物理气相沉积技术优秀课件
合集下载
物理气相沉积PPT课件
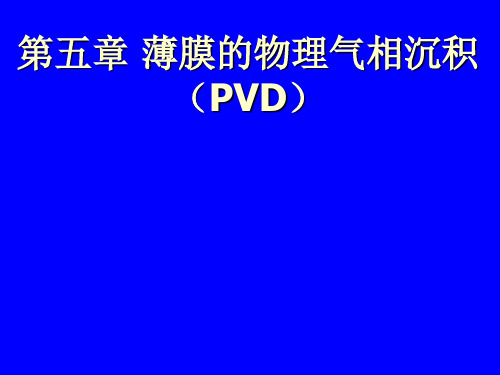
成膜机理? 真空蒸发所得到的薄膜,一般都是多晶膜或无定 形膜,经历成核和成膜两个过程。蒸发的原子(或分子)碰撞 到基片时,或是永久附着在基片上,或是吸附后再蒸发而离开 基片,其中有一部分直接从基片表面反射回去。粘附在基片表 面的原子(或分子)由于热运动可沿表面移动,如碰上其它原 子便积聚成团。这种团最易于发生在基片表面应力高的地方, 或在晶体衬底的解理阶梯上,因为这使吸附原子的自由能最小。 这就是成核过程。进一步的原子(分子)淀积使上述岛状的团 (晶核)不断扩大,直至展延成连续的薄膜。
Stranski-Krastanov Mode
Layer Plus Island Growth
衬底
( 2D-3D )
PVD所需实验条件
►高真空 (HV) ►高纯材料 ►清洁和光滑的衬底表面 ►提供能量的电源
PVD的通用实验配置
衬底
真空室 反应气体管道
充气管道
Plume
厚度监控仪 靶材
真空泵
一、蒸发镀膜
提高薄膜纯度的方法: –降低残余气体分压,提高真空度; –提高基片温度,提高沉积速率;
二、溅射镀膜
溅射镀膜是利用电场对辉光放电过程中产生出来的带电离子进行加速,使其获得一 定的动能后,轰击靶电极,将靶电极的原子溅射出来,沉积到衬底形成薄膜的方法。
辉光放电
溅射沉积薄膜原理
Al膜
阳
避免金属 真空 原子氧化
7、薄膜的纯度:
蒸发源纯度的影响: 加热器、坩埚、支撑材料等的污染: 残余气体的影响:
Substrate
残留气体在衬底上形成一单原子层所需时间
生长材料的分子 残留气体分子
Pressure (Torr) 10-4 10-5 10-6 10-7 10-8 10-9 10-10 10-11
10气相沉积技术PPT课件

可推导出特殊情况下的理想气体定律:
波义尔定律: PV=C (m、T不变)
盖.吕萨克定律: V=CT (m、P不变)
常用薄膜性质
58.8 670 58.3 660 56.8 630 56.3 620 55.2 600 54.7 590
50.5 520 49.8 510
SOH58 SOH56 SUS420J2
SUS3
材料 TiN TiCN ZrN HfN CrN TiAlN
硬 度(HV) 色 彩
空热处理和真空脱水 高真空:10-1-10-6Pa,分子间碰撞基本不发生;镀膜工作压强 超高真空:10-6-10-10Pa,分子间碰撞极少;纯净的气体和固体表面 极高真空:<10-10Pa,分子间不发生碰撞;科学研究用
2021
19
2、稀薄气体的基本性质
稀薄气体:与理想气体差异很小,可直接应用理想气体的状态方程。
11
真空在薄膜技术中的作用: 减少杂质 减少散射 有利于蒸发等进行
2021
12
1、 真空的基本知识
真空: 低于一个大气压的气体空间(气体状态)。
