轴承套圈锻造工艺研究
圆锥滚子轴承套锻工艺研究
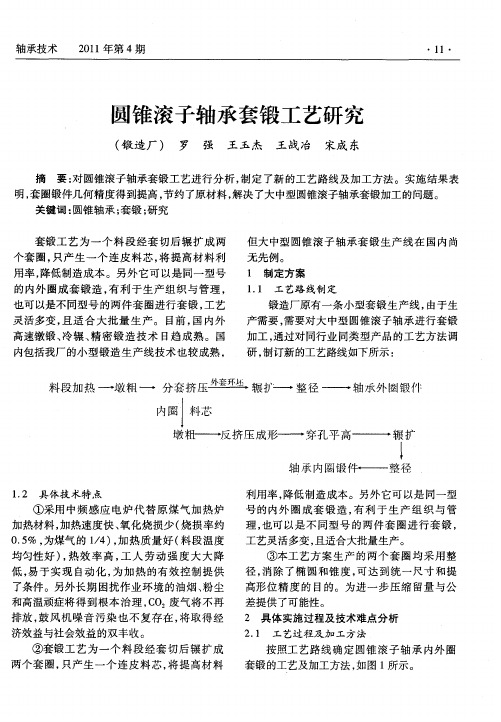
理, 也可 以是不 同型 号的两件套圈进行套 锻 , 工 艺灵 活 多变 , 且适合 大批 量生 产 。 ③本工艺方 案生产 的两个套 圈均采用 整
・
l 2・
轴承技术
2 1 年第 4 01 期
『 [一 『 I ] ] 趱
l
’
一
扩、 径 孔 外
扩孔 、整 内径
轴承技 术
21 0 1年第 4期
圆锥滚 子轴承 套锻工 艺研究
( 锻造 厂) 罗 强 王玉杰 王战 冶 宋成 东
摘 要 : 圆锥滚 子 轴承 套锻 工 艺 进行 分 析 , 定 了新 的工 艺路 线 及 加 工方 法 。实施 结 果 表 对 制
明, 套圈锻件几何精度得到提高 , 节约了原材料 , 解决了大中型圆锥滚子轴承套锻加工的问题 。 关键 词 : 圆锥 轴 承 ; 锻 ; 究 套 研 套锻工艺为 一个料段 经套切后辗 扩成两 个套 圈, 只产生一个连 皮料芯 , 提高材料利 将 用率 , 降低制造成本 。另外它可以是 同一型号 的内外 圈成套锻 造 , 有利于生产组织 与管理 , 也 可 以是不 同 型号 的两 件 套 圈 进 行套 锻 , 工艺 灵活多变 , 且适 合大批 量生产 。 目前 , 国内外 高速镦锻、 冷辗 、 精密锻造 技术 日趋 成熟。国 内包括我厂的小型锻造生产线技术也较成熟 ,
轴承技术
2 1 年第 4 01 期
・ 3・ 1 ຫໍສະໝຸດ 整体 式结构 图4 组合式结构
图 4中左 图所 示 为最 初 的涨 孔 工序 , 图 右
让金 属 沿 最 小 阻力 方 向 流 动 。原 小 型 圆锥 内
为改进后 的涨孔 工序。其 中两 图的主要 区别
浅谈轴承套圈锻造工艺基本设计原则与优化

越高 , 提高 了对 前道工序 的质量要 求 , 增加 了消耗 , 因此扩孔 比的取值不可 能无 限小 , 一 般轴承 套 圈锻 造规格 、 规 范及生 产实 际经验要 求扩 孔 比的取值范 围在
1 . 2 - 1 . 6较为合 适 。 ②压 平量 的取值 越大 , 涨 孔压平 后的 毛坯表 面形成 的 外观 缺 陷影 响较大 , 要 求适 当大 的扩 孔 比进行 充分辗 扩消 除缺 陷, 压 平量的 取值越
子轴 承的 内圈 , 其 方法 完全相 同, 只是 最后 省去 了整 径工序 。
包 括半 公差) 。 ③扩 孔 比和压平 量的 共同取值 , 既要分别 符合 上述要 求 , 相互 取 值 的分布 应符 合 线性 同比分布 这一 规律 。
2 . 轴 承套 圈锻 造工 艺的 基本设 计 原则 轴 承套 圈锻 造工艺 的设 计有 三项基 本 原则 。 第 一条是 重量 不变原 则 。 它 是说参 与锻 造的锻 件应重量 相等 。 这 一原则 不 但需要 考虑 锻件 的重量 在经 过煅烧 后的 平均损 失情况 , 即考 虑火 耗 、 锻件余量 及尺寸 公差的 实际状 况、 合理 配置重量 等 , 而且还要考 虑到锻件 在煅烧 过程 中, 因为 温度 不同 , 而对 锻件 尺寸造 成的影 响 , 以便 能够准确 设计 出不 同状 态下 的
度在 7 0 0 5 2 以上 的 , 不得堆积 摆放 。 以 圆锥 滚子轴 承套圈 的锻造 为例 来探析 我国
