注塑机设计
机械设计中的注塑机设计

机械设计中的注塑机设计注塑机是一种常见的机械设备,被广泛应用于工业生产中的塑料制品制造过程中。
机械设计中的注塑机设计是一个复杂而关键的任务,需要考虑多方面的因素。
本文将从材料选择、结构设计、加工工艺等方面对机械设计中的注塑机设计进行探讨。
1. 材料选择注塑机设计的第一步是选择合适的材料。
注塑机通常需要承受较大的压力和摩擦力,因此需要选择具有良好机械性能和耐磨性的材料。
常见的材料包括工程塑料、合金钢等。
在选择材料时,还需要考虑环境因素和成本因素。
2. 结构设计注塑机的结构设计是保证其正常工作的重要一环。
在结构设计中,需要考虑注塑机的整体刚性、减少振动、提高稳定性等因素。
注塑机通常由注射系统、射出系统、保压系统、冷却系统等多个组成部分组成。
每个部分的设计都需要经过精确计算和合理布局,以确保注塑机的高效运行。
3. 加工工艺注塑机设计中的加工工艺对产品质量和生产效率有着重要影响。
在注塑机设计中,需要考虑加工时的温度、压力、速度等参数的控制。
这些参数的合理控制可以保证塑料熔化、注射、冷却等过程的顺利进行,从而确保产品的精度和质量。
4. 安全设计在机械设计中,安全始终是一个重要的考虑因素。
注塑机设计也不例外,需要遵循相关的安全规范和标准。
例如,注塑机应该具备防护装置,以避免操作人员的意外伤害。
此外,还需要考虑火灾、泄漏等事故的防范和应急处理措施。
5. 自动化设计随着科技的发展,注塑机的自动化程度越来越高。
自动化设计可以提高生产效率,减少人为操作错误的风险。
在自动化设计中,可以利用传感器、控制系统等设备,实现对注塑机各个环节的自动化控制和监测。
总结:机械设计中的注塑机设计是一项复杂而关键的任务,需要综合考虑材料选择、结构设计、加工工艺、安全设计和自动化设计等多个方面的因素。
只有在合理设计的基础上,注塑机才能高效运行,生产出优质的塑料制品。
通过不断的创新和优化,注塑机设计将为工业生产带来更多的便利和效益。
注塑机液压系统回路i设计
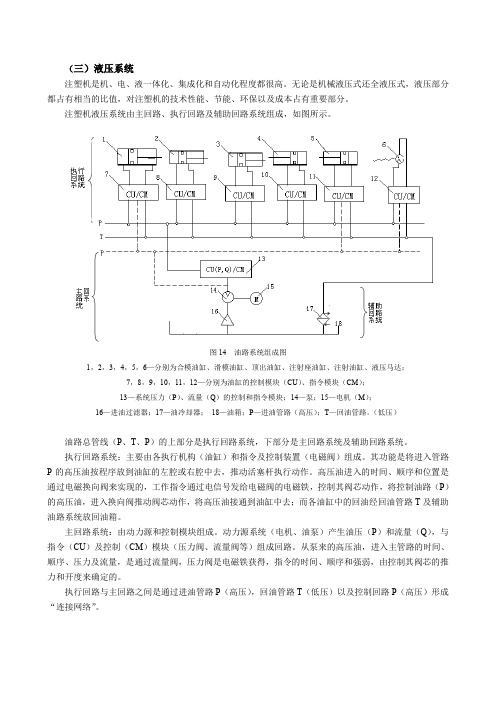
注塑机是机、电、液一体化、集成化和自动化程度都很高。
无论是机械液压式还全液压式,液压部分都占有相当的比值,对注塑机的技术性能、节能、环保以及成本占有重要部分。
注塑机液压系统由主回路、执行回路及辅助回路系统组成,如图所示。
图14 油路系统组成图1,2,3,4,5,6—分别为合模油缸、滑模油缸、顶出油缸、注射座油缸、注射油缸、液压马达;7,8,9,10,11,12—分别为油缸的控制模块(CU)、指令模块(CM);13—系统压力(P)、流量(Q)的控制和指令模块;14—泵;15—电机(M);16—进油过滤器;17—油冷却器;18—油箱;P—进油管路(高压);T—回油管路。
(低压)油路总管线(P、T、P)的上部分是执行回路系统,下部分是主回路系统及辅助回路系统。
执行回路系统:主要由各执行机构(油缸)和指令及控制装置(电磁阀)组成。
其功能是将进入管路P的高压油按程序放到油缸的左腔或右腔中去,推动活塞杆执行动作。
高压油进入的时间、顺序和位置是通过电磁换向阀来实现的,工作指令通过电信号发给电磁阀的电磁铁,控制其阀芯动作,将控制油路(P)的高压油,进入换向阀推动阀芯动作,将高压油接通到油缸中去;而各油缸中的回油经回油管路T及辅助油路系统放回油箱。
主回路系统:由动力源和控制模块组成。
动力源系统(电机、油泵)产生油压(P)和流量(Q),与指令(CU)及控制(CM)模块(压力阀、流量阀等)组成回路。