1643年,意大利物理学家托里拆利(E.Torricelli)首创著名的大 气压实验,获得真空。
自然真空:气压随海拔高度增加而减小,存在于宇宙空间。
2021
14
真空是相对的,绝对的真空是不存在的。
n=7.2×1022P/T (个/cm3)
太阳系: n=102个/m3 恒星空间: n=101个/m3
(温度:0-107K)
2021
15
真空度的度量: 压强、气体分子密度、气体分子的平均自由程、形成一个分子层
所需的时间等。
真空度和压强: 压强越低意味着单位体积中气体分子数愈少,真空度愈高;反之
表面处理第十二讲气相沉积(共16张PPT)
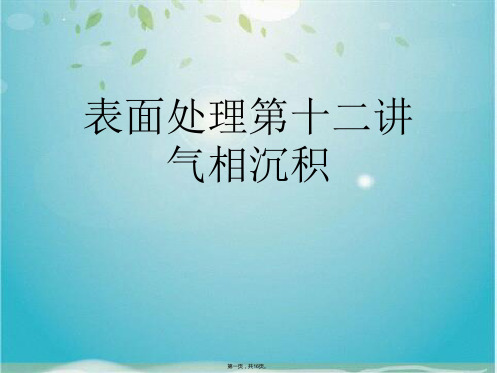
4、CVD装置及工艺应用:
)成膜机理 表面温度(低利于凝聚成膜,但结合力不高。
2 3)影响蒸镀过程的状态与参数:
二、化学气相沉积(CVD) 二、化学气相沉积(CVD) (1)真空度:一般为10-2~10-4Pa; 二、化学气相沉积(CVD) 表面处理第十二讲气相沉积 概念:在真空条件下,以各种物理方法产生的原子或分子沉积在基材上,形成薄膜或涂层的过程。 一、物理气相沉积(PVD) (2)高频感应加热蒸发源:(3)电子束蒸发源: 2)反应物供给及配比:要选择常温下是气态的物质或具有高蒸气压的液体或固体。 由于溅射沉积到基材表面的粒子能量比蒸发时高50倍,对基材表面有清洗和升温作用,所以镀膜附着力较大。 二、化学气相沉积(CVD) 缺点是需要在较高温度下反应,基材温度高,沉积速率较低(每小时几微米到几百微米),基材难以进行局部沉积,参加沉积反应的气源和反应 后的余气有一定的毒性。 基材表面晶体结构(单晶体则镀膜也长成单晶体); 氩离子高速轰击基材并溅射清洗活化其表面,然后接通交流电,加热蒸发蒸发源中的膜料,蒸发出的粒子通过辉光放电的等离子区时部分被电离 ,成为正离子,高速打在基材表面。 (2)高频感应加热蒸发源:(3)电子束蒸发源: 把待镀膜材料置于高真空室内,通过加热使蒸发材料汽化(或升华),以原子、分子或原子团离开熔体表面,凝聚在具有一定温度的基材或工件 表面,并冷凝成薄膜的过程。 1、概念:把一种或几种含有构成薄膜元素的单质气体或化合物通入放置有基材的反应室,借助气相作用或在基材上的化学反应生成所希望的薄膜 。
3、应用:在电子、机械等工业领域有广泛应用,特别用于 氧化物、碳化物、金刚石和类金刚石等功能薄膜和超硬薄 膜的沉积。分常压和低压(数百至数十Pa)CVD。后者镀
膜均匀性好,针孔较少,反应气体利用率高。
)成膜机理 表面温度(低利于凝聚成膜,但结合力不高。
2 3)影响蒸镀过程的状态与参数:
