机械加工工艺表格
数控加工工艺与编程课程设计加工工艺过程卡片(空白表格)
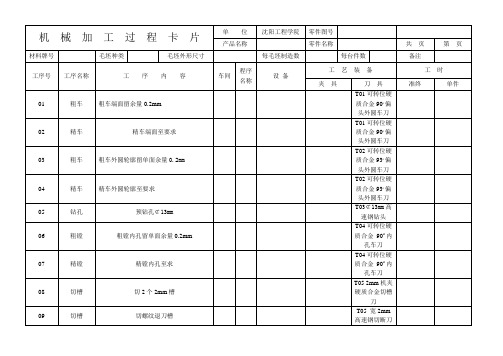
精镗
精镗内孔至求
T04可转位硬质合金90º内孔车刀
08
切槽
切2个2mm槽
T05 2mm机夹硬质合金切槽刀
09
切槽
切螺纹退刀槽
T05宽2mm高速钢切断刀
10
车
车螺纹
T06可转位硬质合金外螺纹刀
11
切断
切断
T07宽4mm高速钢切断刀
设计(日期)
审核(日期)
标准化(日期)
会签(日期)
标记
处数
更改标记
更改文件号
日期
签字
T01可转位硬质合金90º偏头外圆车刀
03
粗车
粗车外圆轮廓留单面余量0.2mm
T02可转位硬质合金93º偏头外圆车刀
04
精车
精车外圆轮廓至要求
T02可转位硬质合金93º偏头外圆车刀
05
钻孔
预钻孔¢13mm
T03¢13mm高速钢钻头
06
粗镗
粗镗内孔留单面余量0.2mm
T04可转位硬质合金90º内孔车刀
机 械 加 工 过 程 卡 片
单 位
沈阳工程学院
零件图号
产品名称
零件名称
共页
第页
材料牌号
毛坯种类
毛坯外形尺寸
每毛坯制造数
每台件数
备注
工序号
工序名称
工 序 内 容
车间
程序
名称
设备
工 艺 装 备
工
粗车
粗车端面留余量0.2mm
T01可转位硬质合金90º偏头外圆车刀
02
精车
精车端面至要求
调速杠杆的机械加工工艺规程及专用夹具设计
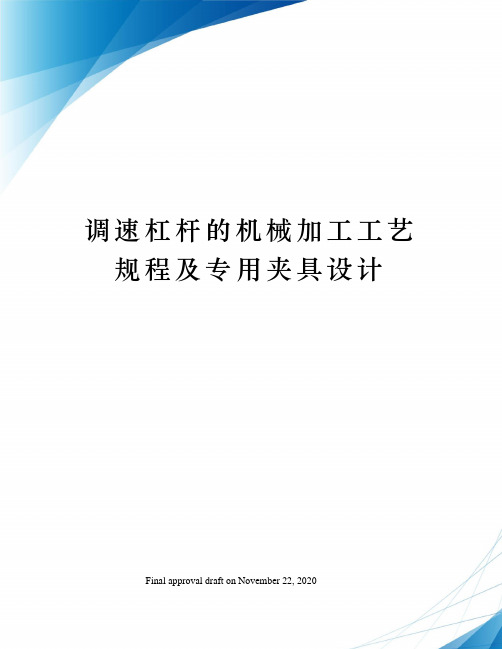
调速杠杆的机械加工工艺规程及专用夹具设计 Final approval draft on November 22, 2020135调速杠杆的机械加工工艺规程及专用夹具设计二〇一一 年 十二 月机制工艺与夹具设计任务书1. 工件零件图(2天)2. 机械加工工艺过程卡(2天)3. 机械加工工序卡(5天)4. 专用夹具装配图(5天)5. 夹具体零件图(3天)6. 专用夹具三维造型(5天)7. 设计说明书(3天)说明书书写注意事项1. 目录页没有页码2. 大的章要另起页3. 参考文献另起页4. 每个图下面要有图标及说明(例如图1-1工件零件图)5. 每个表格上面要有表头及说明(例如表1-1工艺方案比较)目 录第1章 杠杆机械加工工艺规程及夹具设计.................................4 分析零件图..................................................................4 零件的作用 ...............................................................4 零件的工艺分析............................................................4 