固定管板式换热器计算
固定式管板式换热器

计算换热面积,以换热管外径为基准,扣除不参与换热的换热管长度后,计算得到的外表面积。
公称换热面积,圆整为整数后的计算换热面积。
管程——介质流经换热管内的通道及与其相贯通部分。
以换热器的长度作为管壳式热交换器的公称长度。
换热管为直管时,取直管长度;换热管为U形管时,取U形管直管段的长度。
为消除换热管与管板管孔之间缝隙的轻度胀接。
管程——换热管常用排列形有正三角行排列(30°)、转角正三角形排列(60°)、正方形排列(90°)、转角正方形排列(45°)。
注:流向垂直于折流板缺口。
换热管中心距不宜小于1.25倍的换热管外径。
管箱平盖与管箱的连接紧固件宜采用双头螺柱。
与管板连接的强化传热管端部光管长度不应小于管板厚度加30mm;未作规定时光管长度为120mm。
换热管材料的硬度应低于管板的硬度。
强度焊接的焊脚高度ι应满足7.4.7中换热管与管板连接拉脱力的要求,且ι不应小于δt。
折流板间距管束两端的折流板尽可能靠近壳程进、出口接管,其余折流板宜按等间距布置。
折流板最小间距不宜小于圆筒内径的1/5且不小于50mm,特殊情况下也可取较小的间距。
当不能利用接管(或接口)进行放气或排液时,应在管程和壳程的最高点设置放气口,在最低点设置排液口。
设备法兰优先采用NB/T47021~47023、GB/T29465中的法兰。
热交换器的公称长度不大于3m时,鞍座间距L B宜取0.4倍~0.6倍热交换器的公称长度;热交换器的公称长度大于3m时,鞍座间距L B宜取0.5倍~0.7倍热交换器的公称长度;必要时应对支座和壳体进行强度和稳定性校核;鞍座支座可按JB/T4712.1选用。
换热管的厚度应按GB150.3-2011中的外径公式进行计算,必要时还应进行外压校核。
管板换热器采用焊接连接时,管板最小厚度应满足结构设计和制造要求,且不小于12mm。
换热管直管或直管段长度大于6000mm时允许拼接;且应符合以下要求:设备法兰、分程隔板的密封面应在热处理后加工。
固定管板式换热器计算解析
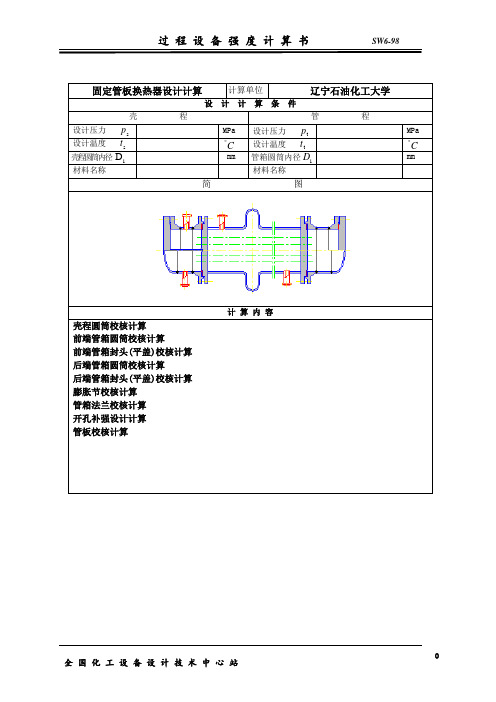
厚度及重量计算
形状系数
K= =
计算厚度
= =
mm
有效厚度
e=n-C1- C2=
mm
最小厚度
min=
mm
名义厚度
n=
mm
结论
满足最小厚度要求
重量
Kg
压力计算
最大允许工作压力
[Pw]= =
MPa
结论
合格
后端管箱筒体计算
计算单位
辽宁石油化工大学
计算条件
筒体简图
计算压力Pc
MPa
设计温度t
C
内径Di
MPa
压力试验允许通过
的应力水平T
T0.90s=
MPa
试验压力下
圆筒的应力
T= =
MPa
校核条件
TT
校核结果
合格
压力及应力计算
最大允许工作压力
[Pw]= =
MPa
设计温度下计算应力
t= =
MPa
t
MPa
校核条件
t≥t
结论
筒体名义厚度大于或等于GB151中规定的最小厚度6.00mm,合格
后端管箱封头计算
旋转刚度
MPa
材料名称
壳
壳体法兰厚度
mm
法兰外径
管板和管子连接型式
管板和管子胀接(焊接)高度l
mm
胀接许用拉脱应力[q]
MPa
焊接许用拉脱应力[q]
MPa
管
材料名称
管箱法兰厚度
mm
法兰外径
mm
箱
基本法兰力矩
Nmm
管程压力操作工况下法兰力
Nmm
法兰宽度
列管换热器的换热面积是如何计算的呢?

