游梁式抽油机设计计算
游梁式抽油机的设计.

绪论CYJY12-4.8-73HB型抽油机设计1 绪论1.1抽油机的应用油田开采原油的方法分为两类:一类是利用地层本身的能量来举升原油,称为自喷采油法,常见于新开发且储量大的一些油田;另一类是到了油田开发的中后期,地层本身能量不足以使原油产生自喷,必须人为地利用机械设备将原油举升到地面,称为人工举升采油法或机械采油法[1]。
上述采油方法中不利用抽油杆传递能量的抽油设备统称为无杆抽油设备,利用抽油杆上下往复进行驱动的抽油设备统称为有杆抽油设备。
利用抽油杆旋转运动驱动井下单螺旋泵装置,虽然也有抽油杆,但习惯上不列入有杆抽油设备[3]。
有杆泵采油技术是应用最早也最为广泛的一种人工举升机械采油方法。
有杆抽油系统主要有三部分组成:一是地面驱动设备即抽油机,它由电动机、减速器和四连杆机构(包括曲柄、连杆和游梁)等组成:二是井下的抽油泵(包括吸入阀、泵筒、柱塞和排出阀等),安装于油管的下端:三是抽油杆,它把地面驱动设备的运动和动力传给井下抽油泵。
抽油机是一种把原动机的连续圆周运动变成往复自线运动,通过抽油杆带动抽油泵进行抽油的机械设备。
游梁式抽油机是机械采油设备中问世最早的抽油机机种,1919年美国就开始批量生产这种抽油机。
目前我国大多数油田己相继进入了开发的中后期,油井逐渐丧失自喷能力,基本上己从自喷转入机采。
80年代初,我国拥有机采油井2万口,占总油井数的57.3%,机采原油产量占总产量的27 %,2000年我国油气田共有抽油机采油井约8万口,占油田总井数的90%。
在这些机采油井中,采用抽油机有杆式抽油的占90%,采用电潜泵、水力活塞泵、射流泵、气举等其它无杆式抽油的只占10%。
近几年,随着稳油控水和节能的要求不断提高,各种型式的节能型抽油机和长冲程抽油机的数量不断增加。
由此可见,抽油机在各油田的生产中有着举足轻重的地位,并且随着油田的进一步开发,各种新型节能抽油机将会得到广泛地推广和应用。
1.2 国内外抽油机的发展概况CYJY12-4.8-73HB型抽油机设计1.2.1国外抽油机的发展概况在国外,研究开发与应用抽油机已有100多年的历史[4]。
机械设计制造及其自动化专业毕业设计论文-游梁式抽油机结构设计

大学毕业设计题目游梁式抽油机结构设计专业班级学生学号指导教师二〇一四年五月五日1 前言1.1 设计目的本设计首先通过现场实习对游梁式抽油机进行选型,对异相游梁式抽油机进行结构设计。
同时以悬点加速度最小为目标,对抽油机的四杆机构进行优化设计。
最后根据现有的各种异相游梁抽油机学术资料,选取其它基本参数,设计出性能完善的的异相游梁式抽油机。
1.2 设计意义常规游梁抽油机自诞生以来,历经百年使用,期间经历了各种工况和各种地域油田生产的考验,经久不衰,至今国内外仍广泛使用。
有着结构简单、耐用、操作简便、维护费用低等优点,因此游梁式抽油机一直在有杆泵采油地面设备中占主导地位.但其在结构上存在不合理性,故常规游梁式抽油机有着能耗高的缺点。
然而随着世界石油工业的飞速发展,常规游梁式抽油机得到了广泛应用。
为了追求开采效益最大化,以最少的投入来换取最大回报,这就要求进一步研究抽油机设备,对游梁式抽油机结构进行优化设计,以此减少游梁式抽油机在采油时的能耗。
为克服常规抽油机驴头悬点运动的加速度较大,平衡效果较差,效率较低,能耗高等缺点,经过百年时间各种改革和实验找到了两个途径:一个是在常规游梁式抽油机的基础上进行技术革新和创造,继承其优点,克服其缺点,从平衡方式上着手改进,按照变矩平衡原理,对抽油机的四杆机构采取优化技术参数,研制开发了许多节能高效异相游梁式抽油机,使传统的游梁式抽油机又呈现出强大的生命力和使用空间。
