液压系统设计计算实例
液压系统设计计算实例

12.13,液压缸的工况图如图12.8所示。
➢ 设计内容与方法
4.拟定液压系统原理图
➢ 设计内容与方法 5.液压元件选择
(1)选择液压泵 ①液压泵最高工作压力 管路总压力损失ΣΔp初步按
0.6MPa估算,有Pp≥pmax+ΣΔp=(4.5+0.6)MPa=5.1MPa ②液压泵最大供油量 取K=1.1,有
➢ 设计内容与方法
3.液压缸参数确定
(5) 采最用低无稳杆定腔速进度油验,算单向最行低程速调度速为阀工调进速时,vm查in=得5最0m小m稳/m定in流,量工进时,
qmin=0.1×10-3m3/min,则
A1≥ qmin 0.1106
vm in
ቤተ መጻሕፍቲ ባይዱ
50
mm2=2 000mm2 满足最低速度要求。
(6) 绘制液压缸工况图 计算各工况下的压力、流量和功率汇总于表
液压与气动控制
F 33667 p 4.5106
4A 4 7482106
3.14
➢ 设计内容与方法
3.液压缸参数确定
( (12) )选 确4 定 定工 液作 压4压 缸力 有效p 工根作据面表积1A2.3和表12.4,初选工作压力p=4.5MPa。
4
4
A= 4 m24=7 482×10-6m2
(3)确定缸筒内径D、活塞杆直径d
➢ 设计内容与方法 5.液压元件选择
①油管 初步选取v=4m/s,则d=m=14.5×103m=14.5mm 查手册确定采用φ18×1.5的紫铜管。 ②滤油器 采用XU-J40×80型过滤器。 ③油箱容积的确定 V=(5~7)qP=(5~7)×20L=(100~140)L
➢ 设计内容与方法
液压系统设计计算实例3
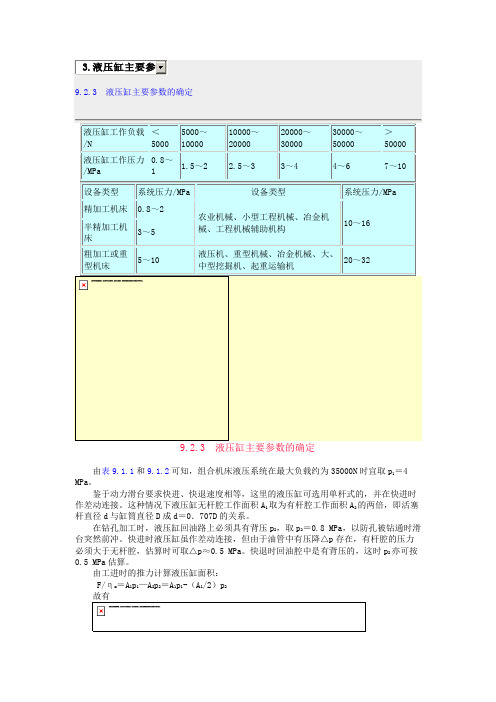
3.液压缸主要参数9.2.3 液压缸主要参数的确定液压缸工作负载/N <50005000~1000010000~2000020000~3000030000~50000>50000液压缸工作压力/MPa 0.8~11.5~22.5~33~44~67~10设备类型系统压力/MPa设备类型系统压力/MPa 精加工机床0.8~2农业机械、小型工程机械、冶金机械、工程机械辅助机构10~16半精加工机床3~5粗加工或重型机床5~10液压机、重型机械、冶金机械、大、中型挖掘机、起重运输机20~329.2.3 液压缸主要参数的确定由表9.1.1和9.1.2可知,组合机床液压系统在最大负载约为35000N时宜取p1=4 MPa。
鉴于动力滑台要求快进、快退速度相等,这里的液压缸可选用单杆式的,并在快进时作差动连接。
这种情况下液压缸无杆腔工作面积A1取为有杆腔工作面积A2的两倍,即活塞杆直径d与缸筒直径D成d=0.707D的关系。
在钻孔加工时,液压缸回油路上必须具有背压p2,取p2=0.8 MPa,以防孔被钻通时滑台突然前冲。
快进时液压缸虽作差动连接,但由于油管中有压降△p存在,有杆腔的压力必须大于无杆腔,估算时可取△p≈0.5 MPa。
快退时回油腔中是有背压的,这时p2亦可按0.5 MPa估算。
