输油管道、泵站工艺流程(DOC)
7.0输油站的工艺流程

输油管道设计与管理
20
我国过去所建管线使用的加热炉多为方箱式加热炉, 炉膛大、热惯性大,升温降温都需要较长的时间,一 般在正式投入运行前要先用木材等烘炉5天左右。若管 线突然停输,由于炉内温度很高,炉管内的存油会汽 化,使炉管内压力过高,或结焦穿孔,易发生事故。
2015/12/22
第七章 输油站
输油站的基本任务是给油流提供能量(压力能、热能), 安全经济地将油品输送到终点。
一、输油站工艺流程
输油站的工艺流程是指油品在站内的流动过程,实际上就 是站内管道、管件、阀门所组成的、并与其它输油设备 (包括泵机组、加热炉和油罐)相连的输油管道系统。该 系统决定了油品在站内可能流动的方向、输油站的性质和 所承担的任务。
采用密闭输油流程时,该流程仅存在于首、末站。
2015/12/22
输油管道设计与管理
3
(3) 正输流程 先泵后炉流程:
罐→阀组→泵→炉→阀组→下站(首站)
上站来油→阀组→泵→炉→阀组→下站(中间站) 先炉后泵流程: 罐→给油泵→阀组→炉→泵→阀组→下站(首站) 上站来油→阀组→炉→泵→阀组→下站(中间站) 用于管线的正常输油。
2015/12/22
输油管道设计与管理
23
③ 热效率高且效率基本上不随热负荷变化,因而对输量和热 负荷的适应性强。加热炉的效率可达92%以上,考虑到热 媒系统设备的动力消耗和热媒罐、加热管线及热媒原油换 热器的热损失又增加了能源损失,所以整个间接加热系统 的综合热效率要比热媒加热炉低5%左右,可达87%。 ④ 体积小,重量轻,便于实现加热炉系统的轻型化和预制化。
输油管道设计与管理
21
2、间接加热 以某种中间热载体为热媒,燃料直接加热热媒,在换 热器中热媒加热原油。 目前油田上广泛采用的水套式加热炉即为一种间接加 热系统。另外,在东黄复线上,我国从国外引进的热 媒炉间接加热系统是长输管线上广泛使用的原油加热 系统,并已开始在老线的改造中使用。
典型输油工艺流程
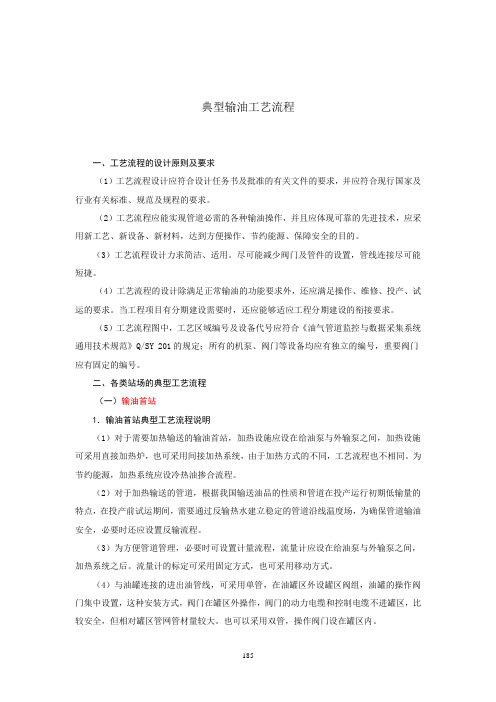
典型输油工艺流程一、工艺流程的设计原则及要求(1)工艺流程设计应符合设计任务书及批准的有关文件的要求,并应符合现行国家及行业有关标准、规范及规程的要求。
(2)工艺流程应能实现管道必需的各种输油操作,并且应体现可靠的先进技术,应采用新工艺、新设备、新材料,达到方便操作、节约能源、保障安全的目的。
(3)工艺流程设计力求简洁、适用。
尽可能减少阀门及管件的设置,管线连接尽可能短捷。
(4)工艺流程的设计除满足正常输油的功能要求外,还应满足操作、维修、投产、试运的要求。
当工程项目有分期建设需要时,还应能够适应工程分期建设的衔接要求。
(5)工艺流程图中,工艺区域编号及设备代号应符合《油气管道监控与数据采集系统通用技术规范》Q/SY 201的规定;所有的机泵、阀门等设备均应有独立的编号,重要阀门应有固定的编号。
二、各类站场的典型工艺流程(一)输油首站1.输油首站典型工艺流程说明(1)对于需要加热输送的输油首站,加热设施应设在给油泵与外输泵之间,加热设施可采用直接加热炉,也可采用间接加热系统,由于加热方式的不同,工艺流程也不相同。
为节约能源,加热系统应设冷热油掺合流程。
