9-组件热斑效应的原因与防护之欧阳家百创编
光伏板热斑效应
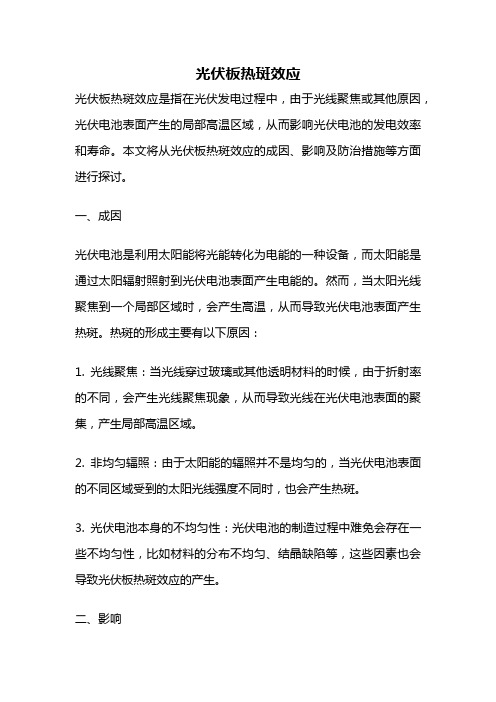
光伏板热斑效应光伏板热斑效应是指在光伏发电过程中,由于光线聚焦或其他原因,光伏电池表面产生的局部高温区域,从而影响光伏电池的发电效率和寿命。
本文将从光伏板热斑效应的成因、影响及防治措施等方面进行探讨。
一、成因光伏电池是利用太阳能将光能转化为电能的一种设备,而太阳能是通过太阳辐射照射到光伏电池表面产生电能的。
然而,当太阳光线聚焦到一个局部区域时,会产生高温,从而导致光伏电池表面产生热斑。
热斑的形成主要有以下原因:1. 光线聚焦:当光线穿过玻璃或其他透明材料的时候,由于折射率的不同,会产生光线聚焦现象,从而导致光线在光伏电池表面的聚集,产生局部高温区域。
2. 非均匀辐照:由于太阳能的辐照并不是均匀的,当光伏电池表面的不同区域受到的太阳光线强度不同时,也会产生热斑。
3. 光伏电池本身的不均匀性:光伏电池的制造过程中难免会存在一些不均匀性,比如材料的分布不均匀、结晶缺陷等,这些因素也会导致光伏板热斑效应的产生。
二、影响光伏板热斑效应的产生会对光伏电池的发电效率和寿命产生影响。
1. 发电效率:当光伏电池表面产生热斑时,会导致该区域的电流和电压下降,从而影响了光伏电池的发电效率。
2. 寿命:光伏板热斑效应会导致光伏电池的热应力增大,从而导致光伏电池的寿命缩短。
三、防治措施为了减少光伏板热斑效应的产生,需要采取相应的防治措施。
1. 优化光伏电池结构:可以通过优化光伏电池的结构、材料、制造工艺等方面,减少光伏电池本身的不均匀性,从而降低光伏板热斑效应的产生。
2. 选择适当的材料:可以选择透过率较高的玻璃或其他材料,减少光线的聚焦现象,从而减少光伏板热斑效应的产生。
3. 风冷散热:可以通过在光伏电池表面安装散热器或其他散热设备,将热量散发出去,减少局部高温区域的产生。
4. 防止非均匀辐照:可以通过安装防反射膜等设备,使太阳能辐射均匀分布在光伏电池表面,从而减少光伏板热斑效应的产生。
光伏板热斑效应是光伏电池中的一种常见问题,产生的原因主要包括光线聚焦、非均匀辐照和光伏电池本身的不均匀性等。
组件热斑效应

组件热斑效应众所周知为了使组件达到最高的功率输出,光伏组件中的单体电池须具有相似的特性,对于组串及阵列也是如此。
但在实际使用过程中,可能出现电池裂纹或不匹配、内部连接失效、局部被遮光或弄脏等情况,导致一个或一组电池的特性与整体不谐调。
失谐电池不但对组件输出没有贡献,而且会消耗其他电池产生的能量,导致局部过热。
这种现象称为热斑效应。
当组件被短路时,内部功率消耗最大,热斑效应也最严重。
热斑效应不仅会严重影响组件的性能和使用寿命,还有可能引发燃烧及火灾,给电站带来财产损失和人员伤害,因此有效的判断热斑效应的发生及严重性是电站长期的工作。
下左图是电站现场发生的组件背板灼烧现象。
对于热斑效应的判断,切记勿用手去触摸组件,因为当热斑发生时,组件的局部温度非常高,极有可能造成灼伤。
运维人员应选择相应的测试仪器去对组件整体温度进行测试判断,并提早发现组件是否已经存在局部温度异常。
此时选用最方便最快捷的测试仪器即是红外热像仪。
红外热像仪可以全方位拍摄整个组件甚至阵列的温度分布情况,及时发现热斑所在。
并通过软件全面了解组件当前的发热情况,对于明显有热斑的组件可以清楚判断,同时可对组件中尚不明显的热点进行分析判断。