由工进时的推力计算液压缸面积:F/ηm=A1p1—A2p2=A1p1-(A1/2)p2故有D= =11.12cm;d=0.707D=7.86 cm当按GB 2348-80将这些直径圆整成就近标准值时得:D=11 cm,d=8 cm。
由此求得液压缸两腔的实际有效面积为:A1=πD2/4=95.03 cm2,A2=π(D2-d2)/4=44.77 cm2。
经检验,活塞杆的强度和稳定性均符合要求。
根据上述D与d的值,可估算液压缸在各个工作阶段中的压力、流量和功率,如表9.2.2所示,并据此绘出工况图如图9.2.2所示。
表9.2.2 液压缸在不同工作阶段的压力、流量和功率值工况负载F/N回油腔压力p2/Mpa进油腔压力p1/Mpa输入流量Q/(L/min)输入功率P/kw计算式快进(差动) 启动2180 p2=0 0.434 --p1=(F+A2Δp)/(A1-A2)q=(A1-A2)υlP=p1q1回速l738 p2=p l+△p(△p=0.5MPa)0.79l --恒速1090 0.662 35.19 0.39工进34943 0.8 4.054 0.5 0.034 p1=(F+p2A2)/A l q=A lυ2P=p1q快退启动2180 p2=0 0.487 --p1=(F+p2A l)/A2q=A2υ2P=p l q加速17380.51.45 --恒速1090 1.305 31.34 0.68。
液压传动系统设计计算例题
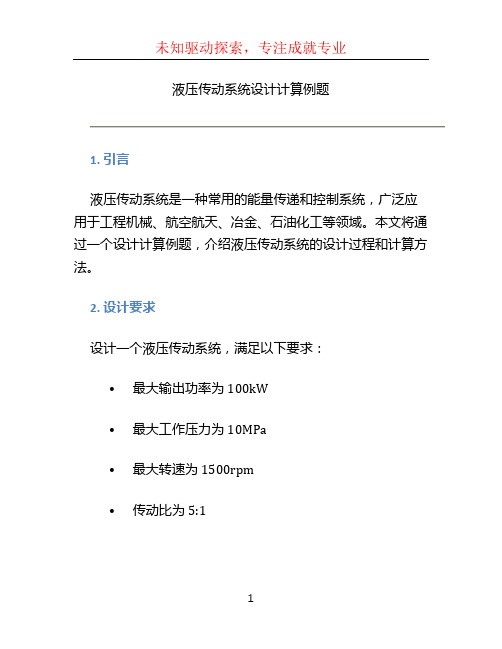
液压传动系统设计计算例题1. 引言液压传动系统是一种常用的能量传递和控制系统,广泛应用于工程机械、航空航天、冶金、石油化工等领域。
本文将通过一个设计计算例题,介绍液压传动系统的设计过程和计算方法。
2. 设计要求设计一个液压传动系统,满足以下要求:•最大输出功率为100kW•最大工作压力为10MPa•最大转速为1500rpm•传动比为5:13. 功率计算根据设计要求,最大输出功率为100kW,转速为1500rpm,可以通过以下公式计算液压机的排量:功率(kW)= 排量(cm^3/rev) × 转速(rpm) × 压力(MPa) × 10^-6由于传动比为5:1,液压泵的排量为液压马达的5倍,因此液压泵的排量为:排量(cm^3/rev) = 功率(kW) / (转速(rpm) × 压力(MPa) × 10^-6 × 5)= 100 / (1500 × 10 × 10^-6 × 5)= 0.133 cm^3/rev4. 泵和马达的选择根据计算结果,液压泵的排量为0.133 cm^3/rev。
在实际中,可以选择一个接近或等于该排量的标准泵来满足需求。
假设我们选择了一台0.15 cm^3/rev的液压泵。
由于传动比为5:1,液压马达的排量为液压泵的1/5,因此液压马达的排量为:排量(cm^3/rev) = 液压泵排量 / 5= 0.15 / 5= 0.03 cm^3/rev同样地,我们可以选择一个接近或等于该排量的标准马达。
