先进制造技术论文(中英文翻译)
模具制造论文中英文对照资料外文翻译文献

中英文对照资料外文翻译文献英文原文:High-speed cutting processing in mold manufactureapplicationAbstractThe current mold application is widespread, also had the very big development with it related die making technology. At present, used the high-speed cutting production mold already to become the die making the general trend. In some mold Manufacturer, the high speed engine bed big area substitution electrical discharge machine, the high-speed cutting production mold already gradually became the die making the general trend. It can improve mold's size, the shape and the surface roughness, reduces even omits the manual sharpening, thus reduces production cost and the reduction manufacturing cycle. This article through to the traditional mold processing craft and the high speed mold processing craft's contrast, elaborated the high-speed cutting processing superiority. In the article also briefly introduced the high-speed cutting processing in the processing craft aspect key technologies.Keywords High-speed cutting Grinding tool Grinding tool processing Process technology1 Introduction1.1 IntroductionAlong with the advance in technology and the industry swift development, the mold already became in the industrial production to use the extremely widespread main craft to equip now. The mold takes the important craft equipment, in Industry sectors and so on consumable, electric appliance electron, automobile, airplane manufacture holds the pivotal status. The manufactured products components rough machining 75%, the precision work 50% and the plastic parts 90% will complete by the mold. At present the Chinese mold market demand has reached 50,000,000,000 Yuan scales, our country die making market potential is huge. The mold is one kind of special-purpose tool, uses in forming () each metal or the nonmetallic material needs the components the shape product, this kind of special-purpose tool general designation mold. The mold is in the industrial production the most foundation equipment, is realizes the few cuttings and the non-cutting essential tool. The mold has widely used in the industrial production each domain, like the automobile, the motorcycle, the domestic electric appliances, the instrument, the measuring appliance, the electron and so on, in them 60%~80% components need the mold to carry on the manufacture; The highly effective production in enormous quantities's, bolt, nut and gasket standard letters and so on plastic also need the mold to produce; The engineering plastics, the powder metallurgy, the rubber, the alloy compression casting, the glass formation and so on need to use the mold to take shape.1.2 High-speed cutting process technologyAs the name suggests, the high-speed cutting, first is the high speed, namely must have the high spindle speed, for instance 12000r/min, 18000r/min, 30000r/min, 40000r/min, even also had a higher rotational speed still in the experiment; On the other hand, should also have the bigger to feed quantity, like 30000mm/min, 40000mm/min, even 60000mm/min; Has is after again the rapid traverse, trades fast the knife, the main axle trade the knife, from the static state arrives its needs rotational speed rise time and so on, only then achieved the above standards to be able to call it high speed.Next is must aim at the different processing object, the different degree of hardness, thedifferent material quality, the different shape to choose the corresponding reasonable parameter, but cannot pursue constantly to be high speed and be high speed, regarding the die space processing, the shape is specially complex, but the cutting tool diameter is also small time, because cutting tool's path is not the simple translation, but is the curve, even has right angle corner time, technological parameter rational especially important, if because wants to maintain the identical feed rate carries on the orthogonal cutting, will not be able to do well will cause as a result of the engine bed moving part's huge inertia the cutting tool will make when the bend angle movement to break suddenly, but the variable motion can, becauseMovements and so on acceleration and deceleration create the thickness of cutting the instantaneous change, but causes the cutter change to enable the work piece surface to have cuts, from this causes the processing drop in quality, therefore, in view of the different processing object, needs the programmers to choose the reasonable cutting tool path, optimized cutting parameter; On the other hand, according to needs to choose the suitable cutting velocity, only then can display the high-speed cutting truly like the strong point.The high-speed cutting (HSC) is an advanced technique of manufacture which for the past ten years rapidly rises. Because the high-speed cutting technology has the cutting efficiency to be high, the processing quality high, can process the hard steel stock and the good efficiency directly, causes profession and so on aviation, mold, automobile, light industry and information production efficiencies and the manufacture quality obviously enhances, and causes the processing craft and the equipment corresponding renewal. Therefore is similar to the numerical control technology is the same, the high-speed cutting and the high speed processing have become in the 21st century a machine-building industry influence profound technological revolution. At present, adapts the HSC request high speed machining center and other high speed numerically-controlled machine tool has assumed the popularization tendency in the developed country, our country recently is also speeding up the development.The high-speed cutting processing is faces for the 21st century a high technology and new technology, it is one kind is different with the traditional processing processing way. Compares with it, the high-speed cutting processing main axle rotational speed high, cuts high for the speed, the cutting quantity is small, but in the unit time material excises the quantity to increase 3 ~ 6 times actually. It take the high efficiency, the high accuracy and the high surface quality as the basic characteristic, in profession and so on in automobile industry, aerospace, mold manufacture and instrument measuring appliance has obtained the increasingly widespread application, and has obtained the significant technology economic efficiency, is the contemporary advanced manufacture technology important constituent.When with traditional way processing mold, often uses the electric spark machining, but the electrode design and makes itself is the technological process which time-consuming takes the trouble. But after uses the high-speed cutting processing, because the narrow and small region processing realization