自磨机和半自磨机的尺寸规格
自磨、半自磨技术的新进展
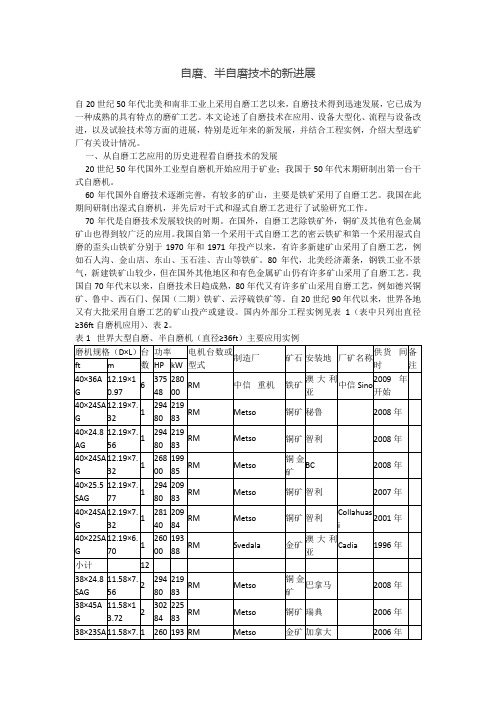
自磨、半自磨技术的新进展自20世纪50年代北美和南非工业上采用自磨工艺以来,自磨技术得到迅速发展,它已成为一种成熟的具有特点的磨矿工艺。
本文论述了自磨技术在应用、设备大型化、流程与设备改进,以及试验技术等方面的进展,特别是近年来的新发展,并结合工程实例,介绍大型选矿厂有关设计情况。
一、从自磨工艺应用的历史进程看自磨技术的发展20世纪50年代国外工业型自磨机开始应用于矿业;我国于50年代末期研制出第一台干式自磨机。
60年代国外自磨技术逐渐完善,有较多的矿山,主要是铁矿采用了自磨工艺。
我国在此期间研制出湿式自磨机,并先后对干式和湿式自磨工艺进行了试验研究工作。
70年代是自磨技术发展较快的时期。
在国外,自磨工艺除铁矿外,铜矿及其他有色金属矿山也得到较广泛的应用。
我国自第一个采用干式自磨工艺的密云铁矿和第一个采用湿式自磨的歪头山铁矿分别于1970年和1971年投产以来,有许多新建矿山采用了自磨工艺,例如石人沟、金山店、东山、玉石洼、吉山等铁矿。
80年代,北美经济萧条,钢铁工业不景气,新建铁矿山较少,但在国外其他地区和有色金属矿山仍有许多矿山采用了自磨工艺。
我国自70年代末以来,自磨技术日趋成熟,80年代又有许多矿山采用自磨工艺,例如德兴铜矿、鲁中、西石门、保国(二期)铁矿、云浮硫铁矿等。
自20世纪90年代以来,世界各地又有大批采用自磨工艺的矿山投产或建设。
国内外部分工程实例见表1(表中只列出直径≥36ft自磨机应用)、表2。
表1 世界大型自磨、半自磨机(直径≥36ft)主要应用实例表2 国内大型自磨机应用实例*为原初步设计。
二、自磨设备大型化取得新进展自磨设备大型化是降低基建投资和生产费用、提高劳动生产率的重要途径,也是自磨技术发展的重要标志之一。
自自磨工艺在工业上应用以来,自磨机的大型化一直是选矿界河设备制造部门的重要开发研究课题,并不断取得新进展。
50年代自磨工艺刚刚在工业上应用,自磨机规格较小。
60年代出现了φ9.75m(32英尺)自磨机,并先后应用于某些矿山。
磨机主要参数的确定
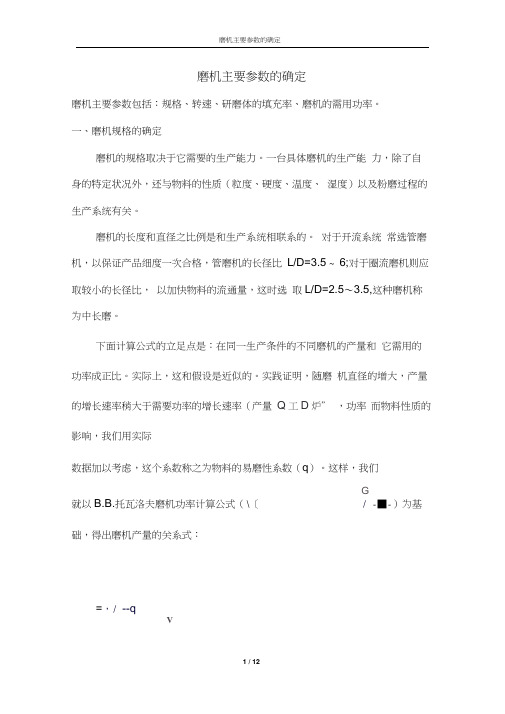
磨机主要参数的确定磨机主要参数包括:规格、转速、研磨体的填充率、磨机的需用功率。
一、磨机规格的确定磨机的规格取决于它需要的生产能力。
一台具体磨机的生产能力,除了自身的特定状况外,还与物料的性质(粒度、硬度、温度、湿度)以及粉磨过程的生产系统有关。
磨机的长度和直径之比例是和生产系统相联系的。
对于开流系统常选管磨机,以保证产品细度一次合格,管磨机的长径比L/D=3.5 ~ 6;对于圈流磨机则应取较小的长径比,以加快物料的流通量,这时选取L/D=2.5〜3.5,这种磨机称为中长磨。
下面计算公式的立足点是:在同一生产条件的不同磨机的产量和它需用的功率成正比。
实际上,这和假设是近似的。