轴承套 圈锻 造工 艺 的现状 。
小, 对 涨孔压 平后 毛坯表 面形成 的外观 缺陷影 响较小 , 因此 较小 的扩孔 比辗 扩
即能消 除 , 但 是 比较小的压 平量 不足 以消除套 切形成 的两端 平面缺 陷 , 也达 不
轴承内外圈套锻工艺研究

摘要锻造工业是一个国家的重要产业,套锻工艺的发展无时不刻都在影响着国家经济的发展,人类的进步离不开套锻工艺的发展。
在全球经济发展的大环境下,中国各个行业被其他国家的先进技术影响的同时,越来越多的外国企业和品牌传播到中国已经成为现实。
在新的市场需求的推动下,对轴承内外圈套锻工艺进行改良和优化是当务之急。
生产轴承内外圈套锻工艺的企业,必须充分考虑到在轴承内外圈套锻工艺运行中可能出现的问题,尽量使轴承内外圈套锻工艺的自动化程度越高越好,从而来保证轴承的传动精度,特别是针对圆锥滚子轴承,国内轴承内外圈套锻工艺的研发及制造要与全球号召的高效、精度高等主题保持一致。
套锻工艺是通过一次对轴承毛坯进行加热同时生产出两个套圈,本文就轴承的内外圈套锻工艺进行了设计,通过阐述了套锻工艺的发展现状以及工艺流程,最后设计出针对圆锥滚子轴承的套锻模具。
关键词:套锻轴承内外圈制造模具Abstract:This graduation design is the optimization design of driving roller conveyor, first on the driving roller type conveyer is summarized; then analyzed the selection principle and calculating method of driving roller conveyor; then calculated based on these design criteria and abase is designed; then checked on the main parts selected conveyor. Is the drive roller conveyor consists of four main parts: driving device, tension device, middle rack, and the moving part. Finally, a simple description of the installation and maintenance of transport. At present, the drive roller conveyor is moving towards long distance, high speed, low friction direction, air cushion conveyor in recent years is one of the. the motion trajectory when the diagonal curve is slanting line do the walking motion, robot. The miniature walking robot is mainly driven by DC servo motor, so