列管换热器的换热面积是如何计算的呢?是以内径还是外径为计算基准呢?如25*3的管长度2m 数量300理论计算的换热面积该是多少呢?1. 一般是按外径来计算,不过也有按中径计算的,但没听说过按内径的。
2. 换热器如果是固定管板式换热器,按外径计算的话:换热面积=3.1415926xD(外径)x L(长度)xn(数量)=3.1415926 x0.025x2x300=47.12平方米3. 提醒一点:L长度应该为有效长度,即为两管板间的距离,等于换热管长度减去两端伸出管板高度,再减去两倍管板厚度的长度。
版主说的对,但结论47.12有误。
换热面积=3.1415926xD(外径)x L(长度)x n(数量)=3.1415926x0.025xLx300=23.5 619xL平方米外径单位:m ;长度单位:m------------------------------换热器设计手册P19这个我们通常按外径计算,但是我要提醒楼主的是计算换热面积和传热系数是对应. 我们制作换热器是都是按照外径计算的,还要减去管板与折流板的面化工原理列管换热器设计!求指导多谢2013-01-03 15:08黄141|分类:工程技术科学|浏览101次设计题目:列管式换热器设计二、操作条件及设计任务1、操作条件柴油处理能力:学号1-18号(进料量)10000吨+学号*1000吨/年学号19-37号(进料量)10000吨+学号*500吨/年(注:本处学号为两位数字的序号)操作时间:8000小时/年进出口温度:学号1-18号:原油;入口温度70℃,出口温度110℃;柴油:入口温度175℃,出口温度130℃学号19-37号:原油;入口温度65℃,出口温度100℃;柴油:入口温度170℃,出口温度130两侧压力降都不应超过0.3at厂址:宁波地区。
2、设计任务:(1)选择适宜的列管式换热器:流程的选择、流速的选择、流体阻力的计算。
(2)工艺计算:有效平均温度差、传热系数K、传热面积A。
四管程固定管板式换热器设计
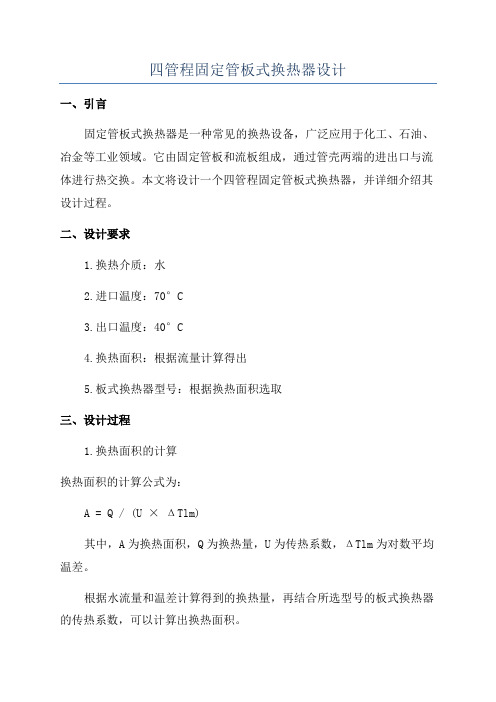
四管程固定管板式换热器设计一、引言固定管板式换热器是一种常见的换热设备,广泛应用于化工、石油、冶金等工业领域。
它由固定管板和流板组成,通过管壳两端的进出口与流体进行热交换。
本文将设计一个四管程固定管板式换热器,并详细介绍其设计过程。
二、设计要求1.换热介质:水2.进口温度:70°C3.出口温度:40°C4.换热面积:根据流量计算得出5.板式换热器型号:根据换热面积选取三、设计过程1.换热面积的计算换热面积的计算公式为:A = Q / (U × ΔTlm)其中,A为换热面积,Q为换热量,U为传热系数,ΔTlm为对数平均温差。
根据水流量和温差计算得到的换热量,再结合所选型号的板式换热器的传热系数,可以计算出换热面积。
2.板式换热器的选取根据计算得到的换热面积,选择合适的型号的板式换热器。
在选型时,要考虑换热器的材质、耐压性能、传热系数等因素。
3.管程的设计四、设计结果根据设计要求和计算过程,可以得出四管程固定管板式换热器的设计结果。
1.换热面积:根据计算结果得出换热面积为X平方米。
2.板式换热器型号:根据换热面积和选取条件,最终确定使用XX型号的板式换热器。
3.管程设计:根据流体的温度差和流速等因素,按照长度逐渐增加的方式,确定四个管程的设计。
五、结论本文根据给定的设计要求,设计了一个四管程固定管板式换热器,并详细介绍了设计过程。
