IE与效率提升培训课件
美的IE现场培训-IE效率提升技法PPT58页课件
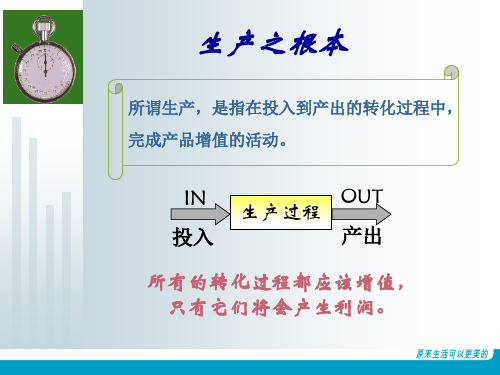
自我问答:为何曾发生?是否有再发防止的措施?
2、加工的浪费
内容:即过分加工的浪费, (1)多余的加工和过分精确的加工。 例如实际加工精度过高造成资源浪费。 (2)需要多余的作业时间和辅助设备,还要增加生产用电、 气压、油等能源的浪费,另外还增加了管理的工时。
按照过去的管理理念,人们认为库存虽然是不好的东西,但却是必要的。精益生产的观点认为,库存是没有必要的,甚至认为库存是万恶之源。
库存掩盖问题
故障
不良品
调整时间长
点点停
能力不平衡
品质不一致
计划有误
缺勤
协作问题
运输问题
水平线
6、制造过多(早)的浪费
内容:流程阻碍,不良的发生、库存,半成品的增加,材料、 零件的滥用,资金周转率下降,计划柔软性的阻碍。
只要条件允许,工具和物料应放在预先确定的位置。
尽可能采用“下坠式”传送方式。
在所有的操作中,可以不用手的场合,尽量不用。
物料和工具应放在能获得最好的动作顺序的位置,使手的动作 简便而有节奏。
减少或消除骤然和急剧改变方向的、曲折的或直接往复的动作, 采用流畅和连续的动作。
三角形原理
物料(或工具)放置点、产品组装点、操作者手的位置形成的三角形的边长越小越好。
提出问题无人处理
检验指导书不完善
无检验标准
流程问题
来料不良
人员操作
设备故障多
库存时间长
采购过多
质检没有发现
要因分析图(鱼骨图)
生产品质
要因解析的方法(三)
突发性不良、慢性不良、周期性不良
上限
下限
如何运用IE手法提升生产效率(PPT)

1、测出各工序的实际(shíjì)作业时间
5.3 对耗时较短的工序采取:
2、制作(zhìzuò)平衡分析图
.分割作业,移动局部到
3、计算生产不平衡损失时间
耗时较短的工序
4、计算生产平衡率及损失率
.从耗时长的工序移动局部
5、分析和改进:
.
作业过来;
5.1 作业改善的根本原那么〔ECRS)
5.2 对耗时较长的工序采取:
车床区进出(j码ìn头chū)货组装区
铣床(xǐchuáng)磨区钻床床区(zuàn chuáng)区
功能式:适用于种类多、数量少的个别生产。
第三十三页,共八十七页。
4.3 工厂布置的根本形式
原料(yuánliào)
成品(chéngpǐn)
原料(yuánliào)
成品
流程式:适用于数量多、重复的流水线生产。
4.常常(chángcháng)为「无法做」找理由,不如以「如何做」「為何不能做」而想方法。
5.经常的提出「为什么?为什么?为什么?」的问题意识,找出根本原因. 6.只要目前的工作稍有改善,就有所获了;不求完美,馬上去做. 7.切勿有「小小的改善有什么用?」的观念。
8.從不花錢的項目開始改善.