二、化学气相沉积(CVD) 二、化学气相沉积(CVD) (1)真空度:一般为10-2~10-4Pa; 二、化学气相沉积(CVD) 表面处理第十二讲气相沉积 概念:在真空条件下,以各种物理方法产生的原子或分子沉积在基材上,形成薄膜或涂层的过程。 一、物理气相沉积(PVD) (2)高频感应加热蒸发源:(3)电子束蒸发源: 2)反应物供给及配比:要选择常温下是气态的物质或具有高蒸气压的液体或固体。 由于溅射沉积到基材表面的粒子能量比蒸发时高50倍,对基材表面有清洗和升温作用,所以镀膜附着力较大。 二、化学气相沉积(CVD) 缺点是需要在较高温度下反应,基材温度高,沉积速率较低(每小时几微米到几百微米),基材难以进行局部沉积,参加沉积反应的气源和反应 后的余气有一定的毒性。 基材表面晶体结构(单晶体则镀膜也长成单晶体); 氩离子高速轰击基材并溅射清洗活化其表面,然后接通交流电,加热蒸发蒸发源中的膜料,蒸发出的粒子通过辉光放电的等离子区时部分被电离 ,成为正离子,高速打在基材表面。 (2)高频感应加热蒸发源:(3)电子束蒸发源: 把待镀膜材料置于高真空室内,通过加热使蒸发材料汽化(或升华),以原子、分子或原子团离开熔体表面,凝聚在具有一定温度的基材或工件 表面,并冷凝成薄膜的过程。 1、概念:把一种或几种含有构成薄膜元素的单质气体或化合物通入放置有基材的反应室,借助气相作用或在基材上的化学反应生成所希望的薄膜 。
3、应用:在电子、机械等工业领域有广泛应用,特别用于 氧化物、碳化物、金刚石和类金刚石等功能薄膜和超硬薄 膜的沉积。分常压和低压(数百至数十Pa)CVD。后者镀
膜均匀性好,针孔较少,反应气体利用率高。
第七章气相沉积技术ppt课件
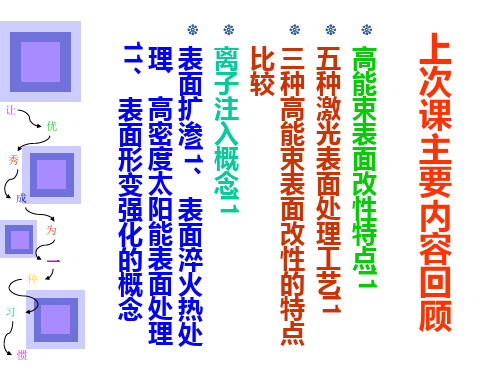
让 优
秀
成 为
一
种 习
惯
定义:等离子体是指存在的时间和
空间均超过某一临界值的电离气体
产生途径——宇宙、天体、上层气
体、放射线及同位素、X射线、粒子 加速器、反应堆、场致电离、冲击波、 燃烧、激光、真空紫外光、发电等, 在气相沉积中广泛采用的是气体放电 产生等离子体。
等离子体特征
让 优
秀
成 为
一
种
惯
离子镀膜的应用
让 优
秀
成 为
一
种 习
惯
①首先,离子镀是各种刀具的保护神。可 以在各种齿轮、模具或刀具上离子镀氮化 钛、碳化钛、氮碳化钛、碳化钨、氮化锆 等多种硬质膜。 ②其次,离子镀技术还是美化人民生活的 得力工具。从我们手上带的手表表壳、表 带,到手机外壳,鼻梁上的眼镜,再到我 们衣服上的扣子、领带夹,腰上别的钥匙 扣、链子及腰带头。这些都是离子镀的杰 作。颜色也是多种多样。 ③离子镀膜还广泛应用于耐腐蚀、耐热、 润滑及电子工业的集成电路等中。
让 优
秀
成 为
一
种 习
惯
化学气相沉积
什么东西最硬?(钻石、铬钴) 沉积原理?
外延
让 优
秀
成 为
一
种
习
外延的概念:外延是指在单晶基片上生长出位向 相同的同类单晶体(同质外延),或者生长出具 有共格或半共格联系的异类单晶体(异质外延)。
外延分为——气相外延、液相外延和分子束外延
气相外延就是化学气相沉积在单晶表面的沉积过 程。
有基体支撑:依附于固体表面并得到 其支撑而存在,并具有与支撑固体不 同结构和性能的二维材料
手机贴膜
手机贴膜
塑料膜
让 优
物理气相沉积(PVD)PPT课件.