as to drive the leg action driven synchronous belt wheel by a crank and rocker mechanism.In the design, driving roller type conveyer manufacture and application, at present our country compared with foreign advanced level there are still large gaps, domestic in the design and manufacture of driving .This design is the optimization design of driving roller conveyor.Keywords:Driving roller Crankshaft Processing craft Significance目录1 绪论 (1)1.1课题的来源与研究的目的和意义 (7)1.2本课题研究的内容 (10)1.3研究的意义 (10)2 轴承内外圈套锻工艺总体结构的设计 .......... 错误!未定义书签。
轴承套圈锻件加工工艺

轴承套圈锻件加工工艺轴承套圈锻件是一种常见的机械零件,通常用于支撑或引导旋转轴,起到支撑,定位和传递运动的作用。
在轴承套圈锻件加工工艺中,一些关键的工艺流程必须被重视和掌握。
以下是关于轴承套圈锻件加工的详细流程,以便更好地理解。
第一步,材料选择。
轴承套圈锻件通常由大量的金属材料制成。
常见的材料类型包括钢、铜、铝和钛等。
选择合适的材料可以大大提高轴承套圈锻件的机械强度和耐用性。
第二步,坯料的制备。
在轴承套圈锻件的制造过程中,坯料的制备非常重要。
其一种常见的方法是通过热镦,先制造出一根粗坯。
然后再通过热成形将其加工成所需的轴承套圈锻件。
第三步,火焰切割。
一旦坯料经过镦粗后,需要进行火焰切割。
这项工艺可以将较大的坯料切割成所需的形状和大小,为下一步的冷成形做好准备。
第四步,冷锻成形。
在这个阶段,坯料被夹在工艺模具中进行成型。
轴承套圈锻件的形状和尺寸可通过调整模具的设计来获得。
活塞冷锻机或连续式冷锻机都可以用于这一步骤。
第五步,热处理。
热处理是将铸件或锻件施加热力,使其加热到一个特定温度下,然后在适当的温度保温一段时间并于冷却,目的是通过改变其结构来提高其物理性质和力学性质的过程。
由于轴承套圈锻件的应用场景要求其具备相当的机械强度,因此对于这一步骤需要格外重视。
第六步,机械加工。
热处理后的轴承套圈锻件需要进行机械加工,以获得更高的精度和表面光滑度。
常用的机械加工设备包括车床、铣床、钻床和磨床等。
第七步,质量检测。
为了保证轴承套圈锻件的质量和安全性,必须对其进行质量检测。
这些包括尺寸检查、表面瑕疵的检查、硬度测试和耐蚀性测试等。
总之,轴承套圈锻件加工工艺复杂,需要经验丰富的专业技术人员才能操作,勤奋的工人和高性能的机械设备。
通过严格的质量控制,可确保轴承套圈锻件具有良好的耐用性和长期的稳定性。
圆锥滚子轴承套圈内外同套锻造工艺及其控制
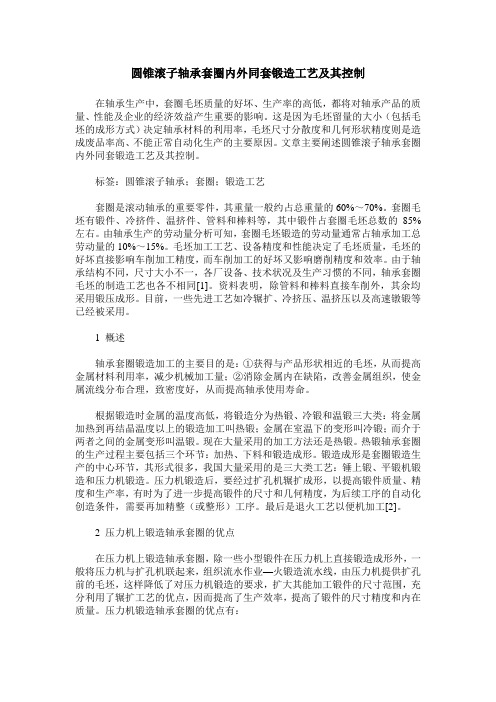
