所有制程标准工时计算范例
工时计算方法五篇范文
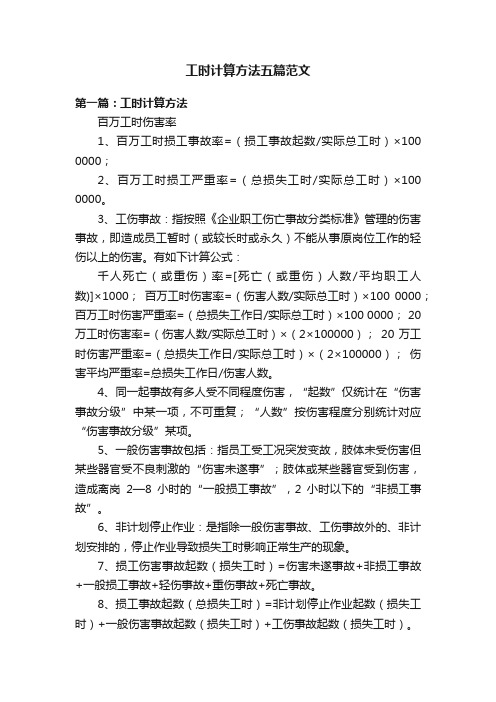
工时计算方法五篇范文第一篇:工时计算方法百万工时伤害率1、百万工时损工事故率=(损工事故起数/实际总工时)×100 0000;2、百万工时损工严重率=(总损失工时/实际总工时)×100 0000。
3、工伤事故:指按照《企业职工伤亡事故分类标准》管理的伤害事故,即造成员工暂时(或较长时或永久)不能从事原岗位工作的轻伤以上的伤害。
有如下计算公式:千人死亡(或重伤)率=[死亡(或重伤)人数/平均职工人数)]×1000;百万工时伤害率=(伤害人数/实际总工时)×100 0000;百万工时伤害严重率=(总损失工作日/实际总工时)×100 0000; 20万工时伤害率=(伤害人数/实际总工时)×(2×100000);20万工时伤害严重率=(总损失工作日/实际总工时)×(2×100000);伤害平均严重率=总损失工作日/伤害人数。
4、同一起事故有多人受不同程度伤害,“起数”仅统计在“伤害事故分级”中某一项,不可重复;“人数”按伤害程度分别统计对应“伤害事故分级”某项。
5、一般伤害事故包括:指员工受工况突发变故,肢体未受伤害但某些器官受不良刺激的“伤害未遂事”;肢体或某些器官受到伤害,造成离岗2—8小时的“一般损工事故”,2小时以下的“非损工事故”。
6、非计划停止作业:是指除一般伤害事故、工伤事故外的、非计划安排的,停止作业导致损失工时影响正常生产的现象。
7、损工伤害事故起数(损失工时)=伤害未遂事故+非损工事故+一般损工事故+轻伤事故+重伤事故+死亡事故。
8、损工事故起数(总损失工时)=非计划停止作业起数(损失工时)+一般伤害事故起数(损失工时)+工伤事故起数(损失工时)。
9、表中工时单位统一为:小时;1个工作日=8小时。
实际总工时=平均职工人数×实际工作日×8。
在计算时,损失工时与实际总工时的“单位”统一使用“日”或“小时钻井队、海洋平台作业队、勘探队等野外作业活动,作业区和生活区一直暴露在与工作有关的危险中,员工每人每天按24工时计算,为其提供相关服务的员工每人每天按12工时计算。
制程标准工时计算范例

制程标准工时计算范例制程标准工时是指在标准工时内完成一个制程所需的时间。
它是制造业中用来度量生产效率的重要指标之一,对于企业的生产安排和成本控制具有重要意义。
制程标准工时的计算需要考虑到一系列因素,如生产线的设备状况、操作员的熟练程度、产品的复杂程度等。
下面以一家制造企业的某个制程为例,介绍如何计算制程标准工时。
首先,我们需要确定计算制程标准工时的基本单位。
一般情况下,制程标准工时是以分钟为单位进行计算的,因为分钟是一个比较小的单位,更能体现工作过程中的细节。
所以,在计算制程标准工时时,可以把制程的时间分为若干个操作步骤,分别计算每个步骤的工时,并将其相加得到制程的标准工时。
接下来,我们需要明确计算制程标准工时的流程和内容。
以某工厂生产手机壳为例,该制程分为原材料准备、注塑、磨光和组装四个步骤。
我们分别计算每个步骤的工时,并在最后汇总得出制程的标准工时。
1. 原材料准备:这个步骤包括从仓库取出原材料并上料到生产线的过程。
假设从仓库取出原材料需要5分钟,上料需要1分钟。
则原材料准备的标准工时为6分钟。
2. 注塑:这个步骤是将原材料进行熔化、注射到模具中并冷却成型的过程。