确定生产类型..................................................................5 确定毛坯类型 ...............................................................6 确定毛坯类型 (6)JIANGSU TEACHERS UNIVERSITY OF TECHNOLOGY机制工艺夹具课程设计与综合训练确定锻件及形状 (6)机械加工工艺过程设计 (7)选择定位基准 (8)拟定工艺过程 (8)选择机床和工艺装备 (8)选择机床 (9)选择夹具 (9)选择刀具 (9)选择量具 (9)确定工序尺寸 (9)确定切削用量和时间定额 (10)工序1切削用量及基本时间的确定 (10)工序2切削用量及基本时间的确定 (12)工序3切削用量及基本时间的确定 (14)工序4切削用量及基本时间的确定 (16)工序5切削用量及基本时间的确 (17)工序6切削用量及基本时间的确定 (17)工序7切削用量及基本时间的确定 (17)工序8切削用量及基本时间的确定 (18)工序9切削用量及基本时间的确定 (20)工序10切削用量及基本时间的确定 (20)工序11切削用量及基本时间的确定 (22)夹具设计有关计算 (24)定位基准的选择 (24)工切削力及夹紧力的计算 (24)工定位误差分析 (25)夹具设计结构设计及操作简要说明 (25)第2章综合训练 (27)夹具造型(小4号黑体) (27)铣夹具立体图 (27)铣夹具三视图…………………………...……………………… .28夹具各零件造型过程简述 (30)夹具体 (30)定位元件 (31)夹紧元件 (34)参考文献 (37)总结………………………………………………………………… .38第1章左摆动杠杆机械加工工艺规程设计分析零件图零件的作用杠杆原理亦称“杠杆平衡条件”。
阀体零件机械加工工艺规程及关键工序夹具设计(机械工艺学课程设计)
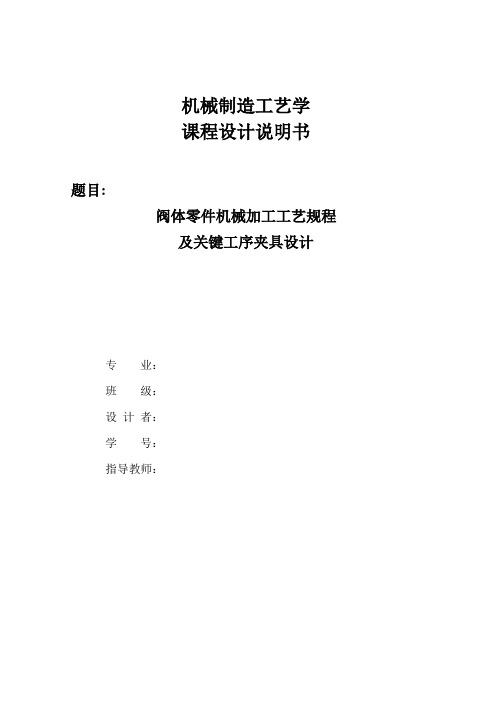
机械制造工艺学课程设计说明书题目:阀体零件机械加工工艺规程及关键工序夹具设计专业:班级:设计者:学号:指导教师:机械制造工艺学课程设计任务书题目:阀体零件机械加工工艺规程及关键工序夹具设计内容:1.零件图1张2.毛坯图1张3.机械加工工艺过程综合卡片张4.机械加工工序卡片张5.夹具结构设计装配图1张6.夹具结构设计零件图张7.