异相游梁式抽油机有很多优点,其最基本的优点是:结构简单,制造容易,维修方便,特别是它可以长期在油田全天候运转,使用可靠。
大大提高了采油效率,而且维护简单,节省了劳动力为采油行业带了极大地效益。
从异相游梁式抽油机外形上看,它与常规型游梁式抽油机并没有特别显著的区别,主要不同点有两处:一是将减速器背离支架后移,增大了减速器输出轴中心和游梁摆动中心之间的水平距离,形成了较大的极位夹角(即驴头处于上、下死点位置时连杆中心线之间的夹角);二是平衡块重心与曲柄轴中心连线和曲柄销中心与曲柄轴中心连线之间构成一定的夹角,该角称为平衡相位角。
10型游梁式抽油机参数优化设计

5 5
本 文 以1 O 型 游 梁 式
抽 油机 为模 型,确定 了 抽 油机 参数优 化设计 的
目标 பைடு நூலகம்数 ,给 出了优 化
设 计 中的约束条件 ,采
1 0 型游 梁式抽油 机参数优化设计
◇胜利 油 田 东胜精 攻 石 油开发 集 团股 份 有 限公 司 孙 雅 斐
式 望 甲 标 函 f ( x =
:
=
一
s i n r
2 a " 一 一s i n I 1 ( ( R s i n ( O +妒 ) ) / 三 ) 一 C O S 一 ( ( 三 +C 一 P ) / 2 L C ) 一 ( +尹 ) ,
为曲 柄与 连杆 的 夹 角 ,o ; =C O S 一 ( ( c: +P 一 K 一R 。 + 2 K Rc o s ( 0 + ) ) , ( 2 尸 c) ), 为连杆 与 游 梁后
柄 平衡 重 偏置 角 彳 为优 化 设 计变 量 。
则设 计 变 量为 : X =[ A , , , H, P, R , C , f 】 =【 ( 1 ) 1 ( 2 ) , ( 3 ) , ( 4 ) , x ( 5 ) , ( 6 ) , ( 7 ) 】 。
一
电动机采用 Y 2 2 5 M一 8 型.由基本型游梁式抽油机与深井泵组合
的特性图取Q = 5 O m / d ,经 计 算 可 得 :考 虑沉 没 压 力后 ,作 用 在
、
抽 油 机优 化设 计
(一 )设 计 变量 、
整个柱塞截面积上的液柱载荷为3 8 3 6 4 N,考虑液体浮 力后的抽 油杆柱载荷为4 1 6 6 9 N,折算到 曲柄上 回旋半径 , 处的平衡重量
游梁式抽油机调平衡三种方法的计算与比较
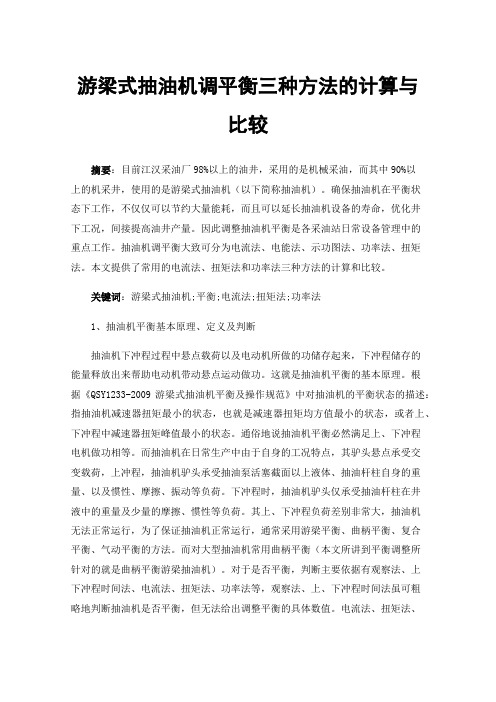
游梁式抽油机调平衡三种方法的计算与比较摘要:目前江汉采油厂98%以上的油井,采用的是机械采油,而其中90%以上的机采井,使用的是游梁式抽油机(以下简称抽油机)。
确保抽油机在平衡状态下工作,不仅仅可以节约大量能耗,而且可以延长抽油机设备的寿命,优化井下工况,间接提高油井产量。
因此调整抽油机平衡是各采油站日常设备管理中的重点工作。
抽油机调平衡大致可分为电流法、电能法、示功图法、功率法、扭矩法。
本文提供了常用的电流法、扭矩法和功率法三种方法的计算和比较。
关键词:游梁式抽油机;平衡;电流法;扭矩法;功率法1、抽油机平衡基本原理、定义及判断抽油机下冲程过程中悬点载荷以及电动机所做的功储存起来,下冲程储存的能量释放出来帮助电动机带动悬点运动做功。
这就是抽油机平衡的基本原理。
根据《QSY1233-2009游梁式抽油机平衡及操作规范》中对抽油机的平衡状态的描述:指抽油机减速器扭矩最小的状态,也就是减速器扭矩均方值最小的状态,或者上、下冲程中减速器扭矩峰值最小的状态。
通俗地说抽油机平衡必然满足上、下冲程电机做功相等。