9.小小的巧思,可能就是改善的开始。
品保人员的巡回检查 (制程稽核)
停机检查 or 不停机检查
检查工程、检查数量
:
第二十三页,共八十七页。
3.5 搬运(bānyùn)的浪费与防治
进出库作业
生产作业中搬運
制令变更-换线
设计变更-材料更换
经济生产批量
工厂 布置
(gōngchǎng)
:
第二十四页,共八十七页。
如何利用IE提升效率ppt课件
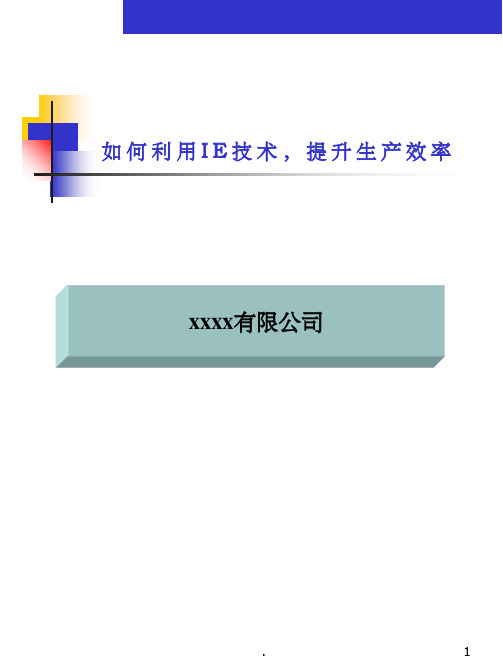
.
11
时间计划
X月X
待定
待定
待定
提交建 议书
课程设计 进一步确认需求
培训实施
提交培训报告
.
12
投资
为了达成理想的培训效果,可以提供下列服务: 培训调研
部分关键的工艺人员,生产管理人员
培训实施 ( ?人左右)
如何利用IE技术提高生产效率
1天
培训报告
天
培训投资:
元/天
为此培训发生的交通食宿费用由贵司按实际支付
辅导案例:
1.TCL集团XX公司 其主要产品是液态和固态锂离子充电电池。通过一年的辅导和 改善,其生产流程从2805米缩短到480米,单块电芯的生产工时由176分钟缩短到28分 钟,交货周期由36天缩短到5天。由于改善成果显著,客户对顾问的工作十分满意, 并为顾问颁发了特别的奖励。(见图片)。
董事长在晚会前颁奖牌
.
13
为什么选择我们
1. 我们的工作方法可以深刻客户的需求
2. 本次培训以结果为导向,对IE中的实用方法和 工具将在培训中研讨和总结,对公司实际的工 作有借鉴意义
3. 讲师有为多家企业提供IE 咨询和培训的经验, 对IE有深刻理解,将与学员一起分享
4. 讲师多年年的培训行业经验和在此领域内的丰 富实践案例,为TCL、万源德密封、龙大等企 业提供IE 的咨询和培训。
.
9
工作流程
(续…)
➢ 培训实施
➢ 汇报和总结 • 提交培训报告 • 和管理层总结培训的效果 提交的报告包括: a)培训主要理念 b)培训学员的评价 c)学员的后期行动计划 d)学员反馈(问题,挑战,进一步需求) e)在培训中开发的“实用方法和工具”的展示
应用IE技术提高生产效率课件(PPT62张)
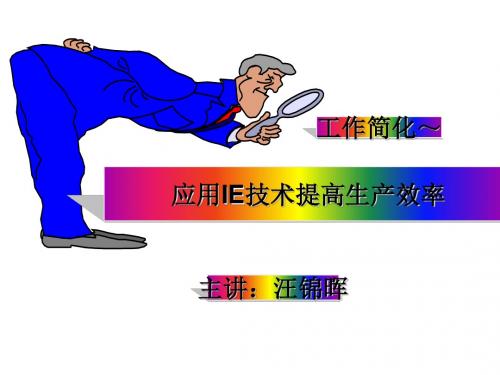
工作简化的目的
积极性
管理
人员
缩短工时 提高效率 轻松愉快
工作 简化
机器
尽量有效 使用每一 机器能力 工作简化的
原料
改善材料 之种类用 量及供应
对象
工作简化的
目标
工作简化的
有效地
生产
结果
生产资源管理的 + 4M 1I
4.METHOD
管制:装配线 、作业标准
RMATION
管制:信息\可见性管制 例:指导表、REPORT、 CONTROL CHART
动作
+
A
程序
组合
工 作
B
操作或制
造方法不 当所产生
C
管理不良
而增加的 无效时间
D
工人自己 本身的问 题增加的
基本工作量
产品设计
或规格不 良所产生
的无效工
作量
的无效工
作量
无效时间
动作经济原则~量具
题 发 掘
问
建
立
新 方
法
动作经济原则22条
一、关于人体的运用: 1-双手应同时开始,并同时完成其动作
2-除规定时间外,双手不应同时空闲
画上样子 30秒钟 拿起木板 送到锯处(30米)
5 6 7 3
3 1
图例
多段作业程序组合工作的表示
泵及接受器之装箱 接受器
3 加工检查 5 缚札 6 附标签
泵
2 全部检查 2 打印号码
箱子
