表面粗糙度的评定参数
第五章表面粗糙度

图4 -9 不同形状轮廓的支承长度 轮廓的支承长度率 Rmr (c) 是反映零件表面耐磨性能的指标 , 零件(b)的 Rmr (c) 数值比零件(a)大,其表面耐磨性能好。
(二)GB/T 3505—2000 与GB 3505—1983 两标准中基本术语与参数符号的比较
表面粗糙度新旧标准基本术语与参数符#39; i i 1
算术平均中线 F1
F2
Fi
F1′
F2′
Fi′
lr
图4-5表面粗造度轮的算术平均中线
三、 表面粗糙度评定参数
(一)表面粗糙度评定参数 1.轮廓的算术平均偏差
在一个取样长度lr内,被测轮廓线上各点到中线纵坐标绝 l 1 对值的算术平均值,记为 Ra Ra y dx
第五章 表面粗糙度
主要内容: 1、表面粗糙度的概念;
2、表面粗糙度的评定参数;
3、表面粗糙度的代号; 4、表面粗糙度的选择及标注;
表面粗糙度的相关标准
GB/T 3505—2000《产品几何技术规范 表面结构 轮廓法 表面结构的术语、定义及参数》; GB/T 18618—2002《产品几何技术规范(GPS)表面结 构轮廓法图形参数》; GB/T1031—1995《表面粗极度参数及其数值》; GB/T 131—1993《机械制图表面粗糙度符号、代号及 其注法》。 GB/T 10610—1998《产品几何技术规范表面结构轮廓法 评定表面结构的规则和方法》。
1.一般选择原则 1)同一零件上,工作表面的粗糙度参数值小于非工作表面的粗糙度 参数值。 2)摩擦表面比非摩擦表面的粗糙度参数值要小;滚动摩擦表面比滑 动摩擦表面的粗糙度数值要小;运动速度高、单位压力大的摩擦表面, 应比运动速度低、单位压力小的摩擦表面的粗糙度参数值要小。 3)有循环载荷的表面及易引起应力集中的部分(如圆角、沟槽), 表面粗糙度参数值要小。 4)配合性质要求高的结合表面,配合间隙小的配合表面以及要求连 接可靠、受重载的过盈配合表面等,都应取较小的粗糙度参数值。 5)配合性质相同,零件尺寸越小则表面粗糙度参数值应越小;同一 精度等级,小尺寸比大尺寸、轴比孔的表面粗糙度参数值要小。
粗糙度对比Ra、Rz、RMS、国内外标准对照

表面粗糙度高度参数有3种:1.轮廓算数平均偏差:轮廓算数平均偏差Ra是指在取样长度L内,被测轮廓上各点到基准线的距离Yi的绝对值的算数平均平均值。
2.微观不平度十点高度:微观不平度十点高度Rz是指在取样长度L内,被测轮廓上五个最大轮廓峰高Ypi的平均值与五个最大轮廓谷底Yvi的平均值之和。
3.轮廓最大高度:轮廓最大高度Ry是指在取样长度L内,被测轮廓的峰顶线与轮谷线之间的距离。
表征微观不平度高度特性的评定参数Ra、Rz、Ry的数值愈大则表面越粗糙。
在高度评定参数中,Ra的概念颇为直观,Ra值反应实际轮廓微观几何形状特性的信息量最大,且Ra值用触针式电动轮廓仪测量比较容易。
因此对于光滑表面和半光滑表面,普遍采用Ra作为评定参数。
但受测量仪器的限制,极光滑和极粗糙的表面不能用Ra评定。
评定参数Rz的概念较为直观,Rz值通常用非接触式的光切显微镜测量。
但Rz值只反应取样长度内峰高和谷底的十个点,不能反应峰顶的尖锐和平顿的几何形状特性,因此Rz值不如Ra值反应得微观几何形状特性全面。
评定参数Ry的概念简单,Ry值得测量方便,但Ry值不及Rz、Ra值反应的微观几何形状特性全面。
