SMT钢网目前主要有的制造技术
(整理)SMT技术简介.
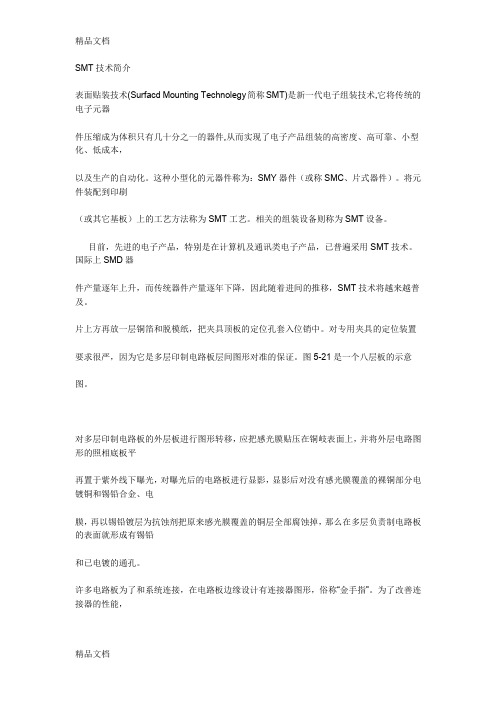
SMT技术简介表面贴装技术(Surfacd Mounting Technolegy简称SMT)是新一代电子组装技术,它将传统的电子元器件压缩成为体积只有几十分之一的器件,从而实现了电子产品组装的高密度、高可靠、小型化、低成本,以及生产的自动化。
这种小型化的元器件称为:SMY器件(或称SMC、片式器件)。
将元件装配到印刷(或其它基板)上的工艺方法称为SMT工艺。
相关的组装设备则称为SMT设备。
目前,先进的电子产品,特别是在计算机及通讯类电子产品,已普遍采用SMT技术。
国际上SMD器件产量逐年上升,而传统器件产量逐年下降,因此随着进间的推移,SMT技术将越来越普及。
片上方再放一层铜箔和脱模纸,把夹具顶板的定位孔套入位销中。
对专用夹具的定位装置要求很严,因为它是多层印制电路板层间图形对准的保证。
图5-21是一个八层板的示意图。
对多层印制电路板的外层板进行图形转移,应把感光膜贴压在铜岐表面上,并将外层电路图形的照相底板平再置于紫外线下曝光,对曝光后的电路板进行显影,显影后对没有感光膜覆盖的裸铜部分电镀铜和锡铅合金、电膜,再以锡铅镀层为抗蚀剂把原来感光膜覆盖的铜层全部腐蚀掉,那么在多层负责制电路板的表面就形成有锡铅和已电镀的通孔。
许多电路板为了和系统连接,在电路板边缘设计有连接器图形,俗称“金手指”。
为了改善连接器的性能,表面电镀镍层和金层,为了防止镀液污染电路板其它部位,应先在金手掼上方贴好胶带再进行电镀,电镀后揭下加热使原镀有的锡铅层再流,再在组装时对不需焊接的部位覆盖上阻焊膜,防止焊接时在布线间产生焊锡连桥或伤。
然后在阻焊膜上印刷字符图(指元器件的框、序号、型号以及极性等),待字符油漆固化,再在电路板上钻电路板要经过通断测试,要保证电路布线和互连通孔无断路、而布线间没有短路现象。
一般可采用程控多探针针目检电路图形、阻焊膜和字符图是否符合规范。
2.SMOBC工艺SMOBC工艺如图5-20所示,前部分工艺和在锡铅层涂覆阻焊膜的多层板工艺相同。
smt的两种生产工艺

smt的两种生产工艺
SMT(Surface Mount Technology)是现代电子产品制造中普
遍采用的一种电路组装技术。
它将电子元件直接粘贴到印刷电路板(PCB)上,而不是像传统的TH(Through-Hole)技术
那样通过插入孔进行连接。
以下是SMT的两种常见的生产工艺。
1. 贴片工艺
贴片工艺是SMT中最常用的一种工艺。
在贴片工艺中,电子
元件(如电阻、电容、二极管、集成电路等)通过粘贴或焊接方式固定在PCB上。
贴片电子元件通过自动化设备,如贴片机,根据PCB上的元件位置标记进行准确定位和精确贴装。
贴片工艺的优势在于其快速、高效、自动化的特点,可以大大提高生产效率和质量。
