汽车塑料件设计要求——【塑胶模具与塑胶件】
汽车注塑件(塑料件)设计时需要遵循的14个基本原则

(2)拔模角和高度 通常,筋的拔模角在1-1.5度,最小不能小于0.5度,否则会导致零件脱模困
难。越高的筋顶部往往很薄,导致注塑过程中难以充满也就失去了筋的意义。筋 的顶端厚度一般不低于1毫米,高度一般为零件壁厚的2.5-3倍。当然也会有例外, 需要具体分析。
0.5 deg min 筋厚
Байду номын сангаас
1 min 壁厚
D min D min
塑料件中的柱销也是我们常用到的结构,主要用于提供连接和定位。 • 设计要点:
(1)像筋的设计一样要考虑拔模角度、出模方向、根部厚度与基本壁厚的比 例等。
(2)另外,我们还有一个相互矛盾的问题需要考虑。一方面,我们希望销柱 的厚度(B)尽量薄些,以防止表面出现缩痕。另一方面,我们希望其厚度能厚 一些,以增加结构强度。最终,我们要根据产品结构和材料等综合分析确定。
塑料件翻边结构十分重要,它能够明显提高制件的结构刚度控制变形,是很 有用的结构,我们设计时必须尽量考虑增加翻边结构。 • 设计要点:
(1)翻边的厚度应该与基本壁厚一致。 (2)考虑到零件花纹,我们对翻边的拔模角度有特殊的要求,一般在3-6度之 间。但是不同的花纹会有不同的要求,设计时应根据花纹要求及制造和质量要求 选择适当的拔模角。
P/L P/L
8 有许多种类型的花纹可以用于零件表面的装饰。我们设计时需要针对不同的
花纹选择合适的设计结构。 • 设计要点:
(1)拔模角—总的规则是每增加0.025毫米的花纹深度,需要增加至少1度的拔 模角。关于花纹和拔模角需要设计者和花纹供应商共同检查和确认,并得到 OEM的认可。
(2)翻边—对于翻边结构,花纹和拔模角的关系是最突出的。翻边结构就需 要一定的脱摸角度,以便零件从模具内移出。越长的翻边需要越大的脱模角度, 越深的花纹,也需要越大的脱模角度。如果不注意这点就会产生零件脱模困难, 甚至擦伤零件花纹表面。
浅谈汽车塑料件的结构设计原则

经济及科技 的发展为汽车行业带来 了机 遇 , 而汽 车产业 的发展 要适 当缩 减 , 拔模 的角度要控 制在 0 . 5 — 1度 , 这样 的设 计可 以使 汽 离不开塑料的使用 。 塑料在汽车生产的应用不仅深化 了汽车的机动 车塑料 件的成 品脱模 ;要对 螺钉安装柱的一部分予 以减胶处理 , 这 及越野性 能 , 同时还减轻 了汽车车体 的 自重 , 因此从侧 面降低 了燃 样的设计 能够 降低 汽车塑料件 的外形 的缩痕 。 这样 的结构设计 能够 料消耗 , 节约了资源。 汽车塑料件 主要应用 于汽 车的内外装饰 , 同时 确保 汽车塑料 件结 构设计 的精准度 , 进 而能够深化汽车塑料件产 品 在不断推广并发挥其有效性 。 对汽车塑料件 的结构设计予以分析及 的质量与汽车整体的品质 , 促进汽车领域的发展 。 研究针对汽车制造及整个汽车产业的发展意义深远。 文章将以浅谈 4 汽 车 塑 料 件 定 位 销 设 计 原 则 汽车塑料件 的结构设计原则作为切人点 , 在此基础上予 以深 入的探 针对汽车塑料件 的定位 销结 构位置 的设计 , 在设计 过程要确保 究, 相关 内容如下所述。 定位销位置的汽车塑料件成品外形没有缩痕 的问题 , 同时在汽 车塑 1 汽 车塑 料 件 壁厚 设计 原 则 料件的装配过程 , 定 位销的首部要 确保导 向的 c角 , 与其 对应 的安 在种类趋于多元化 的汽车塑料件 中 , 针对热塑性高 的汽车塑料 装孔位置也要 有一 定的倾斜 。 