课程设计说明书1份专业:班级:设计者:学号:指导教师:目录序言 (4)一、零件的分析 (4)(一)零件的功用、材料和性能 (4)(二)形体分析 (4)二、确定生产类型 (5)三、确定毛坯 (5)(一)选择毛坯 (5)(二)确定机械加工余量、毛坯尺寸和公差 (6)四、工艺规程设计 (6)(一)技术要求分析 (6)(二)零件的加工工艺性分析 (7)(三)选择基面 (7)(四)安排加工工艺路线 (8)(五)确定工序内容 (8)五、夹具设计 (17)(一)机床夹具的组成 (17)(二)机床的分类 (18)(三)工件的装夹方法 (18)(四)工件在夹具中的定位 (19)(五)夹紧装置的组成 (21)(六)阀体零件的钻床专用夹具的总体设计 (24)参考文献 (27)序言机械制造技术基础课程设计是在学完了机械制造技术机车和大部分专业课,并进行了生产实习的基础上进行的又一个实践性教学环节。
这次设计使我们能综合运用机械制造技术基础中的基本理论,并结合生产实习中学到的实践知识,独立地分析和解决了零件机械制造工艺问题,设计了机床专用夹具这一典型的工艺装备,提高了结构设计能力,为今后的毕业设计及未来从事的工作打下了良好的基础。
由于能力所限,经验不足,设计中还有许多不足之处,希望各位老师多加指教。
一、零件的分析(一)零件的功用、材料和性能该阀体是一个管道控制阀,通过一处外螺纹,一处带螺纹孔的方形壁与其他物体连接。
顶部内螺纹是用来安装控制阀门,利用阀门来控制液体的开关以及流量的大小。
阀体的材料是普通碳素结构钢Q235,其屈服值为235。
机械加工工艺手册表2
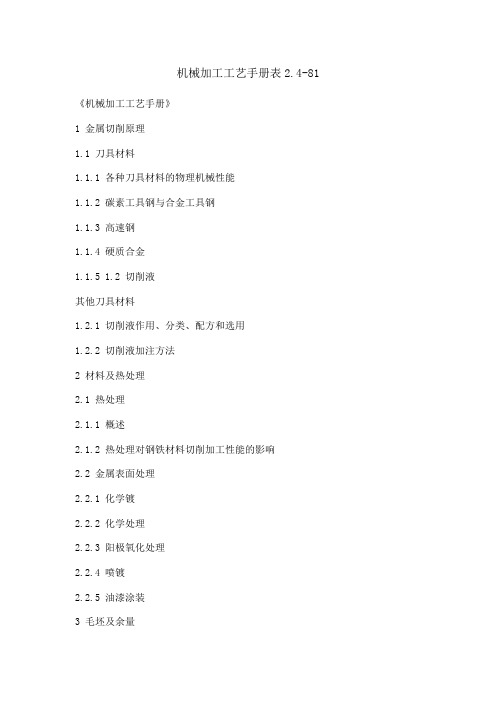
机械加工工艺手册表2.4-81 《机械加工工艺手册》1 金属切削原理1.1 刀具材料1.1.1 各种刀具材料的物理机械性能1.1.2 碳素工具钢与合金工具钢1.1.3 高速钢1.1.4 硬质合金1.1.5 1.2 切削液其他刀具材料1.2.1 切削液作用、分类、配方和选用1.2.2 切削液加注方法2 材料及热处理2.1 热处理2.1.1 概述2.1.2 热处理对钢铁材料切削加工性能的影响2.2 金属表面处理2.2.1 化学镀2.2.2 化学处理2.2.3 阳极氧化处理2.2.4 喷镀2.2.5 油漆涂装3 毛坯及余量3.1 毛坯种类和毛坯余量3.1.1 轧制件3.1.2 铸铁3.1.3 锻件3.1.4 冲压件3.1.5 焊接件3.2 工序间加工余量3.2.1 外圆柱表面加工余量及偏差3.2.2 内孔加工余量及偏差3.2.3 轴端面加工余量及偏差3.2.4 平面加工余量及偏差3.2.5 有色金属及其合金的加工余量3.2.6 切除渗碳层的加工余量3.2.7 齿轮和花键精加工余量4 机械加工质量4.1 机械加工精度4.2 机械加工表面质量4.2.1 已加工表面粗糙度4.2.2 加工硬化5 机械加工工艺规程制定5.1 工艺规程的编制5.2 零件结构的切削加工工艺性5.2.1 工件便于装夹和减少装夹次数5.2.2 减少刀具的调整与走刀次数5.2.3 采用标准刀具,减少刀具种类5.2.4 减少刀具切削空行程5.2.5 避免内凹表面及内表面的加工5.2.6 加工时便于进刀、退刀和测量5.2.7 减少加工表面数和缩小加工表面面积5.2.8 增加刀具的刚度与耐用度5.2.9 