(2)对于加热输送的管道,根据我国输送油品的性质和管道在投产运行初期低输量的特点,在投产前试运期间,需要通过反输热水建立稳定的管道沿线温度场,为确保管道输油安全,必要时还应设置反输流程。
(3)为方便管道管理,必要时可设置计量流程,流量计应设在给油泵与外输泵之间,加热系统之后。
流量计的标定可采用固定方式,也可采用移动方式。
(4)与油罐连接的进出油管线,可采用单管,在油罐区外设罐区阀组,油罐的操作阀门集中设置,这种安装方式,阀门在罐区外操作,阀门的动力电缆和控制电缆不进罐区,比较安全,但相对罐区管网管材量较大。
也可以采用双管,操作阀门设在罐区内。
(5)倒罐流程可在管线停输和不停输两种情况下进行,后者流程较为复杂,需设专门的倒罐泵。
为了简化流程,也可不设专门的倒罐流程,采用给油泵在停输的情况下进行倒罐。
原油管道输送方式及工艺流程

原油管道输送方式及工艺流程一、组成长距离输油管道由输油站和线路组成;输油站就是给油流一定的能量(压力能和热力能),按所处位置分首站、中间站、末站;中间站按任务不同分加热站、加压站、热泵站(加压、加热);首站:输油管道起点的输油站,任务是接受(计量、储存)原油,经加压、加热向下一站输送;输油管道终点的输油站称末站,接受来油和把油品输给用油单位,配有储罐、计量、化验及运转设施。
二、输送工艺1、“旁接油罐”式输送工艺:上站来油可进入泵站的输油泵也可同时进入油罐的输送工艺,油罐通过旁路连接到干线上,当本站与上下站的输量不平衡时,油罐起缓冲作用特点;a 各管段输量可不等,油罐起缓冲作用;b 各管段单独成一水力系统,有利于运行调节和减少站间的相互影响;c 与“从泵到泵”相比,不需较高的自动调节系统,操作简单。
2、“从泵到泵” 输送工艺:为密闭输送工艺,中间站不设缓冲罐,上站来油全部直接进泵特点:a 可基本消除中间站的蒸发损耗;b整个管道成一个统一的水力系统,充分利用上站余压,减少节流,但各站要有可靠的自动调节和保护装置;c工艺流程简单。
三、输油站的基本组成1、主生产区(1)油泵房(输油泵机组、润滑、冷却、污油回收等系统);(2)加热系统(加热炉和换热器);(3)总阀室(控制和切换流程);(4)清管器收发室;(5)计量间(流量计及标定装置);(6)油罐区;(7)站控室;(8)油品预处理设施(热处理、添加剂、脱水等)。
2、辅助生产区(1)供电系统(变、配、发电);(2)供热系统(锅炉房、燃料油系统、热力管网等);(3)给排水系统(水源、循环水、软化水、消防水等);(4)供风系统(仪表风、扫线用风);(5)阴极保护设施;(6)消防及警卫、机修化验、库房、办公后勤设施等。
四、确定工艺流程的原则1、满足输送工艺及各生产环节(试运投产、正常输送、停输再启动等)的要求。
输油站的主要操作:a、来油与计量;b、正输;c、反输(投产前预热管道或末站储罐已满、或首站油源不足,被迫正、反输以维持热油管道最低输送量);d、越站输送(全越站、压力越站、热力越站);e、收发清管器;f、站内循环或倒罐(机组试运转或烘炉);g、停输再启动。
原油管道输送方式及工艺流程

原油管道输送方式及工艺流程一、组成长距离输油管道由输油站和线路组成;输油站就是给油流一定的能量(压力能和热力能),按所处位置分首站、中间站、末站;中间站按任务不同分加热站、加压站、热泵站(加压、加热);首站:输油管道起点的输油站,任务是接受(计量、储存)原油,经加压、加热向下一站输送;输油管道终点的输油站称末站,接受来油和把油品输给用油单位,配有储罐、计量、化验及运转设施。