根据生产实际情况,我们已经确定注塑的标准周期为30秒。
所以,注塑的标准工时为30秒。
3. 磨光:这个步骤是将注塑成型后的产品进行磨光处理,使其表面平滑。
根据过去的生产数据,我们已经确定磨光的平均工时为10秒。
所以,磨光的标准工时为10秒。
4. 组装:这个步骤是将磨光后的产品进行组装,包括插入电池、安装零件等。
根据生产数据,我们已经确定组装的平均工时为2分钟。
所以,组装的标准工时为2分钟。
最后,我们把每个步骤的标准工时相加就得到了整个制程的标准工时。
在这个例子中,原材料准备的标准工时为6分钟,注塑的标准工时为30秒,磨光的标准工时为10秒,组装的标准工时为2分钟。
所以,整个制程的标准工时为6分钟加上30秒加上10秒加上2分钟,即为8分钟。
工时计算方法大全(各机床工时、各工序工时)
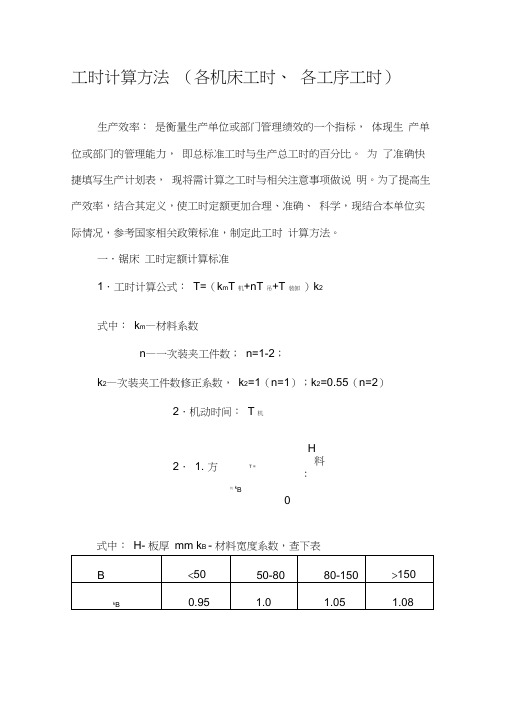
工时计算方法(各机床工时、各工序工时)生产效率:是衡量生产单位或部门管理绩效的一个指标,体现生产单位或部门的管理能力,即总标准工时与生产总工时的百分比。
为了准确快捷填写生产计划表,现将需计算之工时与相关注意事项做说明。
为了提高生产效率,结合其定义,使工时定额更加合理、准确、科学,现结合本单位实际情况,参考国家相关政策标准,制定此工时计算方法。
一.锯床工时定额计算标准1.工时计算公式:T=(k m T 机+nT 吊+T 装卸)k2式中:k m—材料系数n—一次装夹工件数;n=1-2;k2—次装夹工件数修正系数,k2=1(n=1);k2=0.55(n=2)2.机动时间:T 机H2.1. 方T =料:2机k B式中:H- 板厚mm k B - 材料宽度系数,查下表D2.2.棒料:T2 机= 4式中 D —棒料外径 mmDd 022.3. 管料 :T 机=2 — 1000 4 0 式中 d 0—管料内径; mmHH 0*B 0T 机 = —28000—方管外形高3.吊料时 L 间:T1吊=4.装卸料时 000 间及其它时间:装卸2.4..方管:式中: Hmm ;H 0—方管内腔高 mm ; B 0—方管内腔宽 mm ;800综上所述:方料:T=(0.12+n0.0519H+0.001L )k 2-0.00013 H 0*B 0 (min ) 圆料:T=(0.12+n0.0429D+0.001L )k 2-0.0001 d 02 (min ) n —一次装夹工件数; n=1-2;k 2—次装夹工件数修正系数, k 2=1(n=1);k 2=0.55(n=2)二.剪板冲压折弯工时定额计算标准1..剪板工时定额计算方法剪板单件工时定a —每块工时系数、见表b —剪角次数剪板工时系数表=0.12+ 403额:注:准备工时按100 件基数计算,每件0.2,共计200分剪板毛刺工时:T=0.3 + 处理长度/400剪板校正T 校=k*T材料系数K=1~1.52.冲压每冲一次工时3..折弯工时定额计算方法折弯工时定额:t2=Σa i折弯工时定额系数表注:规格栏中,为折弯长度,a 为每折一刀的工时(理论计算:每刀0.15 分×折1.5=0.225+0.2=0.425→0.5)↓准备工时三.风割焊接工时定额计算标准1.风割工时T 风割割长度× 公式:3+1.5修磨工时含补焊工时: T 修磨2= T 风割/2.焊接单件工时:T 焊接=T 工件装卸+T 点焊+ T 全焊2.1 装卸工件工时:T 工件装卸= (T01+0.2n)B式中:T01—装卸基本工时;(取T01=0.2);n-- 工件数B-- 重量系数(见表)2.2.