电子产品高可靠性装联工艺下汇总.
高密度高可靠电子封装关键技术及成套工艺
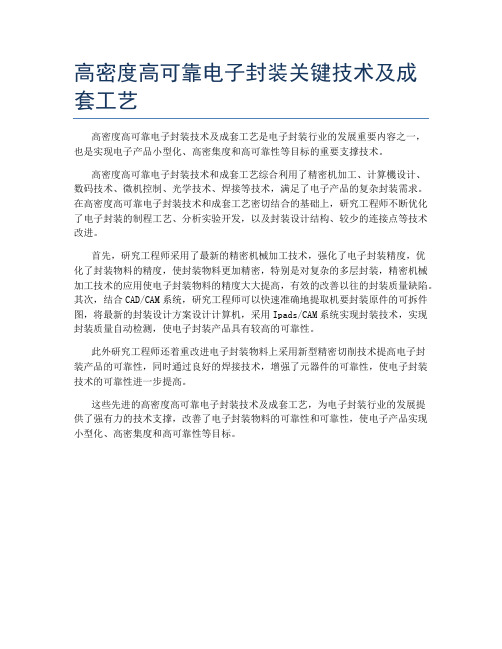
高密度高可靠电子封装关键技术及成套工艺
高密度高可靠电子封装技术及成套工艺是电子封装行业的发展重要内容之一,
也是实现电子产品小型化、高密集度和高可靠性等目标的重要支撑技术。
高密度高可靠电子封装技术和成套工艺综合利用了精密机加工、计算機设计、
数码技术、微机控制、光学技术、焊接等技术,满足了电子产品的复杂封装需求。
在高密度高可靠电子封装技术和成套工艺密切结合的基础上,研究工程师不断优化了电子封装的制程工艺、分析实验开发,以及封装设计结构、较少的连接点等技术改进。
首先,研究工程师采用了最新的精密机械加工技术,强化了电子封装精度,优
化了封装物料的精度,使封装物料更加精密,特别是对复杂的多层封装,精密机械加工技术的应用使电子封装物料的精度大大提高,有效的改善以往的封装质量缺陷。
其次,结合CAD/CAM系统,研究工程师可以快速准确地提取机要封装原件的可拆件图,将最新的封装设计方案设计计算机,采用Ipads/CAM系统实现封装技术,实现封装质量自动检测,使电子封装产品具有较高的可靠性。
此外研究工程师还着重改进电子封装物料上采用新型精密切削技术提高电子封
装产品的可靠性,同时通过良好的焊接技术,增强了元器件的可靠性,使电子封装技术的可靠性进一步提高。
这些先进的高密度高可靠电子封装技术及成套工艺,为电子封装行业的发展提
供了强有力的技术支撑,改善了电子封装物料的可靠性和可靠性,使电子产品实现小型化、高密集度和高可靠性等目标。
电子产品装配工艺规范方案
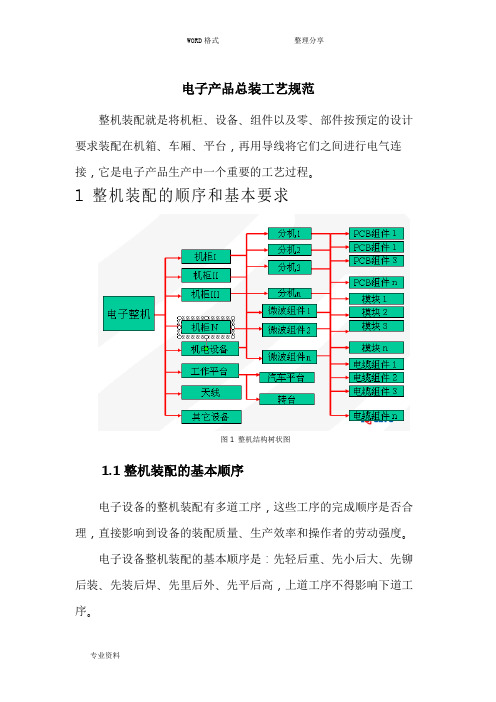
电子产品总装工艺规范整机装配就是将机柜、设备、组件以及零、部件按预定的设计要求装配在机箱、车厢、平台,再用导线将它们之间进行电气连接,它是电子产品生产中一个重要的工艺过程。
1 整机装配的顺序和基本要求图1 整机结构树状图1.1整机装配的基本顺序电子设备的整机装配有多道工序,这些工序的完成顺序是否合理,直接影响到设备的装配质量、生产效率和操作者的劳动强度。
电子设备整机装配的基本顺序是:先轻后重、先小后大、先铆后装、先装后焊、先里后外、先平后高,上道工序不得影响下道工序。
1.2整机装配的基本要求电子设备的整机装配是把半成品装配成合格产品的过程。
对整机装配的基本要求如下:1)整机装配前,对组成整机的有关零部件或组件必须经过调试、检验,不合格的零部件或组件不允许投入生产线。
检验合格的装配件必须保持清洁。
2)装配时要根据整机的结构情况,应用合理的安装工艺,用经济、高效、先进的装配技术,使产品达到预期的效果,满足产品在功能、技术指标和经济指标等方面的要求。
3)严格遵循整机装配的顺序要求,注意前后工序的衔接。
4)装配过程中,不得损伤元器件和零部件,避免碰伤机壳、元器件和零部件的表面涂敷层,不得破坏整机的绝缘性。
保证安装件的方向、位置、极性的正确,保证产品的电性能稳定,并有足够的机械强度和稳定度。
5)小型机大批量生产的产品,其整机装配在流水线上按工位进行。