二、输送工艺1、“旁接油罐”式输送工艺:上站来油可进入泵站的输油泵也可同时进入油罐的输送工艺,油罐通过旁路连接到干线上,当本站与上下站的输量不平衡时,油罐起缓冲作用特点;a 各管段输量可不等,油罐起缓冲作用;b 各管段单独成一水力系统,有利于运行调节和减少站间的相互影响;c 与“从泵到泵"相比,不需较高的自动调节系统,操作简单。
2、“从泵到泵” 输送工艺:为密闭输送工艺,中间站不设缓冲罐,上站来油全部直接进泵特点:a 可基本消除中间站的蒸发损耗;b整个管道成一个统一的水力系统,充分利用上站余压,减少节流,但各站要有可靠的自动调节和保护装置;c工艺流程简单。
三、输油站的基本组成1、主生产区(1)油泵房(输油泵机组、润滑、冷却、污油回收等系统); (2)加热系统(加热炉和换热器);(3)总阀室(控制和切换流程);(4)清管器收发室;(5)计量间(流量计及标定装置);(6)油罐区;(7) 站控室;(8) 油品预处理设施(热处理、添加剂、脱水等)。
2、辅助生产区(1)供电系统(变、配、发电);(2)供热系统(锅炉房、燃料油系统、热力管网等);(3)给排水系统(水源、循环水、软化水、消防水等);(4)供风系统(仪表风、扫线用风);(5)阴极保护设施;(6)消防及警卫、机修化验、库房、办公后勤设施等。
四、确定工艺流程的原则1、满足输送工艺及各生产环节(试运投产、正常输送、停输再启动等)的要求。
输油站的主要操作:a、来油与计量;b、正输;c、反输(投产前预热管道或末站储罐已满、或首站油源不足,被迫正、反输以维持热油管道最低输送量);d、越站输送(全越站、压力越站、热力越站);e、收发清管器;f、站内循环或倒罐(机组试运转或烘炉);g、停输再启动.2、中间站的工艺流程要和所采用的输送方式相适应(旁接油罐、从泵到泵)。
输油管道_泵站工艺流程

第三章输油站场及阀室第一节典型输油站场工艺流程一、工艺流程的设计原则及要求(1)工艺流程设计应符合设计任务书及批准的有关文件的要求,并应符合现行国家及行业有关标准、规范及规程的要求。
(2)工艺流程应能实现管道必需的各种输油操作,并且应体现可靠的先进技术,应采用新工艺、新设备、新材料,达到方便操作、节约能源、保障安全的目的。
(3)工艺流程设计力求简洁、适用。
尽可能减少阀门及管件的设置,管线连接尽可能短捷。
(4)工艺流程的设计除满足正常输油的功能要求外,还应满足操作、维修、投产、试运的要求。
当工程项目有分期建设需要时,还应能够适应工程分期建设的衔接要求。
(5)工艺流程图中,工艺区域编号及设备代号应符合《油气管道监控与数据采集系统通用技术规范》Q/SY 201的规定;所有的机泵、阀门等设备均应有独立的编号,重要阀门应有固定的编号。
二、各类站场的典型工艺流程(一)输油首站1.输油首站典型工艺流程说明(1)对于需要加热输送的输油首站,加热设施应设在给油泵与外输泵之间,加热设施可采用直接加热炉,也可采用间接加热系统,由于加热方式的不同,工艺流程也不相同。
为节约能源,加热系统应设冷热油掺合流程。
(2)对于加热输送的管道,根据我国输送油品的性质和管道在投产运行初期低输量的特点,在投产前试运期间,需要通过反输热水建立稳定的管道沿线温度场,为确保管道输油安全,必要时还应设置反输流程。
