机械制造技术基础(第二章)讲解
机械制造技术基础 第2章
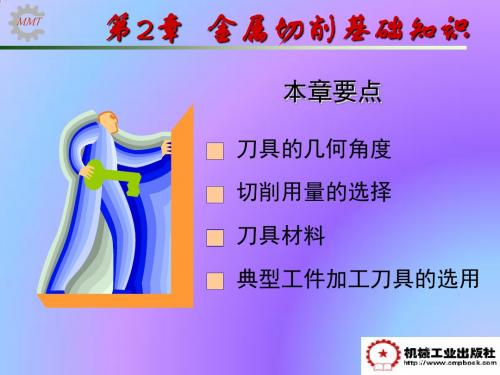
MMT
2.2.3 刀具工作角度
• 在横向进给切削或切断 工件时,随着进给量f值的增 加和加工直径d的减小,工作 后角不断减小,刀尖接近工 件中心位置时,工作后角的 减小特别严重,很容易因后 面和工件过渡表面剧烈摩擦 使刀刃崩碎或工件被挤断, 切削中应引起充分重视。因 此,切断工件时不宜选用过 大的进给量f,或在切断接近 结束时,应适当减小进给量 或适当加大标注后角。
MMT
2.2.3 刀具工作角度
当工件材料和加工性质不同时,常用硬质合金车刀的 合理前角如表2-1所示。
表2-1 合理前角 粗 车 精 车 硬质合金车刀合理前角的参考值 合理前角 粗 车 精 车
工件材料 低碳钢 中碳钢 合金钢 淬火钢
工件材料 灰铸铁 铜及铜合金 铝及铝合金 钛合金 ≤1.177 GP a
MMT
2.1.1 切削运动
3、合成切削运动
刀具与工件间的相对切削运 动是主运动和进给运动的合成运 动。切削刃上选定点相对于工件 的主运动的瞬时速度,称为切削 速度,以vc表示。切削刃上选定点 相对于工件的进给运动的瞬时速 度,称为进给速度,以vf表示。合 成切削运动的瞬时速度用ve表示。 则ve=vc+vf 。
MMT
2.2.2 刀具静止角度参考系及其坐标平面
MMT
2.2.2 刀具静止角度参考系及其坐标平面
刀具静止角度
2.
MMT
2.2.2 刀具静止角度参考系及其坐标平面
刀具在正交平面参考系中定义的标注角度有: (1)前角 γo :前刀面与基面间的夹角(正交平面中测量) 作用:影响切屑的变形程度; 影响刀刃强度
后角α0:后刀面与切削平面间的夹角(正交 平面中测量)
MMT
2.2.2 刀具静止角度参考系及其坐标平面
机械制造(第2版)第二章课后习题解答
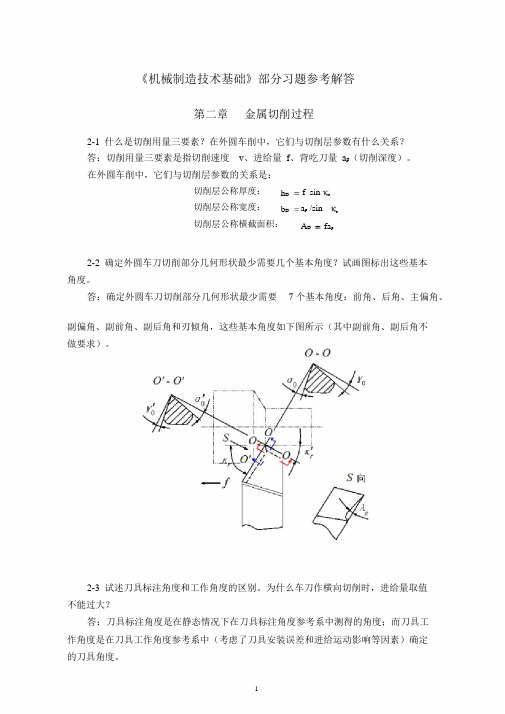
Fc
C a f v K x Fc pFc
yFc n
c Fc
sFc
900 31 0.4 0.75 80 0 1.0 1358N
Fp
xFp
yFp nFp
CFpap f vc K sFp
530 3 0.9 0.4 0.75 80 0 1.5 1075N
Ff
xFf
yFf nFf
CFf ap f vc K sFf
450 31 0.4 0.4 80 0 0.75 702N
再根据 p38公式(2-17),可得切削功率 P c Fcvc 10 3 1358 80/ 60 10 3 1.81 KW
2-11 影响切削力的主要因素有哪些?试论述其影响规律。 答:(P41-42)影响切削力的主要因素有工件材料、切削用量、刀具几何参数、刀具 磨损、切削液和刀具材料。 工件材料的影响:工件材料强度、硬度越高,切削力越大; 切削用量的影响:背吃刀量 ap影响最大,几乎成正比; f 次之,v 最小。