保证零件加工时必要的刚度5.2.10 合理地采用组合件和组合表6 车削6.1 车削用量与车削参数计算6.1.1 车床切削用量、车削力与车削功率6.1.2 自动车床的车削用量6.2 卧式车床与立式车床加工7 铣削7.1 铣床7.1.1 铣床主轴联系尺寸与工作台T形槽尺寸7.1.2 铣床附件7.1.3 铣床附加装置7.2 铣刀及其辅具7.2.1 铣刀类型、几何参数与规格7.2.2 硬质合金可转位铣刀与刀片7.2.3 其他铣刀7.2.4 铣刀直径和角度的选择7.2.5 铣刀的安装与铣刀辅具7.3 铣削用量及铣削钢的参数计算7.3.1 铣削进给量的选择7.3.2 确定铣削用量及功率常用表格7.3.3 铣削切削时间的计算7.4 铣削加工工艺7.4.1 分度头的分度计算与分度头应用7.4.2 平面的精铣7.4.3 型面精铣8 钻削8.1 钻床8.1.1 钻床类型、技术参数与联系尺寸8.1.2 立式钻床型号、技术参数与联系尺寸8.1.3 摇臂钻床型号、技术参数与联系尺寸8.1.4 排式钻床型号与技术参数8.1.5 铣端面、打中心孔机床型号与技术参数8.1.6 数控钻床与十字工作台钻床型号与技术参数8.2 刀具及其辅具8.2.1 钻头8.2.2 深孔钻8.2.3 扩孔钻、锪钻(平底、锥面)8.2.4 铰刀8.2.5 孔加工复合刀具8.2.6 辅具8.3 钻、扩、铰孔切削用量及钻削参数计算8.4 钻、扩、铰加工工艺8.4.1 加工方法选择8.4.2 钻、扩、铰加工工艺举例8.5 孔的挤光和滚压9 镗削9.1 镗床9.1.1 镗床类型与技术参数9.1.2 镗床附件9.2 镗刀及其辅具9.2.1 镗刀分类、装夹和调节方式9.2.2 单刃镗刀9.2.3 双刃镗刀9.2.4 刀杆与镗杆9.2.5 系列刀具9.3 镗床的切削用量9.3.1 卧式镗床的镗削用量与加工精度9.3.2 金刚镗床的精密镗削用量9.3.3 坐标镗床的切削用量9.4 镗削加工工艺9.4.1 金刚镗床加工9.4.2 坐标镗床加工10 拉削10.1 拉刀10.1.1常用拉刀设计10.1.2拉刀技术条件10.1.3圆拉刀设计10.1.4常用拉刀结构特点10.1.5挤压推刀10.2 拉削工艺10.2.1拉削切削液及其浇注方法10.2.2拉刀的刃磨工艺和方法11 磨削11.1 磨料与磨具11.1.1各种磨料的主要物理性能11.1.2磨具大致分类11.1.3普通磨料及其选择11.1.4超硬磨料磨具11.1.5涂覆磨具11.2 磨床与磨床夹具11.3 普通磨削11.3.1外圆磨削11.3.2内圆磨削11.3.3平面磨削11.3.4无心磨削11.3.5砂轮平衡与修整11.3.6磨削液11.4 高效与精密磨削11.4.1高速磨削11.4.2高速重负荷磨削11.4.3低粗糙度磨削11.5 超硬磨料磨具磨削11.5.1金刚石砂轮磨削11.5.2立方氮化硼(CBN)砂轮磨削11.5.3超硬磨料砂轮修整11.6 