1 内部检查 1 装保护衬里 3 放入泵 4 放装箱衬片
7 放入接受器
8 封闭盖
4 过称
成 品 出 货 流 程 ﹁ 客 户 现 款 提 货 ﹂
IE及效率提升培训

IE及效率提升培训1. 简介IE(Information Engineering)是一种以信息为核心,以实施信息系统为目标的工程方法,旨在通过规划、分析、设计、构造和支持整个信息系统的生命周期,提高信息系统的开发效率和质量。
IE同样适用于提升个人和团队的效率,通过学习和应用IE的方法论,可以在工作和生活中取得更好的成果。
本文将介绍IE的基本概念和原理,并讨论如何通过学习和实施IE方法来提升个人和团队的效率。
2. IE的基本概念和原理2.1 信息系统的生命周期信息系统的生命周期包括需求分析、系统设计、系统构造、系统测试和系统支持五个阶段。
在每个阶段中,IE提供了一套系统化的方法和工具,帮助开发人员和团队完成各项任务。
2.2 IE的核心原则IE的核心原则包括以下几个方面:2.2.1 信息为核心IE以信息为核心,将信息视为组织的重要资产,通过对信息进行分析、组织和应用,提升组织的竞争力和效率。
2.2.2 系统化方法IE提供了一套系统化的方法和工具,帮助开发人员和团队规划、分析、设计、构造和支持信息系统。
这些方法和工具包括数据流图、实体关系图、状态转换图等,能够有效地提高开发效率和质量。
2.2.3 面向目标IE的方法和工具都是以实施信息系统为目标,旨在解决业务问题和需求,并提升组织的效率和竞争力。
3. 学习IE的方法和工具3.1 数据流图数据流图是IE中常用的一种工具,用于描述信息系统中数据的流动和转换过程。
通过绘制数据流图,可以清晰地了解数据的来源、流向和处理过程,从而更好地进行需求分析和系统设计。
3.2 实体关系图实体关系图用于描述不同实体之间的关系,包括实体的属性和实体之间的关联关系。
通过绘制实体关系图,可以帮助开发人员和团队建立清晰的数据库模型,便于后续的系统构造和数据管理。
3.3 状态转换图状态转换图用于描述系统或对象在不同状态之间的转换过程。
通过绘制状态转换图,可以清晰地了解系统或对象的行为和状态变化,有助于进行系统设计和测试。
IE培训教材(PPT 47页)

动作经济原则
3、 机械设计原则
a、用夹具固定产品及工具 b、使用专用工具 c、合并两种工装为一种 d、提高工装设计的便利性,减少疲劳 e、机械操作动作相对稳定,操作程序流程化、标准化 f、操作程序与作业程序配合
Working Sampling (作业取样 )举例
Working Sampling (作业取样 )举例
• 设定、重设:8% • 测定:12% • 搬运:10%
• 待料:34% • 停机:15% • 停工(设备故障):15% • 清扫:6%
Working Sampling (作业取样 )举例
Time study
一些术语的界定
•净作业测试时间(Cycle Time):
----------指在无干扰下完成某一工序的时间;
IE是对人员、物料、设备、能 源和信息所组成的集成系统进行设 计、改善和设置的一门学科。
IE basic function(IE 基本功能)
IE的基本职能
规划
设计
评价
创新
企业(微观)
业务发展规划 业务扩充规模 新产品开发规划 技术革新规划 成本降低规划 产品系列化计划 产品标准化计划 产品、工艺专业化计划
2.IE是什么?