Ry值与Ra、Rz值连用控制微观不平度的谷深用来评定某些不允许出现较大加工痕迹和受交变应力作用的表面。
RMS值实际就是有效值,就是一组统计数据的平方的平均值的平方根。
因为RMS系统是英制单位一般的有:RMS*25.4/1000=RA举例:RMS64 = 64*25.4/1000= RA 1.6几个常用的如下:RMS250 = RA6.4RMS125 = RA3.2RMS64 = RA1.6RMS32 = RA0.8表面粗糙度外国与中国标准对照N1--0.025um;N2--0.05um;N3--0.1um;N4--0.2um;N5--0.4um;N6--0.8um;N7--1.6um;N8--3.2um;N9--6.3um;N10--12.5um;N11--25um;日本表面粗糙度的老标准。
表面粗糙度的评定参数及其数值的选用

12.5 12.5
图5-16 表面粗糙度代号注法
3.2 30º 3.2
3.2 30º 3.2
图5-17 表面粗糙度在图样上的标注
3.2 3.2
C×45º
3.2 0.4
φ
1.6 1.6
φ
3.2 M
12.5
φ
12.5
表面粗糙度重复表面的注法
a
c)
tp70%、C50%
a
a
b)
Sm0.05max
d)
tp70%min、C50%
其他各项规定的标注.2
③、加工纹理方向、加工方法的标注
纹理方向符号见表5-9。
铣
a
a
⊥
表5-15 表面加工纹理的标注
二、表面粗糙度要求的图样标注
表面粗糙度符号、代号一般标注在可见轮 廓线、尺寸界线、引出线或其延长线上, 见图5-16、5-17。
各种加工方法对应表面粗糙度见表5.6。 ⑴、满足使用要求的前提下,尽量选用较
大的粗糙度数值。 ⑵、同一零件,工作表面比非工作表面粗
糙度值小。 ⑶、摩擦表面比非摩擦表面、滚动摩擦比
滑动摩擦表面粗糙度值小。
参数值的选择.1
⑷、运动速度高、单位压力大的摩擦表面, 比速度低、压力小的表面,Ra数值小。 受交变载荷的表面及易引起应力集中的 部分(圆角、沟槽等),Ra数值小。
表5-4 轮廓微观不平度的平均间距Sm和轮廓的单 峰平均间距S的数值mm
0.006
0.1
1.6
0.0125
0.2
3.2
Sm 、S
0.025
0.4
6.3
表面粗糙度参数Rz、Rmax、Rt、R3z、RPc等的测量

表面粗糙度参数Rz、Rmax、Rt、R3z、RPc等的测量在GB/T3505-2000《产品几何技术规范表面结构轮廓法表面结构术语、定义及参数》中定义了表面粗糙度幅度参数(纵坐标平均值)R a、R q、R sk、R ku和间距参数、混合参数等,虽然该标准等效采用了ISO4287:1997《几何产品规范(GPS)表面特征:轮廓法表面结构的术语、定义及参数》,但这些参数远远不能满足我国目前工业生产的需要,特别是在涉外产品中常常会提出一些非标的表面粗糙度参数的技术要求,例如R max(DIN EN ISO 4287)、RP c(prEN 10049)、R3z(Daimler Benz Standard 31007)等。
这些参数的正确测量直接影响产品符合性的判断,因此生产部门对这些参数的准确测量都有迫切的需求。
同时,对这些参数的正确认识及理解能有效地指导生产过程,在使产品技术指标满足要求的同时可有效降低生产成本。
笔者在实际工作中经常会为一些厂家测量这样的参数,如发动机冷凝管内表面的R max、R t等参数、轴类零件的RP c参数。
