PFMEA示例
六步法pfmea案例
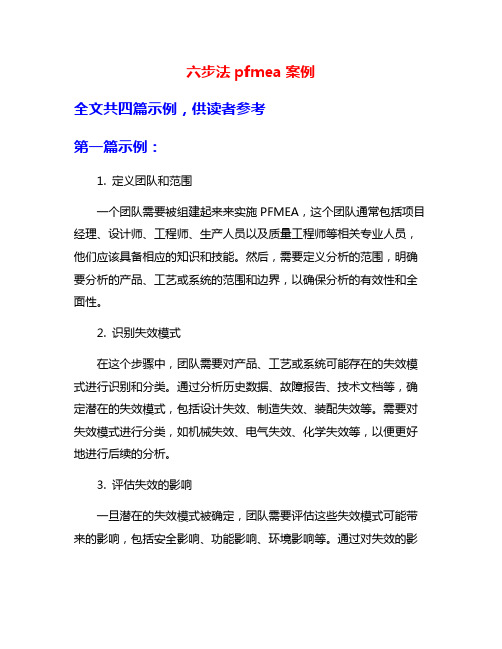
六步法pfmea案例全文共四篇示例,供读者参考第一篇示例:1. 定义团队和范围一个团队需要被组建起来来实施PFMEA,这个团队通常包括项目经理、设计师、工程师、生产人员以及质量工程师等相关专业人员,他们应该具备相应的知识和技能。
然后,需要定义分析的范围,明确要分析的产品、工艺或系统的范围和边界,以确保分析的有效性和全面性。
2. 识别失效模式在这个步骤中,团队需要对产品、工艺或系统可能存在的失效模式进行识别和分类。
通过分析历史数据、故障报告、技术文档等,确定潜在的失效模式,包括设计失效、制造失效、装配失效等。
需要对失效模式进行分类,如机械失效、电气失效、化学失效等,以便更好地进行后续的分析。
3. 评估失效的影响一旦潜在的失效模式被确定,团队需要评估这些失效模式可能带来的影响,包括安全影响、功能影响、环境影响等。
通过对失效的影响进行评估,可以确定关键的失效模式,并优先制定控制措施,以确保产品质量和可靠性。
4. 评估失效的频率和检测能力在这一步骤中,团队需要评估每个失效模式发生的频率和检测能力,即失效的可能性和检测的有效性。
通过对失效频率和检测能力的评估,可以确定高风险的失效模式,并制定相应的控制措施,以减少失效的发生和提高检测的有效性。
5. 制定和实施控制措施基于前面的分析,团队需要制定和实施相应的控制措施,以减少潜在的失效发生和影响。
这些控制措施可以包括设计改进、工艺优化、操作规程更新等,确保产品或系统在生产和使用过程中能够达到预期的性能和可靠性要求。
6. 监控和持续改进团队需要建立一个监控机制来跟踪控制措施的实施效果,并进行持续改进。
通过监控失效模式的发生和影响,可以及时调整和改进控制措施,以确保产品或系统的质量和可靠性得到持续改进。
通过六步法PFMEA的实施,可以帮助团队深入分析潜在失效模式,制定有效的控制措施,从而提高产品质量、减少生产成本和不良问题,提升企业的竞争力。
建议企业在产品设计和生产过程中广泛应用PFMEA方法,并不断优化和完善实施流程,以实现持续的质量改进和效率提升。
aiag vda pfmea例子

aiag vda pfmea例子
AIAG(汽车行业行动组)和VDA(德国汽车工业协会)合作制定了一种统一的PFMEA(过程失效模式和影响分析)标准,以确保汽车制造过程中的质量和安全。
以下是一个关于AIAG-VDA PFMEA的示例:
在汽车制造过程中,某公司决定对其发动机装配线进行PFMEA 分析。
首先,团队收集了有关发动机装配过程的数据,包括从零部件到最终装配的所有步骤。
然后,团队识别了潜在的失效模式,例如零部件装配不当、零部件缺陷、工具磨损等。
接下来,团队评估了每种失效模式可能对产品质量和安全性造成的影响,以及当前的控制措施是否足够有效。
团队还分配了严重性、发生频率和探测能力的评分,以确定优先级。
最后,团队提出了改进措施,例如改进装配工艺、增加检查步骤、提高员工培训等,以减少潜在的失效和提高质量水平。
这个示例展示了AIAG-VDA PFMEA的应用,通过系统性的分析和改进,可以帮助汽车制造公司识别和管理潜在的质量问题,从而提高产品质量和可靠性。
