对刀仪调试
自动对刀仪的设置与操作

自动对刀仪的设置与操作内容来源网络,由“深圳机械展(11万㎡,1100多家展商,超10万观众)”收集整理!更多cnc加工中心、车铣磨钻床、线切割、数控刀具工具、工业机器人、非标自动化、数字化无人工厂、精密测量、3D打印、激光切割、钣金冲压折弯、精密零件加工等展示,就在深圳机械展.自动对刀的操作和设定一:准备工作1:自动对刀的目的是让刀具自动跑到对刀点,然后把Z轴的机械坐标设到自己想要的工件坐标系统中,比如G54,G55,G59.7,G59.8, 从而省去人工对刀的麻烦.2:实现自动对刀前的准备a :在自己想要的地方装好对刀仪,对刀仪的种类有很多,选其中一种举例说明,该对刀仪构造为一个传感器(接近开关)和一个铁块,当有铁块的物体接近它的时候,该传感器就会+24v输出,(传感器接线方法说明书上有)。
B:传感器和新代组件的接线方法把传感器+24v信号输出线接到标有SYNTEC –TB16-5。
0的板子上的一个空闲的端子上,,比如I24(以后都以I14为例)。
C:修改PLC:在软驱中插入一空白软盘,找到诊断功能----》系统备份,把PLC备份出来,在个人电脑用OPENPLC 这个软件打开软盘中CNC。
LAD ,可在程序里添加一行语句(I14只是举例,如果你接的是I15,相应改为I15)。
二,自动对刀的动作步骤:1,Z轴先向上跑到机械原点(目的是为了防止撞刀)。
2,Z轴在X,Y平面上移动到对刀仪的上方,(准备对刀)3,Z轴以第一段速率快进到对刀仪的铁块上方,改用慢速(第二段速率)慢慢接近铁块,把铁块往下压,一直到铁块靠近传感器,这时传感器红灯会亮,有+24v信号输入到I14,当控制器I14端子接受到信号后,Z轴此时会自动上升到机械原点,(这里采用两段速率的目的是第一段快进,节省时间,为了防止速度太快,把刀具撞坏,在快要接近对刀仪时慢速前进,这样就不会损坏刀具)。
4,当Z轴上升到机械原点后,这时,自动对刀的坐标就已经设到工件坐标系中了(这个程式是设到G59。
对刀仪的使用方法
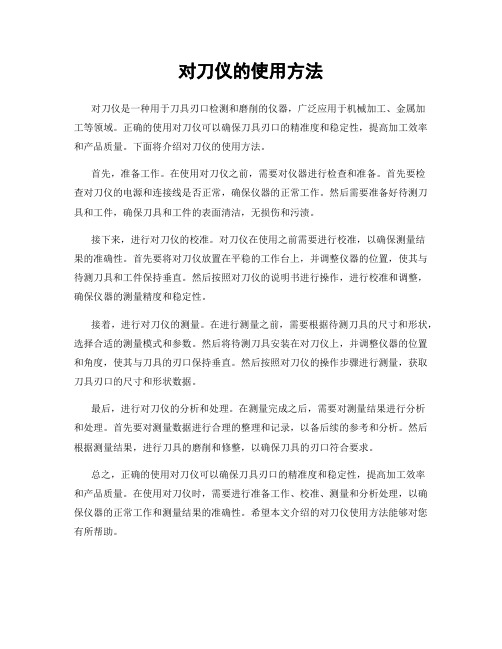
对刀仪的使用方法对刀仪是一种用于刀具刃口检测和磨削的仪器,广泛应用于机械加工、金属加工等领域。
正确的使用对刀仪可以确保刀具刃口的精准度和稳定性,提高加工效率和产品质量。
下面将介绍对刀仪的使用方法。
首先,准备工作。
在使用对刀仪之前,需要对仪器进行检查和准备。
首先要检查对刀仪的电源和连接线是否正常,确保仪器的正常工作。
然后需要准备好待测刀具和工件,确保刀具和工件的表面清洁,无损伤和污渍。
接下来,进行对刀仪的校准。
对刀仪在使用之前需要进行校准,以确保测量结果的准确性。
首先要将对刀仪放置在平稳的工作台上,并调整仪器的位置,使其与待测刀具和工件保持垂直。
然后按照对刀仪的说明书进行操作,进行校准和调整,确保仪器的测量精度和稳定性。
接着,进行对刀仪的测量。
在进行测量之前,需要根据待测刀具的尺寸和形状,选择合适的测量模式和参数。