5. 油液流量计算油液流量可以通过以下公式计算:流量(L/min) = 排量(cm^3/rev) × 转速(rpm) / 1000液压泵的流量为:流量(L/min) = 0.15 × 1500 / 1000= 0.225 L/min液压马达的流量为:流量(L/min) = 0.03 × 1500 / 1000= 0.045 L/min6. 液压系统元件选择在设计液压传动系统时,除了液压泵和液压马达,还需要选择其他的液压元件,如油箱、油管、阀门等。
液压系统设计计算公式
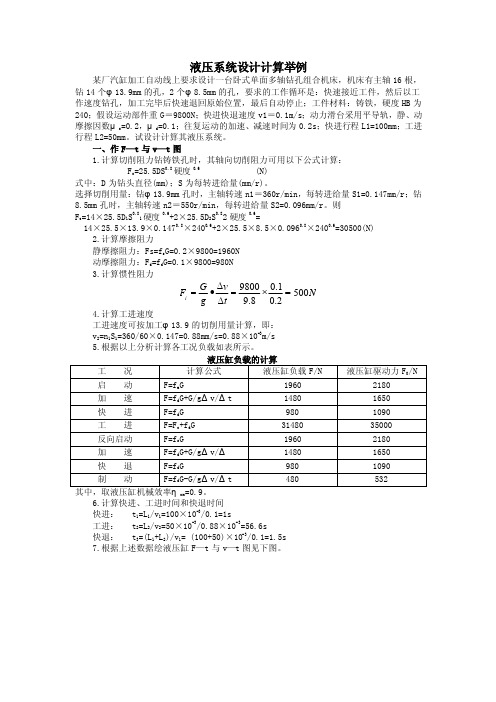
液压系统设计计算举例某厂汽缸加工自动线上要求设计一台卧式单面多轴钻孔组合机床,机床有主轴16根,钻14个φ13.9mm 的孔,2个φ8.5mm 的孔,要求的工作循环是:快速接近工件,然后以工 作速度钻孔,加工完毕后快速退回原始位置,最后自动停止;工件材料:铸铁,硬度HB 为240;假设运动部件重G =9800N ;快进快退速度v1=0.1m/s ;动力滑台采用平导轨,静、动摩擦因数μs =0.2,μd =0.1;往复运动的加速、减速时间为0.2s ;快进行程L1=100mm ;工进行程L2=50mm 。
试设计计算其液压系统。
一、作F —t 与v —t 图1.计算切削阻力钻铸铁孔时,其轴向切削阻力可用以下公式计算:F c =25.5DS 0.8硬度0.6(N)式中:D 为钻头直径(mm);S 为每转进给量(mm/r)。
选择切削用量:钻φ13.9mm 孔时,主轴转速n1=360r/min ,每转进给量S1=0.147mm/r ;钻8.5mm 孔时,主轴转速n2=550r/min ,每转进给量S2=0.096mm/r 。
则F c =14×25.5D 1S 0.81硬度0.6+2×25.5D 2S 0.82硬度0.6=14×25.5×13.9×0.1470.8×2400.6+2×25.5×8.5×0.0960.8×2400.6=30500(N) 2.计算摩擦阻力静摩擦阻力:Fs=f s G=0.2×9800=1960N 动摩擦阻力:F d =f d G=0.1×9800=980N 3.计算惯性阻力4.计算工进速度工进速度可按加工φ13.9的切削用量计算,即:v 2=n 1S 1=360/60×0.147=0.88mm/s=0.88×10-3m/s 5.根据以上分析计算各工况负载如表所示。
液压课程设计-卧式钻、镗组合机床液压系统

设计一台卧式钻、镗组合机床液压系统1.液压系统用途(包括工作环境和工作条件)及主要参数:1)工作循环:“快进—工进—死挡铁停留—快退—原位停止”。
组合机床动力滑台工作循环2)工作参数轴向切削力12000N,移动部件总重10000N,工作循环为:“快进——工进——死挡铁停留——决退——原位停止”。
行程长度为0.4m,工进行程为0.1,快进和快退速度为0.1m/s,工过速度范围为0.0003~0.005,采用平导轨,启动时间为0.2s。
要求动力部件可以手动调整,快进转工进平稳、可靠。