此设计模 式能够 降低汽 车塑料件 成品 件 的壁厚设计要遵循硬性指标 , 确保壁厚 的均匀性及统 一性 。若汽 的缺陷 , 确保外 观上 良好 的形象 , 同时可以确保装 配环节 的顺利进 车塑料件 的壁厚之差超过 2 5 %, 那么汽车塑料件重 的内部应 力会显 行。在予以汽车塑料件的定位销结构设计过程 , 要遵循相关指标 予 著提 升 , 因此造成汽 车塑料件产生萎缩 、 发 生气泡及严 重变形 等问 以设计 , 尽可 能降低误差与相关 干扰 因素 , 把汽 车塑料件 的结构 与 题 。 即使 是 遵 循 指 标 汽 车 塑 料 件 间的 壁 厚 之 差 没 有 大 于 2 5 %, 壁 厚 质量控制在最佳水平 , 最大 限度 的发挥 汽车塑料件在汽车 整体 中的 的改变也需要 有过渡时 间 , 模具填 充环节 , 要是材料从 汽车 塑料件 有 效 性 。 较厚 的位置 向较薄 的位置填充 。 若汽车塑料件的壁厚设计缺乏合理 5 结 论 性, 那么汽车塑料件的转角位置与左右均会较厚 , 中间趋于偏薄 , 偏 综上所述 , 对热塑性高 的汽车塑料 件的壁厚设计 要遵循硬性 指 薄 的位置就需要一定 的时间予 以凝 固 , 左右 区域凝 固需 要的时问也 标 ,确保 壁厚的均匀性 及统一性 。若 汽车塑料 件的壁厚 之差超 过 较长 , 那么最终生产的汽车塑料件就会存在一定 的问题。为了规避 2 5 %, 那 么汽车 塑料件重 的 内部应力 会显著 提升 , 因此造 成汽 车塑 这些 问题 汽车塑料件就要对 汽车塑料 件的结构设计予 以有效处理 , 料件产生萎缩 、 发生气泡及严 重变形等问题 。即使是遵循 指标 汽车 较厚 的位 置予 以调整 , 实现汽 车塑料件 的壁厚 的匀称性 , 达 到结构 塑 料 件 间 的 壁 厚 之差 没 有 大 于 2 5 %,壁 厚 的 改 变 也 需 要 有 过 渡 时 的要 求 , 进而汽车塑料件 的生产质量上才会有所提高。 间, 模具填 充环节 , 要是材料从 汽车塑料件较厚 的位 置向较薄 的位 2 汽 车 塑 料 件 加 强 筋 设 计 原 则 置填充 。 加强筋 的拔模角度设置值要在指标范围内 , 若角度设置小 , 在实施 汽车塑料件 的结 构设计 过程 中, 在 汽车塑料件上使用加 汽车塑料件对模具型芯的包紧力会提高 ,需要调 节模 具顶 出力 , 不 强筋 能够 有增加 高汽车塑料件 的强度 。 在对 汽车 塑料件加强筋设计 谈很可能会发生汽车塑料件表面有顶 白的情 况 ,角度设置过大 , 会 前, 要控制好三个部分 的布局 : a . 从 加强 筋的拔模 角度分析 。加强筋 致使加 强筋顶端太 薄 ,只能够利用 加压及加 温才可 以确保物 料填 的拔模角度设 置值要在 指标范 围内 , 若角度设 置小 , 汽 车塑料件对 充 。在加强筋及汽车塑料件壁 的交叉位 置画圈 , 词语 安全 会与加强 模具型芯 的包紧力会 提高 , 需 要调节模具顶 出力 , 不谈很 可能会发 筋 和汽车塑料件壁有三个交点 , 处于汽车塑料件壁 的壁厚处与加强 此 圆圈的直径要小 于汽车塑料件公称壁厚 的 生汽车塑 料件表面有顶 白的情况 , 角度设 置过大 , 会致使 加强筋顶 筋底部两端 内角位置 。 端太薄 , 只能够利用加压及加温才 可以确保 物料填充 。因此要科学 两倍 , 设计 过程要注意的是正确判断加强筋 的最厚处 。在实际的结 螺钉安装 柱外部尺寸在 拔模 过程 中要 适 当缩 减 , 拔模 的控制拔模角度 , 控制好汽车塑料件 的成 型及品质 , 降低 生产成本 。 