然后将待测刀具安装在对刀仪上,并调整仪器的位置和角度,使其与刀具的刃口保持垂直。
然后按照对刀仪的操作步骤进行测量,获取刀具刃口的尺寸和形状数据。
最后,进行对刀仪的分析和处理。
在测量完成之后,需要对测量结果进行分析和处理。
首先要对测量数据进行合理的整理和记录,以备后续的参考和分析。
然后根据测量结果,进行刀具的磨削和修整,以确保刀具的刃口符合要求。
总之,正确的使用对刀仪可以确保刀具刃口的精准度和稳定性,提高加工效率和产品质量。
在使用对刀仪时,需要进行准备工作、校准、测量和分析处理,以确保仪器的正常工作和测量结果的准确性。
希望本文介绍的对刀仪使用方法能够对您有所帮助。
对刀仪使用说明
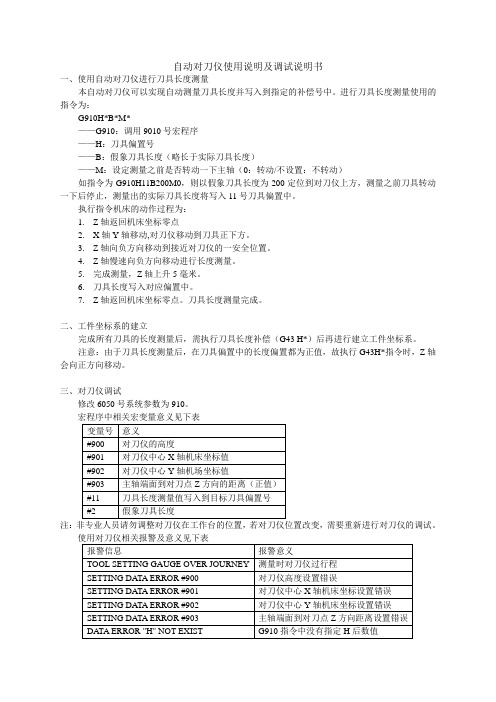
自动对刀仪使用说明及调试说明书一、使用自动对刀仪进行刀具长度测量本自动对刀仪可以实现自动测量刀具长度并写入到指定的补偿号中。
进行刀具长度测量使用的指令为:G910H*B*M*——G910:调用9010号宏程序——H:刀具偏置号——B:假象刀具长度(略长于实际刀具长度)——M:设定测量之前是否转动一下主轴(0:转动/不设置:不转动)如指令为G910H11B200M0,则以假象刀具长度为200定位到对刀仪上方,测量之前刀具转动一下后停止,测量出的实际刀具长度将写入11号刀具偏置中。
执行指令机床的动作过程为:1.Z轴返回机床坐标零点2.X轴Y轴移动,对刀仪移动到刀具正下方。
3.Z轴向负方向移动到接近对刀仪的一安全位置。
4.Z轴慢速向负方向移动进行长度测量。
5.完成测量,Z轴上升5毫米。
6.刀具长度写入对应偏置中。
7.Z轴返回机床坐标零点。
刀具长度测量完成。
二、工件坐标系的建立完成所有刀具的长度测量后,需执行刀具长度补偿(G43 H*)后再进行建立工件坐标系。
注意:由于刀具长度测量后,在刀具偏置中的长度偏置都为正值,故执行G43H*指令时,Z轴会向正方向移动。
三、对刀仪调试修改6050号系统参数为910。
宏程序中相关宏变量意义见下表注:需要重新进行对刀仪的调试。
四、附件宏程序:O9010(AUTOMATIC TOOL OFFSET)(S.T X500.0 Y400.0 Z330.0+150+HC)(TOOL OFFSET MACRO PROGRAM FOR OFFSET MEMORY B,C V4.0) (G910 H** B*** M0 )(CHANGE PARAMETER NO.6050 DA TA 910)(START)#30=#4001#31=#4003IF[#900GE100.0]GOTO10#3000=110(SETTING DATA ERROR #900)N10IF[#901NE#0]GOTO20#3000=110(SETTING DATA ERROR #901)N20IF[#902NE#0]GOTO30#3000=110(SETTING DATA ERROR #902)N30IF[#903NE#0]GOTO40#3000=110(SETTING DATA ERROR #903)N40IF[#11NE#0]GOTO50#3000=110(DATA ERROR "H" NOT EXIST)N50IF[#905EQ0]GOTO60IF[#905EQ#0]GOTO60#24=#905GOTO70N60#24=5.0N70IF[#906EQ480.0]GOTO80IF[#906EQ580.0]GOTO80IF[#906EQ680.0]GOTO80IF[#906EQ780.0]GOTO80#3000=110(SETTING DATA ERROR #906)N80G91G28G00Z0#22=#5043#20=#5021#21=#5022G01X[#901-#20]Y[#902-#21]F500M19N1000(AUTOMA TIC TOOL MEASURING)IF[#2EQ#0]GOTO100IF[#2GT30]GOTO110#3000=110(DATA ERROR "B")N100#2=250.0N110IF[#7EQ#0]GOTO120G00X#7N120G00Z-[#906-#900-#2-25.0](*)IF[#13EQ#0]GOTO130S50M03G04X0.1M05M00N130M21G04 X1M22G31Z-[25.0+#24]F100(*)#25=#5063#26=#903-[ABS[#22-#25]]IF[[ABS[#906-#900-#2+#24-ABS[#22-#25]]]GT0.001]GOTO160 #3000=110(DATA ERROR B TOOL SHORT)N160Z5.0G90G10L10P#11R#26G91G28Z0IF[#7EQ#0]GOTO3000G00X-#7GOTO3000N3000G#30G#31M05M99。
自动对刀仪的设置与操作学习
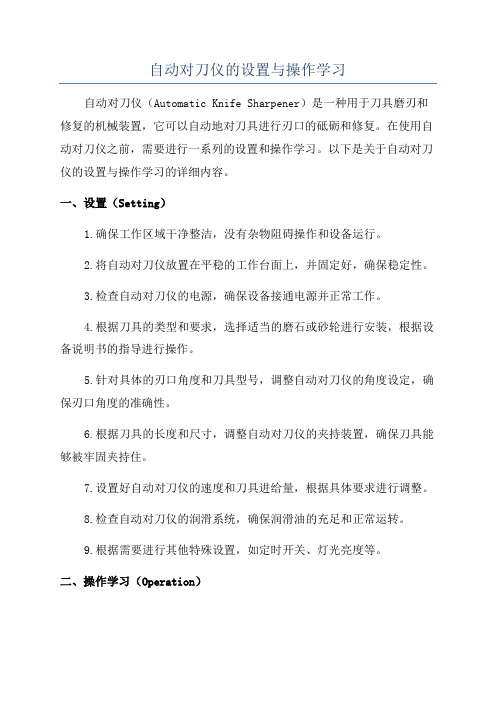
自动对刀仪的设置与操作学习自动对刀仪(Automatic Knife Sharpener)是一种用于刀具磨刃和修复的机械装置,它可以自动地对刀具进行刃口的砥砺和修复。
在使用自动对刀仪之前,需要进行一系列的设置和操作学习。
以下是关于自动对刀仪的设置与操作学习的详细内容。
一、设置(Setting)1.确保工作区域干净整洁,没有杂物阻碍操作和设备运行。
2.将自动对刀仪放置在平稳的工作台面上,并固定好,确保稳定性。
3.检查自动对刀仪的电源,确保设备接通电源并正常工作。
4.根据刀具的类型和要求,选择适当的磨石或砂轮进行安装,根据设备说明书的指导进行操作。
5.针对具体的刃口角度和刀具型号,调整自动对刀仪的角度设定,确保刃口角度的准确性。
6.根据刀具的长度和尺寸,调整自动对刀仪的夹持装置,确保刀具能够被牢固夹持住。
7.设置好自动对刀仪的速度和刀具进给量,根据具体要求进行调整。
8.检查自动对刀仪的润滑系统,确保润滑油的充足和正常运转。
9.根据需要进行其他特殊设置,如定时开关、灯光亮度等。
二、操作学习(Operation)1.将待处理的刀具固定在自动对刀仪的夹持装置中,确保刀具被牢固夹持住。