设计结果包括换热面积、板式换热器型号和管程设计。
通过本文的设计,可以满足给定的换热要求,并提供一个可行的四管程固定管板式换热器设计方案。
固定管板式换热器

固定管板式换热器一 换热管1换热管外径取换热管外径为25*2.5。
2换热管数量及长度*(0.1)An d L π=-A 换热面积D 换热管外径l 换热管长度A=402m取安全系数1.125,1*1.12546A A == 140*1.125248*(0.1) 3.14*0.02*(30.1)A n d L π==≈--n=248L=33布管(1)换热管排列方式采用正三角形排列(2)换热管中心距查阅课本139页表5-3确定换热管中心距是32mm 。
二换热器壳体1换热器内径计算0*(1)(2~3)*D t b d =-+t 管心距d 0 换热管外径D 壳体内径17.32281b ===0*(1)(2~3)*D t b d =-+t=32mm32*(17.322811)2*25572.32992D =-+=取D=600mm2筒体壁厚计算水蒸气工作压力1.27Mpa ,脱盐水工作压力1.28Mpa 。
材料选16MnR工作温度T=150/170℃查阅课本32页确定设计设计温度T W =170/190℃脱盐水走壳程,水蒸气走管程。
*2*[]*c i t c p D p δσφ=-δ 圆筒的计算壁厚c p 圆筒的计算压力[]t σ 许用应力φ 焊接接头系数[]t σ 156查阅课本32页确定c p =1.28+0.18=1.46MpaGB150规定焊接接头系数容器受压元件焊接接头的工艺特点以及无损检测的抽查率确定,查阅课本38页确定φ=0.85。
* 1.46*600 3.322*[]*2*156*0.86 1.46c i t c p D mm p δσφ==≈--d C δδ=+查阅课本40也确定C 2=1.5mm 。
查阅课本39页确定C 1=0.3mmC= C 1 + C 2=1.8mm3.321 1.8 5.121d C mm δδ=+=+=元整后6n mm δ=(3)布管限定圆查阅GB15132*L i D D b =-L D 布管限定圆i D 圆筒内直径3b 最外层换热管外表面至壳体内壁的最短距离,30.25*b d =30.25* 6.25b d ==3b 一般不小于8mm32*6002*8584L i D D b mm =-=-=三管板设计1管板厚度GB151-1999规定00250.75*d mm d δ≤≥时018.75d mm ≥020d mm =2管板与换热管的连接胀结受到压力和温度的限制。
固定管板式换热器结构设计与强度计算
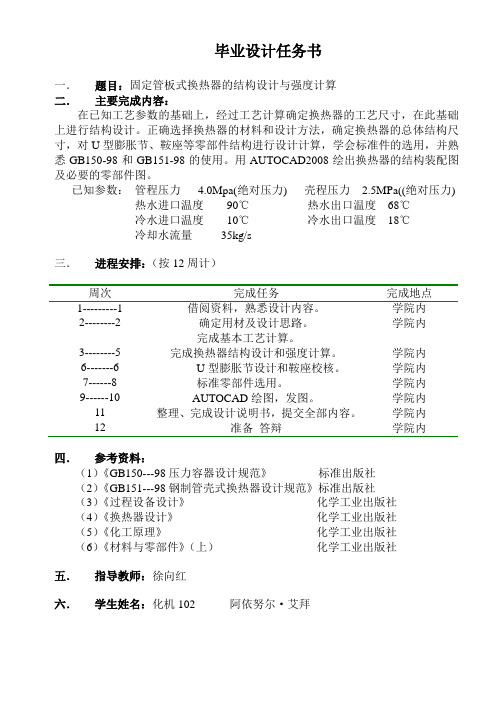
毕业设计任务书一.题目:固定管板式换热器的结构设计与强度计算二.主要完成内容:在已知工艺参数的基础上,经过工艺计算确定换热器的工艺尺寸,在此基础上进行结构设计。
正确选择换热器的材料和设计方法,确定换热器的总体结构尺寸,对U型膨胀节、鞍座等零部件结构进行设计计算,学会标准件的选用,并熟悉GB150-98和GB151-98的使用。
用AUTOCAD2008绘出换热器的结构装配图及必要的零部件图。
已知参数:管程压力 4.0Mpa(绝对压力) 壳程压力 2.5MPa((绝对压力) 热水进口温度90℃热水出口温度68℃冷水进口温度10℃冷水出口温度18℃冷却水流量35kg/s三.进程安排:(按12周计)1---------1 借阅资料,熟悉设计内容。