2.执行元件类型:液压油缸设计内容1. 拟订液压系统原理图;2. 选择系统所选用的液压元件及辅件;3. 验算液压系统性能;4. 编写计算说明书。
目录序言: (5)1 设计的技术要求和设计参数 (6)2 工况分析 (6)2.1确定执行元件 (6)2.2分析系统工况 (6)2.3负载循环图和速度循环图的绘制 (8)2.4确定系统主要参数2.4.1初选液压缸工作压力 (9)2.4.2确定液压缸主要尺寸 (9)2.4.3计算最大流量需求 (11)2.5拟定液压系统原理图2.5.1速度控制回路的选择 (12)2.5.2换向和速度换接回路的选择 (12)2.5.3油源的选择和能耗控制 (13)2.5.4压力控制回路的选择 (14)2.6液压元件的选择2.6.1确定液压泵和电机规格 (16)2.6.2阀类元件和辅助元件的选择 (17)2.6.3油管的选择 (19)2.6.4油箱的设计 (20)2.7液压系统性能的验算2.7.1回路压力损失验算 (22)2.7.2油液温升验算 (22)序言作为一种高效率的专用机床,组合机床在大批、大量机械加工生产中应用广泛。
本次课程设计将以组合机床动力滑台液压系统设计为例,介绍该组合机床液压系统的设计方法和设计步骤,其中包括组合机床动力滑台液压系统的工况分析、主要参数确定、液压系统原理图的拟定、液压元件的选择以及系统性能验算等。
液压系统设计计算实例(共18张PPT)优秀
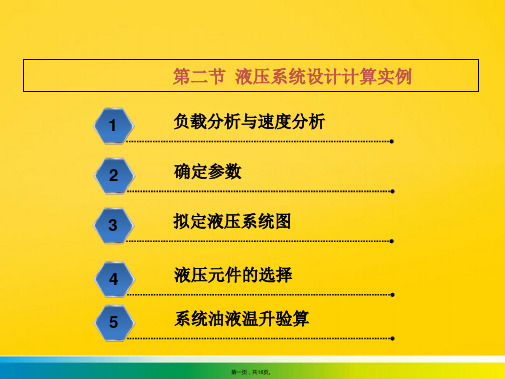
3)计算液压缸在工作循环各阶段的压力、流量和功率 值
差动时液压缸有杆腔压力大于无杆腔压力,取两腔间回路及阀的压 力损失为0.5MPa,则p2= p1+0.5MPa。计算结果见表9.5。
由教材中9-5表即可画出液压缸的工况图(略)。
第七页,共18页。
表9-5:液压缸工作循环各阶段压力、流量和功率值
工作循环 计算公式 量 输入功率
负载
P kW
快 启动加速
p1=F+A2(p2-p1) 3289
A1 -A2
q1=(A1 -A2)v1
p2= p1+0.5
进恒速
P= p1 q1
2178
回油背进油压力 输入流
p1MPa
q110-3 m3/s
-
0.88
0.50
0.44
p1= F+ A2p2
20mm/min~120mm/min按上述分析可绘制出负载循环图和速度循环图(略)
。
第三页,共18页。
第四页,共18页。
2.确定参数
1)初选液压缸的工作压力
由最大负载值查教材中表9-3,取液压缸工作压力为4MPa。
2)计算液压缸结构参数
为使液压缸快进与快退速度相等,选用单出杆活塞缸差动连接的方式实现快进
采用平(导轨4,)其换摩擦向系回数f=路0. :为了换向平稳,选用电液换向阀。为便于实现液压缸中位停止和
0大0流31量泵的输差入动功0率.连经接计算,为采70.用三位五通阀。
(5)压力控制回路:系统在工作状态时高压小流量泵的工作压力由溢 流阀调整,同时用外控顺序阀实现低压大流量泵卸荷。
第九页,共18页。
(3 据此选用Y112M—6—B5立式电动机,其额定功率为2.