现结合实例对这些参数的定义和测量方法作一些说明,以供参考。
一、参数的定义1.参数R z(GB/T3505-2000)在一个取样长度lr内,最大轮廓峰高和最大轮廓谷深之和的高度如图1所示。
<CTSM>图1参数R z示意图</CTSM>这里R z的定义和GB/T3505-1983《表面粗糙度术语表面及其参数》中的定义已经完全不同。
GB/T3505-1983中R z符号曾用于指示“不平度的十点高度”。
正在使用中的一些表面粗糙度测量仪器大多只能测量以前的参数R z。
因此,采用现行的技术文件和图样时必须小心慎重,因为用不同类型的仪器按不同的规定计算所取得的结果之间的差别,并不都是非常微小而可忽略的。
'2.参数R max(DIN EN ISO 4287)参数R max与参数R zi之间有些关系,因此首先介绍R zi的定义。
表面粗糙度的评定

表面粗糙度的评定表面粗糙度的评定表面粗糙度的评定对于具有表面粗糙度要求的零件表面,加工后需要测量和评定其表面粗糙度的合格性。
1. lc滤波器(lc profile filter)lc滤波器是指确定粗糙度与波纹度成分之间相交界限的滤波器2. ls滤波器(ls profile filter)ls滤波器是指确定存在于表面上的粗糙度与比它更短的波的成分之间相交界限的滤波器。
3.原始轮廓(primary profile)原始轮廓是指在应用短波长滤波器ls之后的总的轮廓。
4.粗糙度轮廓(roughness profile)粗糙度轮廓是对原始轮廓采用lc滤波器抑制长波成分以后形成的轮廓。
这是故意修正的轮廓。
以下所涉及到的轮廓,若无特殊说明,均指粗糙度轮廓。
评定基准为了合理、准确地评定被测表面的粗糙度,需要确定间距和幅度两个方向的评定基准,即取样长度、评定长度和轮廓中线。
1. 取样长度(lr )取样长度是指用于判别被评定轮廓不规则特征的X 轴向上的长度,即测量和评定表面粗糙度时所规定的X 轴方向上的一段长度,取样长度在数值上与lc 滤波器的标志波长相等。
X 轴方向与间距方向一致。
规定取样长度的目的是为了限制和减弱被测表面其它几何形状误差,特别是表面波纹度对测量、评定表面粗糙度的影响。
表面越粗糙,取样长度就越大。
2. 评定长度ln(evaluation length)用于判别被评定轮廓的X 轴方向上的长度。
由于零件表面粗糙度不一定均匀,在一个取样长度上往往不能合理地反映整个表面粗糙度特征,因此,在测量和评定时,需规定一段最小长度作为评定长度。
评定长度包含一个或几个取样长度,如图4-2 所示。
一般取ln =5lr ,如被测表面均匀性较好,测量时可选ln <5lr ;均匀性差的表面,可选ln >5lr 。
3. 轮廓中线(mean lines)用轮廓滤波器lc 抑制了长波轮廓成分相对应的中线。
即具有几何轮廓形状并划分轮廓的基准线。
粗糙度检测标准

3.2
用任何方法获得的表面,Ra的上限值为3.2μm
3.2
用去除材料方法获得的表面,Ra的上限值为3.2μm
3.2
用不去除材料方法获得的表面,Ra的上限值为3.2μm
1.6
光面
可辨加工痕迹方向
金刚石、车刀精车、精铰、拉力加工、精磨、研磨、抛光
要求保证定心剂配合特性的表面,如轴承配合表面、锥孔等
0.6
微辩加工痕迹方向
要求能长期保持规定的配合特性,如标准公差为IT6、IT7的轴和孔