学院内2--------2 确定用材及设计思路。
学院内完成基本工艺计算。
3--------5 完成换热器结构设计和强度计算。
学院内6-------6 U型膨胀节设计和鞍座校核。
学院内7------8 标准零部件选用。
学院内9------10 AUTOCAD绘图,发图。
学院内11 整理、完成设计说明书,提交全部内容。
学院内12 准备答辩学院内四.参考资料:(1)《GB150---98压力容器设计规范》标准出版社(2)《GB151---98钢制管壳式换热器设计规范》标准出版社(3)《过程设备设计》化学工业出版社(4)《换热器设计》化学工业出版社(5)《化工原理》化学工业出版社(6)《材料与零部件》(上)化学工业出版社五.指导教师:徐向红六.学生姓名:化机102 阿依努尔·艾拜。
固定管板式换热器工艺计算 说明书
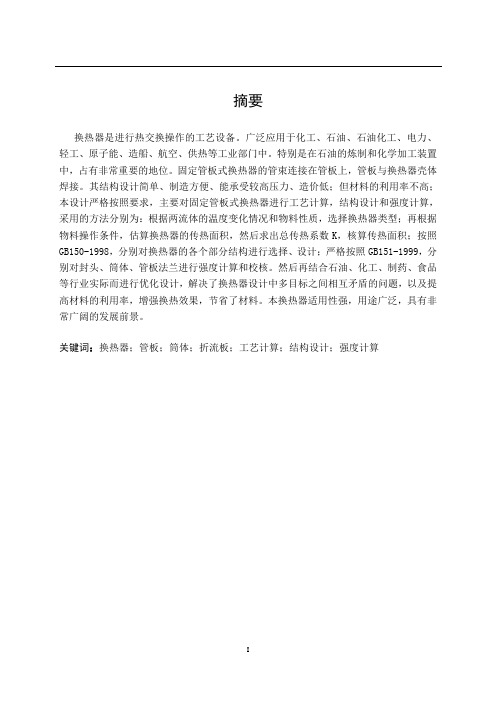
摘要换热器是进行热交换操作的工艺设备。
广泛应用于化工、石油、石油化工、电力、轻工、原子能、造船、航空、供热等工业部门中。
特别是在石油的炼制和化学加工装置中,占有非常重要的地位。
固定管板式换热器的管束连接在管板上,管板与换热器壳体焊接。
其结构设计简单、制造方便、能承受较高压力、造价低;但材料的利用率不高;本设计严格按照要求,主要对固定管板式换热器进行工艺计算,结构设计和强度计算,采用的方法分别为:根据两流体的温度变化情况和物料性质,选择换热器类型;再根据物料操作条件,估算换热器的传热面积,然后求出总传热系数K,核算传热面积;按照GB150-1998,分别对换热器的各个部分结构进行选择、设计;严格按照GB151-1999,分别对封头、筒体、管板法兰进行强度计算和校核。
然后再结合石油、化工、制药、食品等行业实际而进行优化设计,解决了换热器设计中多目标之间相互矛盾的问题,以及提高材料的利用率,增强换热效果,节省了材料。
本换热器适用性强,用途广泛,具有非常广阔的发展前景。
关键词:换热器;管板;筒体;折流板;工艺计算;结构设计;强度计算AbstractHeat exchanger for heat exchange operation is a common process equipment. Widely used in chemical, petroleum, petrochemical, power, light industry, metallurgy, nuclear, shipbuilding, aviation, heating and other industrial sectors. Particularly in the oil refining and chemical processing unit, occupies an extremely important position. Fixed tube plate heat exchanger tubes connected to the tube sheet, tube sheet and shell welding. Its simple structure, convenience, able to withstand high pressure, low cost; but the material utilization is not high; designed in strict