丰田的秘密(丰田生产方式)
当日本经济还处在漫长的、不见出口的隧道 之中时,丰田却取得了赢利一万多亿日元的惊人 成绩。其中一个主要原因是丰田有『赚钱的IE』 。
2.IE是什么?
精益生产的典范——戴尔
戴尔一生的目标就是把公司所有业务效率提高到极致。
2.IE是什么?
美国工业工程师学会的定义
2.IE是什么?
历史人物
时间研究之父——泰勒
成本减少 收入增加
IE生产效率提升课件(PPT 43张)

什么是工业工程
工业工程的核心技术——工作研究 可以分析工作效率的各种影响因素,帮助企 业挖掘、革新、消除人力、物力、财力和时 间方面的浪费,合理安排作业,减轻劳动强 度,用新的更为合理的作业方法替代旧的不 良的作业方法,并制定作业标准,从而提高 劳动生产率。 制定标准方法和标准时间的技术 包括方法研究和作业测定两项内容
沙布利克分析与作业改善
2. 动作要素解释 ① 第一类动作 (1)空手(Transport Empty)…… A. 把手伸向某一目的物。 B. 把目的物放到某一场所后,再把手放回原来 的位置。 (2)抓(Grasp)……∩ 抓住螺丝刀。 抓住杯子。
沙布利克分析与作业改善
(3)搬运(Transport Loaded)…… A. 搬运 B. 压、推 C. 使之滑动 D. 拉、拖 E. 转送 (4)修正位置(Position)…… 9 为了使目的物适合于一动作的需要,必须 进行位置的修正或改变拿法的动作。
工程分析概述
何谓工程分析 对工程加以分析、调查,找出其中 浪费、不均匀、不合理的地方,进而进 行改善的方法,称之为工程分析。 工程分析的目的 1. 对现有工程进行改善 2. 建立新的工程体系 工程分析的种类
工程分析的记号 1. 基本记号
工程分析概述
工程分析概述
3. 基本记号的组合
工程分析概述
沙布利克分析与动作改善 1. 沙布利克分析的基本步骤(图表2)
沙布利克分析与作业改善
2. 运用分析结果进行改善 沙布利克分析的重点,在于消除第三类动作,尽量减少第二类动 作,有可能的话也要对第一类动作进行简化。 观察分析表中第三类动作的比例,寻找消除或减少的方法 图表3
①
IE与效率提升培训课件(ppt 99页)

三、作业流程分析
作业流程分析的实施步骤
四、联合作业分析
定义:通过图表的形式分析人与设备、人与 人之间的组合作业时间流程样式,找出人或 及其在作业中因作业流程不顺畅而产生的浪 费,从而达到有效改善作业流程的目的。
目的:暴露作业流程中的不合理现象,从而 发现作业中因不均衡、不合理而导致的浪费, 通过改善,达到用更少的作业员、更短的时 间,使作业员在作业负荷均等的情况下有效 完成工作任务。
目的:在分析过程中通过对各工序的作业内 容、使用设备工装、作业时间及搬运距离的 调查记录和分析,发现生产流程中存在的问 题,并进行有效的改善,消除生产过程中的 不合理和浪费。
二、产品工艺分析
工艺流程基本符号
作业者
机械
单独
与设备及其他作业者 无时间关系的操作
自动
与操作者无关,自动 工作的状态
联合
设备与人共同作业, 相互制约作业时间
时间研究 完成工作时间分析
6
工作抽样 调查操作者或机器效率
7 预定时间标准 制订标准工时
二、工业工程的来历
工业工程发展简历
二、工业工程的来历
工业工程发展简历
二、工业工程的来历
工业工程之父
二、工业工程的来历
工业工程之父
二、工业工程的来历
“美国在世界上值得夸耀的东西就 是IE。美国之所以打胜第一次世界 大战,又有打胜第二次世界大战的 力量,就是因为美国有IE。”