从泵来的高压油,进入主管路的时间、顺序、压力及流量,是通过流量阀,压力阀是电磁铁获得,指令的时间、顺序和强弱,由控制其阀芯的推力和开度来确定的。
执行回路与主回路之间是通过进油管路P(高压),回油管路T(低压)以及控制回路P(高压)形成“连接网络”。
注塑机应用液压组件非常广泛。
⑴.动力组件由电机带动泵实现电能—机械能—液压能的转换。
有各种油泵和液压马达。
油泵是靠封闭容腔使其容积发生变化来工作的。
理想的泵是没有的,因为结构上总会有制品缝隙就会有泄漏,而且机械磨损也会产生间隙,所以就要考虑泵的效率。
注塑机设计中常用的计算规范(个人从实践经验总结)

注塑机设计中常用的计算规范一、螺杆塑化能力:G = 0.017682D·h3·n·ρSD/4*L理论注射容积:V=π2S式中:D s——螺杆直径(cm)L——螺杆行程(cm)实际注射量:G1=ρV式中:ρ—熔料的密度(g/cm3),计算时选PS料,ρ= 0.92。
V——理论注射容积(cm3)注1:计算公式来源于经验公式。
二、螺杆的强度根据螺杆最常见的破坏,是在加料段螺槽根径处发生断裂,所以螺杆的强度计算就以此处计算其应力。
σr =224τσ+c≤〔σ〕 式中:压缩应力σc =sF P 0= 210⎪⎪⎭⎫ ⎝⎛d D 0p剪应力 τ=stW M 材料许用应力〔σ〕=ny σ式中三、熔胶筒的壁厚:(按厚壁筒计算中的能量理论,校核其强度或计算壁厚)熔胶筒的总应力σr = P 1322-K K ≤ 〔σ〕熔胶筒壁厚 δ= 2b D (P3-〔σ〕〔σ〕- 1 ) 式中部分熔胶筒的K 值四、螺杆驱动功率:采用经验公式计算N s = C·5.2D·n4.1S式中:N s——螺杆驱动功率(kw)C ——与螺杆结构参数及传动方式有关的系数取C=0.00016D s——螺杆直径(cm)n ——螺杆转速(r/min)螺杆所需扭矩与直径及转速之间的关系,可用下式表示:M t = 10α·D mS式中:M t——螺杆扭矩(N·m)——螺杆直径(cm)DSα——比例系数,对于热塑性塑料α=1.2~1.5m ——由树脂性能而定的指数,m=2.7~3螺杆的驱动功率一般需留20~30%的余量,以作备用。
五、传动轴的强度:传动轴最常见的破坏是在承受扭矩的最小截面处发生断裂,所以传动轴的强度计算就以此处进行计算:σr =224τσ+c ≤〔σ〕 式中:压缩应力σc = sF P= 210⎪⎪⎭⎫ ⎝⎛d D 0p剪应力 τ=stW M 材料许用应力〔σ〕=ny σ式中六、轴 承1、基本额定动负荷计算:C =Tn dm h f f f f f ·P < C r (或C a ) 式中C ——基本额定动负荷计算值(N ); P ——当量动负荷,见下式(N ); h f ——寿命系数,按表7-2-4选取; n f ——速度系数,按表7-2-5选取;m f ——力矩负荷系数,力矩负荷较小时1.5,力矩负荷较大时2; d f ——冲击负荷系数,按表7-2-6选取; T f ——温度系数,按表7-2-7选取;C r ——轴承尺寸及性能表中所列径向基本额定动负荷(N ); C a ——轴承尺寸及性能表中所列轴向基本额定动负荷(N )。
注塑机设计中常用的计算规范

注塑机设计中常用的计算规范1.注射压力计算:注射压力是指将塑料熔化后注入模具中所需要的压力。
注塑机的注射压力应该根据模具的尺寸、注射物料的熔化温度和所需的成品尺寸进行计算。
