,信号导线在与NSMD铜焊盘的连接处应该具有瓶颈形状,其宽度不超过与之连接的NSMD焊盘半径的1/2。
使用最小的4 mil - 5 mil导线宽度设计就能实现这一目标。
这种颈状导线与元件焊盘的连接应该是对称的以防止回流焊接时不平衡的浸润力造成元件的位移。
bga的良好焊接方法
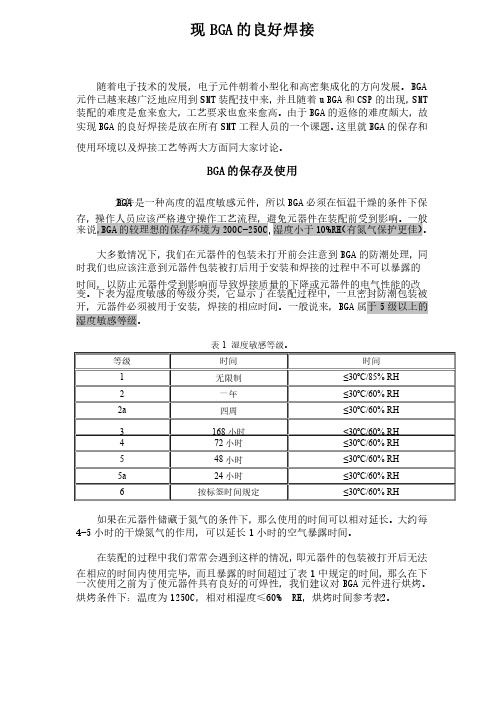
现BGA 的良好焊接随着电子技术的发展,电子元件朝着小型化和高密集成化的方向发展。
随着电子技术的发展,电子元件朝着小型化和高密集成化的方向发展。
BGA BGA 元件已越来越广泛地应用到SMT 装配技中来,并且随着u BGA 和CSP 的出现,SMT 装配的难度是愈来愈大,装配的难度是愈来愈大,工艺要求也愈来愈高。
工艺要求也愈来愈高。
工艺要求也愈来愈高。
由于由于BGA 的返修的难度颇大,的返修的难度颇大,故故实现BGA 的良好焊接是放在所有SMT 工程人员的一个课题。
这里就BGA 的保存和使用环境以及焊接工艺等两大方面同大家讨论。
使用环境以及焊接工艺等两大方面同大家讨论。
BGA 的保存及使用BGA 元件是一种高度的温度敏感元件,元件是一种高度的温度敏感元件,所以所以BGA 必须在恒温干燥的条件下保存,操作人员应该严格遵守操作工艺流程,操作人员应该严格遵守操作工艺流程,避免元器件在装配前受到影响。
避免元器件在装配前受到影响。
避免元器件在装配前受到影响。
一般一般来说,BGA 的较理想的保存环境为200C-250C,200C-250C,湿度小于湿度小于10%RH (有氮气保护更佳)。
大多数情况下,我们在元器件的包装未打开前会注意到BGA 的防潮处理,同时我们也应该注意到元器件包装被打后用于安装和焊接的过程中不可以暴露的时间,以防止元器件受到影响而导致焊接质量的下降或元器件的电气性能的改变。
下表为湿度敏感的等级分类,下表为湿度敏感的等级分类,它显示了在装配过程中,它显示了在装配过程中,它显示了在装配过程中,一旦密封防潮包装被一旦密封防潮包装被开,元器件必须被用于安装,焊接的相应时间。
一般说来,开,元器件必须被用于安装,焊接的相应时间。
一般说来,BGA BGA 属于5级以上的湿度敏感等级。
湿度敏感等级。
表1 湿度敏感等级。
湿度敏感等级。
等级 时间 时间 1 无限制 ≤30ºC/85% RH 2 一年 ≤30ºC/60% RH 2a 四周 ≤30ºC/60% RH 3168小时 ≤30ºC/60% RH 4 72小时 ≤30ºC/60% RH 5 48小时 ≤30ºC/60% RH 5a 24小时 ≤30ºC/60% RH 6按标签时间规定≤30ºC/60% RH如果在元器件储藏于氮气的条件下,那么使用的时间可以相对延长。
pcb板bga焊盘规则
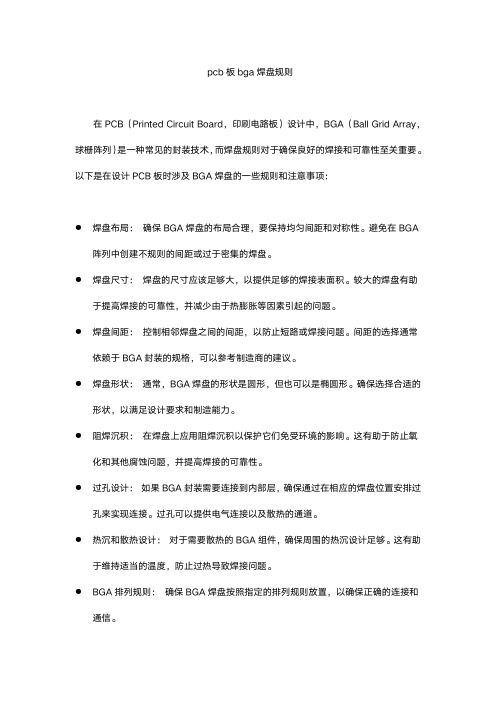
pcb板bga焊盘规则在PCB(Printed Circuit Board,印刷电路板)设计中,BGA(Ball Grid Array,球栅阵列)是一种常见的封装技术,而焊盘规则对于确保良好的焊接和可靠性至关重要。
以下是在设计PCB板时涉及BGA焊盘的一些规则和注意事项:●焊盘布局:确保BGA焊盘的布局合理,要保持均匀间距和对称性。
避免在BGA阵列中创建不规则的间距或过于密集的焊盘。
●焊盘尺寸:焊盘的尺寸应该足够大,以提供足够的焊接表面积。
较大的焊盘有助于提高焊接的可靠性,并减少由于热膨胀等因素引起的问题。
●焊盘间距:控制相邻焊盘之间的间距,以防止短路或焊接问题。
间距的选择通常依赖于BGA封装的规格,可以参考制造商的建议。
●焊盘形状:通常,BGA焊盘的形状是圆形,但也可以是椭圆形。
确保选择合适的形状,以满足设计要求和制造能力。
●阻焊沉积:在焊盘上应用阻焊沉积以保护它们免受环境的影响。
这有助于防止氧化和其他腐蚀问题,并提高焊接的可靠性。
●过孔设计:如果BGA封装需要连接到内部层,确保通过在相应的焊盘位置安排过孔来实现连接。
过孔可以提供电气连接以及散热的通道。