2. 焊接工艺
焊接工艺是SMT中另一种重要的生产工艺。
在SMT焊接中,焊接过程分为两个步骤:回流焊和波峰焊。
回流焊是通过加热整个PCB,使焊膏熔化并形成焊点。
这个过程中需要控制温
度和时间,以确保焊点的质量。
回流焊的主要优点是可以同时焊接多个焊点,缩短生产周期。
波峰焊则是将PCB的一侧浸
入熔化的焊料波峰中,使焊料通过离子化的方法与电路板实现焊接。
波峰焊适用于较大的电路板或需要更强的焊接强度的应用。
总结:这两种SMT生产工艺在电子产品制造中起到了至关重
要的作用。
贴片工艺使得电子元件的贴装速度更快、更准确,
提高了生产效率。
而焊接工艺则确保电子元件与PCB的可靠焊接,保证产品的质量和性能。
在实际制造中,通常会根据产品的需求和工艺要求来选择合适的工艺,以达到最佳的生产效果。
SMT钢网制作要求—范文

SMT钢网制作要求—范文一.网框选择使用与印刷机对应的相应规格型材的银白色铝框,常用网框有以下几种:1.大小:736×736mm,边框:宽40×厚40mm2.大小:580×580mm3.大小:370×470mm二.绷网先用细砂纸将钢片表面粗化处理并打磨钢片边缘,再进行绷网。
绷网用材料为不锈钢钢丝,使钢网与网框处于电导通状态,便于生产时板上静电的释放;钢网丝目数应不低于100目,其最小屈服张力应不低于45N。
绷网完成后,在钢网的正面,钢片与丝网结合部位及丝网与网框结合部位,必需用强度足够的胶水填充。
所用的胶水不应与清洗钢网用的清洗溶剂(工业酒精、二甲苯、丙酮等)起化学反应。
三.钢片为保证钢网有足够的张力和良好的平整度,所做钢片距外框内侧应保留有25mm 的距离。
建议根据不同的元件选择相应的钢片厚度,主要依据最小开孔和最小间距为考虑,详见下表或可根据公式进行计算得出:若焊盘尺寸L>5W 时,则依据宽厚比确定钢片的厚度:W/T≥1.5若焊盘呈正方形或圆形,则依据面积比确定钢片的厚度:L×W/[2T(L+W)]≥0.66元件对应钢片厚度表四.字符为方便公司与供应商沟通,应在钢片和网框上附上以下字符(特殊要求除外)(应该加上流扳方向以及上钢网方向)MODEL:(产品型号)P/C:(供应商制作型号)T:(钢片厚度)DATE:(生产日期)QA:检验员标识区:刻钢网厂家LOGO、要求字符等俯视图侧视图六.开孔方式说明:以下开孔方式仅包含常见典型零件,若碰到以下规范中未提及之焊盘类型,可参考元件焊盘外形类似之开孔设计方案制作。
6.1 锡膏制程中钢网开孔方式:此钢网开孔方式满足大部分产品达到最佳锡膏释放效果的要求,所有开孔方式试用于有铅制程,如有特殊要求应按要求制作。
