铸件缺陷分析与失效分析
【干货】铸造过程FMEA实战精选全文完整版
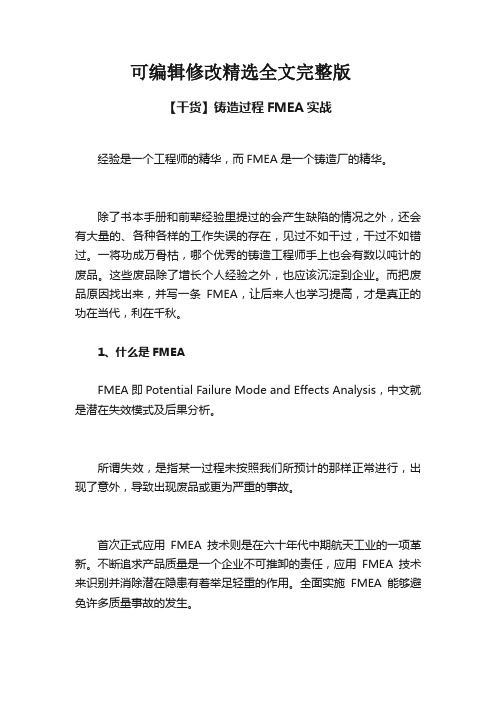
可编辑修改精选全文完整版【干货】铸造过程FMEA实战经验是一个工程师的精华,而FMEA是一个铸造厂的精华。
除了书本手册和前辈经验里提过的会产生缺陷的情况之外,还会有大量的、各种各样的工作失误的存在,见过不如干过,干过不如错过。
一将功成万骨枯,哪个优秀的铸造工程师手上也会有数以吨计的废品。
这些废品除了增长个人经验之外,也应该沉淀到企业。
而把废品原因找出来,并写一条FMEA,让后来人也学习提高,才是真正的功在当代,利在千秋。
1、什么是FMEAFMEA即Potential Failure Mode and Effects Analysis,中文就是潜在失效模式及后果分析。
所谓失效,是指某一过程未按照我们所预计的那样正常进行,出现了意外,导致出现废品或更为严重的事故。
首次正式应用FMEA技术则是在六十年代中期航天工业的一项革新。
不断追求产品质量是一个企业不可推卸的责任,应用FMEA技术来识别并消除潜在隐患有着举足轻重的作用。
全面实施FMEA能够避免许多质量事故的发生。
FMEA包括设计FMEA和过程FMEA。
而铸造厂多是按图纸开模生产,不涉及产品设计,因此所做大多指过程FMEA,即针对生产过程所制订的潜在失效模式及后果分析——PFMEA。
2、FMEA有什么作用FMEA是一组系统化的活动,其目的是:•发现、评价产品/过程中潜在的失效及其后果。
•找到能够避免或减少这些潜在失效发生的措施。
•书面总结上述过程。
•为确保客户满意,这是对设计过程的完善。
FMEA能够减少或消除因修改而带来更大损失的机率。
对于某些缺陷的产生,我们并非完全想不到,而是没去想。
“上工治未病”,出现问题能解决的,是好工程师,而能写FMEA的,是一流工程师。
一条FMEA,能将废品的起因机理,预防措施,检测方法解释的清清楚楚。
FMEA也是编制控制计划的依据。
这在新品开发过程中起到重要的作用。
3、什么时候需要写FMEA及时性是成功实施FMEA的最重要因素之一,它是一个“事前的行为”,而不是“事后的行为”,为达到最佳效益,FMEA必须在设计或过程失效模式被无意纳入设计产品之前进行。
失效分析基本方法

(3)无损探伤检查(涡流、着色、磁粉、同位 素、X射线、超声波等)
(4)表面及界面成分分析(俄歇能谱) (5)局部或微区成分分析(辉光光谱、能谱、 电子探针) (6)相结构分析(X射线衍射法) (7)断裂韧性检查,强度、韧性及刚度校核
26
5 综合分析归纳,推理判断提出初步结论 根据失效现场获得的信息、背景材料及各种实测
27
机械产品的失效分析报告通常应包括的内容
(1)概述 首先介绍失效事件的自然情况:事件发生的时
间、地点,失效造成的经济损失及人员伤亡情况;受何部门或
单位的委拓;分析的目的及要求;参加分析人员情况;起止时
间等。
(2)失效事件的调查结果 简明扼要地介绍失效部件的损坏