实践证明,随磨机直径的增大,产量的增长速率稍大于需要功率的增长速率(产量Q工D炉” ,功率而物料性质的影响,我们用实际数据加以考虑,这个系数称之为物料的易磨性系数(q)。
这样,我们G就以B.B.托瓦洛夫磨机功率计算公式(\〔/ -■-)为基础,得出磨机产量的关系式:=,/ --qV= 」丽勺,t/h其中:\ [ -- 磨机的粉碎能力,(kw)U 7 nV—磨机有效容积,(\ rvi j ,()D――磨机有效直径,(m1 ------ 磨机有效长度,(m)¥――研磨体填充率,S ――研磨体装入量,(t)(取的容重为4.5「一)n ---- 磨机转速,(rpm)q――物料易磨性(单位电能的产量),(〔)/kw.h易磨性系数普通管磨、圈流、干法窑的 熟料0.035 〜 -0.037 比面积2600〜3000nT*管磨、开流、湿法窑的 0.031 〜 -0.033比面积3000〜3400 ni'f熟料管磨、圈流、湿法窑的 0.037 〜 -0.039比面积2600〜3000册熟料500#普通管磨、开流、干法窑的0.038 〜0.04细度5〜8% (4900孔熟料/(出】筛余)管磨、圈流、干法窑的0.046 〜-0.048细度5〜8% (4900孔熟料/上出】筛余)管磨、开流、湿法窑的0.040 〜-0.042细度5〜8% (4900孔熟料/】筛余)管磨、圈流、湿法窑的0.048 〜-0.050细度5〜8% (4900孔熟料5血?筛余)当预计生产能力Q 给定后,再选定磨机的转速比①,以及研磨体将计算所得之D ,圆整成系列值([)=1.83、2.0、22、2.4、2.6、3.0、3.2、3.5……)。
面粉机械尺寸规格表

面粉机械尺寸规格表因不同的品牌和型号而异,但以下是一些常见的面粉机械尺寸规格:
1. 小型磨面机:该机器通常较小,适用于小型家庭使用。
常见尺寸为长80厘米,宽60厘米,高120厘米。
2. 中型磨面机:适合中小型企业或个体户使用。
常见尺寸为长120厘米,宽70厘米,高130厘米。
3. 大型全自动面粉机:该机器可以一次磨出不同粗细的面粉,适用于大型面粉厂或面粉加工企业。
常见的尺寸为长2米以上,宽度和高度根据具体型号而异。
4. 面粉搅拌机:用于将面粉和其他原料混合在一起。
常见的尺寸为长度在60-70厘米之间,宽度和高度在40-50厘米之间。
5. 面粉分级机:用于将面粉按照颗粒大小进行分级,以便于进一步加工或销售。
常见的尺寸为长度在1-2米之间,宽度和高度根据具体型号而异。
需要注意的是,以上尺寸仅供参考,具体的面粉机械尺寸规格还需根据生产厂家和型号而定。
此外,选购面粉机械时,除了考虑尺寸外,还需考虑其他因素,如性能、效率、耐用性、维护成本等。
此外,除了机械尺寸外,面粉加工设备的产量也是需要考虑的因素之一。
不同的面粉加工设备有不同的产量,可以根据自己的需求选择合适的设备。
同时,还需要注意设备的适用范围和加工精度等因素,以确保所选设备能够满足生产要求。
MZS5525半自磨机参数的确定

机 ),其 值 为 :K : 。