如上右图所示。
从图中可看出组件靠近地面的部位均存在一定程度的热斑效应,这是热斑效应发生概率较高的部位,原因是:(1)这部分组件最容易被遮挡,被遮挡的时间也最长;(2)灰尘覆盖最严重,有时候清洗的不干净时,这部分囤积的灰尘也越多。
(3)靠近地面,通风较差,散热不佳。
因此发生热斑效应的概率较高。
当然引起热斑效应的原因并不止这些,组件本身的性能差别,是否存在隐裂,是否有损伤等等也会造成热斑效应。
HT测试仪器建议在运维过程中,对于已经存在热斑效应的组件,需要对其进行I-V曲线测试判断其功率下降的比例,对于热斑效应较严重的组件可考虑更换组件,避免对整个组串造成过大影响。
对于尚未存在热斑效应的组件,最好进行抽查,对部分组件的I-V曲线进行测试,这样可以提前发现造成组件功率下降的原因,并及时改进。
组件热斑效应的原因与防护
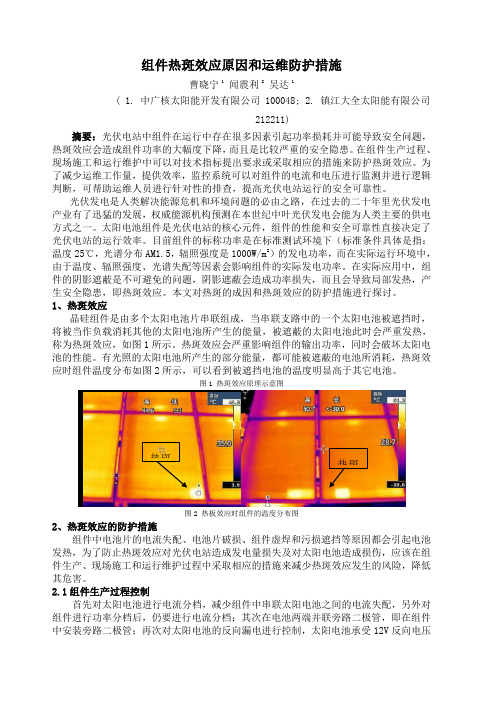
组件热斑效应原因和运维防护措施曹晓宁1 闻震利2 吴达 1( 1. 中广核太阳能开发有限公司 100048; 2. 镇江大全太阳能有限公司212211)摘要:光伏电站中组件在运行中存在很多因素引起功率损耗并可能导致安全问题,热斑效应会造成组件功率的大幅度下降,而且是比较严重的安全隐患。
在组件生产过程、现场施工和运行维护中可以对技术指标提出要求或采取相应的措施来防护热斑效应。
为了减少运维工作量,提供效率,监控系统可以对组件的电流和电压进行监测并进行逻辑判断,可帮助运维人员进行针对性的排查,提高光伏电站运行的安全可靠性。
光伏发电是人类解决能源危机和环境问题的必由之路,在过去的二十年里光伏发电产业有了迅猛的发展,权威能源机构预测在本世纪中叶光伏发电会能为人类主要的供电方式之一。
太阳电池组件是光伏电站的核心元件,组件的性能和安全可靠性直接决定了光伏电站的运行效率。
目前组件的标称功率是在标准测试环境下(标准条件具体是指:温度25℃,光谱分布AM1.5,辐照强度是1000W/m 2)的发电功率,而在实际运行环境中,由于温度、辐照强度、光谱失配等因素会影响组件的实际发电功率。
在实际应用中,组件的阴影遮蔽是不可避免的问题,阴影遮蔽会造成功率损失,而且会导致局部发热,产生安全隐患,即热斑效应。
本文对热斑的成因和热斑效应的防护措施进行探讨。
1、热斑效应晶硅组件是由多个太阳电池片串联组成,当串联支路中的一个太阳电池被遮挡时,将被当作负载消耗其他的太阳电池所产生的能量,被遮蔽的太阳电池此时会严重发热,称为热斑效应,如图1所示。
热斑效应会严重影响组件的输出功率,同时会破坏太阳电池的性能。
有光照的太阳电池所产生的部分能量,都可能被遮蔽的电池所消耗,热斑效应时组件温度分布如图2所示,可以看到被遮挡电池的温度明显高于其它电池。
图 1 热斑效应原理示意图图2 热板效应时组件的温度分布图 2、热斑效应的防护措施组件中电池片的电流失配、电池片破损、组件虚焊和污损遮挡等原因都会引起电池发热,为了防止热斑效应对光伏电站造成发电量损失及对太阳电池造成损伤,应该在组件生产、现场施工和运行维护过程中采取相应的措施来减少热斑效应发生的风险,降低其危害。
简述热斑效应,如何防止热斑效应
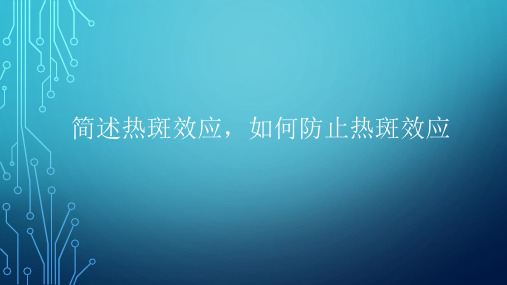
热斑效ห้องสมุดไป่ตู้的概念
