TUST_Guidelines for tunnelling risk management-隧道风险管理指南-2004
Guidelinesforcor...
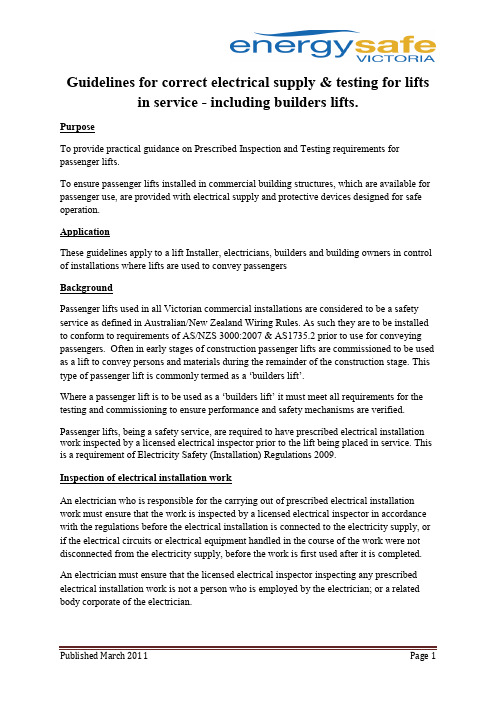
Guidelines for correct electrical supply & testing for lifts in service - including builders lifts.PurposeTo provide practical guidance on Prescribed Inspection and Testing requirements for passenger lifts.To ensure passenger lifts installed in commercial building structures, which are available for passenger use, are provided with electrical supply and protective devices designed for safe operation.ApplicationThese guidelines apply to a lift Installer, electricians, builders and building owners in control of installations where lifts are used to convey passengersBackgroundPassenger lifts used in all Victorian commercial installations are considered to be a safety service as defined in Australian/New Zealand Wiring Rules. As such they are to be installed to conform to requirements of AS/NZS 3000:2007 & AS1735.2 prior to use for conveying passengers. Often in early stages of construction passenger lifts are commissioned to be used as a lift to convey persons and materials during the remainder of the construction stage. This type of passenger lift is commonly termed as a ‘builders lift’.Where a passenger lift is to be used as a ‘builders lift’ it must meet all requirements for the testing and commissioning to ensure performance and safety mechanisms are verified. Passenger lifts, being a safety service, are required to have prescribed electrical installation work inspected by a licensed electrical inspector prior to the lift being placed in service. This is a requirement of Electricity Safety (Installation) Regulations 2009.Inspection of electrical installation workAn electrician who is responsible for the carrying out of prescribed electrical installation work must ensure that the work is inspected by a licensed electrical inspector in accordance with the regulations before the electrical installation is connected to the electricity supply, or if the electrical circuits or electrical equipment handled in the course of the work were not disconnected from the electricity supply, before the work is first used after it is completed. An electrician must ensure that the licensed electrical inspector inspecting any prescribed electrical installation work is not a person who is employed by the electrician; or a related body corporate of the electrician.Energy Safe Victoria requirementsThe passenger lift shall pass all requirements of the Prescribed Inspection before handover for use.Recommended items to be inspected for verification∙All mains and sub mains cables from the point of supply through to the lift switchboard associated with the lift installation to ensure appropriate WS rating is provided∙Basic protection (protection against direct contact with live parts), e.g. insulation and enclosure∙Fault protection (protection against indirect contact with exposed conductive parts)∙Protection against hazardous parts, e.g. enclosure, guarding or screening of flammable materials, hot surfaces and parts that may cause physical injury∙Protection against spread of fire, e.g. penetration of fire barriers∙Motor room door installation and labelling∙General condition of the electrical equipment, e.g. signs of damage that could impair safe operation, disconnection of unused electrical equipmentMains∙Identification of cable cores∙Current carrying capacity of mains∙Voltage drop, e.g. size and length of conductors and load∙Underground installation conditions, e.g. enclosure, depth of burial, mechanical protection∙Connection of wiring∙Protection against external influencesSwitchboards∙Location, e.g. access and egress, not in restricted location∙Protective devices, e.g. selection and setting of adjustable protective devices for compliance with over current protection, arc fault protection and discrimination∙Isolating devices, e.g. main switches∙Connecting devices, e.g. neutral bars, earth bars and active links∙Connection and fixing of wiring and switchgear∙Identification and labelling of electrical equipment, and∙Protection against external influences, e.g. mechanical damageDefinitionsLicensed Electrical Inspector means a person holding an inspector's licence underthe Electricity Safety (Installations) Regulations 2009Passenger lift in this document means an electrically controlled lift that is capable of conveying passengers, but does not include a lift installed in a single private residence in accordance with AS1735.18Safety service has the same meaning as it has in the Australian/New Zealand Wiring Rules AS/NZS 3000:2007Prescribed electrical installation work. For the purposes of Electricity Safety Act 1998 section 45, prescribed electrical installation work means work on all or part of any of the following electrical installations if they are ordinarily operated at low voltage or a voltage exceeding low voltage— circuit protective devices, switchgear, control gear, wiring systems and accessories (other than fire detection and alarm systems) installed to provide control and protection of passenger liftsVerification— All measures by means of which compliance of the electrical installation with the relevant requirements of AS/NZS 3000 and AS/NZS3017:2000 is checked. Further informationElectricity Safety Act 1998Electricity Safety (Installation) Regulations 1999Acts & Regulations are available from Information Victoria on 1 300 366 366 or order on line at .au. They can be viewed by visiting the ESV web site at .auAustralian/New Zealand Wiring Rules means AS/NZS 3000, Australian/New Zealand Standard, "Electrical installations", as published or amended from time to timeAS/NZS 3017:2000 means AS/NZS 3017:2000, Australian/New Zealand Standard, Electrical installations – Verification guidelinesAS1735.2 means AS1735.2, Australian/New Zealand Standard, "Lifts, escalators and moving walks – General requirements", as published or amendedfrom time to timeStandards Australia publications can be obtained by contacting Standards Australia on 1 300 654 646 or by visiting the web site at .auThis guidance material has been prepared using current and best information available to Energy Safe Victoria. You should check the legislation referred to in this document and make your own judgement about what action you need to undertake to ensure compliance with the law.。
特殊性质药品的污染控制丁之章1赵汝萍2
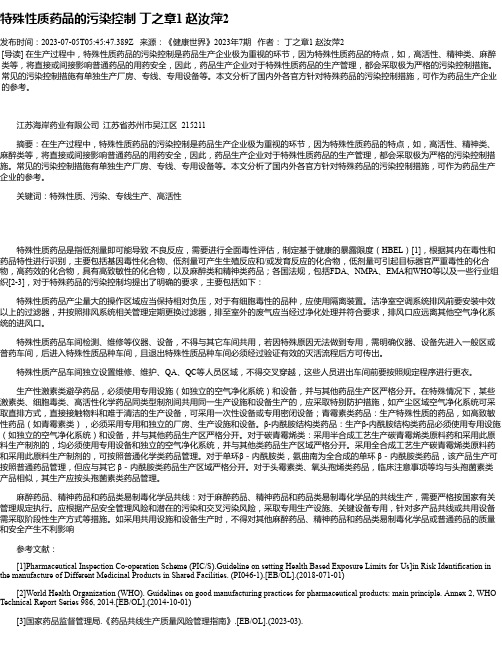
特殊性质药品的污染控制丁之章1 赵汝萍2发布时间:2023-07-05T05:45:47.389Z 来源:《健康世界》2023年7期作者:丁之章1 赵汝萍2 [导读] 在生产过程中,特殊性质药品的污染控制是药品生产企业极为重视的环节,因为特殊性质药品的特点,如,高活性、精神类、麻醉类等,将直接或间接影响普通药品的用药安全,因此,药品生产企业对于特殊性质药品的生产管理,都会采取极为严格的污染控制措施。
常见的污染控制措施有单独生产厂房、专线、专用设备等。
本文分析了国内外各官方针对特殊药品的污染控制措施,可作为药品生产企业的参考。
江苏海岸药业有限公司江苏省苏州市吴江区 215211摘要:在生产过程中,特殊性质药品的污染控制是药品生产企业极为重视的环节,因为特殊性质药品的特点,如,高活性、精神类、麻醉类等,将直接或间接影响普通药品的用药安全,因此,药品生产企业对于特殊性质药品的生产管理,都会采取极为严格的污染控制措施。
常见的污染控制措施有单独生产厂房、专线、专用设备等。
本文分析了国内外各官方针对特殊药品的污染控制措施,可作为药品生产企业的参考。
关键词:特殊性质、污染、专线生产、高活性特殊性质药品是指低剂量即可能导致不良反应,需要进行全面毒性评估,制定基于健康的暴露限度(HBEL)[1],根据其内在毒性和药品特性进行识别,主要包括基因毒性化合物、低剂量可产生生殖反应和/或发育反应的化合物,低剂量可引起目标器官严重毒性的化合物,高药效的化合物,具有高致敏性的化合物,以及麻醉类和精神类药品;各国法规,包括FDA、NMPA、EMA和WHO等以及一些行业组织[2-3],对于特殊药品的污染控制均提出了明确的要求,主要包括如下:特殊性质药品产尘量大的操作区域应当保持相对负压,对于有细胞毒性的品种,应使用隔离装置。
洁净室空调系统排风前要安装中效以上的过滤器,并按照排风系统相关管理定期更换过滤器,排至室外的废气应当经过净化处理并符合要求,排风口应远离其他空气净化系统的进风口。
Guideline_Normothermia
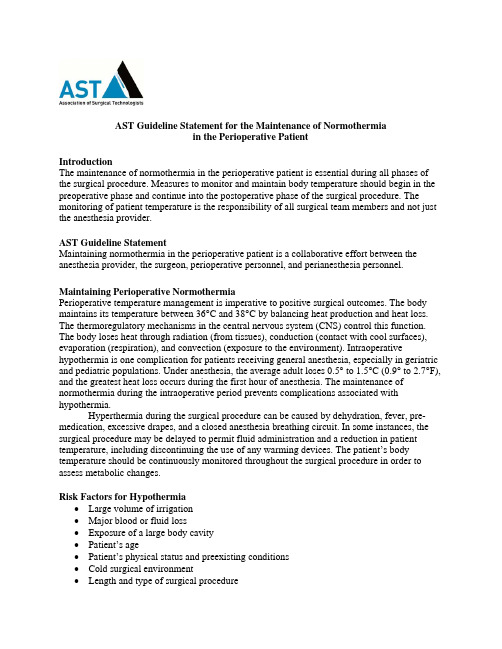