一般来说,注射压力的计算可以根据注射物料的熔化温度和熔体粘度进行估算。
2.注射速度计算:注塑机的注射速度决定了塑料进入模具的速度。
注射速度的计算应根据注射物料的熔化温度、熔体粘度、模具的尺寸和所需的成品尺寸进行。
一般来说,注射速度应根据所需的成品尺寸和模具的填充时间来确定。
3.冷却时间计算:冷却时间是指模具中注入塑料后,需要等待成型品冷却固化的时间。
冷却时间的计算应考虑注射物料的熔化温度、模具的尺寸、模具的冷却方式和所需的成品尺寸。
一般来说,冷却时间的计算可以根据模具材料的热传导系数和成品的固化时间来估算。
4.压力和流量计算:注塑机的液压系统需要提供足够的压力和流量来驱动注塑机的各个动作。
压力和流量的计算应考虑注射物料的熔化温度、注射压力、注射速度和所需的成品尺寸。
一般来说,压力和流量的计算可以根据所需的注射压力和注射速度来确定。
5.机器选择和尺寸计算:注塑机的尺寸选择和计算应根据所需的成品尺寸、注射物料的熔化温度、熔体粘度和注射压力进行。
一般来说,机器选择和尺寸计算可以根据模具的尺寸和所需的注射压力来确定。
以上是个人总结的注塑机设计中常用的计算规范。
在实际设计过程中,还可以根据具体情况,结合经验和实验数据进行调整和优化。
不同的注塑机设计可能存在差异,因此需要根据具体情况进行适当的调整。
重要的是根据实际情况进行综合考虑,确保注塑机的正常工作和成品的质量。
毕业设计注塑机液压系统设计
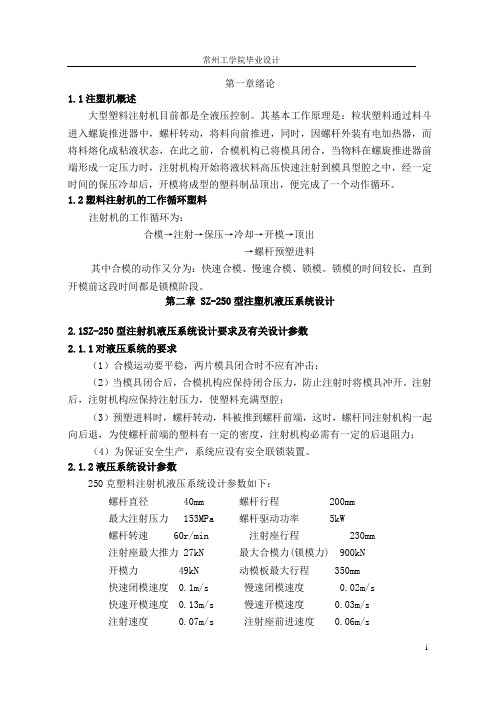
第一章绪论1.1注塑机概述大型塑料注射机目前都是全液压控制。
其基本工作原理是:粒状塑料通过料斗进入螺旋推进器中,螺杆转动,将料向前推进,同时,因螺杆外装有电加热器,而将料熔化成粘液状态,在此之前,合模机构已将模具闭合,当物料在螺旋推进器前端形成一定压力时,注射机构开始将液状料高压快速注射到模具型腔之中,经一定时间的保压冷却后,开模将成型的塑科制品顶出,便完成了一个动作循环。
1.2塑料注射机的工作循环塑料注射机的工作循环为:合模→注射→保压→冷却→开模→顶出→螺杆预塑进料其中合模的动作又分为:快速合模、慢速合模、锁模。
锁模的时间较长,直到开模前这段时间都是锁模阶段。
第二章 SZ-250型注塑机液压系统设计2.1SZ-250型注射机液压系统设计要求及有关设计参数2.1.1对液压系统的要求(1)合模运动要平稳,两片模具闭合时不应有冲击;(2)当模具闭合后,合模机构应保持闭合压力,防止注射时将模具冲开。
注射后,注射机构应保持注射压力,使塑料充满型腔;(3)预塑进料时,螺杆转动,料被推到螺杆前端,这时,螺杆同注射机构一起向后退,为使螺杆前端的塑料有一定的密度,注射机构必需有一定的后退阻力;(4)为保证安全生产,系统应设有安全联锁装置。
2.1.2液压系统设计参数250克塑料注射机液压系统设计参数如下:螺杆直径 40mm 螺杆行程 200mm最大注射压力 153MPa 螺杆驱动功率 5kW螺杆转速 60r/min 注射座行程 230mm注射座最大推力 27kN 最大合模力(锁模力) 900kN开模力 49kN 动模板最大行程 350mm快速闭模速度 0.1m/s 慢速闭模速度 0.02m/s快速开模速度 0.13m/s 慢速开模速度 0.03m/s注射速度 0.07m/s 注射座前进速度 0.06m/s注射座后移速度 0.08m/s2.2液压执行元件载荷力和载荷转矩计算 2.2.1各液压缸的载荷力计算(1)合模缸的载荷力合模缸在模具闭合过程中是轻载,其外载荷主要是动模及其连动部件的起动惯性力和导轨的摩擦力。