每个工位除按工艺要求操作外,要求工位的操作人员熟悉安装要求和熟练掌握安装技术,保证产品的安装质量,严格执行自检、互检与专职调试检查的“三检”原则。
装配中每一个阶段的工作完成后都应进行检查,分段把好质量关,从而提高产品的一次通过率。
2 整机装配中的流水线2.1流水线与流水节拍装配流水线就是把一部整机的装连、调试等工作划分成若干简单操作,每一个装配工人完成指定操作。
在划分时要注意到每人操作所用的时间应相等,这个时间称为流水的节拍。
装配的设备在流水线上移动的方式有好多种。
电子产品制造工艺总结(共7篇)

电子产品制造工艺总结(共7篇):制造工艺电子产品电子产品生产工艺是指电子产品工艺性设计工艺工程师有前途吗篇一:电子产品生产工艺电子产品生产工艺1 电子工艺工作1.1 工艺工作概述什么叫工艺工作呢?工艺工作是对时间、速度、能源、方法、程序、生产手段、工作环境、组织机构、劳动管理、质量监控等生产因素科学研究的总结。
工艺工作的内容又可分为工艺技术和工艺管理两大类。
1.2 电子产品工艺工作程序1 电子产品工艺工作流程图电子产品从研究到生产的整个过程可划分为四个阶段,即方案论证阶段、工程研制阶段、设计定型阶段和生产定型阶段。
在各阶段中都存在着工艺方面的工艺规程,图 3.1是电子产品工艺工作流程图1 电子产品工艺工作流程图2 方案论证阶段的工艺工作3 工程设计阶段的工艺工作4 设计定型阶段的工艺工作5 生产定型阶段的工艺工作2 电子产品制造工艺技术2.1 电子产品制造工艺技术的种类对电子产品制造来讲,工艺技术有很多种,工厂生产规模、设备、技术力量和生产产品的不同,工艺技术种类也不同。
以下简要介绍几种一般工艺技术。
1. 机械加工工艺电子产品很多结构件是通过机械加工而成的,机械类工艺包括车、钳、刨、铣、镗、磨、插齿、冷作、铸造、锻打、冲裁、挤压、引伸、滚齿、轧丝等。
其主要功能是改变材料的几何形状,使之满足产品的装配连接。
2. 表面加工工艺表面加工包括刷丝、抛光、印刷、油漆、电镀、氧化、铭牌制作等工艺。
其主要功能是提高表面装饰性,使产品具有新颖感,同时也起到防腐抗蚀的作用。
3. 连接工艺电子设备在生产制造中有许多连接方法,实现电气连接的工艺主要是焊接(手工和机器焊接)。
除焊接外,压接、绕接、胶接等连接工艺也越来越受到重视。
4. 化学工艺化学工艺包括电镀、浸渍、灌注、三防、油漆、胶木化、助焊剂、防氧化等工艺。
其主要功能是防腐抗蚀、装饰美观等。
5. 塑料工艺塑料工艺主要分为压塑、注塑及部分吹塑。
6. 总装工艺总装工艺包括总装配、装联、调试、包装以及总装前的预加工工艺和胶合工艺。
电子装联工艺技术

保持一定的弯曲半径,以消除应力影响; 保持元器件本体或熔接点到弯曲点的最小距离至少为2倍
的引线直径或厚度,但不得小于0.75mm。 引线成形后的尺寸与PCB安装孔孔距相匹配; 引线直径大于1.3mm时,一般不可弯曲成形,小于1.3mm的硬引线(回火处
3.1 元器件通孔插装(THT)
3.1.2 安装次序 先低后高、先轻后重、先非敏感元器件后敏感元件、先
表面安装后通孔插装、先分立元器件后集成电路。
3.1 元器件通孔插装(THT)