点焊单件工时:T 点焊= T02+0.1J+0.1N式中:T02—点焊基本工时;J—点焊数;N—点焊时工件翻转次数;2.3. 全焊单件工时:T 全焊= T03+0.1M+0.1N+L Σ/200+0.2NC式中:T03—全焊基本工时;M—焊缝段数;N—全焊时工件翻转次数;LΣ--焊缝长NC--- 焊接参数调节次数注:小件装卸与点焊工时合并,统称点焊工时;重量系数(B)1、飞溅按焊接工时的二分之一计算+0.12、校正按焊接工时的二分之一计算+0.13、有辅助工帮助表卸模,从焊接工时中分取三分之一4、焊接有准备工时按每项20 分钟5、点焊螺母按0.5 分钟一个四.钻床工时定额1、T=kT 机+ T 装卸其中k —难度系数有工差要求k=1.5 有深度要求k=1.1 扩孔及攻丝k=0.82、机动时间:T 机注:L/D ≥8 时,须另增排屑时间60% 3、装卸零件时间及辅助时间: T 装卸五.磨床铣床工时定额计算标准1.平面磨工时定额:工作台单行程横向进给量16~24mm/次工件运行行速度8m/min磨一次行程工时2. 无心磨工时定额(含辅助工时) LkT= 1d式中: L—单件被加工零件总长; k d—直径系数,d≤16, k d=1.0; d>16, k d=1.2203.铣端面工时加工段数系数B计算公式加×T= 工长度六。
《标准工时管理规范》

观测时间
宽放时间
纯作业时间
生产准备
预热换线 生
准备等停 理
机时间
宽
放
疲 劳 宽
作 业
放
宽
放
2)标准产能
单位时间的最高产出量。 指作业人数在8小时内能完成的产品数量(要求转化为整数); 计算方法为:(480/瓶颈工序的工序时间) 例:
3)产品生产周期
单个产品从第一个工序开始到最后一个工序结束所需经历的时间。
当发生变更时,制程工程师需要 进行分析,确定为有效变更或准 有效变更即按《标准工时变更评 估表》要求进行相关验证,验证 可行后与修改后标准一并发布。
任何工时的预估、制订、修改须 经制程工程师同意并发布,其它
单位均不得更改标准工时。
当作业内容增加或减少、作业方 法改变,致使超过或无法达成原
来的作业效率。
《标准工时管理规范》
生产技术部
目录
一、规范定义解读 二、工作职责介绍 三、工作程序说明 四、标准模版解析
一、规范定义解读
1)标准工时
是指在正常条件下,一位合格适当且受过一定训练的工作者,按规定作业 ,完成一定数量和质量的工作所需要的时间 。 标准工时的计算公式为:标准工时 = 工序时间(观测)×(1+宽放率)
应随时掌握现场情况,对操作 者的技能水平、宽放率等做出相 应的判断。根据实际情况调整宽 放率。
制程工程师依评审结果和当时 状态,更新该产品的标准工时并 发行修订《工序标准工时表》。
当产品线发生ECN或其它工艺变 更、工位调整、设备升级后,工 序的作业时间改变且各生产条件 均已稳定,各作业均已规范的。
制程工程师
1.排布生产工位,安排作业工序。 2.从效率、生产平衡角度对生产工位排 布和工作负荷进行研究及测定,提出
标准工时的计算公式
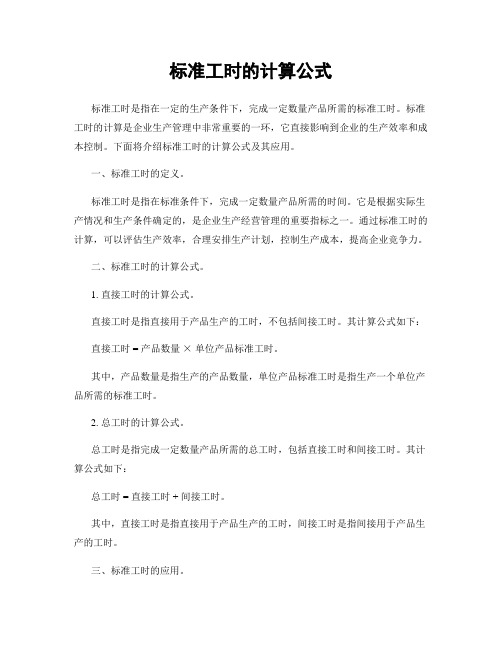
标准工时的计算公式标准工时是指在一定的生产条件下,完成一定数量产品所需的标准工时。
标准工时的计算是企业生产管理中非常重要的一环,它直接影响到企业的生产效率和成本控制。