一般的钻孔、倒角、没有要求的自由表面
50
可见刀痕
25
微见刀痕
12.5
半光面
可见加工痕迹
精车、精刨、精铣、刮研和粗研
支架、箱体和盖等的非配合卖弄,一般螺纹支撑面
6.3
微见加工痕迹
箱、盖、套筒要求紧贴的表面,键和键槽的工作表面
3.2
不可见加工痕迹
要求有不精确定心及配合特性的表面,如支架孔、衬套、带轮工作表面
3.21Βιβλιοθήκη 6用去除材料方法获得的表面,Ra上限值为3.2μm,下限值为1.6μm
Ry3.2
用任何方法获得的表面,Ry的上限值为3.2μm
Rz200
用不去除材料方法获得的表面,Rz的上限值为200μm
Rz3.2
Rz.1.6
用去除材料方法获得的表面,Rz的上限值为3.2μm,下限值为1.6μm
3.2
Ry12.5
用去除材料方法获得的表面,Ra的上限值为3.2μm,Ry的上限值为12.5μmRy
粗糙度检测标准
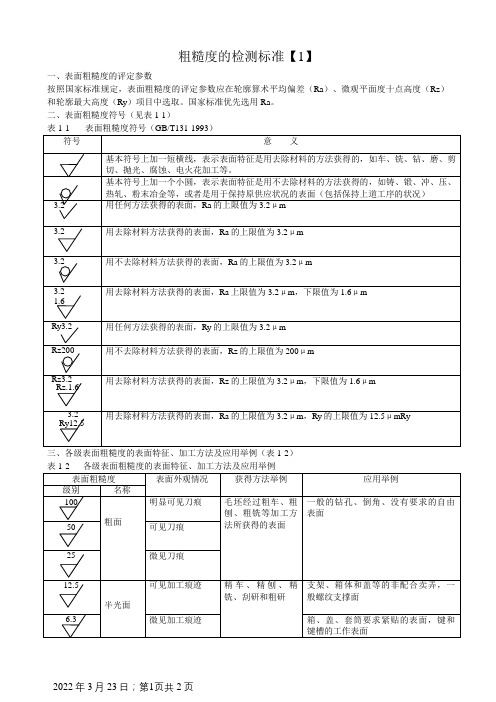
3.2
用任何方法获得的表面,Ra的上限值为3.2μm
3.2
用去除材料方法获得的表面,Ra的上限值为3.2μm
3.2
用不去除材料方法获得的表面,Ra的上限值为3.2μm
用去除材料方法获得的表面,Ra的上限值为3.2μm,Ry的上限值为12.5μmRy
三、各级表面粗糙度的表面特征、加工方法及应用举例(表1-2)
表1-2各级表面粗糙度的表面特征、加工方法及应用举例
表面粗糙度
表面外观情况
获得方法举例
应用举例
级别
名称
100
粗面
明显可见刀痕
毛坯经过粗车、粗刨、粗铣等加工方法所获得的表面
粗糙度的检测标准【1】
一、表面粗糙度的评定参数
按照国家标准规定,表面粗糙度的评定参数应在轮廓算术平均偏差(Ra)、微观平面度十点高度(Rz)和轮廓最大高度(Ry)项目中选取。国家标准优先选用Ra。
二、表面粗糙度符号(见表1-1)
表1-1表面粗糙度符号(GB/T131-1993)
符号
意义
基本符号上加一短横线,表示表面特征是用去除材料的方法获得的,如车、铣、钻、磨、剪切、抛光、腐蚀、电火花加工等。
一般的钻孔、倒角、没有要求的自由表面
50
可见刀痕
25
微见刀痕
12.5
半光面
可见加工痕迹
精车、精刨、精铣、刮研和粗研
支架、箱体和盖等的非配合卖弄,一般螺纹支撑面
6.3
微见加工痕迹
箱、盖、套筒要求紧贴的表面,键和键槽的工作表面
表面粗糙度
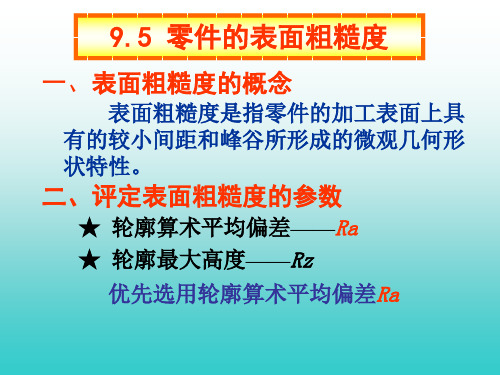
M
12.5
3.2
★ 在不同方向的表面上标注时,代号中的数 字及符号的方向必须按下图规定标注。
3.2
30° 3.2
3.2
3.2
30°
3.2
代号中的数字方向应与尺寸数字的方向一致。
3.2
⒊ 标注示例
6.3 3.2 6.3 2×45°
×
6.3
3.2 ×
1.6 6.3 3.2
★ 符号的尖端必须 从材料外指向被 标注的表面。
2.形位公差代号
在图样中,形、位公差一般采用代号标注,如下图所示。各项形位公 差符号、代号的含义及标注方法请参见 示例一、示例二。
图8-21 形位公差代号与基准代号
形、位公差标注示例一
返回
形、位公差标注示例二
返回
9.7 画零件图的步骤和方法
一、画图前的准备 ⒈ 了解零件的用途、结构特点、材料及相 应的加工方法。 ⒉ 分析零件的结构形状,确定零件的视图 表达方案。 二、画图方法和步骤: 例如画端盖的零件图 ⒈ 定图幅 根据视图数量和大小, 选择适当的绘图比例,确 定图幅大小。