and the high grade superficial result, let the electrode the utilization ratio reduce greatly. Moreover, makes the electrode with the high speed mill also to be possible to make the production efficiency to enhance to a new scale.The major part mold may use the high-speed cutting technology to process, like the forging die, the compression casting mold, cast with the blow molding mold and so on. Hammers the cavity body shallowly, the cutting tool life is long; Compression casting mold size moderate, the productivity is high; Casts with the blow molding mold general size small, quite is economical.2 the high-speed cutting processing mold relative traditionprocesses the mold the superiority2.1 Enhances the productivityIn the high-speed cutting the main axle rotational speed and enters for the speed enhancement, may enhance material removing rate. At the same time, theThe high-speed cutting processing permission use big to feed rate, enhances 5~10 times compared to the convention machining, the unit interval/unit time material excision rate may enhance 3~6 times, the process period may reduce greatly. This may use in processing needs to excise the metal massively the components, specially has the very vital significance regarding the aviation industry.2.2 Improvement processing precishon and surface qualhtyThe high rpeed engine bed must have high performance and so on rigidity and high accuracy, at the same time because cutting force low, the work piece thermal deformation reduces, the cutting tool distorts slightly, the high-speed cutting processing precision Is very high. Depth of cut small, but enters for the speed quickly, the processing surface roughness is very small, cuts when the aluminum alloy may reach Ra0.4 ~ 0.6, when cutting steel stock may reach Ra0.2 ~ 0.4.Compares with the conventional cutting, when high-speed cutting processing the cutting force may reduce 30% at least, this may reduce the processing regarding the processing rigidity bad components to distort, causes some thin wall class fine work piece the machining into possible. Because revolves high speed time the cutting tool cuts the excitation frequency is far away from the craft system's forced oscillation, has guaranteed the good processing condition. Because the cutting force is too small, cut the hot influence to be small, causes the cutting tool, the work piece distortion to be small, maintained the size accuracy, moreover also caused the friction between the cutting tool work piece changes is small, the cutting destruction level thinned, the residual stress was small, has realized the high accuracy, the low roughness processing.2.3 The reduced cutting produces quantity of heatBecause the high-speed cutting processing is the shallow cutting, simultaneously the feed rate is very quick, the knife edge and the work piece contact length and the contact duration were short,reduced the knife edge and the work piece heat conduction, has avoided when the traditional processing met everywhere in the cutting tool and the work piece to have the big calorimetry shortcoming, guaranteed that the cutting tool worked under the temperature not high condition, lengthened cutting tool's service life. As shown in Figure 1, A is time the high-speed cutting processing heat conduction process, B is the traditional processing heat conduction process.Fig.1 high speed processing and traditional processing heat conductionThe high-speed cutting processing process is extremely rapid, 95% above cutting quantity of heat are extremely few, components not because the temperature rise will cause the warp or the inflation distortion. The high-speed cutting is suitable specially for the processing easy thermal deformation components. Is low regarding the processing melting point the metal which, easy to oxidize (for example magnesium), the high-speed cutting has certain significance.2.4 advantageoued in the processing thin wall componentsTime high-speed cutting's cutting force is small, has the high stability, but the high quality processes the thin wall components. Uses as shown in Figure 2 the lamination down milling the processing method, but high-speed cutting wall thickness 0.2mm, wall high 20mm thin wall components. This time, the knife edge and the work piece contact duration was short, has avoided the sidewall distortion.Figure.2 high-speed cutting thin wall components2.5 change the part substitutes certain crafts, like electric spark machining, abrasive machining and so onHigh strength and the high degree of hardness's processing is also a high-speed cutting major characteristic, at present, the high-speed cutting has been possible the work hardness to reach HRC60 the components, therefore, the high-speed cutting can process after the heat treatment hardens the work piece. In the tradition processes in mold's craft, before the precision work, hardens the work piece after the heat treatment to carry on the electric spark machining, may omit in the die making craft with the high-speed cutting processing substitution tradition cutting's processing method the electric spark machining, simplified the processing craft and the cost of investment.the mold's size, the shape and the surface roughness are very important, if after processing the mold cannot meet the requirements the quality precision, needs the massive handworks to rub repairs the work, the handwork rubs repairs can obtain the good surface quality, but it will affect mold's size and the shape precision. Therefore must omit as far as possible in the mold processing rubs manually repairs, improves the mold quality, reduces the production cost and the manufacturing cycle.Figure 3 is the traditional mold processing process: The semifinished materials -> rough machining -> semi-finishing -> heat treatment hardens -> the electric spark machining -> precision work -> to rub manually repairs. Figure 4 is the high speed mold processing process: Hardened semifinished materials -> rough machining -> semi-finishing -> precision work.Figure.3 the traditional mold processes processFigure 4 the high speed mold processes processin Figure 4, in the high speed mold machining process reduced two technological processes,probably reduces the process period 30%~50%. In the traditional processing craft's electric spark machining forms the hardened level easily in the melting processing surface layer, degree of hardness may reach 1000Hv, brings the difficulty for the following machining and the abrasive machining. The electric spark machining also easy to cause the surface layer fatigue cracking and cutting tool's breakage.2.6 Economic efficiency remarkable enhancementSynthesis above all sorts of merits, namely: The comprehensive efficiency will improve, the quality enhances, the