整体硬质合金麻花钻常用槽型性能实验研究
麻花钻切削分析及改进

垂狂虽
赢牺钻头 图一 麻 花钻 的 结构 图
3 麻 花钻 的缺点 3 .1 不利 于切 削的 曲 卷 。因 为 主切 削 刃各 点 前 角 、刃 倾 角 、 切削 速度 、方 向的差 异 ,因而在 各点 处 切 屑流 出方 向不 同 ,并 存在
1 .1 刀体 。刀体 是钻头 的工 作 部 分 , 由切削 部 分 与导 向部 分 共 同组 成 。
2 0 1 7年 6月
西 部 皮 革
工艺 与 技 术
麻 花 钻 切 削 分 析 及 改 进
何剑汇
( 山东科 技 大学 ,山东 青 岛 2 6 6 5 9 0 )
摘 要 :麻花 钻是 通过 其相 对 固定 轴 线的旋 转切 削 以钻 削工件 的 圆孔 的 工具 。 因其 容屑 槽 成 螺旋 状 而形 似 麻 花 而得 名 ,是 最
美键词:麻花钻{分析;改进
申图分类粤i G 童
文献标志码:A
文章编号 :1 6 7 1 —1 6 0 2( 2 0 1 7 )1 2— 0 0 0 1 一 o 1
渐增 大。 2 .5 主 、副偏 角。钻 头切 削刃 上选 定 点 的 主偏 角是 切 削 刃 在
1 麻 花钻 的结 构 麻花钻的组成如下图所示 ,由刀柄 ( 颈部 ,尾部)和刀体 ( 切
常 用的 钻孔 刀具之 一 。它适 合加 工低精 度 的孔 。也可 用 于扩孔 。螺旋 槽有 2槽 、3槽或 更 多槽 ,但 以2槽 最 为常见 。麻 花 钻 可被 夹 持 在手 动 、电动的 手持 式钻孔 工具 或钻 床 料 一般 为 高速 工具 钢或 硬 质 合金 。本 文通 过 对 麻花 钻的 组成部 分 、几何 参数 优缺 点等进 行 分析 ,进 而提 出相应 地 改进 措施 。
麻花钻的建模及强度分析毕业设计论文

麻花钻的建模及强度分析[摘要]:采用三维建模软件建立麻花钻的三维模型,分析刀具在工作时的受力情况。
应用有限元软件对麻花钻进行模态分析,研究其结构的震动特性。
利用deform软件对麻花钻的工作过程进行模拟仿真。
[关键词]:麻花钻;三维建模;ansys分析;deform 仿真Twist drill modeling and the analysis of its intensionAbstract:This artical introduced the 3D mode ling method of twist drill and the analysis of twist drill when it behaves. Finite element software for modal analysis Twist. Deform software using process simulation work.Key Words: twist drill;ansys;deform;simulation目录目录 (I)1绪论 (1)1.1引言 (1)1.2研究背景与国内外研究现状 (2)1.3本课题的研究意义 (5)1.4本课题研究的主要工作 (5)2麻花钻切削理论基础 (8)2.1麻花钻应用到的理论基础 (8)2.1.1麻花钻的组成 (8)2.1.2麻花钻的角度 (9)2.1.3基面和切削平面 (11)2.2钻削力的计算 (12)3 麻花钻的建模 (15)3.1P RO/ENGINEER (15)3.1.1 Pro/ENGINEER的概述 (15)3.2.1创建毛坯 (15)3.2.2创建螺旋槽 (20)3.2.3创建横刃 (25)4有限元数值分析理论与ANSYS软件介绍 (31)4.1有限元方法分析过程概述 (31)4.1.1连续体的离散化 (31)4.1.2单元分析 (32)4.2ANSYS软件介绍 (32)4.2.1软件功能简介 (32)4.2.2前处理模块 PREP7 (33)4.2.3求解模块 SOLUTION (34)4.3静应力分析 (36)4.3.1 麻花钻的静应力分析步骤 (36)4.4模态分析 (45)4.4.1模态分析:模态分析的定义和模态分析介绍 (45)4.4.2 在 ANSYS 中有以下几种提取模态的方法: (46)4.4.3 模态分析中的四个主要步骤: (46)4.4.4 模态分析步骤: (46)5钻削过程的模拟仿真与DEFORM-3D软件介绍 (59)5.1DEFORM-3D软件介绍 (59)5.1.1 deform-3d软件简介 (59)5.1.2deform-3d的操作流程 (59)5.2钻削过程仿真 (63)致谢 (76)参考文献 (77)外文文献译文 (79)1绪论1.1引言切削加工是机械加工制造应用最多的加工方式之一,它可以应用在几乎所有的机械加工制造行业当中,是国民生产的重要支柱。
麻花钻磨损特性的研究

磨损带形状特征及随切削时间和切削条件的变化规律是刀具磨损理论最基本的内容。
与车、铣削刀具不同,钻头前锥的刀刃全部参加切削,其后刀面磨损区域很大,且三维分布于前锥面及与刃带相交的转角区。
为便于观测,在DIMILANO119966检测仪上用一个特制的三向夹头将主刀刃调平,使转角区、主后刀面和一部分横刃的磨损区清晰地显示在一个视图上,再测量绘制出磨损图形或直接拍照成像。
图1为试验所得麻花钻的典型磨损图形,转角磨损区呈不规则的三角形,其高(沿钻头的轴向)是钻头磨损带的最大宽度VBc,而主刀刃及横刃的磨损区为形状较均匀、宽度尺寸VB较小的条形带。
试验表明,无论钻头转速高低或在磨损过程的任意时刻,转角磨损带宽度值最大且扩展速率最快的这种图形特征总是保持不变。
更重要的是,当转速较高时,转角区及相邻小部分主刀刃磨损区的磨损性质与其余主刀刃和横刃磨损区的磨损性质有较大的差异,前者出现明显的烧伤色且规则沟痕形貌的比例减少,这是因为沿刀刃径向的切削速度梯度增大,钻头外缘的温度和摩擦速度急剧增加,热磨损(氧化、扩散磨损)成为主要的磨损形式。
图1 麻花钻后刀面的磨损图形显然,钻头整体的磨损程度以及能否继续切削不仅取决于转角磨损VBc的大小,而且与主、横刀刃磨损VB有关,并受钻削速度的影响。
在改变钻头转速n的钻削试验中,测量不能正常钻削时钻头的转角磨损和主刀刃磨损,结果如图2所示。
转速不同,钻头磨钝时的转角磨损值差异显著,且VBc值随转速的提高而增大。
如当n=1125r/min时,测得VBc=0.90mm时的钻头仍能正常切削;而同样的钻头以n=600rpm钻削时,当VBc=0.76mm时就已磨钝失效,无法继续钻削。
与之相比,转速变化对主刀刃及横刃磨损区的影响却相反。
转速较低时,钻头磨钝失效所对应的VB 值较大;转速较高时,钻头失效对应的VB值却变小,但两者的差别不大。
因此,钻削速度的提高对主刀刃及横刃磨损特性的作用并不显著,这正是钻削与车削的不同之处。
硬质合金麻花钻涂层性能试验研究
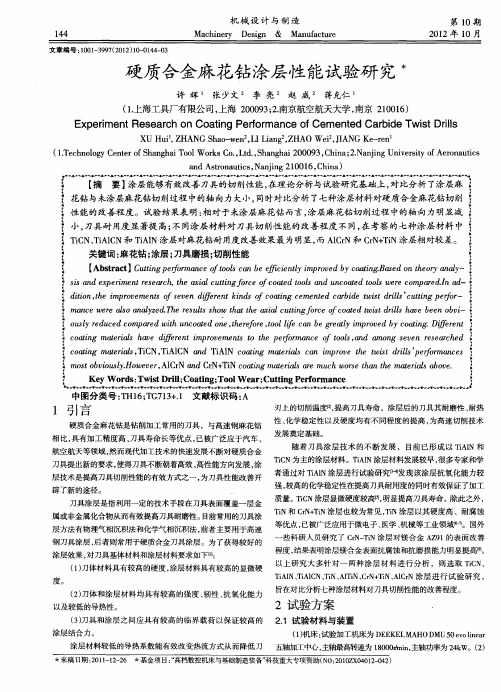
【 摘
要】 涂层 能够有效改善刀具的切削性能 , 在理论分析与试验研究基础上 , 对比分析 了涂层麻