§8.2 物理汽相沉积(PVD)
物理气相沉积
—— Physical Vapor Deposition 缩写为: PVD; 通常用于沉积薄膜和涂层 沉积膜层厚度:10-1nm~mm; 一类应用极为广泛的成膜技术,从装饰涂层到 各种功能薄膜,涉及化工、核工程、微电子以 及它们的相关工业工程。 包括 蒸发沉积(蒸镀)、溅射沉积(溅射) 和离子镀等。
改进工艺:
1)选择基片温度,使之有利于凝聚而不是分凝; 2)选用几个蒸发源,不同温度下分别淀积,但控制困难;
3)氧化物,可采用反应蒸镀法,引入活性气体。
4. 蒸发源类型
(1)电阻加热蒸发源
选择原则:在所需蒸发温度下不软化,饱和蒸气压小,不发生反应; 一般采用高熔点金属如钨、钽、钼等材质,常作成螺旋丝状或箔舟状,如图 8.2.4所示。 特点:结构简单,造价低,使用广泛;存在污染,也不能蒸镀高Tm材料。
电子束加热蒸发源由: 阴极、加速电极、阳极 (膜料)组成。 还有高频加热蒸发源、 激光蒸发源等。
图8.2.5 电子束加热蒸发源
优点:
(1)可以直接对蒸发材料加热;
(2)装蒸发料的容器可以是冷的或者用水冷却,从而 可避免 材料与容器的反应和容器材料的蒸发;
( 3 ) 可 蒸 发 高 熔 点 材 料 , 例 如 : 钨 ( Tm=3380℃ ) 、 钼 (Tm=2610℃)和钽(Tm=3000℃)等耐热金属材料。
(2)封闭体系内的P—T关系:
Lv dP dT TV
(1)
∵
V V汽 V固、 液
1 V汽 RT, P
∴
积分:
dP PLV dT RT 2
LV 1 ln p A R T
(2)
物理气相沉积
—— Physical Vapor Deposition 缩写为: PVD; 通常用于沉积薄膜和涂层 沉积膜层厚度:10-1nm~mm; 一类应用极为广泛的成膜技术,从装饰涂层到 各种功能薄膜,涉及化工、核工程、微电子以 及它们的相关工业工程。 包括 蒸发沉积(蒸镀)、溅射沉积(溅射) 和离子镀等。
改进工艺:
1)选择基片温度,使之有利于凝聚而不是分凝; 2)选用几个蒸发源,不同温度下分别淀积,但控制困难;
3)氧化物,可采用反应蒸镀法,引入活性气体。
4. 蒸发源类型
(1)电阻加热蒸发源
选择原则:在所需蒸发温度下不软化,饱和蒸气压小,不发生反应; 一般采用高熔点金属如钨、钽、钼等材质,常作成螺旋丝状或箔舟状,如图 8.2.4所示。 特点:结构简单,造价低,使用广泛;存在污染,也不能蒸镀高Tm材料。
电子束加热蒸发源由: 阴极、加速电极、阳极 (膜料)组成。 还有高频加热蒸发源、 激光蒸发源等。
图8.2.5 电子束加热蒸发源
优点:
(1)可以直接对蒸发材料加热;
(2)装蒸发料的容器可以是冷的或者用水冷却,从而 可避免 材料与容器的反应和容器材料的蒸发;
( 3 ) 可 蒸 发 高 熔 点 材 料 , 例 如 : 钨 ( Tm=3380℃ ) 、 钼 (Tm=2610℃)和钽(Tm=3000℃)等耐热金属材料。
(2)封闭体系内的P—T关系:
Lv dP dT TV
(1)
∵
V V汽 V固、 液
1 V汽 RT, P
∴
积分:
dP PLV dT RT 2
LV 1 ln p A R T
(2)
第七章 气相沉积技术精品PPT课件

目前 CVD能够制备的硬质膜种类达几十种,并能制 备三层以上的多层膜和梯度膜。
2020/10/13
12
80 年 代 气 相 沉 积 发 展 的 主 要 特 征 是 PVD 沉 积技术进一步完善并扩大应用范围。 等离子激活气相化学沉积(PCVD)技术的 产生,基础研究开始起步并日益受到重视。 1978年,Hazle,Wood和Iondnis首次报道 了用PVCD沉积TiC,发现沉积温度可降至 500℃。