AST Guideline Statement for the Maintenance of Normothermiain the Perioperative PatientIntroductionThe maintenance of normothermia in the perioperative patient is essential during all phases of the surgical procedure. Measures to monitor and maintain body temperature should begin in the preoperative phase and continue into the postoperative phase of the surgical procedure. The monitoring of patient temperature is the responsibility of all surgical team members and not just the anesthesia provider.AST Guideline StatementMaintaining normothermia in the perioperative patient is a collaborative effort between the anesthesia provider, the surgeon, perioperative personnel, and perianesthesia personnel. Maintaining Perioperative NormothermiaPerioperative temperature management is imperative to positive surgical outcomes. The body maintains its temperature between 36°C and 38°C by balancing heat production and heat loss. The thermoregulatory mechanisms in the central nervous system (CNS) control this function. The body loses heat through radiation (from tissues), conduction (contact with cool surfaces), evaporation (respiration), and convection (exposure to the environment). Intraoperative hypothermia is one complication for patients receiving general anesthesia, especially in geriatric and pediatric populations. Under anesthesia, the average adult loses 0.5° to 1.5°C (0.9° to 2.7°F), and the greatest heat loss occurs during the first hour of anesthesia. The maintenance of normothermia during the intraoperative period prevents complications associated with hypothermia.Hyperthermia during the surgical procedure can be caused by dehydration, fever, pre-medication, excessive drapes, and a closed anesthesia breathing circuit. In some instances, the surgical procedure may be delayed to permit fluid administration and a reduction in patient temperature, including discontinuing the use of any warming devices. The patient’s body temperature should be continuously monitored throughout the surgical procedure in order to assess metabolic changes.Risk Factors for Hypothermia∙Large volume of irrigation∙Major blood or fluid loss∙Exposure of a large body cavity∙Patient’s age∙Patient’s physical status and preexisting conditions∙Cold surgical environment∙Length and type of surgical procedure∙Type of anesthesiaComplications Associated with Hypothermia∙Coagulopathy∙Altered metabolism, ie metabolic acidosis∙Wound infections∙Shivering∙Cardiovascular effects∙Surgical bleedingExample Protocol for Preventing Hypothermia in the Surgical Patient1.Limit the amount of skin exposed during all phases of the surgical procedure.Suggestions: Surgical team members coordinate efforts to keep patient covered andwarm during the preoperative and postoperative phases with the use of warm blankets or warming devices.2.Monitor patient’s temperature during all phases of the surgical procedure.Suggestions: This is primarily a role of the anesthesia provider, but the circulating CSTor surgical assistant can provide assistance in monitoring the patient’s temperature bychecking the temperature surface monitor that is placed on the patient’s forehead.e warmed irrigation and infusion fluids/solutions.Suggestions: The CST and surgical assistant should use irrigation fluids obtained fromthe blanket and solution warmer located in the substerile room.e of warmed anesthetic gasesSuggestions: The anesthesia provider is responsible for this function.5.Monitor operating room temperature and humidity closely.Suggestions: The CST and surgical assistant should follow established recommendations for temperature and humidity levels in the operating room, and periodically check andrecord these levels for each operating room.6.Utilize heat-maintenance devices (head coverings, leggings, forced-air warming systems,hypothermia/hyperthermia mattress, reflective blankets/head coverings, radiant heatsources).Suggestions: The CST and surgical assistant should know the proper procedures foroperating warming devices and the safety protocol associated with the use of any type of warming device as established by hospital policy and manufacturer’s recommendations.Competency StatementsCompetency Statement Measurable Criteria1. Surgical technologists and surgical assistants are qualified to identify potential complications, associated with hypothermia and hyperthermia in the perioperative environment, and appropriate interventions for treatment. 1. Educational standards as established by the Core Curriculum for Surgical Technology.12. The subject areas of normothermia, hyperthermia and hypothermia are included in the didactic studies as a student.3. The proper use of thermoregulatory methods and devices is included in the didactic studies as a student.4. Students demonstrate the proper application of thermoregulatory methods during clinical rotation, including the proper use and operation of thermoregulatory devices, and are evaluated by preceptors and instructors.5. CSTs and surgical assistants perform patient care duties by applying thermoregulatory methods and devices in the perioperative setting as practitioners.6. CSTs and surgical assistants identify potential patient complications associated with the use of thermoregulatory methods and devices in the perioperative setting as practitioners, including contributing to the decision-making process of proper interventions to treat hyperthermia and hypothermia.7. CSTs and surgical assistants complete continuing education to remain current in their knowledge of hyperthermia, hypothermia, and maintenance of normothermia for the surgical patient.DefinitionsCore Temperature: A temperature of the interior of the body, ranging from 36.8° to 37.7°C (98° to 100°F)Normothermia: A core temperature range of 36°C to 38°C (96.8°F to 100.4°F) Hypothermia: A core temperature less than 36°C (96.8°F)Hyperthermia: A core temperature greater than 38°C (100.4°F)Unplanned perioperative hypothermia: An unexpected core temperature decrease to less than 36°C (96.8° F) as a result of surgeryReferences1.Core Curriculum for Surgical Technology. 5th ed. Littleton, CO: Association ofSurgical Technologists; 2002.2.DeFazio-Quinn DM, Schick L, eds. PeriAnesthesia Nursing Core Curriculum:Preoperative, Phase I and Phase II PACU Nursing. St Louis, MO: WB Saunders;2004.3.Drain CB. Perianesthesia Nursing: A Critical Care Approach. 4th ed.St Loui,MO: WB Saunders; 2003.4.Meeker M, Rothrock J, eds. Alexander’s Care of the Patient in Surgery. 12th ed.5.St. Louis, MO: CV Mosby; 2003.6.Phillips N. Berry & Kohn’s Operating Room Technique. 10th ed. St Louis, MO:7.2004.8.Price P, Frey K, Junge TL, eds. Surgical Technology for the SurgicalTechnologist: A Positive Care Approach. 2nd ed. Clifton Park, NY: DelmarThomson Learning; 2004.9.Wagner VD. Impact of perioperative temperature management on patient safety.Surgical Services Management, 2003; 9 (4): 38-43.。
2011胃癌临床实践指南(英文)
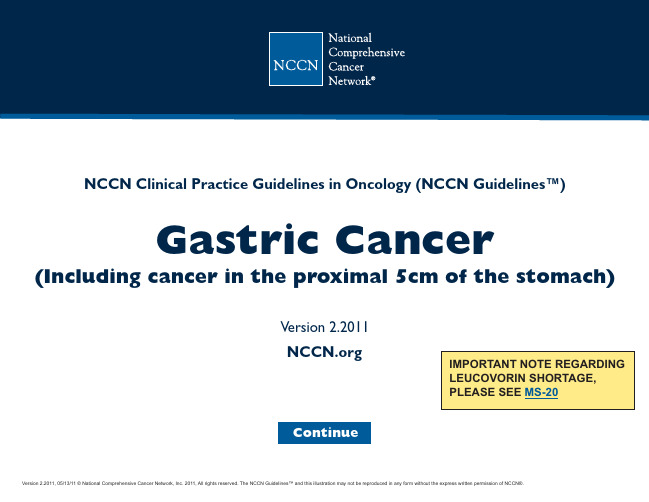
* Hans Gerdes, MD ¤ Þ
Memorial Sloan-Kettering Cancer Center Robert E. Glasgow, MD ¶ Huntsman Cancer Institute at the University of Utah James A. Hayman, MD, MBA § University of Michigan Comprehensive Cancer Center
Printed by jin qingyun on 7/28/2011 9:45:32 PM. For personal use only. Not approved for distribution. Copyright © 2011 National Comprehensive Cancer Network, Inc., All Rights Reserved.