working procedure simplifies, the engine bed investment and the cutting tool investment as well as the maintenance cost increase and so on, will use the high-speed cutting craft to cause the synthesis economic efficiency remarkable enhancement.3 high-speed cutting processing craft essential technologyThe high speed engine bed and the high speed cutter are the realization high-speed cutting premise and the basic condition, has the strict request in the high-speed cutting processing to the high speed engine bed performance and the cutting tool material choice.In order to realize the high-speed cutting processing, uses the high flexible high speed numerical control engine bed, the processing center generally, also some use special-purpose high speed mills, drilling machine. At the same time the engine bed has the high speed main axle to be systematic and the high rapid advance or progress gives the system, the high main axle rigidity characteristic, the high accuracy localization function and the high accuracy insert makes up the function, specially the circular arc high accuracy inserts makes up the function.The high-speed cutting cutting tool and ordinary processes the cutting tool the material to have is very greatly different. The main use cutting tool material has the hard alloy, the crystal combination diamond (PCD), the crystal combination cube boron nitride (PCBN) and the ceramics and so on.The high-speed cutting craft technology also is carries on the high-speed cutting processing the key. The cutting method chooses is improper, can make the cutting tool to intensify the attrition, cannot achieve the high speed processing completely the goal. The practice proved, if only then the high speed engine bed and the cutting tool but do not have the good craft technology to make the instruction, the expensive high-speed cutting processing equipment cannot fully play the role. The high-speed cutting processing craft essential technology mainly includes the cutting method and the cutting parameter choice optimization.a. Cutting way choiseIn the high-speed cutting processing, should select the down milling processing as far as possible, because in down milling time, the cutting tool just cut into the thickness of chip which the work piece produces to a big way, afterward reduces gradually. When up milling, the cutting tool just cut into the thickness of chip which the work piece produces to be smallest, afterward the accumulation, increased the cutting tool and the work piece friction like this gradually, has the big calorimetry on the knife edge, therefore produces in the up milling quantity of heat when down milling are more than, the radial force also greatly increases. Meanwhile in the down milling, the knife edge main compression stress, but when the up milling the knife edge tension stress, the stressful condition is bad, reduced cutting tool's service life, the down milling and the up milling the cutting tool cuts into the work piece the process, as shown in Figure 5.Figure.5 the cutting tool cuts into the work piece the process hintb. Maintains constant metal removing rateThe high-speed cutting processing is shallowly suitable for shallowly to cut the depth, the depth of cut should not surpass 0.2/ 0.2mm (ae/Ap), this is for avoids the cutting tool the position deviation, guarantees processes the mold the geometry precision. Maintains constant metal removing rate, guaranteed adds on the work piece the cutting load is constant, by obtains following several good processing effect: (1) may maintain constant cutting load; (2) may maintain the scrap size constant; (3) has the good hot shift; (4) the cutting tool and the work piece maintain at the cold condition; (5) does not need skilled to operate for the quantity and the main axle rotational speed;(6) may lengthen the cutting tool the life; (7) can guarantee the good processing quality and so on.c.choice of the Feeds wayRegarding has opens the mouth die space the region, feeds as far as possible from material outside, by real-time analysis material cutting condition. But regarding does not have the die space enclosed area, selects the screw feed method, cuts into the local region.d. As far as possible reduced cutting tool's commutation rapidlyReduces the cutting tool as far as possible the rapidly commutation, because the zigzag pattern mainly applies in the traditional processing, mainly chooses the return route or the sole way cutting in the high-speed cutting processing. This is because in commutation time the NC engine bed must stop (urgently changing down) immediately then the again execution next step of operation. As a result of engine bed acceleration limitation, but is easy to create the time the waste, stops anxiously or whips then can destroy the surface roughness, also has the possibility because has cut but produces the broach or in the outside undercut. Chooses the sole way cutting pattern to carry on the down milling, does not sever the cutting process and the cutting tool way as far as possible, reduces the cutting tool to cut into as far as possible cuts the number of times, by obtains the relatively stable cutting process.For example, in the cutting mold corner processing, the traditional processing method is usesthe translation (G1), when the cutting tool cuts to the fillet place, the velocity of movement reduces speed, at the same time when enters for the commutation the cutting tool movement is not continuously, can have the massive friction and the quantity of heat in the intermittent process, if processes the aluminum alloy or other light metal alloys, produces the quantity of heat will damage the work piece surface quality.If uses the high-speed cutting processing the method, the use is smaller than the cutting mold corner radius cutting tool, the use high speed engine bed high accuracy circular arc inserts makes up the function (G2, G3) processes the mold corner, the high speed engine bed circular arc inserts makes up the movement is the continuous process, cannot have the cutting tool intermittent motion, thus reduced the cutting tool and the mold contact length and the time, avoids having the massive heat.e In Z direction cutting continual planeThe traditional processing die space's method uses the profile milling, this processing way increased the cutting tool to cut into, to cut the work piece the number of times, has affected the work piece surface quality, has limited the engine bed and the cutting tool formidable function display. In the high-speed cutting processing, often uses the Z direction cutting continual plane. Uses step pitch which is smaller than the convention, thus reduces each tooth cutting elimination quantity, the improvement processing surface's