太阳能电池(组件)通常安装在地域开阔、阳光充足的地带,在长期使用中 难免落上飞鸟、尘土、落叶等遮挡物,这些遮挡物在太阳电池组件上就形成 了阴影,在大型太阳电池组件方阵中行间距不适合也能互相形成阴影。 , 但组件的其余部分仍处于阳光暴晒之下,这样局部被遮挡的太阳能电池(或 组件)就要由未被遮挡的那部分太阳能电池(或组件)来提供负载所需的功 率,使该部分太阳电池如同一个工作在反向偏置下的二极管,其电阻和压降 较大,从而消耗功率而导致发热,这就是热斑效应。
防止热斑效应
• 为了防止太阳电池由于热斑效应而遭受破坏,最好在太阳电池组件的正负极
间并联一个旁路二极管,以避免光照组件所产生的能量被受遮蔽的组件所消 耗。
• 有时为了防止鸟类的排泄物沾污方阵表面,还要在太阳电池方阵顶端安装驱
鸟装置
• 但是光伏组件热斑需要专用的热成像仪方可检测,通过光伏面板温度差,来
热斑效应的危害
在实际应用中,太阳能电池一般是由多块电池组件串联或并联起来,以获得所 期望的电压或电流的。为了达到较高的光电转换效率,电池组件中的每一块电 池片都须具有相似的特性。在使用过程中,可太能阳电出池现各一组件个故或障一率 组电池不匹配, 如:出现裂纹、内部连接失效或遮光等情况,导致其特性与整体不谐调。 在一 定条件下,一串联支路中被遮蔽的太阳电池组件,将被当作负载消耗其他有光 照的太阳电池组件所产生的能量。这种效应能严重地破坏太阳能电池,有光照 的太阳能电池所产生的部分能量,都可能被遮蔽的电池所消耗,严重的可能使 焊点融化、封装材料破坏,甚至会使整个组件失效。
检测判断面板是否存在隐患。如今的光伏电站大多为人工巡检,由于电站面 积庞大且受地形影响因素,需要耗费大量时间人力成本,容易产生巡检盲点, 建议采用配备高精度热成像红外相机的无人机进行检测。
关于组件热斑产生的原因、问题电池的来源及相应对策
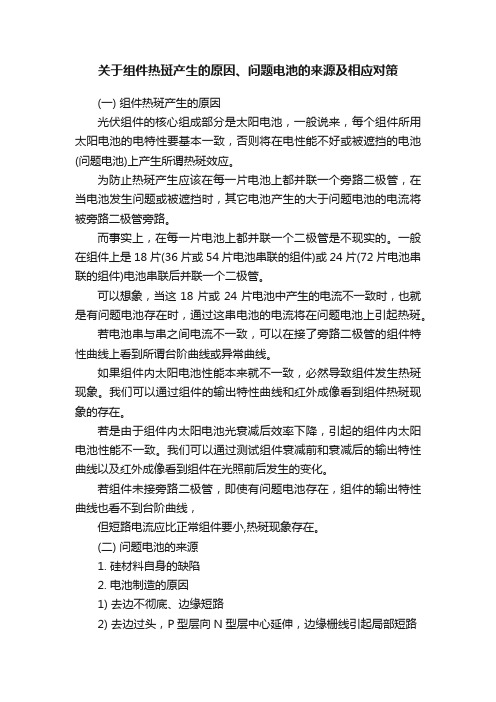
关于组件热斑产生的原因、问题电池的来源及相应对策(一) 组件热斑产生的原因光伏组件的核心组成部分是太阳电池,一般说来,每个组件所用太阳电池的电特性要基本一致,否则将在电性能不好或被遮挡的电池(问题电池)上产生所谓热斑效应。
为防止热斑产生应该在每一片电池上都并联一个旁路二极管,在当电池发生问题或被遮挡时,其它电池产生的大于问题电池的电流将被旁路二极管旁路。
而事实上,在每一片电池上都并联一个二极管是不现实的。
一般在组件上是18片(36片或54片电池串联的组件)或24片(72片电池串联的组件)电池串联后并联一个二极管。
可以想象,当这18片或24片电池中产生的电流不一致时,也就是有问题电池存在时,通过这串电池的电流将在问题电池上引起热斑。
若电池串与串之间电流不一致,可以在接了旁路二极管的组件特性曲线上看到所谓台阶曲线或异常曲线。
如果组件内太阳电池性能本来就不一致,必然导致组件发生热斑现象。
我们可以通过组件的输出特性曲线和红外成像看到组件热斑现象的存在。
若是由于组件内太阳电池光衰减后效率下降,引起的组件内太阳电池性能不一致。
我们可以通过测试组件衰减前和衰减后的输出特性曲线以及红外成像看到组件在光照前后发生的变化。
若组件未接旁路二极管,即使有问题电池存在,组件的输出特性曲线也看不到台阶曲线,但短路电流应比正常组件要小,热斑现象存在。