构设计 环节 , 角度最好控制在 0 . 2 5度 ~ 2度之间 . b . 从加强筋 的厚 度设 计来 分析 。 的角度要 控制在 0 . 5 ~ 1 度, 这样的设计可 以使 汽车塑料件 的成品脱 要对螺钉安装柱的一部分 予以减胶处理 。 。 加强筋厚度设计过程中要依 附于 以下几点 : 在加强筋及汽车塑料件 模 ; 壁的交叉位置画圈 , 词语安全会 与加强筋和汽车塑料件壁有三个交 参 考 文献 1 1 王梦寒 , 董晶 晶, 周杰, 代忠, 邹鹰 , 姚 小兵. 基 于代理模 型和改进 点, 处于汽车塑料件壁 的壁 厚处与加强筋底部两端 内角位置 。此圆 『 J ] . 材料科 学与工 艺, 2 0 1 3 ( 2 ) . 圈的直径要小于汽车塑料件公称壁厚 的两倍 , 设计过程要 注意的是 遗传算法的注塑翘曲优化 f 谈桂春 , 张晓云 , 赵 志鸿 , 肖德 凯. 2 0 0 5年 我 国 工 程 塑料 加 工 技 术 正 确 判 断 加 强 筋 的 最 厚 处 。汽 车 塑 料 件 的 加 强 筋 厚 度 要 在 1 1 - 1 . 5 M M。 c . 汽车塑料件 的结 构设计过程 , 加强筋的高度的极值 即公 进 展 叭 工程 塑料 应 用 。 2 0 1 6 ( 6 ) . 称壁厚 的 3 倍, 最小值是公称壁 厚的 2倍 , 三角筋 同上 ; d . 加强 筋的 『 3 1 孙 宝寿 , 邓益 民, 陈哲 , 王利柱 , 刘军. 基于 T a g u c h i 和U D E试 验 设 有效布局要择取十字交叉 的方法 , 所以此方法能够有效适用 于多种 计 的 注 塑 工 艺 参 数优 化 【 J 1 . 工程 塑料 应 用 , 2 0 1 3 ( 1 2 ) . 4 1 孙宝寿 , 陈哲 , 吴真繁 , 顾 伯勤 , 黄筱调 . 薄壁 注塑件 翘 曲影 响 因素 差异 化的结构 , 同时可应 付差异化 的负荷变化及承 受力 , 能够有 效 『 分 析 及 优 化 研 究 进展 f J 1 . 机 械 制 造 , 2 0 1 2 ( 1 2 ) . 保 障汽车塑料件成 品的应力分布 的均匀 。 不过这一布局会形成一个 节点 , 节 点位置材料 堆积会导致汽 车塑料件 的萎缩 , 针对此情 况我 f 5 1 钱 宇强 , 肖小亭 , 孙友松 , 杨 国华. 注塑成 型工 艺参数 对含 熔接 痕 P改性 塑件 冲击性能的影 响 [ J 】 .高分子材料科 学与工程 , 2 0 1 3 们要将节点位置挖空来规避这一 问题 , 还要注意 的是 注意 避免边交 的 P
汽车塑料件设计要求

二、壁厚均一的设计原则
• 在确定壁厚尺寸时,壁厚均一是一个重要原则。 该原则主要是从工艺角度以及由工艺导致的质量 方面的问题而提出来的。均匀的壁厚可使制件在 成型过程中,熔体流动性均衡,冷却均衡。壁薄 部位在冷却收缩上的差异,会产生一定的收缩应 力,内应力会导致制件在短期之内或经过一个较 长时期之后发生翘曲变形。 • 塑料件最通用料厚是2.5mm,大件适当增加,小件 减小,强烈建议通过增加翻边及加强筋的方式而 不是增加料厚来保证零件强度; PP塑料的壁厚范 围是0.6—3.5mm。
② 受模具活动部分影响的尺寸 b,如图所示,它是 指可活动的模具零件共同作用所构成的尺寸。例 如壁厚和底厚尺寸;受动模零件、定模零件和滑 块共同影响的尺寸。
塑料件连接结构
塑料件的螺钉连接1:
簧片螺母连接,应用于板类零件与塑料件之间的 连接;