2.打开自动对刀仪的电源开关,确认设备正常启动,并检查设备的运行状态。
3.根据自动对刀仪的要求和具体的刀具类型,选择相应的程序进行操作。
4.将自动对刀仪的刀具夹紧装置调整到合适位置,并根据刀具的长度进行调整。
5.使用手轮或控制按钮,调整自动对刀仪的角度设定,确保刃口角度符合要求。
6.按下启动按钮,启动自动对刀仪的磨刃机构,使刀具开始磨刃和修复。
7.监视自动对刀仪的运行状态,确保操作平稳,没有异常情况的发生。
8.根据需要,定期检查磨石或砂轮的磨损程度,并及时更换磨损严重的磨具。
9.当刀具磨刃和修复完成后,关闭自动对刀仪的电源,将刀具取出,并进行必要的清洁和检查。
10.将自动对刀仪进行必要的维护,如润滑加油、清洁、零部件更换等。
11.操作结束后,将工作区域清理干净,并将自动对刀仪固定好,准备下一次使用。
Laser的校准和使用方法方法
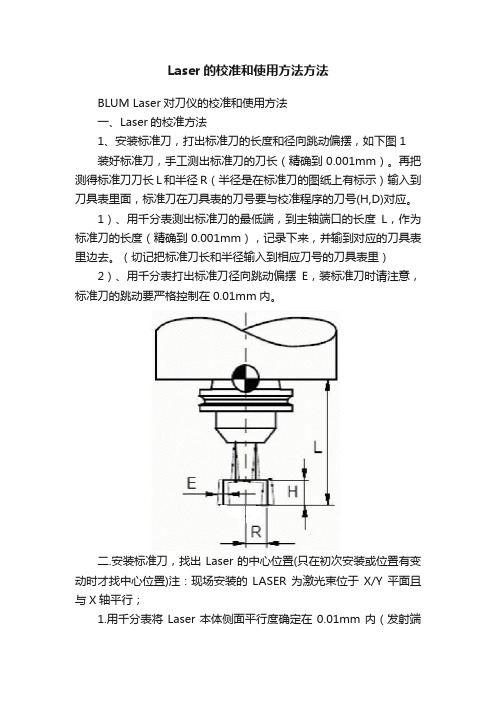
Laser的校准和使用方法方法BLUM Laser对刀仪的校准和使用方法一、Laser的校准方法1、安装标准刀,打出标准刀的长度和径向跳动偏摆,如下图1装好标准刀,手工测出标准刀的刀长(精确到0.001mm)。
再把测得标准刀刀长L和半径R(半径是在标准刀的图纸上有标示)输入到刀具表里面,标准刀在刀具表的刀号要与校准程序的刀号(H,D)对应。
1)、用千分表测出标准刀的最低端,到主轴端口的长度L,作为标准刀的长度(精确到0.001mm),记录下来,并输到对应的刀具表里边去。
(切记把标准刀长和半径输入到相应刀号的刀具表里)2)、用千分表打出标准刀径向跳动偏摆E,装标准刀时请注意,标准刀的跳动要严格控制在0.01mm内。
二.安装标准刀,找出Laser的中心位置(只在初次安装或位置有变动时才找中心位置)注:现场安装的LASER为激光束位于X/Y平面且与X轴平行;1.用千分表将Laser本体侧面平行度确定在0.01mm内(发射端与接收端),如下图:2.手摇手轮,把标准刀移动到Laser的中心位置(目测),用卡尺把标准刀定位在Laser的发射端与接收端的中心位置(精确到0.01mm),记录当前机械坐标值并停止移动。
例如:Laser与机床的X轴平行,就记录当前X轴的机械坐标值。
3.开启Laser(如执行#51524=1 (活塞开启)#51512=1 (模式E0开启)#51513=1 (模式E1开启)),移动标准刀(半径轴方向(Y轴)),手摇手轮,慢慢把标准刀定位到Laser的光线中心处,观察laser上的标有Out put信号灯,当信号灯Out put刚好显示红色时,停止移动,此时的Y轴机械坐标值减去标准刀半径值,将这个值记录;4.手摇手轮移动Z方向,慢慢把标准刀的下端面定位到Laser的中心处,观察信号灯Out put,当信号灯Out put刚好显示红色时,停止移动,此时的Z轴机械坐标值减去标准刀的长度,将这个值记录;如图:三.