●热沉和散热设计:对于需要散热的BGA组件,确保周围的热沉设计足够。
这有助于维持适当的温度,防止过热导致焊接问题。
●BGA排列规则:确保BGA焊盘按照指定的排列规则放置,以确保正确的连接和通信。
检查制造商规范:仔细阅读BGA封装的制造商规范和建议,这通常包含有关焊盘设计和其他关键参数的详细信息。
在PCB设计中,BGA焊盘的设计需要综合考虑电气、热学和制造方面的因素。
与制造商的沟通以及使用专业的PCB设计工具可以帮助确保设计符合最佳实践和规格。
BGA焊盘设计的工艺性要求

BGA焊盘设计的工艺性要求(时间:2007-7-19 14:29:26 共有545 人次浏览)BGA焊盘设计的工艺性要求引言设计师们在电路组件选用BGA器件时将面对许多问题;印制板焊盘图形,制造成本,可加工性与最终产品的可靠性。
组装工程师们也会面对许多棘手问题是;有些精细间距BGA器件甚至至今尚未标准化,却已经得到普遍应用。
本文将要阐述是使用BGA器件时,与SMT组装工艺一些直接相关的主要问题(特别当球引脚阵列间距从1.27mm 减小到0.4mm),这些是设计师们必须清楚知道。
使用BGA封装技术取代周边引脚表贴器件,出自于为满足电路组件的组装空间与功能的要求。
例如周边引脚器件QFP,引脚从器件封装实体4条周边向外伸展。
这些引脚提供器件与PCB间的电路及机械的连接。
BGA器件的互连是通过器件封装底部的球状引脚实现的(如图1所示)。
球引脚可由共晶Pb/Sn合金或含90%Pb的高熔点材料制成。
图 1 从QFP至WS-CSP封装演变,芯片与封装尺寸越来越小。
一般BGA器件的球引脚间距为1.27mm(0.050″)—1.0mm(0.040″)。
小于1.0mm(0.040″) 精细间距, 0.4mm(0.016″)紧密封装器件已经应用。
这个尺寸表示封装体的尺寸已缩小到接近被封装的芯片大小。
封装体与芯片的面积比为1.2:1。
此项技术就是众所周知的芯片级封装(CSP)或称之为精细间距BGA(FBGA)。
芯片级封装的最新发展是晶圆规模的芯片级封装(WS-CSP),CSP的封装尺寸与芯片尺寸相同。
BGA封装的缺点是器件组装后无法对每个焊点进行检查,个别焊点缺陷不能进行返修。
有些问题在设计阶段已经显露出来。
随着封装尺寸的减少,制造过程的工艺窗口也随之缩小。
周边引脚器件封装已实现标准化,而BGA球引脚间距不断缩小,现行的技术规范受到了.限制,且没有完全实现标准化。
尤其精细间距BGA器件,使得在PCB布局布线设计方面明显受到更多的制约。
pcb焊盘设计规范
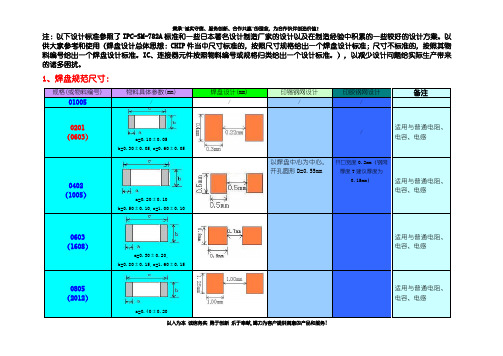
注:以下设计标准参照了IPC-SM-782A标准和一些日本著名设计制造厂家的设计以及在制造经验中积累的一些较好的设计方案。
以供大家参考和使用(焊盘设计总体思想:CHIP件当中尺寸标准的,按照尺寸规格给出一个焊盘设计标准;尺寸不标准的,按照其物料编号给出一个焊盘设计标准。
IC、连接器元件按照物料编号或规格归类给出一个设计标准。
),以减少设计问题给实际生产带来的诸多困扰。
1、焊盘规范尺寸:规格(或物料编号) 物料具体参数(mm) 焊盘设计(mm) 印锡钢网设计印胶钢网设计备注01005 / / / /0201(0603)a=0.10±0.05b=0.30±0.05,c=0.60±0.05 /适用与普通电阻、电容、电感0402(1005)a=0.20±0.10b=0.50±0.10,c=1.00±0.10 以焊盘中心为中心,开孔圆形D=0.55mm开口宽度0.2mm(钢网厚度T建议厚度为0.15mm)适用与普通电阻、电容、电感0603(1608)a=0.30±0.20,b=0.80±0.15,c=1.60±0.15 适用与普通电阻、电容、电感0805(2012)a=0.40±0.20 适用与普通电阻、电容、电感b=1.25±0.15,c=2.00±0.201206(3216)a=0.50±0.20b=1.60±0.15,c=3.20±0.20 