板类零件与塑料件之间 大量使用簧片螺母连接
塑料件的螺钉连接2:
②模具
• 对于小尺寸的塑料件,模具的制造误差占塑料公 差的1/3。
• 与模具上运动的零件有关的塑件尺寸,其精度较 低。
• 模具上浇注系统和冷却系统设计不当,会使成型 塑件的收缩不均匀。 • 脱模系统的作用力不当,会使被顶出塑件变形。
③塑件结构
• 塑料件壁厚均匀一致,形体又对称,可使 塑件收缩均衡。提高塑料件的刚性,如加 强筋的合理设置或采用金属嵌件,能减小 塑件翘曲变形,都有利于提高塑件精度。
塑料螺母连接;应用于板类零件与钣金件之间的 连接。(钣金件方孔开口7*7)
板类零件与钣金件 之间大量使用塑料 螺母连接
塑料件的螺钉连接3:
自攻螺钉柱及螺钉沉台的连接;应用于机壳类塑 料件之间的连接;
机壳类塑料件通过自 攻螺钉柱及螺钉 沉台连接
汽车塑料件设计要求方案
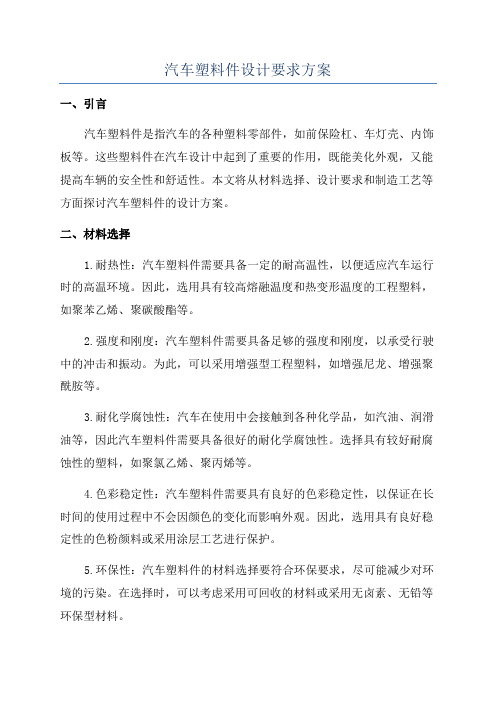
汽车塑料件设计要求方案一、引言汽车塑料件是指汽车的各种塑料零部件,如前保险杠、车灯壳、内饰板等。
这些塑料件在汽车设计中起到了重要的作用,既能美化外观,又能提高车辆的安全性和舒适性。
本文将从材料选择、设计要求和制造工艺等方面探讨汽车塑料件的设计方案。
二、材料选择1.耐热性:汽车塑料件需要具备一定的耐高温性,以便适应汽车运行时的高温环境。
因此,选用具有较高熔融温度和热变形温度的工程塑料,如聚苯乙烯、聚碳酸酯等。
2.强度和刚度:汽车塑料件需要具备足够的强度和刚度,以承受行驶中的冲击和振动。
为此,可以采用增强型工程塑料,如增强尼龙、增强聚酰胺等。
3.耐化学腐蚀性:汽车在使用中会接触到各种化学品,如汽油、润滑油等,因此汽车塑料件需要具备很好的耐化学腐蚀性。
选择具有较好耐腐蚀性的塑料,如聚氯乙烯、聚丙烯等。
4.色彩稳定性:汽车塑料件需要具有良好的色彩稳定性,以保证在长时间的使用过程中不会因颜色的变化而影响外观。
因此,选用具有良好稳定性的色粉颜料或采用涂层工艺进行保护。
5.环保性:汽车塑料件的材料选择要符合环保要求,尽可能减少对环境的污染。
在选择时,可以考虑采用可回收的材料或采用无卤素、无铅等环保型材料。
三、设计要求1.外观设计:汽车塑料件是汽车的重要组成部分,其外观设计要与整车风格相协调。
注重形状的流线化、曲线的柔和、比例的协调等,以提高整体的美观性。
2.强度和刚度:对于需要承受冲击的塑料件,要注重强度和刚度的设计,以确保其在受力时不会发生变形和破裂。
3.安装和拆卸便捷性:汽车塑料件需要便于安装和拆卸,以方便维修和更换。
因此,在设计时要考虑到拆卸和装配的方便性,并采用合适的固定件和连接件。
4.密封性:对于需要防水和密封的汽车塑料件,要注重密封性的设计,以避免水汽渗入和气体泄漏。
5.耐久性:汽车塑料件需要具备一定的耐久性,以承受车辆长期使用带来的磨损和老化。
因此,在设计时要考虑到材料的耐候性和耐磨性,并采取适当的保护措施。
汽车塑料件结构设计的一般原则及精度

3 6
0.08 0.16 0.12 0.22 0.14 0.34 0.18 0.38 0.24 0.44 0.32 0.52 0.48 0.68
±0.12 ±0.22 ±0.16 ±0.26 ±0.24 ±0.34
6 10
0.09 0.18 0.14 0.24 0.16 0.36 0.20 0.40 0.28 0.48 0.38 0.58 0.58 0.78
下表 列出了常用的注射塑料的成型收缩率。 用无机填料填充、用玻璃纤维增强的塑料有较低的成型收 缩率。