(3)为方便管道管理,必要时可设置计量流程,流量计应设在给油泵与外输泵之间,加热系统之后。
流量计的标定可采用固定方式,也可采用移动方式。
(4)与油罐连接的进出油管线,可采用单管,在油罐区外设罐区阀组,油罐的操作阀门集中设置,这种安装方式,阀门在罐区外操作,阀门的动力电缆和控制电缆不进罐区,比较安全,但相对罐区管网管材量较大。
也可以采用双管,操作阀门设在罐区内。
(5)倒罐流程可在管线停输和不停输两种情况下进行,后者流程较为复杂,需设专门的倒罐泵。
石油装备、油管、套管、抽油机加工工艺流程
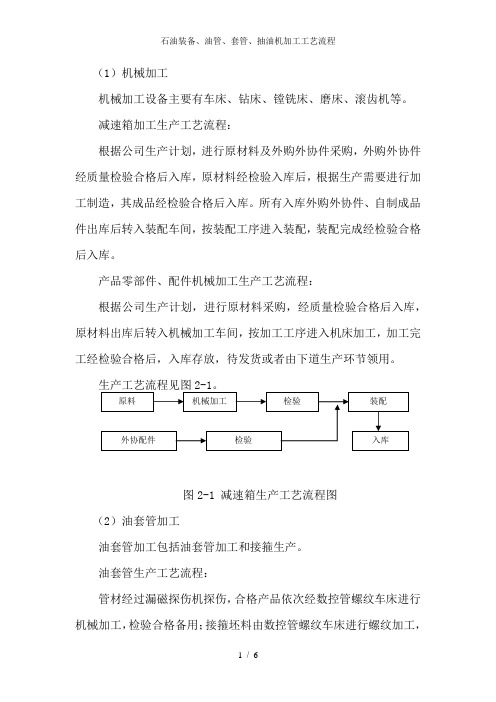
(1)机械加工机械加工设备主要有车床、钻床、镗铣床、磨床、滚齿机等。
减速箱加工生产工艺流程:根据公司生产计划,进行原材料及外购外协件采购,外购外协件经质量检验合格后入库,原材料经检验入库后,根据生产需要进行加工制造,其成品经检验合格后入库。
所有入库外购外协件、自制成品件出库后转入装配车间,按装配工序进入装配,装配完成经检验合格后入库。
产品零部件、配件机械加工生产工艺流程:根据公司生产计划,进行原材料采购,经质量检验合格后入库,原材料出库后转入机械加工车间,按加工工序进入机床加工,加工完工经检验合格后,入库存放,待发货或者由下道生产环节领用。
生产工艺流程见图2-1。
图2-1 减速箱生产工艺流程图(2)油套管加工油套管加工包括油套管加工和接箍生产。
油套管生产工艺流程:管材经过漏磁探伤机探伤,合格产品依次经数控管螺纹车床进行机械加工,检验合格备用;接箍坯料由数控管螺纹车床进行螺纹加工,原料 检验 机械加工 装配 入库检验 外协配件检验后经漏磁探伤机探伤,合格后打标;接下来接箍拧接机将管材与接箍连接,检验合格后用打标机进行打标,经过静水试压机进行压力检测(水压为0~70MPa ,管径不同压力不同),测长称重,管两端上保护环,用自动刷漆机在管外壁均匀涂刷环氧沥青防腐漆,后进行喷标,最后成品检验合格后打包,放到产品存放区。
油管、套管生产工艺流程见图2-2。
图2-2 油套管加工工艺流程图(3)抽油机制造主要生产设备为数控切割机、仿形切割机、锯床、组装焊接台架、电焊机等。
抽油机生产工艺流程:根据公司生产计划,进行原材料及外购外协件采购,经质量检验合格后入库,原材料出库后转入机械加工工序,加工完工后,转入铆焊组装工位进行组焊、装配,外购外协件出库后转入组装工序,整机装配完成后整机试机,合格后入库。
工艺流程见图2-3。
管材 无损探伤 螺纹加工 检验拧接箍 检验 打标接箍坯料 螺纹加工 探伤 打标静水试压测长称重 上保护环 检验 打包 防腐图2-3抽油机生产工艺流程图(4)抽油杆制造抽油杆生产工艺流程:①抽油杆圆钢料经检验合格后经矫直机校直、磁粉探伤机探伤、镦锻。
输油管道工艺技术

也是一种近似。这是因为:
流速不太高时,摩擦升
温尤很其小对,于且南对北油走流向的的加管 线 ,
1、来油温度≠地温。 热但是我均们匀可的以。将其分段,按
照分段等温来考虑。
2、摩擦热加热油流。
3、沿线地温不等于常数。
在工程实际中,一般总把那些不建设专门的加热设施的
管道统称为等温输油管道。它不考虑热损失,只考虑泵所提供 的能量(压头)与消耗在摩阻和高差上的能量(压头)相匹配 (相平衡)。
2、若泵型号不同,如何求泵站的工作特性?