a.CHIP 料元件封装为0402/0603/0805 元件开孔如下图(按焊盘100%开孔;0603 内距保持0.65):封装为0805 以上(不含0805)chip 元件开孔如下图(进行防锡珠设计):0402/0603/0805 元件开孔方式0805 以上元件开孔贴片磁芯电感焊盘如下,钢网开孔方式(进行外延设计):焊盘小于3mm×4mm 时,钢板开孔方式;(焊盘大于3mm×4mm 时,钢网开孔方式详见第8 条)二极管钢网开孔方式:(外扩0.1mm-0.2mm,内间距保持不变)钽电容按100%(外扩0.2mm,内间距保持不变)备注:大CHIP 料无法分类的内距保持不变,全部开1/3 梯形防锡珠(详细开孔方式见0805以上零件防锡珠开孔设计)。
SMT钢网制作要求—范文

SMT钢网制作要求—范文一.网框选择使用与印刷机对应的相应规格型材的银白色铝框,常用网框有以下几种:1.大小:736×736mm,边框:宽40×厚40mm2.大小:580×580mm3.大小:370×470mm二.绷网先用细砂纸将钢片表面粗化处理并打磨钢片边缘,再进行绷网。
绷网用材料为不锈钢钢丝,使钢网与网框处于电导通状态,便于生产时板上静电的释放;钢网丝目数应不低于100目,其最小屈服张力应不低于45N。
绷网完成后,在钢网的正面,钢片与丝网结合部位及丝网与网框结合部位,必需用强度足够的胶水填充。
所用的胶水不应与清洗钢网用的清洗溶剂(工业酒精、二甲苯、丙酮等)起化学反应。
三.钢片为保证钢网有足够的张力和良好的平整度,所做钢片距外框内侧应保留有25mm 的距离。
建议根据不同的元件选择相应的钢片厚度,主要依据最小开孔和最小间距为考虑,详见下表或可根据公式进行计算得出:若焊盘尺寸L>5W 时,则依据宽厚比确定钢片的厚度:W/T≥1.5若焊盘呈正方形或圆形,则依据面积比确定钢片的厚度:L×W/[2T(L+W)]≥0.66元件对应钢片厚度表四.字符为方便公司与供应商沟通,应在钢片和网框上附上以下字符(特殊要求除外)(应该加上流扳方向以及上钢网方向)MODEL:(产品型号)P/C:(供应商制作型号)T:(钢片厚度)DATE:(生产日期)QA:检验员标识区:刻钢网厂家LOGO、要求字符等俯视图侧视图六.开孔方式说明:以下开孔方式仅包含常见典型零件,若碰到以下规范中未提及之焊盘类型,可参考元件焊盘外形类似之开孔设计方案制作。
6.1 锡膏制程中钢网开孔方式:此钢网开孔方式满足大部分产品达到最佳锡膏释放效果的要求,所有开孔方式试用于有铅制程,如有特殊要求应按要求制作。
a.CHIP 料元件封装为0402/0603/0805 元件开孔如下图(按焊盘100%开孔;0603 内距保持0.65):封装为0805 以上(不含0805)chip 元件开孔如下图(进行防锡珠设计):0402/0603/0805 元件开孔方式0805 以上元件开孔贴片磁芯电感焊盘如下,钢网开孔方式(进行外延设计):焊盘小于3mm×4mm 时,钢板开孔方式;(焊盘大于3mm×4mm 时,钢网开孔方式详见第8 条)二极管钢网开孔方式:(外扩0.1mm-0.2mm,内间距保持不变)钽电容按100%(外扩0.2mm,内间距保持不变)备注:大CHIP 料无法分类的内距保持不变,全部开1/3 梯形防锡珠(详细开孔方式见0805以上零件防锡珠开孔设计)。