quality, reduced the process period.4 High-speed cutting process technology in die makingapplicationThe high-speed cutting process technology has a series of characteristics and the production benefit aspect's great potential, already becomes country competition research and so on Germany, US and Japan important areas of technology. Now, US, Germany, Japan, France, Switzerland, Italy produce the different specification's each kind of commercialization high speed engine bed already entered the market, applies in the airplane, the automobile and the die making.Along with the high-speed cutting process technology introduction mold industry, has had the very tremendous influence to the traditional mold processing craft, changed the mold processing technical process. Because the mold profile is the very complex free surface generally, and degree of hardness is very high, uses conventional the machining method to satisfy the precision and the shape request with difficulty. The conventional processing method is after the annealing carries on the milling processing, then carries on the heat treatment, the grinding or the electric spark machining, finally the manual polish, polishing, cause the processing cycle to be very long like this. Specially the manual process period, must account for the entire processing cycle to be very big a part. HSC may achieve the accuracy requirement which the mold processes, reduced has even cancelled the manual processing, because and new cutting tool material (for example PCD, PCBN, cermet and so on) the appearance, HSC may the work hardness achieve HRC60, even degree of hardness higher work piece material, after might process hard mold, substitution electric spark machining and abrasive machining.The high speed milling processing has the highly effective high accuracy in the die making as well as may process the high hard material the merit, already obtained the widespread application in the industrially advanced country. The high-speed cutting process technology introduction mold industry, mainly applies in the following several aspects:1) hard mold die space direct processing. After using the high-speed cutting to be possible to process the hard material the characteristic direct processing hard mold die space, improved the quality which and the efficiency the mold processes, may substitute for the electric spark machining.(2) EDM (electric spark) electrode processing. Applied the high-speed cutting technology processing electrode to raise the electric spark machining efficiency to play the very major role. The high-speed cutting electrode improved electrode's surface quality and the precision, reduced the following working process.3) fast sample workpiece manufacture. Uses the high-speed cutting processing efficiencyhigh characteristic, may use in processing the plastic and the aluminum alloy model. After the CAD design produces the 3D full-scale mockup fast, is higher than the fast prototype manufacture efficiency, the quality is good.(4) mold's fast repair. The mold often needs to repair in the use process, lengthens the service life, in the past was mainly completes depending on the electrical finishing, now uses the high speed processing to be possible to complete this work quickly, moreover might use the original NC procedure, did not need to establish.5 ConclusionThe high-speed cutting processing uses the high cutting velocity and the feed rate, the small radial direction and the axial depth of cut, the cutting force is small, the processing surface roughness is very small, cutting tool life enhancement; With the high-speed cutting processing way substitution tradition processing way processing mold, might omit the electric spark machining and rub manually repairs, raised the productivity which the mold processed, reduced the production cost, reduced the processing cycle; When research high-speed cutting processing, must unify closely with the high-speed cutting processing technology, realizes the high efficiency, the high accuracy truly and the redundant reliable goal.The high-speed cutting process technology is the advanced technique of manufacture, has the broad application prospect. Replaces EDM with the high-speed cutting processing (or majority of replaces) speeds up the mold development speed, realizes the craft update major step. The promoted application high-speed cutting process technology applies in the mold manufacturing industry, not only may enhance the machine-finishing large scale the efficiency, the quality, reduces the cost, moreover may lead a series of high technology and new technology industry the development. Therefore, current strengthens the high-speed cutting technology the basic research, establishes the high-speed cutting database, the high-speed cutting safety work standard, enhances the engine bed and tool profession development innovation ability, speeds up the high-speed cutting cutting tool system, the high-speed cutting engine bed system's research development and the industrial production, already was the urgent matter.References[1] A.C. Low, J.W. Kyle, Grinding tool technology recent development, The Mechanical Engineers Association, London, 1986. High-speed cutting and grinding tool manufacture[2] K.L. Johnson, High-speed cutting and grinding tool manufacture, Cambridge University Press, Cambridge, 1985.[3] W.DMay, E.L. Morris, D. Atack, new using of Cutting technology, Applied Physics 30 (1959) 1713–1724.[4] S.C. Hunter, Grinding tool manufacture, Applied Mechanics 28 (1961) 611–617.[5] G. Lodewijks, Dynamics of Belt Systems, Thesis, Delft University of Technology, Delft, 1995.[6] A.N. Gent, High-speed cutting outline, Carl Hanser Verslag, 2001.中文翻译高速切削加工在模具制造中的新应用摘要当前模具应用广泛,与之相关的模具制造技术也有了很大的发展。
先进制造技术(英文版第三版)唐一平,第一章翻译
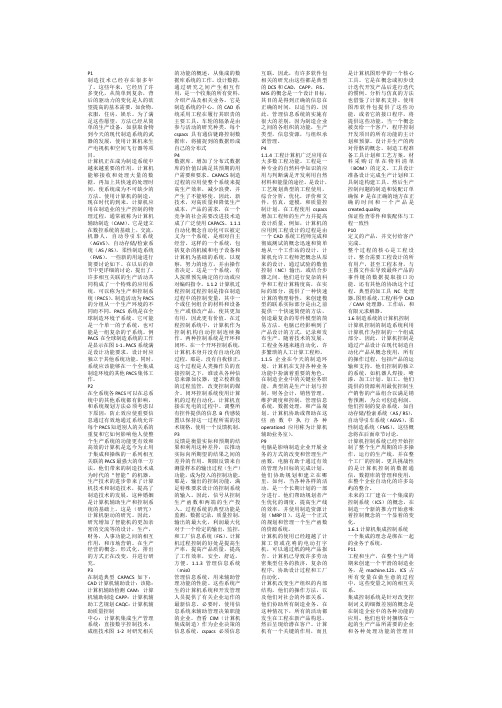
P1制造技术已经存在很多年了。
这些年来,它经历了许多变化,从简单到复杂,背后的驱动力的变化是人的欲望提高的基本需要,如食物,衣服,住房,娱乐。
为了满足这些愿望,方法已经从简单的生产设备,如获取食物到今天的现代制造系统的武器的发展,使用计算机来生产电视机和空间飞行器等项目。
计算机正在成为制造系统中越来越重要的作用。
计算机能够接收和处理大量的数据,再加上其快速的处理时间,使系统成为不可缺少的方法。
使用计算机的制造,现在时代的到来。
计算机应用在制造业的生产控制的物理过程,通常被称为计算机辅助制造(CAM)。
它是建立在数控系统的基础上,交流,机器人,自动导引车系统(AGVS),自动存储/检索系统(AS / RS),柔性制造系统(FMS)。
一些新的用途进行简要讨论如下。
在以后的章节中更详细的讨论,提出了。
许多相互关联的生产活动共同构成了一个特殊的应用系统,可以称为生产和控制系统(PACS)。
制造活动为PACS 的分组从一个生产环境的不同而不同。
PACS系统是在全球制造环境子系统。
它可能是一个单一的子系统,也可能是一组复杂的子系统。
例PACS在全球制造系统的工作是显示在图1-1。
PACS系统满足设计功能要求,设计时应独立于其他系统功能。
同时,系统应该能够在一个全集成制造环境的其他PACS集体工作。
P2在全系统各PACS可以在总系统中的其他系统都有影响,和系统规划方法必须考虑以下原因:防止效应使重要信息通过有效地通过系统允许每个PACS知道别人的关系的重复和它如何影响他人使整个生产系统的功能更有效和高效的计算机是迄今为止用于集成和操纵的一系列相互关联的PACS最强大的单一方法。
他们带来的制造技术成为时代的“智能”的机器。
生产技术的进步带来了计算机技术和制造技术,提高了制造技术的发展。
这种婚姻是计算机辅助生产和控制系统的基础上,这是(研究)计算机驱动的研究。
因此,研究增加了智能机的更加亲密的交流等的设计,生产,财务,人事功能之间的相互作用,和市场营销。
先进制造技术英文版论文
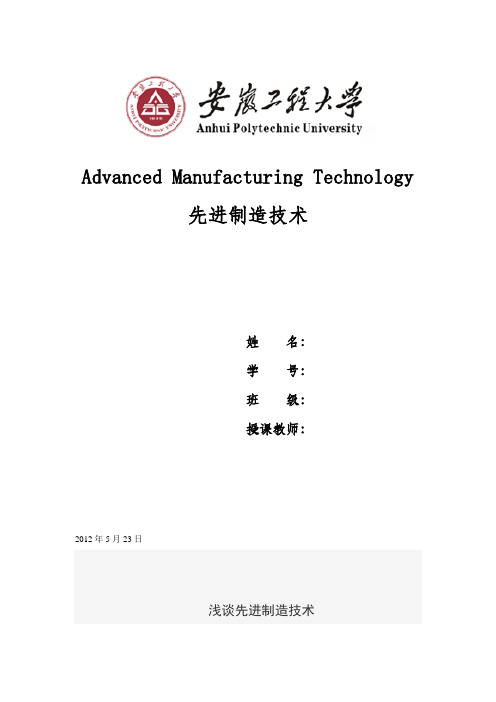