然而,沉积理论落后于沉积技术的现象已在很 大程度上影响了此项技术的进一步发展,例如 镀层质量的测试及评定方法;膜基体系和膜基 间的相互关系的研究;
这些研究将为新材料新工艺转化为生产力提供 有效的基本数据,为进一步发展新材料奠定理 论基础。
2020/10/13
3
气相沉积发展史
气相沉积硬质镀层的发展可追溯到上上个世 纪 末 , 德 国 的 Erlwein等 利 用 化 学 气 相 沉 积 (简称CVD),在氢气的参与下,用挥发性 的金属化合物与碳氢化合物反应,在白炽灯 丝上形成TiC。
2020/10/13
8
在1963年D.M.Mattox已提出了离子镀 技术,并于 1967年取得了美国专利。
时隔两年,美国的IBM公司研制出射频溅 射法。这两种技术与蒸镀构成了PVD的 三大系列。
2020/10/13
9
进人70年代,PVD技术的崛起与CVD技术的提高, 使得表面镀层技术进人了全面的发展阶段。 1972年美国加州大学Bunshan发明了活性反应蒸 镀技术。 1973年前苏联又推出了多弧离子镀;与此同时, 日本的村山洋一发明了射频离子镀。一年之后。 日本的小宫泽治将空心阴极放电技术用于离子镀 形成了目前广泛应用的空心阴极离子镀。
气相沉积PPT课件

蒸镀的膜层其残余应力为拉应力,而离子轰击产生压应力,可以抵消一 部分拉应力。离子轰击可以提高镀料原子在膜层表面的迁移率,这 有利于获得致密的膜层。
如果离子能量过高会使基片温度升高,使镀料原子向基片内部扩散,这 时获得的就不再是膜层而是渗层,离子镀就转化为离子渗镀了。离 子渗镀的离子能量为1000eV左右。
射频溅射:
射频溅射的两个电极,接在交变的射频电源上, ,一个周期内 ,每个电极交替称为阴极和阳极,正离子和电子交替轰击靶 子。
在射频电源交变电场作用下,气体中的电子随之发生振荡,并 使气体电离为等离子体。另一电极对于等离子体处于负电位 ,是阴极,受到离子轰击,用于装置靶材。
缺点:是大功率的射频电源不仅价高,对于人身防护也成问题 。因此,射频溅射不适于工业生产应用。
磁控溅射 :
磁控溅射是70年代迅速发展起来的新型溅射技术,目前 已在工业生产中实际应用。
磁控溅射的镀膜速率与二极溅射相比提高了一个数量级 ,它具有高速、低温、低损伤等优点:
高速是指沉积速率快; 低温和低损伤是指基片的温升低、对膜层的损伤小。
磁控溅射原理:
在阴极靶面上建立一个平行的磁场,使靶放 出的高速电子转向,从而减小了电子冲 击基板发热的影响,在133Pa的低压下, 基本温度在100℃就可成膜。
多弧离子镀
多弧离子镀是采用电弧放电的方法,在 固体的阴极靶材上直接蒸发金属, 电流可达 105-107A/cm2,使金属蒸 发并由于电弧放电中电子的冲击使 蒸发到弧柱的金属电离成等离子状 态,并在负压的基体上沉积。
化合物膜的镀制可选用化合物靶溅射和反应溅射。许多化合物 是导电材料,其电导率有的甚至与金属材料相当,这时可以 采用化合物靶进行直流溅射。对于绝缘材料化合物,则只能 采用射频溅射。
如果离子能量过高会使基片温度升高,使镀料原子向基片内部扩散,这 时获得的就不再是膜层而是渗层,离子镀就转化为离子渗镀了。离 子渗镀的离子能量为1000eV左右。
射频溅射:
射频溅射的两个电极,接在交变的射频电源上, ,一个周期内 ,每个电极交替称为阴极和阳极,正离子和电子交替轰击靶 子。
在射频电源交变电场作用下,气体中的电子随之发生振荡,并 使气体电离为等离子体。另一电极对于等离子体处于负电位 ,是阴极,受到离子轰击,用于装置靶材。