最大极限尺寸≥实际尺寸≥最小极限尺寸。
最小极限尺寸 49.992
最大极限尺寸 50.008
50
⒉
尺寸偏差和尺寸公差
0.016
–0.008 最小极限尺寸 φ49.992
基本尺寸
上偏差 下偏差
统称极限偏差
尺寸公差(简称公差): 允许实际尺寸的变动量。
偏差可 正可负
公差=最大极限尺寸-最小极限尺寸 =上偏差-下偏差
H1
60° 60°
数字与字母高度
2.5 0.25
3.5
- 1、下载文档前请自行甄别文档内容的完整性,平台不提供额外的编辑、内容补充、找答案等附加服务。
- 2、"仅部分预览"的文档,不可在线预览部分如存在完整性等问题,可反馈申请退款(可完整预览的文档不适用该条件!)。
- 3、如文档侵犯您的权益,请联系客服反馈,我们会尽快为您处理(人工客服工作时间:9:00-18:30)。
• 选择原则:一般按五个取样长度来确定。 4.轮廓中线m:是评定表面粗糙度数值的基准线。具有几
何轮廓形状与被测表面几何形状一致,并将被测轮廓加 以划分的线。类型有: • (1)最小二乘中线:
使轮廓上各点的轮廓偏转距y(在测量方向上轮廓上 的点至基准线的距离)的平方和为最小的基准线。
准面1相接触,基准面采用光学玻璃制成的平面或圆弧面,并相对被测表面或工作台面定
位,从而使传感器运行的轨迹依赖于这个参考基准面,根据被测表面的外形作直线或某一 曲率的圆弧线运动。这时触针所描绘的将是包括粗糙度、波纹度相形状误差在内的实际表 面轮廓图形。这种方法对拖动传感器运行的驱动机构(导轨)没有严格要求。
Ry y p max yv max
表面粗糙度的三个水平参数: 轮廓微观不平度的平均间距Sm 轮廓单峰平
均间距S 轮廓支承长度率tp
图4-4 表面粗糙度的水平参数
4.轮廓微观不平度的平均间距Sm
❖ 含有一个轮廓峰和相邻轮廓谷的一段中线长度Sm (图4-4),称为轮廓微观不平度间距。
Sm
1 n
直线,寻头
• 上下位移量非常小加固9—14(a)所示。但若轮廓哆距增大PS头的垂盲位移变化亦将随着增大,直到 它完全和触
• 针同步地作上下运动,如图L14(b).<c)所示,此时圆弧形导头显然E个适用。
•
由于e6针和导头不可能在表面的同一点上接触(不能同袖),因此综合其结果*除了幅度变化LJ
外,还取决于
实际轮廓图
横向实际轮廓图
2.取样长度l:用于判别和测量表面粗糙度时所规定的一段基
准线长度。 • 量取方向:它在轮廓总的走向上。 • 目的:限制和削弱表面波度对表面粗糙度测量结果的影响
。 (几何滤波)
• 选择原则: 5≤ l p /3
• 常用的取样长度见表4-1。
3.评定长度L : 评定轮廓所必须的一段长度,它包括一个或数个取样长 度。
• 4.表面缺陷:评定过程中,不应把表面缺陷(如沟槽、气孔、 划伤等)包含进去。必要时,应单独规定表面缺陷要求。
• 5 .测量部位:为了完整地反映零件表面的实际状况,需要在其 若干具有代表性的位置上进行测量,一般可采取在均匀分布的三 个以上的位置上取其平均值作为最终结果。
1.5 表而粗糙度测量方法综述及测量的 基本原则
• 1.L 2 表面粗糙度测量的基本原则
•
(1)测量方向
•
按现行标准所定义的各种粗糙度评定参数,是基于轮廓法确定数值,是在被测表面的法向截面上的