3.1.3安装要求 安装高度要符合产品防震、绝缘、散热等要求及设计文件要求; 元器件加固要求:7g、3.5g及设计工艺文件的规定; 接线端子、铆钉不应作界面或层间连接用,导通孔(金属化孔)不能安装元器件; 一孔一线,孔径与引线直径的合理间隙(0.2~0.4mm) 空心铆钉不能用于电气连接; 元器件之间有至少为1.6mm的安全间距; 元器件安装后,引线伸出板面的长度应为1.5±0.8mm; 元器件安装后,引线端头采用弯曲连接时,引线弯曲长度为3.5 ~5.5d; 如底面无裸露的电路(印制导线);元件可贴板安装(玻璃二极管除外),如底面有裸露电路,
2.2 元器件引线搪锡工艺
锡和锡铅合金为最佳的可焊性镀层,其厚度
为5~7μm。 镀金引线的搪锡(除金):
Cu μm/s
金镀层是抗氧化性很强的镀层,与SnPb焊料
Ag Au
7
有很好的润湿性,但直接焊接金镀层时,
6
Pb
5
SnPb合金对金镀层产生强烈的溶解作用,金
4
Pt 3
与焊料中的Sn金属结合生成AuSn4合金,枝晶 2
对于表面贴装元器件,不管金层厚度为多少,在焊接前,应去除至少95% 被焊表面的金层;
电子产品装配工艺流程
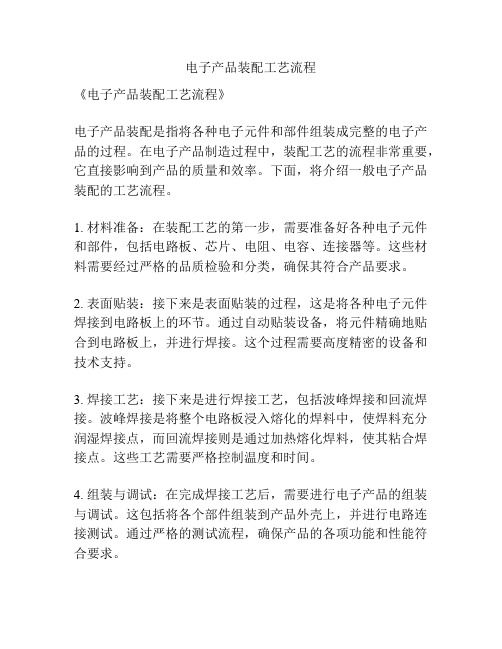
电子产品装配工艺流程
《电子产品装配工艺流程》
电子产品装配是指将各种电子元件和部件组装成完整的电子产品的过程。
在电子产品制造过程中,装配工艺的流程非常重要,它直接影响到产品的质量和效率。
下面,将介绍一般电子产品装配的工艺流程。
1. 材料准备:在装配工艺的第一步,需要准备好各种电子元件和部件,包括电路板、芯片、电阻、电容、连接器等。
这些材料需要经过严格的品质检验和分类,确保其符合产品要求。
2. 表面贴装:接下来是表面贴装的过程,这是将各种电子元件焊接到电路板上的环节。
通过自动贴装设备,将元件精确地贴合到电路板上,并进行焊接。
这个过程需要高度精密的设备和技术支持。
3. 焊接工艺:接下来是进行焊接工艺,包括波峰焊接和回流焊接。
波峰焊接是将整个电路板浸入熔化的焊料中,使焊料充分润湿焊接点,而回流焊接则是通过加热熔化焊料,使其粘合焊接点。
这些工艺需要严格控制温度和时间。
4. 组装与调试:在完成焊接工艺后,需要进行电子产品的组装与调试。
这包括将各个部件组装到产品外壳上,并进行电路连接测试。
通过严格的测试流程,确保产品的各项功能和性能符合要求。
5. 包装与出厂:最后一步是产品的包装与出厂。
在这个环节,需要设计合适的包装方案,以确保产品在运输和储存过程中不受损坏。
同时,产品的出厂需要进行全面的质量检验,确保产品符合相关标准和要求。
总结来说,电子产品装配工艺流程包括材料准备、表面贴装、焊接工艺、组装与调试以及包装与出厂等环节。
在每个环节都需要严格控制质量,并配合先进的设备和技术支持,才能保证产品的质量和效率。
高可靠电子产品中3D-plus器件装配工艺可靠性研究
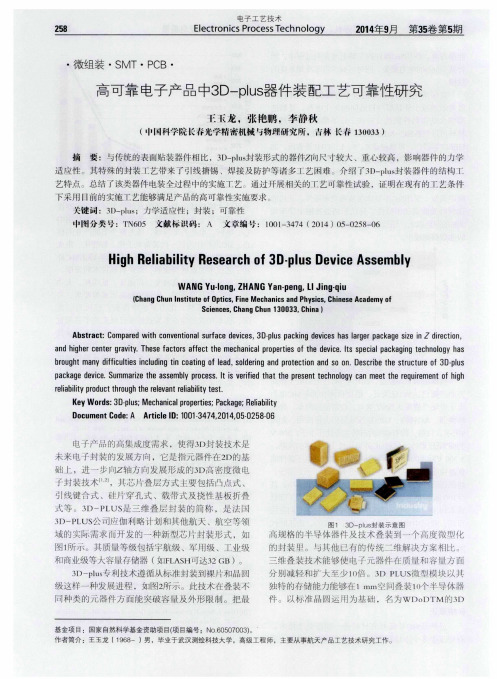