缺点:是大功率的射频电源不仅价高,对于人身防护也成问题 。因此,射频溅射不适于工业生产应用。
磁控溅射 :
磁控溅射是70年代迅速发展起来的新型溅射技术,目前 已在工业生产中实际应用。
磁控溅射的镀膜速率与二极溅射相比提高了一个数量级 ,它具有高速、低温、低损伤等优点:
高速是指沉积速率快; 低温和低损伤是指基片的温升低、对膜层的损伤小。
磁控溅射原理:
在阴极靶面上建立一个平行的磁场,使靶放 出的高速电子转向,从而减小了电子冲 击基板发热的影响,在133Pa的低压下, 基本温度在100℃就可成膜。
多弧离子镀
多弧离子镀是采用电弧放电的方法,在 固体的阴极靶材上直接蒸发金属, 电流可达 105-107A/cm2,使金属蒸 发并由于电弧放电中电子的冲击使 蒸发到弧柱的金属电离成等离子状 态,并在负压的基体上沉积。
化合物膜的镀制可选用化合物靶溅射和反应溅射。许多化合物 是导电材料,其电导率有的甚至与金属材料相当,这时可以 采用化合物靶进行直流溅射。对于绝缘材料化合物,则只能 采用射频溅射。
第8章 气相沉积PPT课件

Co-Cr-Al系合金
Co-Cr-Al-Y系合金
机材料、航空航天器件
耐蚀 润滑 装饰
Al,Zn,Cd,Ta,Ti
Au,Ag,Pb,Cu-Au, Pb-Sn,MoS2
Au,Ag,Ti,Al,TiN, TiC
普通钢、结构钢、不锈钢
飞机、船舶、汽车、管材、 一般结构件
高温合金、轴承钢
喷气发动机轴承、航空航 天及高温旋转器件
12.11.2020
29
二极溅射装置
12.11.2020
四极溅射装置
30
磁控溅射
12.11.2020
31
3、阴极溅射的特点
与真空蒸镀法相比,特点: ① 结合力高; ② 容易得到高熔点物质的膜; ③ 可以在较大面积上得到均一的薄膜; ④ 容易控制膜的组成; ⑤ 可以长时间地连续运转; ⑥ 有良好的再现性; ⑦ 几乎可制造一切物质的薄膜。
12.11.2020
12
不足:真空蒸镀时,蒸发粒子动能为0.1~1.0EV, 膜对基体的附着力较弱。
改进结合力措施:
① 在基板背面设置一个加热器,加热基板,使基 板保持适当的温度,既净化基板,又使膜和基体 之间形成一薄的扩散层,增大附着力;
② 对于蒸镀像Au这样附着力弱的金属,可以先 蒸镀像Cr、Al等结合力高的薄膜作底层。
12.11.2020
电子束加热蒸镀
17
(3)高频感应加热
原理:在高频感应线圈中放入氧化铝和石 墨坩埚,蒸镀的材料置于坩锅中,通过高 频交流电使材料感应加热而蒸发。
特点:得到的膜层纯净而且不受带电粒子 的损害。
应用:主要用于铝的大量蒸发。
12.11.2020
18
(4)激光蒸镀法
- 1、下载文档前请自行甄别文档内容的完整性,平台不提供额外的编辑、内容补充、找答案等附加服务。
- 2、"仅部分预览"的文档,不可在线预览部分如存在完整性等问题,可反馈申请退款(可完整预览的文档不适用该条件!)。
- 3、如文档侵犯您的权益,请联系客服反馈,我们会尽快为您处理(人工客服工作时间:9:00-18:30)。
与化学气相沉积(CVD)工艺相比,PVD工艺处理温度低,在600℃以 下时对材料的抗弯强度无影响;薄膜内部应力状态为压应力,更适于 对硬质合金精密复杂刀具的涂层;PVD工艺对环境无不利影响,符合 现代绿色制造的发展方向。
PVD特点 PVD现状与发展
PVD原理
PVD分类 PVD应用
对高速钢刀具进行涂覆, 可得到致密等轴涂层, 具有优异 的耐磨特性, 可显著提高刀具的使用寿命;
其它生长模式
Frank-van der Merve Mode
衬底
Layer by Layer ( 2D )
Stranski-Krastanov Mode