50条SMT工艺技术
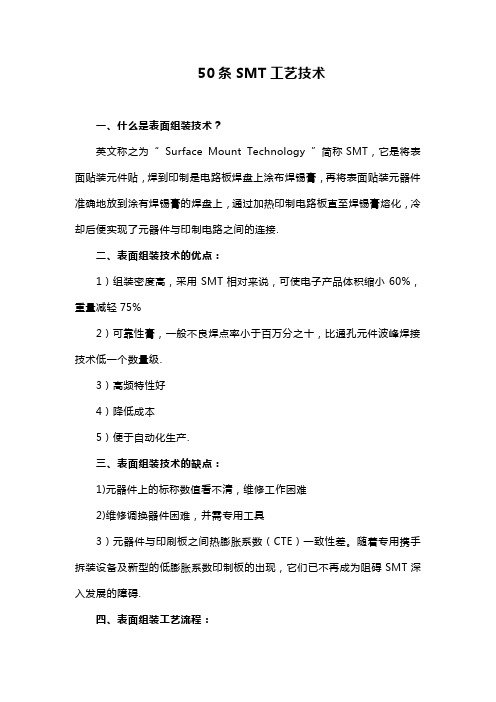
50条SMT工艺技术一、什么是表面组装技术?英文称之为“Surface Mount Technology ”简称SMT,它是将表面贴装元件贴,焊到印制是电路板焊盘上涂布焊锡膏,再将表面贴装元器件准确地放到涂有焊锡膏的焊盘上,通过加热印制电路板直至焊锡膏熔化,冷却后便实现了元器件与印制电路之间的连接.二、表面组装技术的优点:1)组装密度高,采用SMT相对来说,可使电子产品体积缩小60%,重量减轻75%2)可靠性膏,一般不良焊点率小于百万分之十,比通孔元件波峰焊接技术低一个数量级.3)高频特性好4)降低成本5)便于自动化生产.三、表面组装技术的缺点:1)元器件上的标称数值看不清,维修工作困难2)维修调换器件困难,并需专用工具3)元器件与印刷板之间热膨胀系数(CTE)一致性差。
随着专用携手拆装设备及新型的低膨胀系数印制板的出现,它们已不再成为阻碍SMT深入发展的障碍.四、表面组装工艺流程:SMT工艺有两类最基本的工艺流程,一类为锡膏回流焊工艺,另一类是贴片—波峰焊工艺.在实际生产中,应根据所用元器件和生产装备的类型以及产品的需求选择不同的工艺流程,现将基本的工艺流程图示如下:1)锡膏—回流焊工艺,该工艺流程的特点是简单,快捷,有利于产品体积的减小.2)贴片-波峰焊工艺,该工艺流程的特点是利用双面板空间,电子产品的体积可以进一步减小,且仍使用通孔元件,价格低廉,但设备要求增多,波峰焊过程中缺陷较多,难以实现高密度组装。
3)混合安装,该工艺流程特点是充分利用PCB板双面空间,是实现安装面积最小化的方法之一,并仍保留通孔元件价低的特点.4)双面均采用锡膏—回流焊工艺,该工艺流程的特点能充分利用PCB 空间,并实现安装面积最小化,工艺控制复杂,要求严格,常用于密集型或超小型电产品,移动电话是典型产品之一。
我们知道,在新型材料方面,焊膏和胶水都是触变性质流体,它们引起的缺陷占SMT总缺陷的60%,训练掌握这些材料知识才能保证SMT质量.SMT还涉及多种装联工艺,如印刷工艺,点胶工艺,贴放工艺,固化工艺,只要其中任一环节工艺参数漂移,就会导致不良品产生,SMT工艺人员必须具有丰富的工艺知识,随时监视工艺状况,预测发展动向。
SMT钢网设计基本要求
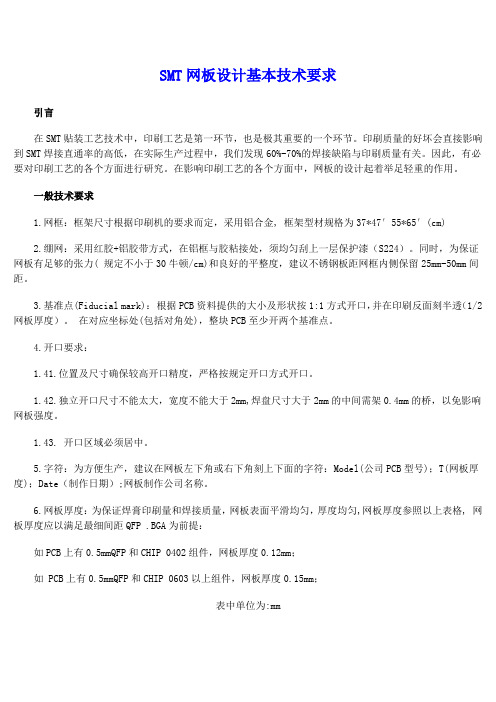
SMT网板设计基本技术要求引言在SMT贴装工艺技术中,印刷工艺是第一环节,也是极其重要的一个环节。
印刷质量的好坏会直接影响到SMT焊接直通率的高低,在实际生产过程中,我们发现60%-70%的焊接缺陷与印刷质量有关。
因此,有必要对印刷工艺的各个方面进行研究。
在影响印刷工艺的各个方面中,网板的设计起着举足轻重的作用。