Advanced Manufacturing Technology先进制造技术姓名:学号:班级:授课教师:2012年5月23日浅谈先进制造技术On the Advanced Manufacturing Technology学号3092101414 班级;机械2094 姓名;许宏摘要;在传统制造的基础上,不断吸收机械、电子、信息、材料、能源和现代管理技术等方面的成果,将其综合应用于产品设计、制造、检测、管理、销售、使用、服务的制造全过程,以实现优质、高效、低耗、清洁、灵活生产关键词;高效精密、超精密加工技术,精密成型制造技术现代特种加工技术,敏捷制造、并行工程、柔性制造英文摘要;on the basis of the traditional manufacturing, constantly absorbing theoutcome of the machinery, electronics, information, materials, energy,and modern management techniques and other aspects of itscomprehensive applied to product design, manufacturing, testing,management , sales, use, service manufacturing process, in order toachieve high-quality, high efficiency, low consumption, clean, flexibleproduction, improve the general term of the dynamic and marketadaptability and competitiveness of manufacturing technologykey words;High precision, super precision machining technology, precision manufacturing technology,Modern special processing technology,agile manufacturing, concurrent engineering, flexiblemanufacturingAdvanced manufacturing technology AMT (Advanced Manufacturing Tecnology) on the basis of the traditional manufacturing, constantly absorbing the outcome of the machinery, electronics, information, materials, energy, and modern management techniques and other aspects of its comprehensive applied to product design, manufacturing, testing, management , sales, use, service manufacturing process, in order to achieve high-quality, high efficiency, low consumption, clean, flexible production, improve the general term of the dynamic and market adaptability and competitiveness of manufacturing technology, but also to achieve the desired technical and economic benefits manufacturing technology, the general term.The current financial crisis and perhaps the birth of a new state-of-the-art manufacturing manufacturing technology, particularly in the production management techniques. Advanced manufacturing technology is not just referring to the process of the process, but across multiple disciplines, including from product design, manufacturing, product sales, consumer services throughout the product lifecycle process for all relevant technologies, involving multiple areas of design, technology, process automation, management and special processing, and the gradual integration and integration. Can be basically grouped into the following four areas:An advanced engineering design techniques, advanced manufacturing technology Three, manufacturing automation technology, advanced production management, manufacturing philosophy and mode of productionV. Development.First,An advanced engineering design techniques Advanced engineering design techniques, including a large number of modern design theory and methods. Including CAD, CAE, CAPP, the CAT, the PDM, the modular design, DFX, optimize design, three design and robust design, innovative design, reverse engineering, collaborative product commerce, virtual reality technology, virtual prototyping, concurrent engineering.(1) Product (market, product and manufacturing process equipment (fixtures, tools, and the amount of check, etc.)) modern design.CAD (modeling, engineering analysis calculation, automatic drawing and digital product information, etc.), a comprehensive application of advanced design methods and concepts. Such as virtual design, optimize design, modular design, finite element analysis, dynamic design, ergonomic design, aesthetic design, green design, and so on;(2) advanced process planning and production technology to prepare the means.Information integration environment, using computer-aided process planning, CAPP, CNC machine tools, industrial robots, coordinate measuring machines and other various computer equipment of automatic control equipment, computer-aided work program design CAM.Second, advanced manufacturing technology(1) high-precision, ultra-precision processing technology, including precision,ultra-precision grinding, turning, fine processing technology, nano-processing technology. Ultra-high speed cutting. Precision processing generally refers to the processing accuracy in the 10 ~ 0.1μm (equivalent to the the IT5 level of accuracy and precision) IT5 level, the surface roughness Ra value less than 0.1μm processing methods, such as King Kong car, diamond boring, grinding, honing, super-fine research, abrasive belt grinding, mirror grinding and cold processing. For the processing of the key parts in the manufacturing of precision machine tools, precision measuring instruments, such as precision screw, precision gears, precision worm gear, precision rail, Precision Bearing, etc., in the current manufacturing industry occupies a very important position.Ultra-precision machining refers to the dimensional tolerances of the parts to bepr ocessed for the 0.1 ~ 0.01μm magnitude, surface roughness Ra value of the the0.001μm magnitude of processing methods.In addition, precision machining and special processing are generally computer-controlled automated processing.(2) precision molding manufacturing technology, including efficient, precise, clean casting, forging, stamping, welding and heat treatment and surface treatment technology.(3) special processing technology, including high-energy beam (laser beam and electron beam, ion beam) machining, electrochemical machining and EDM (molding and wirecutting) machining, ultrasonic machining, and processing of high-pressure water. EDM (Electrical discharge machining (EDM) EDM electric spark machining) refers to the medium, the processing of the workpiece by electric pulse discharge between the tool electrode and workpiece electrode erosion. Restrictions on the processing of material strength and hardness without any conductive material processing. Can be divided into EDM machining (EDM) and EDM wire cutting (EDM wire cutting electrical discharge wire - cutting - EDW)Two categories. General CNC control.(4) rapid prototyping manufacturing (RPM). Rapid prototyping technology is under computer control, based on the discrete accumulation principle in different ways accumulation of material to complete the final parts of the molding and manufacturing technology. Forming the angle of view, the parts can be regarded as a "point" or "face" superposition. Discrete model from the CAD electronic point of the surface of the geometric information, and then combined with the molding process parameter information, control materials regularly and accurately from point to plane, from the surface to the body to the accumulation of parts.