实际轮廓上进行测量的结果。由于垂直于被测表面的法向截面存在各种不同的测量方向.所以规定在垂
直于加工纹理力向的d向截面(参R图g”8)测得的结果,称作横向轮廊的表面粗糙度数值(d);在平行于
加工纹理方向的5向截面上所作的测量,称为纵向轮廓的粗糙度数值(6)。试验表明,大多数的切削加工
表
• 面,在横向轮廓上测得的粗糙度数值比较大,只是有的该铣加工和个别端铣加工表面,在纵向轮廓上会 有较大的数值。 如果在被测表面上难以确定加工纹理方向,以及某些加工纹理紊乱或不存在固定方向 的表面,应分别在多个方向上测量,以获取最大参故值为结果.或取其峰谷高度的最大值,计算一个区 域的测量结果。
• 粗糙度测量方法主要是以不同类型的传感器所反映的测量原理来分类的 。表9—l 4列出了各类转换形式的传感器。运算装置包括信号放大器、 滤波器和各种型式的计算处理(如信号变换、模数转换、时控、数字计算
等)装置。输出设备包括指针式电量表、记录器、光电输出器、电传打字 机、磁带输出器、Tv显示屏、绘图仪等。其中,传感器是基本组成部分 ,在取得表面测量信号以后,亦可用人工进行计算处理给出结果。
• (2)算术平均中线: 在取样长度范围内,划分实际轮廓为上、下两部分,
且使上下两部分面积相等的线。
轮廓的算术平均中线
二、评定参数及数值:
❖ 对评定参数的基本要求: (1)正确、充分反映表面微观几何形状特征; (2)具有定量的结果; (3)测量方便。
❖ 国标从水平和高度两方向各规定了三个评定参数:三个基本 参数(水平),三个附加的评定参数(高度)
5
5
y pi yvi
Rz i1
i 1
5
❖ 在取样长度内,也可从平行于轮廓中线m的任意一根线算起, 计算被测轮廓的五个最高点(峰)到五个最低点(谷)之间 的平均距离
Rz
=
(h2 h4 ...h10 ) (h1 h3 ...h9 ) 5
3.轮廓最大高度
❖ 在取样长度内,轮廓峰顶线和轮廓谷底线之间的距离 (图4-3)。
感谢下 载
tp = (p /L) ×100℅
轮廓支承长度率
三、一般规定
• 1.为保证零件的表面质量,可按功能需要规定表面粗糙度。
• 2 .在规定表面粗糙度要求时,必须给出粗糙度参数值和测定时 的取样长度值两项基本要求,必须时也可规定表面纹理、加工方 法顺序和不同区域的粗糙度等附加要求。
• 3.测量方向:表面粗糙度各参数的值是指在垂直于基准表面( 具有几何表面的形状,它的方位和实际表面走向一致)的各截面 上测得。对给定的表面,如截面方向与高度参数最大值的方向一 致,则可不规定测量方向,否则应在图样上表示截面方向。
2.表面粗糙度:是一种微观几何形状误差又称微观不平度。 3.表面粗糙度的产生原因:在加工过程中,刀具和零件表面
间产生磨擦、高频振动及切削时在工作表面上留下的微观 痕迹。
二.表面粗糙度的影响
• 表面粗糙度对机器零件的使用性能有着重要的影响,主要表 现在:
1.对摩擦和磨损的影响 2.对配合性的影响 3.对接触刚度的影响 4.对疲劳强度的影响 5.对抗腐蚀性的影响 6.对结合密封性的影响 • 此外表面粗糙度还影响检验零件时的测量不确定度、零件外
§4-1 表面粗糙度的评定参数
主要内容:
1、主要术语及定义 取样长度L 评定长度L
n
轮廓中线m 2、6个评定参数
3个基本、3个附加 3、一般规定
重点: 3个基本评定参数
一.主要术语及定义