花钻 与未涂层麻 花钻切 削过程 中的轴 向力 大小 , 同时对 比分析 了七种 涂层材 料对硬 质合金麻 花钻 切 削
性能的改善程度。试验结果表 明: 相对于未涂层麻花钻而言 , 涂层麻花钻切 削过程中的轴向力明显减 小, 刀具耐用度显著提高; 不同涂层材料对刀具切削性能的改善程度 不同, 在考察的七种涂层材料 中
mo t b i u l. we e , C N a d C N+ i o ig mae i s a e mu h w re t a e m t r s a o e s v o syHo v r A1 r r T N c a n t r r c o s h t a e i b . o n t l a n h l a v Ke o d : y W r s Twit i ; a i g; 0 e r Cu tn e f r a c s l C0 tn T0 l Dr l W a ; ti g P r o m n e
XU Hu Z i HANG S a - e L in- Z 。 h o w n , ILa g , HAO W e JANG Ke rn z i,I —e
( . c n l yC ne h nh i ol rs o,t. h n h i 0 0 3 C ia 2N nigU i r t eo at s 1 e h oo e t o S a g a T o Wok . d, ag a 2 0 9 , hn ;.a j nv syo A rn ui T g rf C L S n ei f c a dA t n uisN nig2 0 1 ,hn ) n s o at , aj 1 0 6 C ia r c n
整体硬质合金刀具关键工步磨削工艺实验的研究

11500
茕
曩1000
5D0
磨莉次戢
(c)轴向磨削力
图414初步过程实验磨削力实验结果
由上图4.14可以看出,随着磨削次数的增加.磨削力逐渐增大,但增大的幅度很小。
对于砂轮线速度v。
=30m/s与v。
=60rals这两组参数,第一次的磨削力数值基本接近,但随着磨削次数的增加,v,f30m/s的磨削力基本保持不变,而vs=60m/s的磨削力却逐渐增大,从而v,=30m/s较v。
=60m/s具有更好的磨削稳定性。
4.242系统过程实验
由4.2.4.1中对初步过程实验的实验结果进行分析,选择v:=16m/s、vw=55mm/min、ah-2mm与h=30m/s、Vw=1lOmm/min、口^-2ram这两组磨削参数进行大量磨削实验,并对实验结果进行深入分析。
其实验结果如下。
(1)表面形貌
a)第l攻磨削后(b)第10次磨削后。
整体硬质合金麻花钻常用槽型性能实验研究
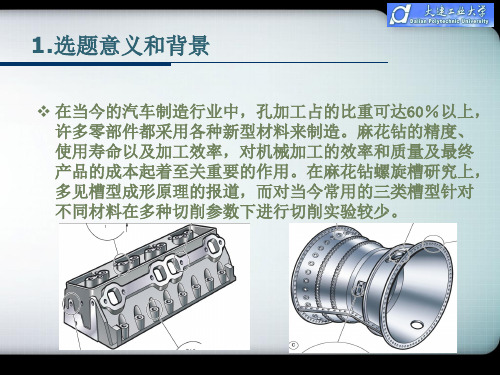
2.麻花钻螺旋槽作用
Company Logo
螺旋槽直接形成钻头的前刀面,影响钻头的容屑及排屑能 力,螺旋槽与钻头的后刀面(后刀面为双平面)相交形成 钻头的主切削刃直接控制钻头法前角的大小及分布,从而 直接影响钻头的切削性能。在钻削过程中,钻身承受着钻 削力,从钻孔中排出钻屑,同时随切屑、冷却液及钻身将 切削热挥发出去。
凹型槽
46 14.2 30° 加工测量 2.09 105.5° 4.1 15.24
误差 -0.47% 0.95%
0.59% -0.58%
7.主切削刃形状
Company Logo