而抽油机在日常生产中由于自身的工况特点,其驴头悬点承受交变载荷,上冲程,抽油机驴头承受抽油泵活塞截面以上液体、抽油杆柱自身的重量、以及惯性、摩擦、振动等负荷。
下冲程时,抽油机驴头仅承受抽油杆柱在井液中的重量及少量的摩擦、惯性等负荷。
其上、下冲程负荷差别非常大,抽油机无法正常运行,为了保证抽油机正常运行,通常采用游梁平衡、曲柄平衡、复合平衡、气动平衡的方法。
而对大型抽油机常用曲柄平衡(本文所讲到平衡调整所针对的就是曲柄平衡游梁抽油机)。
对于是否平衡,判断主要依据有观察法、上下冲程时间法、电流法、扭矩法、功率法等,观察法、上、下冲程时间法虽可粗略地判断抽油机是否平衡,但无法给出调整平衡的具体数值。
电流法、扭矩法、功率法不仅能计算出当前抽油机的平衡率,而且还可以算出达到平衡条件所需要移动平衡块的距离,在现场得到广泛运用。
常规游梁式抽油机设计与仿真(毕业设计)

摘要现在油田的采油方式有两种:一种是利用地层本身的能量来举升原油,称作自喷采油法;另一类是人为的利用机械设备将原油举升到地面,称作机械采油法。
自喷采油法是最经济的方法,但是随着油田的开发,地层压力的降低,地层能量的消耗,油田不能再采用自喷采油法,就需要利用机械采油法。
机械采油法,有杆抽油是国内外油田最主要的,也是至今在机械采油方式中占绝对主导地位的人工举升方式。
有杆抽油系统主要由抽油机、抽油杆、抽油泵三部分组成,抽油机是有杆抽油系统最主要的升举设备。
根据其是否有游梁,抽油机可以划分为游梁式抽油机和无游梁式抽油机。
而常规游梁抽油机自诞生以来,历经百年,经历了各种工况和各种地域油田生产的考验,经久不衰。
目前仍在国内外普通使用。
常规游梁式抽油机以其结构简单、耐用、操作简便、维护费用低等明显优势,一直占据着有杆系采油地面设备的主导地位。
所以研究有杆类采油设备是非常有意义的。
本文介绍了常规抽油机工作原理与节能原理,设计过程中对抽油机运动学和动力学分析与计算,阐述了常规游梁式抽油机运动规律。
游梁式抽油机驴头的悬点载荷标志抽油机的工作能力的重要参数之一,而看它是否节能,其技术指标是抽油机的电动机实耗功率的大小及减速器的工作状态。
本设计全面概述了常规性抽油机的发展概况,抽油机的优化设计及其节能原理,对抽油机得几何参数,运动参数,动力学参数进行了全面的分析计算,以对常规游梁式抽油机进行优化设计。
关键词:常规游梁式抽油机;结构设计计算;优化AbstractMethod of oilfield exploitation of crude oil is divided into two kinds: one kind is uses thehigh energy to lift crude oil, known as the flowing production method; another kind is the use of mechanical equipment for the crude oil onto the ground, called the mechanical recovery method. Flowing production method is the mosteconomical, but with the development of oil fields, lower formation pressure,formation energy consumption, oil field can not use the flowing production method,need to use mechanical recovery method. Machinery