NCCN Guidelines™ Version 2.2011 Panel Members Gastric Cancer
Principles of Systemic Therapy Mary F. Mulcahy, MD ‡/Lead Robert H. Lurie Comprehensive Cancer Center of Northwestern University
Version 2.2011
IMPORTANT NOTE REGARDING LEUCOVORIN SHORTAGE, PLEASE SEE MS-20
Continue
Version 2.2011, 05/13/11 © National Comprehensive Cancer Network, Inc. 2011, All rights reserved. The NCCN Guidelines™ and this illustration may not be reproduced in any form without the express written permission of NCCN®.
Guidelines for Tunnelling Risk Management

International Tunnel Association Working Group No. 2 Guidelines for Tunnelling Risk Management2002-10-21International Tunnelling Association,Working Group No. 2Guidelines for Tunnelling RiskManagement2002-10-21Revision 0Issue 2002-10-21Author Søren Degn Eskesen, Per Tengborg, Jørgen Kampmann, Trine Holst VeichertsContents0Abstract 51Introduction and scope 62Use of risk management 73Objectives of risk management 10 3.1Scope 10 3.2Risk objectives 10 3.3Risk management strategy 114Risk management in early design stages 13 4.1Establish risk policy 13 4.2Risk acceptance criteria 13 4.3Qualitative risk assessment 14 4.4Specific risk assessment 165Risk management during tendering and contractnegotiation 17 5.1Risk management during preparation of tenderdocuments 17 5.2Risk management during selection of contractor 19 5.3Risk clauses in contract 20 6Risk management during construction 22 6.1Contractor's risk management 22 6.2Owner's risk management 23 7Typical components of risk management 24 7.1Introduction 24 7.2Hazard identification 24 7.3Classification 257.4Quantitative risk assessment 328Risk management tools 34 8.1Fault tree analysis 34 8.2Event tree analysis 35 8.3Decision tree analysis 35 8.4Multirisk 36 8.5Monte Carlo simulation 379Glossary 3810References 390AbstractThe paper gives guidance to all those who have the job of preparing the overall scheme for the identification and management of risks in tunnelling and underground projects. The text provides owners and consultants with what is modern-day industry practice for risk assessment, and describes the stages of risk management throughout the entire project from concept to start of operation.1Introduction and scopeTunnelling and underground construction works impose risks on all parties involved as well as on those not directly involved in the project. The very nature of tunnel projects implies that any potential tunnel owner will be fac-ing considerable risks when developing such a project. Due to the inherent uncertainties, including ground and groundwater conditions, there might be significant cost overrun and delay risks as well as environmental risks. Also, as demonstrated by spectacular tunnel collapses and other disasters in the recent past, there is a potential for large scale accidents during tunnelling work. Furthermore, for tunnels in urban areas there is a risk of damage to a range of third party persons and property, which will be of particular con-cern where heritage designated buildings are involved. Finally there is a risk that the problems which the tunnelling project cause to the public will give rise to public protests affecting the course of the project.Traditionally, risks have been managed indirectly through the engineering deci-sions taken during the project development. These guidelines consider that pre-sent risk management processes can be significantly improved by using sys-tematic risk management techniques throughout the tunnel project develop-ment. By the use of these techniques potential problems can be clearly iden-tified such that appropriate risk mitigation measures can be implemented in a timely manner.The use of risk management from the early stages of a project, where major decisions such as choice of alignment and selection of construction methods can be influenced, is essential.The purpose of this document is to1.indicate to owners what is recommended industry best-practice forrisk management; and2.present guidelines to designers as to the preparation and implementa-tion of a comprehensive tunnel risk management system.For the purposes of this document "risk management" is the overall term which includes risk identification, risk assessment, risk analysis, risk elimi-nation and risk mitigation and control. See glossary in section 9.2Use of risk managementIn order to fulfil the scope these guidelines provide a description of risk management activities that may be used for tunnels and underground works. Below is shown how risk management may be used throughout the project from the early planning stage through to start of operation:•Phase 1: Early Design Stage (Feasibility and Conceptual Design) -Establish risk policy (section 4.1)-Risk acceptance criteria (section 4.2)-Qualitative risk assessment of the project (section 4.3)-Detailed analysis of areas of special interest or concern (section4.4)•Phase 2: Tendering & Contract Negotiation-Requirements in tender documents (section 5.1)-Risk assessment in tender evaluation (section 5.2)-Risk clauses in contract (section 5.3)•Phase 3: Construction Phase-Contractor's risk management (section 6.1)-Owner's risk management (section 6.2)-Joint risk management team between the owner and the contractor In phase 1 the responsibility of establishing a risk policy and carrying out risk assessment is the owner's alone. In phase 2 the potential contractor has certain input to the tender regarding risk management, but the owner is still the primary responsible party. In phase 3 however, the primary responsibil-ity moves on to the contractor to establish a risk management system and to carry out effective risk management. The owner should supervise, inspect and participate in this work. The owner should further continue to assess and mitigate risks not covered by the contractor.It is important that the risk management is performed in an environment of good cooperation between the parties. To achieve this, partnering may be a valuable tool. The process of partnering may be formulated as an exercise in encouraging good communications between the parties. It may be a formula for minimising cost to the owner while maximising profit for the contractor and encompasses joint planning and problem solving, scheduling, mitigationof delays and value engineering. The process of "partnering" may therefore be seen as a risk mitigation measure for the owner and the contractor.An overview of the risk management activities as seen from the owner's point of view is presented in figure 1. Risk assessments made by the contractor solely for his own purposes, such as the assessment of the risks he is involved in by submitting the tender, are not included.Owner Contractor Supervision and support ofcontractor's risk managementAssessment and mitigation of owner's riskEstablish risk management system Figure 1 - Risk management activity flow for owner and contractor Joint work in riskmanagement team3Objectives of risk managementThe identification of risks resulting from design and construction is an es-sential task early in a project. In order to form a common reference for all parties involved (e.g. the owner, designers, insurers and contractors) a con-struction risk policy should be established by the owner.A construction risk policy for the project may indicate:•scope,•risk objectives, and•risk management strategy.3.1ScopeAs an example, the scope may include the following risks or consequences: 1.Risk to the health and safety of workers, including personal injury and, inthe extreme, loss of life,2.Risk to the health and safety of third parties,3.Risk to third party property, specifically existing buildings and structures,cultural heritage buildings and above and below ground infrastructure, 4.Risks to the environment including possible land, water or air pollutionand damage to flora and fauna,5.Risk to the owner in delay to the completion,6.Risk to the owner in terms of financial losses and additional unplannedcosts.3.2Risk objectivesThe risk objectives may be given as general objectives supplemented by specific objectives for each type of risk. The general objectives of the con-struction risk policy could be that proper risk management throughout the project will be ensured at all stages of the project by the:•Identification of hazards•Identification of measures to eliminate or mitigate risks•Implementation of measures to eliminate or mitigate risks where economically feasible or required according to the specific risk ob-jectives or health and safety legislation.Economically feasible may be defined using the ALARP principle i.e. to reduce all risks covered to a level as low as reasonably practicable.The construction risk policy may indicate that emphasis should be placed on minimising overall risk by reducing the likelihood of occurrence of events with large consequences, e.g. with several fatalities or of significant political concern. This should be done if the owner considers low probability events with high consequences to be of more concern than high probability events with low consequences; even if the risk, expressed as probability times con-sequence, is the same.The construction risk policy may also include some general statements on allocation of risks between parties, e.g. a risk should be allocated to the party who has the best means for controlling the risk.For each type of risk, specific minimum risk objectives may be defined in addition to the general risk objectives. For example, the general public should be exposed only to a small additional risk from construction of the tunnel or underground works; compared to the risk they are exposed to as users of buildings, cars, bicycles, public transport and when walking in the adjacent streets.3.3Risk management strategyAs part of the construction risk policy a risk management strategy should be adopted. A recommended strategy is to carry out construction risk assess-ments at each stage of design and