圆锥滚子轴承套圈内外同套锻造工艺及其控制在轴承生产中,套圈毛坯质量的好坏、生产率的高低,都将对轴承产品的质量、性能及企业的经济效益产生重要的影响。
这是因为毛坯留量的大小(包括毛坯的成形方式)决定轴承材料的利用率,毛坯尺寸分散度和几何形状精度则是造成废品率高、不能正常自动化生产的主要原因。
文章主要阐述圆锥滚子轴承套圈内外同套锻造工艺及其控制。
标签:圆锥滚子轴承;套圈;锻造工艺套圈是滚动轴承的重要零件,其重量一般约占总重量的60%~70%。
套圈毛坯有锻件、冷挤件、温挤件、管料和棒料等,其中锻件占套圈毛坯总数的85%左右。
由轴承生产的劳动量分析可知,套圈毛坯锻造的劳动量通常占轴承加工总劳动量的10%~15%。
毛坯加工工艺、设备精度和性能决定了毛坯质量,毛坯的好坏直接影响车削加工精度,而车削加工的好坏又影响磨削精度和效率。
由于轴承结构不同,尺寸大小不一,各厂设备、技术状况及生产习惯的不同,轴承套圈毛坯的制造工艺也各不相同[1]。
资料表明,除管料和棒料直接车削外,其余均采用锻压成形。
目前,一些先进工艺如冷辗扩、冷挤压、温挤压以及高速镦锻等已经被采用。
1 概述轴承套圈锻造加工的主要目的是:①获得与产品形状相近的毛坯,从而提高金属材料利用率,减少机械加工量;②消除金属内在缺陷,改善金属组织,使金属流线分布合理,致密度好,从而提高轴承使用寿命。
根据锻造时金属的温度高低,将锻造分为热锻、冷锻和温锻三大类:将金属加热到再结晶温度以上的锻造加工叫热锻;金属在室温下的变形叫冷锻;而介于两者之间的金属变形叫温锻。
现在大量采用的加工方法还是热锻。
热锻轴承套圈的生产过程主要包括三个环节:加热、下料和锻造成形。
锻造成形是套圈锻造生产的中心环节,其形式很多,我国大量采用的是三大类工艺:锤上锻、平锻机锻造和压力机锻造。
压力机锻造后,要经过扩孔机辗扩成形,以提高锻件质量、精度和生产率,有时为了进一步提高锻件的尺寸和几何精度,为后续工序的自动化创造条件,需要再加精整(或整形)工序。
轴承套圈锻造工艺过程数值模拟研究

( 0 9 0 2 10 3 ) 1
参磊 …
热
5 9
2 N 0 k 液压支架内加载整架试验台 00 0 液压系统的设计
阳泉煤 业集 团华 越机械有 限公 司 ( 山西 0 5 0 ) 郝铁栓 4 0 8 李跃 军
随着 国内各大煤业集团煤炭产量的逐年提升 ,
采 煤工 作 面 机 电装 备 的 配 置也 相继 达 到 了国 际先 进
二 、上乙以进 三 、工艺改进
针 对上 述成 形 工艺 ( 见 图 1 )特 点 ,结 合轴 承 生 产 2
大 ,对设备及模具要求较高 。
通过 对工 艺 进 一 步 改进 提 出旋 压方 式 成 形 轴承
套 圈,该成形工艺设备简单 可以提高生产效率和
成 形 质 量 。MW
实际 ,现采用旋 压方式 成形
升至 所 需 的 高度 ,并 用卡 环 将 其 固定 ,然后 加 载 ,
即 可对 液 压 支架 完 成 一 系列 相 关 型式 试 验及 出厂 压 架试 验 。
在对液压支架进行内加载试验时 ,将不 同形状
的试 验 垫 块 ,放 置 在 支架 顶 梁 或底 座 的 规定 位 置 上 模拟 工 况 。然 后 将 支架 在 试 验 台的 工 作 台和 上 梁 之
司 机 电装 备 制造 、修 理和 试 验 的核 心 单 位 ,是 否 拥