适用与普通电阻、电容、电感1210(3225)a=0.50±0.20b=2.50±0.20,c=3.20±0.20 适用与普通电阻、电容、电感1812(4532)a=0.50±0.20b=3.20±0.20,c=4.50±0.20 适用与普通电阻、电容、电感2010(5025)a=0.60±0.20b=2.50±0.20,c=5.00±0.20 适用与普通电阻、电容、电感2512 (6432)适用与普通电阻、电容、电感a=0.60±0.20b=3.20±0.20,c=6.40±0.201:1开口,不避锡珠5700-250AA2-0300排阻0404(1010)a=0.25±0.10,b=1.00±0.10c=1.00±0.10,d=0.35±0.10p=0.65±0.05排阻0804(2010)a=0.25±0.10,b=2.00±0.10c=1.00±0.10,d=0.30±0.15p=0.50±0.05排阻1206(3216)a=0.30±0.15,b=3.2±0.15c=1.60±0.15,d=0.50±0.15p=0.80±0.10排阻1606(4016)a=0.25±0.10,b=4.00±0.20c=1.60±0.15,d=0.30±0.10p=0.50±0.05472X-R05240-10a=0.38±0.05,b=2.50±0.10c=1.00±0.10,d=0.20±0.05d1=0.40±0.05,p=0.50钽质电容适用于钽质电容1206 (3216) a=0.80±0.30,b=1.60±0.20 c=3.20±0.20,d=1.20±0.10 A=1.50,B=1.20,G=1.401411 (3528) a=0.80±0.30,b=2.80±0.20 c=3.50±0.20,d=2.20±0.10 A=1.50,B=2.20,G=1.702312 (6032) a=1.30±0.30,b=3.20±0.30 c=6.00±0.30,d=2.20±0.10 A=2.00,B=2.20,G=3.202917 (7243)a=1.30±0.30,b=4.30±0.30 c=7.20±0.30,d=2.40±0.10A=2.00,B=2.40,G=4.50铝质 电解 电容适用于铝质电解电容(Ø4×5.4)d=4.0±0.5 h=5.4±0.3a=1.8±0.2,b=4.3±0.2 c=4.3±0.2,e=0.5~0.8 p=1.0A=2.40,B=1.00 P=1.20,R=0.50(Ø5×5.4)d=5.0±0.5 h=5.4±0.3a=2.2±0.2,b=5.3±0.2 c=5.3±0.2,e=0.5~0.8 p=1.3A=2.80,B=1.00 P=1.50,R=0.50(Ø6.3×5.4) d=6.3±0.5 h=5.4±0.3a=2.6±0.2,b=6.6±0.2c=6.6±0.2,e=0.5~0.8 p=2.2A=3.20,B=1.00 P=2.40,R=0.50(Ø6.3×7.7) d=6.3±0.5 h=7.7±0.3a=2.6±0.2,b=6.6±0.2c=6.6±0.2,e=0.5~0.8p=2.2A=3.20,B=1.00P=2.40,R=0.50(Ø8.0×6.5) d=6.3±0.5 h=7.7±0.3a=3.0±0.2,b=8.3±0.2c=8.3±0.2,e=0.5~0.8p=2.2A=3.20,B=1.00P=2.40,R=0.50(Ø8×10.5) d=8.0±0.5 h=10.5±0.3a=3.0±0.2,b=8.3±0.2c=8.3±0.2,e=0.8~1.1p=3.1A=3.60,B=1.30P=3.30,R=0.65(Ø10×10.5) d=10.0±0.5 