(二) 问题电池的来源1. 硅材料自身的缺陷2. 电池制造的原因1) 去边不彻底、边缘短路2) 去边过头,P型层向N型层中心延伸,边缘栅线引起局部短路3) 烧结不良,正电极或背电极与硅片接触不良,串联电阻增大4) 烧结过度,即将使PN结烧透,短路以上几种有可能在分选测试时尚未暴露,而做成组件后在长期的使用过程中,逐渐变化而导致愈演愈烈3. 同一档次的电池片性能不一致1) 电池分选测试时的误判a) 分选测试仪自身误差b) 测试仪与测试仪之间的差异c) 分选测试仪的误动作2) 电池自身的衰减不一致3) 人为的混片如电池上信息不准确,有可能贴错标签、混包,电池外观检验时的混片等4. 组件制造的原因1) 焊接前混片或补片时混片2) 电池片自身的隐裂3) 手工焊接过程造成的裂片或隐裂片,机器焊接曲线异常的比例一般小于手工焊接4) 虚焊,每天的巡检报告中几乎都有焊接不良的报道5) 组件生产过程中产生的隐裂,如玻璃弯曲引起裂片或温度过高时装框,万向球顶裂电池6) 返修组件时的焊接不良,互连条之间的搭接,接触电阻大7) 组件中异物引起短路8) 焊背面时,正面互连条脱开,使互连条与电池间存在锡粒,层压造成电池破裂(三) 已经采取的措施1. 电池生产线采用72片一包的包装,避免组件生产线再次数片带来的混片2. 电池生产线先外观检验,后测试分选,防止测试分选后再外观检验造成混片3. 组件生产时用整包的电池片,不用散包,防止混片4. 组件补片原则,一定要补同一档次的电池,(正在准备试75片一包的试验)5. 焊接前检查隐裂片6. 焊串模板定期检查,防止互连条脱焊7. 严格检查异物8. 加强虚焊检查,防止虚焊9. 搬运时尽量减少玻璃弯曲10. 大组件采用4毫米玻璃,以减少弯曲,增加强度11. 搬运周转车改为玻璃垂直放置12. 不允许>50℃时装框13. 返修时不允许互连条对接14. 散包电池必须重新分选测试,凑成整包后再做组件15. 库存超过一定期限的电池在做组件前应经过二次分选测试16. 测试时,组件一定要在规定温度范围内17. 给出发现曲线异常后的处理方法,防止不良组件流到客户手中18. 电池先光衰减后再分选测试(正在试验实施中)虽然采取了以上部分措施,目前曲线异常依然存在,很多组件都有不同程度的热斑,有些措施实施起来有些难度,进展还需要时间和相关设备。
光伏组件热斑效应研究

光伏组件热斑效应研究光伏组件热斑效应是指在光伏组件工作过程中,由于各种原因导致组件表面出现局部热斑现象。
这种现象会对光伏组件的性能产生不利影响,因此对光伏组件热斑效应进行研究具有重要意义。
光伏组件是将太阳光转化为电能的装置,其工作原理是利用光伏效应将光能转化为电能。
在正常工作情况下,光线通过光伏组件的表面玻璃覆盖层,进入光伏电池层,然后被光伏电池层吸收并转化为电能。
然而,光伏组件在工作过程中会受到多种因素的影响,从而导致热斑效应的产生。
光伏组件的表面玻璃覆盖层具有一定的吸收性,会吸收部分光线并将其转化为热能。
这些被吸收的光线会在玻璃覆盖层内部产生热斑,从而使组件局部温度升高。
其次,光伏电池层的材料本身也会存在一定的光吸收能力,这会导致光伏电池层吸收光线后产生热斑。
此外,光伏组件的背面通常有一层金属反射层,该反射层会将未被光伏电池层吸收的光线反射回来,从而形成光热效应。
光伏组件热斑效应的存在对组件性能产生了多重影响。
首先,热斑会使组件局部温度升高,从而导致光伏电池层的工作温度升高。
光伏电池的工作效率与温度密切相关,温度升高会降低光伏电池的转换效率。
此外,热斑还会引起光伏电池层的热应力,从而降低光伏组件的可靠性和寿命。