production equipment from the mode of production can be divided into two kinds: rod production equipment and no rod production equipment, and rod production equipment for the main part,so the energy problem rod production equipment is very meaningful.Beam pumping unit is the main equipment for the production of rod oil extraction equipment in oil field. In some oil fields in China try to use technology to replace theconventional beam pumping machine is advanced, but because the cost is too high, the cost recovery period is too long, so in the field or in the beam pumping unit.This paper introduces the conventional pumping unit working principle and theprinciple of energy saving pumping unit, the analysis and calculation of the kinematics and dynamics of machine design process, the conventional beampumping oil machine movement law. One of the important parameters of the beampumping unit horsehead of the pumping unit horsehead load mark working ability,and to see whether it is energy saving, the technical indicators are motor pumping unit of the actual power consumption and the size of the reducer working state. The design of a comprehensive overview of the development of the conventionalpumping unit, optimizing design and energy-saving principle of oil drawing machine,the geometrical parameters, pumping motion parameters, the kinetic parameterswere analyzed to calculate.目录常规游梁式抽油机设计与仿真第一章绪论1.1游梁式抽油机技术发展抽油机产生和使用由来已久,已有百年的历史。
游梁式液压抽油机系统的动力分析
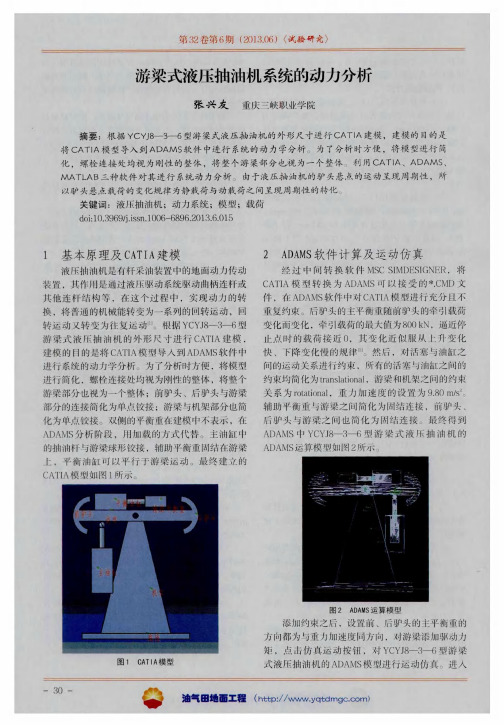
U
_
_ —
幽 0 冒 l 8 螺
一 U
』
\ .