砂带磨削11.6.1砂带磨削11.6.2砂带磨削工艺参数选择11.6.3砂带磨削实例11.7 珩磨11.7.1珩磨油石的选择11.7.2珩磨工艺参数与珩磨液11.7.3特种珩磨工艺11.8 游离磨粒加工11.8.1研磨11.8.2抛光12 精密加工及超精密加工12.1 精密加工和超精密加工的范畴12.2 金刚石刀具的超精密切削12.3 超精密磨料加工12.3.1精密磨削和超精密磨削12.3.2精密和超精密砂带磨削12.3.3精密和超精密研磨12.3.4精密和超精密抛光13 特种加工13.1 概述13.2 电火花穿孔、成形加工13.2.1电火花穿孔、成形加工机床13.2.2电火花加工的工具电极和工作液系统13.3 电火花切割加工13.3.1电火花线切割机床13.3.2常用电火花线切割电源13.3.3若干因素对线切割工艺效果的影响13.4 电化学加工13.4.1电化学加工原理及设备组成13.4.2电解加工13.4.3电化学抛光13.4.4刷镀13.5 超声加工13.6 高能束加工13.6.1激光加工13.6.2电子束加工13.6.3离子束加工13.7 复合加工13.7.1电解-电火花复合加工13.7.2电解磨削与电解研磨13.7.3超声电解复合加工13.8 其他特种加工13.8.1水喷射切割13.8.2磨料喷射加工13.8.3挤压珩磨加工14 螺纹加工14.1 车螺纹14.1.1专用螺纹车床14.1.2螺纹车刀14.1.3工艺参数的选择与计算14.1.4旋风铣削螺纹14.2 丝锥攻螺纹14.2.1普通螺纹丝锥攻螺纹14.2.2螺母丝锥攻螺母螺纹14.2.3锥形丝锥攻锥螺纹14.2.4挤压丝锥挤压螺纹14.3 板牙套螺纹14.3.1板牙及辅具14.3.2圆板牙机动套螺纹的切削速度14.4 螺纹切头切螺纹14.4.1圆梳刀外螺纹切头切螺纹14.4.2径向平梳刀外螺纹切头切螺纹14.4.3切向平梳刀外螺纹切头切螺纹14.4.4径向平梳刀内螺纹切头切螺纹14.5 铣螺纹14.5.1螺纹铣刀14.5.2铣螺纹工艺参数的选择与计算14.6 滚压螺纹14.6.1滚压螺纹对坯件的要求14.6.2滚压工具耐用度14.6.3螺纹滚压头滚压螺纹14.6.4滚丝轮滚压螺纹14.6.5搓丝板滚压螺纹14.7 磨螺纹14.7.1砂轮14.7.2工艺参数的选择与计算14.7.3切削液的选择15 齿轮加工15.1 概述15.2 成形法铣圆柱齿轮15.3 滚齿15.3.1滚刀15.3.2滚齿工艺15.3.3硬齿面滚齿15.4 插齿15.4.1插齿原理15.4.2插齿机15.4.3插齿刀15.4.4插齿工艺15.5 剃齿15.5.1剃齿原理和方法15.5.2剃齿机15.5.3剃齿刀15.5.4剃齿夹具15.5.5剃齿工艺15.5.6小啮合角剃齿15.6 磨齿15.6.1磨齿夹具15.6.2砂轮的选择和修形15.6.3磨齿工艺15.7 珩齿15.7.1珩齿机15.7.2珩齿轮15.7.3珩齿工艺15.8 蜗轮和蜗杆加工15.8.1蜗杆加工15.8.2蜗轮加工15.8.3新型蜗杆副加工15.9 直齿锥齿轮加工15.9.1 成型齿轮铣刀铣齿法15.9.2 刨齿15.9.3 双刀盘滚切法铣齿。