h=10.5±0.3a=3.5±0.2,b=10.3±0.2c=10.3±0.2,e=0.8~1.1p=4.6A=4.20,B=1.30P=4.80,R=0.65二极管(SMA)4500-234031-T04500-205100-T0a=1.20±0.30b=2.60±0.30,c=4.30±0.30d=1.45±0.20,e=5.2±0.30二极管(SOD-323)4500-141482-T0a=0.30±0.10b=1.30±0.10,c=1.70±0.10d=0.30±0.05,e=2.50±0.20二极管(3515)a=0.30b=1.50±0.1,c=3.50±0.20二极管(5025)a=0.55b=2.50±0.10, c=5.00±0.20三极管(SOT-523)a=0.40±0.10,b=0.80±0.05c=1.60±0.10,d=0.25±0.05p=1.00三极管(SOT-23)a=0.55±0.15,b=1.30±0.10c=2.90±0.10,d=0.40±0.10p=1.90±0.10SOT-25a=0.60±0.20,b=2.90±0.20c=1.60±0.20,d=0.45±0.10p=1.90±0.10SOT-26a=0.60±0.20,b=2.90±0.20c=1.60±0.20,d=0.45±0.10p=0.95±0.05SOT-223a1=1.75±0.25,a2=1.5±0.25b=6.50±0.20,c=3.50±0.20d1=0.70±0.1,d2=3.00±0.1p=2.30±0.05SOT-89a1=1.0±0.20,a2=0.6±0.20b=2.50±0.20,c=4.50±0.20d1=0.4±0.10,d2=0.5±0.10d3=1.65±0.20,p=1.5±0.05TO-252a1=1.1±0.2,a2=0.9±0.1b=6.6±0.20,c=6.1±0.20d1=5.0±0.2,d2=Max1.0e=9.70±0.70,p=2.30±0.10TO-263-2a1=1.30±0.1,a2=2.55±0.25b=9.97±0.32,c=9.15±0.50d1=1.3±0.10,d2=0.75±0.24e=15.25±0.50,p=2.54±0.10TO-263-3a1=1.30±0.1,a2=2.55±0.25b=9.97±0.32,c=9.15±0.50d1=1.3±0.10,d2=0.75±0.24e=15.25±0.50,p=2.54±0.10TO-263-5a1=1.66±0.1,a2=2.54±0.20b=10.03±0.15,c=8.40±0.20d=0.81±0.10,e=15.34±0.2p=1.70±0.10SOP(引脚(Pitch>0.65mm)A=a+1.0,B=d+0.1G=e-2*(0.4+a)P=pSOP(Pitch≦0.65mm)A=a+0.7,B=dG=e-2*(0.4+a)P=pSOJ(Pitch≧0.8mm)A=1.8mm,B=d2+0.10mmG=g-1.0mm,P=pQFP(Pitch≧0.65mm)A=a+1.0,B=d+0.05P=pG1=e1-2*(0.4+a)G2=e2-2*(0.4+a)QFP(Pitch=0.5mm)A=a+0.9,B=0.25mmP=pG1=e1-2*(0.4+a)G2=e2-2*(0.4+a)QFP(Pitch=0.4mm)A=a+0.8,B=0.19mmP=pG1=e1-2*(0.4+a)G2=e2-2*(0.4+a) 引脚长由原来的a+0.70mm更改为a+0.80mm,有利于修理和印刷拉尖的处理。
BGA焊盘设计的工艺性要求
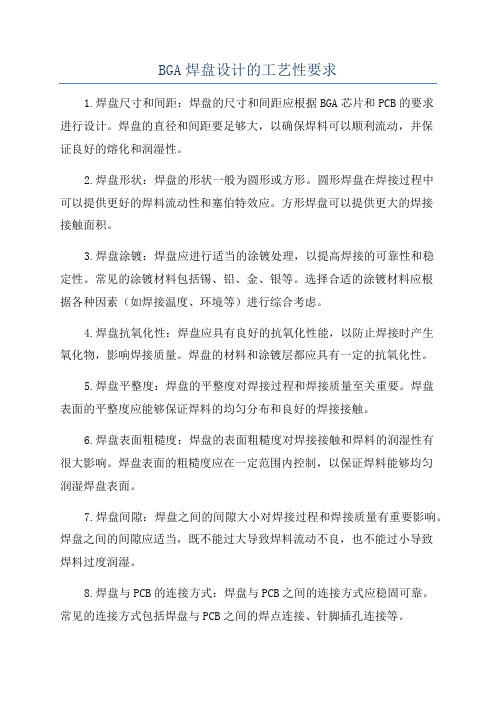
BGA焊盘设计的工艺性要求1.焊盘尺寸和间距:焊盘的尺寸和间距应根据BGA芯片和PCB的要求进行设计。
焊盘的直径和间距要足够大,以确保焊料可以顺利流动,并保证良好的熔化和润湿性。
2.焊盘形状:焊盘的形状一般为圆形或方形。
圆形焊盘在焊接过程中可以提供更好的焊料流动性和塞伯特效应。
方形焊盘可以提供更大的焊接接触面积。
3.焊盘涂镀:焊盘应进行适当的涂镀处理,以提高焊接的可靠性和稳定性。
常见的涂镀材料包括锡、铅、金、银等。
选择合适的涂镀材料应根据各种因素(如焊接温度、环境等)进行综合考虑。
4.焊盘抗氧化性:焊盘应具有良好的抗氧化性能,以防止焊接时产生氧化物,影响焊接质量。