Layer Plus Island Growth
衬底( 2D-3D ) 5可以在较低温度下获得各种功能薄膜, 基材范围广泛。
6
可方便的控制 多个工艺参数 ,易获得单晶 、多晶、非晶 、多层纳米层 结构的功能薄 膜。
无有害气体排出 ,属于无污染技 术。
7
PVD特点
PVD特点 PVD现状与发展
PVD原理
PVD分类 PVD应用
物理气相沉积(PVD )
真空蒸镀 离子镀
电子束蒸发 热蒸发
• 周期结构多层膜
B A B A
Substrate
PVD特点 PVD现状与发展
PVD原理
PVD分类 PVD应用
1
沉积层材料来自固体物质源,采用各种加 热源或溅射源使固态物质变为原子态。
2
物理气相沉积获 得的沉积层薄。
3
涂层组织细密、与基 体和结合强度好。
涂层的纯度高
4 单击此处添加标题
PVD特点
气态
基底 薄膜
以气态方式进行 物质输运 能量输运
能量
块状材料 (靶材)
“物理气相沉积” 通常有下面三个工艺步骤:
1. 所生长的材料(靶材)以物理的方式由固体转化 为气体
2. 生长材料的蒸汽经过一个低压区域到达衬底
3. 蒸汽在衬底表面上凝结,形成薄膜
几种常见的薄膜结构
• 单层膜
A Substrate
在飞机和宇宙飞船的各种形状复杂的零部件上, 可镀制各 种薄膜;
为选择传播射线, 在建筑玻璃上镀制化合物镀层;
为减少摩擦, 在各种工程机械零件上镀制润滑的膜层;
太阳能和光电元件应用的各种薄膜…
ONLY ON THE FILM?
Volmer-Weber Mode
衬底
Island Growth ( 3D )
PVD特点 PVD现状与发展
PVD原理
PVD分类 PVD应用
FROM 1970s
PVD 技术出现于二十世纪七十年代末,制备的薄膜具有高硬度、低摩 擦系数、很好的耐磨性和化学稳定性等优点。近年来,由于PVD技术 和工艺、设备水平的发展,加上使用靶材品种和质量的增加,有效提 高了涂层和基体的结合强度,扩大了涂层材料的种类,是过去难于使 用PVD技术沉积的碳化物、氮化物、氧化物等硬质涂层,现在变成了 可能,极大地扩展了PVD技术的应用范围。
特点:多用于要求纯度极 高的膜、绝缘物的蒸镀和 高熔点物质的蒸镀。
Substrat e fixture
E-Gun Crucible
磁控溅射:使电子的路径不再是直线,而是螺旋线,
增加了与气体原子发生碰撞的几率,在同样的电压和气压 下可以提高气体电离的效率,提高了沉积速率。
附加磁场的优点
• 限制溅射离子的轨道 • 增加离子在气体中停留的时间 • 增强等离子体和电离过程 • 减少溅射原子从靶材到衬底路程中的碰撞 • 高磁场附近的产值比较高
溅射镀
直流溅射 射频溅射 磁控溅射
电子束蒸发镀膜仪 PVD 75 美国 Kurt J Lesker Company
磁控溅射镀膜仪 PVD 75 美国 Kurt J Lesker Company
电子束蒸发原理与特点
原理:热电子由灯丝发射 后,被加速阳极加速,获 得动能轰击到处于阳极的 蒸发材料上,使蒸发材料 加热气化,而实现蒸发镀 膜。
物理气相沉积技术优秀课件
PVD特点
PVD现状与发展
PVD原理
PVD分类 PVD应用
原理:物理气相沉积技术表示在真空条件下 ,采用物理方法,将材料源—固体或液体表 面气化成气态原子、分子或部分电离成离子 ,并通过低压气体(或等离子体)过程,在基 体表面沉积具有某种特殊功能的薄膜的技术
。
PVD的物理原理示意图
PVD特点 PVD现状与发展
PVD原理
PVD分类 PVD应用
对高速钢刀具进行涂覆, 可得到致密等轴涂层, 具有优异 的耐磨特性, 可显著提高刀具的使用寿命;