下面将介绍标准工时的计算公式及其应用。
一、标准工时的定义。
标准工时是指在标准条件下,完成一定数量产品所需的时间。
它是根据实际生产情况和生产条件确定的,是企业生产经营管理的重要指标之一。
通过标准工时的计算,可以评估生产效率,合理安排生产计划,控制生产成本,提高企业竞争力。
二、标准工时的计算公式。
1. 直接工时的计算公式。
直接工时是指直接用于产品生产的工时,不包括间接工时。
其计算公式如下:直接工时 = 产品数量×单位产品标准工时。
其中,产品数量是指生产的产品数量,单位产品标准工时是指生产一个单位产品所需的标准工时。
2. 总工时的计算公式。
总工时是指完成一定数量产品所需的总工时,包括直接工时和间接工时。
其计算公式如下:总工时 = 直接工时 + 间接工时。
其中,直接工时是指直接用于产品生产的工时,间接工时是指间接用于产品生产的工时。
三、标准工时的应用。
1. 生产计划编制。
通过标准工时的计算,可以合理安排生产计划,确定生产周期和生产数量,提高生产效率,确保生产进度。
2. 成本控制。
标准工时的计算可以帮助企业控制生产成本,合理安排生产人员和设备,减少生产浪费,提高生产效率,降低生产成本。
3. 绩效考核。
通过标准工时的计算,可以对生产人员的工作绩效进行考核,激励员工提高工作效率,提高企业生产效率。
四、标准工时的优化。
1. 提高生产效率。
通过优化生产流程,改进生产工艺,提高设备利用率,减少生产中的浪费,可以提高生产效率,减少标准工时。
2. 管理人员培训。
加强生产管理人员的培训,提高他们的管理水平和技能,可以有效地优化生产管理,降低标准工时。
3. 技术改进。
引进先进的生产技术和设备,改进生产工艺,提高产品质量,减少生产成本,降低标准工时。
五、总结。
人工标准工时计算公式

人工标准工时计算公式教科书上面的标准工时计算公式是:标准工时 = 基本时间*(1+宽放率)其中:基本时间 = 观测时间 * (1+评比系数)我们从背景、观测时间、评比系数、宽放率一步步得出标准工时,let’s go!零、背景假设我们现在要测量组装一支自来水笔的标准工时。
笔有4个部分,如下:组装一支笔有三个操作,如下:1.从初始位置取笔筒和笔芯,并组装2.持住笔筒,并取笔头组装3.持住笔筒,并取笔帽组装,放置成品于初始位置一、观测时间观察时间有点像标准工时的原材料,是从观察时间开始加工的。
通过观测,最后得到这样的表格(T表示该操作结束时的累积时间,R代表该操作的测量时间,R是由两个相邻的T值相减得来的。
):最后获得这三个操作,4个循环的平均值就是观测时间了,如下:观测时间 = 2.7+2.5+2.1 = 7.3S,搞定!我们推荐西屋评估方法。
通过打分,可以更科学地确定评价系数,降低对经验的要求,缩小不同工程师的评价差距。
我们来评价一下刚才的演练(其实结合现场操作人员)熟练度:偶尔会有一些失误,还没有足够信心,不过长时间工作没有什么问题,给予尚可,-0.05努力度:建议能接受,但是自主改善有点问题。
给予平均,+0.00操作环境:公司内部差不多都是这样的环境,给予平均,+0.00一致性:没有发生故意拖延,使得每次测量时间不均,给予良好 +0.01综合评比系数为:1-0.05+0.00+0.00+0.01 = 0.96基本时间 =7.3 *0.96 = 7.0S,我们也得到了。