A b s t r a c t : C o mp a r e d wi t h c o n v e n t i o n a l s u r f a c e d e v i c e s , 3 D ・ p l u s p a c k i n g d e v i c e s h a s l a r g e r p a c k a g e s i z e i n d i r e c t i o n , a n d h i g h e r c e n t e r g r a v i t y . T h e s e f a c t o r s a f f e c t t h e me c h a n i c a l p r o p e r t i e s o f t h e d e v i c e . I t s s p e c i a l p a c k a g i n g t e c h n o l o g y h a s b r o u g h t ma n y d i f f i c u l t i e s i n c l u d i n g t i n c o a t i n g o f l e a d , s o l d e r i n g a n d p r o t e c t i o n a n d S O o n . D e s c r i b e t h e s t r u c t u r e o f 3 D . p l u s p a c k a g e d e v i c e . S u mma r i z e t h e a s s e mb l y p r o c e s s . I t i s v e r i f i e d t h a t t h e p r e s e n t t e c h n o l o g y c a n me e t t h e r e q u i r e me n t o f h i g h r e l i a b i l i t y p r o d u c t t h r o u g h t h e r e l e v a n t r e l i a b i l i t y t e s t 。 K e y Wo r d s : 3 D ・ p l u s ; Me c h a n i c a l p r o p e r t i e s ; P a c k a g e ; R e l i a b i l i t y D o c u me n t C o d e : A A r t i c l e I D : 1 0 0 1 . 3 4 7 4 , 2 0 1 4 , 0 5 . 0 2 5 8 . 0 6
电子行业电子产品装配工艺

电子行业电子产品装配工艺1. 引言电子行业是指以电子技术为基础,涉及电子器件、电子元件、电子设备和电子材料等产业的综合性行业。
随着科技的发展,电子产品在人们的日常生活中扮演着越来越重要的角色。
电子产品的装配工艺是确保产品质量和性能的重要环节。
2. 电子产品装配工艺的分类电子产品的装配工艺主要包括表面组装技术(Surface Mount Technology,SMT)和传统组装技术(Through Hole Technology,THT)。
2.1 表面组装技术(SMT)表面组装技术是当前电子产品装配的主流工艺。
它通过将电子元器件直接安装在印刷电路板(Printed Circuit Board,PCB)的表面,采用焊接技术将元器件与PCB连接起来。