焊盘的材料和涂镀层都应具有一定的抗氧化性。
5.焊盘平整度:焊盘的平整度对焊接过程和焊接质量至关重要。
焊盘表面的平整度应能够保证焊料的均匀分布和良好的焊接接触。
6.焊盘表面粗糙度:焊盘的表面粗糙度对焊接接触和焊料的润湿性有很大影响。
焊盘表面的粗糙度应在一定范围内控制,以保证焊料能够均匀润湿焊盘表面。
7.焊盘间隙:焊盘之间的间隙大小对焊接过程和焊接质量有重要影响。
焊盘之间的间隙应适当,既不能过大导致焊料流动不良,也不能过小导致焊料过度润湿。
8.焊盘与PCB的连接方式:焊盘与PCB之间的连接方式应稳固可靠。
常见的连接方式包括焊盘与PCB之间的焊点连接、针脚插孔连接等。
9.焊料选用:焊盘的设计还需要考虑焊料的选用。
常用的焊料有焊锡、无铅焊锡等。
根据焊盘材料和焊接要求,选择合适的焊料材料可以提高焊接质量和可靠性。
总之,BGA焊盘设计的工艺性要求包括焊盘尺寸和间距、焊盘形状、焊盘涂镀、焊盘抗氧化性、焊盘平整度、焊盘表面粗糙度、焊盘间隙、焊盘与PCB的连接方式以及焊料选用等。
这些要求能够确保BGA焊盘设计的可靠性、稳定性和良好的焊接质量。
BGA焊盘设计经验

1◆BGA规格◆BGA设计不良易引起的品质异常◆BGA设计建议目录BGA焊盘设计经验交流2IPC-7095A 中BGA 规格19.0527mmmmmm4.50mmmm。
4.50mm绿油开窗13◆BGA 焊盘可焊性不良,造成虚焊◆BGA 桥连,引起连焊◆BGA 焊盘大小不一致◆BGA 焊点脆性断裂◆激光钻孔未在PAD 中间,造成盲孔崩孔◆……BGA 品质异常分析BGA 设计不良易引起的品质异常:14◆引起BGA 焊盘可焊性不良的原因:1.绿油开窗比BGA 焊盘小2.BGA 焊盘过小3.白字上BGA 焊盘4.BGA 焊盘盲孔未填平5.内层埋孔未填孔……BGA 品质异常分析15定义焊盘大小的两种方式:BGA品质异常分析PAD定义焊盘大小绿油开窗定义焊盘大小通断测试针痕19◆引起桥连,导致连焊的原因:BGA PAD与PAD 间没有保留绿油桥,易导致连焊;狗骨形BGA 易导致漏锡.此设计容易造成焊接连焊,导致短路。
BGA品质异常分析建议保留绿油桥。
201.BGA焊盘与大铜面连在一起2.BGA焊盘与盲孔焊盘相连BGA焊盘与大铜面、盲孔焊盘相连,因绿油开窗按盘开上大铜面及邻近盲孔焊盘,使得实际的焊盘会比正常的大,引起BGA焊盘大小不一致。
3.BGA区域图形分布不均匀BGA区域图形分布不均匀,PCB制作的过程中药水交换能力不一样,引起BGA焊盘大小不一致。
BGA品质异常分析◆引起BGA焊盘大小不一致的原因:21◆引起BGA 焊点脆性断裂的原因:BGA 品质异常分析对于BGA PAD SIZE ≤18mil ,并且BGA 的尺寸>2cm 的沉金板件或沉银板件,因焊点接触面积小,抗应力弱等因素,容易引起BGA 焊点脆性断裂。
但是有激光钻孔的板件,表面处理不能采用喷锡,否则会出现盲孔露铜的品质异常。
而且OSP 表面处理不适用于按键等区域。
建议,组装工艺采用封胶工艺,防止此异常发生.23THE END !谢谢!汕头超声印制板公司技术开发部2007-11-20期望通过与贵司的密切沟通与交流:从CAD 设计到CAM 设计、PCB 制造上消除BGA 设计不良引起的品质异常风险,确保我司与贵司合作的顺利开展和成功!24返回生产样板绿油开窗尺寸>PAD 尺寸保留有绿油桥通断测试针痕图1返回返回。
bga焊盘设计标准
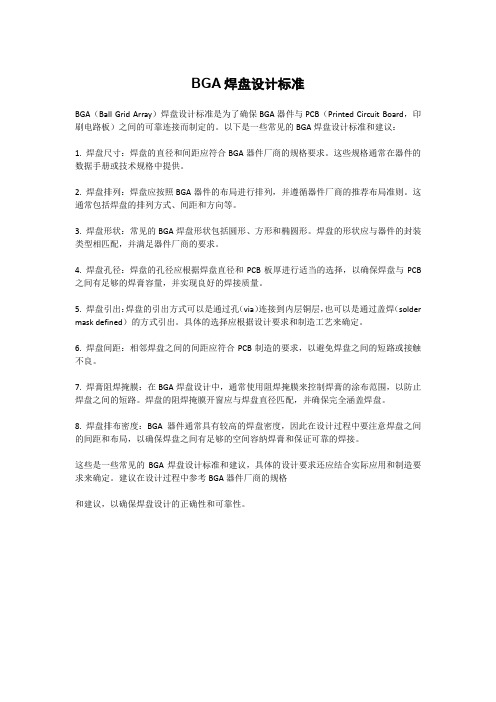
BGA焊盘设计标准BGA(Ball Grid Array)焊盘设计标准是为了确保BGA器件与PCB(Printed Circuit Board,印刷电路板)之间的可靠连接而制定的。
以下是一些常见的BGA焊盘设计标准和建议:1. 焊盘尺寸:焊盘的直径和间距应符合BGA器件厂商的规格要求。
这些规格通常在器件的数据手册或技术规格中提供。
2. 焊盘排列:焊盘应按照BGA器件的布局进行排列,并遵循器件厂商的推荐布局准则。