液压系统的设计计算举例
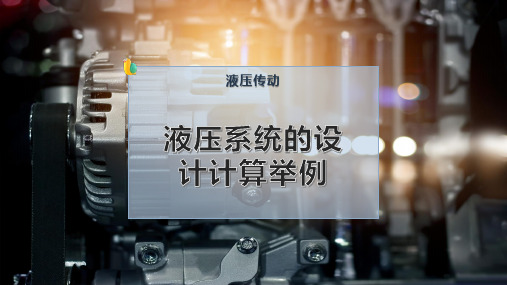
作缸的小腔,即从泵的出口到缸小腔之间的压力损失 Δp = 5.5×105 MPa ,于是小泵出
口压力 pp1 = 21.56×105 MPa (小泵的总效率 η 1 = 0.5 ),大泵出口压力 pp2 =
23.06×105 MPa (大泵的总效率 η 2 = 0.5 )。故电机功率为
P pp1q1 pp2q2 21.56 105 0.167 103 W 23.06 105 0.267 103 W 1 951.5 W
= 0.5 ,大泵出口压力 pp2 = 15.18×105 MPa (大泵的总效率 η 2 = 0.5 )。故电机功率
为
P1
pp1q1 1
pp 2 q2 2
13.68 105 0.167 103 0.5
W 15.18 105 0.267 103 0.5
W
1 267.5 W
(2)工进
小泵的出口压力 pp1 = p1 +Δp1 = 32.19×105 MPa ,大泵卸载,卸载压力取 pp2 =
液压传动
液压系统的设计计算举例
1.1 分析工况及主机工作要求,拟定液压系统方案 1.2 参数设计 1.3 选择元件 1.4 液压系统性能验算
液压系统的设计计算举例
1.1 液分析工况及主机工作要求,拟定液压系统方案
(一) 确定执行元件类型
(二) 确定执行元件的负载、速度变化范围
Fw 18 000 N
1
2
0.5
0.5
综合比较,快退时所需功率最大。据此查产品样本选用Y112M—6型异步电机,
电机功率2.2 kW,额定转速为940 r/min。
(三) 选择液压阀
根据液压阀在系统中的最高工作压力与通过该阀的最大流量,可选出这些元件的 型号及规格。选定的元件列于表中。
液压系统设计计算与应用实例

自动化焊接设备中液压驱动方案设计
焊接机器人
采用液压驱动可实现高精 度、高速度的焊接作业, 提高生产效率和焊接质量。
焊接变位机
通过液压缸和马达的驱动, 实现工件的快速翻转和精 确定位,方便焊接操作。
焊接夹具
利用液压缸的夹紧力,保 证工件在焊接过程中的稳 定性和精度。
总装线上举升、翻转机构实现方式
举升机构
环保型液压油
使用生物可降解液压油,减少 对环境的影响和污染。
能量回收技术
利用液压蓄能器等元件回收系 统中的能量,提高能量利用率 。
智能化节能控制系统
通过传感器和控制系统实时监 测和调整液压系统的运行状态
,实现智能化节能控制。
06 故障诊断与维护保养策略
常见故障类型及诊断方法
液压泵故障
检查泵的运转声音、温度和输出压力,判断 是否需要更换或维修。
定期清洗液压油箱和滤网,保持油液的清 洁度。
检查液压泵和马达
校验压力和流量
定期检查液压泵和马达的运转情况,及时 发现并处理异常。
定期校验系统的压力和流量,确保系统工作 正常。
应急处理措施和备件库存管理建议
应急处理措施
制定针对不同故障的应急处理预案, 包括临时替代方案、现场快速维修方 法等。
备件库存管理建议
液压油缸故障
检查油缸的密封件是否损坏,活塞杆是否弯 曲或磨损。
液压阀故障
观察阀的工作状态和油液流动情况,检查阀 芯是否卡滞或磨损。
液压管路故障
检查管路的连接是否松动或泄漏,判断是否 需要更换或紧固。
预防性维护保养计划制定
定期更换液压油
清洗液压油箱和滤网
根据设备使用情况和厂家建议,制定合理 的液压油更换周期。
- 1、下载文档前请自行甄别文档内容的完整性,平台不提供额外的编辑、内容补充、找答案等附加服务。