注塑机模具定位圈尺寸设计规格表-概述说明以及解释

注塑机模具定位圈尺寸设计规格表-概述说明以及解释1.引言1.1 概述注塑机模具定位圈是注塑模具中的重要组成部分,它的设计和尺寸直接影响到模具的定位精度和稳定性。
在注塑加工过程中,模具的定位圈起着固定模具位置、保证注塑成型品质的关键作用。
因此,准确的尺寸设计是确保模具定位圈功能正常发挥的关键。
本文将介绍注塑机模具定位圈尺寸设计规格表,通过详细分析模具定位圈的设计原理和规格要求,为工程师和设计人员提供参考,帮助他们设计出符合要求的模具定位圈,从而提高注塑成型过程的效率和品质。
1.2 文章结构文章结构部分将主要分为三个部分:引言、正文和结论。
1. 引言部分将介绍本文所涉及的主题,即注塑机模具定位圈尺寸设计规格表。
在概述部分,将简要介绍注塑机模具定位圈的重要性和设计规格表的目的。
在文章结构部分,将说明本文的组织结构和各部分的内容安排。
2. 正文部分将深入探讨注塑机模具定位圈的重要性、尺寸设计规格表以及设计考虑因素。
将对注塑机模具定位圈的作用、设计要求等进行详细阐述,以帮助读者更好地了解该主题。
3. 结论部分将总结本文的观点和主要内容,并探讨设计规格表的应用和未来发展方向。
将对设计规格表的实际应用进行讨论,为读者提供更具实践性的参考,并展望注塑机模具定位圈尺寸设计的未来发展趋势。
1.3 目的:本文的目的旨在通过对注塑机模具定位圈尺寸设计规格表的详细介绍,帮助读者了解注塑机模具定位圈在注塑生产中的重要性和作用,掌握注塑机模具定位圈尺寸设计的基本原则和规范要求。
同时,通过对设计规格表的解读,帮助读者更好地进行注塑机模具定位圈的设计和制造工作,提高生产效率和产品质量。
通过本文的阅读,读者能够全面了解注塑机模具定位圈的相关知识,为其在注塑生产中的实际操作提供参考和指导。
2.正文2.1 注塑机模具定位圈的重要性注塑机模具定位圈是注塑模具中的重要组成部分,它能够确保模具在注塑机上的正确定位并稳固固定。
在注塑加工过程中,模具定位圈起着至关重要的作用,它能够保证模具在注塑机上的准确定位,避免模具在运行过程中出现松动或错位的情况,从而确保产品的加工质量和生产效率。
塑料注塑机设计毕业设计
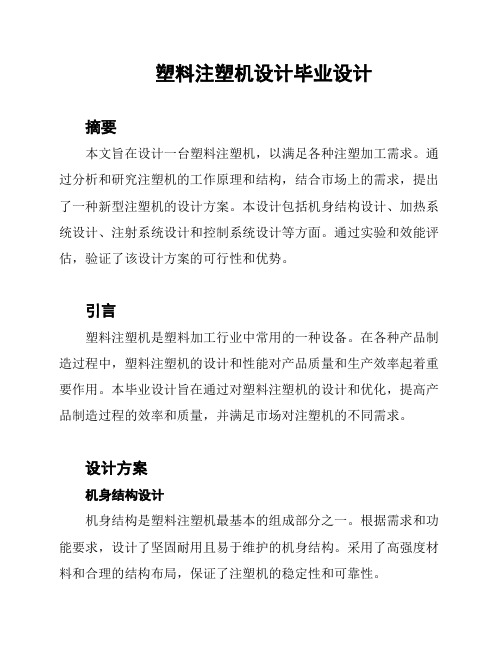
塑料注塑机设计毕业设计摘要本文旨在设计一台塑料注塑机,以满足各种注塑加工需求。
通过分析和研究注塑机的工作原理和结构,结合市场上的需求,提出了一种新型注塑机的设计方案。
本设计包括机身结构设计、加热系统设计、注射系统设计和控制系统设计等方面。
通过实验和效能评估,验证了该设计方案的可行性和优势。
引言塑料注塑机是塑料加工行业中常用的一种设备。
在各种产品制造过程中,塑料注塑机的设计和性能对产品质量和生产效率起着重要作用。
本毕业设计旨在通过对塑料注塑机的设计和优化,提高产品制造过程的效率和质量,并满足市场对注塑机的不同需求。
设计方案机身结构设计机身结构是塑料注塑机最基本的组成部分之一。
根据需求和功能要求,设计了坚固耐用且易于维护的机身结构。
采用了高强度材料和合理的结构布局,保证了注塑机的稳定性和可靠性。
加热系统设计加热系统对注塑机的温度控制至关重要。
设计了先进的加热系统,包括发热体的选用、温度控制装置和安全保护装置等。
通过精确的温度控制和快速的加热速度,提高了注塑机的加热效率和温度稳定性。