通过这种方法,公司可以确保其产品符合行业标准,并满足客户的需求和期望。
pfmea标准案例
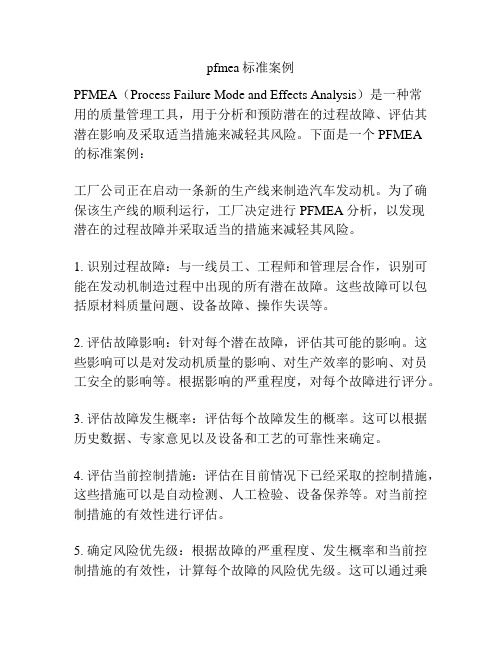
pfmea标准案例PFMEA(Process Failure Mode and Effects Analysis)是一种常用的质量管理工具,用于分析和预防潜在的过程故障、评估其潜在影响及采取适当措施来减轻其风险。
下面是一个PFMEA的标准案例:工厂公司正在启动一条新的生产线来制造汽车发动机。
为了确保该生产线的顺利运行,工厂决定进行PFMEA分析,以发现潜在的过程故障并采取适当的措施来减轻其风险。
1. 识别过程故障:与一线员工、工程师和管理层合作,识别可能在发动机制造过程中出现的所有潜在故障。
这些故障可以包括原材料质量问题、设备故障、操作失误等。
2. 评估故障影响:针对每个潜在故障,评估其可能的影响。
这些影响可以是对发动机质量的影响、对生产效率的影响、对员工安全的影响等。
根据影响的严重程度,对每个故障进行评分。
3. 评估故障发生概率:评估每个故障发生的概率。
这可以根据历史数据、专家意见以及设备和工艺的可靠性来确定。
4. 评估当前控制措施:评估在目前情况下已经采取的控制措施,这些措施可以是自动检测、人工检验、设备保养等。
对当前控制措施的有效性进行评估。
5. 确定风险优先级:根据故障的严重程度、发生概率和当前控制措施的有效性,计算每个故障的风险优先级。
这可以通过乘以这三个因素得到一个风险优先级数值。
6. 制定预防和纠正措施:根据风险优先级数值的高低,确定改进措施的紧急性。
高风险的故障可能需要立即采取纠正措施,而较低风险的故障可以在以后的时间里解决。
7. 实施措施:对确定的措施进行实施,并跟踪它们的有效性。
确保改进措施的有效性并记录结果。
通过这个PFMEA案例,工厂公司可以识别并降低生产线制造发动机过程中的潜在风险,提高发动机质量和生产效率,从而满足客户需求并实现更好的质量管理。
PFMEA分析范例
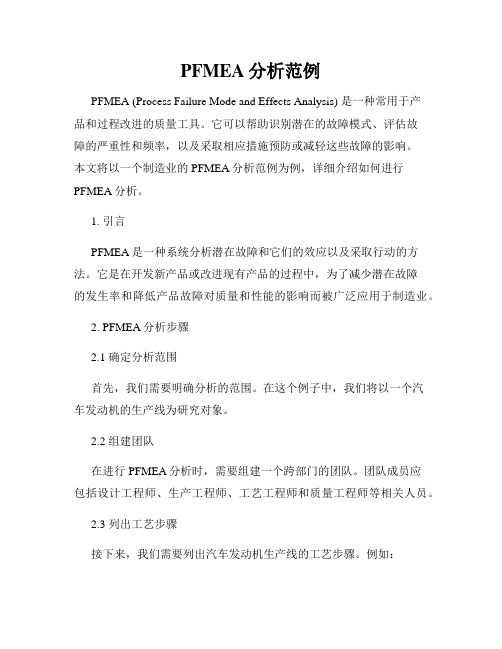
PFMEA分析范例PFMEA (Process Failure Mode and Effects Analysis) 是一种常用于产品和过程改进的质量工具。
它可以帮助识别潜在的故障模式、评估故障的严重性和频率,以及采取相应措施预防或减轻这些故障的影响。
本文将以一个制造业的PFMEA分析范例为例,详细介绍如何进行PFMEA分析。
1. 引言PFMEA是一种系统分析潜在故障和它们的效应以及采取行动的方法。
它是在开发新产品或改进现有产品的过程中,为了减少潜在故障的发生率和降低产品故障对质量和性能的影响而被广泛应用于制造业。
2. PFMEA分析步骤2.1 确定分析范围首先,我们需要明确分析的范围。
在这个例子中,我们将以一个汽车发动机的生产线为研究对象。
2.2 组建团队在进行PFMEA分析时,需要组建一个跨部门的团队。
团队成员应包括设计工程师、生产工程师、工艺工程师和质量工程师等相关人员。
2.3 列出工艺步骤接下来,我们需要列出汽车发动机生产线的工艺步骤。