construction in accordance with the in-formation available and the decisions to be taken or revised at each stage. Any risk management strategy should include:• a definition of the risk management responsibilities of the various par-ties involved (different departments within the owner's organisation,consultants, contractors)• a short description of the activities to be carried out at different stages of the project in order to achieve the objectives• a scheme to be used for follow-up on results obtained through the risk management activities by which information about identified hazards (nature and significance) is freely available and in a format that can be communicated to all parties, which may best be accomplished by some form of comprehensive risk register•follow-up on initial assumptions regarding the operational phase •monitoring, audit and review procedures4Risk management in early design stages For effective risk management of a tunnelling project (or any other type of construction work) it is vital that risk management is begun as early as pos-sible, preferably during the project feasibility and early planning stages. The owner's risk policy sets the objectives of the exercise and existing members of the project team (and new members when they join the project team) should have the whole risk management process in their minds when carry-ing out their work.It is important to note that the success and benefits of implementing effec-tive risk management depends on the quality of the identified risk mitigating actions and on the active involvement, experience and general opinion of the participants (owner, designers and contractors).Risk management is not achieved by the enforcement of systems and proce-dures alone, but can be enhanced through seminars and meetings where an understanding and appreciation of the risk management objectives are dis-seminated throughout the organisations.4.1Establish risk policyThe primary step in establishing a risk management system is for the owner to formulate a risk policy as described in section 3.4.2 Risk acceptance criteriaThe risk objectives expressed in general terms in the owners risk policy should be "translated" into risk acceptance criteria suitable for use in the risk assessment activities planned to be carried out. This may include:•Risk acceptance criteria to be used in qualitative risk assessment. The risk classification shown in section 7.3.3 is an example of such criteria. •Risk acceptance criteria to be used in quantitative risk assessments. For each type of risk to be covered by a quantitative risk assessment theywould usually be expressed as:- A limit above which the risk is considered unacceptable and thus must be reduced regardless of the costs.- A limit below which it is not required to consider further risk re-duction.-An area between the two limits where risk mitigation shall be con-sidered and mitigation measures implemented according to the cir-cumstances, e.g. using the ALARP principle mentioned in section3.A document should be provided that explains how the risk acceptance crite-ria were established in relation to the statements on risk objectives in the owner's risk policy.4.3Qualitative risk assessmentDuring the early design stage, a qualitative risk assessment should be car-ried out focussed on the identification of potential hazards to the construc-tion activities expected to be included in the project, and covering all types of risk noted in the construction risk policy.The main purposes of this work is to raise the awareness of all concerned to the major risks involved in the construction and to provide a structured basis for the design decisions to be taken in the early design stage. The results can also be used for selection of specific topics for more detailed analyses as described in section 4.4. Finally the work can be used as starting point for the risk management during tendering.The timing of the qualitative risk assessment should be such that major de-sign changes are still possible. Depending on the time schedule of the early design it may be feasible to update the first qualitative risk assessment later in this design phase.The qualitative risk assessment should include:•Hazard identification. See section 7.2.•Classification of the identified hazards. See section 7.3. •Identification of risk mitigation measures.•Details of the risks in the project risk register indicating risk class and risk mitigation measures for each hazard.The identification and classification is best carried out through brainstorm-ing sessions with risk screening teams consisting of multi-disciplinary, technically and practically experienced experts guided by experienced risk analysts. The aim should be to identify all conceivable hazardous eventsthreatening the project including those risks of low frequency but high pos-sible consequence.In the identification and classification process due regard should be taken of common causes for hazardous events such as:•Complexity and maturity of the applied technology•Adverse unexpected ground and groundwater conditions •Technical and/or managerial incompetence•Human factors and/or human errors.•Lack of sufficient communication and co-ordination between internal and external interfaces•Combinations of several unwanted events that individually are not necessarily criticalThe identified hazards are classified according to the magnitude of the risk they represent. The purpose of this classification is to provide a framework for the decisions to be made on implementation of risk mitigation measures. Classification systems should be established covering frequencies and con-sequences as well as classification of risks on the basis of the frequency and consequence classes. The classification system may be included in the risk acceptance criteria, see section 4.2.The identification of risk mitigation measures may be carried out by the same or a different team and this team should preferably have a representa-tive of all the major parties to the project.Where risk levels conflict with the project's risk acceptance criteria, it is mandatory to identify risk-reducing actions and provide documentation for the management decision on which actions are to be implemented. The re-sults should be registered in the project risk register.Risk mitigation in this phase of the project will primarily result in changes in technical solutions and possibly in alternative working procedures. Fur-ther, many risk-reducing actions can be decisions or statements to be written into the tender documents.At this point it should be possible to establish whether implementation of a set of risk-mitigating actions will in fact reduce the risk to an acceptable level. If this does not appear to be the case, other approaches must be ex-plored.4.4Specific risk assessmentFor hazards of specific interest, e.g. due to the severity of the risk involved or the significance of the design decision to be taken, a more detailed risk analysis than the general qualitative analysis described in section 4.3 may be carried out. The outcome of this analysis should also be documented in the project risk register.The work may comprise one or more of the following:• A fault tree analysis of the causes of the hazards, see section 8•An event tree analysis of the consequences, see section 8• A full quantification of the risk, see section 7.4, e.g. with the purpose of evaluating the cost-benefit ratio of implementation of mitigating meas-ures or providing a quantitative basis for a decision between alternative courses of action.5Risk management during tendering and contract negotiation5.1Risk management during preparation of tenderdocuments5.1.1Main risk management activitiesThe following risk management activities should be carried out during preparation of the tender documents:•Specification of technical and other requirements in the tender docu-ments such that the risks are managed in accordance with the risk pol-icy. The results of the qualitative risk assessment carried out during the early design stage should be used as part of the basis.The specification of technical and other requirements should detail re-sponsibilities for risks in accordance with any general principlesadopted for the project covering allocation of risks. E.g. risks should be allocated to the party who has the best means for controlling them, as mentioned in section 3.2.•The qualitative risk assessment carried out in the early design stages should be repeated when the tender documents are near completion as the basis for final modifications of the tender documents and to docu-ment that risk has been managed in accordance with the risk policy.•Definition of the information requested from the tenderers in order to allow an evaluation of the tenderers' ability to manage risk and of the differences in risk between the proposals made by the different tender-ers. See section 5.1.2.•Specification of requirements in the tender document concerning the contractor's risk management activities during execution of the contract, see section 5.1.3.5.1.2Information to be provided with the tenderIn order to ensure a basis for comparing and evaluating the tenderers, the tender documents should state the information that each tenderer must pre-sent in this respect. This information should include:•Information on structured risk management in similar projects and their outcomes•CV for persons to be responsible for the risk management and details of any specialist organisation that has been involved•General description of the tenderer's intentions regarding his project-specific organisation and his risk management objectives•Overview and description of the major risks perceived by the tenderer in the project•The tenderer’s proposed strategy for the management of major risks to the project and how success will be defined and measured.It should be stated that some or all of the above information provided by the tenderers will be used as a basis for the owner's tender evaluation. The in-formation will help to illustrate whether the contractor is capable of carrying out the necessary systematic risk analysis, and the expected risk manage-ment performance.5.1.3Requirements to be specified in the tender documentsThe tender documents should specify that the contractor must perform risk management in accordance with the owner's risk policy. The contractor's risk management system and approaches must be compatible with the owner's, thereby reducing and controlling risks both to himself, to the owner and the public.Requirements concerning the contractor's risk management system should be described. This could include such matters as:•Organisation and qualifications of risk management staff•Types of risks to be considered and evaluated. These will be concerned with construction issues and any related design activities under the con-tractor's control.