CO S 0/2
由 于 使 用 环 境 ,所 以 传 动 装 置 要 在 主 电 机 与 小 齿 轮之 间设 置减 速机 。 由主 电机转速 995 r/min,选
和 :分别 为最 内层 物料 (或 介 质 )及 最 外 层 取 减速机 的传 动 比 i=6.5,输 入 转 速为 995 r/min 、
自磨 、半 自磨技术 经 历 了半 个 世纪 的摸 索 、改 进 和研 究 ,已经从 一个 有不 断争议 的技术 ,日趋 发展 成 为成 熟可 靠 的技术 。在 世界各 国 ,无论 是新 建厂 、扩 建 厂 还是 老 厂 的 改 造 ,都 几 乎 要 用 自磨 、半 自磨 技 术 。可 以说 ,自磨 、半 自磨 技术 已经 成 为选矿 领域 的 常规 工艺 了 。 自磨 、半 自磨 技 术 不仅 简化 了选 矿 厂 的工 艺流 程 ,改 善 了操 作 条 件 ,减 轻 了劳 动 强 度 ,更 有利 于环 境 。
德 列夫 “球磨 机 的最适 宜转 数 ”一 文结论 : (1)根据 理论 计算 每 一 充填 率都 对 应 有一 决 定
极 大需 用功 率 的转速 ,充填 率愈 大 ,需 用功 率达 到极 大 值 时所需 的转 速愈 高 。
(2)实 际上 由于球 荷 沿磨 机 简体 内表 面滑 动 故 需 用 功 率 达 到 极 大 值 时 的转 数 应 大 于 理 论 所 计 算 的 。
(3)为 了便 于磨 机 有 最 高 的效 率 ,从 生 产 的 观 点 来看 ,在 任何 情况 下 磨 机 均不 应 以低 于根 据 所 采 用 的率填率 而算 出的理论 转数来 工作 。
现取磨 机 工 作 时 充 填率 =35% ,球 的充 填 率 = 10% ,料 的充 填 率 =25% ,则其 相应 的最 大 功 率 转 速 =78%n 故 半 自磨机 的筒体 转 速 :
碎磨回路设计的新思路和方法

Mia Mib Mic Mih 破碎回路 F80 P80 单位功耗 HPGR回路 F80 P80 单位功耗 筒状磨机回路 F80 P80 单位功耗 总的单位功耗
19.4 18.8 7.2 13.9
μm μm kWh/t
52500 12000 0.3
100000 35000 0.6
100000 6500 1.7
式中:Mib=矿石细磨功指数,kWh/t; P1=闭路筛筛孔尺寸,μm Gbp=磨机每转所生成的筛下粒级的净克数; P80=80%通过的产品粒度,μm F80=80%通过的给矿粒度,μm
©2009NERIN
对常规破碎,公式(1)可表述为:
式中:K2=1.0(闭路破碎时) K2=1.19(开路破碎,即自磨/半自磨回路中的砾石破碎) X1=80%通过的回路给矿粒度,μm X2=80%通过的产品粒度,μm Mic——破碎功指数,由SMC试验提供
单位功耗,Kwh/t
38—2.2
©2009NERIN
表3
三个碎磨回路单位矿石功耗的计算结果