例如:- 工艺步骤1:原材料采购和检验- 工艺步骤2:加工零部件- 工艺步骤3:组装零部件- 工艺步骤4:测试与质检- 工艺步骤5:包装和出厂2.4 识别潜在故障模式对于每个工艺步骤,团队成员需要一起识别潜在故障模式。
例如,在工艺步骤1中,可能存在以下潜在故障模式:- 检验不准确导致不合格原材料被误用于生产- 供应商延迟交付原材料,导致生产停滞2.5 评估故障严重性和频率在确定潜在故障模式后,团队成员需要评估每个故障的严重性和发生频率。
例如,在工艺步骤1中,检验不准确可能导致以下严重性和频率评估:- 严重性:高,因为不合格原材料可能导致发动机故障,导致安全隐患和质量问题- 频率:低,因为QC检验通常能准确发现不合格原材料2.6 识别潜在故障效应接下来,团队成员需要识别潜在故障对产品和过程的效应。
例如,在工艺步骤1中,检验不准确的潜在故障可能导致以下效应:- 效应1:生产线停滞,影响生产计划和交货时间- 效应2:不合格原材料出现在最终产品中,影响产品质量和客户满意度2.7 采取预防和纠正措施在识别潜在故障效应后,团队成员需要采取相应的预防和纠正措施来减轻故障的影响或防止故障发生。
PFMEA案例
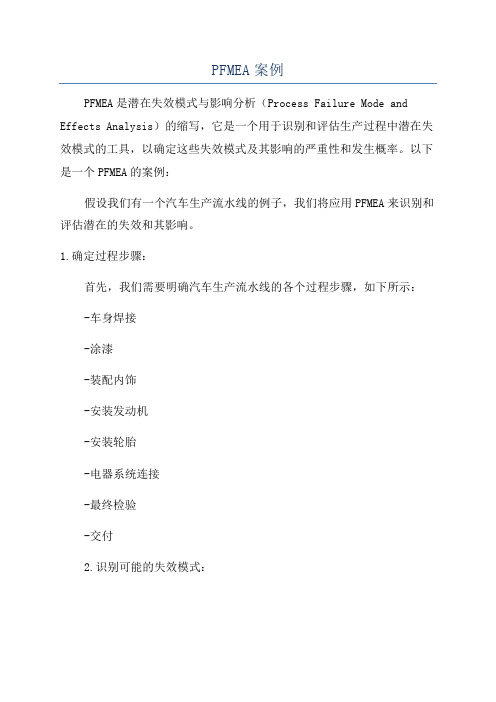
PFMEA案例PFMEA是潜在失效模式与影响分析(Process Failure Mode and Effects Analysis)的缩写,它是一个用于识别和评估生产过程中潜在失效模式的工具,以确定这些失效模式及其影响的严重性和发生概率。
以下是一个PFMEA的案例:假设我们有一个汽车生产流水线的例子,我们将应用PFMEA来识别和评估潜在的失效和其影响。
1.确定过程步骤:首先,我们需要明确汽车生产流水线的各个过程步骤,如下所示:-车身焊接-涂漆-装配内饰-安装发动机-安装轮胎-电器系统连接-最终检验-交付2.识别可能的失效模式:接下来,我们需要识别每个过程步骤中可能出现的失效模式。
例如,在车身焊接过程中,可能出现焊接点不牢固,焊接废弧,焊接接缝不均匀等问题。
相似地,其他过程步骤中也会有各种潜在的失效模式。
3.评估失效模式的严重性:对于每个失效模式,我们需要评估其对整个生产过程和最终产品的严重性。
例如,焊接点不牢固可能导致车身在使用过程中出现裂开的风险,这将对整个汽车的安全性产生严重的影响。
4.评估失效模式的发生概率:除了严重性,我们还需要评估每个失效模式发生的概率。
例如,在对焊接点进行质量控制的流程中,如果该过程的质量控制措施不严密,那么焊接点不牢固的问题就有更大的发生概率。
5.计算并确定潜在失效模式的优先级:最后,我们使用一个数学计算来确定每个失效模式的优先级。
该计算通常是通过将严重性和发生概率乘以一个探测度,来确定每种失效模式的优先级。
通过这种方法,我们可以明确识别并处理那些对整个生产过程和最终产品有重大影响的失效模式。
综上所述,PFMEA是一个重要的工具,可以用于识别和评估生产过程中的潜在失效模式。
通过识别这些模式及其严重性和发生概率,企业可以采取预防措施来降低失效风险,并提高产品和流程的质量。
PFMEA的例子
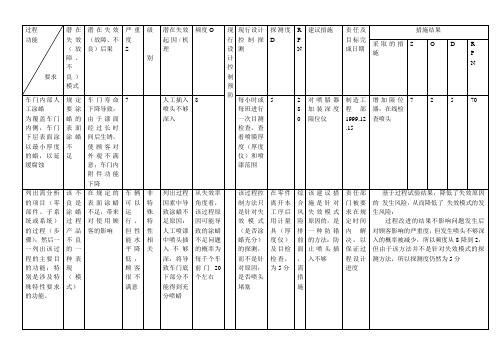