/支 有高性能的制造设备和试验设备 ,直接决定着公司 。 支 架 设 定 在 23 护 高 度 上 ,通 过 油 压 控 制 系 统 , 以 油液 为 动 力 ,操 作 电 磁 阀控 制 升 降缸 ,使移 动 梁 生产制造和维修试验的能力水平及制修质量 。
轴承套圈的锻造工艺流程

轴承套圈的锻造工艺流程
轴承套圈是一种用于支撑轴承的零部件,其制作工艺流程十分关键。
以下是轴承套圈的锻造工艺流程:
1. 原材料准备:选用合适的钢材作为原材料,经过锤击、热处理等加工后,得到符合要求的锻坯。
2. 制模:根据轴承套圈的设计要求,制作模具,并对模具进行加热,以防止热胀冷缩后对成品造成影响。
3. 预热:将锻坯放入加热炉中进行预热,使其达到适宜的锻造温度。
4. 锻造:将预热后的锻坯放入模具中,进行锻造。
锤击的力度、频率和方向必须得到严格控制,以确保锻坯能够达到预期的形状和尺寸。
5. 精修:经过锻造后的轴承套圈需要进行精修,包括去除毛刺、平整表面等工序。
6. 热处理:经过锻造和精修后的轴承套圈需要进行热处理,以提高其机械性能和耐磨性能。
7. 检验:对成品轴承套圈进行非破坏性和破坏性检验,以确保其符合设计要求。
以上是轴承套圈的锻造工艺流程,每个步骤都需要严格把控,以确保成品质量达到要求。
- 1 -。
轴承套圈锻造工艺研究
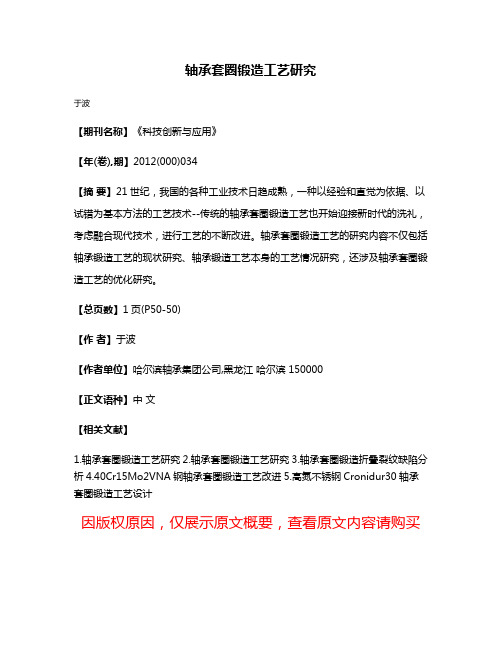
轴承套圈锻造工艺研究
于波
【期刊名称】《科技创新与应用》
【年(卷),期】2012(000)034
【摘要】21世纪,我国的各种工业技术日趋成熟,一种以经验和直觉为依据、以试错为基本方法的工艺技术--传统的轴承套圈锻造工艺也开始迎接新时代的洗礼,考虑融合现代技术,进行工艺的不断改进。
轴承套圈锻造工艺的研究内容不仅包括轴承锻造工艺的现状研究、轴承锻造工艺本身的工艺情况研究,还涉及轴承套圈锻造工艺的优化研究。
【总页数】1页(P50-50)
【作者】于波
【作者单位】哈尔滨轴承集团公司,黑龙江哈尔滨 150000
【正文语种】中文
【相关文献】
1.轴承套圈锻造工艺研究
2.轴承套圈锻造工艺研究
3.轴承套圈锻造折叠裂纹缺陷分析
4.40Cr15Mo2VNA钢轴承套圈锻造工艺改进
5.高氮不锈钢Cronidur30轴承套圈锻造工艺设计
因版权原因,仅展示原文概要,查看原文内容请购买。
- 1、下载文档前请自行甄别文档内容的完整性,平台不提供额外的编辑、内容补充、找答案等附加服务。
- 2、"仅部分预览"的文档,不可在线预览部分如存在完整性等问题,可反馈申请退款(可完整预览的文档不适用该条件!)。
- 3、如文档侵犯您的权益,请联系客服反馈,我们会尽快为您处理(人工客服工作时间:9:00-18:30)。
轴承套圈锻造工艺研究
轴承套圈的锻造是机械锻造中一个核心课题,文章对此展开论述,首先对轴承套圈锻造工艺现状进行简介,接着阐述轴承套圈锻造工艺的基本设计原则,在此基础上结合轴承套圈锻造工艺本身的特殊性,从建立产品及锻造工艺模型以及套圈锻造工艺的优化设计等方面进行深入的阐述。
标签:轴承套圈;锻造工艺;优化设计
引言
轴承套圈的锻造是机械锻造中比较典型的一类加工。
轴承套圈指的是环形且有着多个滚道结构的向心轴承。
轴承在机械制造等领域的应用十分广泛。