2-13 试分析刀具磨损四种磨损机制的本质与特征,它们各在什么条件下产生? 答:(P47)刀具磨损四种磨损机制的本质和特征: 硬质点划痕:工件材料有硬质点,造成机械磨损,有划痕、划伤。 冷焊磨损:即粘接磨损,在高压高温作用下,刀具材料被粘接、撕裂,导致磨损。 扩散磨损:在高温下刀具材料中金属原子扩散,导致材料软化磨损。 化学磨损:由于化学腐蚀、氧化作用产生的磨损。
2-6 怎样划分切削变形区?第一变形区有哪些变形特点? 答:切削形成过程分为三个变形区。第一变形区切削层金属与工件分离的剪切滑移 区域,第二变形区前刀面与切屑底部的摩擦区域;第三变形区刀具后刀面与已加工表面 的摩擦区域。 第一变形区的变形特点主要是:金属的晶粒在刀具前刀面推挤作用下沿滑移线剪切 滑移,晶粒伸长,晶格位错,剪切应力达到了材料的屈服极限。
第2章 机械制造技术基础(2—2)

体现的是工 件中心线
工件与V型块的接 触为:两条母线
●定位基准的选择实际上是定位基面的选择。
●根据是否被加工,定位基面可分精基面(光面) 和粗基面(毛面)。
五、定位误差的分析和计算
1. 定位误差的定义及产生的原因
用调整法加工一批工件时,工件在定位过程中会遇
到如下情况: ● 工序基准与定位基准不重合 ● 基准位置误差
导致工件的工序基 准偏离理想位置而 产生定位误差。
定位误差:工件在夹具(或机床)上定位不准确(工 序基准偏离理想位)而引起的加工误差。
定位误差值的大小d :工序基准沿工序尺寸方向发生 的最大位移量。
(1)基准不重合引起的定位误差
如图所示,用调整法加工C面。工序基准:B面。
B
jb
H4
C H1
H4
H1
H
H1max H1min
A
工件的工序基准与定 位基准不重合。
由于尺寸H1的误差会使工件顶面位置发生变化,从 而使工序尺寸H4产生误差。
基准不重合误差: jb
H H
(2)基准位置误差
定位副制造不准确引起的定位误差
如图所示,用调整法加工键 槽。工序基准:O点。
jy O
d
工件外圆直径尺寸有大有小,会使外圆中心位置 发生变化,从而导致工序尺寸H的变化——基准发生 位移导致工序尺寸H的加工误差。
化的元件拼装而成。
特点:灵活多变,万能 性强,制造周期短,元 件可以重复使用。
(5)随行夹具
这是一种在自动线或柔性制造系统中使用的夹具。工件安 装在随行夹具上,除完成对工件的定位和夹紧外,还载着工件 由运输装置送往各机床,并在各机床上被定位和夹紧。
二、夹具的组成
机械制造技术基础课件第二章

2.1 零件表面成形的方法及机床切削成形运动 2.1.1 零件表面的成形方法 各种表面的组合构成了不同的零件形状,所以 零件的切削加工归根到底是表面成形问题。 组成零件的常见表面有:内、外圆柱面和圆锥 面、平面、球面和一些成形表面(如渐开线面、 螺纹面和一些特殊的曲面等)。
2-1机器零件的组成表面
传动链包括各种传动机构,如带传动、 定比齿轮副、齿轮齿条副、丝杠螺母副、 蜗轮蜗杆副、滑移齿轮变速机构、离合器 变速机构、交换齿轮或挂轮架以及各种电 的、液压的和机械的无级变速机构、数控 机床的数控系统等。上述各种机构又可以 分为具有固定传动比的“定比机构”(例 如定比齿轮副、齿轮齿条副、丝杠螺母副 等)和可变换传动比的“换置机构”(例 如齿轮变速箱、挂轮架、各类无级变速机 构等)两类。