(5) the development trend of advanced manufacturing technology1) the use of simulation technology to optimize the process design;2) forming precision to the development of nearly no margin direction;3) forming a quality development to the nearly-free direction of "defects";4) machined to ultra-sophisticated, ultra-high-speed direction of development;5) the new energy and composite processing, and solve the challenges of new materials processing and surface modification;6) The use of automation technology, optimization of process control;7) the use of cleaner energy and raw materials to achieve cleaner production;8) processing and design of the boundaries between the gradual talk of, and the trend of integration and integration;9) the technology and IT management technologies closely integrated, advanced manufacturing mode to obtain the continuous development.Third, manufacturing automation technology Sentence: computer-controlled automation technology(1) CNC technology and CNC machine tools; CNC machining technology in order to achieve the machine control automation requirements development. It refers to the numbers, letters and symbols of the code of the processing requirements, part dimensions and parameters, process steps, and by controlling the media, the input to the control device, after the computer for processing and calculation, and make all kinds of control signals and data, various parts of the machine automatically coordinated movement, automatic processing technology. Machine tools, CNC machining technology, known as the CNC machine tools. CNC machining of the main features are: high precision machined parts; high production efficiency; particularly suitable for machining complex shape of the contour surface; conducive to the realization of computer-aided manufacturing (excluding the technical level of the programmer) is relatively low; theoperator; initial investment, high processing costs. In addition, the CNC machine tools to mechanical and electrical integration of the technology-intensive products, the complexity and comprehensive CNC machining technology to increase the difficulty of the repair work, maintenance personnel and maintenance of equipment need to be equipped withhigh-quality.(2) industrial robots (for logistics and processing) and logistics equipment; industrial robot is a programmable intelligent automation equipment, highly automated system for the application of computer control of the alternative work. Recently, the robot used by the United Nations Organization for Standardization is defined as: "a repeated programming multi-function, used to move materials, parts, tools, operating machines". Unattended, the industrial robot can automatically according to the different trajectories of different sports to complete the action and a variety of tasks. The main difference of the robot and the robot is: robot autonomy, can not be reprogrammed, only the anchor the same simple repetitive movements; robot is controlled by a computer, can be reprogrammed to complete the arbitrary orientation of the complex movement.(3) flexible manufacturing system (FMC, FMS, FML): including processing equipment (CNC machine tools), test equipment, materials transport (industrial robots, automatic exchange of the tray (APC), automatic conveyor trolley (RGV, AGV), etc.) and storage devices (three-dimensional warehouse, etc.); number of flexible manufacturing system (FMS) is a new automated production equipment in the modern machinery manufacturing, which is developed to fill accounted for 70% of the machinery manufacturing small and medium volume production automation. It mainly includes a number of CNC machine tools and machining centers (or other directly participate in product parts production automation equipment), (including workpiece and tool) an automated material handling system is connected to the integrated management of distributed multi-level computer systems and control to adapt to the flexible processing of high-efficiency parts (or parts production). The so-called flexible part processing refers to the parts of both alternately processing system. The scope of application of the flexible manufacturing system is very broad, it is mainly to solve a single small-batch production automation and automated processing of the large number of multi-species. Its high flexibility, high quality, efficient and unified, with strong vitality in today's(4) Computer Integrated Manufacturing (CIM), and factory automation (FA). Computer Integrated Manufacturing System (CIMS) is a computer management systems, computer-aided design and manufacturing CAD / CAM and Flexible Manufacturing System FMS (there may be other production units) to form. CIMS is a perfect integration of the various subsystems of the production process, namely, engineering design, manufacturing, market analysis and other support functions reasonably organically through the computer network assembled a whole, in order to achieve the production of flexible, optimized automation and integrated, high efficiency, high-quality, low-cost and flexible production purposes.Fourth, advanced production and management technologies, manufacturing philosophy and modeof productionIncluding advanced manufacturing mode of production, integrated management techniques and organization of production methods.Computer-aided production managemomputer-controlled automation technologyent, research and application of advanced production management system and technology. Group technology, total quality management, lean production and JIT, agile manufacturing, concurrent engineering, flexible manufacturing, computer integrated manufacturing, virtual manufacturing, intelligent manufacturing, network manufacturing, green manufacturing, biotechnology manufacturing, reconfigurable manufacturing, MRP MRPII, ERP, SCM, and the CRM, Computer Aided Logistics Support (Computer Aided Logistic Support, CALS), e-commerce, knowledge management.Fifth, the development ofThe current development trend of advanced manufacturing technology to the following aspects:1, IT plays an increasingly important role in the development of advanced manufacturing technology2, the design technology modernizationThe product design is the soul of the manufacturing sector. The major trends of the modern design technology is:(1) computerized design toolsComputer calculation, drawing on the basis of the current highlights in the development of numerical simulation or virtual reality technology in design and modern modeling theory, and to the development of intelligent design direction.