修改程序参数在O9671程序中找出以下参数,并进行修改:1、laser位置定义1)#104等于刀半径测量轴机械坐标值2)#105等于平行激光轴的机械坐标值3)#106等于刀长测量轴的机械坐标值2、标准刀长度定义1)#138标准刀类型定义:=0:BLUM专用标准=1:自备直棒标准刀2)#126等于标准刀的长度L,3)#127等于标准刀的半径R(该半径在标准刀图纸上有标示,请等于标示值)4)#1 等于标准刀的径向跳动偏摆E5)#128等于标准刀的T台高度H(标准刀图纸上有标示,请等于标示值)具体细见下图2图2四、执行校准程序O0601,校准Laser 程序调用G65 P9601 H…D…A... R… X... Z...H .D 刀具长度和半径补偿编号A 重复测量的次数R 测量结果间的最大偏差值X 测量长度时测量位置的径向偏移Z 测量半径时测量位置的轴向偏移例如:O0601T1M06M03S3000.G65P9601 H1 .A3. R0.01 X5. Z5.M30五、执行完程序,整个校正就完成了。
对刀仪使用流程
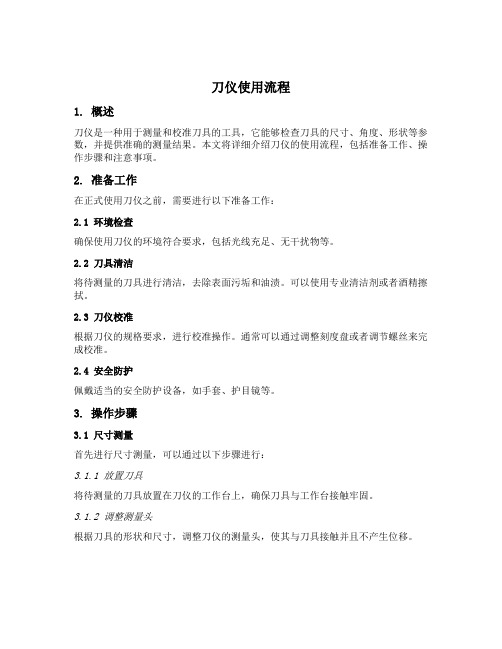
刀仪使用流程1. 概述刀仪是一种用于测量和校准刀具的工具,它能够检查刀具的尺寸、角度、形状等参数,并提供准确的测量结果。
本文将详细介绍刀仪的使用流程,包括准备工作、操作步骤和注意事项。
2. 准备工作在正式使用刀仪之前,需要进行以下准备工作:2.1 环境检查确保使用刀仪的环境符合要求,包括光线充足、无干扰物等。
2.2 刀具清洁将待测量的刀具进行清洁,去除表面污垢和油渍。
可以使用专业清洁剂或者酒精擦拭。
2.3 刀仪校准根据刀仪的规格要求,进行校准操作。
通常可以通过调整刻度盘或者调节螺丝来完成校准。
2.4 安全防护佩戴适当的安全防护设备,如手套、护目镜等。
3. 操作步骤3.1 尺寸测量首先进行尺寸测量,可以通过以下步骤进行:3.1.1 放置刀具将待测量的刀具放置在刀仪的工作台上,确保刀具与工作台接触牢固。
3.1.2 调整测量头根据刀具的形状和尺寸,调整刀仪的测量头,使其与刀具接触并且不产生位移。
按下启动按钮,开始进行尺寸测量。
刀仪会自动移动测量头,并记录下各个位置的尺寸数据。
3.1.4 结果分析等待测量完成后,查看测量结果。
可以通过显示屏或者连接电脑进行数据分析和处理。
3.2 角度测量接下来进行角度测量,可以按照以下步骤进行:3.2.1 安装角度夹具根据待测角度的类型和大小,选择合适的角度夹具,并将其安装在刀仪上。
3.2.2 放置刀具将待测角度的刀具放置在角度夹具上,并固定好位置。
3.2.3 调整测量头根据角度夹具的位置和刀具的形状,调整刀仪的测量头,使其与刀具接触并且不产生位移。
3.2.4 开始测量按下启动按钮,开始进行角度测量。
刀仪会自动移动测量头,并记录下各个位置的角度数据。
3.2.5 结果分析等待测量完成后,查看测量结果。
可以通过显示屏或者连接电脑进行数据分析和处理。
3.3 形状测量最后进行形状测量,可以按照以下步骤进行:3.3.1 安装形状夹具根据待测形状的类型和大小,选择合适的形状夹具,并将其安装在刀仪上。
对刀仪数据校准方法