床、其它机床。每一大类机床中,按结构、性能、
工艺范围、布局形式和结构的不同,还可细分为若 干组,每一组又细分为若干系(系列)。
3)机床型号的编制方法 按1985年国家机械工业部颁布的《金属切 削机床型号编制方法》部颁标准(JB1838-85) 和1994年国家标准局颁布的《金属切削机床型 号编制方法》国家推荐标准(GB/T15375-94),
图2-10 卧式车床所能加工的典型表面
车床按其用途和结构的不同可分为:普通车 床、六角车床、立式车床、塔式车床、自动和半
自动车床、数控车床等等。普通车床是车床中应
用最广泛的一种,约占车床总数的60%,其中 CA6140 卧式车床为目前最为常见的型号之一。 为正确选择和合理使用机床,应了解机床的技术 性能。通常机床的技术性能包括:工艺范围、机
普通机床型号用下列方式表示。
(◎) ○ (○) ◎ ◎ (×◎)(○)(/◎)
机械制造工艺基础(第二章)教案

任课教师:胡迎春 班级:13级车、铣、钳 日期:4.28第二章锻压单元计划目的要求 1、掌握锻造的分类及工艺过程。
2、了解锻造的特点及应用。
3、掌握冲压的分类、特点及应用。
4、能够准确的判断锻造缺陷及产生的原因。
重点 1、锻造的分类及工艺过程。
2、冲压的分类。
3、锻造中的缺陷及产生的原因。
难点 自由锻与模锻的区别、冲压的不同工序。
课时安排 概述(1个课时)金属的加热和锻件冷却(1个课时)自由锻(2个课时)模锻(1个课时)冲压(1个课时)复习(1个课时)讲解习题册(1个课时)任课教师:胡迎春 班级:13级车、铣、钳 日期:4.29课程名称 机械制造工艺基础授课内容 教材对应位置 审批:压力加工 章 节二 1授课时数 1 授课时间 第二周 授课方式 讲授法教学目标认 知 目 标 掌握锻压的定义分类。
掌握锻造、冲压的定义及分类。
了解锻造、冲压的特点。
了解其他的压力加工的方法。
情 感 目 标 开拓思维,全面灵活的考虑、处理问题专业能力目标 锻压的定义及分类。
锻造冲压的定义分类。
教学重难点 教学重点 锻压的定义及分类。
锻造冲压的定义分类。
教学难点 压力加工的工序突破方法 通过观看锻压的加工视频、例举常见的锻压零件的实例加强理解。
自主探究 学生自行讨论在实际中所见到的锻压。
教 具 多媒体教学过程 主要内容及步骤组织教学 维持秩序、清点人数导入新课 把原材料制成毛坯是零件加工的前提,通常是由热加工工序来完成。
确定零件的结构时,必须与毛坯制造的工艺特点相适应,机械加工常用的毛坯有铸件、锻件、焊件和型材。
本章着重介绍应用普遍的锻压。
讲授新课 第二章 锻压§2-1 压力加工锻压:对坯料施加外力,使其产生塑性变形、改变尺寸、形状及改善性能,用以制造机械零件、工件或毛坯的成形加工方法。
一、锻造教学过程 主 要 教 学 内 容 及 步 骤讲授新课锻造:在加压设备及工(模)具的作用下,使金属坯料或铸锭产生局部或全部的塑性变形,以获得一定几何形状、尺寸和质量的锻件的加工方法。