在SMT工艺中,常见的元器件有贴片电阻、贴片电容、贴片二极管、集成电路芯片等。
具体的装配工艺包括以下几个步骤:2.1.1 PCB制板PCB制板是SMT工艺的第一步,主要是通过光刻技术将电路板上的线路图案化。
2.1.2 贴片贴片是指将表面组装元件粘贴到PCB的表面。
贴片过程可以通过自动贴片机完成,也可以通过手工贴片的方式进行。
2.1.3 焊接焊接是将元器件与PCB连接起来的关键环节。
常见的焊接方式有热风焊接、回流焊接和波峰焊接等。
2.1.4 检测和调试在完成焊接后,需要对装配的电子产品进行功能性测试和质量检测,以确保产品的性能和可靠性。
2.2 传统组装技术(THT)传统组装技术主要是指通过插件式元器件与PCB进行连接的装配工艺。
与SMT工艺相比,THT工艺需要在PCB上预留孔位,并通过焊接将插件式元器件与PCB连接起来。
在THT工艺中,常见的插件式元器件有插针、插座、按键开关等。
具体的装配工艺包括以下几个步骤:2.2.1 PCB制板与SMT工艺相同,THT工艺的第一步也是制作PCB板。
2.2.2 插件式元器件安装在制板完成后,通过手工将插件式元器件插入PCB上的孔位中。
电子行业电子设备装配工艺
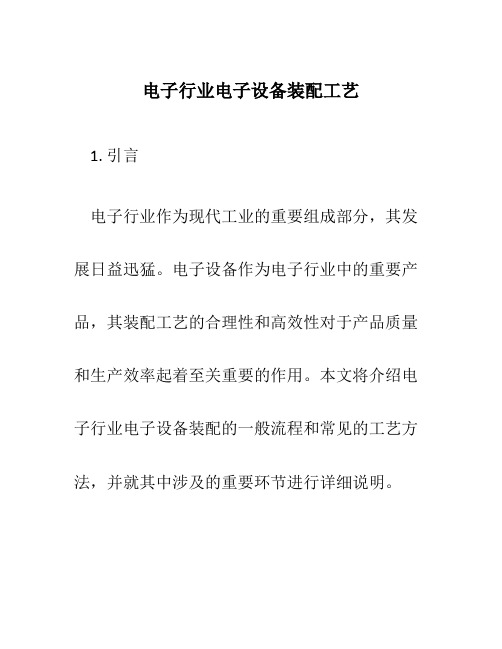
电子行业电子设备装配工艺1. 引言电子行业作为现代工业的重要组成部分,其发展日益迅猛。
电子设备作为电子行业中的重要产品,其装配工艺的合理性和高效性对于产品质量和生产效率起着至关重要的作用。
本文将介绍电子行业电子设备装配的一般流程和常见的工艺方法,并就其中涉及的重要环节进行详细说明。
2. 电子设备装配流程电子设备的装配流程主要包括以下几个环节:2.1 元器件采购与检验在电子设备装配的开始阶段,首先需要对所使用的元器件进行采购。
元器件采购的质量和效率将直接影响到最终产品的质量和生产周期。
因此,对于采购的元器件需要进行严格的检验,包括元器件的尺寸、外观、性能等方面的检查。
2.2 元器件贴装元器件贴装是电子设备装配的核心环节之一。
在元器件贴装过程中,需要根据设备的设计要求,将各个元器件精确地贴装到相应的位置上。
常用的贴装方法包括贴片式贴装和插件式贴装两种。
贴片式贴装是将元器件直接粘贴在印刷电路板(PCB)的表面上,通过贴片机实现自动化贴装。
这种方法可以提高贴装速度和精度,适用于小型电子设备的生产。
插件式贴装是将元器件通过插针或插座的方式连接到PCB上。
这种方法适用于大型或特殊元器件的贴装,例如大功率电阻、大容量电容等。
2.3 焊接焊接是将元器件与PCB之间的电气连接稳固地固定在一起的过程。
常用的焊接方法包括手工焊接、波峰焊接和回流焊接。
手工焊接是通过手工操作焊台、焊丝等工具,将焊锡熔化后涂抹在焊接点上,实现焊接。
这种方法适用于少量和小型电子设备的生产。
波峰焊接是将PCB通过传送带送入预热区、焊接区和冷却区的焊接设备中,通过浸泡在焊锡池中的波头将焊锡涂抹在焊接点上。
这种方法适用于大批量电子设备的生产。
回流焊接是将预先涂有焊膏的PCB和元器件组合,通过加热使焊膏熔化,实现焊接。