情况。当时的环境条件及工况条件;当事人和目击者对失效事
3.1失效分析的方法及程序 相关性分析的思路及方法 系统工程的分析思路及方法 数理统计分析思路及方法
1
相关性分析的思路及方法
一般用于具体零、部件及不太复杂的设备系统的失效分析中。
1. 按照失效件制造的全过程及使用条件的分析方法 2. 根据产品的失效形式及失效模式分析的思路及方法 3. “四M”分析思路及方法
(3)加工制造缺陷分析 铸、锻、焊、热处理缺陷,冷 加工缺陷,酸铣、电镀缺陷,碰伤,工序间锈蚀严重,装配 不当,异物混入及漏检等。
(4)使用及维护情况分析 超载、超温、超速,启动、 停车频繁或过于突然,润滑制度不正确,润滑剂不合格,冷 却介质中混有硬质点,未按时维修保养,意外灾害预防措施 不完善等。
(1)操作人员情况的分析 如工作态度不好、责任心不强、 玩忽职守、主观臆断和违章作业等不安全行为以及缺乏经验、反应 迟钝和技术低劣等局限性。
铸件有损和无损检测方法
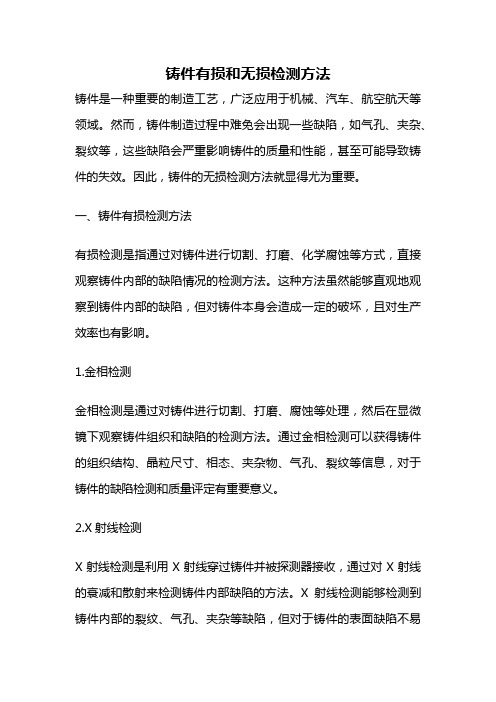
铸件有损和无损检测方法铸件是一种重要的制造工艺,广泛应用于机械、汽车、航空航天等领域。
然而,铸件制造过程中难免会出现一些缺陷,如气孔、夹杂、裂纹等,这些缺陷会严重影响铸件的质量和性能,甚至可能导致铸件的失效。
因此,铸件的无损检测方法就显得尤为重要。
一、铸件有损检测方法有损检测是指通过对铸件进行切割、打磨、化学腐蚀等方式,直接观察铸件内部的缺陷情况的检测方法。
这种方法虽然能够直观地观察到铸件内部的缺陷,但对铸件本身会造成一定的破坏,且对生产效率也有影响。
1.金相检测金相检测是通过对铸件进行切割、打磨、腐蚀等处理,然后在显微镜下观察铸件组织和缺陷的检测方法。
通过金相检测可以获得铸件的组织结构、晶粒尺寸、相态、夹杂物、气孔、裂纹等信息,对于铸件的缺陷检测和质量评定有重要意义。
2.X射线检测X射线检测是利用X射线穿过铸件并被探测器接收,通过对X射线的衰减和散射来检测铸件内部缺陷的方法。
X射线检测能够检测到铸件内部的裂纹、气孔、夹杂等缺陷,但对于铸件的表面缺陷不易检测。
3.超声波检测超声波检测是利用超声波在铸件内部传播并被探测器接收,通过分析超声波的传播时间和衰减程度来检测铸件内部缺陷的方法。
超声波检测可以检测到铸件内部的裂纹、气孔、夹杂等缺陷,并且对于铸件的表面缺陷也有一定的检测能力。
二、铸件无损检测方法无损检测是指不对铸件进行任何破坏的情况下,通过一些物理、化学或其他手段,检测铸件内部缺陷的方法。
无损检测方法不仅能够提高生产效率,减少铸件的损耗,还能够保持铸件的完整性,降低生产成本。
1.磁粉检测磁粉检测是利用铸件表面涂上磁粉,然后通过磁场磁化铸件,观察磁粉的分布情况来检测铸件表面和内部的裂纹、气孔等缺陷的方法。
磁粉检测能够检测到铸件表面和内部的裂纹、气孔等缺陷,但对于夹杂等缺陷的检测能力有限。