一般技术要求1.网框:框架尺寸根据印刷机的要求而定,采用铝合金, 框架型材规格为37*47′55*65′(cm)2.绷网:采用红胶+铝胶带方式,在铝框与胶粘接处,须均匀刮上一层保护漆(S224)。
同时,为保证网板有足够的张力( 规定不小于30牛顿/cm)和良好的平整度,建议不锈钢板距网框内侧保留25mm-50mm间距。
3.基准点(Fiducial mark):根据PCB资料提供的大小及形状按1:1方式开口,并在印刷反面刻半透(1/2网板厚度)。
在对应坐标处(包括对角处),整块PCB至少开两个基准点。
4.开口要求:1.41.位置及尺寸确保较高开口精度,严格按规定开口方式开口。
1.42.独立开口尺寸不能太大,宽度不能大于2mm,焊盘尺寸大于2mm的中间需架0.4mm的桥,以免影响网板强度。
1.43. 开口区域必须居中。
5.字符:为方便生产,建议在网板左下角或右下角刻上下面的字符:Model(公司PCB型号);T(网板厚度);Date(制作日期);网板制作公司名称。
6.网板厚度:为保证焊膏印刷量和焊接质量,网板表面平滑均匀,厚度均匀,网板厚度参照以上表格, 网板厚度应以满足最细间距QFP .BGA为前提:如PCB上有0.5mmQFP和CHIP 0402组件,网板厚度0.12mm;如 PCB上有0.5mmQFP和CHIP 0603以上组件,网板厚度0.15mm;表中单位为:mm元件间距网板厚度元件间距网板厚度QFP SQIC SOP TSOP 1.27 0.2/.03 LCC 1.27 2.0 0.8 0.18BGA1.5 0.15 0.65 0.18 1.27 0.15 0.5 0.12/0.15 1 0.12 0.4 0.12 0.8 0.12 0.3 0.1 0.65 0.1PLCC 1.27 2.0 0.5 0.1 印锡网板开口形状及尺寸要求1.总原则:依据IPC-7525 钢网设计指南要求,为保证锡膏能顺畅地从网板开孔中释放到PCB焊盘上,在网板的开孔方面,主要依赖于三个因素:1.)面积比/宽厚比 (Area Ratio/Aspect Ratio)面积比(Area Ratio)>0.66 (见下图)2.)网孔孔壁光滑。
SMT钢网知识介绍

..........
7
二、钢网的制作工艺
钢网的制作方法: 1、蚀刻法 2、激光法 3、电铸法
..........
8
1、蚀刻制作工艺
客户的原始资料 数据处理 菲林制作 双面压膜 曝光显影 蚀刻 脱膜 粘网 检验、包装
先用光绘或照相的方法制出底板,底板是曝光的掩膜,上有整 块电路板的焊盘图案。
③、位置精度低,开孔尺寸不准确。因为需要光 绘或照相才可获得掩膜底板,又必须曝光才能完 成图形转移,使最终模板的尺寸受多个过程影响, 难免出现位置误差。同时,底板的精度,图形转 移过程,侧腐蚀都使开孔尺寸难于控制。
..........