这通常包括焊盘的排列方式、间距和方向等。
3. 焊盘形状:常见的BGA焊盘形状包括圆形、方形和椭圆形。
焊盘的形状应与器件的封装类型相匹配,并满足器件厂商的要求。
4. 焊盘孔径:焊盘的孔径应根据焊盘直径和PCB板厚进行适当的选择,以确保焊盘与PCB 之间有足够的焊膏容量,并实现良好的焊接质量。
5. 焊盘引出:焊盘的引出方式可以是通过孔(via)连接到内层铜层,也可以是通过盖焊(solder mask defined)的方式引出。
具体的选择应根据设计要求和制造工艺来确定。
6. 焊盘间距:相邻焊盘之间的间距应符合PCB制造的要求,以避免焊盘之间的短路或接触不良。
7. 焊膏阻焊掩膜:在BGA焊盘设计中,通常使用阻焊掩膜来控制焊膏的涂布范围,以防止焊盘之间的短路。
焊盘的阻焊掩膜开窗应与焊盘直径匹配,并确保完全涵盖焊盘。
8. 焊盘排布密度:BGA器件通常具有较高的焊盘密度,因此在设计过程中要注意焊盘之间的间距和布局,以确保焊盘之间有足够的空间容纳焊膏和保证可靠的焊接。
这些是一些常见的BGA焊盘设计标准和建议,具体的设计要求还应结合实际应用和制造要求来确定。
建议在设计过程中参考BGA器件厂商的规格和建议,以确保焊盘设计的正确性和可靠性。
- 1、下载文档前请自行甄别文档内容的完整性,平台不提供额外的编辑、内容补充、找答案等附加服务。
- 2、"仅部分预览"的文档,不可在线预览部分如存在完整性等问题,可反馈申请退款(可完整预览的文档不适用该条件!)。
- 3、如文档侵犯您的权益,请联系客服反馈,我们会尽快为您处理(人工客服工作时间:9:00-18:30)。
BGA焊盘设计的工艺性要求引言设计师们在电路组件选用BGA器件时将面对许多问题;印制板焊盘图形,制造成本,可加工性与最终产品的可靠性。
组装工程师们也会面对许多棘手问题是;有些精细间距BGA器件甚至至今尚未标准化,却已经得到普遍应用。
本文将要阐述是使用BGA器件时,与SMT组装工艺一些直接相关的主要问题(特别当球引脚阵列间距从1.27mm减小到0.4mm),这些是设计师们必须清楚知道。
使用BGA封装技术取代周边引脚表贴器件,出自于为满足电路组件的组装空间与功能的要求。
例如周边引脚器件QFP,引脚从器件封装实体4条周边向外伸展。
这些引脚提供器件与PCB间的电路及机械的连接。
BGA器件的互连是通过器件封装底部的球状引脚实现的(如图1所示)。
球引脚可由共晶Pb/Sn合金或含90%Pb的高熔点材料制成。
图 1 从QFP至WS-CSP封装演变,芯片与封装尺寸越来越小。
一般BGA器件的球引脚间距为1.27mm(0.050″)―1.0mm(0.040″)。
小于1.0mm(0.040″) 精细间距, 0.4mm(0.016″)紧密封装器件已经应用。
这个尺寸表示封装体的尺寸已缩小到接近被封装的芯片大小。
封装体与芯片的面积比为1.2:1。
此项技术就是众所周知的芯片级封装(CSP)或称之为精细间距BGA (F BGA)。
芯片级封装的最新发展是晶圆规模的芯片级封装(WS-CSP),CSP的封装尺寸与芯片尺寸相同。
BGA封装的缺点是器件组装后无法对每个焊点进行检查,个别焊点缺陷不能进行返修。
有些问题在设计阶段已经显露出来。
随着封装尺寸的减少,制造过程的工艺窗口也随之缩小。
周边引脚器件封装已实现标准化,而BGA球引脚间距不断缩小,现行的技术规范受到了.限制,且没有完全实现标准化。
尤其精细间距BGA器件,使得在PCB布局布线设计方面明显受到更多的制约。
综上所述,设计师们必须保证所选用的器件封装形式能够SMT组装的工艺性要求相适应。
通常,制造商会对某些专用器件提供BGA印制板焊盘设计参数,于是设计师只能照搬,使用没有完全成熟的技术。
当BGA器件尺寸与间距减小,产品的成本趋于增高,这是加工与产品制造技术高成本的结果。
设计师必须对制造成本,可加工性与可靠性进行巧妙处理。
为了支持BGA器件的基本物理结构,必须采用先进的PCB设计与制造技术。
信号线布线原先是从器件周边走线,现应改为从器件底部下面PCB的空闲部分走线,这球引脚间距大的BGA器件并不是难题,球引脚阵列的行列间有足够的信号线布线空间。