•Activities, i.e. description of a minimum requirement of activities to be included in the contractor's risk management, including systematic risk identification, classification of risks by frequency and consequence, and identification of risk elimination and risk mitigating measures•Time schedule for risk management activities (including requirements to carry out risk assessment in time to allow implementation of identi-fied risk mitigating measures)•Co-ordination with the owner's risk management and risk management team•Co-ordination with the other contractors' risk management•Co-ordination between risk management and the contractor's other sys-tems, such as quality management and environmental management.•Control of risks from sub-contractors’ activities•Specific requirements concerning risk management in explicit fields should be stated (examples could be modification to the construction methods for areas identified as of particular concern, i.e. construction methods related to risk to third party buildings or requirements concern-ing securing against unintentional ground water lowering)The owner's risk policy, risk acceptance criteria and risk classification sys-tem should be stated in the tender documents. The owner's risk management activities should be briefly mentioned. It should be carefully considered and pointed out to what extent the contractor will have insight into the owner's risk analysis results. Further, it should be stated in the tender documents that the contractor is responsible for effective risk management regardless of the extent and detail of the risk information deriving from the owner.It is recommended that the tender documents require that the owner be in-volved in the risk management during construction and that a risk manage-ment team is established with participants from the contractor and from the owner (see figure 1).5.2Risk management during selection of contractor Providing tenderers are clearly informed in tender documents, the applica-tion of risk management techniques by the owner can be valuable in the se-lection of the successful tenderer. Identifying risk issues in the tenders can be used as a basis for tender negotiations. The evaluation of tenders in re-spect of risk may be qualitative (based on a points system) or on a quantita-tive basis to the extent that the tender price might be adjusted accordingly.The evaluation of the risk issues in the tenders should include:•An evaluation of the contractor's ability to identify and control risks by the choice and implementation of technical solutions. An evaluation is also needed of his ability to apply systematic risk management in the work that he will undertake;•Systematic assessment of the differences in risk between the project proposals by different tenderers;•Evaluation of the risk management expertise at the contractor's disposalWhere a qualitative risk assessment is envisaged, the means of achieving this need to be considered during the preparation of the tender documenta-tion. For each identified risk, the tenders need to be compared and areas where there are differences should be highlighted.Where a quantitative risk assessment is envisaged, the recommended ap-proach is first to carry out a quantitative risk assessment on the owner's pro-ject as described in Section 7.4. This could be carried out in the time period between the issue and the receipt of tenders. The risk in each tender is quantified by taking the owner's quantitative risk assessment and for each risk considering the differences in frequency and consequence. The input to the quantification could be obtained from reliable information obtained from external sources and/or through brainstorming sessions. The experience and competence of those on the brainstorming team is vital. The final outcome will be the quantification of the risks involved in each tender. This has the benefit of a level comparison even if the absolute value of the risk is uncer-tain.This quantification is particularly useful for the risk of economic loss to the owner, and the risk of delay to the completion of the project. These evalua-tions could be directly compared with the contract price in the tenders and the assignment of a certain monetary value might be made per month's esti-mated or potential delay of project completion.For other risks it may be more difficult to obtain reliable results from a full quantification analysis, and a qualitative comparison may be all that is practi-cable.5.3Risk clauses in contractWhen a contractor has been chosen, negotiations between the owner and the contractor may lead to a detailed contractual description of the risk man-agement system to be implemented on the project. This may be based on a combination of the intentions of the owner and the suggested procedures of the contractor with the purpose of improving the co-operation between the parties.Alternative technical solutions will also be negotiated on the basis of risk assessments carried out and stated in the contract.The risk assessment of the successful tender may have identified some pre-viously undetected areas of risk or special concern. In order to reduce these risks to an acceptable level, additional risk mitigation clauses may be intro-duced in the contract. An example could be that the contractor has proposed a modification to the construction methods envisaged by the owner, which is advantageous except for a secondary risk of impact to the environment. This risk to the environment is then mitigated by additional requirements.6Risk management during constructionIn the early design and tender and contract negotiation phases certain risks may be transferred, either contractually or through insurance, others may be retained and some risks can be eliminated and/or mitigated. In the construc-tion phase, possibilities of risk transfer are minimal and the most advanta-geous strategy for both owner and contractor is to reduce the severity of as many risks as possible through the planning and implementation of risk eliminating and/or risk mitigating initiatives.6.1Contractor's risk managementBased on what has been agreed in the contract, the contractor's responsibil-ity could be as proposed in figure 1. The contractor is responsible for the fulfilment of the owner's risk policy and should start by establishing a care-fully planned, well-structured and easy-to-use risk management system. The structure of the risk management system is of great importance for the straightforwardness of the further work with detailed identification of haz-ards and assessment of risks. See section 7.The contractor must identify hazards and classify risks using systems which are compatible with the systems used by the owner (see section 7.2 and 7.3) and should propose mitigation measures to reduce the identified risks. In cases where the implementation of the mitigation measures could lead to major delay or could in any other way cause a loss to the owner, the owner should approve the intended mitigation prior to its implementation.The contractor's risk management strategy should be implemented by all members of his staff whatever their job functions. The identification of haz-ards and control of risk, and the techniques involved, should be seen as an essential part of all the design and construction activities of the project. In-formation and training should be given, as necessary, to all personnel throughout the project. The owner should be invited to be present and to participate in the contractor's risk management meetings, presentations and training sessions.Timely consideration and actions are of the essence in risk mitigation meas-ures. The aim is to anticipate, and put in place effective proactive preventa-。
最新欧洲急性肺栓塞指南,看这5张图就够了!GW-ICC2019

最新欧洲急性肺栓塞指南,看这5张图就够了!GW-ICC2019 控制血糖果然重要,但降低CVD风险才是首要目标。
静脉血栓栓塞(VTE)包括深静脉血栓(DVT)或肺栓塞(PE),是仅次于心肌梗死和卒中的全球第三常见的急性心血管综合征。
PE的年发病率为39-115/100000,纵向研究表明,每年PE发病率呈上升趋势。
在美国,PE每年可能导致<30万人死亡,是心血管疾病的一个重要死因。
而在中国,PE的30天全因死亡率约为4.9%-6.6%。
2019年8月31日在巴黎举行的ESC大会上发布了第4版急性肺栓塞诊断和管理指南,相比于2014年版指南,新指南在诊断、风险评估、急性期治疗、慢性期治疗、特殊人群管理和随访等方面进行了更新。
在2019年第三十届长城心脏病学会议(GW-ICC)上,来自首都医科大学附属北京安贞医院的刘巍教授对2019年ESC/ERS急性肺栓塞诊断和管理指南进行了解读,获得了与会人员的广泛关注。
精彩抢先看,相较于2014版肺栓塞指南,今年的指南更新了以下内容:•血流动力学不稳定和高危肺栓塞•适应风险的诊断方法•新的诊断建议•对右心室功能障碍的风险评估及其预后重要性的新建议•综合管理办法•急性肺栓塞后延长治疗的适应症•肿瘤相关的肺栓塞•长期随访与晚期后遗症01PE危险因素02血流动力学不稳定和高危PE的定义03高危PE的诊断流程无血流动力学障碍PE的诊断流程05修订的日内瓦肺栓塞临床预测规则诊断方法推荐07肺栓塞严重指数(PESI)及其简化版本sPESI08风险评估新增推荐09基于早期死亡风险的PE分层10急性肺栓塞经风险调整治疗策略11急性期治疗新增推荐12高危PE急性期治疗新增推荐13急性期治疗▎血流动力学和呼吸支持•氧气和通气•急性右室衰竭药物治疗•机械循环支持和氧合:ECMO的使用与较高的并发症发生率相关,即使使用时间很短。
目前,单独使用ECMOO联合抗凝仍存在争议。
•心脏骤停的高级生命支持:如果心脏骤停可能是急性肺栓塞引起的,应遵循指南进行生命支持。
妇科手术感染预防指南PPT课件
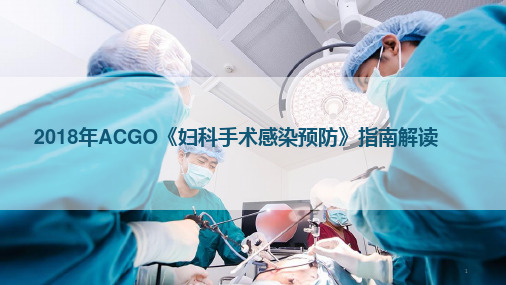
干预措施
术前
➢控制感染:远离手术部位的感染,在择期手术前都认真甄别并予以合理治疗。 ➢积极控制血糖:围术期积极控制血糖,争取血糖控制在200mg/dl(11.1mmol/L)以内*。 ➢清洁皮肤:2018年ACOG 指南建议,腹部手术患者术前夜间行(全身)淋浴或沐浴, 但指南未明确指出最佳洗涤剂及洗涤时间。 ➢细菌阴道病筛查问题:细菌性阴道病为术后感染的重要因素。该指南建议子宫切除 术前筛查细菌性阴道病,对合并细菌性阴道病患者,术前及术后需应用甲硝唑治疗至 少4d,以降低阴道残端感染的发生率。
13
结语
20世纪80年代初,预防性抗生素的应用使许多术后感染得以避免,但也 因药物的滥用导致了许多耐药的发生。.
