分离器液位自动控制系统的研制与应用
例析液位自控系统的应用

例析液位自控系统的应用一、引言在现在矿山选矿自动化系统中,液位自控技术已经被广泛使用。
其中基于超声波检测的液位自控方式作为众多液位检测技术中发展较快、应用较广的一种测量方式,开始越来越多的替代传统液位测量方式。
它是利用超声波在同种介质中传播速度相对恒定以及碰到障碍物能反射的原理研制而成的,具有非接触、高精度、适用范围广、寿命长等优点。
近年来,随着高速数字信号处理技术与微处理器技术的进步,超声波液位检测自控技术得到了长足的发展。
本篇主要介绍基于超声波检测的液位自控系统在罗河选厂的使用现状及未来在磨选分级优化自控系统中作用。
二、超声波液位检测的工作原理超声波测量方法应用最广泛的是脉冲回波法,它的基本原理是:发射声波传感器由脉冲信号激励发出超声波,通过传声介质传到被测液面,形成反射波;反射波再通过传声介质返回到接收传感器,传感器把声信号转换成电信号,由仪表计算出超声波从发射到接收所传播的时间,再根据超声波在介质中传播的速度,利用计算公式得出液位的高度。
如下图所示:其中,C是超声波在空气中的传播速度,随着温度、湿度及粉尘的变化而变化,在厂矿企业应用中,可以默认为不变的定值。
△t为超声波传感器从发射超声波到超声波接触被测液面返回至传感器的时间差。
可以得出液位的高度H为:H1 及H2 为厂房现场安装实际测量数据。
现场仪表将测量处理后的数据H转换成在显示屏上显示的液位高度数字或百分比数字。
同时,将液位信号转换成4-20mA电信号,传输至上位机PLC参与过程控制,并设置上下限报警。
三、基于超声波检测的液位自控系统现阶段在罗河选矿厂的使用及未来在磨矿分级优化系统中的作用。
现阶段罗河选矿厂液位检测自控系统现主要用于一次、二次矿浆池的矿浆液位的检测控制,其主要控制流程如下图2所示;安装在矿浆池上面的超声波液位计,在正常工作时,将接收的液位数据信号在主机内进行运算,再通过模数转换电路转换成4-20mA电信号,通过现场总线传输至PLC。
分离器液位自动控制系统的研制与应用

为了解决零散井站点的天然气和原油在分离过程中,因为不能自动调节和控制分离器内的液位,造成天然气进入储油罐或原油进入气管线的难题,利用分离器现有的部件,通过加装干簧管远传、数显表、记录仪、电磁阀、报警器等仪器,研发制造出了一种分离器液位自动控制系统。
该系统具有自动化程度高,实现了分离器自动完成气液分离,连续计量及液位超限报警等功能,避免了现有技术需要人工操作,值班员工24小时盯住液位计进行量油,一旦值班人员精力不集中,将会造成天然气管线内进入液体,储液罐内进入天然气等事故的发生。
关键词:自动控制,信号远传,运行安全,降本增效在油田开发过程中有大量的区块含油面积小,呈零散分布,区块间生产的油气不能进行汇集处理,只能在井站点自行气液分离,液体进入储液罐,通过罐车外运,天然气除自用外,多余的气量供给附近的用户。
通过人工来调节排液阀门的开度,使分离器进、出液量在相对时间内保持平衡,但因油井生产状态及用户用气量的不同,使分离器进、出液量不平衡,当进液量多,出液量少时,就会发生分离器内的液体进入到天然气管线内,堵塞气线,不但损坏设备造成经济损失,而且降低企业的声誉;当进液量少,出液量多,气、液一同从排液阀中排出,进入到储液罐内,使大量的天然气外泄,既损失了气量又对环境造成污染,还造成了安全隐患。
针对以上所述的困难,应研发、设计一种具有高度自动化分离器液位自动控制系统,从而解决现有技术中的难题。
一、改进思路及方案实施1.设计思路。