8.三种槽型的切削实验
Company Logo
机床:美国HASS VOP-D VF5型加工中心主要性能 参数:最高钻速8000rad/mim;功率 20马力;直线 分辨率 0.001mm
2500mm/min 0.15mm/r、
2500mm/min 0.2mm/r
四种切削参数下分别加工三种不同材料,这三种材料分别 为HT200(铸铁)、42crmo(合金钢)、 1cr18ni9ti(不锈钢)三种材料,测量扭矩和轴向力。 后面将分析切屑
9.轴向力对比
Company Logo
1.选题意义和背景
Company Logo
在当今的汽车制造行业中,孔加工占的比重可达60%以上, 许多零部件都采用各种新型材料来制造。麻花钻的精度、 使用寿命以及加工效率,对机械加工的效率和质量及最终 产品的成本起着至关重要的作用。在麻花钻螺旋槽研究上, 多见槽型成形原理的报道,而对当今常用的三类槽型针对 不同材料在多种切削参数下进行切削实验较少。
13.凹型槽的改进
Company Logo
加工材料:合金钢 切削速度:62.8m/min
硬质合金切削工具材料性能研究
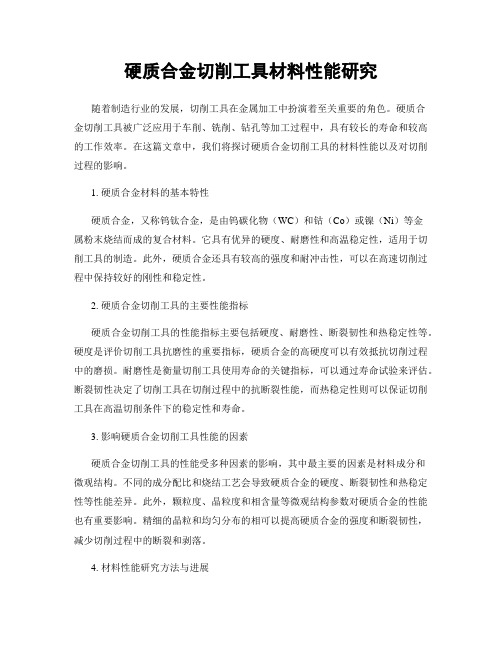
硬质合金切削工具材料性能研究随着制造行业的发展,切削工具在金属加工中扮演着至关重要的角色。
硬质合金切削工具被广泛应用于车削、铣削、钻孔等加工过程中,具有较长的寿命和较高的工作效率。
在这篇文章中,我们将探讨硬质合金切削工具的材料性能以及对切削过程的影响。
1. 硬质合金材料的基本特性硬质合金,又称钨钛合金,是由钨碳化物(WC)和钴(Co)或镍(Ni)等金属粉末烧结而成的复合材料。
它具有优异的硬度、耐磨性和高温稳定性,适用于切削工具的制造。
此外,硬质合金还具有较高的强度和耐冲击性,可以在高速切削过程中保持较好的刚性和稳定性。
2. 硬质合金切削工具的主要性能指标硬质合金切削工具的性能指标主要包括硬度、耐磨性、断裂韧性和热稳定性等。
硬度是评价切削工具抗磨性的重要指标,硬质合金的高硬度可以有效抵抗切削过程中的磨损。
耐磨性是衡量切削工具使用寿命的关键指标,可以通过寿命试验来评估。
断裂韧性决定了切削工具在切削过程中的抗断裂性能,而热稳定性则可以保证切削工具在高温切削条件下的稳定性和寿命。
3. 影响硬质合金切削工具性能的因素硬质合金切削工具的性能受多种因素的影响,其中最主要的因素是材料成分和微观结构。
不同的成分配比和烧结工艺会导致硬质合金的硬度、断裂韧性和热稳定性等性能差异。
此外,颗粒度、晶粒度和相含量等微观结构参数对硬质合金的性能也有重要影响。
精细的晶粒和均匀分布的相可以提高硬质合金的强度和断裂韧性,减少切削过程中的断裂和剥落。
4. 材料性能研究方法与进展研究硬质合金切削工具材料性能的方法主要包括实验测试和数值模拟。
实验测试可以通过切削试验、硬度测试、显微镜观察等手段来获取硬质合金的性能数据。
数值模拟则通过计算机模拟切削过程中的材料应力、变形和热传导等物理过程,预测硬质合金切削工具的性能。
近年来,基于人工智能和机器学习的模型也逐渐应用于硬质合金材料性能研究中,提高了研究效率和准确性。
5. 切削工具性能改善的途径为了改善硬质合金切削工具的性能,研究人员采取了多种途径。
麻花钻结构参数及刃磨方法的研究(毕业论文钻头部分)
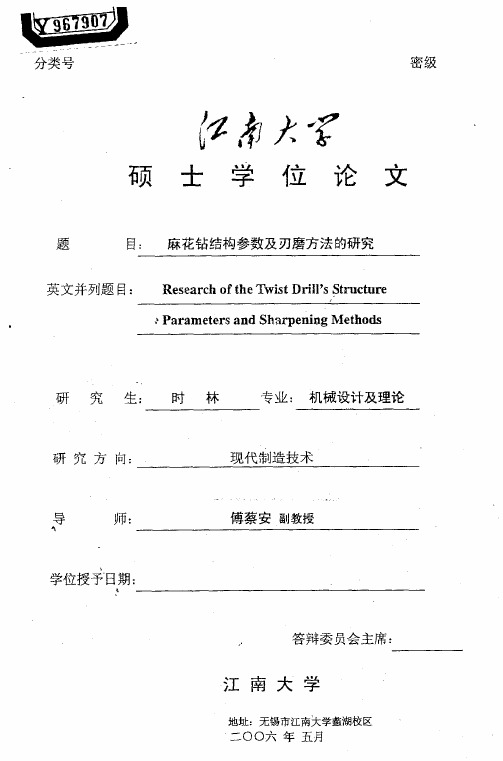
江南大学十学位论文2.1引言第二章螺旋前刀面方程的推导麻花钻的前刀面一一即螺旋槽表面,是切屑沿着流出的表面。