时 壬 间 \ \ f /
图 4 相 对 位 移 曲 线
。
图 3 活 塞 运 动 规 律
由图 3 可 以看 出 ,主油 缸 活 塞 的运 动规 律呈 现 周期 性 ,半个 周期 之 内 ,主油 缸 活塞 的速 度先 是 为
第3 2 卷第 6 期 ( 2 0 1 3 . 0 6 )( 试验 研 究) p l o t t i n g 模块 ,得 出仿 真过程 中的各种 曲线 。
2 . 1 主油 缸 活塞运 动 规律
对位 移 曲线 ,见 图 4 。
根 据 A D A MS软 件 运 动 仿 真 结 果 , 得 出
头悬点的运动 ;前者频率为激振位移的频率 ,后者 频 率为 系统 的 固有频 率 。
由 图 5可 见 ,在 上 、下 冲 程 交 替 时 刻 ( = 1 0 S 、f = 0 或2 0 S ) ,抽 油泵 位 移 大 于驴 头 悬 点 位 移 ,
2 . 2 主油 缸 与平衡 油 缸 的工作 压 力 对于Y C Y J 8 —3 —6 型 游 梁 式 液 压 抽 油 机 , 主 油缸 承 受 主要 的惯 性 载 荷 ,提 供 吸 油 的 主要 动 力 。 前 驴 头悬 点与 后驴 头悬 点非 严 格对 称结 构 ,所 以在 游 梁运 动 的过 程 中 ,存 在需 要 调整 的动 平衡 。这 部
油气 田地 面工程 .2 0 1 1 .3 0( 5 ) .1 0 1
9 5 m m,抽 油杆直径为 3 2 m m,冲程长度为 6 . 5 m, 冲次 3 . 5 次/ 分 。应 用 MA T L A B软 件 进 行 建 模 分 析 , 得到抽油泵柱塞的位移响应曲线及与驴头悬点的相
游梁式抽油机曲柄平衡控制简易算法

游梁式抽油机曲柄平衡控制简易算法黄伯棠【摘要】根据游梁式抽油机曲柄平衡基本原理,导出了控制平衡重块的一种简易算法.以CYJ12-4.8-73HB型抽油机为例,利用驴头悬点上、下冲程测得的电流和SG7示功诊断仪测得示功图中的参数,计算并调整了曲柄平衡重块的位置.该方法计算简单,便于现场应用.【期刊名称】《长江大学学报(自然版)理工卷》【年(卷),期】2004(001)002【总页数】2页(P7-8)【关键词】游梁式抽油机;曲柄;平衡块;控制;示功图;算法【作者】黄伯棠【作者单位】长江大学机械工程学院,湖北,荆州,434023【正文语种】中文【中图分类】TE933.102在游梁式抽油机的机械平衡方式中,按照平衡重块安装的位置不同,分为游梁平衡、曲柄平衡和复合平衡3种。
从目前各油田所使用的大型游梁式抽油机来看,大部分采用的是曲柄平衡装置,即在曲柄上安装平衡重块。
现在的问题是,平衡重块的位置不是一成不变的,那么如何对它进行控制。
文献[1~3]提供的控制方法比较复杂,难以据此调整好平衡重块位置。
为此,笔者从游梁式抽油机曲柄平衡的基本原理出发,提出一种控制平衡重块的简易算法。
1 算法推导游梁式抽油机采用曲柄平衡时,在悬点下冲程,要把平衡重块从低处抬到高处,增加它的位能,除了依靠抽油杆下落所释放的位能外,还要电动机付出部分能量,从而消除了下冲程时电动机接受能量的现象;在悬点上冲程,平衡重块由高处落下,释放位能,帮助电动机提升抽油杆柱和液柱,这就减少了电动机上冲程时所需要付出的能量。
如果平衡重块选择合适,可使得电动机上冲程时输出的能量等于下冲程时输出的能量,则上、下冲程时电动机所做的功相等。
游梁式抽油机起初所加曲柄平衡重块的大小和安装位置,是根据上、下冲程时电动机所做的功相等这一原理进行设计计算的。
设I上max和I下min分别为驴头悬点上冲程和下冲程时用钳形电流表测得的最大、最小电流值,此时电动机电流值与减速箱曲柄轴扭矩间存在正比关系。
工程训练报告 游梁式抽油机课程设计