三、宽放率一般来说,我们有四种:生理宽大、疲劳宽大、作业延误宽大、管理宽大,分别以集中和非集中的方式给予。
集中注意力的方法是休息和晨会。
非集中化的方式是在每个操作周期中留出较宽的释放时间。
宽放率和评比系数一样也有类似评价表格,不过还是需要IE 们在自己的工厂结合工作环境去修正完善这样的宽放率。
这里给大家提供一个:我们这里使用的是宽放率 = 3.5% + 0.30% + 0.70% + 3% + 3.5% = 11%最后的标准工时 = 7.0*1.11 = 7.8S。
标准工时

标准工时、瓶颈工时
在IE中,有几个关于产品的工时需要了解并掌握,特整理如下:
1、循环工时(Cycle Time)--C/T
单个站位周期作业时间、不包含作业放宽的工时,一个产品的Cycle Time,即为该产品所有站位的Cycle Time总和。
2、标准工时(Standand Time)--S/T
在适宜的操作条件下,用最合适的操作方法,以普通熟练工人的正常速度完成标准作业所需的劳动时间。
其构成为:
计算方式为:
标准工时=正常时间+放宽时间
=正常时间×(1+放宽率)
=平均操作时间×评比系数+放宽时间
=平均操作时间×(1+评比系数+放宽率)其中:平均时间是指观察后:(∑产品C/T/观测周期数)
3、瓶颈工时(Bottleneck Time)--B/T
在流水线作业下,产品产能可透过B/T进行计算,如下:
日平均产能=日工作时间/Bottlenect Time×生产效率
4、实际作业时间(Actual Tact Time)--T/T
与客户需求量相关,取决于客户需求,其计算过程为:
T/T=日工作时间/日客户需求量
其中,又以T/T来变更产品的C/T,当C/T接近于T/T时为最佳管理要求。
C/T>T/T时,
说明产线有改善空间,而C/T<T/T时,又会造成多生产,增加库存。
5、总制造时间
即一个产品所有站位的C/T总和。
6、总制程时间
包含平衡损失的工时通常为:
B/T*站位数
7、平衡率
即编程效率,计算过程为:
总制造时间/总制程时间。
各工序工时计算表
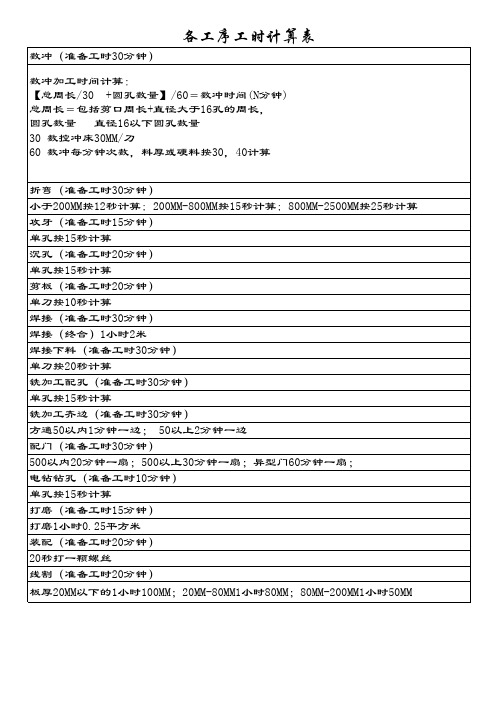
- 1、下载文档前请自行甄别文档内容的完整性,平台不提供额外的编辑、内容补充、找答案等附加服务。
- 2、"仅部分预览"的文档,不可在线预览部分如存在完整性等问题,可反馈申请退款(可完整预览的文档不适用该条件!)。
- 3、如文档侵犯您的权益,请联系客服反馈,我们会尽快为您处理(人工客服工作时间:9:00-18:30)。
烘烤 0.95
卸網版 清潔 1.79
標準工時應為 8.49 + 5.96 + 5.83 = 20.28 sec/pc 每人
所有制程标准工时计算范例
其他考量A
網版印刷製程
考量每次需求產量因素下: 預烘烤 30 * 60 * 5/(60 * 42) = 3.57 sec/pc每人 烘烤 8 * 60 * 5/(60 * 42) = 0.95 sec/pc每人 架網版調墨 20 * 60 * 5/(60 * 42) = 2.38 sec/pc每人 卸網版清潔 15 * 60 * 5/(60 * 42) = 1.79 sec/pc每人
人員 5
6 sec/片
0.375 sec/pc
人員 5
60 sec/車
0.0375 sec/pc
人員 1-5
假設,每5片需進行網板擦拭作業,此時機台停機,每次擦拭需要90sec.