14
半成品 13 存放处
12
热处理
11
半成品 存放处
半成品 10 存放处
机加工
15
半成品 存放处
16
检查点
17
成品存 放处
半成品
- 1、下载文档前请自行甄别文档内容的完整性,平台不提供额外的编辑、内容补充、找答案等附加服务。
- 2、"仅部分预览"的文档,不可在线预览部分如存在完整性等问题,可反馈申请退款(可完整预览的文档不适用该条件!)。
- 3、如文档侵犯您的权益,请联系客服反馈,我们会尽快为您处理(人工客服工作时间:9:00-18:30)。
某轮毂制造企业车间布局(改善前)
建筑外墙
精益生产中最为推崇的布局
——流程性布局
钻孔
4 3
X光检查
2
压铸设备
1
熔铸炉
铝锭存放处
半成品
存放处
5
热处理
6
半成品 存放处
7
机加工
8
检查
9
原生产场地 (现为节省空间)
成品库
原成品库 (现为节省空间)
某轮毂制造企业车间布局(改善后)
建筑外墙 传送带
三、柔性生产(布局角度)
五、布局常用的分析工具
布局成本函数 来往矩阵分析法 工作相关图法 综合因素矩阵分析法
布局成本函数
n为工作中心或部门的总数量; i,j为各部门; Xij为从部门i到部门j物品流动的数量; Cij为一件物品在部门i和部门j之间流动的成本。
来往矩阵分析法
利用图表列出及其或设备之间的相对位置, 以对角线元素为基准计算工作地之间的相对距离, 从而找出整个生产单元物料总运量最小的布置方 案。
——质量管理权威朱兰博士
二、工业工程的来历
IE
制
造
强 ,
第二章
中
国 强
布局分析
,
管
理
改
变
中
国
布局是指为高效率生产,安排生产作业单位 和设施的相对位置与面积、车间内部生产设备 的布置相对应,以达到人和物流顺畅的目的, 更是为了激活公司内部物流,缩短生产组织的 时间。
布局必须是管理理念先行,否则,以后的优
混合生产 不同型号的产品在同一场所、同一生产线可以 同时进行生产。
固定+变动生产 生产量M=基本量x+变动量α
细胞式的柔性生产 生产量M=最小生产单位*n
四、布局的经济性原则
相邻原则 充分利用立体空间 统一原则 最短距离原则 物流畅通原则 减少存货原则 便于信息的流动原则 安全满意原则 灵活机动原则 环境和美观
7 预定时间标准 制订标准工时
二、工业工程的来历
工业工程发展简历
二、工业工程的来历
工业工程发展简历
二、工业工程的来历
工业工程之父
二、工业工程的来历
工业工程之父
二、工业工程的来历
“美国在世界上值得夸耀的东西就 是IE。美国之所以打胜第一次世界 大战,又有打胜第二次世界大战的 力量,就是因为美国有IE。”
插床 16.9 0.6 1.2 4.6 2.2
单位距离每月总运输成本(单位:元)
锯床 磨床 冲床 钻床 车床 插床
锯床
44.9③ 86.2① 2.3 10.8 22.4
磨床
10.7 63.9② 8.8
3.8
冲床
11
7.2
5.5
钻床
32.9④ 12.7
车床
29.7⑤
插床
来往矩阵分析法
From—To矩阵分析结果
锯床 ③ 磨床
① 冲床 ② 钻床
⑤ 插床 ④ 车床
工作相关图法
工作相关图法分析
1、总经理 2、王女士 3、事务室 4、秘书 5、事务室入口 6、文件柜 7、设备间 8、影印室 9、文具贮存室
I
U
A
A
I
I
O
I
I
I
A
U
A
E
O
O
E
E
U
O
U
EE
U
U
A
O
O
U
I
O
X
UEA
I
代号 A E I O U X
亲切程度 绝对重要 特别重要