东北石油大学工程训练研究报告2012年6月18日目录任务书第1章概述 (1)1.1 抽油机的特点 (1)1.2 抽油机分类 (1)1.3 抽油机的发展趋势 (2)第2章常规游梁式抽油机传动方案设计 (3)2.1抽油机系统的组成 (3)2.2抽油机工作原理 (3)2.2系统的机构(运动)简图 (4)第3章曲柄摇杆机构设计 (4)3.1 设计参数分析与确定• (4)3.2 按K设计曲柄摇杆机构 (5)3.3 曲柄摇杆机构优化设计分析 (6)3.4结论和机构运动简图.......................... 错误!未定义书签。
第4章常规游梁式抽油机传动系统运动和动力参数分析计算 .. (8)4.1 传动比分配和电动机选择 (8)4.2 各轴转速计算 (10)4.3各轴扭矩计算 (10)4.4各轴功率计算 (10)第5章齿轮减速器设计计算 (11)5.1 高速级齿轮传动设计计算 (11)5.2 低速级齿轮传动设计计算 (12)5.3结论及运动简图 (14)第6章带传动设计计算 (14)6.1 带链传动的方案比较 (14)6.2 带传动设计计算 (15)6.3结论及运动简图 (16)第7章轴系部件设计计算 (16)7.1 各轴初算轴径 (16)7.2 轴的结构设计 (17)7.3滚动轴承寿命验算 (18)7.4轴的强度和刚度验算 (22)第8章连接件的选择和计算 (26)8.1 齿轮连接平键的选择与计算 (26)8.2 带轮连接平键的选择与计算 (27)8.3螺纹连接件的选择 (28)第9章设计结论汇总 (29)总结 (31)参考书目 (31)东北石油大学工程训练任务书课程机械设计基础题目常规游梁式抽油机传动系统设计专业姓名学号主要内容、基本要求、主要参考资料等一、设计的目的1、综合利用所学的知识,培养解决生产实际问题的能力。
2、掌握一般的机械传动系统设计方法和步骤。
3、掌握基本机构一般的设计方法和步骤。
- 1、下载文档前请自行甄别文档内容的完整性,平台不提供额外的编辑、内容补充、找答案等附加服务。
- 2、"仅部分预览"的文档,不可在线预览部分如存在完整性等问题,可反馈申请退款(可完整预览的文档不适用该条件!)。
- 3、如文档侵犯您的权益,请联系客服反馈,我们会尽快为您处理(人工客服工作时间:9:00-18:30)。
游梁式抽油机设计计算卢国忠编 05-04游梁式抽油机的主要特点是:游梁在上、下冲程的摆角相等,即上下冲程时间相等。
且减速器被动轴中心处游梁后轴承的正下方。
一、几何计算1.计算(核算) 曲柄半径R和连杆有效长度P己知:冲程S、游梁后臂长C、游梁前臂长A、极距K(参见图1)由余弦定理推导可得:公式: ()b t CK K C CK K CR ψψcos 2cos 2212222-+--+=------(1)R CK K C P t --+=ψcos 222 -------(2)式中:1090δφψ+-=t 2090δφψ--=bH I tng 1-=φ AS mas πδδ4360021⨯==22H I K +=2. 计算光杆位置系数R P :PR 是在给定的曲柄转角θ时,光杆从下死点计算起的冲程占全冲程的百分比。
(图2)(图3) 公式:10⨯--='=bt t mas S s PR ψψψψ% -----------(3)曲柄max S PR s ∙='()121δδ∙-=PR式中:b t ψψ, 分别代表下死点和上死点的ψ角的值ρχψ-=()⎥⎦⎤⎢⎣⎡-=-J R φϑρsin sin 1 βcos 222PC C P J -+= ⎪⎪⎭⎫⎝⎛-+=-CJ P J C 2cos 2221χ⎪⎪⎭⎫⎝⎛---++=-CP R K KR P C 2)cos(2cos 22221ϕθβ ()φθψβα--+= 上冲程 ()[]φθψβα--++=360 下冲程 二运动计算己知:曲柄角速度ω、曲柄转角θ,分析驴头悬点的位移s 、速度v 、加速度a 的变化规律。