机械制造技术基础-课件

图15
图16
(2)孔加工刀具
孔加工刀具一般 可分为两大类:一 类是从实体材料上 加工出孔的刀具, 常用的有麻花钻、 中心钻和深孔钻等; 另一类是对工件上 已有孔进行再加工 用的刀具,常用的 有扩孔钻、铰刀及 镗刀等。
在法平面参考系中,只需标注γn 、 αn 、 κr 和λs四个角度即可确 定主切削刃和前、后刀面的方位。在假定工作平面参考系中,只 需标注γf 、αf 、γp 、 αp 四个角度便可确定车刀的主切削刃和前、 后刀面的方位。
四、刀具的工作角度
在实际的切削加工中,由于刀具安装位置和进给运动的影响,上 述标注角度会发生一定的变化。角度变化的根本原因是切削平面、 基面和正交平面位置的改变。以切削过程中实际的切削平面Ps、基 面Pr和主剖面P0为参考平面所确定的刀具角度称为刀具的工作角度, 又称实际角度。
(6)刀尖 主切削刃和副切削刃连接处的一段刀刃。它可以是小 的直线段或圆弧。
具体参见切削运动与切削表面图和车刀的组成图。其它各类刀具,
如刨刀、钻头、铣刀等,都可以看作是车刀的演变和组合。
刨刀
图4
钻头
(二)刀具角度的参考系
为了确定刀具切削
部分各表面和刀刃的空 间位置,需要建立平面 参考系。按构成参考系 时所依据的切削运动的 差异,参考系分成以下 两类:
2、车刀安装偏斜对工作角度的影响
图12
当车刀刀杆的纵向轴线与进给方向不垂直时,将会引起 工作主偏角κre和工作副偏角κre‘的变化,如上图所示。
(二)进给运动对工作角度的影响
1、横向 进给运 动对工 作角度 的影响
图13 车端面或切断时,加工表面是阿基米德螺旋面,如上图所示。因此,实际 的切削平面和基面都要偏转一个附加的螺旋升角μ,使车刀的工作前角γoe增 大,工作后角αoe减小。一般车削时,进给量比工作直径小很多,故螺旋升 角μ很小,它对车刀工作角度影响不大,可忽略不计。但在车端面、切断和 车外圆进给量(或加工螺纹的导程)较大,则应考虑螺旋升角的影响。
机械制造基础第二章2

位错对材料性能的影响比点缺陷更大, 位错对材料性能的影响比点缺陷更大 , 对金属材料的影 响尤甚。理想晶体的强度很高,位错的存在可降低强度, 响尤甚 。 理想晶体的强度很高,位错的存在可降低强度 , 但 是当错位量急剧增加后,强度又迅速提高。 是当错位量急剧增加后,强度又迅速提高。 生产中一般都是增加位错密度来提高强度, 生产中一般都是增加位错密度来提高强度 , 但是塑性 随之降低,可以说, 随之降低 , 可以说 , 金属材料中的各种强化机制几乎都是 以位错为基础的。 以位错为基础的。 3. 面缺陷:指在两个方向上的尺寸很大,第三个方向上的 面缺陷:指在两个方向上的尺寸很大, 尺寸很小而呈面状的缺陷。 尺寸很小而呈面状的缺陷。面缺陷的主要形式是各种类型 的晶界。 的晶界。 晶界:指晶粒与晶粒之间的边界。 晶界:指晶粒与晶粒之间的边界。
图1-6 冷却曲线