(2) new design ideas and methods emerging(3) to the full life cycle design and development(4) the design process by simply taking into account technical factors to consider technical, economic and social factorsThe design is not simply the pursuit of advanced and high and low for a performance indicator, but rather to consider the impact of the market, price, safety, aesthetics, resources, environment and other aspects.3, forming and improving the manufacturing technology to the development of precise, accurate, and less energy consumption, pollution-free directionForming manufacturing technology is the casting, plastic processing, connectivity, and powder metallurgy unit general term.4, processing and manufacturing technology toward the ultra-sophisticated, ultra-high speed and the development of a new generation of manufacturing equipment, the direction of5, process skills development for the engineering sciences, process simulation technology have developed rapidlyAn important development trends of advanced manufacturing technology, process design experience to judge to the quantitative analysis, and process skills development for the engineering sciences.Professional, interdisciplinary boundaries gradually fade and disappear7, green manufacturing will become an important feature of the 21st century manufacturingIncreasingly stringent environmental and resource constraints, green manufacturing is becoming increasingly important, it is an important feature of the manufacturing industry in the 21st century, accordingly, green manufacturing technology will also be rapid development. Mainly reflected in:(1) green product design technology, product life cycle to meet the environmental, human health, low energy consumption, resource utilization requirements.(2) green manufacturing technology throughout the manufacturing process, making the minimum negative impact on the environment of the minimum, waste and hazardous substances emissions, resource use efficiency maximum. Green manufacturing technology mainly includes three aspects of the green resources, green manufacturing processes and green products.(3) The product recovery and recycling of manufacturing cars and other products, for example, demolition and recycling, as well as eco-factory cycle manufacturing technology. It mainly includes the factory of production systems - committed to product design and material handling, processing and assembly stage, the recovery system plant - the end of the life cycle of products (materials used), material handling cycle.8, virtual reality technology to get more and more applications in manufacturingVirtual reality technology (Virtual Reality Technology) including the two parts of the virtual manufacturing and virtual enterprises.9, information technology, management techniques and technology closely integrated, advanced manufacturing mode to obtain the continuous development of manufacturing industry in experienced a few varieties of large quantities of small quantities - less variety - the transition of the more varieties of small batch production mode, 70 era, the 1980s began to use the computer integrated manufacturing system (CIMS) manufacture of flexible production mode, and gradually develop in the direction of Intelligent Manufacturing Technology (IMT) and the Intelligent Manufacturing Systems (IMS). Lean Production (LP), Agile Manufacturing (AM) and other advanced manufacturing mode appeared in succession, and expected the early 21st century, advanced manufacturing mode is bound to continue development.核心内容选取Third, manufacturing automation technology Sentence: computer-controlled automation technology(1) CNC technology and CNC machine tools; CNC machining technology in order to achieve the machine control automation requirements development. It refers to the numbers, letters and symbols of the code of the processing requirements, part dimensions and parameters, process steps, and by controlling the media, the input to the control device, after the computer for processing and calculation, and make all kinds of control signals and data, various parts of the machine automatically coordinated movement, automatic processing technology. Machine tools, CNC machining technology, known asthe CNC machine tools. CNC machining of the main features are: high precision machined parts; high production efficiency; particularly suitable for machining complex shape of the contour surface; conducive to the realization of computer-aided manufacturing (excluding the technical level of the programmer) is relatively low; the operator; initial investment, high processing costs. In addition, the CNC machine tools to mechanical and electrical integration of the technology-intensive products, the complexity and comprehensive CNC machining technology to increase the difficulty of the repair work, maintenance personnel and maintenance of equipment need to be equipped with high-quality.(2) industrial robots (for logistics and processing) and logistics equipment; industrial robot is a programmable intelligent automation equipment, highly automated system for the application of computer control of the alternative work. Recently, the robot used by the United Nations Organization for Standardization is defined as: "a repeated programming multi-function, used to move materials, parts, tools, operating machines". Unattended, the industrial robot can automatically according to the different trajectories of different sports to complete the action and a variety of tasks. The main difference of the robot and the robot is: robot autonomy, can not be reprogrammed, only the anchor the same simple repetitive movements; robot is controlled by a computer, can be reprogrammed to complete the arbitrary orientation of the complex movement.(3) flexible manufacturing system (FMC, FMS, FML): including processing equipment (CNC machine tools), test equipment, materials transport (industrial robots, automatic exchange of the tray (APC), automatic conveyor trolley (RGV, AGV), etc.) and storage devices (three-dimensional warehouse, etc.); number of flexible manufacturing system (FMS) is a new automated production equipment in the modern machinery manufacturing, which is developed to fill accounted for 70% of the machinery manufacturing small and medium volume production automation. It mainly includes a number of CNC machine tools and machining centers (or other directly participate in product parts production automation equipment), (including workpiece and tool) an automated material handling system is connected to the integrated management of distributed multi-level computer systems and control to adapt to the flexible processing of high-efficiency parts (or parts production). The so-called flexible part processing refers to the parts of both alternately processing system. The scope of application of the flexible manufacturing system is very broad, it is mainly to solve a single small-batch production automation and automated processing of the large number of multi-species. Its high flexibility, high quality, efficient and unified, with strong vitality in today's(4) Computer Integrated Manufacturing (CIM), and factory automation (FA). Computer Integrated Manufacturing System (CIMS) is a computer management systems, computer-aided design and manufacturing CAD / CAM and Flexible Manufacturing System FMS (there may be other production units) to form. CIMS is a perfect integration of the various subsystems of the production process, namely, engineering design, manufacturing, market analysis and other support functions reasonably organically through the computer network assembled a whole, in order to achieve the production of flexible, optimized automation and integrated, high efficiency, high-quality, low-cost andflexible production purposes.Main ReferencesEditor in chief of the Advanced Manufacturing Technology: Li Wei Machinery Industry Press, 2005.7The editor of advanced manufacturing systems: Daiqing Hui Machinery Industry Press, 2007.3Advanced manufacturing technology (English) Editor: Tang Yiping Science Press, 2002核心内容译文制造自动化技术(1)数控技术与数控机床;数控加工技术是为了实现机床控制自动化要求而发展的。