10
2、激光制作工艺
客户的原始资料
数据处理(计算机控 制)
激光切割(计算机控 制)
⑧、针对同一PCB不同电子元件锡量的要求,可在同 一块模板上做出不同厚度,从而极大地提高了印刷焊接工 艺。
缺点:①、成本比激光法更高。
..........
14
三、钢网开口规则
钢网的厚度和开口尺寸决定了锡膏的涂覆 量和准确程度。
在大的开口原则(IPC模板开口规范)下, 要根据PCB表面处理方式的不同、焊盘大小 的不同、锡量要求的不同等自身实际情况 确定不同的开口方法。
..........
5
3、网框
网框由铝合金制成。不同尺寸大小的钢网, 对网框的厚度、宽度要求不同。目前我厂 使用的550*500㎜的钢网网框宽(40㎜)厚 (30㎜)370*470㎜的钢网,网框宽(30㎜) 厚(20㎜)
..........
6
4、粘结胶水
胶水早期国内制造商采用930快干胶水, 但这种胶水虽然干燥快速,但耐清洗能力 欠佳,因此后来逐渐被双组分树脂胶水所 取代。
浅谈SMT Stencil(SMT钢网)制造

随着SMT行业01005元件、0.5 pitch BGA、0.4 pitch IC及排阻的广泛应用,作为表面贴装的第一道工序锡膏印刷中使用到的关键耗材---SMT Stencil品质的优劣,对SMT工艺有着关键影响,因为在某些时候Stencil品质决定了锡膏印刷质量。
如何利用SMT Stencil去解决一些印刷中出现的不良呢?光韵达公司通过多年的积累,探索和沉淀了一些重要SMT Stencil制造的参数,愿与大家一起分享:1、 SMT Stencil设计常见原则a) 钢片厚度选择SMT Stencil钢片一般选择SUS304不锈钢片,它的常见厚度有0.10mm\0.12mm\0.15mm。
在一些特殊模板制造上,还会使用到一些更薄的钢片,如0.08mm\0.05mm\0.06mm\0.03mm。
众所周知,在开口面积相等的情况下,钢片的厚薄对锡量有着决定性的影响。
SMT Stencil钢片厚度选择一般依据开孔零件的精密程度,零件开口越小,钢片厚度选择相对较薄。
钢片厚度选择的通用原则:λ Aspect Ratio(宽厚比)=孔的宽度/金属片的厚度=W/T 宽厚比≥1.66λ Area Ratio(面积比)=焊盘的面积/孔壁面积=L*W/2*(L+W)*T 面积比≥0.66钢片厚度选择的常见原则λ手机板常见厚度选择0.10mm、0.12mm,多数会选择0.10mm,因为手机板零件较密且精密元件较多,选择0.10mm是最适宜的。
λ FPC常见厚度选择0.10mm、0.08mm甚至更薄,这主要取决于FPC上零件的精密程度和客户工艺。
通常做法是如果PCB板上有01005 CHIP零件,大多选择0.05-0.06mm厚度的钢片。
对于含0.4 pitch IC、0.5 pitch BGA或0.4pitch 排阻,0.08-0.10mm厚度的钢片是首选。
b) 常见元件开口设计原则CHIP开口设计重点是防锡珠,如:1)1:1开,方形内凹长宽的1/3即:W2=1/3W1 L2=1/3L12)内距S1依据元件大小保持适当内距IC开口设计重点是开口宽度和保证锡量,如:1)0.4pitch IC开口宽度0.18mm;0.5pitch IC开口宽度0.23mm;0.65pitch IC 开口宽度0.32mm;0.80pitch IC 开口宽度0.40mm;1.0pitchIC 开口宽度0.50mm;1.27pitch及以上宽度1:1开口;2) 0.65 Pitch及以下IC长度外加0.10mm,0.65Pitch及以上IC长度外加0.20mmBGA开口设计重点是如何保证锡量和避免连锡,如:0.5Pitch开0.29方孔四角倒0.05圆角;0.65Pitch开0.35圆孔;0.80Pitch开0.42圆孔;1.0Pitch开0.53圆孔;1.27 Pitch或以上按1:1开.