对刀仪数据校准方法一. S NK对刀方法1.JOG方式下,将标准刀具装在主轴上。
2.在MDI方式下,执行G65P9391A**H**Q**,(注释:A**代表当前附件铣头号,例如在CUSTOM1中显示为M31时,表示的是当前装载了A31号铣头,此时就要输入A31;H**代表制定的长度结果存储的位置,请输入H01;Q**代表当前标准刀具的长度,例如:刀具的长度是150.01MM,就输入Q150.01)3.等程序运行完毕后,在setting菜单中‘刀偏’键进入补偿画面中的(如下图所示)001号的长度列中的形状就是实际测量值,偏差=标准刀具的长度-实际测量值。
4.设定为MDI方式,SETTING菜单。
将写参数改为1。
(如下图所示)5.按功能键[SYSTEM] 数次,或者在按下功能键[>] 后,按下章节选择软键[参数],显示出参数画面。
将参数3202的#4(NE9)改为0。
(如图所示)6.在EDIT方式下,按[PROG]键,进入当前程序目录。
(如下图所示)7.按[设备选择]键,选择[CNCMEM]键,进入CNC目录。
(如下图所示)8. 程序目录,按向下键将光标移到MTB1按[input]键,再按向下键将光标移到调用O9399程序,选择[主程序]键。
(如下图所示)9. 修改程序段N31标号下的#145的数据。
#145=原始数据+偏差。
注意此处的偏差值是运算的带符号的值。
例如:#145=112.45,偏差=-2.3,数据就设定为#145=112.45-2.3。
(如下图所示)10.按功能键数次,或者在按下功能键后,按下章节选择软键[参数],显示出参数画面。
将参数3202的#4(NE9)改为1。
设定为MDI方式,SETTING菜单。
将写参数改为0。
11.第6步中,N31代表的是A31铣头,同理N**标号代表的各个铣头号,如果要校准其它铣头,只需要在更换铣头,然后在第2步中修改A**的头号,再依次执行3到5步,在第6步中选择修改N**代表的铣头号下的#145的数据。
Fanuc机床TS27R对刀仪安装调试说明
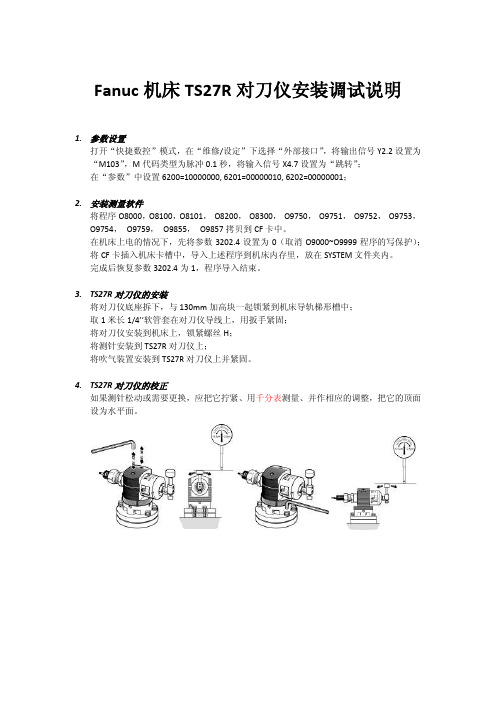
Fanuc机床TS27R对刀仪安装调试说明1.参数设置打开“快捷数控”模式,在“维修/设定”下选择“外部接口”,将输出信号Y2.2设置为“M103”,M代码类型为脉冲0.1秒,将输入信号X4.7设置为“跳转”;在“参数”中设置6200=10000000, 6201=00000010, 6202=00000001;2.安装测量软件将程序O8000,O8100,O8101,O8200,O8300,O9750,O9751,O9752,O9753,O9754,O9759,O9855,O9857拷贝到CF卡中。
在机床上电的情况下,先将参数3202.4设置为0(取消O9000~O9999程序的写保护);将CF卡插入机床卡槽中,导入上述程序到机床内存里,放在SYSTEM文件夹内。
完成后恢复参数3202.4为1,程序导入结束。