注射系统设计注射系统是塑料注塑机的核心部分,直接影响产品的注塑质量。
设计了高精度的注射系统,包括注射缸、注射嘴和注射机构等。
通过优化注射参数和控制方式,提高了注塑机的注度和稳定性,保证了产品的注塑质量。
控制系统设计控制系统对注塑机的运行和操作起着关键作用。
设计了智能化的控制系统,包括人机界面、控制器和传感器等。
通过优化控制算法和界面设计,提高了注塑机的操作便捷性和生产效率。
实验与评估为验证设计方案的效果和优势,进行了一系列实验和评估。
通过对不同注塑机参数和工艺条件的测试,评估了设计方案在性能和效能上的表现。
实验结果表明,该设计方案具有较高的效率和稳定性,能够满足各种注塑加工需求。
结论本文提出了一种新型塑料注塑机的设计方案,通过对机身结构、加热系统、注射系统和控制系统的设计和优化,提高了注塑机的性能和质量。
实验和评估结果验证了该设计方案的可行性和优势。
【精品】立式注塑机机械结构设计设计

第1章注射成型机的概述和发展趋势1.1概述注射成型机是将热塑性塑料或热固性塑料制成各种塑料制件的主要成型设备,是集机械、电气、液压于一体的塑料成型设备。
随着现代工业和尖端科学技术的发展,塑料制件被越来越广泛地应用到国防工业、机械、电气、航空、交通运输、建筑、农业、文教、卫生及人们生活各个领域。
注射成型法是塑料制品的主要成型方法之一.它是利用注射装置将注射机筒中已经熔融的热塑性塑料或热固性塑料以高压、高速注入到闭合的成型模具型腔中,经冷却固化成型后,制成与模具型腔形状几乎完全一致的塑料制品。
它具有以下特点:可成型形状复杂、尺寸精确及带有嵌件的是塑料制件;对各种塑料加工的适应性强;机器生产率高以及易于实现自动化生产等。
因此注射成型技术及注射成型机得到极为广泛的应用,现在已成为塑料加工业和塑料机械行业中的一个重要组成部分。
1.2我国立式塑料注射成型机的技术水平及发展趋势国内生产立式注塑机的厂家寥寥无几,一方面是由于市场的需求量不是很大,另一方面国内立式注塑机的研发技术水平还比较落后,生产的立式机市场竞争能力较弱.国内立式注塑机基本上通过进口来满足市场的需求,立式注塑机生产实力较强的企业主要分布在中国台湾地区,如台湾丰铁机械公司等,这些公司经过多年的生产实践经验,逐步掌握了立式注塑机的生产技术,在立式机的生产领域独领风骚.近几年来,世界上工业发达国家的注塑机生产厂家都在不断提高普通注塑机的功能、质量、辅助设备的配套能力,以及自动化水平。
同时大力开发、发展大型注塑机、专用注塑机、反应注塑机和精密注塑机,以满足生产塑料合金、磁性塑料、带嵌件和数码光盘制品的需求.注塑机是目前中国塑料机械中发展速度最快、水平与工业发达国家差距较小的塑机品种之一。
但这主要指普通型注塑机,在特大型、特殊、专用、精密注塑机、立式注塑机等品种方面,有的尚属空白,这是与工业发达国家的主要差距。
当今世界,注射成型技术发展迅猛,新技术、新设备层出不穷。
- 1、下载文档前请自行甄别文档内容的完整性,平台不提供额外的编辑、内容补充、找答案等附加服务。
- 2、"仅部分预览"的文档,不可在线预览部分如存在完整性等问题,可反馈申请退款(可完整预览的文档不适用该条件!)。
- 3、如文档侵犯您的权益,请联系客服反馈,我们会尽快为您处理(人工客服工作时间:9:00-18:30)。
浅谈注塑机机架设计--------------------------------------------------------------------------------(时间:2009-4-1 9:50:34 共有 526 人次浏览)所谓机架,即在机器(或仪器)中支承或容纳零、部件的零件。