将分离器液体排出阀由普通阀门改为自动控制开关的电磁阀,原来由人工操作控制的分离器液位高度,实现由电信号自动控制,同时该系统具有自动报警功能,在值班室设有报警装置,当分离器计量排液系统不能自动排液,分离器内的液位超过上下警戒位时,报警系统开始启动运行,发出声光警报,提示工人及时进行排除。
通过在现有的计量系统基础上进行改动,在实现以上功能的同时,做到既不违反安全规定,又尽量减少投入。
尽量利用分离器现有的磁翻板液位计中的功能,根据磁翻板液位计内的磁浮标随分离器内液位高低发生移动,磁浮标移动到什么位置,就在什么位置发出磁力线的特性,在磁翻板液位计上下计量标高处及在分离器上下液位警戒位处磁感电器元件,当磁浮标达到计量标高时,磁感电器元件在磁浮标磁力线的作用上,通过仪表转换成控制电磁阀的电信号,实现分离器排液阀门根据高度的设定值实现自动开关;如果出现故障不能自行关闭和开启排液阀时,磁浮标将继续上行或下移,到达分离报警高度时,磁感电器元件转变成报警信号,值班室内的警铃或警灯开始运行,警示值班人员去排除故障,故障不排除,警示不停。
三相分离器自动控制系统的设计

中图分 类号 : T E 3 5 7
从油井开采 出来 的原油一 般都要 经过温度调
节、 油气 水 分离 、 脱 盐 脱 水 等 环节 , 使 原 油 中的含 水 量 以及 盐分 达 到一定 的指标 才能 进行 外输 。三相 分 离 器是 原 油集 输系统 中对原 油进 行油 气水 分 离处 理 的一种 主要 设 备 , 一 般 海 洋 油 气 处 理 平 台或 陆 地 油
现 场每 台调节 阀进行 手 动 控 制 , 以备 特殊 情 况 下使
用。
4 . 3 软件 设计
软 件设 计包 括 过程 控 制 及 画面 监控 两 部分 , 利 用 西 门子 S T E P 7软 件 编 程完 成 对 整 个 系统 的 自动 控制 , 利用 西 门子 WI N C C软 件 编 程 完 成 对 整 个 工 艺 流程 的运 行情 况进行 监控 。系 统软件 设计 具有 以
3 控制 系统组成
如 图 2所 示 , 控 制 系统 采 用 陆 地 D C S系 统 + 现场 监 控 计算 机 +P L C三 级 控制 模式 , 即 现场 P L C
2 工 艺 系统 介 绍
本设备包括一台三相分离器 , 设计处理量为: 原
油 l O 0 0 m。 / d , 天 然气 1 0 0 0 0 m。 / d 。人 l Y l 原 油 经 过 设
自动采集设备 运行 状态 和各种在 线仪表 的参数 , 并 对 数据 进 行 处 理 和 贮 存 , 通 过 MO D B U S协 议 供
现 场 监控 计 算 机 及 陆 地 D C S系 统调 用 。陆 地 D C S 系统 和 现 场监 控 计 算 机 则 随时 跟 踪 接 收 P L C 的数
油田气液分离器中应用的控制规律
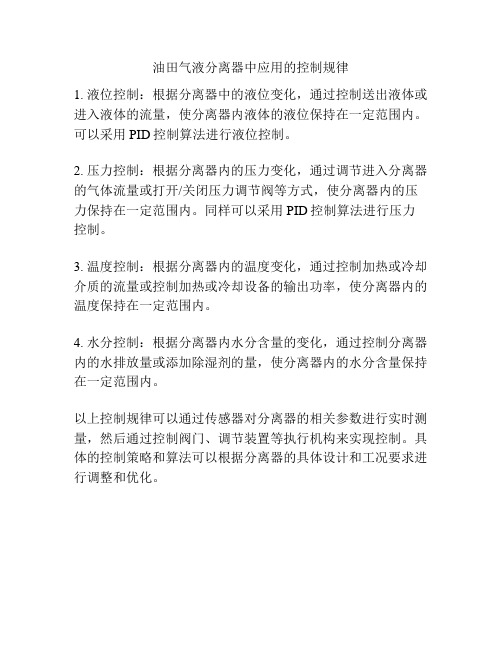
油田气液分离器中应用的控制规律
1. 液位控制:根据分离器中的液位变化,通过控制送出液体或进入液体的流量,使分离器内液体的液位保持在一定范围内。
可以采用PID控制算法进行液位控制。
2. 压力控制:根据分离器内的压力变化,通过调节进入分离器的气体流量或打开/关闭压力调节阀等方式,使分离器内的压力保持在一定范围内。
同样可以采用PID控制算法进行压力控制。
3. 温度控制:根据分离器内的温度变化,通过控制加热或冷却介质的流量或控制加热或冷却设备的输出功率,使分离器内的温度保持在一定范围内。
4. 水分控制:根据分离器内水分含量的变化,通过控制分离器内的水排放量或添加除湿剂的量,使分离器内的水分含量保持在一定范围内。
以上控制规律可以通过传感器对分离器的相关参数进行实时测量,然后通过控制阀门、调节装置等执行机构来实现控制。