为了研究光伏组件热斑效应并寻找相应的解决办法,科研人员进行了大量的实验和理论分析。
实验方面,他们通过在实验室中搭建光伏组件测试平台,模拟不同工况下的光伏组件工作情况,然后通过红外热成像技术等手段对组件表面的温度分布进行测量和分析。
理论方面,他们运用热传导和光学等相关理论,建立了热斑效应的数学模型,从而对热斑的形成机制进行解释和预测。
根据研究结果,科研人员提出了一些减轻光伏组件热斑效应的方法。
首先是优化组件结构和材料,使其具有更好的光吸收和热传导性能,从而减少热斑的产生。
其次是改进光伏组件的散热设计,增加散热设备和通风孔,提高组件的散热效果。
另外,科研人员还提出了一些新颖的解决方案,如利用热管技术和热电联供等方法来处理热斑问题。
组件缺陷原因分析及对策
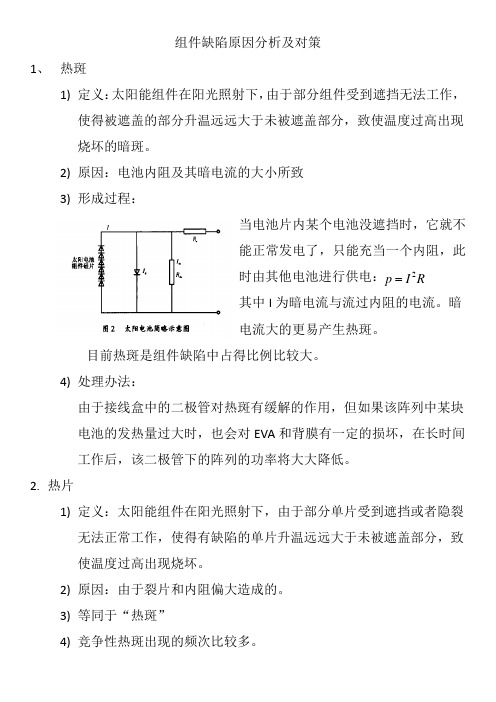
组件缺陷原因分析及对策1、 热斑1) 定义:太阳能组件在阳光照射下,由于部分组件受到遮挡无法工作,使得被遮盖的部分升温远远大于未被遮盖部分,致使温度过高出现烧坏的暗斑。
2) 原因:电池内阻及其暗电流的大小所致3) 形成过程:当电池片内某个电池没遮挡时,它就不能正常发电了,只能充当一个内阻,此时由其他电池进行供电: 其中I 为暗电流与流过内阻的电流。
暗电流大的更易产生热斑。
目前热斑是组件缺陷中占得比例比较大。
4) 处理办法:由于接线盒中的二极管对热斑有缓解的作用,但如果该阵列中某块电池的发热量过大时,也会对EVA 和背膜有一定的损坏,在长时间工作后,该二极管下的阵列的功率将大大降低。
2. 热片1) 定义:太阳能组件在阳光照射下,由于部分单片受到遮挡或者隐裂无法正常工作,使得有缺陷的单片升温远远大于未被遮盖部分,致使温度过高出现烧坏。
2) 原因:由于裂片和内阻偏大造成的。
3) 等同于“热斑”4) 竞争性热斑出现的频次比较多。
RI p 23.接线盒1)缺陷种类:二极管烧坏、接线盒功率增大、盒体破裂、水汽进入2)3)引线断裂现象:引线出现一根或多跟在引线开口处断裂。
步骤:①、用刀片在已断裂引线下方切出一块,露出残留引线②、取一根新引线,将电烙铁加热至380℃,在残留引线上焊新引线③、用剪刀将新焊上的引线剪成与其余引线相同长度4.铝框1)缺陷类型:铝框脱落、铝框变形5.内部电极接触不良(虚焊、漏焊等)1)原因:前期工艺问题、后期腐蚀造成2)对策:先找到断点(若无法肉眼发现,可1/2法逐个测电压查出),使用4mm玻璃钻头在断点处打孔,打孔时只需打通玻璃即可,切不可太深;清理断点处赃物,使用铜粉或者铝粉填充该处,之后使用4mm铜皮紧紧压在圆孔上,然后使用玻璃胶密封。
6.温度对组件的影响:1)电池电压温度系数:-(2.0---2.2)mv/℃2)西宁地区数据:夏天组件背表面温度可达70度,此时工作温度达100度,此时该组件的开路电压与额定值相比将降低:7.受遮挡时的I-V曲线有旁路二极管时(受遮挡)8、层压件返工工艺1)一般盖背板类a)背板划伤现象:层压后的TPT上有一道或多道被尖锐物品划伤割伤的划痕步骤:①、将层压件用抹布沾上酒精擦洗干净②、风干酒精后铺上EVA,在规定位置开缝③、盖上TPT,用美纹胶带贴住引线,并在层压件尾部粘美纹胶固定④、将组件抬入层压机内,盖上高温布层压,层压后冷却50℃削边⑤、、未冷却不可将组件翻倒过来,否则会造成凹坑b)鼓包现象:层压后的TPT上有明显的凸起感,可见,可触觉。