按制造方法,机架可分为铸造机架、焊接机架和螺栓联接或铆接机架,而注塑机机架一般为框架式的焊接金属机架。
机架设计的准则1、工况要求:即任何机架的设计首先必须保证机器的特定工作要求。
例如,保证机架上安装的零部件能顺利运转,机架的外形或内部结构不致有阻碍运动件通过的突起;设置执行某一工况所必需的平台;保证上下料的要求、人工操作的方便及安全等。
2、刚度要求:在必须保证特定的外形条件下,对机架的主要要求是刚度。
如果基础部件的刚性不足,则在工作的重力、夹紧力、摩擦力、惯性力和工作载荷等的作用下,就会产生变形,振动或爬行,而影响产品定位精度、加工精度及其它性能。
例如机床的零部件中,床身的刚度则决定了机床的生产率和加工产品的精度。
3、强度要求:对于一般设备的机架,刚度达到要求,同时也能满足强度的要求4、稳定性要求:对于细长的或薄壁的受压结构及受弯-压结构存在失稳问题,某些板壳结构也存在失稳问题或局部失稳问题。
失稳对结构会产生很大的破坏,设计时必须校核。
5、美观:目前对机器的要求不仅要能完成特定的工作,还要使外形美观。
6、其它:如散热的要求,防腐蚀及特定环境的要求。
机架设计的一般要求在满足机架设计准则的前提下,必须根据机架的不同用途和所处环境,考虑下列各项要求,并有所偏重。
1、机架的重量轻,材料选择合适,成本低。
2、结构合理,便于制造。
3、结构应使机架上的零部件安装、调整、修理和更换都方便。
4、结构设计合理,工艺性好,还应使机架本身的内应力小,由温度变化引起的变形应力小。
5、抗振性能好。
6、耐腐蚀,使机架结构在服务期限内尽量少修理。
7、有导轨的机架要求机架导轨面受力合理,耐磨性良好。
设计步骤1、初步确定机架的形状和尺寸。
根据设计准则和一般要求,初步确定机架结构的形状和尺寸,以保证其内外部零件能正常运转。
2、根据机架的制造数量、结构形状及尺寸大小,初定制造工艺。
例如非标准设备单件的机架、机座、可采用焊接代替铸造。
3、分析载荷情况,载荷包括机架上的设备重量、机架本身重量、设备运转的动载荷等。
4、确定结构的形式,例如采用桁架结构还是板结构等。
再参考有关资料,确定结构的主要参数(即高、宽、板厚与材料等)。
5、画出结构简图。
6、参照类似设备的有关规范、规程,确定本机架结构所允许的挠度和应力。
7、进行计算,确定尺寸。
8、有必要时,进行详细计算并校核或做模型试验,对设计进行修改,确定最终尺寸。
综上所述:注塑机机架设计要符合机架设计的准则与一般要求,并要注意以下几点:1、应根据锁模结构在容模量最大时及射移行程最大的状态确定机架的长度,并兼顾油箱及电机油泵的布局具体确定。
根据锁模、射台、油箱、电箱及电机油泵布局确定机架的宽度与高度,高度要考虑人机工程学,适当时候要考虑用高低机架结构。
2、机架结构的主要构件是梁。
梁分纵梁与端梁。
注塑机中的梁可以是型材(角钢、槽钢、方通、工字钢、H型钢等),也可以的折弯板材焊接梁,也可以是型材与折弯板组焊梁。
3、机架结构还有另一主要构件是柱。
焊接柱按外形分为实腹柱和格构柱。
实腹柱分为型钢实腹柱和钢板实腹柱两种,前者焊缝少,应优先选用。
后者适应性强,可按使用要求设计成各种大小尺寸。
当腹板的计算高度h与腹板厚度δ之比大于80时,应有横向隔板加强,间距不得大于3h;柱腹外伸自由宽度b不宜超过15t,箱形柱的两腹板间宽度b也不宜超过40t (t为板厚)。