- 2、"仅部分预览"的文档,不可在线预览部分如存在完整性等问题,可反馈申请退款(可完整预览的文档不适用该条件!)。
- 3、如文档侵犯您的权益,请联系客服反馈,我们会尽快为您处理(人工客服工作时间:9:00-18:30)。
P=
p P1 q1 + p P 2 q 2
ηP
=27.313 kW 考虑到注射时间较短,不过 3s, 而电动机一般允许短时间超载 25%, 这样电动机功率还可降低一些。 P=27.313×100/125 =21.85 kW 验算其他工况时,液压泵的驱动 功率均小于或近于此值。 查产品样本, 选用 22kW 的电动机。 5.3 液压阀的选择 选择液压阀主要根据阀的工作压 力和通过阀的流量。本系统工作压力 在 7MPa 左右, 所以液压阀都选用中、 高压阀。所选阀的规格型号见表 5。 5.4 液压马达的选择 在 3.3 节已求得液压马达的排量 为 0.8L/ r,正常工作时,输出转矩 769N.m,系统工作压力为 7MPa。 选 SZM0.9 双斜盘轴向柱塞式液 压马达。其理论排量为 0.873L/r,额定压力为 20 MPa,额定转速为 8~l00r/min, 最高转矩为 3057N·m,机械效率大于 0.90。 5.5 油管内径计算 本系统管路较为复杂,取其主要几条(其余略),有关参数及计算结果列于表 6。
9
5.6 确定油箱的有效容积 按下式来初步确定油箱的有效容积 V=aqV 已知所选泵的总流量为 201.4L/min, 这样,液压泵每分钟排出压力油的体积 为 0.2m3。参照表 4—3 取 a=5,算得 有效容积为 V=5×0.2m3=1 m3
6.液压系统性能验算 6.液压系统性能验算
6.1 验算回路中的压力损失 本系统较为复杂, 有多个液压执行元 件动作回路,其中环节较多,管路损失较 大的要算注射缸动作回路, 故主要验算由 泵到注射缸这段管路的损失。 ⑴沿程压力损失 沿程压力损失,主要是注射缸快速注射时进油管路的压力损失。此管路长 5m,管内径 0.032m,快速时通过流量 2.7L/s;选用 20 号机械系统损耗油,正常运 转后油的运动粘度ν=27mm2/s,油的密度ρ=918kg/m3。 油在管路中的实际流速为
6
液压执行元件以及各基本回路确定之后,把它们有机地组合在一起。去掉重复 多余的元件,把控制液压马达的换向阀与泵的卸荷阀合并,使之一阀两用。考虑注 射缸同合模缸之间有顺序动作的要求,两回路接合部串联单向顺序阀。再加上其他 一些辅助元件便构成了 250 克塑料注射机完整的液压系统图,见图 2,其动作循环 表,见表 4。
⑵)注射座移动缸的活塞和活塞杆直径 座移动缸最大载荷为其顶紧之时, 此时缸的回油流量虽经节流阀, 但流量极小, 故背压视为零,则其活塞直径为
Dy =
4F 4 × 3 × 10 4 = m = 0.076m ,取 Dy=0.1m πp1 π × 6.5 × 10 6
由给定的设计参数知,注射座往复速比为 0.08/0.06=1.33,查表 2—6 得 d/D =0.5,则活塞杆直径为: dy=0.5×0.1m=0.05m ⑶确定注射缸的活塞及活塞杆直径 当液态塑料充满模具型腔时, 注射缸的载荷达到最大值 213kN, 此时注射缸活 塞移动速度也近似等于零,回油量极小;故背压力可以忽略不计,这样
1
液压系统设计计算实例