3.TS27R对刀仪的安装将对刀仪底座拆下,与130mm加高块一起锁紧到机床导轨梯形槽中;取1米长1/4’’软管套在对刀仪导线上,用扳手紧固;将对刀仪安装到机床上,锁紧螺丝H;将测针安装到TS27R对刀仪上;将吹气装置安装到TS27R对刀仪上并紧固。
4.TS27R对刀仪的校正如果测针松动或需要更换,应把它拧紧、用千分表测量、并作相应的调整,把它的顶面设为水平面。
按本说明内容调整测针:先通过L1,L2调整前后,前高后低则松开L1,紧固L2;前低后高则松开L2,紧固L1;通过L3,L4调整左右,左高右低则松开L4,紧固L3;左低右高则松开L3,紧固L4。
最终将测针平台校正到5um内。
5.对刀仪及控制盒MI8-4的连接1)电源供给B1--24V B2--0V B3--地2)X4.7跳转信号A10--24V A11--X4.7 A12--0V3)连接对刀仪A1--地A2--蓝色A3--红色6.TS27R对刀仪的标定调出各工序中固定的对刀仪校正程序O8000确认程序的内容正确:如标准刀尺寸:长度及直径值等;将标准到手动定位到探针大致中心上方约10mm高度位置;确认以上无误后,按下程序启动进行测头标定;标定程序将找到测针的半径大小以及其机床坐标位置,结果存储在宏变量#520~#525中;7. 测量刀具的长度将待测刀具安装到主轴上,执行测量程序,例如:G90G40G49G00 M6T2 G65P9857B1T2D10. M308. 测量刀具的直径将待测刀具安装到主轴上,执行测量程序,例如: O8102(REN MEAS SINGLE TOOL DIAMETER) G90G40G49G00M6T2 G65P9857B2T2D10. M309. 测量刀具的长度和直径将待测刀具安装到主轴上,执行测量程序,例如: O8103(REN MEAS SINGLE TOOL L&D)G90G40G49G00 M6T2 G65P9857B3T2D10. M3010. 加工中快速检测格式:G65P9857A1.T2H0.02。
- 1、下载文档前请自行甄别文档内容的完整性,平台不提供额外的编辑、内容补充、找答案等附加服务。
- 2、"仅部分预览"的文档,不可在线预览部分如存在完整性等问题,可反馈申请退款(可完整预览的文档不适用该条件!)。
- 3、如文档侵犯您的权益,请联系客服反馈,我们会尽快为您处理(人工客服工作时间:9:00-18:30)。
对刀仪调试
袁绿赞
在实际加工中,对刀仪是很常用的一种测量工具。
使用对刀仪测量可以自动地计算每把刀的刀长与刀宽的差值,并将其存入系统中;在加工零件的时候一般只需要使用标准刀进行一次对刀即可,这样就可以大大的节约了加工时间,除此之外,也可免去人手测量时产生的误差,提高对刀的精度。
一般来说,对刀仪需要编辑宏程序,以下将使用技术支持工程师“郭柯”编写的宏程序来进行对刀仪调试的说明。
以下将采用技术支持工程师郭柯编写的宏程序来说明对刀仪的调试思路:
1、宏程序编程思路
对刀仪用于刀具长度补偿,是以基准刀的长度作为基准,测量出第二把刀,第三把刀等相对于基准刀在长度方向上的差值,然后进行刀具的长度补偿。