这种方法适用于小批量电子设备的生产,具有焊接速度快、效果好的优点。
2.4 测试与调试在电子设备装配完成后,需要进行测试和调试,以确保设备的正常运行。
- 1、下载文档前请自行甄别文档内容的完整性,平台不提供额外的编辑、内容补充、找答案等附加服务。
- 2、"仅部分预览"的文档,不可在线预览部分如存在完整性等问题,可反馈申请退款(可完整预览的文档不适用该条件!)。
- 3、如文档侵犯您的权益,请联系客服反馈,我们会尽快为您处理(人工客服工作时间:9:00-18:30)。
2.导线与焊杯(槽)接线端子的焊接
电连接器上的连接点若是镀金连接点,必须经 过除金处理后,才能进行焊接。
当焊杯(槽)连接点的电流不大于3A时,焊接时 电烙铁的功率,一般应采用20W控温电烙铁。烙铁 头部的温度,一般为(265±5)℃。焊接的时间,一 般为1~2s。 当焊杯(槽)连接点的电流不小于5A时,焊接时 电烙铁的功率,一般应采用30~50W控温电烙铁。 烙铁头部的温度,一般为 (300±10)℃。焊接的时 间,一般为2~3s。
导线的绝缘层,应离焊杯(槽)入口点距离,一
般为0.5~1mm。 导线端头插入焊杯的距离,如图9-4所示。
0.5~1mm
图9-4
不应该选用多芯数电连接器,来连接少数几根 导线。另外,当电连接器上焊接的连接点与空余连 接点,数字相差比较悬殊时,应合理地分配电连接 器上的连接点,导线应尽量分配在电连接器连接点 的中心部位,不应布局在其周边或两端。
为不可活动的结构 ,可采用单股导线进行连接。 导线芯线总的截面积,不应超过每个焊杯(槽) 内径截面积。导线与焊杯(槽)匹配是否合理,决定 于导线芯线的直径(A)与电连接器焊杯(槽)内径(B) 的比值关系。 导线芯线的直径(A)与电连接器焊杯(槽)内径 (B)匹配状态,如图9-2所示。
B A 造成焊槽 根部应力 造成芯线 根部应力
把预搪锡的导线芯线,应分别垂直插入到经过 除金处理后的焊杯(槽)底部,并与焊杯(槽)底部的
内壁相接触。不允许将2~3根芯线经过扭绞后,再 进行搪锡。然后,插入焊杯(槽)底部。
电连接器焊杯端子的连接,如图9-3所示。
导线离开焊杯距离 芯线接触杯底
图9-3
每个焊杯(槽)内导线芯线的数量,应限制在能 与焊杯(槽)内壁的整个空间都相接触为宜,一般允 许插入二根芯线,但不允许超过三根芯线。
电子产品高可靠性电装工艺
(下 )
编 写 徐飞
中国航天科技集团公司 五三九厂
第九章
整机装联
为了确保电子产品的整机装联质量,电装人员 必须掌握电子装联方面的各种工艺技术,严格按电 子装联工艺规程进行整机装联。 整机装联工作包括:整机的接口布局、电连接 器的装联、印制电路板组装件的组合安装、面板上 元器件及部(组)件的组合安装、导线束的敷设与绑 扎、整机的防护与加固等。同时,还应充分考虑到 整机内的散热效果。
用导热硅脂后,可降低接触热阻25﹪~35﹪。 对流——是指热源周围的空气受热后,因密度 降低而上升,利用温差而形成空气的自然流动,让 附近较冷空气置换到较热空气位置。整机内的对流 散热,是利用冷空气从下方流入,带走整机内一部 份热量,由上方排出。当采用对流散热时,应防止 进风口与出风口二者之间的气流发生短路现象。 热辐射是以电磁波形式向外辐射能量的过程。 物体表面辐射率与材料温度、表面粗糙度和涂复情 况有关。常用的喷涂材料如:黑色无光漆,在温度 40℃~100℃ 时其表面辐射率最高,辐射散热效果