其它生长模式
Frank-van der Merve Mode
衬底
Layer by Layer ( 2D )
Stranski-Krastanov Mode
Layer Plus Island Growth
衬底( 2D-3D ) 5可以在较低温度下获得各种功能薄膜, 基材范围广泛。
6
可方便的控制 多个工艺参数 ,易获得单晶 、多晶、非晶 、多层纳米层 结构的功能薄 膜。
无有害气体排出 ,属于无污染技 术。
7
PVD特点
PVD特点 PVD现状与发展
PVD原理
PVD分类 PVD应用
物理气相沉积(PVD )
真空蒸镀 离子镀
电子束蒸发 热蒸发
• 周期结构多层膜
B A B A
Substrate
PVD特点 PVD现状与发展
PVD原理
PVD分类 PVD应用
1
沉积层材料来自固体物质源,采用各种加 热源或溅射源使固态物质变为原子态。
2
物理气相沉积获 得的沉积层薄。
3
涂层组织细密、与基 体和结合强度好。
涂层的纯度高
4 单击此处添加标题
PVD特点
气态
基底 薄膜
以气态方式进行 物质输运 能量输运
能量
块状材料 (靶材)
“物理气相沉积” 通常有下面三个工艺步骤:
1. 所生长的材料(靶材)以物理的方式由固体转化 为气体
2. 生长材料的蒸汽经过一个低压区域到达衬底
3. 蒸汽在衬底表面上凝结,形成薄膜
几种常见的薄膜结构
• 单层膜
A Substrate
在飞机和宇宙飞船的各种形状复杂的零部件上, 可镀制各 种薄膜;
为选择传播射线, 在建筑玻璃上镀制化合物镀层;
为减少摩擦, 在各种工程机械零件上镀制润滑的膜层;
太阳能和光电元件应用的各种薄膜…
ONLY ON THE FILM?
Volmer-Weber Mode
衬底
Island Growth ( 3D )
PVD特点 PVD现状与发展
PVD原理
PVD分类 PVD应用
FROM 1970s
PVD 技术出现于二十世纪七十年代末,制备的薄膜具有高硬度、低摩 擦系数、很好的耐磨性和化学稳定性等优点。近年来,由于PVD技术 和工艺、设备水平的发展,加上使用靶材品种和质量的增加,有效提 高了涂层和基体的结合强度,扩大了涂层材料的种类,是过去难于使 用PVD技术沉积的碳化物、氮化物、氧化物等硬质涂层,现在变成了 可能,极大地扩展了PVD技术的应用范围。
特点:多用于要求纯度极 高的膜、绝缘物的蒸镀和 高熔点物质的蒸镀。
Substrat e fixture
E-Gun Crucible
磁控溅射:使电子的路径不再是直线,而是螺旋线,
增加了与气体原子发生碰撞的几率,在同样的电压和气压 下可以提高气体电离的效率,提高了沉积速率。
附加磁场的优点
• 限制溅射离子的轨道 • 增加离子在气体中停留的时间 • 增强等离子体和电离过程 • 减少溅射原子从靶材到衬底路程中的碰撞 • 高磁场附近的产值比较高
溅射镀
直流溅射 射频溅射 磁控溅射
电子束蒸发镀膜仪 PVD 75 美国 Kurt J Lesker Company
磁控溅射镀膜仪 PVD 75 美国 Kurt J Lesker Company
电子束蒸发原理与特点
原理:热电子由灯丝发射 后,被加速阳极加速,获 得动能轰击到处于阳极的 蒸发材料上,使蒸发材料 加热气化,而实现蒸发镀 膜。
物理气相沉积技术优秀课件
PVD特点
PVD现状与发展
PVD原理
PVD分类 PVD应用
原理:物理气相沉积技术表示在真空条件下 ,采用物理方法,将材料源—固体或液体表 面气化成气态原子、分子或部分电离成离子 ,并通过低压气体(或等离子体)过程,在基 体表面沉积具有某种特殊功能的薄膜的技术
。
PVD的物理原理示意图