精益生产中最为推崇的布局
——流程性布局
半成品 存放处
14
半成品 13 存放处
12
热处理
11
半成品 存放处
半成品 10 存放处
机加工
15
半成品 存放处
16
检查点
17
成品存 放处
半成品
5
存放处
钻孔
9
X光检查
半成品 8 存放处
7
6 半成品 存放处
熔铸炉
1
铝锭存放处
压铸设备
2
18
4
半成品存放处
3
检查点
成品库
锯床 磨床 冲床 钻床 车床 插床
锯床
0.12 0.12 0.13 0.11 0.13
磨床 0.15
0.12 0.11 0.11 0.11
冲床 0.12 0.12
0.11 0.11 0.12
钻床 0.15 0.12 0.12
0.11 0.12
车床 0.13 0.15 0.13 0.12
0.11
插床 0.13 0.13 0.13 0.11 0.11
重要 一般 不重要 不予考虑
综合因素矩阵分析法
布局综合因素分析矩阵表
方案A 方案B 方案C 方案D 方案E
来往矩阵分析法
设备间月平均移动次数矩阵(单位:次)
锯床 磨床 冲床 钻床 车床 插床
锯床
166 350
6 76 42
磨床 167
54 381 21 25
冲床 368 35
32 50 33
钻床 11 165 65
255 74
车床 8 51 6 21
250
插床 130
5 10 38 20
单位距离运输成本矩阵(单位:元)
来往矩阵分析法
单位距离每月运输成本(单位:元)
锯床 磨床 冲床 钻床 车床 插床
锯床
24.9 42 0.9 9.9 5.5
磨床 20
6.5 45.7 3.2 3.3
冲床 44.2 4.2
3.8 6.5 4.3
钻床 1.4 18.2 7.2
30.6 8.1
车床 0.9 5.6 0.7 2.3
27.5
制
造
强
,
中 国
IE与效率提升
强,管源自理改变中
国
目录
第一章 工业工程在制造行业的应用 第二章 布局分析 第三章 程序分析 第四章 价值流程分析 第五章 标准时间的设定 第六章 时间模特法 第七章 流水线平衡度分析 第八章 设备效率与快速模 第九章 IE改善步骤
制 造
第一章
强
, 中
工业工程在制造
产出 OUTPUT
产品或服务
检 出 测 定
IE研究的工作系统
一、工业工程的定义
IE七大手法详解
序号
名称
内容简介
1
程序分析 整个制造程序分析
2
操作分析 人机操作分析、联合操作分析
3
动作分析 人动作分析与动作经济性
4
作业测定 按照标准完成基本工作所需的时间
5
时间研究 完成工作时间分析
6
工作抽样 调查操作者或机器效率
国
强 ,
行业的应用
管
理
改
变
中
国
一、工业工程的定义
“工 永程 ‘远师 变不座 化变右 ’的铭 ”是:
IE
定义:IE的本质就是不断追求以更安全、更舒适、更经济、 更快速、更好的品质去完成工作。
一、工业工程的定义
输入 INPUT
材料
反 馈 调 整
转换条件
设备、能源 人的力量 变换方法
布局
评价尺度
时间[T] 品质[Q] 成本[C]
化、改善、统计是“捡了芝麻丢了西瓜”
一、布局理念
激活公司内部物流 “流水不腐”
缩短生产实物流时间 材料回转率 制造周期 成品回转率
二、布局常见的形式
1、集约式布局
二、布局常见的形式
2、流程性布局
二、布局常见的形式
3、固定布局
二、布局常见的形式
4、混合布局
1)集约式布局+流程性布局 2)集约式布局+固定布局 3)流程性布局+固定布局 4)集约式布局+流程性布局+固定布局