accordance with the requirements of the standard GB151-1999, mainly on the fixed tube heat exchanger for process calculation, structural design and strength calculations, the methods used were: two-fluid temperature changes according to circumstances and nature of the materials, select the type of heat exchanger; according to the operating conditions of the material, estimate the heat transfer area, and then find the overall heat transfer coefficient K, accounting for heat transfer area; according to GB150-1998, were all part of the structure of the heat exchanger selection and design; in strict accordance with GB151-1999, respectively, on the head, cylinder, pipe flange for strength calculation and checking. Then combine the oil, chemical, pharmaceutical, food and other industries to optimize the design of practical and solve multi-objective design of heat exchanger between the conflicting issues, and improve material utilization, enhanced heat transfer effect, savings in materials. The heat exchanger applicability, versatility, and has broad prospects for development.Keywords: heat exchanger; bundle; tube plate; head; cylinder; flange; process calculation; structural design; strength calculation目录摘要 (I)Abstract (II)第一章绪论 (1)1.1 选题背景和意义 (1)1.2 国内外研究现状 (1)第2章设计方案 (3)2.1 选择换热器的类型 (3)2.2 物料流程安排 (3)第3章工艺计算 (4)3.1 确定物性参数 (4)3.2 估算传热面积 (4)3.3.1 热流量 (4)3.3.2 平均传热温差 (4)3.3.3 传热面积 (5)3.3.4 冷却水用量 (5)3.4 工艺结构尺寸 (5)3.4.1 管径和管内流速 (5)3.4.2 管程数和传热管数 (5)3.4.3 平均传热温差校正及壳程数 (6)3.4.4 传热管排列和分程方法 (6)3.4.5 壳体内径 (7)3.4.6 折流板 (7)3.4.7 接管 (7)3.5 换热器核算 (7)3.5.1 热流量核算 (7)3.5.1.1 壳程表面传热系数 (7)3.5.1.2 管内表面传热系数 (8)3.5.1.3 污垢热阻和管壁热阻 (9)3.5.1.4 计算传热系数 (9)3.5.1.5 换热器的面积裕度 (9)3.5.2 换热器内流体的流动阻力 (10)3.5.2.1 管程流体阻力 (10)3.5.2.2 壳程流体阻力 (10)3.5.3壁温核算 (11)3.6 换热器主要结构尺寸和计算结果表 (11)第4章强度计算 (13)4.1 壳体、管箱壳体和封头的设计 (13)4.1.1 壁厚的确定 (13)4.1.2 封头的设计 (14)4.1.3 进出口的设计 (14)4.1.3.1 接管外伸长度 (14)4.1.3.2 接管与筒体、管箱壳体的链接 (14)4.1.3.3 接管位置 (14)4.2 管板与换热管 (15)4.2.1 管板 (15)4.2.1.1 管板结构 (15)4.2.1.2 管板最小厚度 (16)4.2.1.3 管板尺寸 (16)4.3 壳体与管板、管板与法兰及换热管的连接 (16)4.3.1 壳体与管板的连接结构 (16)4.3.2 管板与法兰的连接 (16)4.3.3 管子与管板 (16)4.4 螺栓法兰连接设计 (17)4.4.1 垫片选择 (17)4.4.2 螺栓设计 (17)4.5 管板设计 (18)第5章其他各部件结构 (20)5.1 折流板 (20)5.1.1 折流板管孔 (20)5.1.2 折流板的布置 (20)5.2 拉杆 (20)5.3 防冲板 (21)5.4 支座 (21)5.5 膨胀节 (21)5.6 鞍座的选择 (23)5.7 各种可能情况下的应力校核 (26)5.7.1 只有壳程设计压力而管程设计压力 (26)5.7.2 只有管程设计压力而壳程设计压力 (33)结论 (40)参考文献 (41)致谢 (42)第一章绪论1.1 选题背景和意义换热器是将热流体的部分热量传递给冷流体的设备,又称热交换器。
固定管板式换热器壳程体积计算
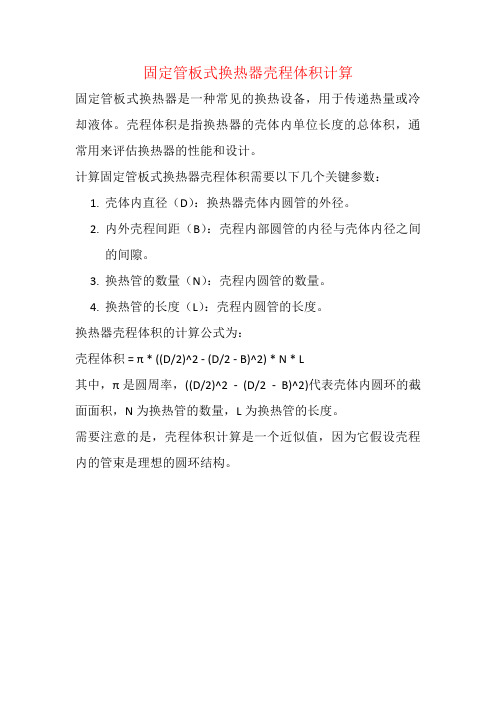
固定管板式换热器壳程体积计算
固定管板式换热器是一种常见的换热设备,用于传递热量或冷却液体。
壳程体积是指换热器的壳体内单位长度的总体积,通常用来评估换热器的性能和设计。
计算固定管板式换热器壳程体积需要以下几个关键参数:
1.壳体内直径(D):换热器壳体内圆管的外径。
2.内外壳程间距(B):壳程内部圆管的内径与壳体内径之间
的间隙。
3.换热管的数量(N):壳程内圆管的数量。
4.换热管的长度(L):壳程内圆管的长度。
换热器壳程体积的计算公式为:
壳程体积= π * ((D/2)^2 - (D/2 - B)^2) * N * L
其中,π是圆周率,((D/2)^2 - (D/2 - B)^2)代表壳体内圆环的截面面积,N为换热管的数量,L为换热管的长度。
需要注意的是,壳程体积计算是一个近似值,因为它假设壳程内的管束是理想的圆环结构。
- 1、下载文档前请自行甄别文档内容的完整性,平台不提供额外的编辑、内容补充、找答案等附加服务。
- 2、"仅部分预览"的文档,不可在线预览部分如存在完整性等问题,可反馈申请退款(可完整预览的文档不适用该条件!)。