1.实际轮廓:平面与实际表面相交所得的轮廓线。
按照相截方向的不同,它又可分为横向实际轮廓和纵向实 际轮廓。在评定或测量表面粗糙度时,除非特别指明,通 常均指横向实际轮廓,即与加工纹理方向垂直的截面上的 轮廓。
• 两者相对运动的相位变化。导头相对于触针的位置,无论是在一条测量线上还足在侧边,都会产生 相位的影响。同
• 相位时,触针相对于导头的位移量减小(加固9‘14L);相位差189’时,则位移量增大(如图9—14c )。由于一般加11
• 表面的粗杨度间距呈不规则状态,5然测得的轮廓图形E失真,但平均效应恰与实际测员结果相近似 。
• 2.1.2测量基准线
•
传感器中触针的运行轨迹必须沿着与被测表面基本平行的基准线移动.才能获得其实
的被测轮廓形状。触针式仪器建立测量基准线的方式有独立基准和相对基准两类:
•
(I)独立其难
Hale Waihona Puke •独立的测量基准.是使传感器按直线或一定的弧形线运动。图9—23为较易调整的直
线或弧形线测量装置的示意图。在传感器壳体中触针3的上方有——半球形触头2,它和基
1、轮廓算术平均偏差Ra
在取样长度L内,轮廓偏转距绝对值的算术平均值。
用公式表示为:
1l
Ra L 0 y(x) dx
Ra
1 n
n i 1
yi
Rz
图4-3 表面粗糙度的高度参 数
2.微观不平度十点高度
❖ 在取样长度内五个最大的轮廓峰高的平均值与五个最大的轮
廓谷深的平均值之和,如图4-3所示。用公式表示为:
•
(2)表面缺陷
•
在表面上偶然出现的微观不平度,如划痕、碰伤,以及并非由于加工造成的材料缺陷,如气孔.裂
纹、砂眼均属于表面缺陷。在表面祖糙度的评定中不应把表面缺陷包含进去,因此在测量时.原则上应
将其影响排除在外,尤其是对于比—股加工痕迹(微观不平度)的深度或宽度大得多的缺陷要特别注意。
如果零件表面不允许有某种缺陷或对它要加以控制,应另作规定。
第四章
表面粗糙度的测 量
一.表面形貌误差的概念与形成
1.表面形貌误差分类: 实际加工表面通常包含如下三种表面形貌误差:
• 表面粗糙度:波距λ小于1mm,大体呈周期性变化, 属于微观几何形状误差;
• 表 面 波度:波距λp在1~10mm,呈周期性变化, 属于中间几何形状误差;
• 形状 误 差:波距大于10mm,无明显周期性变化, 属于宏观几何状误差 。
—13(a)所示,传感器壳
• 体通过铰链和驱动器相连接,在触针3附近的圆弧形导头1装在传感器壳休上.测量时传感
器通过导头支承在被
• 测表面5上,由此形成的测量基准线为圆弧形导头曲率中心的移动轨迹,所测得的轮廓信 息是触针相对于导头
• (基准线)的垂直位移量,
• 使用圆弧形导头时.若轮廓哆相当密集,导头的半径k峰距大很多,则导头的移动软迹将近似成一
形的美观等等。
三.表面形貌测量的特点与范围
• 特点:通常为量程小、测量分辨率高(nm)、
• 表面粗糙度测量的范围
现在表面分析技术已远走出机器零件,如:
• 微电子工业:硅片、磁盘表面、光盘、光学元件、窗片 • 材料科学:表面形貌分析、材料微裂纹 • 生物工程:细胞生物、芯片、遗传学 • 科学研究:纳米技术、物理、化学、生物等基础科学等
•
另一种形式为利用精密导轨结构,如直线性很好的轴带动传感器作直线运动,形成独
立的测量基准线。
•
采用独立基淮需要配备复杂的附属装置(或具有精密导轨的驱动装置),在使用时还需
要精细调整,因此其应