1. 假定驴头悬点随u 点作简谐振动:()ϑωϑωϑcon C AR a CARv CARs ⨯⨯=⨯⨯=-⨯=2sin cos 1 以C AR S 2max =代入得: ()ϑωϑωϑc o s 21s i n 21c o s 1212m a xm a x m a x S a S v S s ==-=2max max 21ωS a =2.接严格的数学推导 ⎪⎭⎫⎝⎛+=P R S a 121max 2max ω三动力计算1.从示功图上求悬点载荷W示功图是抽油机悬点载荷W 与光杆位置PR 的关系曲线图。
是用示功仪在抽油机井口实测出来的。
设计中无法实测,只好用理论公式计算并绘制------称为人工示功图,为以后的受力分析、强度计算提供主要依据。
2. 光杆载荷W 加在曲柄轴上的扭矩的计算(见图2 ,图3)a. 美国石油学会(API)定义TF 为扭矩因素,表示单位光杆载荷W 在减速器上产生的扭矩T 。
计算公式推导如下:API 规定生产厂要向抽油机用户提供一张θ角每变化15度的TF 值变化表。
βαsin sin ⋅==C AR W T TF ααββsin sin sin sin q l l q l l F F R F R F C AWF C F WA =∴==∴= W C AR R F T q ⨯⨯==βαsin sin考虑抽油机的结构不平衡重B 的影响: ()B W C AR T -∙∙=βαsin sin 光杆载荷在减速器上产生的扭矩:()B W TF T Wn -∙=b.应用PR 表、示功图和TF 表求出悬点载荷在减速器上产生的扭矩曲线,如 030=θ: ()B W TF T -⋅=3030303〃曲柄、平衡重加在曲柄轴上的扭矩计算设曲柄自重为q ,其重心到转轴中心距为r 平衡重总重为Q ,其重心到转轴中心距为R 产生的最大平衡力矩为: QR r q M +⋅=max4计算减速器净扭矩当曲柄处于θ角位置时,其平衡力矩为 M =(QR+qr) ×sin θ悬点载荷在减速器上产生的扭矩()B W TF T Wn -∙=其净扭矩为()ϑsin max ⋅--⋅=M B W TF T n由此式可以绘制曲柄扭矩图。
5〃电动机功率计算 a. 理论计算由于曲柄受规律变化的扭矩作用,其计算功率用的扭矩值只能应用均方根扭矩来计算。
式中 0,,21≥nm n n T T T曲柄轴的计算功率为: n T N n ⨯'⨯⨯=-410424.1 电机功率为: μη∙=d d NN 式中 N---曲柄轴的计算功率 HP n T --曲柄轴扭矩, N mmT T T T T nmn n n n 2232221++++='n---曲柄转速,冲次,μη,d --抽油机总效率,取0.6—0.8 b.估算公式 3900LQ N ⨯=KW 式中 Q —深井泵理论日产量,d m /3 n S A Q ⨯⨯⨯=1440 d m /3 L--深井泵下泵深度,m A--深井泵柱塞面积,2m—抽油机冲次, 1/minS —抽油机冲程长度, m 5. 平衡计算在抽油机的设计和使用中,被普遍采用的平衡准则有三种:1。
上、下冲程中,电动机所付出的平均功率相等。
2.上、下冲程中,减速箱曲柄轴的输出扭矩峰值相等。
3.在抽油机的整个冲程中,曲柄轴舜时的扭矩与平均扭矩偏差的平方和最小。
第1条准则的平衡计算简单、实用。