41
6、注塑件的精度
42
②模具
6、注塑件的精度
对于小尺寸的塑料件,模具的制造误差占塑料公差的1/3。 与模具上运动的零件有关的塑件尺寸,其精度较低。 模具上浇注系统和冷却系统设计不当,会使成型塑件的 收缩不均匀。 脱模系统的作用力不当,会使被顶出塑件变形。
30
5、抗变形设计 防止变形的措施
前述的避免应力集中以及刚性设计的一些措施,也都有 助于防止或者降低制件的变形。此外,设计时考虑防止产品 变形,在形状上进行规避。
31
5、抗变形设计
矩形的薄壁容器的侧壁容易发生内凹变 形,为此可将侧壁设计得稍微外凸一些
32
5、抗变形设计
深度较浅的盒类制品,为避免翘曲变形, 可将其底边设计成倒角形状
后果:塑料是对缺口和尖角之类比较敏感的材料,在应 力作用下,这些部位会逐渐产生微细裂纹,随后逐步扩展到 大的裂纹,而裂纹的不断延伸终将导致制件的损坏。
17
3、避免应力集中原则
避免应力集中应作为一条基本的准则
避免应力集中最直接最有效的方法就是在拐角、棱边、 凹槽灯等轮廓过渡与厚薄交接处采用圆弧过渡。
5、抗变形设计
汽车一般塑料件设计标准
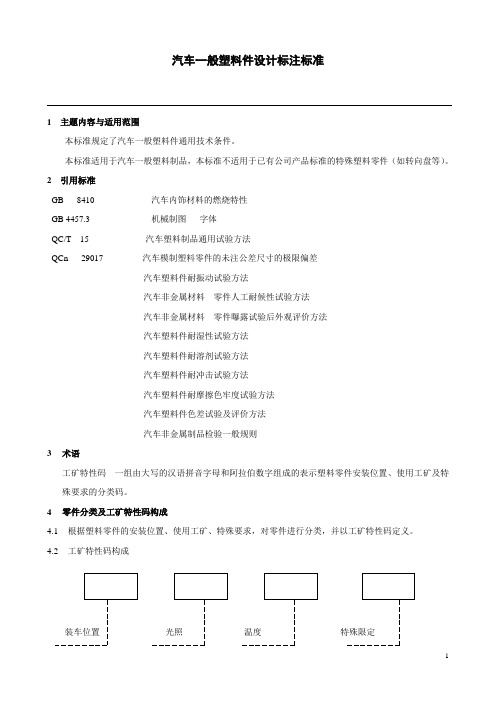
汽车一般塑料件设计标注标准1 主题内容与适用范围本标准规定了汽车一般塑料件通用技术条件。
本标准适用于汽车一般塑料制品,本标准不适用于已有公司产品标准的特殊塑料零件(如转向盘等)。
2 引用标准GB 8410 汽车内饰材料的燃烧特性GB 4457.3 机械制图字体QC/T 15 汽车塑料制品通用试验方法QCn 29017 汽车模制塑料零件的未注公差尺寸的极限偏差汽车塑料件耐振动试验方法汽车非金属材料零件人工耐候性试验方法汽车非金属材料零件曝露试验后外观评价方法汽车塑料件耐湿性试验方法汽车塑料件耐溶剂试验方法汽车塑料件耐冲击试验方法汽车塑料件耐摩擦色牢度试验方法汽车塑料件色差试验及评价方法汽车非金属制品检验一般规则3术语工矿特性码---一组由大写的汉语拼音字母和阿拉伯数字组成的表示塑料零件安装位置、使用工矿及特殊要求的分类码。
4零件分类及工矿特性码构成根据塑料零件的安装位置、使用工矿、特殊要求,对零件进行分类,并以工矿特性码定义。
工矿特性码构成4.2.1 装车位置根据零件在车上的位置处分为四类,分别用大写汉语拼音字母表示。
具体规定如下:A ——车身内部零件B ——车身外部零件C ——发动机舱内零件D ——底盘上零件4.2.2 光照根据零件的光照情况分为两种,用一位阿拉伯数字表示,具体规定如下:0 ——不受阳光照射1 ——受阳光照射4.2.3 温度根据零件的温度工况分为四种,用一位阿拉伯的数字表示,具体规定如下:0 ——温度不高工况,如门里板堵盖、轮罩、座椅调节手柄等。
1 ——较高温度工况,如仪表板下挡板、开关固定板、保险杠、灯圈、车门户板等。
2 ——高温工况,如仪表板上部零件、烟灰缸等。
3 ——特高温度工况4.2.4 特殊限定零件有特殊性能要求时,增加特殊限定码,特殊限定码由一位或一组大写汉语拼音字母组成。
具体规定如下:T ——装饰性:用于有装饰性要求的内饰及外装件F ——阻燃性:用于有阻燃要求的内饰件S ——冲击性:用于受冲击作用的零件,冲击性分为三种,具体规定如下:S ——普通冲击S1 ——中冲击S2 ——高冲击4.3 工况特性码在图样上的标注例:仪表板中下挡板ABS-AI该零件安装在车身内部(位置码为A),受阳光照射(光照码为1),在较高温度工况下工作(温度码为1),属内饰件(增加T),有阻燃要求(增加F),有抗中等冲击要求(增加S1)、其工况特性码为:AIITFSI 在图样材料中标注: ABS—AI EQC—300—93AIITFSI EQC—302—945 技术要求5.1 一般规定5.1.1 一般塑料零件必须符合本标准,并严格按经过规定程序批准的图样及有关技术文件制造。