2.涡流检测涡流检测是利用涡流原理,在铸件表面或内部引入高频交流电磁场,通过涡流感应电流的变化来检测铸件的缺陷的方法。
失效分析知识点

失效分析知识点第一章概论1.失效的定义:当这些零件失去其应有的功能时,则称该零件失效。
2.失效三种情况:(1).零件由于断裂、腐蚀、磨损、变形等从而完全丧失其功能;(2).零件在外部环境作用下,部分的失去其原有功能,虽然能工作,但不能完成规定功能,如由于磨损导致尺寸超差等;(3).零件能够工作,也能完成规定功能,但继续使用时,不能确保安全可靠性。
3. 失效分析定义:对失效产品为寻找失效原因和预防措施所进行的一切技术活动。
也就是研究失效的特征和规律,从而找出失效的模式和原因。
4. 失效分析过程:事前分析(预防失效事件的发生)、事中分析(防止运行中设备发生故障)、事后分析(找出某个系统或零件失效的原因)。
5. 失效分析的意义:(1).失效分析的社会经济效益:失效将造成巨大的经济损失;质量低劣、寿命短导致重大经济损失;提高设备运行和使用的安全性。
(2).失效分析有助于提高管理水平和促进产品质量提高;(3).失效分析有助于分清责任和保护用户(生产者)利益;(4).失效分析是修订产品技术规范及标准的依据;(5).失效分析对材料科学与工程的促进作用:材料强度与断裂;材料开发与工程应用。
第二章失效分析基础知识一.机械零件失效形式与来源:1.按照失效的外部形态分类:(1)过量变形失效:扭曲、拉长等。
原因:在一定载荷下发生过量变形,零件失去应有功能不能正常使用。
(2)断裂失效:一次加载断裂(静载荷):由于载荷或应力超过当时材料的承载能力而引起;环境介质引起的断裂:环境介质和应力共同作用引起的低应力脆断;疲劳断裂(交变载荷):由于周期作用力引起的低应力破坏。
(3)表面损伤失效:磨损:由于两物体接触表面在接触应力下有相对运动,造成材料流失所引起的一种失效形式;腐蚀: 环境气氛的化学和电化学作用引起。
(4).注:断裂的其他分类断裂时变形量大小:脆性断裂、延性断裂;裂纹走向与晶相组织的关系:穿晶断裂、沿晶断裂;2.失效的来源:(1).设计的问题:高应力部位存在沟槽、机械缺口及圆角半径过小等;应力计算错误;设计判据不正确。
铸造缺陷种类

铸造缺陷种类
1、气孔缺陷。
铸铁件在凝固过程中未能逸出的气体留在铸件内部形成的小孔洞,内壁光滑,有气体。
表面一般情况下呈球状或椭球状,对于超声波具有较高的反射率,因此可以通过超声波进行检测。
2、缩松、缩孔缺陷。
铸铁件在冷却凝固时,体积收缩,在最后凝固的时候得不到充足的铁液的补充便会形成空洞状的缺陷,内壁粗糙,周围多伴有许多杂质和细小的气孔。
缩松呈现细小而分散的空隙,缩孔呈现大而集中的空洞。
3、偏析缺陷。
指铁合金在冶炼过程中或铁金属在熔化的过程中因为成分分布不均而形成的成分偏析,有偏析存在的区域其力学性能和整个金属的力学性能有较大的差别。
4、裂纹缺陷。
铸铁件中的裂纹主要时由于金属材料的强度难以支撑金属在冷却凝固时的收缩应力,这与金属中的合金含量、铸铁件的形状设计和铸造工艺有很大的关系。