在规定的表面涂蜡不足,带来对使用顾客的影响
车辆可以运行,但性能水平降低,顾客很不满意
非特殊特性相关
列出过程因素中导致涂蜡不足原因:人工喷漆中喷头插入不够深,将导致车门底下部分不能得到充分喷蜡
从失效率角度看,该过程原因可能导致的涂蜡不足问题的概率为每千个车前门20个左右
RPN
建议措施
责任及目标完成日期
措施结果
采取的措施
S
O
D
R
P
N
车门内部人工涂蜡
为覆盖车门内侧,车门下层表面涂以最小厚度的蜡,以延缓腐蚀
规定要涂蜡的表面涂蜡不足
车门寿命下降导致:由于漆面经过长时间后生锈,使顾客对外观不满意;车门内附件功能下降
7
人工插入喷头不够深入
8
每小时或每班进行一次目测检查,查看厚度(厚度仪)和喷漆范围
7
人工插入喷头不够深入
8
每小时或每班进行一次目测检查,查看喷膜厚度(厚度仪)和喷漆范围
5
280
对喷腊器加装深度限位仪
制造工程部1999.12.15
增加限位器,在线检查喷头
7
2
5
70
列出需分析的项目(零部件、子系统或系统)的过程(步骤);然后一一列出该过程的主要目的功能;特别是涉及特殊特性要求的功能。
过程改进的结果不影响问题发生后对顾客影响的严重度,但发生喷头堵塞的概率被减少,所有频度从5降到1(完全不会发生),但由于该方法并不是针对失效模式的探测方法,所有探测度仍然为5分。
ቤተ መጻሕፍቲ ባይዱ过程
功能
要求
潜在失效(故障、不良)模式
潜在失效(故障、不良)后果
严重度
PFMEA分析范例(第四版)

过程失效模式及后果分析P FMEA
本体吹塑成型:塑料以熔融状态在封闭模具型
腔内成型
1、项目:填入需分析的项目名称(系统)和所属专业室(子系统)。
供方名称/代码:输入负有过程设计职责的OME、组织或部门,及供方组织的代码。
编号:填入一个用于识别PFMEA文件的数字列,用于文件控制。
关键日期:填入PFMEA的初始日期,但不能超过预期的生产日期的开始时间,如果是供方组织,日期不能超过顾客要求的PPAP提交日期。
编制:填入负责编制PFMEA的工程师/小组的名字和联系信息。
项目型号/年份:填入将使用或将分析过程影响的型号投产年度和项目代号。
最初:PFMEA完成的最早日期。
修订:PFMEA修订日期。
2、表格末尾的编制、审查、批准及日期必须手签。
注意:不够可以加页。
扬声器PFMEA案例

有警告的危害
当潜在的失效模式在有警告的情况下影响车辆安全运行和/或涉及不符合政府法规的情形时,严重度定级非常高
或可能在有警告的情况下对(机器或总成)操作者造成危害
9
很高
车辆/项目不能工作(丧失基本功能)
或100%的产品可能需要报废,或者车辆/项目需在返修部门返修1个小时以上
8
高
车辆/项目可运行但性能水平下降。
案例:
某音响制造公司为某汽车制造商设计制造一车用扬声器。以下是汽车制造商提出的(部分)要求:
安装尺寸▼:外形图标注,为4’扬声器。
可靠性要求:3年无故障▼。
阻抗:8.0±0.8 OHM at 400Hz
特性灵敏度级:88±2dB
f0:120±15Hz
额定功率:8W
长期最大功率:20W
注:其中带▼为特殊特性。
扬声器主要技术参数:
…………
内部要求:
易于装配,一次装配合格率(直通率)大于99%。