3.串、并联泵机组数的确定
选择泵机组数的原则主要有四条: ①满足输量要求; ②充分利用管路的承压能力; ③泵在高效区工作; ④泵的台数符合规范要求(不超过四台)。
⑴ 并联泵机组数的确定
n Q q
其中 : Q为设计输送能力, q为单泵的额定排量 。
显然 n不一定是整数 ,只能取与之相近的整数,这就是泵机
第二节 输油管道的压能损失
一、管路的压降计算
根据流体力学理论,输油管道的总压降可表示为:
H hL h z j zQ
其中:hL为沿程摩阻 hξ为局部摩阻 (zj-zQ) 为计算高程差
二、水力摩阻系数的计算
计算长输管道的摩阻损失主要是计算沿程摩阻损失 hL 。
达西公式 :
hL
L D
V2 2g
流态 层流
水力光滑区 紊 流 混合摩擦区
粗糙区
划分范围 Re<2000
59.7
3000<Re<Re1= 8/7
59.7
8/7 <Re<Re2
665 765lg Re>Re2=
λ =f(Re,ε)
λ =64/Re
(工艺流程)输油管道泵站工艺流程
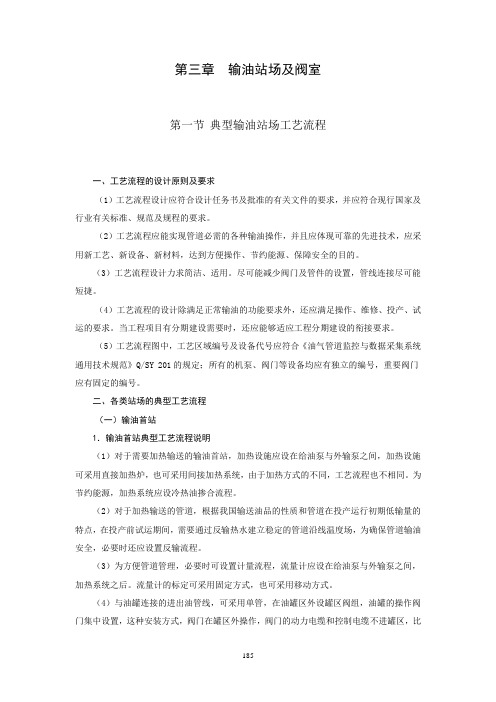
第三章输油站场及阀室第一节典型输油站场工艺流程一、工艺流程的设计原则及要求(1)工艺流程设计应符合设计任务书及批准的有关文件的要求,并应符合现行国家及行业有关标准、规范及规程的要求。
(2)工艺流程应能实现管道必需的各种输油操作,并且应体现可靠的先进技术,应采用新工艺、新设备、新材料,达到方便操作、节约能源、保障安全的目的。
(3)工艺流程设计力求简洁、适用。
尽可能减少阀门及管件的设置,管线连接尽可能短捷。
(4)工艺流程的设计除满足正常输油的功能要求外,还应满足操作、维修、投产、试运的要求。
当工程项目有分期建设需要时,还应能够适应工程分期建设的衔接要求。
(5)工艺流程图中,工艺区域编号及设备代号应符合《油气管道监控与数据采集系统通用技术规范》Q/SY 201的规定;所有的机泵、阀门等设备均应有独立的编号,重要阀门应有固定的编号。
二、各类站场的典型工艺流程(一)输油首站1.输油首站典型工艺流程说明(1)对于需要加热输送的输油首站,加热设施应设在给油泵与外输泵之间,加热设施可采用直接加热炉,也可采用间接加热系统,由于加热方式的不同,工艺流程也不相同。
为节约能源,加热系统应设冷热油掺合流程。
(2)对于加热输送的管道,根据我国输送油品的性质和管道在投产运行初期低输量的特点,在投产前试运期间,需要通过反输热水建立稳定的管道沿线温度场,为确保管道输油安全,必要时还应设置反输流程。
(3)为方便管道管理,必要时可设置计量流程,流量计应设在给油泵与外输泵之间,加热系统之后。
流量计的标定可采用固定方式,也可采用移动方式。
(4)与油罐连接的进出油管线,可采用单管,在油罐区外设罐区阀组,油罐的操作阀门集中设置,这种安装方式,阀门在罐区外操作,阀门的动力电缆和控制电缆不进罐区,比较安全,但相对罐区管网管材量较大。
也可以采用双管,操作阀门设在罐区内。
(5)倒罐流程可在管线停输和不停输两种情况下进行,后者流程较为复杂,需设专门的倒罐泵。
- 1、下载文档前请自行甄别文档内容的完整性,平台不提供额外的编辑、内容补充、找答案等附加服务。
- 2、"仅部分预览"的文档,不可在线预览部分如存在完整性等问题,可反馈申请退款(可完整预览的文档不适用该条件!)。
- 3、如文档侵犯您的权益,请联系客服反馈,我们会尽快为您处理(人工客服工作时间:9:00-18:30)。