随着医疗技术的发展及临床实践不断总结,抗生素的使用逐渐规范。
减少术后切口感染作为一项长期而艰巨的工作,医务人员应严格执 行《消毒隔离管理总则》,术前加强患者无菌宣传教育,术中严格 遵循无菌原则,规范操作,术后加强护理,注意心理干预,严密把 控治疗的各环节,以期降低切口感染的发生率,提高医疗质量。
14
THANK YOU
感谢聆听,批评指导
15
10
抗生素应用原则:适应症
阴式
经腹
腹腔镜
机器人
子宫切除术的患者应接受单剂量的 抗菌药物,目前推荐的单剂量的药物为 头孢唑林,指南不建议诊断性腹腔镜及 开腹探查的患者预防性应用抗生素。
11
抗生素应用原则:适应症
对于行子宫输卵管造影/输卵管通液的患者,若术前有盆腔炎性疾病病史或手术 时发现输卵管异常,建议预防性使用抗生素,常用多西环素。 行超声宫腔造影术、子宫内膜活检或消融、宫内节育器置入、宫颈组织活检的 患者因感染率微乎其微,均不推荐预防性应用抗生素。 人工流产的女性应预防性使用抗生素,研究发现,该举措可降低术后41%的感 染率。 阴道前后壁修补或阴道网片植入术者的患者可预防性应用抗生素。 目前尚不清楚预防性抗生素在外阴切除术中的作用,鉴于外阴皮肤上的细菌菌 群较多,此类手术切口类似清洁-污染手术,故给予单剂抗生素预防。
残留溶剂的指导原则英文

All residual solvents should be removed to the extent possible to meet product specifications, good manufacturing practices, or other quality-based requirements.
Drug products should contain no higher levels of residual solvents than can be supported by safety data.
Some solvents that are known to cause unacceptable toxicities (Class 1, Table 1) should be avoided in the production of drug substances, excipients, or drug products unless their use can be strongly justified in a risk-benefit assessment.
PART I:
Impurities:guidline for residual solvents
Introduction
The objective of this guideline is to recommend acceptable amounts for residual solvents in pharmaceuticals for the safety of the patient. The guideline recommends use of low toxic solvents and describes levels considered to be toxicologically acceptable for some residual solvents.
- 1、下载文档前请自行甄别文档内容的完整性,平台不提供额外的编辑、内容补充、找答案等附加服务。
- 2、"仅部分预览"的文档,不可在线预览部分如存在完整性等问题,可反馈申请退款(可完整预览的文档不适用该条件!)。
- 3、如文档侵犯您的权益,请联系客服反馈,我们会尽快为您处理(人工客服工作时间:9:00-18:30)。
TopicRESEARCHTitleGuidelines for tunnelling risk management: International Tunnelling Association, Working GroupNo. 2AuthorS. D. Eskesen, P. Tengborg, J. Kampmann, T. H. VeichertsOriginally publishedin the Journal "Tunnelling and Underground Space Technology",Vol. 19, Nr. 3, pp. 217 - 237, Year 2004.Copyright © 2004, Elsevier Science Limited, ; All Rights reserved. Working Group:WG 2 - "Research"Open Session, Seminar, Workshop:-Others:ReportAbstract:These guidelines, prepared by Working Group 2 (Research) of the International Tunnelling Association, are repared in order to give guidance to all those who have the job of preparing the overall scheme for theidentification and management of risks in tunnelling and underground projects. The guidelines provide ownersand consultants with what is modern-day industry practice for risk assessment, and describes the stages of riskmanagement throughout the entire project implementation from concept to start of operation.Résumé:-Remarks:-Secretariat : ITA-AITES c/o EPFL - Bât. GC – CH-1015 Lausanne - SwitzerlandFax : +41 21 693 41 53 - Tel. : +41 21 693 23 10 - e-mail : secretariat@ - ITA/AITES Accredited MaterialGuidelines for tunnelling risk management:InternationalTunnelling Association,Working Group No.2qSøren Degn Eskesen,Per Tengborg,Jørgen Kampmann,Trine Holst VeichertsITA Working Group 2,Research,ITA-AITES,c/o EPFL,Bat GC,CH 1015Lausanne,SwitzerlandAbstractThese guidelines,prepared by Working Group 2(Research)of the International Tunnelling Association,are prepared in order to give guidance to all those who have the job of preparing the overall scheme for the identification and management of risks in tunnelling and underground projects.The guidelines provide owners and consultants with what is modern-day industry practice for risk assessment,and describes the stages of risk management throughout the entire project implementation from concept to start of operation.Ó2004Elsevier Ltd.All rights reserved.PrefaceFront page articles in the news on spectacular tunnel collapses during the 1990s focused the public and in particular potential tunnel owners Õattention on the in-herent risk associated with underground construction works.As a result,risk management became an integral part of most underground construction projects during the late 1990s.However,from discussions in interna-tional forums,it became clear that handling and man-agement of risks were performed in many different ways,some more concise than others.Out of the discussions came the idea of establishing international guidelines on tunnelling risk management.Work on these guidelines began at the meeting of ITA Working group 2‘‘Research’’in Oslo in June 1999.After much study,discussions and investigations,the guidelines were completed in April 2003.These guidelines consider that present risk manage-ment processes can be significantly improved by using systematic risk management techniques throughout thetunnel project development.By the use of these tech-niques,potential problems can be clearly identified such that appropriate risk mitigation measures can be implemented in a timely manner.The guidelines show how risk management may be utilised throughout the phases of a project implemen-tation:1.Early Design Phase2.Tendering and Contract Negotiation Phase3.Construction PhaseThe guidelines also contain some typical components of risk management and a short introduction to general risk management tools as well as a glossary of risk terms.Finally,an example of how risk management was carried out for the Copenhagen Metro following prin-ciples similar to those presented in the guidelines is in-cluded as an appendix.The practice of performing risk management requires much experience,practical and theoretical knowledge.It is,therefore,not expected that these guidelines will cover every aspects of tunnelling risk management,but it isqDisclaimer:The International Tunnelling Association (ITA)publishes this report to,in accordance with its statutes,facilitate the exchange of information,in order:to encourage planning of the subsurface for the benefit of the public,environment and sustainable development to promote advances in planning,design,construction,maintenance and safety of tunnels and underground space,by bringing together information thereon and by studying questions related thereto.However,ITA accepts no responsibility or liability whatsoever with regard to the material published in this report.This material is:information of a general nature only which is not intended to address the specific circumstances of any particular individual or entity;not necessarily comprehensive,complete,accurate or up to date;sometimes collected from external sources over which ITA services have no control and for which ITA assumes no responsibility;may not be ITA position,not professional or legal advice (if you need specific advice,you should always consult a suitably qualified professional).0886-7798/$-see front matter Ó2004Elsevier Ltd.All rights reserved.doi:10.1016/j.tust.2004.01.001Space Technology 19(2004)217–237/locate/tustTunnelling andUnderground Space Technologyincorporating Trenchless Technology Researchintended to provide some basic knowledge and indicate what is recommended industry best practice for tunnel-ling risk management.It is hoped that this knowledge will be continuously improved by the use of these guidelines.As coordinator of preparing the guideline within the ITA Working Group No.2,I wish to acknowledge the important contributions of the following persons:Mr. Jørgen Kampmann and Mrs.Trine Hoist Veicherts, who have provided major contributions based on their valuable experience gained from working as risk man-ager and risk coordinator on major underground pro-jects,Dr.Birger Schmidt and Mr.Per Tengborg and all members of working group No.2,who contributed greatly to the study,Mr.John Summers,Dr.John An-derson,Dr.Robert Sturk,Prof.Fulvio Tonon,Mr. Peter Lundhus and Mr.Donald Lamont,who reviewed the guidelines and provided valuable comments and contributions,Prof.Andre Assis and Herr Dr.Harald Wagner,who guided our study as Tutors and Mssr. Yann Leblais,who led the study as Animateur assisted by Vice-Animateaur Mr.Yoshihiro Hiro Takano.Søren Degn EskesenCoordinator,ITA Working Group2Research 1.Introduction and scopeTunnelling and underground construction works impose risks on all parties involved as well as on those not directly involved in the project.The very nature of tunnel projects implies that any potential tunnel owner will be facing considerable risks when developing such a project.Due to the inherent uncertainties,including ground and groundwater conditions,there might be significant cost overrun and delay risks as well as envi-ronmental risks.Also,as demonstrated by spectacular tunnel collapses and other disasters in the recent past, there is a potential for large scale accidents during tunnelling work.Furthermore,for tunnels in urban ar-eas there is a risk of damage to a range of third party persons and property,which will be of particular con-cern where heritage designated buildings are involved. Finally,there is a risk that the problems which the tunnelling project cause to the public will give rise to public protests affecting the course of the project.Traditionally,risks have been managed indirectly through the engineering decisions taken during the project development.These guidelines consider that present risk management processes can be significantly improved by using systematic risk management tech-niques throughout the tunnel project development.By the use of these techniques potential problems can be clearly identified such that appropriate risk mitigation measures can be implemented in a timely manner.The use of risk management from the early stages of a project,where major decisions such as choice of align-ment and selection of construction methods can be in-fluenced,is essential.The purpose of this document is to1.indicate to owners what is recommended industrybest-practice for risk management and2.present guidelines to designers as to the preparationand implementation of a comprehensive tunnel risk management system.For the purposes of this document,‘‘risk manage-ment’’is the overall term which includes risk identifi-cation,risk assessment,risk analysis,risk elimination and risk mitigation and control,see Glossary.e of risk managementIn keeping with the task of the Working Group,these guidelines provide a description of risk management activities that may be used for tunnels and underground works.Below is shown how risk management may be used throughout the project from the early planning stage through to start of operation:•Phase1:Early Design Stage(Feasibility and Concep-tual Design)-Establish risk policy(Section4.1),-Risk acceptance criteria(Section4.2),-Qualitative risk assessment of the project(Section4.3),-Detailed analysis of areas of special interest or con-cern(Section4.4).•Phase2:Tendering and Contract Negotiation -Requirements in tender documents(Section5.1), -Risk assessment in tender evaluation(Section5.2), -Risk clauses in contract(Section5.3).