——250 克塑料注射祝液压系统设计计算 大型塑料注射机目前都是全液压控制。其基本工作原理是:粒状塑料通过料斗 进入螺旋推进器中,螺杆转动,将料向前推进,同时,因螺杆外装有电加热器,而 将料熔化成粘液状态,在此之前,合模机构已将模具闭合,当物料在螺旋推进器前 端形成一定压力时,注射机构开始将液状料高压快速注射到模具型腔之中,经一定 时间的保压冷却后,开模将成型的塑科制品顶出,便完成了一个动作循环。 现以 250 克塑料注射机为例,进行液压系统设计计算。 塑料注射机的工作循环为: 合模→注射→保压→冷却→开模→顶出 │→螺杆预塑进料 其中合模的动作又分为:快速合模、慢速合模、锁模。锁模的时间较长,直到 开模前这段时间都是锁模阶段。 1.250 克塑料注射机液压系统设计要求及有关设计参数 1.1 对液压系统的要求 ⑴合模运动要平稳,两片模具闭合时不应有冲击; ⑵当模具闭合后, 合模机构应保持闭合压力, 防止注射时将模具冲开。 注射后, 注射机构应保持注射压力,使塑料充满型腔; ⑶预塑进料时,螺杆转动,料被推到螺杆前端,这时,螺杆同注射机构一起向 后退,为使螺杆前端的塑料有一定的密度,注射机构必需有一定的后退阻力; ⑷为保证安全生产,系统应设有安全联锁装置。 1.2 液压系统设计参数 250 克塑料注射机液压系统设计参数如下: 螺杆直径 40mm 螺杆行程 200mm 最大注射压力 153MPa 螺杆驱动功率 5kW 螺杆转速 60r/min 注射座行程 230mm 注射座最大推力 27kN 最大合模力(锁模力) 900kN 开模力 49kN 动模板最大行程 350mm 快速闭模速度 0.1m/s 慢速闭模速度 0.02m/s 快速开模速度 0.13m/s 慢速开模速度 0.03m/s 注射速度 0.07m/s 注射座前进速度 0.06m/s 注射座后移速度 0.08m/s 2.液压执行元件载荷力和载荷转矩计算 2.液压执行元件载荷力和载荷转矩计算 2.1 各液压缸的载荷力计算 ⑴合模缸的载荷力 合模缸在模具闭合过程中是轻载, 其外载荷主要是动模及其连动部件的起动惯
按表 2—5 取 d/D=0.7,则活 塞杆直径 dh=0.7×0.2m=0.14m, 取 dh=0.15m。 为设计简单加工方便, 将增压 缸的缸体与合模缸体做成一体(见 图 1) ,增压缸 的活塞直径也 为 0.2m。其活塞杆直径按增压比为 5,求得
dz =
2 Dh = 5
0.2 2 = 0.089m ,取 dz=0.09m。 5
FW =
π
4
d2p
式中,d——螺杆直径,由给定参数 知:d=0.04m;p——喷嘴处最大注射压 力,已知 p=153MPa。由此求得 Fw= 192kN。 各液压缸的外载荷力计算结果列于 表 l。取液压缸的机械效率为 0.9,求得 相应的作用于活塞上的载荷力,并列于 表 1 中。 2.2 进料液压马达载荷转矩计算
2
性力和导轨的摩擦力。 锁模时,动模停止运动,其外载荷就是给定的锁模力。 开模时,液压缸除要克服给定的开模力外,还克服运动部件的摩擦阻力。 ⑵注射座移动缸的载荷力 座移缸在推进和退回注射座的过程中, 同样要克服摩擦阻力和惯性力, 只有当 喷嘴接触模具时,才须满足注射座最大推力。 ⑶注射缸载荷力 注射缸的载荷力在整个注射过程中是变化的,计算时,只须求出最大载荷力。
VM =
2πTW 2 × 3.14 × 796 3 = m / r = 0.8 × 10 −3 m 3 / r p1η m 65 × 10 5 × 0.95
3.4 3.4 计算液压执行元件实际工作压力 按最后确定的液压缸的结构尺寸和液压马达排量, 计算出各工况时液压执行元 件实际工作压力,见表 2。
TW =
Pc 5 × 10 3 = = 796 N ⋅ m 2πn 2 × 3.14 × 60 / 60
取液压马达的机械效率为 0.95,则其载荷转矩
T=