其在结构上的优势是装拆过程十分简易、轴向不会发生改变、且轴向的位置能够轻易被调整。
轴承套圈结合具体的结构,也可以细分成不少类型,例如圆锥内圈与外圈、双滚道内外圈等等。
在机械锻造领域,对于轴承套圈锻造工艺的经验总结和方法优化是一个核心课题,掌握好轴承套圈锻造的工艺,一方面能够降低加工的支出成本,另一方面也能够保证套圈产品的质量,具有比较好的理论价值和实践意义。
1 轴承套圈锻造工艺概述
轴承套圈是一种应用非常广泛的机械部件,一个轴承套圈锻件成品一般都要经过多道次的毛坯逐点逐步锻造变形而获得,其具体的制造可以细分成四个步骤:粗模的锻造、锻件的热处理、在电脑监控下进行精确磨削、标志的添加。
文章关注的重点是其在锻造的时候所采用的工艺。
在零件的锻造中,如果由于工艺的不完善而导致的过烧、过热等情况发生,便会显著影响到轴承本身的强度和质量。
因此一定要在锻造过程的全程中严格实时控制锻造环境的温度、循环加热等参数,尤其是一些体积相对较大的轴承品种,如果成品的温度超过了七百摄氏度,严禁以堆积的方式进行码放。
文章的阐述均以圆锥滚子轴承套圈为例。
此类轴承的锻造大部分使用的是单挤工艺,尤其是对一些体积偏大的轴承而言,应把锻造原料进行加热,并通过挤压使其基本成形,然后通过切芯扩孔,进行外径和内径的调整,形成轴承。
2 轴承套圈锻造工艺原则
(1)重量守恒。
指的是所有锻造的锻件在质量方面要完全相同。
这个准则一方面应该考虑参与锻造的锻件在煅烧工序之后的材料损失,包括火耗、尺寸公差等因素,另一方面还应顾及参与锻造的锻件在工序中,由于温度的变化,导致锻件本身的大小受到影响,只有严格控制以上的因素,才能够作出隔阂的轴承套圈锻造产品。
(2)减少缺陷。
轴承套圈的锻造是一个相对复杂的工艺过程,绝非几项简单操作的集合,必须在各类参数严格控制之下才能产出成品,由于外界环境并非完全理想,因此所有的工序均能够存在一些扰动因素而导致缺陷的发生。
缺陷的外在表现形式,有时是毛刺、凹坑,有时是圆角等,假若无法在具体的工
艺中进行圆整操作,将会使各类缺陷最终反映在锻件成品上,导致锻件的质量发生重大缺陷。
因此在具体操作的工艺中,要尽最大努力保证锻件的毛皮条件,并且锻造应有足够大的变形量,从而降低毛坯中缺陷的发生率。
(3)同比例变形。
一个合格的轴承套圈产品,需要经历多个锻造工序,在各类工序之中均会经历很多次变形过程,假若半成品的每一个部分在变形方面没能遵循比例,则会由于误差的叠加导致毛刺、凹坑、圆角等各类缺陷的产生,又由于在加工过程中的变形导致的短剑内部应力,最终很容易使其发生变形,成为不合格产品。
3 轴承套圈套锻造工艺及优化
对于轴承套圈的锻造,本身具备一些特殊之处。
此处以内外圈双扩孔工艺作为案例进行探讨,其具体的步骤包括九项,分别是原料的准备、原料加热至适合温度、对原料进行套切、套切后的涨孔压平、对外圈进行扩孔、对内外径进行调整、轴承内圈成形、轴承切底以及轴承内圈扩孔。
在这九项工序之中,尤以其中的套切工序最为重要。
原因是此工序能够决定将来成品的内、外圈配重、扩孔比等重要参数,因此该工序基本上决定了最终成形的锻件的质量。
而锻件扩孔比的选取则能够决定着单件生产时间,因此对批量生产产品的情况非常重要。
此外还有一个关键工序控制,就是压平量及扩孔比。