但对球引脚间距小的BGA器件,球引脚间内部信号只能使用更窄的导线布线(图2)。
图 2 板面走线的焊盘图形设计阵列最外边行列球引脚间的空间很快被走线塞满。
导线的最小线宽与间距是由电性能要求与加工能力决定,所以这种布线设计的导线数量是有限制的。
为解决导线与线距问题,可以结合其他一些设计方法,其中包括狗骨通孔焊,通孔焊盘图形设计(图 3 / 图4)图 3 狗骨通孔,通孔焊盘图形图 4 狗骨通孔,通孔焊盘截面图示狗骨通孔图形的导线走向连接空孔或印制板直通孔。
通孔镀复导电层,提供与内层布线连接构成通路。
另一种变形的狗骨通孔图形是通孔焊盘图形,从印制板顶面与第二层或第三层钻孔相通,镀复导电层构成通路,这两种图形的连线方法使得信号直接由焊盘与内层相连接。
看起来这种图形连接方法简单,却直接受到加工能力,制造成本与组装工艺等因素的制约。
上述讨论的导线与线距问题,并非所有制造商都有能力解决这些设计问题。
PCB上的电学与非电特征图形的位置配准成为关键要素,包括制造工艺的可靠性。
例如;阻焊膜层的对准是极其重要的,阻焊层不能超出设计要求而侵入焊盘图形,大尺寸面积PCB板的阻焊膜层对准难度增加,也驱动了制造成本的升高。
表 1 概括PCB狗骨通孔/通孔焊盘图形设计的比较;设计狗骨通孔通孔焊盘使用类型球引脚间距≥0.75mm 球引脚间距≤0.75mm优点宽间距大尺寸BGA减少互连层数激光钻孔,制造过程可靠性变化缺点通孔成形加工与PCB厚度,及通孔直径/孔高比相关成本中等,当器件尺寸小,PCB厚度增加时,成高等,小批量加工需要技术与能力本提高限制性受印制板厚度,焊盘间的间距空间限于1-2层PCB制造产能优良,图形细节可靠稳定清晰,依赖于激光打孔与电镀工艺的精度组装因素返工――通孔与焊盘间的连线可靠如通孔形装太圆,一般会增加空隙焊接可靠性优良,技术成熟,工艺参数控制适宜,一些未知因素表1狗骨通孔/通孔焊盘设计的比较印制板SMT组装工艺PCB组装工艺直接或间接受到BGA器件,及BGA贴装随之带来印制板设计要素变化的影响。
使用先进BGA 器件需要采用更为复杂的组装技术。
这些组装技术能经受过程优化,例如焊膏印刷模板设计必许满足焊膏转印量的一致性要求。
如贴装设备的视觉系统不能胜任BGA球引脚阵列器件贴装要求,SMT组装设备需要更新升级,。
有关BGA器件SMT组装流程的一些特定要素,设计师能够影响的范围在表2中概括列示;SMT组装工序设计影响程度设计减轻措施焊膏印刷直接制造商与组装厂间相互协调设计合理的BGA焊盘图形设计工艺产能直接尽可能选用大引脚间距的封装器件共面性受限制尽可能选用大直径球引脚封装器件检查受限制尽可能选用高支承高度的封装器件返工直接制造商与组装厂间相互协调提供合适的空间,不纳入技术条件测试受限制无装载/传送直接BGA安装位置偏离PCB边沿或高应力区表 2 设计对BGA工艺的影响l 焊膏模板印刷当使用精细间距BGA器件,PCB连接BGA器件球引脚的焊盘尺寸(或BGA封装基板焊盘)也随之减小。
BGA器件焊膏印刷模板窗口尺寸,一般采用与PCB焊盘大约1:1的尺寸比。
PCB使用小的间距与焊盘,模板窗口尺寸也随之减小。
模板窗口形态比(窗口宽度与孔厚比或窗口面积与孔壁面积比)表示印刷过程焊膏脱模的能力。
对于一个给定厚度的模板而言,存在一个临界窗口开孔尺寸(或窗口形态比),低于此值,焊膏将部分脱模,或全部不能脱模。
因此当BGA焊盘减小,模板设计变得更加关键。
设计师应与制造商及组装厂相互协调决定合适的解决方法,防止潜在的危险。
l 工艺产能使用精细间距BGA器件,组装工艺的优化成为关键。
发展可靠的组装工艺是工艺窗口缩小的最大需要。
在大批量组装生产中,精细BGA器件的数量有限,BGA的产能期望值没有被表征。
间距≥1.0mm的BGA器件已有许多数据,这些器件的数据分析表明组装工艺优化的结果是优良的,甚至要比其他SMT引脚器件更好。
重要的是应该意识到有些贴装设备没有能力贴装精细间距BGA器件,因为这些设备视觉系统的软件与硬件不能正确对准球引脚,直接影响组装的产能。