案例:为了保证产品设计意图完整地贯彻到生产过程中,公司组建了PFMEA小组。小组组长由工艺工程师王五担任,小组成员有品质工程师赵六,SQE钱七,以及计划将来进行该产品生产的生产车间主任贾师傅。
PFMEA小组首先利用特性矩阵,将产品关键特性对应到生产过程的中,在此基础上,PFMEA小组开发了PFMEA
2006-10-30:SQE小组,确定批准要求并完成供应商手册。2008-10-01,供应商满足手册要求
尤全
10-30前投入使用
5
2
2
20
过程FMEA的标准表
系统潜在失效模式及后果FMEA编号
子系统(PFMEA)共页,第页
部件设计责任编制人
车型年/车辆类型关键日期FEMA日期(编制)(修订)
- 1、下载文档前请自行甄别文档内容的完整性,平台不提供额外的编辑、内容补充、找答案等附加服务。
- 2、"仅部分预览"的文档,不可在线预览部分如存在完整性等问题,可反馈申请退款(可完整预览的文档不适用该条件!)。
- 3、如文档侵犯您的权益,请联系客服反馈,我们会尽快为您处理(人工客服工作时间:9:00-18:30)。
潜在失效模式及后果分析
(PFMEA)
项目名称:BABY—PHONE过程责任部门:涂装一厂 FMEA编号:
页码:第1页共8页关键日期:06.10.18 FMEA日期(编制): 06.10.16 编制者:王俊伟
(PFMEA)
项目名称:BABY—PHONE 过程责任部门:涂装一厂 FMEA编号:
页码:第2页共8页关键日期:06.10.18 FMEA日期(编制):06.10.16 编制者:王俊伟
主要参加人:李宝玉、王妙英、许博
潜在失效模式及后果分析
(PFMEA)
项目名称:BABY—PHONE 过程责任部门:涂装一厂 FMEA编号:
页码:第3页共8页关键日期:06.10.18 FMEA日期(编制): 06.10.16 编制者:王俊伟
主要参加人:李宝玉、王妙英、许博
潜在失效模式及后果分析
(PFMEA)
项目名称:BABY—PHONE 过程责任部门:涂装一厂 FMEA编号:
页码:第4页共8页关键日期:06.10.18 FMEA日期(编制): 06.10.16 编制者:王俊伟
(PFMEA)
项目名称:BABY—PHONE过程责任部门:涂装一厂 FMEA编号:
页码:第5页共8页关键日期:06.10.18 FMEA日期(编制): 06.10.16 编制者:王俊伟
潜在失效模式及后果分析
(PFMEA)
项目名称:BABY—PHONE 过程责任部门:涂装一厂 FMEA编号:
页码:第6页共8页关键日期:06.10.18 FMEA日期(编制): 06.10.16 编制者:王俊伟
主要参加人:李宝玉、王妙英、许博
潜在失效模式及后果分析
(PFMEA)
项目名称:BABY—PHONE 过程责任部门:涂装一厂 FMEA编号:
页码:第7页共8页关键日期:06.10.18 FMEA日期(编制): 06.10.16 编制者:王俊伟
主要参加人:李宝玉、王妙英、许博
潜在失效模式及后果分析
(PFMEA)
项目名称:BABY—PHONE 过程责任部门:涂装一厂 FMEA编号:
页码:第8页共8页关键日期:06.10.18 FMEA日期(编制): 06.10.16 编制者:王俊伟。