小于30mm,但不应该大于50mm。 凡是有接触电阻值、导电性能要求的安装件,
对于表面镀层的处理,一般不宜在安装过程中,由 操作人员临时进行去除表面镀层的工艺处理。
当整机中的元器件有绝缘和导热要求时,安装 的材料尺寸,应超过元器件壳体边缘1~2mm。 导线束穿过底板孔壁时,应在孔内安装绝缘圈 (如:橡胶圈),防止磨损导线的绝缘层。 二 散热要求 元器件工作时消耗的功率,除部分转换成有用 的能量外,其余部分均被转换成热量。为了降低整
当焊杯(槽)连接点的电流不小于 10A时,焊接
时电烙铁的功率,一般应该采用50~70W控温电烙 铁。烙铁头部的温度,一般为 (340±10)℃。焊接 的时间,一般为2~3s。 焊接时焊料应浸润焊杯中所有的内表面,在芯 线和焊杯(槽)的进线开槽口之间,应该形成角缝焊。 焊料要适量,焊料的填充量为100﹪。 焊杯经过焊接后,焊料不能溢出焊杯接线端子, 外表面不应有突起部分及焊料溅出物的积聚。 电连接器的焊杯经过焊接后,焊料在焊杯外表 面的要求,如图9-5所示。
第一节
一 一般要求
整机装联的要求
整机装联的原则是:先轻后重、先里后外、先 铆后装、先低后高、先装后连、易碎后装,上道工允许采用其它加固方式 (如:安装加强筋)、高温 烘烤等措施,来对其扭曲或弓曲变形进行矫正。 当印制电路板组装件采用紧固件紧固在金属框 架上时,螺钉紧固的距离,一般为30~50mm。可以
匹配(A/B=0.6~0.9)
不匹配(A/B>1) 不匹配(A/B<0.6)
图9-2
当电连接器焊杯(槽)中焊接一根芯线时,芯线与电 连接器焊杯 (槽)的占空比A/B最佳为0.75,一般为 0.6~0.9。 当电连接器焊杯(槽)中焊接二根芯线时,芯线 与电连接器焊杯(槽)的占空比A/B最佳为0.5,一般 为0.4~0.7。 当电连接器焊杯(槽)中焊接三根芯线时,芯线 与电连接器焊杯 (槽)的占空比A/B最佳为0.65,一 般为0.4~0.75。
最好。通常是对散热器表面进行喷粗砂处理,表面 粗糙后辐射率可提高3﹪。进行黑色氧极化处理后, 黑体容易辐射。温度越高,辐射效果越显著。
第二节
焊接连接
一 导线与焊杯(槽)接线端子的连接
1.导线与焊杯(槽)电连接器的连接方法 电连接器中连接点与连接点之间的相互连接, 必须采用多股导线,并要有一定的活动余量来进行 释放应力。只有在电连接器内的相临两点或接触对
机内的工作温度,应对已经产生的热量,要采取一 切有效的措施进行散热。 散热的方式主要有热传导、对流和热辐射。 热传导——是指直接接触物体的各部分热量, 进行交换的现象。为了使热传导的热量传递得快, 通常是在发热元器件上装置散热器,散热器一般用 铝材料制作,并将表面进行化学黑色氧极化处理。 经过黑色氧极化处理后,可降低热阻约25﹪,同时 增加了表面辐射率。在大功率管壳与散热器之间涂 复一层导热硅脂后,不但能减小交界面的热阻,而 且能减少接触间隙,还能防止潮湿空气的侵入。采
外表面无焊料积聚
外表面有焊料积聚
外表面有焊料拉尖