具体的控制策略和算法可以根据分离器的具体设计和工况要求进行调整和优化。
液液分离器的原理

液液分离器的原理液液分离器(Liquid-Liquid Separator)是一种常见的分离技术,广泛应用于化工、制药、石化等领域。
其原理是利用两种密度不同的液体在重力作用下产生的分层现象,将混合液分离成两个不同的液相。
液液分离器的工作原理可以简单地概括为以下几个步骤:1.混合液进入分离器:混合液通过进料管道进入分离器,通常进料口位于分离器的顶部。
2.混合液分层:由于两种液体的密度不同,混合液在分离器中发生分层现象。
相对密度较大的液体沉积到底部,而相对密度较小的液体则浮在顶层。
3.收集液体:根据需要,分离器的底部和顶部分别安装有液体排出口,用于收集底层和顶层的液体。
4.控制液位:为了保证分离器的稳定运行,需要控制分离器中液位的高度。
通常,分离器内部设有液位计,可以监测分离器内的液位,并通过自动控制系统调整进料量、排放量等参数,以保持液位稳定。
液液分离器的原理十分简单,但是实际上操作起来并不容易。
在使用液液分离器时,需要注意以下几个问题:1.选择合适的分离器:液液分离器的尺寸和几何形状要根据混合液的性质和需要分离的液体相的比例来选择,以保证分离效果。
2.控制液位:分离器内液位的高度对分离效果有直接影响。
要严格控制液位高度,避免不必要的干扰。
3.调整操作参数:运行过程中需要根据实际情况调整进料量、排出量等操作参数,以达到最佳分离效果。
4.清洁维护:经常进行清洁和维护可以避免分离器内部产生积垢、结垢等问题,从而提高整个系统的效率和安全性。
综上所述,液液分离器采用两种不同密度的液相在重力作用下分层的原理,实现混合液的分离。
在应用时需要注意合适的分离器选择、液位控制、操作参数调整和定期维护等问题。
分离器液面和压力的控制

浅谈分离器液面和压力的控制郭长会侯志峰摘要分离器要能保持良好的分离效果,需对其液位和压力进行控制。
传统分离器液位和压力的控制采用定压控制技术。
在分离器的变压力液面控制中,利用浮子液面控制器带动油和气调节阀,使其联合动作,控制原油和天然气的液量,完成对分离器中液位的调节,而不对分离器的压力进行控制。
变压力的液面控制方法可以最大程度地减小油气出口阀的节流,减小分离器的压力,提高分离效果。
主题词三相分离器油气分离油水分离调节阀浮子油气分离器和油气水三相分离器在油田接转站和联合站中有着广泛的应用。
分离器要能保持良好的分离效果,需要对其液位和压力进行控制。
本文从减小工艺流程中的节流损失、节能降耗、提高分离效率的角度,分析了传统分离器液面和压力的控制工艺,提出了一种简单可靠、降低能耗的分离器变压力液面控制方法。
1.传统分离器液位和压力的控制1.1 油气两相分离器油气两相分离器将油气混合物来液分离成单一相态的原油和天然气,压力由天然气出口处的压力控制阀控制,液面由控制器控制的出油阀调节。
天然气出口处的压力控制阀通常是自力式调节阀或配套压力变送器、控制器、气源的气动薄膜调节阀等。
出油阀通常为配套液位传感器、控制器、气源的气动薄膜调节阀或浮子液面调节器操纵的出油调节阀等。
有的油气两相分离器是用气动薄膜调节阀控制分离器的压力,用浮子液面调节器操纵出油阀控制分离器液面。
1.2 油气水三相分离器油气水三相分离器在油井产物进行气液分离的同时,还能将原油中的部分水分离出来。
随着油田的开发,油井产出液的含水量逐渐增多,三相分离器的应用也逐渐增多。
结构不同,三相分离器的控制方法也不同。
两种典型分离器的控制原理如下:(1)油气水混合物进入分离器后,进口分流器把混合物大致分成汽液两相,液相进入集液部分。
集液部分有足够的体积使自由水沉降至底部形成水层,其上是原油和含有较小水滴的乳状油层。