在允许的范围内,应尽可能选用最大间距的BGA器件封装,以提高获得最高产能的可能性。
而且最大BGA封装尺寸,最大焊点尺寸将具有优良的焊接可靠性,且较容易进行检查。
l 共面性由于封装‘超差’,BGA器件的球引脚的变量很大,这样在组装过程可能造成共面性问题;在球引脚阵列中,若某个球引脚尺寸要比其他球引脚小很多,此引脚就不可能形成正确的焊点,结果在再流焊后导致开路。
这类缺陷可使用X射线检测系统被检查出来,整个器件需要返修,此类问题单靠设计改善,则也难以避免。
l 焊后检查BGA器件焊后检查是很困难的,特别是BGA器件阵列的内行列的球引脚焊点是无法视觉观察到的,有些工具可检查BGA器件再流焊后的焊点,但可见视场有限。
透射X射线检查与分层X射线检测技术用于检查BGA焊点,相对直接视觉观察检查方法,使用这种方法采集的数据信息就容易很,但是在SMT生产现场快速分析器件焊点缺陷也存在一定困难。
随着器件封装尺寸的减小,检查的难度也随之增加。
l 返工与返修BGA器件的返工与返修需要专用设备,才能保证拆除与更新器件的一致性。
大多数返工与返修的操作使用热风对器件局部加热到焊料熔解温度的方法,使用小型BGA器件,器件间的排列间距缩小,以及器件本身的几何尺寸减小成为一个重要问题。
必须仔细保证需要返修的器件加热,相邻与镜像位置的器件需要受到保护。
其后,当新器件重新贴装到位,在再流时应小心,防止突然将器件从PCB上被吹落。
l 测试缺少BGA器件内行列球引脚的通路,阻碍了器件测试的完全复盖面。
用于测试的IC T测试夹具对组件焊点施加应力,造成焊点早期缺陷。
l 装载/传送BGA器件的小尺寸,由于在组装过程的不正确装载/传送使其更容易受到损坏。
即使焊点坚固,但也容易受到损伤。
在组装过程从一道工序转移到另一道工序,PCB板的柔软性也会对焊点施加应力。
PCB布局设计时,应将BGA器件的贴装位置偏离PCB边沿与高应力区域。
带散热凸台BGA的焊接问题研究带散热凸台的BGA是一种新近出现的BGA封装形式,其特点是在BGA封装的底部中间位置(芯部)加有一个散热的铜块,主要用于高功耗器件的封装,如图1所示。
由于它目前还没有统一的名称,在本文中我们将其称为Slug-BGA。
由于底部散热凸台的支撑作用,在焊接过程中,Slug- BGA封装体相对于一般的P BGA不能自由的伸缩,冷却时会产生较大的应力,位于边缘处的焊点很容易拉裂,如图2所示。
一般BGA的焊接过程BGA的焊接与一般器件的焊接有所不同,存在两个特殊的热过程:两次塌落与热变形。
: 两次塌落BGA焊接时,先是焊膏熔化并塌落,然后焊球熔化并二次塌落。
许多的试验证明,只有发生二次塌落,BGA 才能实现自动校准和焊膏焊球成分的融合,这就需要合适的温度与焊接时间。
: 热变形对BGA来说,焊接加热时总是BGA表面先被加热,接下来是封装体被加热,最后才是焊点被加热并最终熔化,冷却时则相反。
这样的加热过程必然导致升温时BGA的顶部比底部温度高,因而向上弓曲,冷却时,则是顶部比底部的温度低,因而四角上翘,如图3所示。
也就是BGA进行回流焊接时存在一个热胀冷缩的变形过程。
由于BGA器件的I/O端是以焊球形式存在并布局在封装体的底部,在焊接过程中,封装体的形变必然影响到焊点的形成过程,特别是BGA的周边焊点。
这两次的变形都发生在温度变化比较快的阶段,不管上弓还是四角上翘,他们都发生在焊接过程中。
对一般的P BGA而言,焊接完成后BGA会基本恢复到焊接前的状态,也就是封装体仍然会基本平整。
但对Slug-BGA而言,由于其芯部存在散热凸台,冷却时芯部不能自由收缩,焊接完成后热变形不能完全恢复;焊点,特别是靠近BGA四边的焊点就会存在一些应力。
如果焊接时,BGA封装体还没有完全达到热平衡状态就转入冷却阶段,这时的应力就会很大,在冷却时有可能使焊点发生断裂。
Slug-BGA的焊接问题Slug-BGA焊接时容易发生两个问题:一是焊接温度不够,达不到二次塌落的温度。
这样,焊点在凝固时焊球仍处于半固半液的“糊状”形态,焊点很容易发生断裂。