5、冷隔缺陷。
这是指在浇注铁液时,由于飞溅、浇注中断或来自不同方向的两股金属流相遇,液态金属表面冷却形成的半固态薄膜留在铸铁件内而形成的一种隔膜状的面积型缺陷。
压铸件常见缺陷及解决办法手册 (完整版)
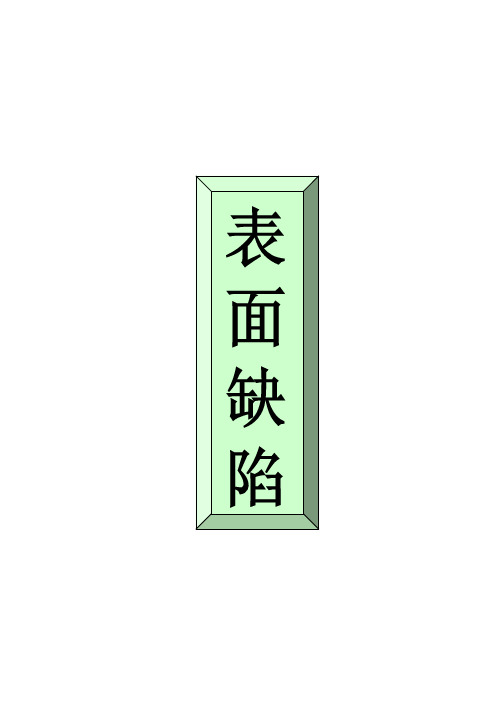
产生原因分析判断及解决办法1、金属液浇注温度低或模具温度低;2、合金成分不符合标准,流动性差;3、金属液分股填充,熔合不良;4、浇口不合理,流程太长;5、填充速度低或排气不良;6、压射比压偏低。
1、产品发黑,伴有流痕。
适当提高浇注温度和模具温度;2、改变合金成分,提高流动性;3、烫模件看铝液流向,金属液碰撞产生冷隔出现一般为涡旋状,伴有流痕。
改进浇注系统,改善内浇口的填充方向。
另外可在铸件边缘开设集渣包以改善填充条件;4、伴有远端压不实。
更改浇口位置和截面积,改善排溢条件,增大溢流量;5、产品发暗,经常伴有表面气泡。
提高压射速度,6、铸件整体压不实。
提高比压(尽量不采用)。
缺陷1 ---- 冷隔缺陷现象:温度较低的金属流互相对接但未熔合而出现的缝隙,呈不规则的线形,有穿透的和不穿透的两种,在外力的作用下有发展的趋势。
其他名称:冷接(对接)缺陷2 ---- 擦伤其他名称:拉伤、拉痕、粘模伤痕缺陷现象:顺着脱模方向,由于金属粘附,模具制造斜度太小而造成铸件表面的拉伤痕迹,严重时成为拉伤面甚至产生裂纹。
产生原因 分析判断及解决办法 1、型芯、型壁的铸造斜度太小或出现倒斜度; 2、型芯、型壁有压痕; 3、合金粘附模具;4、铸件顶出偏斜,或型芯轴线偏斜;5、型壁表面粗糙;6、涂料常喷涂不到;7、铝合金中含铁量低于0.6%; 8、合金浇注温度高或模具温度太高;9、浇注系统不正确, 直接冲击型壁或型芯 ; 10、填充速度太高;11、型腔表面未氮化。
1、产品一般拉出亮痕,不起毛。
修正模具,保证制造斜度; 2、产生拉毛甚至拉裂。
打光压痕、更换型芯或焊补型壁; 3、拉伤起毛。
抛光模具; 4、单边大面积拉伤,顶出时有异声修正模具结构; 5、拉伤为细条状,多条。
打磨抛光表面; 6、模具表面过热,均匀粘铝。
涂料用量薄而均匀,不能漏喷涂料; 7、型腔表面粘附铝合金。
适当增加含铁量至0.6~0.8%;8、型腔表面粘附铝合金,尤其是内浇口附近。
Q345铸件失效分析报告

Q345铸件失效分析报告
发表时间:2015-05-29T16:41:36.320Z 来源:《工程管理前沿》2015年第7期供稿作者:周亮[导读] 高强大体积混凝土不仅要保证实现强度,尤其要预防开裂,尽可能提高密实性,降低水化热。
周亮(江苏省特种设备安全监督检验研究院徐州分院江苏徐州 221007)某厂一铸钢件在使用过程中发生断裂,应企业要求,对其宏观形貌、化学成分、金相组织、硬度、冲击性能、微观组织等进行分析。
线切割取样位置如图1所示。
1、宏观形貌及断口分析(1)整体检查图1为该断裂铸件的宏观形貌。
图2为铸件内外表面腐蚀情况。