第三章输油站场及阀室第一节典型输油站场工艺流程一、工艺流程的设计原则及要求(1)工艺流程设计应符合设计任务书及批准的有关文件的要求,并应符合现行国家及行业有关标准、规范及规程的要求。
(2)工艺流程应能实现管道必需的各种输油操作,并且应体现可靠的先进技术,应采用新工艺、新设备、新材料,达到方便操作、节约能源、保障安全的目的。
(3)工艺流程设计力求简洁、适用。
尽可能减少阀门及管件的设置,管线连接尽可能短捷。
(4)工艺流程的设计除满足正常输油的功能要求外,还应满足操作、维修、投产、试运的要求。
当工程项目有分期建设需要时,还应能够适应工程分期建设的衔接要求。
(5)工艺流程图中,工艺区域编号及设备代号应符合《油气管道监控与数据采集系统通用技术规范》Q/SY 201的规定;所有的机泵、阀门等设备均应有独立的编号,重要阀门应有固定的编号。
二、各类站场的典型工艺流程(一)输油首站1.输油首站典型工艺流程说明(1)对于需要加热输送的输油首站,加热设施应设在给油泵与外输泵之间,加热设施可采用直接加热炉,也可采用间接加热系统,由于加热方式的不同,工艺流程也不相同。
为节约能源,加热系统应设冷热油掺合流程。
(2)对于加热输送的管道,根据我国输送油品的性质和管道在投产运行初期低输量的特点,在投产前试运期间,需要通过反输热水建立稳定的管道沿线温度场,为确保管道输油安全,必要时还应设置反输流程。
(3)为方便管道管理,必要时可设置计量流程,流量计应设在给油泵与外输泵之间,加热系统之后。
流量计的标定可采用固定方式,也可采用移动方式。
(4)与油罐连接的进出油管线,可采用单管,在油罐区外设罐区阀组,油罐的操作阀门集中设置,这种安装方式,阀门在罐区外操作,阀门的动力电缆和控制电缆不进罐区,比较安全,但相对罐区管网管材量较大。
也可以采用双管,操作阀门设在罐区内。
(5)倒罐流程可在管线停输和不停输两种情况下进行,后者流程较为复杂,需设专门的倒罐泵。
为了简化流程,也可不设专门的倒罐流程,采用给油泵在停输的情况下进行倒罐。
(6)输油泵根据需要可采用串联、并联或串并结合的运行方式,由于输油泵运行方式的不同,管线的连接流程也不相同。
(7)当原油采用热处理输送时,为节约能源,热处理后的原油应采用急冷方式与冷油进行换热,再输油泵前设置冷、热油换热器。
当采用加剂输送时,降凝剂应在油品加热前注入,减阻剂应在输油主泵后注入。
(8)管道出站应设高压泄压阀,泄压阀可接入油罐,也可直接接到油罐出口管线(给油泵入口管线)。
(9)对于顺序输送的管道首站,应设油品切换阀组,其阀门应为快速开启、关闭的阀门,开关的时间不宜超过10s。
2.输油首站工艺流程应具有的功能(1)接收来油进罐;(2)油品切换;(3)加热/增压外输;(4)站内循环;(5)压力泄放;(6)清管器发送。
必要时还应具有反输和交接计量流程。
成品油首站出站端还应设置油品界面检测系统。
3.输油首站典型工艺流程图输油管道首站输油工艺有油品的常温输送、加热输送、顺序输送等,由于输送工艺的不同,其流程也不相同。
常温输送首站典型工艺流程举例:图3-1-1为“泵串联运行、罐区单管”的流程,图3-1-2为“泵并联运行、罐区双管”的流程。
顺序输送首站典型工艺流程举例:图3-1-3为“泵并联运行、混油掺合”的流程,图3-1-4为“泵串联运行、混油掺合”的流程。
加热输送首站典型工艺流程举例:图3-1-5为“泵串联运行、直接加热炉”的流程,图3-1-6为“泵并联运行、热媒加热炉”的流程,图3-1-7为“直接加热炉、带反输”的流程,图3-1-8为“直接加热炉、带交接计量”的流程,图3-1-9为“直接加热炉、热处理”的流程。