SABC HPGR/B 19.4 18.8 7.2 13.9 C/B 19.4 18.8 7.2 13.9 kWh/t kWh/t kWh/t kWh/t
莫勒曾对一个经粗碎后P80=100mm到磨 矿最终产品P80=106μm的矿石,经SMC试验 获得:Mia=19.4 kWh/t,Mic=7.2 kWh/t, Mih=13.9 kWh/t,帮德球磨功指数Mib=18.8 kWh/t,按下述三种碎磨回路计算其回路的 单位矿石功耗的结果列于表3。 · 半自磨——球磨——砾石破碎回路 (SABC) · 第二段破碎——高压辊磨——球磨回 路(HPGR/B) · 第二/第三段破碎——球磨回路(C/B)
水泥磨规格3.2m

水泥磨规格3.2m水泥磨是一种用于生产水泥的设备,其规格为 3.2m,属于比较常见的水泥磨型号之一。
以下是对水泥磨规格3.2m的详细说明:一、基本参数水泥磨规格3.2m是一种比较通用的型号,其磨机直径为3.2米,长度在10-15米之间,属于长磨机。
这种型号的水泥磨通常适用于中小型水泥厂的生产线,可以满足不同种类和规格的水泥生产需求。
二、结构特点水泥磨主要由进料装置、磨机本体、出料装置和传动装置等部分组成。
其中,进料装置通常采用斜槽、皮带输送机或者提升机等设备将物料送入磨机内部;磨机本体由研磨体、衬板和隔仓板等组成,是水泥磨的核心部分;出料装置一般采用空气输送斜槽或者振动筛等设备将磨好的水泥排出;传动装置则由电机、减速机和轴承座等组成,为磨机的运转提供动力。
三、工作原理水泥磨的工作原理主要是通过磨机的旋转运动,将物料进行反复的碾压、研磨和冲击,从而将物料磨细,达到所需的水泥细度。
在磨机旋转的过程中,研磨体和衬板之间会产生摩擦力,使得物料在摩擦力的作用下不断被磨细。
同时,隔仓板的作用可以将物料进行分级研磨,保证不同粒度的物料都能够得到充分的研磨。
四、操作流程水泥磨的操作流程主要包括以下步骤:1.启动前检查:在启动水泥磨之前,需要对设备进行检查,确保进料装置、出料装置、传动装置等各部分都处于正常状态,无异常情况。
2.启动操作:启动水泥磨的传动装置,让磨机开始旋转。
然后逐渐增加喂料量,并观察磨机的运行状态,确保其运转正常。
3.生产操作:在磨机正常运转后,可以根据生产需求进行生产操作。
根据物料的性质和产品要求,可以调整喂料量、研磨体级配和隔仓板的分隔比例等参数,以保证生产出的水泥质量符合要求。
4.停机操作:当需要停机时,首先需要逐渐减少喂料量,待磨机内的物料全部磨完后,再停止传动装置,关闭各部分的电源。
5.维护保养:定期对水泥磨进行检查和维护保养,保证设备的正常运行。
例如检查传动装置的润滑情况、清理进料和出料装置的堵塞物等。
自磨机分类及工作原理介绍

立志当早,存高远自磨机分类及工作原理介绍自磨机是一个筒体,直径很大、转动缓慢的粉磨机。
物料通过入料端的中空轴颈给入磨机内,在物料相互作用下,磨碎至一定细度的物料通过排料端的中空轴颈排出机外。
自磨机是一种兼有破碎和粉磨两种功能的新型磨矿设备,主要用于选矿工业。