4、梁和柱的连接有铰接和刚性连接两种。
以焊接连接为主,很少用螺钉或铆接。
焊接方法可参看有关焊接规范和手册。
5、油箱的设计油箱在系统中的功能,主要是储油和散热,也起着分离油液中的气体及沉淀物的作用。
根据系统的具体条件,合理选用油箱的容积、形式和附件,以使油箱充分发挥作用。
油箱有开式和闭式两种,油箱的形状一般采用矩形、而容量大于2立方米的油箱采用圆筒形结构比较合理,设备重量轻,油箱内部压力达0.5MPa。
其中油箱的构造与设计要点:(1)必须有足够大的容量,以保证系统工作时能够保持一定的液位高度,在油箱容积不能够增大而又不能满足散热要求时,需要设冷却装置。
(2)设置过滤器。
油箱的回油口一般都设置系统所要求的过滤精度的回油过滤器,以保持返回油箱的油液具有允许的污染等级。
油箱的排油口(即泵的吸口)为了防止意外落入油箱中的污染物,有时也装设吸油网式过滤器。
(3)设置油箱主要油口。
油箱的排油口与回油口之间的距离应尽可能远些,管口都应插入最低油面之下,以免发生吸空和回油冲溅产生气泡。
管口制成45度的斜角,以增大吸油及出油的截面,使油液流动时速度变化不致过大。
管口应面向箱壁。
吸油管离箱底距离H≥2D(D 为管径),距箱边不小于3D。
回油管离箱底距离h≥3D。
(4)设置隔板将吸、回油管隔开,使液流循环,油流中气泡与杂质分离和沉淀。
隔板结构有溢流式标准型。
回流式及溢流式等几种。
另外还可根据需要在隔板上安置滤网。
(5)在开式油箱上部的通气孔上必须配置空气滤清器。
兼作注油口用。
油箱的注油口一般不从油桶中将油液直接注入油箱,而是经过滤车从注油口注入,这样可以保证注入油箱中的油液具有一定的污染等级。
(6)放油孔要设置在油箱底部最低的位置,使换油时油液和污物能顺利地从放油孔流出。
(7)为了能够观察向油箱注油的液位上升情况和系统过程中看见液位高度,必须设置液位计。
(8)按GB/T3766-1983中的5、2、3a规定:“油箱底部应离地面150mm以上,以便于搬移、放油和散热。
(9)油箱内壁应进行抛丸或喷砂处理,以清除焊渣和铁锈。
待灰砂处理干净之后,按不同工作介质进行处理或者涂层。
6、电箱的设计要根据所安装元器件的需要设定电箱所需空间,并要注意防水、防尘,必要时安装排气扇,加强电箱散热功能。
7、合理布局肋板和加强筋及周边封板。
肋板和加强筋的布局有纵向、横向和斜向布局,主要起到提高抗弯、抗扭刚度作用。
封板起到美观的作用。
8、必要时对机架进行去应力退火处理,以削除焊接应力,提高机架的稳定性。
告诉你准确的计算方法:克数=(螺杆的直径/2)2 * π * 螺杆的最大后退距离 * 0.85 * 塑料材料的密度与吨位大体上是正向关系,但联系并不密切,因为小吨位的机器也可以装稍大一号的螺杆,或者为了提高注塑速度、压力换装小一号的螺杆。
大致上:100T -- 150克200T -- 500克300T -- 800克500T -- 2000克700T -- 3200克仅供参考所谓机架,即在机器(或仪器)中支承或容纳零、部件的零件。
按制造方法,机架可分为铸造机架、焊接机架和螺栓联接或铆接机架,而注塑机机架一般为框架式的焊接金属机架。
机架设计的准则1、工况要求:即任何机架的设计首先必须保证机器的特定工作要求。
例如,保证机架上安装的零部件能顺利运转,机架的外形或内部结构不致有阻碍运动件通过的突起;设置执行某一工况所必需的平台;保证上下料的要求、人工操作的方便及安全等。