所有制程标准工时计算范例
計算公式
網版印刷製程
架網版 調墨
人員 1-5
清潔
sec/pc
1次印刷 3.57 + 3.13 + 1.79 = 8.49 sec/pc每人 2次印刷 2.38 + 1.79 + 1.79 = 5.96 sec/pc每人 3次印刷 2.38 + 1.66 + 1.79 = 5.83 sec/pc每人
標準工時 = 8.49 + 5.96 + 5.83 = 20.28 sec/pc每人
此時間為每次印刷之瓶頸 時間,通常為印刷這個作業.
After 2’nd printing
所有制程标准工时计算范例
情況A
網版印刷製程
1. 網印機台 1 台 2. 需先烘烤 30 min 3. 網版架設 20 min 4. (含定位與試印) 4. 網版拆卸與清洗 15 min 5. 每次印刷後需烘烤 8 min 6. 每片 42 pc 7. 每次投產 60 片
印刷C/T = (100+20) * 60 /[(60/10)*100] = 12 sec/pc
所有制程标准工时计算范例
補充說明
一般加工製程
6. 印刷、硬鍍、噴漆或類似製程 C). 烘烤部分:使用輸送帶式烘乾機則不納入工時計算,非使 用輸送帶式烘乾機則以下列方式考慮:
多套載具之情況 Ⅰ).印刷時間比烘烤時間(分攤成每pc後)大時, 則烘烤時間不納入工時計算,以印刷工時為主. Ⅱ).印刷時間比烘烤時間(分攤成每pc後)小時, 則以烘烤時間當印刷工時.
所有制程标准工时计算范例
情況B
網版印刷製程
1. 網印機台 1 台
2. 需先烘烤 30 min
3. 網版架設 20 min
4. (含定位與試印)
4. 網版拆卸與清洗 15 min
5. 每次印刷後需烘烤 8 min
6. 每片 42 pc
7. 只有一班,每日印刷完需拆
下網版
3
Print 2
UV Oven 4
人工台
成型製程
定義:有人員隨台顧台,產品為人工方式取出,人員需進行開 關門之動作,置入皮革,螺帽等元件,通常成型機台作業時,人 員會伴隨進行其他作業.
開模 開門 取出 置入 關門 關模 注塑 開模 開門
T7 T1 T2 T3
T4 T5
T6
T7 T1
開門 取出 置入 關門 剪膠 檢包
開門
T1 T2 T3
架網版 調墨
人員 1-5
清潔
人員 1
印刷
人員2
架網版 調墨
人員 1-5
清潔
人員 1
印刷
人員2
架網版 調墨
人員 1-5
清潔
人員 1
印刷
人員2
網版印刷製程
每片需重覆之動作
檢查
人員3、4
取料
人員5
烘烤
人員5
卸網版 清潔
人員 1-5
檢查
人員3、4
取料
人員5
烘烤
人員5
卸網版 清潔
人員 1-5
檢查
人員3、4
取料
2
3
T1 T2
置入
5 T3
關門 剪膠
2
4
T4
T8
檢包
6 T9
開門
2 T1
人機比 = 人時 : 機時 = 22 : 40 = 1 : 1.81 人時 = T1 + T2 + T3 + T4 + T8 + T9 = 22 機時 = T1 + T2 + T3 + T4 + T5 + T6 + T7 = 40
T3
人員週期
設備週期 = T1 + T2 人員週期 = T2 + T3 作業週期 = Max( T1 + T2 , T2 + T3 ) 每時產能 = 3600 / [Max(T1 + T2 , T2 + T3 )]
所有制程标准工时计算范例
注意事項
一般加工製程
➢ 必須將所有之作業考量在內,特別是非 每pc執行之作業,但不含不正常作業部 份.