- 3、如文档侵犯您的权益,请联系客服反馈,我们会尽快为您处理(人工客服工作时间:9:00-18:30)。
计
系数(按K,Q或Qex查图30)
法兰力矩折减系数
管板边缘力矩变化系数
算
法兰力矩变化系数
管
管板开孔后面积Al= A- 0.25nd2
mm2
板
参
管板布管区面积
(三角形布管)
(正方形布管)
mm2
数
管板布管区当量直径
mm
系数
系
系数
数
系数
计
系数(带膨胀节时 代替Q)
算
管板布管区当量直径与壳体内径之比
Wp=Fp+F=
N
所需螺栓总截面积Am
Am= max (Ap,Aa) =
mm2
实际使用螺栓总截面积Ab
Ab= =
mm2
力矩计算
操
FD= 0.785 pc
=
N
LD=LA+ 0.5δ1
=
mm
MD=FDLD
=
N.mm
作
FG=Fp
=
N
LG= 0.5 (Db-DG)
=
mm
MG=FGLG
=
N.mm
Mp
FT=F-FD
mm
材料
试验温度许用应力
MPa
设计温度许用应力t
MPa
试验温度下屈服点s
MPa
钢板负偏差C1
mm
腐蚀裕量C2
mm
焊接接头系数
厚度及重量计算
计算厚度
= =
mm
有效厚度
e=n-C1- C2=
mm
名义厚度
n=
mm
重量
Kg
压力试验时应力校核
压力试验类型
液压试验
试验压力值
PT= 1.25P =(或由用户输入)
旋转刚度无量纲参数
膨胀节总体轴向刚度
N/mm
管板第一弯矩系数(按 , 查<<GB151-1999>>图27)
系
系数
系数(按 查<<GB151-98>>图29)
换热管束与不带膨胀节壳体刚度之比
数
换热管束与带膨胀节壳体刚度之比
管板第二弯矩系数(按K,Q或 查<<GB151-1999>>图28(a)或(b))
管板校核通过
筒体法兰计算结果
计算单位
辽宁石油化工大学
设计条件
简图
设计压力p
MPa
计算压力pc
MPa
设计温度t
C
轴向外载荷F
N
外力矩M
N.mm
壳
材料名称
体
许用应力
MPa
法
材料名称
许用
[]f
MPa
兰
应力
[]tf
MPa
材料名称
螺
许用
[]b
MPa
应力
[]tb
MPa
栓
公称直径dB
mm
螺栓根径d1
mm
数量n
个
Di
=
N
LT=0.5(LA+1+LG)
=
mm
MT=FTLT
=
N.mm
外压:Mp=FD(LD-LG)+FT(LT-LG);内压:Mp=MD+MG+MTMp=
N.mm
预紧Ma
W=
N
LG=
mm
Ma=WLG=
N.mm
计算力矩Mo=Mp与Ma[]ft/[]f中大者Mo=
N.mm
计算单位
辽宁石油化工大学
计算条件
椭圆封头简图
计算压力Pc
MPa
设计温度t
C
内径Di
mm
曲面高度hi
mm
材料
设计温度许用应力t
MPa
试验温度许用应力
MPa
钢板负偏差C1
mm
腐蚀裕量C2
mm
焊接接头系数
厚度及重量计算
形状系数
K= =
计算厚度
= =
mm
有效厚度
e=n-C1- C2=
mm
最小厚度
min=
mm
mm
系数Cr=
比值lcr/i
管子稳定许用压应力( )
MPa
管
管子稳定许用压应力( )
MPa
材料名称
设计温度tp
管
设计温度下许用应力
MPa
设计温度下弹性模量Ep
MPa
管板腐蚀裕量C2
mm
管板输入厚度n
mm
管板计算厚度
mm
隔板槽面积(包括拉杆和假管区面积)Ad
mm2
板
管板强度削弱系数
管板刚度削弱系数
管子加强系数 K=
=
壳体法兰力矩系数
计算值
许用值