塑胶材料对模具设计要求
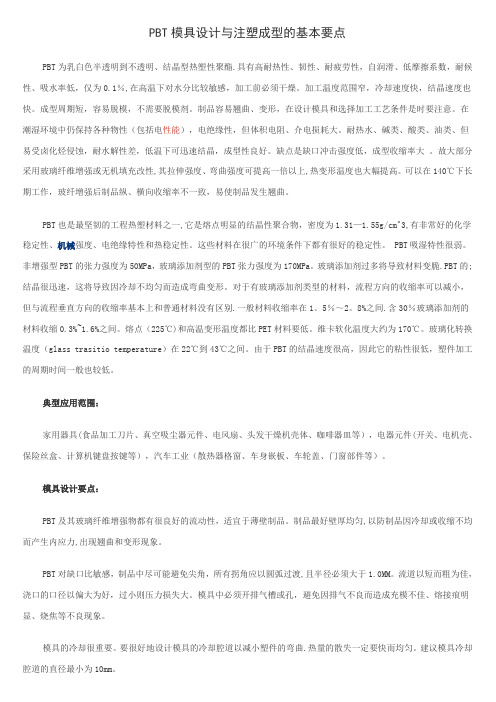
PBT模具设计与注塑成型的基本要点PBT为乳白色半透明到不透明、结晶型热塑性聚酯.具有高耐热性、韧性、耐疲劳性,自润滑、低摩擦系数,耐候性、吸水率低,仅为0.1%,在高温下对水分比较敏感,加工前必须干燥。
加工温度范围窄,冷却速度快,结晶速度也快。
成型周期短,容易脱模,不需要脱模剂。
制品容易翘曲、变形,在设计模具和选择加工工艺条件是时要注意。
在潮湿环境中仍保持各种物性(包括电性能),电绝缘性,但体积电阻、介电损耗大。
耐热水、碱类、酸类、油类、但易受卤化烃侵蚀,耐水解性差,低温下可迅速结晶,成型性良好。
缺点是缺口冲击强度低,成型收缩率大。
故大部分采用玻璃纤维增强或无机填充改性,其拉伸强度、弯曲强度可提高一倍以上,热变形温度也大幅提高。
可以在140℃下长期工作,玻纤增强后制品纵、横向收缩率不一致,易使制品发生翘曲。
PBT也是最坚韧的工程热塑材料之一,它是熔点明显的结晶性聚合物,密度为1.31—1.55g/cm^3,有非常好的化学稳定性、机械强度、电绝缘特性和热稳定性。
这些材料在很广的环境条件下都有很好的稳定性。
PBT吸湿特性很弱。
非增强型PBT的张力强度为50MPa,玻璃添加剂型的PBT张力强度为170MPa。
玻璃添加剂过多将导致材料变脆.PBT的;结晶很迅速,这将导致因冷却不均匀而造成弯曲变形。
对于有玻璃添加剂类型的材料,流程方向的收缩率可以减小,但与流程垂直方向的收缩率基本上和普通材料没有区别.一般材料收缩率在1。
5%~2。
8%之间.含30%玻璃添加剂的材料收缩0.3%~1.6%之间。
熔点(225℃)和高温变形温度都比PET材料要低。
维卡软化温度大约为170℃。
玻璃化转换温度(glass trasitio temperature)在22℃到43℃之间。
由于PBT的结晶速度很高,因此它的粘性很低,塑件加工的周期时间一般也较低。
典型应用范围:家用器具(食品加工刀片、真空吸尘器元件、电风扇、头发干燥机壳体、咖啡器皿等),电器元件(开关、电机壳、保险丝盒、计算机键盘按键等),汽车工业(散热器格窗、车身嵌板、车轮盖、门窗部件等)。
塑胶件结构设计规范

产品设计者在选定尺寸公差时要考虑使用之塑料材料、产品形状及将来之使用条件等。 随着公差的严格要求,其制造加工精度与模具价格亦相对提高,所以产品设计者于图面上记 入公差时,要审慎的设定适用于此公差的使用条件。因此,产品设计者所设定之总公差应该 包含了使用条件和环境条件下的尺寸变化。
关键词 塑料零件、壁厚、脱模斜度、加强筋、材料选择 1、零件的形状应尽量简单、合理、便于成型
1.1 在保证使用要求前提下,力求简单、便于脱模,尽量避免或减少抽芯机构,如采用下 图例中(b)的结构,不仅可大大简化模具结构,便于成型,且能提高生产效率。
1.2 利用转换区的方法来防止突然的递变。
1.3 利用肋及浮凸物和铸空法使设计更合理。 1.4 转角处用圆弧过渡。
聚苯乙烯、有机玻璃 热固性塑料
脱模斜度 30′~1° 40′~1°30′ 50′~2° 20′~1°