3.结晶过程。 晶体形核和成长过程。如图1-7所示,在液 3.结晶过程。 晶体形核和成长过程。如图1 所示, 结晶过程 体金属开始结晶时, 体金属开始结晶时,在液体中某些区域形成一些有规则排 列的原子团,成为结晶的核心, 形核过程)。 列的原子团,成为结晶的核心,即晶核 (形核过程)。 然后原子按一定规律向这些晶核聚集,而不断长大, 然后原子按一定规律向这些晶核聚集,而不断长大,形成 晶粒(成长过程)。在晶体长大的同时, )。在晶体长大的同时 晶粒(成长过程)。在晶体长大的同时,新的晶核又继续 产生并长大。当全部长大的晶体都互相接触,液态金属完 产生并长大。当全部长大的晶体都互相接触, 全消失,结晶完成。由于各个晶粒成长时的方向不一, 全消失,结晶完成。由于各个晶粒成长时的方向不一,大 晶界。 小不等,在晶粒和晶粒之间形成界面,称为晶界 小不等,在晶粒和晶粒之间形成界面,称为晶界。
机械制造技术第二章课后答案
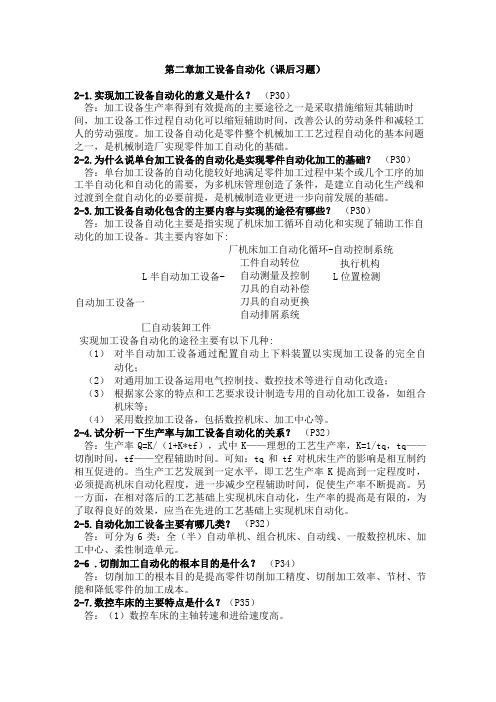
第二章加工设备自动化(课后习题)2-1.实现加工设备自动化的意义是什么? (P30)答:加工设备生产率得到有效提高的主要途径之一是采取措施缩短其辅助时 间,加工设备工作过程自动化可以缩短辅助时间,改善公认的劳动条件和减轻工 人的劳动强度。
加工设备自动化是零件整个机械加工工艺过程自动化的基本问题 之一,是机械制造厂实现零件加工自动化的基础。
2-2.为什么说单台加工设备的自动化是实现零件自动化加工的基础? (P30) 答:单台加工设备的自动化能较好地满足零件加工过程中某个或几个工序的加 工半自动化和自动化的需要,为多机床管理创造了条件,是建立自动化生产线和 过渡到全盘自动化的必要前提,是机械制造业更进一步向前发展的基础。
2-3.加工设备自动化包含的主要内容与实现的途径有哪些? (P30)答:加工设备自动化主要是指实现了机床加工循环自动化和实现了辅助工作自 动化的加工设备。
其主要内容如下:匚自动装卸工件实现加工设备自动化的途径主要有以下几种:(1) 对半自动加工设备通过配置自动上下料装置以实现加工设备的完全自动化;(2) 对通用加工设备运用电气控制技、数控技术等进行自动化改造;(3) 根据家公家的特点和工艺要求设计制造专用的自动化加工设备,如组合机床等;(4) 采用数控加工设备,包括数控机床、加工中心等。
2-4.试分析一下生产率与加工设备自动化的关系? (P32)答:生产率Q=K/(1+K*tf ),式中K ——理想的工艺生产率,K=1/tq ,tq —— 切削时间,tf ——空程辅助时间。
可知:tq 和tf 对机床生产的影响是相互制约 相互促进的。
当生产工艺发展到一定水平,即工艺生产率K 提高到一定程度时, 必须提高机床自动化程度,进一步减少空程辅助时间,促使生产率不断提高。
另 一方面,在相对落后的工艺基础上实现机床自动化,生产率的提高是有限的,为 了取得良好的效果,应当在先进的工艺基础上实现机床自动化。
- 1、下载文档前请自行甄别文档内容的完整性,平台不提供额外的编辑、内容补充、找答案等附加服务。