光伏组件中的“热斑效应”原理
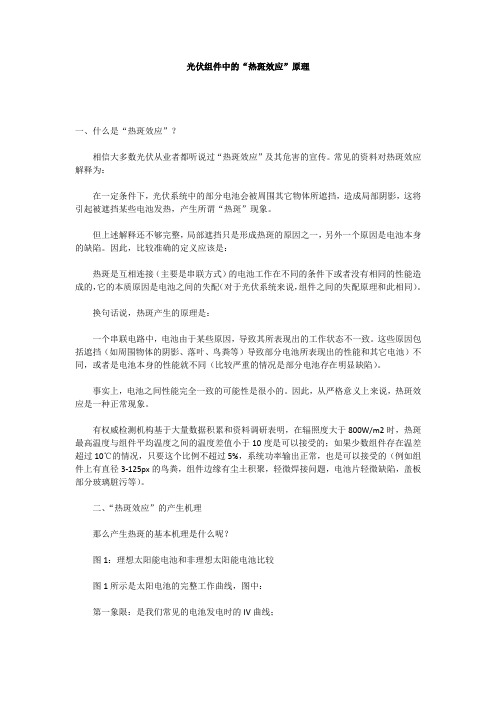
光伏组件中的“热斑效应”原理一、什么是“热斑效应”?相信大多数光伏从业者都听说过“热斑效应”及其危害的宣传。
常见的资料对热斑效应解释为:在一定条件下,光伏系统中的部分电池会被周围其它物体所遮挡,造成局部阴影,这将引起被遮挡某些电池发热,产生所谓“热斑”现象。
但上述解释还不够完整,局部遮挡只是形成热斑的原因之一,另外一个原因是电池本身的缺陷。
因此,比较准确的定义应该是:热斑是互相连接(主要是串联方式)的电池工作在不同的条件下或者没有相同的性能造成的,它的本质原因是电池之间的失配(对于光伏系统来说,组件之间的失配原理和此相同)。
换句话说,热斑产生的原理是:一个串联电路中,电池由于某些原因,导致其所表现出的工作状态不一致。
这些原因包括遮挡(如周围物体的阴影、落叶、鸟粪等)导致部分电池所表现出的性能和其它电池)不同,或者是电池本身的性能就不同(比较严重的情况是部分电池存在明显缺陷)。
事实上,电池之间性能完全一致的可能性是很小的。
因此,从严格意义上来说,热斑效应是一种正常现象。
有权威检测机构基于大量数据积累和资料调研表明,在辐照度大于800W/m2时,热斑最高温度与组件平均温度之间的温度差值小于10度是可以接受的;如果少数组件存在温差超过10℃的情况,只要这个比例不超过5%,系统功率输出正常,也是可以接受的(例如组件上有直径3-125px的鸟粪,组件边缘有尘土积聚,轻微焊接问题,电池片轻微缺陷,盖板部分玻璃脏污等)。
二、“热斑效应”的产生机理那么产生热斑的基本机理是什么呢?图1:理想太阳能电池和非理想太阳能电池比较图1所示是太阳电池的完整工作曲线,图中:第一象限:是我们常见的电池发电时的IV曲线;第二象限:代表给太阳电池加反向偏压时,电池由发电变为耗电(分界点是纵轴短路电流处);第四象限:代表给太阳电池加正向偏压,正向电压产生的电流方向是从P区流向N区,和光生电流方向相反,所以当正向偏压大于电池的开路电压时,电流反向,电池由发电变为耗电(分界点是横轴开路电压处)。
- 1、下载文档前请自行甄别文档内容的完整性,平台不提供额外的编辑、内容补充、找答案等附加服务。
- 2、"仅部分预览"的文档,不可在线预览部分如存在完整性等问题,可反馈申请退款(可完整预览的文档不适用该条件!)。
- 3、如文档侵犯您的权益,请联系客服反馈,我们会尽快为您处理(人工客服工作时间:9:00-18:30)。
组件热斑效应原因和运维防护措施
欧阳家百(2021.03.07)
曹晓宁1闻震利2吴达1
( 1. 中广核太阳能开发有限公司 100048;2. 镇江大全
太阳能有限公司 212211)
摘要:光伏电站中组件在运行中存在很多因素引起功率损耗并可能导致安全问题,热斑效应会造成组件功率的大幅度下降,而且是比较严重的安全隐患。
在组件生产过程、现场施工和运行维护中可以对技术指标提出要求或采取相应的措施来防护热斑效应。
为了减少运维工作量,提供效率,监控系统可以对组件的电流和电压进行监测并进行逻辑判断,可帮助运维人员进行针对性的排查,提高光伏电站运行的安全可靠性。
光伏发电是人类解决能源危机和环境问题的必由之路,在过去的二十年里光伏发电产业有了迅猛的发展,权威能源机构预测在本世纪中叶光伏发电会能为人类主要的供电方式之一。
太阳电池组件是光伏电站的核心元件,组件的性能和安全可靠性直接决定了光伏电站的运行效率。