118711881189119011911921119311941195(二)中间泵站1.中间泵站典型工艺流程说明(1)中间泵站的输油泵根据需要可采用并联或串联运行方式,采用输油泵并联运行时应设压力自动越站流程。
(2)管道清管流程根据需要可设清管器接收、发送设施,也可采用清管器自动越站方式。
2.中间泵站工艺流程应具有的功能(1)增压外输;(2)清管器接收、发送或越站;(3)压力越站;(4)全越站;(5)压力泄放;(6)泄压罐油品回注。
必要时还应设反输流程。
3.中间泵站典型工艺流程图中间泵站根据输油泵的运行方式和清管功能的不同,工艺流程也不相同。
中间泵站典型工艺流程图举例:图3-1-10为“泵并联运行、清管器收发”的流程,图3-1-11为“泵串联运行、清管器越站”的流程。
197198(三)中间加热站1.中间加热站典型工艺流程说明(1)为节约能源加热系统应设冷热油掺合流程。
(2)为保证管道的安全运营,必要时还应设反输流程。
(3)中间加热站根据需要可设进站超压泄放流程,若采用泄压罐,还需设泄压罐油品回注流程。
2.中间加热站工艺流程应具有的功能(1)加热外输;(2)清管器接收、发送或越站;(3)热力越站;(4)全越站。
必要时还应设反输流程。
3.中间加热站典型工艺流程图中间加热站根据加热方式及清管功能的不同,工艺流程也不相同。
中间加热站典型工艺流程图举例:图3-1-12为“直接加热炉、清管器越站”的流程,图3-1-13为“直接加热炉、反输”的流程,图3-1-14为“热媒加热炉、反输、清管器收发”的流程。
200201202(四)中间热泵站1.中间热泵站典型工艺流程说明(1)为降低加热设备的设计压力,提高加热设备运行操作的安全性,热泵站应采用“先炉后泵”的流程,加热设备应设置在外输主泵前。
为节约能源加热系统还应设冷热油掺合流程。
(2)为保证管道的安全运营,必要时还应设反输流程。
(3)中间泵站的输油泵根据需要可采用并联或串联运行方式,采用输油泵并联运行时应设压力自动越站流程。
(4)根据需要可设清管器收、发设施,也可采用清管器自动越站方式。
2.中间热泵站工艺流程应具有的功能(1)加热/增压外输;(2)清管器接收、发送或越站;(3)压力/热力越站;(4)全越站;(5)压力泄放;(6)泄压罐油品回注。
必要时还应设反输流程。
3.中间热泵站典型工艺流程图中间热泵站根据输油泵的运行方式和清管功能及加热方式的不同,工艺流程也不相同。
中间热泵站典型工艺流程图举例:图3-1-15为“泵并联运行、热媒加热炉、清管器收发”的流程,图3-1-16为“泵串联运行、直接加热炉、清管器收发”的流程,图3-1-17为“泵串联运行、直接加热炉、带反输”的流程。
(五)中间分输站中间分输站根据功能不同分为:分输泵站、干线分输计量站、支线分输计量站等。
1.中间分输站典型工艺流程说明(1)中间分输泵站需设进、出站的超压泄放流程,因此还需设泄压罐油品回注流程;分输加热站根据需要设进站泄压流程,若采用泄压罐,还需设泄压罐油品回注流程。
(2)为保证管道的安全运营,必要时还应设反输流程。
2.中间分输站工艺流程应具有的功能(1)加热/增压外输;(2)调压、分输;(3)计量、标定;(4)清管器接收、发送或越站;(5)压力/热力越站;(6)全越站;(7)压力泄放;(8)泄压罐油品回注。
成品油分输站还应设置油品界面检测系统。