ca6140型卧式车床主轴的加工工艺过程
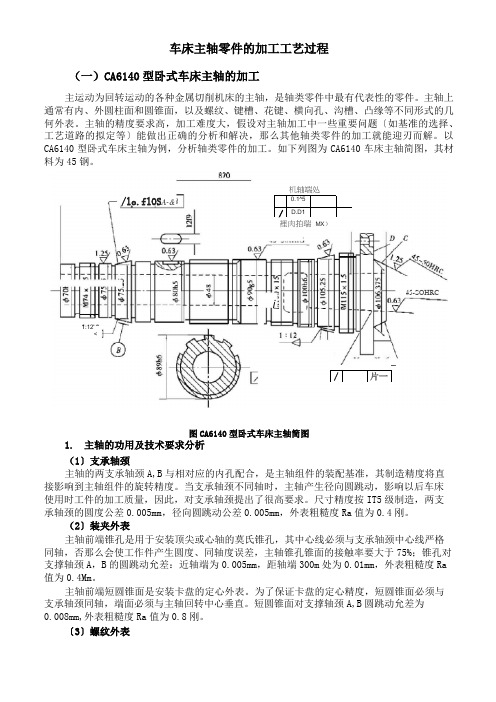
车床主轴零件的加工工艺过程(一)CA6140型卧式车床主轴的加工主运动为回转运动的各种金属切削机床的主轴,是轴类零件中最有代表性的零件。
主轴上通常有内、外圆柱面和圆锥面,以及螺纹、键槽、花键、横向孔、沟槽、凸缘等不同形式的几何外表。
主轴的精度要求高,加工难度大,假设对主轴加工中一些重要问题〔如基准的选择、工艺道路的拟定等〕能做出正确的分析和解决,那么其他轴类零件的加工就能迎刃而解。
以CA6140型卧式车床主轴为例,分析轴类零件的加工。
如下列图为CA6140车床主轴简图,其材料为45钢。
1. 主轴的功用及技术要求分析(1〕支承轴颈主轴的两支承轴颈A,B 与相对应的内孔配合,是主轴组件的装配基准,其制造精度将直接影响到主轴组件的旋转精度。
当支承轴颈不同轴时,主轴产生径向圆跳动,影响以后车床使用时工件的加工质量,因此,对支承轴颈提出了很高要求。
尺寸精度按IT5级制造,两支承轴颈的圆度公差0.005mm ,径向圆跳动公差0.005mm ,外表粗糙度Ra 值为0.4刚。
(2〕装夹外表主轴前端锥孔是用于安装顶尖或心轴的莫氏锥孔,其中心线必须与支承轴颈中心线严格同轴,否那么会使工作件产生圆度、同轴度误差,主轴锥孔锥面的接触率要大于75%;锥孔对支撑轴颈A ,B 的圆跳动允差:近轴端为0.005mm ,距轴端300m 处为0.01mm ,外表粗糙度Ra 值为0.4Mm 。
主轴前端短圆锥面是安装卡盘的定心外表。
为了保证卡盘的定心精度,短圆锥面必须与支承轴颈同轴,端面必须与主轴回转中心垂直。
短圆锥面对支撑轴颈A,B 圆跳动允差为0.008mm,外表粗糙度Ra 值为0.8刚。
〔3〕螺纹外表0.1^5/D.D 1/片一/lo.flOS A-&裡肉拍瑞MX )帖45-SOHRC1:12<i图CA6140型卧式车床主轴简图机轴端处主轴的螺纹外表用于锁紧螺母的配合。
当螺纹外表中心线与支承轴颈中心线歪斜时,会引起主轴组件上锁紧螺母的端面跳动,导致滚动轴承内圈中心线倾斜,引起主轴径向跳动,因此,加工主轴上的螺纹外表时,必须控制其中心线与支承轴颈中心线的同轴度。
机械加工工艺规程制订
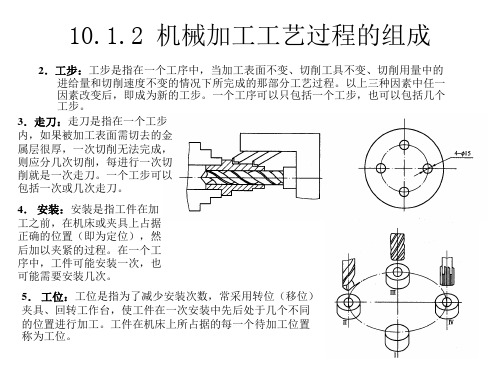
⑴为使加工时工件安装稳定,有些铸件毛坯需要铸 出工艺凸台,如图10-5所示。工艺凸台在零件加工 后一般均应切除。
⑵将几个零件制成一个整体毛坯,加工到一定阶段 后再切割分离。如图10-6所示。