原油和乳状油从挡板上面溢出。
挡板下游的油面由液面控制器操纵出油阀控制于恒定的高度。
液位控制系统毕业论文
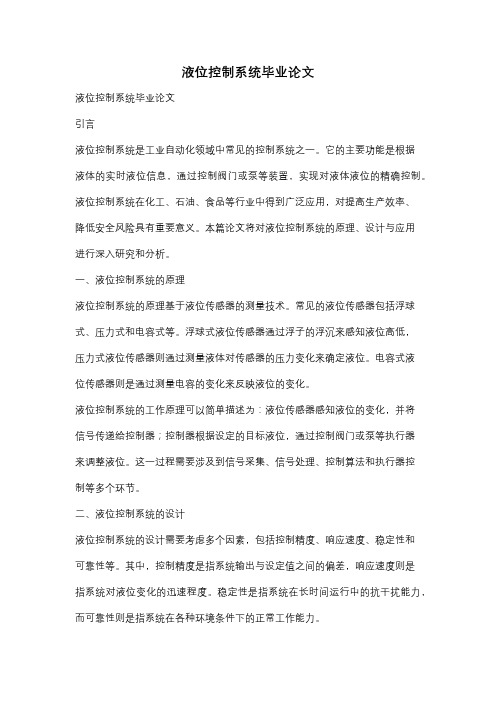
液位控制系统毕业论文液位控制系统毕业论文引言液位控制系统是工业自动化领域中常见的控制系统之一。
它的主要功能是根据液体的实时液位信息,通过控制阀门或泵等装置,实现对液体液位的精确控制。
液位控制系统在化工、石油、食品等行业中得到广泛应用,对提高生产效率、降低安全风险具有重要意义。
本篇论文将对液位控制系统的原理、设计与应用进行深入研究和分析。
一、液位控制系统的原理液位控制系统的原理基于液位传感器的测量技术。
常见的液位传感器包括浮球式、压力式和电容式等。
浮球式液位传感器通过浮子的浮沉来感知液位高低,压力式液位传感器则通过测量液体对传感器的压力变化来确定液位。
电容式液位传感器则是通过测量电容的变化来反映液位的变化。
液位控制系统的工作原理可以简单描述为:液位传感器感知液位的变化,并将信号传递给控制器;控制器根据设定的目标液位,通过控制阀门或泵等执行器来调整液位。
这一过程需要涉及到信号采集、信号处理、控制算法和执行器控制等多个环节。
二、液位控制系统的设计液位控制系统的设计需要考虑多个因素,包括控制精度、响应速度、稳定性和可靠性等。
其中,控制精度是指系统输出与设定值之间的偏差,响应速度则是指系统对液位变化的迅速程度。
稳定性是指系统在长时间运行中的抗干扰能力,而可靠性则是指系统在各种环境条件下的正常工作能力。
液位控制系统的设计需要根据具体的应用场景来确定。
在化工行业中,由于液体的性质多变,设计师需要考虑液体的温度、压力、粘度等因素对系统的影响。
在石油行业中,由于液位控制系统通常需要应对高温、高压等极端环境,设计师需要选择适合的材料和技术来保证系统的可靠性。
在食品行业中,设计师还需要考虑食品安全和卫生要求,确保系统不会对食品质量产生负面影响。
三、液位控制系统的应用液位控制系统在工业生产中有着广泛的应用。
在化工行业中,液位控制系统可以用于控制反应釜中液位的变化,确保反应过程的稳定性和安全性。
在石油行业中,液位控制系统可以用于储罐的液位控制,避免液位过高或过低带来的安全隐患。
浅谈钢水液位自动控制系统的实际运用

浅谈钢水液位自动控制系统的实际运用浅谈钢水液位自动控制系统的实际运用摘要:本文主要介绍了连铸检测装置结晶器液位的工作原理,特别列出了实际运用测量系统出现的故障及解决方法,阐述了系统的技术和特点,同时对整个系统的PID调节控制系统都做了简要的介绍。
关键词:PID;液位探测器;前言随着实际运用质量和效益的需要,炼钢连铸结晶器液位自动控制系统已成为现代化冶金企业重要的铸成局部。
我公司也已实现了连铸液位自动控制。
通过具体的实践对结晶器液位自动控制有了较大的理解。
1. 结晶器液位自动控制系统的组成1. 1结晶器液位检测由于结晶器是控制液位的设备,其工作条件很恶劣----高温,蒸汽,灰尘,震动等。
而且安装困难,所以我们选用的是同位素仪表。
由于测量技术的进步,同位素的剂量已越来越小,铯137放射源已完全能满足稳定.准确.测量的要求。
且对人体的危害已很小。
Cs-137有良好的渗透性和30年的半衰期。
放射源被双层不锈钢用氩弧焊方式密封起来并放入一放射棒内。
放射源棒被放入一注满了铅的铁制容器内。
液位探测器:液位探测器的中心检测元件是光电倍增管,测量原理是利用γ射线的高穿透能力。
安装在结晶外的铯137棒源发出的ν射线,穿过结晶器直射到安装在结晶器弧外侧的传感器内的闪烁体上,激发闪烁体发光。
当钢水液位增至最高时,射线被钢水全部挡住,射线射到传感器上的量最少。