根据磨机简体内钢球充填率的不同分为自磨机和半自磨机; 为了消除顽石积累的影响,自磨机允许添加3%左右的大球(φ80~φ120),半自磨机钢球充填率一般为8%~12%,最大可达15%。
从排料类型上分为干式和湿式,一般情况下均采用湿式,干式自磨机和半自磨机仅在无水地区或需要干产品的特殊情况下才考虑应用。
磨机的传动型式分为同步电机传动、异步电机传动和无齿轮传动。
根据功率大小,同步电机传动和异步电机传动分为单传动和双传动。
对于单传动的磨机,按其布置型式分为左装和右装(面对进料端顺着料流方向看,主电机在筒体左侧的是左装,主电机在筒体右侧的是右装)。
根据工艺流程布置的需要,传动装置放置在进料端、出料端法兰均可。
干式和湿式虽有所差别,但工作原理基本相同。
都要求稳定的给矿量(保持物料充填率不变);大小块矿度成一定比例(配比);都是靠筒体的旋转将物料提升到一定的高度,然后抛落下来产生冲击和研磨作用使矿石被磨碎。
从自磨机断面观察可以分成破碎区、磨碎区和瀑落区。
矿石在自磨机中的运动情况如图。
由于在自磨机运动中矿块存在分级作用,所以不同块度的矿石运动轨迹亦不一样。
大块矿石处于旋转的内层(靠近磨机中心),基本上呈泻落状态,形成一个压碎和磨碎区。
它的循环周期短,很快地落在筒体下部,遭到瀑落下来的矿块冲击被碎裂成较小的矿块。
中等和较小的矿块提升高度比大块高,脱离筒体后被抛落下来,形成瀑落区。
在瀑落区收内层到外层矿块逐渐变。
自磨和半自磨技术的进展
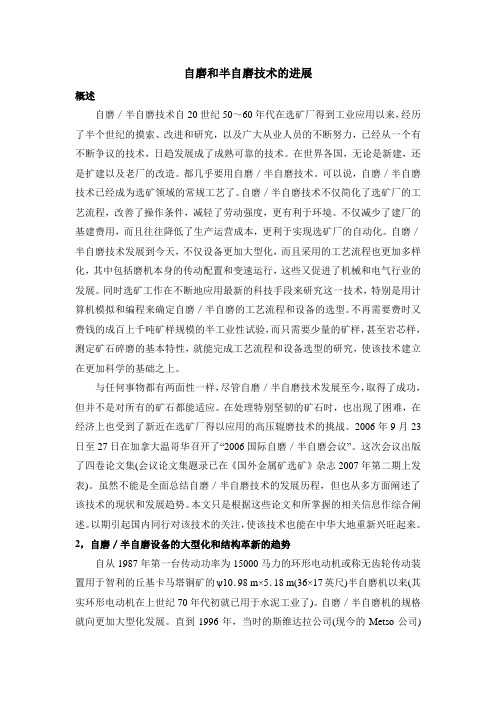
自磨和半自磨技术的进展概述自磨/半自磨技术自20世纪50~60年代在选矿厂得到工业应用以来,经历了半个世纪的摸索、改进和研究,以及广大从业人员的不断努力,已经从一个有不断争议的技术,日趋发展成了成熟可靠的技术。
在世界各国,无论是新建,还是扩建以及老厂的改造。
都几乎要用自磨/半自磨技术。
可以说,自磨/半自磨技术已经成为选矿领域的常规工艺了。
自磨/半自磨技术不仅简化了选矿厂的工艺流程,改善了操作条件,减轻了劳动强度,更有利于环境。
不仅减少了建厂的基建费用,而且往往降低了生产运营成本,更利于实现选矿厂的自动化。
自磨/半自磨技术发展到今天,不仅设备更加大型化,而且采用的工艺流程也更加多样化,其中包括磨机本身的传动配置和变速运行,这些又促进了机械和电气行业的发展。
同时选矿工作在不断地应用最新的科技手段来研究这一技术,特别是用计算机模拟和编程来确定自磨/半自磨的工艺流程和设备的选型。
不再需要费时又费钱的成百上千吨矿样规模的半工业性试验,而只需要少量的矿样,甚至岩芯样,测定矿石碎磨的基本特性,就能完成工艺流程和设备选型的研究,使该技术建立在更加科学的基础之上。
与任何事物都有两面性一样,尽管自磨/半自磨技术发展至今,取得了成功,但并不是对所有的矿石都能适应。
在处理特别坚韧的矿石时,也出现了困难,在经济上也受到了新近在选矿厂得以应用的高压辊磨技术的挑战。
2006年9月23日至27日在加拿大温哥华召开了“2006国际自磨/半自磨会议”。