经检查发现,该铸件除断口外,有4条明显裂缝,如图所示。
另外,该铸件内外表面腐蚀严重,多处地方存在明显生锈和剥落,如图2所示。
3、金相组织分析
分别对裂纹处试样及冲击试样进行金相检测,参考GB/T 8493-1987《一般工程用铸造碳钢金相》,经打磨、抛光后,用4%硝酸酒精腐蚀,100倍观察,所得金相照片如图10、11所示。
其金相组织为魏氏体+块状铁素体+珠光体。
6、结论
(1)由于Q345作为铸件使用时没有对应的标准或者相近材料作为参照对比,企业也没提供产品执行的技术指标,因此本分析报告只
能给出相对应的测试结果,供分析参考。
其中:C%- ,Si%- ;Mn%- ,P%- ,S%- ,Ni%- ,Cr%- ;金相组织为魏氏体+块状铁
素体+珠光体;硬度平均值为HV 113.06;冲击功AkV为7.0J,冲击韧性ak为8.8J;(2)铸件在使用过程中受到较大冲击力,产生裂缝并导致断裂;(3)铸件存在大量铸造缺陷,致使其性能下降。
铸件缺陷检测报告(超声波)模板

铸件缺陷检测报告(超声波)模板1. 概要本报告为对铸件进行超声波缺陷检测的结果进行总结和分析。
以下是对铸件缺陷检测的评估和建议。
2. 缺陷检测结果根据超声波检测,发现了以下缺陷:- 缺陷1:位置:铸件底部,尺寸:直径5mm,形状:圆形,缺陷类型:气孔。
- 缺陷2:位置:铸件壁厚区域,尺寸:长度15mm,缺陷类型:夹杂物。
- 缺陷3:位置:铸件表面,尺寸:直径10mm,形状:不规则,缺陷类型:裂纹。
3. 缺陷评估根据缺陷检测结果,对各个缺陷的评估如下:- 缺陷1:气孔缺陷位于铸件底部,尺寸较小,对铸件的机械性能影响较小,建议可以接受或进行补救措施。
- 缺陷2:夹杂物缺陷出现在铸件壁厚区域,长度较长,可能会降低铸件的强度和可靠性,建议采取修复或替换措施。
- 缺陷3:裂纹缺陷位于铸件表面,尺寸较大且形状不规则,可能会导致铸件的破裂和失效,强烈建议进行修复或重新铸造。
4. 修复建议根据缺陷的评估,提出以下修复建议:- 缺陷1:可以采取填充和打磨的方式修复气孔缺陷,并进行二次超声波检测确认修复效果。
- 缺陷2:建议切除铸件壁厚区域的夹杂物,并进行补焊或更换材料,确保铸件的完整性和可靠性。
- 缺陷3:对于铸件表面的裂纹缺陷,建议进行局部修复或重新铸造,以避免安全事故的发生。
5. 结论本次铸件缺陷检测通过超声波技术获得了详细和准确的结果。
通过对缺陷的评估和修复建议,可以有效提升铸件的质量和性能。
建议根据本报告提供的结果进行相应的修复措施,并在修复后进行复检以确保缺陷被彻底解决。
以上为铸件缺陷检测报告(超声波)模板的内容总结。
如有任何问题或需要进一步的帮助,请随时与我们联系。
谢谢!。
- 1、下载文档前请自行甄别文档内容的完整性,平台不提供额外的编辑、内容补充、找答案等附加服务。
- 2、"仅部分预览"的文档,不可在线预览部分如存在完整性等问题,可反馈申请退款(可完整预览的文档不适用该条件!)。