- 2、"仅部分预览"的文档,不可在线预览部分如存在完整性等问题,可反馈申请退款(可完整预览的文档不适用该条件!)。
- 3、如文档侵犯您的权益,请联系客服反馈,我们会尽快为您处理(人工客服工作时间:9:00-18:30)。
七.磨削
砂轮的修整 由于砂轮的“自锐性”以及切屑和碎磨粒会阻塞砂轮,
在磨削一定时间后,需用金刚石车刀等对砂轮进行修整
磨床是精加工机床, 磨削 精度可达IT6—IT4, 表面粗糙 度Ra可达1.25—0.01μm, 甚至 可达0.1—0.008μm.往往作为 最终加工工序.磨削的另一特 点是可以对淬硬的金属材料进 行加工。磨削时, 产生热量大, 需有充分的切削液进行冷却。
1.轨迹法 2.成形法 3.相切法 4.展成法
四、零件表面的成形运动
1.主运动(只有一个) 2.进给运动 3.辅助运动
分度运动 切入运动
2.3外圆表面加工
外圆表面的技术要求一般为: (1)外圆面直径和长度的尺寸精度。 (2)圆度、圆柱度和轴线的直线度 等形状精度。 (3)与其他外圆面(或孔)之间的 同轴度,与相关平面的垂直度和径向 圆跳动等。 (4)表面粗糙度、表面 层硬度等热处理要求等。
机械制造技术基础
(第二章 机械制造中的加工方法)
主讲: 肖新华
天津工业大学机械工程学院
2.1 概述
机械零件的结构形状千变万化。零件结构形式的 不同,使之有很多的加工方法,根据加工过程中零 件质量的变化情况,零件的制造过程可分为Δm<0, Δm=0和Δm>0三种形式,不同的类型有不同的工艺 方法。
一. Δm<0的制造过程
质量减少的加工过程, 即零件的切削加工, 零件的主要加工形式, 是本书的研究重点。
2.1 概述
切削加工是通过刀具与工件之间的相对 运动,逐渐切除材料而得到所需要的零件表 面形状的方法。为了保证工件与刀具之间的 相互位置关系,工件往往通过夹具安装在机 床上,机床主轴带动刀具或工件运动。
在切削加工过程中,由于力、热、振动、 磨损等因素会综合影响零件最终的加工精度 和表面质量。
(1)高精度磨削
高精度磨削是在普通磨削方法的基 础上:
提高砂轮磨粒的等高性 选择合适的砂轮(材料、粒度、硬度) 选择合适的磨削用量 (磨削速度、进
给量、磨削深度) 性能良好的切削液 精度和刚度较高的磨床
(2)超精加工
超精加工视频 强烈切削阶段 、正常切削阶段 、微弱切削阶段 、停止 切削阶段
4)工件的外圆表面与其它表面的位置精度较 低。
5)整加工是从工件表面不切除 或切除极薄金属层,以提高工件表 面的尺寸和形状精度、减小表面粗 糙度和提高表面性能为目的的加工 方法。加工精度能达到IT6以上,表 面粗糙度能达到小于0.2μm。外圆 表面的光整加工方法有高精度磨削、 超精加工、研磨、珩磨及抛光等。
外圆表面的磨削
1.中心磨削
(1)纵磨 (2)横磨 (3)复合磨
2.无心磨削(纵磨、横磨、复合磨)
纵磨特点:工件或砂轮需作轴向进给。磨削深度小、磨削接触面积 小,散热较好,容易得到较高的精度和表面质量,因而应用广泛。 但由于走刀次数多,生产效率低,适用于单件小批生产中磨削较长 的外圆表面。
横磨