3.中间分输站典型工艺流程图中间分输站典型工艺流程图举例:图3-1-18为“中间分输泵站(泵串联运行、清管器收发)典型工艺流程”,图3-1-19为“干线分输计量站典型工艺流程图”,图3-1-20为“支线分输计量站典型工艺流程图”。
205206207208209210(六)中间输入站1.中间输入站典型工艺流程说明中间输入站包括:输入站、输入泵站、输入加热站、干线输入站等。
(1)中间输入泵站需设进、出站的超压泄放流程,因此还需设泄压罐油品回注流程;输入加热站根据需要设进站泄压流程,若采用泄压罐,还需设泄压罐油品回注流程。
(2)输入站应设油品切换阀组,其阀门应为快速开启、关闭的阀门,开关的时间不宜超过10s(3)为保证管道的安全运营,必要时还应设反输流程。
2.中间输入站工艺流程应具有的功能(1)接收来油进罐;(2)油品切换;(3)加热/增压外输;(4)调压输入;(5)站内循环;(6)压力泄放;(7)泄压罐油品回注。
(8)清管器接收、发送或越站。
成品油输入站还应设置油品界面检测系统。
3.中间输入站典型工艺流程图中间输入站典型工艺流程图举例:图3-1-21为“中间输入泵站(泵并联运行)典型工艺流程图”,图3-1-22为“中间输入泵站(泵串联运行)典型工艺流程”。
(七)中间减压站中间减压站包括:减压站、减压分输站等。
1.中间减压站典型工艺流程说明(1)为保证管道的运行产安全,减压站必须设进站和出站压力泄放系统。
(2)减压阀上下游应设置截断阀。
减压阀应设两组以上,热备。
2.中间减压站工艺流程应具有的功能:(1)减压/加热外输;(2)压力泄放;(3)清管器接收、发送;(4)压力泄放;(5)泄压罐油品回注。
3.中间减压站典型工艺流程图中间减压分输站典型工艺流程图举例:3-1-23为“减压站工艺流程图(带分输)”,对于独的减压站,取消分输部分。
(八)中间清管站中间清管站主要包括:清管站、清管分输站、清管输入站等。
1.中间清管站典型工艺流程说明(1)单独的清管站操作阀门可采用手动阀门,若阀门的口径较大,操作不便,可对操作的阀门可采用电动阀门,阀门可采用临时移动电源。
(2)清管分输站根据需要,设进站的超压泄放流程,可采用泄压罐,也可采用泄入管道下游段,若采用泄压罐,还需设泄压罐油品回注流程。
2.中间清管站工艺流程应具有的功能(1)越站外输;(2)清管器接收、发送。
3.中间清管站典型工艺流程图中间清管站典型工艺流程图举例:图3-1-24为“清管站典型工艺流程图”,图3-1-25为“清管分输站典型工艺流程图”。
213214215216217(九)末站1.输油末站典型工艺流程说明输油末站根据输送油品的不同,主要分为单一油品末站和多种油末站。
根据末站的外输功能不同,输油末站外输应包括:管道转输、油品装火车/汽车、装船等。
(1)对于装船、火车、汽车的流程部分根据规范要求,应在装车栈桥及装车台的规定部分设置便于操作的紧急切断阀。
(2)对于加热输送的输油管道,必要时还应设置反输流程。
(3)在进站压力允许的情况下,流程应做到接收上站来油后,不进油罐,可直接经计量后外输。
(4)输油末站和输油首站一样,油罐区的管线可采用单管或双管。
倒罐流程根据需要可设独立的流程,也可不设。
(5)在有油品交接的管道末站,应设管道交接计量流程,流量计的标定应为在线标定,设固定式标准体积管及水标定系统。
(6)对于易凝原油的装船管线应设置为双线,并应具有管线循环功能。
2.输油末站工艺流程应具有的功能根据末站的外输功能不同,输油末站外输应包括:管道转输、油品装火车/汽车、装船等。