这次会议出版了四卷论文集(会议论文集题录已在《国外金属矿选矿》杂志2007年第二期上发表)。
虽然不能是全面总结自磨/半自磨技术的发展历程,但也从多方面阐述了该技术的现状和发展趋势。
本文只是根据这些论文和所掌握的相关信息作综合阐述。
以期引起国内同行对该技术的关注,使该技术也能在中华大地重新兴旺起来。
2,自磨/半自磨设备的大型化和结构革新的趋势自从1987年第一台传动功率为15000马力的环形电动机或称无齿轮传动装置用于智利的丘基卡马塔铜矿的ψ10.98 m×5.18 m(36×17英尺)半自磨机以来(其实环形电动机在上世纪70年代初就已用于水泥工业了)。
- 1、下载文档前请自行甄别文档内容的完整性,平台不提供额外的编辑、内容补充、找答案等附加服务。
- 2、"仅部分预览"的文档,不可在线预览部分如存在完整性等问题,可反馈申请退款(可完整预览的文档不适用该条件!)。
- 3、如文档侵犯您的权益,请联系客服反馈,我们会尽快为您处理(人工客服工作时间:9:00-18:30)。
自磨机和半自磨机的尺寸规格及衬板和钢球选择
1、自磨机和半自磨机的尺寸及发展趋势
自磨机和半自磨机刚出现时规格较小。
20世纪70年代中期10.75m(36英尺)自磨机被制造出来,并首先应用于美国希宾铁矿,这是当时最大规格的自磨机。
由于受齿轮传动功率的限制,在此后一段较长时间内自磨机规格没有新的突破。
直至20世纪90年代中期,随着无齿轮传动方式的应用相继制造了Φ11.58m和Φ12.19m(40英尺)的自磨机。
直径为Φ12.20m,电动机动率为20MW,安装于澳大利亚卡地亚山的半自磨机是当今世界上最大的自磨机。
据报道,更大规格的Φ12.80m~Φ13.50m 的半自磨机正在设计中。
国内的公司尤其是中信重工机械股份有限公司,先后自主开发并发展自磨机和半自磨机产业,已形成φ5m、φ5.5m、φ6.0m、φ6.1m、φ6.7m、φ7.0m、φ7.3m、φ7.5m、φ8.0m、φ8.8m、φ9.15m(双传动)、φ9.75m(双传动)、φ10.37m(双传动)、φ12.2m(无齿轮驱动)半自磨机系列。
2、自磨机和半自磨机衬板的选择
2.1衬板材料
磨机衬板的磨损是一个复杂的过程,它包括三方面的材料消磨机理:磨蚀、腐
蚀和冲击。
每一机理的相关作用及材料的总磨损率系受磨矿环境中的一些参数所支配,如矿石磨蚀特性、粒度、矿浆性质和磨矿操作条件以及衬板材料本身的机械与化学性质。
由于每一矿山的矿石类型、磨矿设备和操作条件的综合情况各异,为了寻求最耐磨的磨机衬板材料,均需试验多种可供选择的材料。
一般说来,衬板材料选择都不可能十全十美。
在市场上可购得的材料中,包括金属、合成橡胶和陶瓷材料(单独使用或混合使用),各自的耐磨蚀性、耐腐蚀性和抗冲击性均不相同。
原料费用和衬板加工费用又限制了材料选择的范围。
磨机衬板材料选择时首要考虑的问题是材料应具有在使用过程中避免断裂的足够韧性。
在大型自磨机和半自磨机中,存在着冲击状态,这就完全排除了在直接承受瀑落和泻落负荷的磨机内任何部位使用陶瓷材料作衬里的可能性。