反之最大,发光的次数跟放射量的多少成正比,这样,通过光电倍增数,准确记录闪烁体的发光次数就得到了液位信号。
每次使用前,要对仪表进行标定,控制范围是155mm,故距结晶器铜管上口50mm定为最高液位,距上口205mm定为最低液位,检测范围为155mm。
当结晶器内的钢水液位越高,对射线的阻挡能力就越强,探测器接收到的粒子数就越少,系统就认为液位高。
由于是采用线性棒源,这样标好之后,就可以按时间内的记数值的多少来表示液位的上下,到达钢水检测的目的。
二次仪表:SC3000是一种集成的专用PLC系统,用于结晶器钢水液位的检测及控制。
- 1、下载文档前请自行甄别文档内容的完整性,平台不提供额外的编辑、内容补充、找答案等附加服务。
- 2、"仅部分预览"的文档,不可在线预览部分如存在完整性等问题,可反馈申请退款(可完整预览的文档不适用该条件!)。
- 3、如文档侵犯您的权益,请联系客服反馈,我们会尽快为您处理(人工客服工作时间:9:00-18:30)。
为了解决零散井站点的天然气和原油在分离过程中,因为不能自动
调节和控制分离器内的液位,造成天然气进入储油罐或原油进入气管
线的难题,利用分离器现有的部件,通过加装干簧管远传、数显表、
记录仪、电磁阀、报警器等仪器,研发制造出了一种分离器液位自动
控制系统。
该系统具有自动化程度高,实现了分离器自动完成气液分离,连续计量及液位超限报警等功能,避免了现有技术需要人工操作,值班员工24小时盯住液位计进行量油,一旦值班人员精力不集中,
将会造成天然气管线内进入液体,储液罐内进入天然气等事故的发
生。
关键词:自动控制,信号远传,运行安全,降本增效
在油田开发过程中有大量的区块含油面积小,呈零散分布,区块间生产的油气不能进行汇集处理,只能在井站点自行气液分离,液体进入储液罐,通过罐车外运,天然气除自用外,多余的气量供给附近
的用户。
通过人工来调节排液阀门的开度,使分离器进、出液量在相对时间内保持平衡,但因油井生产状态及用户用气量的不同,使分离器进、出液量不平衡,当进液量多,出液量少时,就会发生分离器内的液体
进入到天然气管线内,堵塞气线,不但损坏设备造成经济损失,而且
降低企业的声誉;当进液量少,出液量多,气、液一同从排液阀中排出,进入到储液罐内,使大量的天然气外泄,既损失了气量又对环境
造成污染,还造成了安全隐患。
针对以上所述的困难,应研发、设计
一种具有高度自动化分离器液位自动控制系统,从而解决现有技术中
的难题。
一、改进思路及方案实施
1.设计思路。
将分离器液体排出阀由普通阀门改为自动控制开关的电磁阀,原来由人工操作控制的分离器液位高度,实现由电信号自动控制,同时该系统具有自动报警功能,在值班室设有报警装置,当分离器计量排液系统不能自动排液,分离器内的液位超过上下警戒位时,报警系统开始启动运行,发出声光警报,提示工人及时进行排除。
通过在现有
的计量系统基础上进行改动,在实现以上功能的同时,做到既不违反安全规定,又尽量减少投入。
尽量利用分离器现有的磁翻板液位计中的功能,根据磁翻板液位计内的磁浮标随分离器内液位高低发生移动,磁浮标移动到什么位
置,就在什么位置发出磁力线的特性,在磁翻板液位计上下计量标高处及在分离器上下液位警戒位处磁感电器元件,当磁浮标达到计量标高时,磁感电器元件在磁浮标磁力线的作用上,通过仪表转换成控制电磁阀的电信号,实现分离器排液阀门根据高度的设定值实现自动开关;如果出现故障不能自行关闭和开启排液阀时,磁浮标将继续上行
或下移,到达分离报警高度时,磁感电器元件转变成报警信号,值班
室内的警铃或警灯开始运行,警示值班人员去排除故障,故障不排除,警示不停。
2.组成及特征。
分离器液位自动控制系统主要由分离计量系统、信号传输系统、。