排阻开口设计重点是元件本体与焊盘焊接效果,如:1)Pin脚宽度按照以上IC对应Pitch开口;2)Pin脚长外加0.15mm,倒圆角0.05mm.2、利用Stencil设计解决SMT印刷不良范例设计思路:1) 到客户SMT线上了解现在的印刷效果;2) 测量Gerber文件焊盘长宽、间距;3) 测量元件本体大小;4) 计算钢网开口面积与锡膏占有量;具体改善方案:1) Stencil钢片厚度设定0.10mm,便于下锡;2) 通过测量元件本体PIN脚和Gerber焊盘内距,将Stencil内扩至元件本体内距再各加0.05mm;3) 为保证锡膏过炉后元件PIN脚锡量,依据焊盘本身长度外加0.05mm;4) 依据以上数据计算开口锡膏饱和度已达到客户理想要求;问题描述:因本身是FPC,固定精度不高,此元件焊盘大小比较特殊,即长宽不成比例,印锡后成形较差,且锡量严重不足,导致印刷不良率偏高;解决方案:1)从钢片厚度入手,将原厚度为0.08mm钢片修改成0.05mm,促进下锡程度;2)将IC开口长宽设计更加协调,易于印刷成形。
- 1、下载文档前请自行甄别文档内容的完整性,平台不提供额外的编辑、内容补充、找答案等附加服务。
- 2、"仅部分预览"的文档,不可在线预览部分如存在完整性等问题,可反馈申请退款(可完整预览的文档不适用该条件!)。
- 3、如文档侵犯您的权益,请联系客服反馈,我们会尽快为您处理(人工客服工作时间:9:00-18:30)。
SMT钢网目前主要有的制造技术SMT钢网的制造技术目前主要有激光切割、化学蚀刻、电铸成型、机械加工等方式。
关于这些技术的具体工艺,我以前有篇论文已经做了详细介绍,这里就不在累述。
从上面的信息我们可以看出,曾经在国内占主流地位的化学蚀刻模板渐渐日薄西山,目前只能做一些简单的要求不高的SMT钢网。
甚至很多蚀刻模板厂家其主业已经不是模板,而是一些金属器件。
电子产品的短、小、轻、薄化发展,使得电子装联技术向高密度互联工艺方向发展,这给了SMT钢网蚀刻工艺以致命的打击。
当然,国内蚀刻厂商的不思进取,技术上没有任何改进也是其没落的原因之一。
另一个曾经由于0201、01005器件的兴起而被寄予厚望的电铸制造SMT钢网工艺,由于其高昂的成本、可能的环境污染以及激光工艺的进步,也没有在SMT模板被广泛应用。
国内掌握电铸工艺的仅有几家厂家也把市场方向放在了OLED掩膜板、触摸屏模板等非SMT 市场。
激光制造工艺能够在SMT模板制造市场占据统治地位,精度高、环保的特点是其牢固根基。
国内化学蚀刻工艺制作SMT钢网的精度最高不到10μm,而激光切割精度最高可达1μm。
激光工艺的环保,是众所周知的,在全球越来越对环保重视的情形下,蚀刻和电铸都不会成为一个主流工艺。
虽然激光切割会有毛刺的产生,从而影响脱膜,但激光模板制造商的积极研发,用后处理的抛光工艺,能够去除绝大部分的毛刺,从而使孔壁接近电铸模板。
用于SMT模板是个消耗品,因此,行业一直在寻找是否有工艺能替代模板印刷工艺,从而减少或放弃模板的使用,但很遗憾一直没有进展由于还有很多因素的限制,如效率、锡膏的配合等很难解决的问题,也注定这种无网板喷印方式只能被一些研究机构所使用,而不能被行业广泛采用。
因此,目前SMT不锈钢模板还无法找到其替代品或替代工艺。
参考资料:东莞市麦特好电子有限公司。