钢和铁是自磨机和半自磨机衬板的最常用材料。
虽然橡胶具备一些良好的特性,特别是韧性。
除极少数例外,对于作为大型自磨机和半自磨机衬板材料来说,橡胶并不是一种经济的选择,虽然它己广泛用作砾磨机的衬板。
据我们的经验,橡胶用作大型自磨机的衬板,其磨损率按单位时间内的体积损失计比马氏体铬钥铁合金材料的磨损率大1一3倍。
为了达到与铬钥铁合金衬板可比的使用寿命,橡胶衬板一般都设计为带有较高的提升板。
此种设计型式不论所用衬板材料如何,均可提高衬板寿命。
一般来说,橡胶衬板的提升板的高度即使增加50一100%仍抵不过Cr一Mo铁合金衬板的良好耐磨性。
此外,橡胶衬板增加的体积减少了磨机内矿石的可用容积,这也就降低了磨机能力。
像胶衬板制造厂家己意识到自磨机和半自磨机用橡胶衬板的上述缺点,从而转向研制橡胶一金属复合衬板。
2.11自磨机衬板材料
自磨机所受到的冲击不如半自磨机那样严重,主要是因为没有钢质磨矿介质,而且容积负荷率一般只为35%左右。
因此,钢和铸铁可广泛地被选作自磨机衬板材料。
但是,这些材料在耐磨蚀性方面和经济效果方面仍有着明显的差别。
除极少数例外,Cr一Mo铁合金作为大型自磨机的衬板材料是最经济的。
由于Cr一Mo铁合金的铬和钥含量较高,制造方法又较复杂,一般来说,其价格高于钢和铸铁,但由于其寿命较长,因而维修停机时间相应减少,故此足可低偿其较高的价格。
表l列出了几个用马氏体Co-Mo铁合金与钢铁做自磨机衬板材料的使用性能对比示例。
表中耐磨性的排列次序及相对差异同处理钥矿石粗磨球机中用作介质
的同类合金的试验结果是基本一致的。
马氏体Cr一Mo合金的耐磨性优于钢铁,主要原因在于其微观结构。
一般来说,铸铁合金的微观结构是10一40%块状碳化物组成的,这是在凝固过程中形成的粗晶初生或共析碳化物。
这些块状碳化物被金属基质所支持,这种基质可能是奥氏体、马氏体、铁素体一碳化物集合体或是这些物质的混合物,随其化学成分及原先的热过程铸模冷却状态、及续后的热处理而异。
虽然总含碳量一般高达3%,但金属基质的含碳量却低得多,通常约为0.5%,因此该基质可认为是一种合金钢。
控制碳化物量及基质微观结构的能力有可能给耐磨性和韧性带来良好影响。
具有马氏体一奥氏体基质微观结构的铁比具有珠光体基质的铁的耐磨性要好得多。
因此通过调节化学成分及热处理方法来避免珠光体的形成是很重要的。
奥氏体含量较低也可能获得较好的耐磨性。
控制奥氏体含量的能力,特别是采用亚相变热处理方法意味着奥氏体含量可以按规定的用途予以优化。
增加脆性碳化物的含量会降低在静负荷和动负荷条例下的抗断裂韧性。
对于碳化物含量高的铁来说,如其碳化物含量与韧度要求一致时,可能具有较好的耐磨性。
通常带有多块断面较小的铸件集合而成的排矿格栅板一般是由珠光体或马氏体Cr一Mo合金制成的。
有些操作工人在使用Cr一Mo合金格栅板时,在磨损到50mm之前,即将其拆除。
此外,不用小断面铸件的所谓“砾石窗”型格子板,
一般是用Cr一Mo合金做成的。