- 3、如文档侵犯您的权益,请联系客服反馈,我们会尽快为您处理(人工客服工作时间:9:00-18:30)。
热处理缺陷
四.其他缺陷 ⒈冷处理裂纹 A→M转变,同淬火裂纹 ⒉自生裂纹 淬火后在室温下放置,残A会 继续转变成M,产生组织应力 淬火后的零件,其组织是马氏体和残余奥氏体, 常温下残余奥氏体不断转变成马氏体,发生体积膨 胀,因此淬火零件不加处理放在常温下,往往会发 生自生裂纹 。因此防止自生裂纹的方法是淬过火的 零件应及时回火,最好在3小时内进行回火。
铸造缺陷
是遗留在钢液中的熔炼渣或耐火材料与脏物 聚集在铸件的上表面或型腔内角.如出现在 内部,破坏了金属的连续性,是不允许存在的 缺陷. ⒉夹杂:钢在冶炼过程中参与物化反应 (如脱氧脱硫脱磷等)的金属元素和非金属元 素相互作用的产物,由于溶解度的变化而析 出的夹杂.夹杂物按GB/T 10561-2005《钢中
机械构件失效的主要形式及其特征
二.断裂失效 ㈠塑性断裂失效 当构件所承受的实际应力大于材料的屈服 强度时,将产生塑性变形,应力进一步增大 时,就会产生断裂。称为塑性断裂失效。通 常是指室温下的塑性断裂。 ①塑性断裂的特征 在裂纹或断口附近有 宏观塑性变形,或者在塑性变形处有裂纹出 现。塑性断裂的一个典型断口如同韧性材
㈡淬火裂纹形成机理 淬火裂纹的形成机理:钢中奥氏体向马氏 体转变时体积增大所产生的表面涨开的内应 力大于零件外层淬火状态的马氏体的强度时, 便出现淬火裂纹。
热处理缺陷
㈢影响淬火裂纹的因素 ⒈钢的化学成分对淬火裂纹的影响 磷的影响最大,最易引起淬火裂纹;含碳 量增加开裂倾向大;含Cr含Mo量增加,开裂 倾向大。 ⒉原材料缺陷对淬火裂纹的影响 冶金过程的缺陷(夹杂偏析等)、热加工
铸造缺陷
二.疏松 最后凝固的液态金属在它们凝固过程中没 有液态金属的补充,在完全凝固后产生许多 细小的孔洞形成疏松。又分一般疏松,中心 疏松。在铸件和铸锭中所出现的组织不致密 现象称为疏松。
铸造缺陷
一般疏松3级, 中心疏松3级,
铸造缺陷
三.缩孔 由于最后凝固部位得不到液态金属的补充 而形成的空洞.缩孔的特征是宏观酸蚀试样的 中心区域呈不规则的折皱裂纹或孔洞,经常伴 随严重疏松夹渣和成分偏析. 四.夹杂 分非金属夹杂和异金属夹杂 ㈠非金属夹杂物 ⒈夹渣:形状不规则的非金属夹杂物,通常
㈠弹性变形失效: 弹性变形过量造成弹性 丧失。 ㈡塑性变形失效: 塑性变形过量造成变形 量超过一定极限,形状或尺寸变化造成失效不 能使用。
㈢蠕变变形失效: 零件长时期在一定温度 和压力作用下工作,即使小于屈服点也会缓 慢地产生塑性变形,这种现象称为蠕变。当 蠕变变形量超过规定数值后就会发生失效, 甚至产生蠕变断裂。 ㈣高温松弛失效: 零件在高温下失去弹性 功能,产生塑性变形而失效。
锻造缺陷
当碳化物级别较高时,降低锻造变形性能, 容易引起淬火裂纹,降低刀具使用寿命。 ⒊缩管残余 由于钢锭冒口部分切除不干 净,在开坯和轧制时将冒口部分存在的夹杂 物缩松缩孔偏析残留在钢材内部,锻造时或 锻后热处理时,从这种心部缺陷向外发展成 裂纹。