原因在于:首先绕过所选择的扩孔比足够大,则避免毛坯锻件产生缺陷的能力就越高,锻件经过辗扩以后便会形成更为致密的内部组织,而因为被很多外部条件所制约,导致锻件的扩孔比是无法取太大数值的,而假若扩孔比不够大,则避免毛坯锻件缺陷的能力便会较低,这就对前道工序提出了更高的要求,使锻造流程的消耗上升,所以扩孔比在取值方面也不能过于低,结合作者的经验,在轴承套圈锻造的过程中,将扩孔比控制在1.5左右能够达到较好的效果。
其次是对压平量的参数控制,如果此参数过大,则锻件在涨孔压平操作之后,其所形成的毛坯便会在表面出现一些外观缺陷,只有继续增加锻件的扩孔比,再能通过辗扩的工序尽量减少这些缺陷,如果此参数过小,则毛坯锻件表面的外观缺陷便会比较少,所以只需不大的扩孔比便可消除这些缺陷,而另一方面,结合笔者的实践经验,此参数的选取可控制在20%Cn左右。
以上所阐述的是传统的成熟锻造工艺,从传统工艺的典型步骤能够看出,如果要进一步增强锻造材料的利用率以及产品的质量合格率,最核心的步骤便是辗扩工序。
当前较常使用的辗扩工序一般多为直圈辗扩方式。
不少实践领域的技术人员和工程专家均在最新的研究中将原直圈辗扩升级成仿形辗扩,其工艺的优化来自两个方面,一是对套圈锻件的尺寸留量进行调节,二是对其形状进行调整,最终达到增加材料利用率的目的。
而其中最为关键的轴承套圈辗扩工序,目前难以完全令人满意。
随着技术的发展,不少专家学者和生产实践的一线人员均在探索轴承套圈锻造工艺的优化方法策略,并已经取得了值得引入的方法。
文章重点阐述的优化方法是:下料、加热、镦粗、挤压、切底、辗扩、喷丸。
锻造流程阐述如下:(1)轴承数据库的构建。
此库中动态存储了轴承工艺参数信息,为锻造过程的实时控制提供支持。
(2)轴承模型的构建。
首先能够在轴承模型内通过具体的程序来验证数据库中信息的准确性,此外也能够通过轴承模型提供成品加工的模板。
(3)构建轴承套圈优化模型。
在优化模型中应该包含轴承套圈公差标准
和尺寸等关键信息。
在具体的设计过程只,仅需提供必要的轴承产品信息,便能够在工艺模型库中生成所需的工艺数据。
在具体的锻造过程中,应结合所述的优化工艺。
结合23222CA的轴承内圈工艺标准进行锻造,需要注意的是,锻造流程的粗车工序,应该及时去除半成品滚道由于高温而产生的氧化薄层,从而确保刀具的精度。
这一步骤能够以多种方式完成:例如可以通过仿形法去掉产品圆弧表面,也可以通过成型车刀等等。
作者结合自身的实践经验,在实际操作的过程中采取了第二个方案,结果显示完全能够达到轴承套圈的技术标准,材料利用率可以在原来基础上平均提高3~4%。
表1所示为测试结果。
表1 轴承套圈优化前后技术数据对比
4 结束语
在机械锻造领域,轴承套圈锻造工艺的研究一直是一个焦点,良好的锻造工艺能够保证工业资源的节约、减少制造成本。
在实践中,有不少专家学者和技术领域的人才均在不断地摸索锻造工艺的优化方案,最终提高金属材料利用率,节约原材料,减少机械加工量,降低成本保证产品的质量。
参考文献
[1]谢懿.实用锻压技术手册[M].北京:机械工业出版社,2013.
[2]周大隽,韩鹏彪.锻压技术数据手册[M].北京:机械工业出版社,2008.
[3]王荣桥,朱凯.UG零件设计教程(UnigraphicsV18.0)[M].北京:北京希望电子出版社,2012.。