一般会采用两到三次对刀以更精确的确定其他刀与标准刀的相差值。
此对刀宏程序编辑便是按照这个思路进行的。
2、使用的系统功能和信号
跳转功能(或高速跳转功能);跳转信号(或高速跳转信号)
l当使用跳转功能和跳转信号时,无需进行参数修改,仅需使用X4.7作为跳转信号即可。
l当使用高速跳转功能和高速跳转信号时需进行如下修改
系统参数修改:
P6200#4=1 在跳过功能中,使用高速跳过信号
P6201#7=1 在跳过指令(G31)中,跳过信号SKIP无效
P6202#0=1 使用高速跳过信号HDI0组
F122.0-F122.3 高速跳过状态信号HDO0-HDO3
高速跳过信号(HDI)信号的连接:
1、 连接于JA40的1,2脚
2、 注意,1,2角仅需短接即可出现高速跳过
信号F122.0,请不要将外部24V 引入
3、 动作时序
动作时序如上图所示:
1) 主轴夹刀并将Z 轴定位到初始平面;快速下降到中间位置
2)
较慢速度下降到中间位置,使用跳过功能缓慢下降直至刀尖碰到对刀仪表面 3) 如3所示返回某一高度
4) 再次以跳转功能缓慢下降进行对刀
5) 如5所示快速返回初始平面,然后将测量计算出来的长度差值补偿到刀具长度补偿里面
4、 宏程序
Ø 调用格式
G65 P9002 Hh (h 是刀具长度补偿号)
第一次使用对刀仪需先进行1号到的对刀,即标准刀的长度测量。
3
Ø宏程序内容
%
O9002;
#30=#4001;
#31=#4003;
#32=#4109;
#1=300.; #1为动作一移动距离
#2=68.2; #2*2为动作二移动距离
#3=68.2;
G28G91Z0.;
#4=#5003;
G00G90G53X-314.412Y-255.895; 将此坐标修改为对刀仪所在位置G91G43Z-#1H#11;
#5=#5003-#2;
IF[#11GT1]GOTO3;
G31Z-[#2*2]F300;
G00G91G49Z#3;
#6=#5063-#[11000+#11];
IF[#6LE[#5-#2]]GOTO9;
#[11000+#11]=#5063-#5;
G31G91G43H#11Z-[#3*2]F50;
#506=#5023;
G00G90G49Z#4;
#6=#5063-#[11000+#11];
IF[#6LE[#5-#2]]GOTO9;
#[11000+#11]=#5063-#5;
#11001=0;
N2G#30G#31F#32;
M99;
N3G31Z-[#2*2]F300;
#507=#5023;
G00G91G49Z#3;
#6=#5063-#[11000+#11]
IF[#6LE[#5-#2]]GOTO9;
#[11000+#11]=#507-#506;
G31G91G43H#11Z-[#3*2]F50;
#507=#5023;
G00G90G49Z#4;
#6=#5063-#[11000+#11];
IF[#6LE[#5-#2]]GOTO9;
#[11000+#11]=#507-#506;
IF[11GT1]GOTO2;
N9#3000=1;
%。