W系高速钢共晶碳化物不均匀度级别,按GB/T149791994第一级别图。3级
铸造缺陷
非金属夹杂物显微评定方法》在纵截面上评 定。在宏观断口上也能观察到亮带亮块亮线 ㈡异金属夹杂 异金属夹杂(包括‘冷豆’)是由于冶 炼操 作不当,合金料未熔化或浇铸系统中掉入异 金属所致。异金属夹杂是不允许存在的缺 陷。
铸造缺陷
五.偏析 钢中存在的化学成分的不均匀现象。 六.铸造裂纹 ⒈热裂纹 合金在凝固过程中结晶收缩过 程产生应力形成的裂纹。特征是沿晶界或枝 晶扩展;呈连续或断续延伸;裂纹末端无尖 尾;裂纹内有氧化皮;裂纹周围有共晶体。
热处理缺陷
⒊磨削烧伤 ⒋磨削裂纹 磨削表面出现网状龟裂或与 磨削方向垂直的种磨削裂纹与磨削方向成直角的若 干平行线,称为第二种磨削裂纹。 ⒌淬火软点 局部区域未淬硬 软点软块 ⒍未淬硬 硬度低。原因
第 四 节 机械产品失效分析的目的意义
热处理缺陷
⒉引起形状变化的原因 内应力与外应力的作用 内应力:相变的组织应力和加热冷却的热 应力和零件内部的残余应力(前期铸、锻、机 加工工序产生的应力) 外应力:工件自重、工件夹持、工件装夹 等受力
热处理缺陷
⑴加热的影响 温度分布不均匀,零件有效厚度越大、冷 却越快,变形越大。 ⑵冷却的影响 冷却不均匀,冷却太快造成热应力引起变 形。 ⑶残余应力的影响 残余应力在加热时会释放引起变形。
机械产品失效分析的目的意义
二.意义 ⒈具有显著的经济意义 通过失效分析,找出造成机械装备失效的 原因,采取改进措施,可防止重大事故的发 生,减少损失。 ⒉促进科学技术的发展 一些新的学科往往在失效分析过程中发现 发展的。如
机械产品失效分析的目的意义
⒊是质量管理的重要环节 ⑴现代的机械设计和质量管理要求对产品 做‘危险度分析’,就是运用失效分析的经 验和知识去分析审查设计方案是否存在某些 会导致失效的因素及万一失效后又会产生何 种程度的危害。例如‘FEMA’ 、‘PFEMA’ (潜在的失效模式及后果分析)
铸造缺陷
⒉内部气泡 特征:位于铸件内部的气泡.内壁光滑呈圆 形或椭圆形,宏观横断面低倍组织可观察到内 壁发亮的气泡. ㈡ 气泡的形成机理 ⒈析出气泡:钢液内气体随着温度降低溶解 度而析出,来不及逸出. ⒉侵入气泡:模壁泥芯壁的水分有机物挥发 分解碳酸盐分解的气体,来不及逸出.
铸造缺陷
⒊反应气泡:液态金属中的金属氧化物和液 态金属中的其它元素反应,液态金属与型腔壁 芯壁中的物质反应产生的气体.来不及逸出. ⒋卷入气泡:浇铸过程中,由于先注入的金 属液体表面已凝固,浇铸时带入的气体来不及 逸出.
热处理缺陷
二.回火脆性 ⒈第一类回火脆 (低温回火脆,不可逆回火 脆)。 淬火后在250~400℃范围内回火出现脆性, 冲击韧性降低,断裂方式以沿晶脆断为主. ⒉第二类回火脆 (高温回火脆,可逆回火脆) 在450 ℃ ~550℃或更高至650 ℃回火时 出现的脆性。合金钢尤其是镍铬钢更易发生.