TW
ηm
=
796 = 838 N ⋅ m 0.95
3.液压系统主要参数计算 3.液压系统主要参数计算 3.1 初选系统工作压力 250 克塑料注射机属小型液压机,载荷最大时为锁模工况,此时,高压油用增 压缸提供;其他工况时,载荷都不太高,参考设计手册,初步确定系统工作压力为 6.5MPa。 3.2 计算液压缸的主要结构尺寸 ⑴确定合模缸的活塞及活塞杆直径 合模缸最大载荷时,为锁模工况,其载荷力为 1000kN,工作在活塞杆受压状 态。活塞直径
8
为满足整个工作循环的需要,按较大功率段来确定电动机功率。 从工况图看出,快速注射工况系 统的压力和流量均较大。此时,大小 泵同时参加工作,小泵排油除保证锁 模压力外,还通过顺序阀将压力油供 给注射缸,大小泵出油汇合推动注射 缸前进。 前面的计算已知,小泵供油压力 为 pP1=6.9MPa, 考虑大泵到注射缸之 间的管路损失, 大泵供油压力应为 pP2 =(5.9+0.5)MPa=6.4MPa,取泵的总 效率ηP=0.8,泵的总驱动功率为
5
计参数可知,锁模时所需的力最大,为 900kN。为此设置增压液压缸,得到锁模时 的局部高压来保证锁模力。 ⑵合模缸动作回路 合模缸要求其实现快速、慢速、锁模,开模动作。其运动方向由电液换向阀直 接控制。快速运动时,需要有较大流量供给。慢速合模只要有小流量供给即可。锁 模时,由增压缸供油。 ⑶液压马达动作回路 螺杆不要求反转,所以液压马达单向旋转即可,由于其转速要求较高,而对速 度平稳性无过高要求,故采用旁路节流调速方式。 ⑷注射缸动作回路 注射缸运动速度也较快,平稳性要求不高,故也采用旁路节流调速方式。由于 预塑时有背压要求,在无杆腔出口处串联背压阀。 ⑸注射座移动缸动作回路 注射座移动缸, 采用回油节流调速回路。 工艺要求其不工作时, 处于浮动状态, 故采用 Y 型中位机能的电磁换向阀。 ⑹安全联锁措施 本系统为保证安全生产,设置了安全门,在安全门下端装一个行程阀,用来 控制合模缸的动作。将行程阀串在控制合模缸换向的液动阀控制油路上,安全门没 有关闭时,行程阀没被压下,液动换向阀不能进控制油,电液换向阀不能换向,合 模缸也不能合模。 只有操作者离开, 将安全门关闭, 压下行程阀, 合模缸才能合模, 从而保障了人身安全。 ⑺液压源的选择 该液压系统在整个工作循环中需油量变化较大,另外,闭模和注射后又要求 有较长时间的保压,所以选用双泵供油系统。液压缸快速动作时,双泵同时供油, 慢速动作或保压时由小泵单独供油,这样可减少功率损失,提高系统效率。 4.2 拟定液压系统图
7
5.液压元件的选择 5.液压元件的选择
5.1 液压泵的选择 ⑴液压泵工作压力的确定 pP≥pl+∑Δp pl 是液压执行元件的最高工作压力,对于本系统,最高压力是增压缸锁模时的 入口压力,pl=6.4MPa;∑Δp 是泵到执行元件间总的管路损失。由系统图可见, 从泵到增压缸之间串接有一个单向阀和一个换向阀,取∑Δp=0.5MPa。 液压泵工作压力为 pP=(6.4+0.5)MPa=6.9MPa ⑵液压泵流量的确定 qP≥K(∑qmax) 由工况图看出,系统最大流量发生在快速合模工况,∑qmax=3L/s。取泄漏系 数 K 为 1.2,求得液压泵流量 qP=3.6L/s (216L/min) 选用 YYB-BCl71/48B 型双联叶片泵, 当压力为 7 MPa 时, 大泵流量为 157.3L/min, 小泵流量为 44.1L/min。 5.2 电动机功率的确定 注射机在整个动作循环中, 系统的压力和流量都是变化的, 所需功率变化较大,