计算值
许用值
管板径向应力
1.5
3
MPa
管板布管区周边处径向应力
1.5
3
MPa
管板布管区周边剪切应力
0.5
1.5
MPa
壳体法兰应力
1.5
3
MPa
换热管轴向应力
3
MPa
壳程圆筒轴向应力
MPa
换热管与管板连接拉脱应力q=
[q]
3[q]焊接
[q]胀接
MPa
计算结果
管板名义厚度
mm
Do
垫
结构尺寸
Db
D外
D内
δ0
mm
Le
LA
h
δ1
材料类型
N
m
y(MPa)
压紧面形状
b
DG
片
b0≤6.4mmb=b0
b0≤6.4mmDG= (D外+D内)/2
b0>6.4mmb=2.53
b0>6.4mmDG=D外- 2b
螺栓受力计算
预紧状态下需要的最小螺栓载荷Wa
Wa=πbDGy=
N
操作状态下需要的最小螺栓载荷Wp
MPa
平均金属温度下管子材料弹性模量Et
MPa
平均金属温度下管子材料热膨胀系数t
mm/mm
管
管子外径d
mm
管子壁厚t
mm
注:
管子根数n
换热管中心距S
mm
换
一根管子金属横截面积
mm2
换热管长度L
mm
管子有效长度(两管板内侧间距)L1
mm
管束模数Kt=Etna/LDi
MPa
管子回转半径
mm
热
管子受压失稳当量长度lcr
管板周边不布管区无量纲宽度k = K(1-t)
壳体法兰应力
1.5
3
MPa
换热管轴向应力
3
MPa
壳程圆筒轴向应力
MPa
换热管与管板连接拉脱应力q=
[q]
3[q]焊接
[q]胀接
MPa
仅有管程压力Pt作用下的危险组合工况(Ps= 0)
不计温差应力
计温差应力
换热管与壳程圆筒热膨胀变形差
= (t -t )- (t -t )
开孔补强设计计算
管板校核计算
前端管箱筒体计算
计算单位
辽宁石油化工大学
计算条件
筒体简图
计算压力Pc
MPa
设计温度t
C
内径Di
mm
材料
试验温度许用应力
MPa
设计温度许用应力t
MPa
试验温度下屈服点s
MPa
钢板负偏差C1
mm
腐蚀裕量C2
mm
焊接接头系数
厚度及重量计算
计算厚度
= =
mm
有效厚度
e=n-C1- C2=
厚度及重量计算
计算厚度
= =
mm
有效厚度
e=n-C1- C2=
mm
名义厚度
n=
mm
重量
Kg
压力试验时应力校核
压力试验类型
液压试验
试验压力值
PT= 1.25P =(或由用户输入)
MPa
压力试验允许通过
的应力水平T
T0.90s=
MPa
试验压力下
圆筒的应力
T= =
MPa校核条件TT Nhomakorabea校核结果
合格
压力及应力计算
名义厚度
n=
mm
结论
满足最小厚度要求
重量
Kg
压力计算
最大允许工作压力
[Pw]= =
MPa
结论
合格
壳程圆筒计算
计算单位
辽宁石油化工大学
计算条件
筒体简图
计算压力Pc
MPa
设计温度t
C
内径Di
mm
材料
试验温度许用应力
MPa
设计温度许用应力t
MPa
试验温度下屈服点s
MPa
钢板负偏差C1
mm
腐蚀裕量C2
mm
焊接接头系数
当量压力组合
MPa
有效压力组合
MPa
操作情况下法兰力矩系数
管板边缘力矩系数
管板边缘剪力系数
管板总弯矩系数
系数 仅用于 时
系数
当 时,按K和m查图31(a)实线
当 时,按K和m查31(b)
系数 >0, = ;
<0 , =
管板径向应力系数
带膨胀节Q为Q
=
管板布管区周边
处径向应力系数
=
管板布管区周边
处剪切应力系数
Mpa
程
平均金属温度下弹性模量Es