为了降低造价,也用珠光体Cr一MO合金之类的廉价合金制造磨机的最初一组衬板。
在预计新选厂调试中操作条件变化很大时,也可用钢衬板。
钢衬板的冲击韧度较好,例如,当磨机突然发生半“空磨”时,可减少衬板断裂的危险。
试运转期间用低耐磨度的钢衬板还有另一个好处,即可以较快地看出磨损形态,以使今后采用的Cr一Mo合金衬板可在设计上弥补这种磨损形态。
2.12半自磨机衬板材料
在使用直径100一130mm钢球的半自磨机中发生的球与机壳衬板的碰撞使磨机受到严重冲击。
在磨机的高球荷(大于10%)及低充填率(低于20%)操作的条件下,冲击情况尤为严重。
按这样的操作条件,衬板材料的选择一般只限于韧性很好的钢。
合金选择的难度很大,因为从马氏体微观结构中看出,当韧性较好时,就难以达到高耐磨性和高硬度。
令人奇怪的是,12%Mn奥氏体钢同时具有较好的韧度和硬度,但一般认为这种材料不适宜作半自磨机的衬板材料。
原因是12%Mn钢的屈服强度甚低,会产生很大的塑性形变,导致螺栓断裂,并对磨机机壳施加巨大应力。
珠光体Cr一Mo合金现己十分广泛地用作半自磨机衬板材料。
特别是对于必须承受磨球正面冲击的壳体衬板而言,加工良好的珠光Cr一Mo合金具有经得起反复冲击的能力,并且还有相当好的耐磨性能。
珠光体Cr一Mo。
合金用作磨机衬板及其它耐磨部件己有多年历史,所以其铸造加工方法也熟为人知。
马氏体钢的耐磨强度较之珠光体Cr一Mo。
合金高20一40%,用作比机壳衬板所受冲击少些的半自磨机给料端衬板,效果十分良好。
在自磨机和半自磨机问世之时,就出现了衬板的磨损问题,由于当时磨机直径小,自动化程度低,因此对衬板的磨损没有引起重视。
随着磨机规格加大和自动化程度提高,衬板磨损问题已变得越来越突出,因衬板耐磨性差,导致频繁更换衬板,降低了设备运转率,提高了磨矿成本。
目前制造自磨机和半自磨机衬板的主要材质是高锰钢,高锰钢衬板使用中受到的冲击力较小,很难产生高程度的加工硬化,因此耐磨性较低,不能满足生产要求。
并且锰钢衬板寿命短、噪声大、能耗高,严重影响生产和环境。
近20a来,橡胶衬板已在自磨机和半自磨机上取得了广泛的应用。
橡胶衬板主要有以下优点:1)噪音低;2)橡胶衬板较轻,橡胶的比重约是钢铁的1/5,因此减轻了磨机的重量,减轻了更换衬板的劳动强度,降低了维修费用;3)橡
胶衬板的能耗低;4)钢铁衬板的磨损由衬板的硬度和被磨物料的硬度来决定,而橡胶衬板的硬度比被磨物料软得多,其磨损基本与被磨物料的硬度无关,所以当矿石较硬时,采用橡胶衬板合适;5)使用橡胶衬板可降低磨矿成本。
3、半自磨机钢球大小的选择
以某铜矿进口大型半自磨机φ8. 53m×3. 96m为例,按冲击破碎的力度和几率分析,现用φ130mm钢球偏小,改用重量与最大粒度原矿块相等的φ180mm钢球。
处理量增加60%以上,钢球消耗下降40%左右。
提出钢球球径加大到原矿最大粒度即φ240mm钢球,钢球抛落几乎都冲砸在矿块上,其冲击破粉碎效果(破碎比、处理量能耗和物耗),都优于任何破碎机和其他磨机。