横磨特点:砂轮宽度大于磨削宽度。工件不需作轴
2.2 零件的成形方法
一、零件表面的形状
锥面 外圆 渐开线表面
螺纹表面 内孔 平面
二、零件表面成形原理
零件表面可看成母线沿着导线运动形成的轨迹。 母线A和导线B统称为形成表面的发生线。根据母 线和导线的运动关系,常见零件表面可分成3类
1.旋转表面 2.纵向表面 3.特形表面
三、零件表面成形方法
无心磨削
加工视频
无心磨削特点
1)生产效率较高,省去了打中心孔的工序。 同时,由于有导轮和托板全长支撑工件,即使刚度 较差的工件也可以用较大的磨削深度进行磨削。
2)无心磨削所获得的外圆表面的尺寸精度和 形状精度较高,表面质量也比较好。这是因为没有 中心孔之间误差的影响,主轴跳动的影响。
3)配以适当的自动装卸工件机构,容易实现 加工过程的自动化。
二.Δm=0的制造过程
在制造过程中,如果工件加工前后质量基 本不变 。比如铸造、锻造、焊接、冲压等。 加工特点是生产效率高,但是精度较低,多 用于制造毛坯。据统计,机电产品40%~50% 的零件是由模具成形的。模具可分为注射模、 压铸模、锻模、冲裁模、拉伸模、吹塑膜等。 模具设计制造是一个技术密集型的产业,涉 及CAD、CAE、CAM等一系列技术。
2.3外圆表面加工
1.车削 2.磨削 3.光整加工
2.3外圆表面加工
车削加工
钳工和机械加工
车削加工范围
车削的四个阶段:
外圆车削
粗车
半精车
精车
精细车
IT13~IT10 Ra12.5~6.3m IT8~IT7 Ra3.2~0.8m
IT10~IT9 Ra6.3~3.2m
IT7~IT6 Ra0.8~0.2m
三.Δm>0的制造过程
可以成形任意复杂形状的零件,而无须刀
具、夹具等生产准备活动。这类加工方法包括
电镀、化学镀、喷涂等沉积加工以及快速原型
制造等。 快速原形(Rapid Prototyping:RP,3D
打印)技术是在零件三维CAD模型建立之后,可 立即输入快速成形系统,然后自动生成数控代 码控制成形机进行零件的制造。快速制造出来 的原型可作为设计评估、投标或展示的样件, 有些甚至可以用于样机试验。
七.磨削
特点:主运动是砂轮的旋转运动; 磨削过程:实际上是磨粒对工件表面的切削、刻削和滑擦三种
作用的综合效应; 砂轮的“自锐性” :磨削中,磨粒本身也会由尖锐逐渐磨钝,
使切削能力变差,切削力变大,当切削力超过粘结剂强度时, 磨钝的磨粒会脱落,露出一层新的磨粒,这就是砂轮的“自 锐性”。
向进给,砂轮相对工件连续或断续地作径向进给。
横磨法生产效率高,但加工精度低,表面粗糙度大。主要原因是磨 削时工件与砂轮的接触面积大,磨削力大,发热较多,容易产生磨 削烧伤和变形。适用于大批大量生产中磨削刚性较好的工件外圆。
复合磨
对于刚性较好的长轴外圆表面,可以先用横磨法分段粗 磨外圆表面的全长,相邻各段留5~15mm重合区域,最后 用纵磨法进行精磨,此法即为复合磨法。复合磨法兼有横 磨法的高生产效率和纵磨法加工质量较好的优点。
(3)研磨
研磨是由游离的磨粒通过研 具对工件进行微量切削的过 程,其精度可达到亚微米级