目前组件的标称功率是在标准测试环境下(标准条件具体是指:温度25℃,光谱分布AM1.5,辐照强度是1000W/m2)的发电功率,而在实际运行环境中,由于温度、辐照强度、光谱失配等因素会影响组件的实际发电功率。
在实际应用中,组件的阴影遮蔽是不可避免的问题,阴影遮蔽会造成功率损失,而且会导致局部发热,产生安全隐患,即热斑效
应。
本文对热斑的成因和热斑效应的防护措施进行探讨。
1、热斑效应
晶硅组件是由多个太阳电池片串联组成,当串联支路中的一个太阳电池被遮挡时,将被当作负载消耗其他的太阳电池所产生的能量,被遮蔽的太阳电池此时会严重发热,称为热斑效应,如图1所示。
热斑效应会严重影响组件的输出功率,同时会破坏太阳电池的性能。
有光照的太阳电池所产生的部分能量,都可能被遮蔽的电池所消耗,热斑效应时组件温度分布如图2所示,可以看到被遮挡电池的温度明显高于其它电池。
图1 热斑效应原理示意图
图2 热板效应时组件的温度分布图
2、热斑效应的防护措施
组件中电池片的电流失配、电池片破损、组件虚焊和污损遮挡等原因都会引起电池发热,为了防止热斑效应对光伏电站造成发电量损失及对太阳电池造成损伤,应该在组件生产、现场施工和运行维护过程中采取相应的措施来减少热斑效应发生的风险,降低其危害。
2.1组件生产过程控制
热斑
热斑
首先对太阳电池进行电流分档,减少组件中串联太阳电池之间的电流失配,另外对组件进行功率分档后,仍要进行电流分档;其次在电池两端并联旁路二极管,即在组件中安装旁路二极管;再次对太阳电池的反向漏电进行控制,太阳电池承受12V 反向电压时漏电流不超过 1.5A,最后,对电池的隐裂和组件焊接工艺可靠性进行控制,组件在生产过程中需进行两次电致发光测试(EL测试)。
电流分档:如果串联太阳电池的工作电流相差较大,则电池串的总电流将受到小电流电池的限制。
则大电池产生的额外电流(比小电流电池高出的那部分电流)将变成小电流电池的前置偏压。
当数量很多的串联电池一起把前置偏压变成小电流电池的反向电压时,在小电流电池处将会有大的能量耗散,这就是热点加热现象。
巨大的能量消耗在一片小小的区域,局部过热就会发生,或者叫“热点”,极端情况下导致破坏性影响,例如电池或玻璃破碎、焊点熔化或电池性能的退化。
针对这个问题,电池片进行效率分档的同时,对效率相同的电池片进行电流分档,同一档位的电流相差不超过0.1A。
在光伏电站的设计中,组件要先进行串联组成一个组件串,然后通过汇流箱汇流,最后接入逆变器,因此也应减少组件之间的电流失配,组件进行功率分档,然后对同一功率档位的组件进行工作电流分档,同一档位的电流相差不超过0.1A。
旁路二极管保护:在太阳电池并联一个旁路二极管,当电池正常工作时,旁路二极管承受方向电压,处于反向截止状态,当
电池被遮挡时,旁路二极管会导通,起到分流的作用,可以避免光照组件所产生的能量被受遮蔽的组件全部消耗,同时起到保护电池的作用,原则上每个电池片应并联一个旁路二极管,以便更好保护并减少在非正常状态下无效电池片数目,但因为旁路二极管价格成本的影响和暗电流损耗以及工作状态下压降的存在,目前由60片电池片封装成的多晶硅组件是每二十个电池可并联一个旁路二极管。
组件的电路结构如图3所示。
图3 晶硅组件电路结构图