⑶有些表面不要求制出,如孔、槽、凹坑等。
10.3 机械加工工艺路线的拟定
10.3.1 基准及其分类
在机床上加工工件时,必须使工件在机床或夹具上处于某一正确的位置,这一过程称为定位。 工件定位之后一般还需夹紧,以便在承受切削力时仍能保持其正确位置。在零件图样和实际 零件上,总要依据一些指定的点、线、面来确定另一些点、线、面的位置。这些作为依据的 点、线、面就称为基准。根据基准功用的不同,它可以分为设计基准和工艺基准两大类。
应尽量选择加工表面本身作为精 工精度和表面粗糙度来确定。确定应使用的最终加工方
基准,但该表面与其它表面的位 法,由最终加工反推至第一次加工,而形成一个获得该 置精度由前道工序保证,即“自 加工表面的加工方案。表10-10、表10-11、表10-12
为基准”原则。
10.3.4 加工顺序的安排
1.加工阶段的划分 划分加工阶段的作用是: (1)保证加工质量, (2)合理使用设备,(3)便于安排热处理工序, (4)
4. 安装:安装是指工件在加 工之前,在机床或夹具上占据 正确的位置(即为定位),然 后加以夹紧的过程。在一个工 序中,工件可能安装一次,也 可能需要安装几次。
5. 工位:工位是指为了减少安装次数,常采用转位(移位) 夹具、回转工作台,使工件在一次安装中先后处于几个不同 的位置进行加工。工件在机床上所占据的每一个待加工位置 称为工位。
机械加工工艺表格

3
铣
铣六面,厚面留磨削余量0.4mm,侧面留磨削余量0.3mm
X5012
游标卡尺0.02×125mm
φ8端面铣刀
4
磨
磨上下面留磨削余量0.2mm,磨基准侧面
M7012
外径千分尺(25-50)0.02mm
P300×30×75WA60L5V穿丝孔线
内径千分尺)0-20)0.02mm
10
钳工
去毛刺,研磨型孔
11
检验
按图样尺寸检验
游标卡尺0.02×125mm
修改
标记
学生班级
学生姓名
指导教师
完成日期
签名
6
钻铣
在型孔内钻穿丝孔,钻φ5mm孔,攻螺纹,钻销孔,铣型孔
ZX6350A
塞规
φ6,φ5直柄麻花钻
φ5直柄机用铰刀
7
热处理
淬火硬度为58-62HRC
内径千分尺)0-20)0.02mm
φ5球头铣刀
8
电火花
与凸凹模配作加工型孔
D7140
9
磨
磨两端面,保证与型面垂直
M7012
P300×30×75WA60L5V35
四川工程职业技术学院
产品型号
机 械 加 工 工 艺 过 程 卡
零件编号
第页
零件名称
凹模板
共页
材料
名称
型号及规格
毛坯种类
毛坯尺寸
毛重(kg)
Cr12
净重(kg)
序号
工序名称
工序内容
设备
工艺装备名称与编号
工时定额(小时)
夹具
量具
刃具
辅具
准备
操作
单件
工艺表格模板
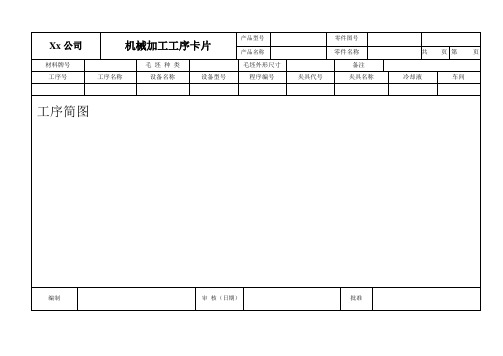
产品型号 产品名称 毛坯外形尺寸 车 间 工 设 段 备