热处理缺陷
铸造缺陷
⒋石墨漂浮 壁厚超过25mm的球铁铸件 断口上,常可见表面有一层深黑色区,金相 观察为开花状石墨聚集,以及较多镁的氧化 物夹杂和硫化物夹杂。原因:壁厚过厚,冷 却太慢,碳当量过高,加镁处理和孕育处理 温度太低
第二节 锻造缺陷
一.原材料缺陷造成的锻件缺陷 ⒈层状断口 在纵向断口上,沿热加工方 向呈现出无金属光泽的凹凸不平的层状伏的 条带,条带中伴有白色或灰色线条。 ⒉碳化物偏析 原材料存在较严重的碳化 物偏析,锻造时的锻压比又不够,碳化物偏 析程度没有多大改善,级别仍超差。反复锻 压可以打碎、打细粗大的带状的碳化物 。
热处理缺陷
过程中的缺陷(过热、折叠等)都可以成为 淬火裂纹的诱发源。 ⒊形状结构对淬火裂纹的影响 形状结构设计不合理 截面尺寸不均匀 带有应力集中部位 ⒋原始组织对淬火裂纹的影响 均匀的球化P淬火后转变成M其比容变化 较小,故得到的M内应力较小不易开裂
热处理缺陷
⒌淬火加热温度对淬火裂纹的影响 淬火加热温度高,奥氏体晶粒较大,淬 透性增大,容易产生淬火裂纹。 ⒍冷却速度对淬火裂纹的影响 冷却速度愈快, 马氏体相变发生时应力 愈大,愈易发生开裂
锻造缺陷
⒋材质缺陷开裂 锻造时在缩孔、夹渣、 碳化物偏析等材料缺陷处形成锻造裂纹。 ⒌带状组织 原材料存在的带状组织,在 锻造加热时会因扩散而改善。锻造时要有一 定的变形量,尽可能将带状碳化物带状碳化 物等打碎。 二.落料不当造成的缺陷 ⒈锻件端面与轴线倾斜 ⒉撕裂
锻造缺陷
⒊ 毛刺 ⒋端部裂纹 ⒌凸芯开裂 三.锻造工艺不当造成的缺陷 ⒈过热 ⒉过烧
失效分析是一门新兴发展中的学科。它具 有两个特点: 第一.综合性 即涉及广泛的学科领域和技 术门类,如金属物理、材料力学、金相学、 断裂力学、无损检测、机械设计、工艺学等 等。 第二.是实用性 即具有很强的生产应用背 景,与国民经济与生产生活密切相关。
机械产品失效分析的目的意义
一.目的 ⒈为了提高产品质量 ⒉为了技术开发、技术改进、技术进步 ⒊为了劣质产品的处理 ⒋为了事故仲裁 ⒌为了进行修复而作
锻造缺陷
⒊锻造裂纹 ⒋脱碳增碳 ⒌锻造折叠 ⒍组织缺陷
第三节 热处理缺陷
热处理缺陷类型较多,常见的有淬火裂 纹、变形、软点、回火脆性等 一.淬火裂纹 是指淬火过程中或淬火后室 温放置过程中产生的裂纹。淬火后室温放置 过程中产生的裂纹又叫时效裂纹(自生裂 纹)。冷处理是淬火的继续
热处理缺陷
㈠淬火裂纹的类型和特征 ⒈纵向裂纹 裂纹沿工件轴向分布一条或 几条,裂纹较深而长,有的会贯穿整个零件 长度方向。 ⒉横向裂纹 垂直于轴向的裂纹
机械构件常见的失效形式通常有四种类型: 变形失效、断裂失效、腐蚀失效、磨损失效。
机械构件失效的主要形式及其特征
一.变形失效 金属构件在外力作用下产生形状和尺寸的 变化称为变形,当变形达到一定程度后,构 件完全丧失或部分丧失其规定的功能称为变 形失效。变形失效都是逐渐发生的,一般都 属于非灾难性。但是忽视变形失效的监督和 预防,也会导致很大的损失。 室温下的变形失效主要有弹性变形失效和 塑性变形失效。高温下的变形失效主要有蠕 变失效和高温松弛失效。
料(45钢、40Cr钢等)抗拉试棒拉断后的 样子。塑性断口的微观形态主要为韧窝。 ②引起塑性断裂的原因 通常情况下塑性 断裂是由于外应力超过材料的屈服强度所致。 超过屈服强度产生变形然后断裂
机械构件失效的主要形式及其特征
㈡脆性断裂失效 脆性断裂是指断裂前几乎不产生显著的塑 性变形。脆性断裂是一种危险的突发事故, 危害性很大,脆性断裂按裂纹扩展的路径可 分为穿晶脆性断裂和沿晶脆性断裂。 ⒈穿晶脆性断裂 穿晶脆性断裂的断裂主要有解理断裂和准 解理断裂。
铸造缺陷
⒉冷裂纹 合金在凝固时,由于收缩产生铸 造应力和组织转变的应力超过材料强度时产生 的裂纹。 七.金相组织缺陷 ⒈白口 ⒉反白口 一般的灰口铸铁断口有可能表面 几毫米区域冷却太快而出现一层白口。而反白 口是铸件断口的四周边缘是正常的灰口,中心