太阳电池漏电流控制:旁路二极管作为组件的保护元件,可以提高组件被遮挡时的安全可靠性,旁路二极管的保护原理就是依赖其单向导电的特性,而旁路二极管两端的电压是由与之并联的电池片的电流电压特性决定的,在被遮挡情况下,电池片的暗特性决定了旁路二极管两端的电压极性,也决定了旁路二极管能否导通起到保护作用。
当组件被遮挡时,若要旁路二极管导通,则被遮挡电池两端的压降应大于与同一个旁路二极管并联且未被遮挡电池的电压之和,因此太阳电池的反向漏电流要足够小,否则电池被遮挡时旁路二极管导通需要较大的电流,被遮挡电池的发热较大,在光照条件较差的情况,旁路二极管可能会无法导通,起不到保护作用;在极端情况下,例如电池在承受反向12V 电压时的漏电流大小超过其短路电流,则电池在被遮挡时旁路二极管无法导通。
对于晶硅电池片的漏电流大小的控制标准,有的研究人员曾利用软件模拟和试验验证的方法进行分析,结果表明电池片的在承受12V反向电压时漏电流应小于 1.9A,否则旁路
二极管在电池被遮挡时不能导通起到保护作用。
EL测试:组件的虚焊、过焊等都可能导致焊点接触电阻过大,造成局部发热;硅片的弯曲和扭曲与组件生产工艺过程可能引起电池片隐裂,在户外使用时,裂纹将会演变为碎片,导致组件功率损失甚至开路,严重影响组件的使用寿命和可靠性。
在组件生产过程中,在层压工艺前后对组件进行两次EL测试,用以监控焊接质量和组件的隐裂。
2.2 现场施工过程控制
在光伏电站的施工现场,安装组件时主要注意两点,第一是杜绝搬运和安装组件时野蛮施工,不能蹬踏、拖拽及乱摔组件,以免产生隐裂;第二是在进行组件安装时,根据组件包装箱上电流分档标示,保证同一个支架上的组件是相同的电流档位。
2.3、运行维护措施
在实际组件的实际运行中,灰尘遮蔽、组件破损等原因都会引起热斑效应,运维人员应对电站进行必要巡检,对于灰尘遮蔽严重时应及时清洗组件,而且特别注意要避免组件局部清洗不干净,因此组件的遮蔽面积比例与造成的功率损失比例不对等,例如遮蔽一片电池(即面积的1/60)会引起功率损失1/3,因此如图4中的情况一定要杜绝。
对于光伏电站中以外导致的破损组件应立即予以更换,例如图5中所示以外碰撞导致组件玻璃破碎。
图4 局部清洗不干净的组件
图5 玻璃破损组件
当组件发生热斑效应时,电池片的温度会明显升高,在日常
维护中可以通过监测阵列的温度来进行判别。
在组件采购的技术协议中,已要求组件厂家提供备品备件、钳表、红外热成像仪等设备,便于日常维护和检修。
针对组件的热斑效应问题,可以使用红外热成像仪监测组件阵列的温度,如果发现局部发热点,如图4所示,应该检查发热原因,如果是污损遮蔽引起,应对组件进行清洗,如果是组件自身问题,应更换损坏组件。
图4组件温度红外成像图
3、组件运行情况监测
在大型光伏电站中都采用集中逆变的方式,即一台逆变器控制多个组件串,大型光伏电站中常用逆变器的规格为500KW。
光伏并网逆变器均为电流型逆变器,即逆变器控制的组件串的工作电压相同,若某一组件串出现热斑,那么其电流与其它组串的电流会有明显差别,目前汇流箱会采集各个组串的电流值和电压值,并通过通讯模块传到监控后台,监控后台对每串的电流电压的不平衡度进行逻辑判断,对于电流异常的组件进行提示,运维人员可以针对性进行排查,保证光伏电站安全和可靠的运行。
4、结论
阴影遮挡、组件破损等原因都会导致电流失配,进而导致热斑效应,可在组件生产阶段、安装阶段和电站运营阶段采取措施对组件热斑效应的风险和造成的损失进行控制,同时可以通过对组件串的电流和电压进行监测来帮助对热板效应的排查,提高光伏电站的可靠性。