零件图号 零件名称 每毛坯件数 每 台 件 数 共 页 第 备 注 工 工 艺 装 备 准终 单件 时 页
设 计(日 期)
校 对(日期)
审 核(日期) 标准化(日期)
会 签(日期)
标记 处数 更改文件号 签
字 日
期 标记 处数 更改文件号 签
字
批准
Xx 公司
材料牌号 工序号 工序名称
机械加工工序卡片
毛 坯 种 类 设备名称 设备型号
产品型号 产品名称
零件图号
零件名称 备注 夹具代号 夹具名称
共
页 第
页
毛坯外形尺寸 程序பைடு நூலகம்号
冷却液
车间
工序简图
编制
审 核(日期)
批准
机械加工工艺过程卡片
材 料 牌 号 工 序 号 序 称 工 名 工 序 内 容 毛 坯 种 类
日
期
机械加工工序卡片
产品型号 产品名称
零件图号
零件名称
共
页 第
页
材料牌号 工序号 工序名称
毛 坯 种 类 设备名称 设备型号
毛坯外形尺寸 程序编号 夹具代号
备注 夹具名称 冷却液 车间
工步号
工
步
内
容
刀具号
刀具
量具及检具
主轴转速 r/min
切削速度 m/min
进给量 mm/r
背吃刀量 mm
备注
编制
审 核(日期)
- 1、下载文档前请自行甄别文档内容的完整性,平台不提供额外的编辑、内容补充、找答案等附加服务。
- 2、"仅部分预览"的文档,不可在线预览部分如存在完整性等问题,可反馈申请退款(可完整预览的文档不适用该条件!)。
- 3、如文档侵犯您的权益,请联系客服反馈,我们会尽快为您处理(人工客服工作时间:9:00-18:30)。
产品型号
机械加工工艺过程卡
零件编号
第页
零件名称
凹模板
共页
材料
名称
型号及规格
毛坯种类
毛坯尺寸
毛重(kg)
Cr12
净重(kg)
序号
工序名称
工序内容
设备
工艺装备名称与编号
工时定额(小时)
夹具
量具
刃具
辅具
准备
操作
单件
1
备料
按尺寸85mm×65mm×15mm锻造毛柸
2
热处理
退火
3
铣
铣六面,厚面留磨削余量0.4mm,侧面留磨削余量0.3mm
修改
标记
学生班级
学生姓名
指导教师
完成日期
签名
X5012
游标卡尺0.02×125mm
φ8端面铣刀
4
磨
磨上下面留磨削余量0.2mm,磨基准侧面
M7012
外径千分尺(25-50)0.02mm
P300×30×75WA60L5V35
5
划线
划型孔线,穿丝孔线
内径千分尺)0-20)0.02mm
6
钻铣
在型孔内钻穿丝孔,钻φ5mm孔,攻螺纹,钻销孔,铣型孔
ZX6350A
塞规
φ6,φ5直柄麻花钻
φ5直柄机用铰刀
7
热处理
淬火硬度为58-62HRC
内径千分尺)0-20)0.02mm
φ5球头铣刀
8
电火花
与凸凹模配作加工型孔
D7140
9
磨
磨两端面,保证与型面垂直
M7012
P300×30×75WA60L5V35
10钳工去毛刺,研来自型孔11检验按图样尺寸检验
游标卡尺0.02×125mm