切削刃上任一点的前角是这一点的基面与前而(或前面的切平面)之间的夹角。
”。
在麻花钻钻削过程中,各切削刃及前、后刀面会出现磨损或破损的情况,或者为了适麻不同的加工材料,要改变某些角度或钻头的形式,这时就要求对麻花钻进行修磨,比较常见的就是对麻花钻后刀而进行修磨。
然而,我们在对麻花钻后刀面进行修磨之后,其土刀刃为前刀面和后刀面的交线,如果没有前刀面方程,我们就无法求出修磨后主刀刃的方程,也就无法求出沿主刀刃上各点处的后角的大小,因此,必须要建立起前刀面的方程。
经翻阅相关资料,虽然有些文中给出了前刀面的方程,但并未指出是在一个什么样的坐标系下建立的方程,也没有给出前刀面方程的推导过程,而且各种资料中的前刀而方程不尽致。
为此,本文在研究麻花钻前刀面的性质后,建立了麻花钻前刀面的数学模型。
2.2前刀面的数学建模麻花钻前刀面如图2.1所示,这个前刀面足一个螺旋面,是由过直线刃上一系列等螺距的螺旋线组成。
图2.1麻花钻前刀面根据这个原理,建立了其数学模型,其过程如r图2.2中相关符号的说明:R——麻花钻的半径“直线刃上任一点的、卜径第七章其于Pro/E的麻花钻前、后刀面的参数化建模机器刃磨参数的优化7.2.1直线主刀刃及轴线绘制—1Od0i一.图7.1生成钻头轴线和直线刃b蕊秘毽鼬鲻’一‘一州崮F¨eEdnlnsert眦nniesShow日a品电Bxl舻I扣嘲国=?F团国{——CurrentComext—叫I口sz嘲ss]I湖m_sd0=sqrtl瞰R-Rc’Rc)Aanl59)■l-_-*1^1¨TⅢ-厂五]勋setIcance-l引呷llIU娥l』江南大学士学位论文图7.8生成砂轮然后,将圆锥母线E绕其轴线F旋转900生成一个圆锥砂轮s1,由此砂轮磨出的后刀面后角为O度,为了使刃磨出的后刀面有后角,将此砂轮绕一个由点1指向点11的向量旋转一个角度a(在模型中没茕为afa),生成另一个砂轮S2。
- 1、下载文档前请自行甄别文档内容的完整性,平台不提供额外的编辑、内容补充、找答案等附加服务。
- 2、"仅部分预览"的文档,不可在线预览部分如存在完整性等问题,可反馈申请退款(可完整预览的文档不适用该条件!)。
- 3、如文档侵犯您的权益,请联系客服反馈,我们会尽快为您处理(人工客服工作时间:9:00-18:30)。
Company Logo
实验说明
为验证三种槽型钻头的性能,对三种槽型的钻头进行对比 试验。让三种槽型钻头在 切削速度 进给量 1500mm/min 0.15mm/r、 1500mm/min 0.2mm/r、 2500mm/min 0.15mm/r、 2500mm/min 0.2mm/r 四种切削参数下分别加工三种不同材料,这三种材料分别 为HT200(铸铁)、42crmo(合金钢)、 1cr18ni9ti(不锈钢)三种材料,测量扭矩和轴向力。 后面将分析切屑
Company Logo
Hale Waihona Puke 展望 本论文通过实验来验证三种槽型的性能,希望能够对加
工铸铁、合金钢和不锈钢的企业有所帮助。但是如果要把 螺旋槽研究透彻,还需要大量的工作要做。 随着刀具技术的高速发展,槽型前部的形状也不在局限于 以上所研究的三种,而有了更多的变化,需要后面的工作 者再加以研究。 凹型槽弯曲的趋势也不完全相同,有大有小,可能这也会 有不同的性能,需要再加以研究。
倒棱深度 0.15~0.25 0.25~0.35 0.35~0.45 0.45~0.55 0.55~0.65