•Phase3:Construction Phase-ContractorÕs risk management(Section6.1),-OwnerÕs risk management(Section6.2),-Joint risk management team between the owner and the contractor.In phase1,the responsibility of establishing a risk policy and carrying out risk assessment is the ownerÕs alone.In phase2,the potential contractor has certain input to the tender regarding risk management,but the owner is still the primary responsible party.In phase3, however,the primary responsibility moves on to the contractor to establish a risk management system and to carry out effective risk management.The owner should supervise,inspect and participate in this work.The owner should further continue to assess and mitigate risks not covered by the contractor.It is important that the risk management is performed in an environment of good cooperation between the parties.To achieve this,partnering may be a valuable tool.The process of partnering may be formulated as an218S.Degn Eskesen et al./Tunnelling and Underground Space Technology19(2004)217–237ITA/AITES Accredited Materialexercise in encouraging good communications between the parties.It may be a formula for minimising cost to the owner while maximising profit for the contractor and encompasses joint planning and problem solving, scheduling,mitigation of delays and value engineering. The process of‘‘partnering’’may therefore be seen as a risk mitigation measure for the owner and the contractor.An overview of the risk management activities as seen from the ownerÕs point of view is presented in Fig.1. Risk assessments made by the contractor solely for his own purposes,such as the assessment of the risks he is involved in by submitting the tender,are not included.3.Objectives of risk managementThe identification of risks resulting from design and construction is an essential task early in a project.In order to form a common reference for all parties involved (e.g.,the owner,designers,insurers and contractors),a construction risk policy should be established by the owner.A construction risk policy for the project may indicate:•scope,•risk objectives,and•risk managementstrategy.Fig.1.Risk management activityflow for owner and contractor.S.Degn Eskesen et al./Tunnelling and Underground Space Technology19(2004)217–237219ITA/AITES Accredited Material3.1.ScopeAs an example,the scope may include the following risks or consequences:1.Risk to the health and safety of workers,includingpersonal injury and,in the extreme,loss of life.2.Risk to the health and safety of third parties.3.Risk to third party property,specifically existingbuildings and structures,cultural heritage buildings and above and below ground infrastructure.4.Risks to the environment including possible land,water or air pollution and damage toflora and fauna.5.Risk to the owner in delay to the completion.6.Risk to the owner in terms offinancial losses and ad-ditional unplanned costs.3.2.Risk objectivesThe risk objectives may be given as general objectives supplemented by specific objectives for each type of risk. The general objectives of the construction risk policy could be that proper risk management throughout the project will be ensured at all stages of the project by the:•Identification of hazards.•Identification of measures to eliminate or mitigate risks.•Implementation of measures to eliminate or mitigate risks where economically feasible or required accord-ing to the specific risk objectives or health and safety legislation.Economically feasible may be defined using the ALARP principle,i.e.,to reduce all risks covered to a level a s l ow a s r easonably p racticable.The construction risk policy may indicate that em-phasis should be placed on minimising overall risk by reducing the likelihood of occurrence of events with large consequences, e.g.,with several fatalities or of significant political concern.This should be done if the owner considers low probability events with high consequences to be of more concern than high prob-ability events with low consequences;even if the risk, expressed as probability times consequence,is the same.The construction risk policy may also include some general statements on allocation of risks between par-ties,e.g.,a risk should be allocated to the party who has the best means for controlling the risk.For each type of risk,specific minimum risk objec-tives may be defined in addition to the general risk ob-jectives.For example,the general public should be exposed only to a small additional risk from construc-tion of the tunnel or underground works;compared to the risk they are exposed to as users of buildings,cars, bicycles,public transport and when walking in the ad-jacent streets.3.3.Risk management strategyAs part of the construction risk policy,a risk man-agement strategy should be adopted.A recommended strategy is to carry out construction risk assessments at each stage of design and construction in accordance with the information available and the decisions to be taken or revised at each stage.Any risk management strategy should include:•a definition of the risk management responsibilities of the various parties involved(different depart-ments within the ownerÕs organisation,consultants, contractors),•a short description of the activities to be carried out at different stages of the project in order to achieve the objectives,•a scheme to be used for follow-up on results obtained through the risk management activities by which in-formation about identified hazards(nature and sig-nificance)is freely available and in a format that can be communicated to all parties,which may best be accomplished by some form of comprehensive risk register,•follow-up on initial assumptions regarding the opera-tional phase,•monitoring,audit and review procedures.4.Risk management in early design stagesFor effective risk management of a tunnelling project (or any other type of construction work),it is vital that risk management is begun as early as possible,prefera-bly during the project feasibility and early planning stages.The ownerÕs risk policy sets the objectives of the exercise and existing members of the project team(and new members when they join the project team)should have the whole risk management process in their minds when carrying out their work.It is important to note that the success and benefits of implementing effective risk management depends on the quality of the identified risk mitigating actions and on the active involvement,experience and general opinion of the participants(owner,designers and contractors).Risk management is not achieved by the enforcement of systems and procedures alone,but can be enhanced through seminars and meetings where an understanding and appreciation of the risk management objectives are disseminated throughout the organisations.4.1.Establish risk policyThe primary step in establishing a risk management system is for the owner to formulate a risk policy as described in Section3.220S.Degn Eskesen et al./Tunnelling and Underground Space Technology19(2004)217–237ITA/AITES Accredited Material4.2.Risk acceptance criteriaThe risk objectives expressed in general terms in theownerÕs risk policy should be‘‘translated’’into risk ac-ceptance criteria suitable for use in the risk assessmentactivities planned to be carried out.This may include:•Risk acceptance criteria to be used in qualitative risk assessment.The risk classification shown in Section7.3.3is an example of such criteria.•Risk acceptance criteria to be used in quantitative risk assessments.For each type of risk to be covered by a quantitative risk assessment,they would usually be expressed as:-A limit above which the risk is considered unac-ceptable and thus must be reduced regardless ofthe costs.-A limit below which it is not required to considerfurther risk reduction.-An area between the two limits where risk mitiga-tion shall be considered and mitigation measuresimplemented according to the circumstances,e.g.,using the ALARP principle mentioned in Section3.A document should be provided that explains howthe risk acceptance criteria were established in relationto the statements on risk objectives in the ownerÕs riskpolicy.4.3.Qualitative risk assessmentDuring the early design stage,a qualitative risk as-sessment should be carried out focussed on the identi-fication of potential hazards to the constructionactivities expected to be included in the project,andcovering all types of risk noted in the construction riskpolicy.The main purposes of this work are to raise theawareness of all concerned to the major risks involved inthe construction and to provide a structured basis forthe design decisions to be taken in the early design stage.The results can also be used for selection of specifictopics for more detailed analyses as described in Section4.4.Finally the work can be used as a starting point forthe risk management during tendering.The timing of the qualitative risk assessment shouldbe such that major design changes are still possible.Depending on the time schedule of the early design itmay be feasible to update thefirst qualitative risk as-sessment later in this design phase.The qualitative risk assessment should include:•Hazard identification,see Section7.2.•Classification of the identified hazards,see Section7.3.•Identification of risk mitigation measures.•Details of the risks in the project risk register indicat-ing risk class and risk mitigation measures for each hazard.The identification and classification is best carried out through brainstorming sessions with risk screening teams consisting of multi-disciplinary,technically and practically experienced experts guided by experienced risk analysts.The aim should be to identify all con-ceivable hazardous events threatening the project in-cluding those risks of low frequency but high possible consequence.In the identification and classification process,due regard should be taken of common causes for hazardous events such as:•Complexity and maturity of the applied technology.•Adverse unexpected ground and groundwater conditions.•Technical and/or managerial incompetence.•Human factors and/or human errors.•Lack of sufficient communication and co-ordination between internal and external interfaces.