2、刚度要求:在必须保证特定的外形条件下,对机架的主要要求是刚度。
如果基础部件的刚性不足,则在工作的重力、夹紧力、摩擦力、惯性力和工作载荷等的作用下,就会产生变形,振动或爬行,而影响产品定位精度、加工精度及其它性能。
例如机床的零部件中,床身的刚度则决定了机床的生产率和加工产品的精度。
3、强度要求:对于一般设备的机架,刚度达到要求,同时也能满足强度的要求4、稳定性要求:对于细长的或薄壁的受压结构及受弯-压结构存在失稳问题,某些板壳结构也存在失稳问题或局部失稳问题。
失稳对结构会产生很大的破坏,设计时必须校核。
5、美观:目前对机器的要求不仅要能完成特定的工作,还要使外形美观6、其它:如散热的要求,防腐蚀及特定环境的要求。
机架设计的一般要求在满足机架设计准则的前提下,必须根据机架的不同用途和所处环境,考虑下列各项要求,并有所偏重。
1、机架的重量轻,材料选择合适,成本低。
2、结构合理,便于制造。
3、结构应使机架上的零部件安装、调整、修理和更换都方便。
4、结构设计合理,工艺性好,还应使机架本身的内应力小,由温度变化引起的变形应力小。
5、抗振性能好。
6、耐腐蚀,使机架结构在服务期限内尽量少修理。
7、有导轨的机架要求机架导轨面受力合理,耐磨性良好。
设计步骤1、初步确定机架的形状和尺寸。
根据设计准则和一般要求,初步确定机架结构的形状和尺寸,以保证其内外部零件能正常运转。
2、根据机架的制造数量、结构形状及尺寸大小,初定制造工艺。
例如非标准设备单件的机架、机座、可采用焊接代替铸造。
3、分析载荷情况,载荷包括机架上的设备重量、机架本身重量、设备运转的动载荷等。
上一页 [1] [2] [3] [4] [5] [6] 下4、确定结构的形式,例如采用桁架结构还是板结构等。
再参考有关资料,确定结构的主要参数(即高、宽、板厚与材料等)。
5、画出结构简图。
6、参照类似设备的有关规范、规程,确定本机架结构所允许的挠度和应力。
7、进行计算,确定尺寸。
8、有必要时,进行详细计算并校核或做模型试验,对设计进行修改,确定最终尺寸。
综上所述:注塑机机架设计要符合机架设计的准则与一般要求,并要注意以下几点:1、应根据锁模结构在容模量最大时及射移行程最大的状态确定机架的长度,并兼顾油箱及电机油泵的布局具体确定。
根据锁模、射台、油箱、电箱及电机油泵布局确定机架的宽度与高度,高度要考虑人机工程学,适当时候要考虑用高低机架结构。
2、机架结构的主要构件是梁。
梁分纵梁与端梁。
注塑机中的梁可以是型材(角钢、槽钢、方通、工字钢、H型钢等),也可以的折弯板材焊接梁,也可以是型材与折弯板组焊梁。
3、机架结构还有另一主要构件是柱。
焊接柱按外形分为实腹柱和格构柱。
实腹柱分为型钢实腹柱和钢板实腹柱两种,前者焊缝少,应优先选用。
后者适应性强,可按使用要求设计成各种大小尺寸。
当腹板的计算高度h与腹板厚度δ之比大于80时,应有横向隔板加强,间距不得大于3h;柱腹外伸自由宽度b不宜超过15t,箱形柱的两腹板间宽度b也不宜超过40t (t为板厚)。
腹钢板柱4、梁和柱的连接有铰接和刚性连接两种。
以焊接连接为主,很少用螺钉或铆接。
焊接方法可参看有关焊接规范和手册。
5、油箱的设计油箱在系统中的功能,主要是储油和散热,也起着分离油液中的气体及沉淀物的作用。
根据系统的具体条件,合理选用油箱的容积、形式和附件,以使油箱充分发挥作用。
油箱有开式和闭式两种,油箱的形状一般采用矩形、而容量大于2立方米的油箱采用圆筒形结构比较合理,设备重量轻,油箱内部压力达0.5MPa。