在具体选择时,还应注意以下几个问题: 3.1 凡塑件精度要求高时,应采用较小的脱模斜度; 3.2 凡较高、较大的尺寸,应选用较小的脱模斜度; 3.3 塑件形状复杂的、不易脱模的应选用较大的脱模斜度; 3.4 塑件的收缩率大的应选用较大的斜度值; 3.5 塑件壁较厚时,会使成形收缩增大,脱模斜度应采用较大的数值; 3.6 如果要求脱模后塑件保持在型芯的一边,那么塑件的内表面的脱模斜度可选的比外表
塑胶零件结构设计规范
摘要 随着公司的不断发展和产品的增加,为了造型的需要产品结构件中塑料零件用 的越来越多。那么在具体设计塑料零件的结构时需要考虑哪些方面的问题?怎样合理地设计 塑料零件的结构?如何选择塑料零件的材料?壁厚选择多少合适?等等。本文对这些具体问 题进行了详细的总结。希望对大家在今后的设计中有所帮助并希望大家一起来补充完善。
- 1、下载文档前请自行甄别文档内容的完整性,平台不提供额外的编辑、内容补充、找答案等附加服务。
- 2、"仅部分预览"的文档,不可在线预览部分如存在完整性等问题,可反馈申请退款(可完整预览的文档不适用该条件!)。
- 3、如文档侵犯您的权益,请联系客服反馈,我们会尽快为您处理(人工客服工作时间:9:00-18:30)。
②结构泡沫:具有致密表皮层和呈微孔结构 的芯部,这种结构具有高的比强度,可应用 在受力结构中。
③口字形结构、T 形结构以及工字梁结构,与矩形截面的实心结构比 较,这种结构既能节省材料,又不降低刚性。
④圆锥体结构,相对圆柱体结构,这种结构 能承受很大的压缩载荷,弯曲稳定性好。
‹# ›
⑤双壁结构,有不少工艺可成型具有双壁结构的制件,这种结构的制 件有较高的刚性、冲击韧性和抗弯能力。
形状和结构的简化 壁厚均一
避免应力集中 加强刚度的设计
抗变形设计 注塑件的精度
‹# ›
一、 形状和结构的简化
产品形状和结构复杂
产品形状和结构简单
模具结构的复杂性
熔体充模也就越容易
增加模具制造的难度
质量就越有保证
产品性能不稳定性和经济成 本
‹# ›
理想的产品简洁化设计基本原则:
①有利于成型 加工;
‹# ›
(3) 尺寸设计要考虑成型的可能性,不同的成型工艺对制件的尺寸 设计,包括尺寸大小,尺寸变化会有一定的限制。
‹# ›
二、壁厚均一的设计原则
• 在确定壁厚尺寸时,壁厚均一是一个重要原则。该 原则主要是从工艺角度以及由工艺导致的质量方面 的问题而提出来的。均匀的壁厚可使制件在成型过 程中,熔体流动性均衡,冷却均衡。壁薄部位在冷 却收缩上的差异,会产生一定的收缩应力,内应力 会导致制件在短期之内或经过一个较长时期之后发 生翘曲变形。 • 塑料件最通用料厚是2.5mm,大件适当增加,小件 减小,强烈建议通过增加翻边及加强筋的方式而不 是增加料厚来保证零件强度; PP塑料的壁厚范围 是0.6—3.5mm。
• 后果:塑料是对缺口和尖角之类比较敏感的材料, 在应力作用下,这些部位会逐渐产生微细裂纹, 随后逐步扩展到大的裂纹,而裂纹的不断延伸终 将导致制件的损坏。
‹# ›
避免应力集中应作为一条基本的准则
• 避免应力集中最直接最有效的方法就是在拐角、棱边、凹槽灯等轮 廓过渡与厚薄交接处采用圆弧过渡。
‹# ›
(a)为阶梯式过 渡,应尽力避免; (b)为锥形过渡, 比较好; (c)是圆弧过渡, 应是最好的。
‹# ›
(2)将尖角改为圆角处理,两个壁厚相同的壁面成直角的连接,破 坏了壁厚均一的原则。
转角处的最大厚度是壁厚的1.4倍,如果将内角处 理成圆角而外角仍是直角,则在转角处的最大厚 度(W)可增加到壁厚的1.6-1.7 倍。正确的设计 应是内外角均进行圆角处理,以确保壁厚均匀。 圆角处理还可避免应力集中,以及改善塑料成型 时熔体的流动性和成型性。