•Combinations of several unwanted events that indi-vidually are not necessarily critical.The identified hazards are classified according to the magnitude of the risk they represent.The purpose of this classification is to provide a framework for the decisions to be made on implementation of risk mitiga-tion measures.Classification systems should be estab-lished covering frequencies and consequences as well as classification of risks on the basis of the frequency and consequence classes.The classification system may be included in the risk acceptance criteria,see Section4.2.The identification of risk mitigation measures may be carried out by the same or a different team and this team should preferably have a representative of all the major parties to the project.Where risk levels conflict with the projectÕs risk ac-ceptance criteria,it is mandatory to identify risk-re-ducing actions and provide documentation for the management decision on which actions are to be im-plemented.The results should be registered in the pro-ject risk register.Risk mitigation in this phase of the project will pri-marily result in changes in technical solutions and pos-sibly in alternative working procedures.Further,many risk-reducing actions can be decisions or statements to be written into the tender documents.At this point,it should be possible to establish whe-ther implementation of a set of risk-mitigating actions will in fact reduce the risk to an acceptable level.If this does not appear to be the case,other approaches must be explored.4.4.Specific risk assessmentFor hazards of specific interest,e.g.,due to the se-verity of the risk involved or the significance of the de-sign decision to be taken,a more detailed risk analysis than the general qualitative analysis described in SectionS.Degn Eskesen et al./Tunnelling and Underground Space Technology19(2004)217–237221ITA/AITES Accredited Material4.3may be carried out.The outcome of this analysis should also be documented in the project risk register.The work may comprise one or more of the following:•A fault tree analysis of the causes of the hazards,see Section8.•An event tree analysis of the consequences,see Section8.•A full quantification of the risk,see Section7.4,e.g., with the purpose of evaluating the cost-benefit ratio of implementation of mitigating measures or provid-ing a quantitative basis for a decision between alter-native courses of action.5.Risk management during tendering and contract negotiation5.1.Risk management during preparation of tender documents5.1.1.Main risk management activitiesThe following risk management activities should be carried out during preparation of the tender documents:•Specification of technical and other requirements in the tender documents such that the risks are managed in accordance with the risk policy.The results of the qualitative risk assessment carried out during the early design stage should be used as part of the basis.The specification of technical and other requirements should detail responsibilities for risks in accordance with any general principles adopted for the project covering allocation of risks,e.g.,risks should be allo-cated to the party who has the best means for control-ling them,as mentioned in Section3.2.•The qualitative risk assessment carried out in the early design stages should be repeated when the ten-der documents are near completion as the basis forfi-nal modifications of the tender documents and to document that risk has been managed in accordance with the risk policy.•Definition of the information requested from the ten-derers in order to allow an evaluation of the tender-ersÕability to manage risk and of the differences in risk between the proposals made by the different ten-derers,see Section5.1.2.•Specification of requirements in the tender document concerning the contractorÕs risk management activi-ties during execution of the contract,see Section5.1.3.rmation to be provided with the tenderIn order to ensure a basis for comparing and evalu-ating the tenderers,the tender documents should state the information that each tenderer must present in this respect.This information should include:•Information on structured risk management in simi-lar projects and their outcomes.•CV for persons to be responsible for the risk manage-ment and details of any specialist organisation that has been involved.•General description of the tendererÕs intentions re-garding his project-specific organisation and his risk management objectives.•Overview and description of the major risks perceived by the tenderer in the project.•The tendererÕs proposed strategy for the management of major risks to the project and how success will be defined and measured.It should be stated that some or all of the above in-formation provided by the tenderers will be used as a basis for the ownerÕs tender evaluation.The information will help to illustrate whether the contractor is capable of carrying out the necessary systematic risk analysis, and the expected risk management performance.5.1.3.Requirements to be specified in the tender docu-mentsThe tender documents should specify that the con-tractor must perform risk management in accordance with the ownerÕs risk policy.The contractorÕs risk management system and approaches must be compati-ble with the ownerÕs,thereby reducing and controlling risks both to himself,to the owner and the public.Requirements concerning the contractorÕs risk man-agement system should be described.This could include such matters as:•Organisation and qualifications of risk management staff.•Types of risks to be considered and evaluated.These will be concerned with construction issues and any re-lated design activities under the contractorÕs control.•Activities,i.e.,description of a minimum requirement of activities to be included in the contractorÕs risk management,including systematic risk identification, classification of risks by frequency and consequence, and identification of risk elimination and risk mitigat-ing measures.•Time schedule for risk management activities(includ-ing requirements to carry out risk assessment in time to allow implementation of identified risk mitigating measures).•Co-ordination with the ownerÕs risk management and risk management team.•Co-ordination with the other contractorsÕrisk management.•Co-ordination between risk management and the contractorÕs other systems,such as quality manage-ment and environmental management.•Control of risks from sub-contractorsÕactivities.•Specific requirements concerning risk management in explicitfields should be stated(examples could be222S.Degn Eskesen et al./Tunnelling and Underground Space Technology19(2004)217–237ITA/AITES Accredited Materialmodification to the construction methods for areas identified as of particular concern,i.e.,construction methods related to risk to third party buildings or re-quirements concerning securing against unintentional ground water lowering).The ownerÕs risk policy,risk acceptance criteria and risk classification system should be stated in the tender documents.The ownerÕs risk management activities should be briefly mentioned.It should be carefully considered and pointed out to what extent the contrac-tor will have insight into the ownerÕs risk analysis re-sults.Further,it should be stated in the tender documents that the contractor is responsible for effective risk management regardless of the extent and detail of the risk information deriving from the owner.It is recommended that the tender documents require that the owner be involved in the risk management during construction and that a risk management team is established with participants from the contractor and from the owner(see Fig.1).5.2.Risk management during selection of contractorProviding tenderers are clearly informed in tender documents,the application of risk management tech-niques by the owner can be valuable in the selection of the successful tenderer.Identifying risk issues in the tenders can be used as a basis for tender negotiations. The evaluation of tenders in respect of risk may be qualitative(based on a points system)or on a quanti-tative basis to the extent that the tender price might be adjusted accordingly.The evaluation of the risk issues in the tenders should include:•An evaluation of the contractorÕs ability to identify and control risks by the choice and implementation of technical solutions.An evaluation is also needed of his ability to apply systematic risk management in the work that he will undertake.•Systematic assessment of the differences in risk be-tween the project proposals by different tenderers.•Evaluation of the risk management expertise at the contractorÕs disposal.Where a qualitative risk assessment is envisaged,the means of achieving this need to be considered during the preparation of the tender documentation.For each identified risk,the tenders need to be compared and areas where there are differences should be highlighted.Where a quantitative risk assessment is envisaged,the recommended approach isfirst to carry out a quantita-tive risk assessment on the ownerÕs project as described in Section7.4.This could be carried out in the time period between the issue and the receipt of tenders.The risk in each tender is quantified by taking the ownerÕs quantitative risk assessment and for each risk consid-ering the differences in frequency and consequence.The input to the quantification could be obtained from re-liable information obtained from external sources and/ or through brainstorming sessions.The experience and competence of those on the brainstorming team is vital. Thefinal outcome will be the quantification of the risks involved in each tender.This has the benefit of a level comparison even if the absolute value of the risk is uncertain.This quantification is particularly useful for the risk of economic loss to the owner,and the risk of delay to the completion of the project.These evaluations could be directly compared with the contract price in the tenders and the assignment of a certain monetary value might be made per monthÕs estimated or potential delay of project completion.For other risks,it may be more difficult to obtain reliable results from a full quantification analysis,and a qualitative comparison may be all that is practicable.5.3.Risk clauses in contractWhen a contractor has been chosen,negotiations between the owner and the contractor may lead to a detailed contractual description of the risk management system to be implemented on the project.This may be based on a combination of the intentions of the owner and the suggested procedures of the contractor with the purpose of improving the co-operation between the parties.Alternative technical solutions will also be negotiated on the basis of risk assessments carried out and stated in the contract.The risk assessment of the successful tender may have identified some previously undetected areas of risk or special concern.In order to reduce these risks to an acceptable level,additional risk mitigation clauses may be introduced in the contract.An example could be that the contractor has proposed a modification to the con-struction methods envisaged by the owner,which is advantageous except for a secondary risk of impact to the environment.This risk to the environment is then mitigated by additional requirements.6.Risk management during constructionIn the early design and tender and contract negotia-tion phases,certain risks may be transferred,either contractually or through insurance,others may be re-tained and some risks can be eliminated and/or miti-gated.In the construction phase,possibilities of risk transfer are minimal and the most advantageous strat-egy for both owner and contractor is to reduce the se-verity of as many risks as possible through the planning and implementation of risk eliminating and/or risk mitigating initiatives.S.Degn Eskesen et al./Tunnelling and Underground Space Technology19(2004)217–237223ITA/AITES Accredited Material。