卸網版 清潔
人員 1-5
標準工時 = Max (A,B,C,D)*5+1.125 *5 = 0.75*5+5.625 = 9.375 sec/pc 線平衡係數 = [( 0.375 +… + 0.0375) + 5.625] / 9.375 = 89.7 %
所有制程标准工时计算范例
作業流程
本例為三次印刷
補充說明
一般加工製程
3. 無需人員操作 案例:人員只需設定參數,或運送至該處. A). 只需運送:將運送時間攤換成每pc所需之時間,並將時間 加到上一站之作業時間.(有時可能為後一站) B). 需設定參數:將設定與運送時間攤換成每pc所需之時間, 並將時間加到上一站之作業時間.(有時可能為後一站)
3
Print 2
UV Oven 4
Clear
3
1
所有制程标准工时计算范例
工時分析A
網版印刷製程
預烘烤 30 min
架網版 調墨 20 min
A
1次印刷 3.13
烘烤 8 min
卸網版 清潔 15 min
架網版 調墨 20 min
B
2次印刷 1.79
烘烤 8 min
卸網版 清潔 15 min
代表同步工時,不納入標準工時計算
此時,人員閒置時間過長,需加以改善,改善方式有兩個方向:
1. 縮短機器時間 : 重點在於縮短開模,關模,注塑之時間.
2. 增加人員作業時間 : 下製程之作業可拉至成型(CFM),.
3.
一人兩機(機器時間需拉長或人員時間需縮短).
所有制程标准工时计算范例
表單填寫
成型製程
請將前述所提之 標準工時計算結
A 0.375 sec/pc
人員 2
0.75 sec/pc
B 0.75 sec/pc
人員 3、4
1.25 sec/pc
C 0.625 sec/pc
人員 5
0.375 sec/pc
人員 5
0.0375 sec/pc
D 0.4125 sec/pc
擦拭分攤 = 90 /(5*16) = 1.125 sec/pc
Clear
3
1
所有制程标准工时计算范例
工時分析B
網版印刷製程
預烘烤 30 min
架網版 調墨 20 min
一套載具之情況 印刷之工時 = 實際印刷工時 + 烘乾工時(分攤後)
所有制程标准工时计算范例
主要作業與假定
網版印刷製程
1. 總投入人數 5 人 2. 印刷後烘烤 80 min 3. 烘烤單位為一車100片 4. 網版拆卸與清洗 15 min 5. 網版架設 20 min 6. (含定位與試印) 6. 每片 16 pc 7. 假設烤箱是足夠的
4. 需分模號:需將分模號之時間分攤到每pc. 案例:銑膠有分模號之情形 EX:每盤24pc,銑膠時間 5 sec;分模號時間 24 sec/盤 銑膠C/T = 銑膠時間 + 分模號時間 / 數量
= 5 + 24 / 24 = 6 sec/pc
所有制程标准工时计算范例
補充說明
5. 元件是用載具承裝時(或類似情況): 需將拿取與放置載具之時間分攤
設備A 設備B 人員
取放 T1
取放 T1
壓合 T2 取放 T1
檢查 取放 T3 T1
取放
壓合 T2
檢查 取放 T3
壓合 取放
檢查 取放
壓合 檢查
設備週期 = T1 + Max(T2, T3+T1+T3) 人員週期 = T1 + T3 作業週期 = Max( 人員週期 , 設備週期/2 )
所有制程标准工时计算范例
所有制程标准工时计算 范例
2020/11/19
所有制程标准工时计算范例
自動台
成型製程
定義:無人隨台顧台,產品為頂出,手臂夾取等方式取出
開模 取出 關模
T1
T2
T3
注塑
T4
完整週期
開模 取出 關模
T1
T2
T3
完整週期
注塑
T4
標準工時(循環時間) = T1 + T2 + T3 + T4
所有制程标准工时计算范例
設備週期 = T1 + Max( T2 + T3 , T5 + T6 ) 人員A週期 = T2 + T3 + T4 人員B週期 = T5 + T6 作業週期 = Max( T1 , T4 ) + Max( T2 + T3 , T5 + T6 )