根据不同的壁厚和圆角半径对应的应力集中系数, 得出应力集中系数与半径R 与壁厚T之比的关系
图中曲线表明,半径R 与壁厚T之比,即R/T 在 0.6 以后,曲线趋于平缓,由此可知,内圆角之 半径应至少为壁厚的一半,最好为壁厚的0.60.75。
‹# ›
四、加强刚度的设计
刚性不足
外载和自重
引起变形、翘曲、蠕变
‹# ›
(3)嵌件的加强作用
• 在制件中设置金属嵌件,可以提高塑料制件局部或 整体的强度。
如汽车方向盘、活动手柄、塑料门窗框、 带有金属嵌件的塑料齿轮等。
‹# ›
(4)结构上的设计,在产品设计中,有几种 结构具有比较高的刚性/质量比。
① 蜂窝夹层结构:刚性的设计效果好,缺点是工艺上比较复杂,成 本和价格较高。
‹# ›
五、抗变形设计
两种能引起制件 变形的情况
由制件的内应力 引起的翘曲变形
由热效应引起的 热变形。
‹# ›
(一)由内应力引起的制件变形
• 这种变形由制件内的内应力所导致。 • 通常不均匀的内应力分布是翘曲变形的主要原因,而内应力的不
均匀分布则可能是加工条件(如温度、压力的不均匀分布,收缩 率的各向异性等)、材料组成(结晶型材料的百年形倾向较大)、 模具结构(特别是浇口设计)和制品形状共同作用的结果。
‹# ›
因壁厚不同,壁厚处的塑料完全固化后, 会对先行固化的薄壁部位施以拉力,导 致制件出现变形
‹# ›
办法。
‹# ›
采用加强筋来防止框形结构变形
‹# ›
‹# ›
壁厚不均匀造成制 件翘曲变形
‹# ›
不均匀壁厚部位设置圆 孔,由于收缩不均匀, 难以成为正圆。
壁厚不均匀时常用处理办法
(1)厚薄交接处的平稳过渡,当制件厚度不可避免需设计成不一致 时,在厚薄交接处应逐渐过渡,避免突变,厚度比例变化在一合适 的范围(一般不超过3:1)。
‹# ›
壁厚过渡形式
‹# ›
防止变形的措施
• 前述的避免应力集中以及刚性设计的一些措施,也都有助于防止或 者降低制件的变形。此外,设计时考虑防止产品变形,在形状上进 行规避。
‹# ›
矩形的薄壁容器的侧壁容易发生内凹变 形,为此可将侧壁设计得稍微外凸一些
‹# ›
深度较浅的盒类制品,为避免翘曲变形, 可将其底边设计成倒角形状
②节约原材料, 降低成本;
③简洁、美观;
‹# ›
简化设计的一些建议和提示
(1) 结构简单,形状对称,避免不规则的几何图形;
结 构 简 单 容 易 成 型
‹# ›
对 称 设 计
‹# ›
(2) 产品侧孔和侧壁内表面的凹凸形状成型困难,需要在产品成型 后进行二次加工,设计时应避免。
‹# ›
设 计 改 进 避 免 侧 向 抽 芯
‹# ›
(3)厚壁部位减薄,使厚壁趋于一致,壁厚差异大的制件可通过增 设工艺孔、开槽或设置加强筋的方式,使厚壁部位减薄,厚薄趋于 一致。
厚壁减薄
‹# ›
开槽
‹# ›
设置加强筋
三、避免应力集中
• 对制件上有孔洞、切口、拐角等几何不连续部位施 加一定的力,在这个部位的断面上将产生远比给予 的表观应力大得多的应力,这个现象称为应力集中。 局部产生的很大应力对于表现应力之比为应力集中 系数。
‹# ›
加强刚度
材料
形状和结 构
几何形状的改变
加强筋
嵌件的加强作用
‹# ›
(1)几何形状的改变
• 薄壳状的平板制件,将其表面设计成波纹形、瓦楞形、拱形、球形、 抛物面,其刚性比同样重量的平板要高得多
‹# ›
(2)加强筋的设计和运用
通过加强筋提高轴套扭转刚 性和弯曲刚性
‹# ›
容器沿口部位的设计起到了边缘增强 的作用,实质上这种突变的边缘可以 看作是加强筋的变异。