表示为:下冲程时平衡重所储存的能量o A 等于电动机下冲程所做的功dx A 加上下冲程抽油杆下落所做的功xx A ,即xx ds A A A +=0上冲程时,平衡重所放出的能量o A 加上电动机上冲程所做的功ds A 等于上冲程驴头悬点提升抽油杆和液柱所做的功xs A ,即xs ds o A A A =+由于上、下冲程中,电动机所作的功相等,即dx ds A A =,由此可求得平衡重所储存的能量:20xxxs A A A +=a. 如已测得抽油机驴头悬点的实际示功图如图-4,则:sp sp 0q q )ABCD 21OADCFO (q q 2OADCFOOABCFO ∙∙+=∙∙+=面积面积面积面积A 式中 p q ----示功图纵坐标比例,N/mm s q ----示功图横坐标比例,m/mmb. 如果没有实际示功图,亦可用静力示功图作近似计算,如图5 max maxmax 0)2(2S W W S W S W A y g y g ∙+=∙+∙=式中 Wg ----抽油杆在油液中的重量,Ny W ----油井中动液面以上,断面积等于柱塞面积的油柱重量,Nmax S ----抽油机的最大冲程,m 计算平衡重储能以图-3的复合平衡为例,图中:y Q ----游梁平衡重;y c Q K ---离游梁支点O 的距离;b Q ----曲柄平衡重;b Q R ---的平衡半径;y q ----游梁总成的重量; y l ----游梁重心距; b q ----曲柄自重; b l ----曲柄重心距;下冲程时,游梁平衡重抬高的距离为CK r C A r A K S A K c c c ∙=∙∙=∙2)2(max 储存能量为 CKQ r c y ∙∙2曲柄平衡重抬高的距离为 2R , 储存能量为 b Q R ∙2 游梁总成的重量抬高的距离为Cl r y ∙2,储存能量为Cl q r y y ∙∙2曲柄自重抬高的距离为b l ∙2,储存能量为b b q l ∙∙2 总储存能量为 b b b y b c y o q l Clq r Q R C K Q r A ∙+∙∙∙+∙+∙∙=2222 为方便计算,设cy y y K l q Q ∙=' ----游梁总成的重量所相当的游梁平衡重大小;bbb Q l q R ∙='----曲柄自重所相当的曲柄平衡重的平衡半径。
代入上式,求得游梁平衡重的大小: y b cc o y Q Q CK r R R C K r A Q '-∙∙'+-∙=2 曲柄平衡重的平衡半径:R CK r Q Q Q Q A R c b yy b o '-∙∙'+-=2, 对于单独的游梁平衡,0=b Q ,同时曲柄自重的影响,则: y coy Q Cr A Q '-∙=2 对于单独的曲柄平衡,0=y Q ,同时游梁自重的影响,则: R Q A R bo'-=2四.主要构件的受力计算(见图-3) 1.游梁受力分析()A B W C F MLo∙-=∙∙∴=∑βsin 0连杆轴向力 ()βsin ∙-∙=C B W A F L游梁切向力 βsin ∙L F 游梁纵向力 βcos ∙LF ()δβ+-=-=∴=∑cos 0LLx o oF F x X ()()B W F F y YLLy o o-++-=-=∴=∑δβsin 02.支架受力分析H x D y E y MO OQ H∙'+∙'=∙∴=∑0 ()()()[]δβδβ+∙+∙-++∙=cos sin H C B W C EFy L Q()H x D B y E y Mo oH Q∙'--∙'=∙∴=∑0 ()()()()()[]δβδβ+∙--∙-++∙-=cos sin H D E B W D E EFy L H()δβ+∙='=+∴=∑cos 0Lo Q HF x x xX 3. 曲柄—减速器被动轴总成受力分析()C C Q L o r F r q R Q F M ~sin sin 0+∙+∙=∙∴=∑'θα()θαsin sin ∙+∙-∙=∙qr R Q F r F LC C ()δβ+∙=∴=''∑cos 0Lo o F x X ()CL o o F F q Q y Y-+∙-+=∴=''∑δβsin 0 4. 曲柄肖轴受力分析曲柄肖轴受一对大小等于LF 的剪切力作用。
5. 减速器受力分析 6. 支座受力分析五.各另部件强度计算 (略)。