φ21~26mm
0.65~0.75
Company Logo
结论
与直线型、凸型螺旋槽相比,凹型槽在轴向力和扭矩的值 整体上是最低的,切屑的形状也是非常好的,凹型槽在加 工HT200,42CrMo,1Cr18Ni9Ti是比直线型和凸 型好些。但凹型槽的钻头由于径向前角过大,在高进给穿 透工件时容易崩刃。这时就需要在槽型周刃上加工一个保 护倒棱,就是让凹型槽的径向前角为负,这种边缘负角的 设计,可以有效抑制高进给穿透工件时造成的崩刃。
加工测量
2.09 105.5° 4.1 15.24
误差
-0.47% 0.95% 0.59% -0.58%
Company Logo
7.主切削刃形状
8.三种槽型的切削实验
Company Logo
机床:美国HASS VOP-D VF5型加工中心主要性能 参数:最高钻速8000rad/mim;功率 20马力;直线 分辨率 0.001mm 测量装置:使用压电式测量仪。该测量仪主要有三个压 电式二维力传感器组成,可测量轴向力力和钻削扭矩。
Company Logo
9.轴向力对比
10.扭矩对比
Company Logo
Company Logo
11.切屑对比
加工材料:1Cr18Ni9Ti(不锈钢) 切削速度:62.8m/min 进给量:500mm/min 孔深:20mm 使用设备: 美国HASS VOP-D VF5型加工中心
Company Logo
Company Logo
2.麻花钻螺旋槽作用
螺旋槽直接形成钻头的前刀面,影响钻头的容屑及排屑能 力,螺旋槽与钻头的后刀面(后刀面为双平面)相交形成 钻头的主切削刃直接控制钻头法前角的大小及分布,从而 直接影响钻头的切削性能。在钻削过程中,钻身承受着钻 削力,从钻孔中排出钻屑,同时随切屑、冷却液及钻身将 切削热挥发出去。
Company Logo
3.螺旋槽数学模型
螺旋槽数学模型
Company Logo
4.双平面后刀面数学模型
后刀面数学模型
Company Logo
5.典型槽型的提出
Company Logo
6.螺旋槽的测量
凹型槽 中心距 偏心距 螺旋角 软件仿真 芯厚 螺旋槽圆周角 刃背宽 螺旋槽长
2.1 106.5° 4.076 15.33 46 14.2 30°
凸型槽
直线型 槽 凸型槽
-18°
0° 17°
Company Logo
13.凹型槽的改进
Company Logo
加工材料:合金钢 切削速度:62.8m/min 进给量:500mm/min 孔深:20mm(通孔) 使用设备:日本牧野数控机床
工件直径 φ2~3mm φ4~5mm φ6~7mm φ8~12mm φ13~20mm
加工材料:42CrMo(合金钢) 切削速度:62.8m/min 进给量:500mm/min 孔深:20mm 使用设备: 美国HASS VOP-D VF5型加工中心
Company Logo
12.径向前角的定义
8mm直径的测量深度L为0.4-0.5,径向前角对切削的影响,径向 前角的大小影响切屑的形状和大小
Company Logo
1.选题意义和背景
在当今的汽车制造行业中,孔加工占的比重可达60%以上, 许多零部件都采用各种新型材料来制造。麻花钻的精度、 使用寿命以及加工效率,对机械加工的效率和质量及最终 产品的成本起着至关重要的作用。在麻花钻螺旋槽研究上, 多见槽型成形原理的报道,而对当今常用的三类槽型针对 不同材料在多种切削参数下进行切削实验较少。