先进制造技术的新发展中英文翻译、外文翻译、外文文献翻译

外文原文:The new advanced manufacturing technology developmentAbstract : This paper has presented the problems facing today's manufacturing technology, advanced manufacturing discussed in the forefront of science, and a vision for the future development of advanced manufacturing technology.Keyword:Advanced manufacturing technologies; Frontier science; Applications prospectsModern manufacturing is an important pillar of the national economy and overall national strength and its GDP accounted for a general national GDP 20%~55%. In the composition of a country's business productivity, manufacturing technology around 60% of the general role. Experts believe that the various countries in the world economic competition, mainly manufacturing technology competition. Their competitiveness in the production of the final product market share. With the rapid economic and technological development and customer needs and the changing market environment, this competition is becoming increasingly fierce, and that Governments attach great importance to the advanced manufacturing technology research.1 .Current manufacturing science to solve problemsManufacturing science to solve the current problems focused on the following aspects :(1) Manufacturing systems is a complex systems, and manufacturing systems to meet both agility, rapid response and rapid reorganization of the capacity to learn from the information science, life science and social science interdisciplinary research, and explore new manufacturing system architecture, manufacturing models and manufacturing systems effective operational mechanism. Manufacturing systems optimized organizational structure and good performance is manufacturing systemmodelling, simulation and optimization of the main objectives. Manufacturing system architecture not only to create new enterprises both agility and responsiveness to the needs and the ability to reorganize significance, but also for the soft production equipment manufacturing enterprises bottom reorganization and dynamic capacity to set higher demands. Biological manufacturing outlook increasingly being introduced to the system to meet new demands manufacturing systems.(2) The rapid rise in support of manufacturing, geometric knowledge sharing has become a modern manufacturing constraints, product development and manufacturing technologies of the key issues. For example, in computer-aided design and manufacturing (CAD/CAM) integration, coordinates measurements (CMM) and robotics fields, in 3D real space (3-Real Space), there are a lot of geometric algorithm design and analysis, especially the geometric said, geometric calculation and geometric reasoning; In measurement and robot path planning and parts search spaces (such as Localization), the existence of space C- interspace (configuration space Configuration Space) geometric calculation and geometric reasoning; Objects in operation (rescue, paying and assembly, etc.) means paying more description and robot planning, campaign planning and assembly operations planning is needed in the types of space (Screw Space) geometric reasoning. Manufacturing process of physical and geometric mechanics phenomenon of scientific research to create a geometric calculation and geometric reasoning, and other aspects of the research topic, the theory pending further breakthrough, the new one door disciplines -- computer geometric are being increasingly broad and in-depth study.(3) In the modern manufacturing process, information not only manufacturing industries have become dominated the decisive factor, but also the most active ones. Manufacturing information systems to improve throughput of modern manufacturing has become a focus of scientific development. The manufacturing information system organization and structure required to create information access, integration and integration show three-dimensional in nature, measuring the multidimensional nature of the information, and information organizations nature. Information structure models in the manufacturing, manufacturing information consistency constraint, andthe dissemination of data processing and the manufacture of enormous knowledge base management, and other areas, there is a need to further breakthroughs.(4) The calculation of the wisdom of artificial intelligence tools and methods in the manufacture of a wide range of applications for manufacturing smart development. Category based on the calculation of biological evolution algorithms smart tools, including activation issues optimize GPS technology portfolio by growing concern is in the manufacture of the complete portfolio optimization problems combined speed and precision of GPS issues both in size constraints. Manufacturing wisdom manifested in the following aspects : wisdom activation, wisdom design, intelligent processing, robotics, intelligent control, intelligent process planning, smart diagnostic, and other aspects. These innovative products are the key theoretical issues, but also by creating a door for a science skills in the important basic issues. The focus in these issues, we can form the basis of product innovation research system.2. Modern mechanical engineering at the frontiers of scienceCross-integration between the different science will produce new scientific gathering, economic development and social progress of science and technology created new demands and expectations, thus creating a frontier science. Frontier science is settled and unsettled issues between the scientific community. Frontier science, with a clear domain, and dynamic character of the area. Works frontier science from the general basic science is an important characteristic of the actual works, it covers the key emerging science and technology issues. Ultrasonic electrical, ultra-high-speed machines, green design and manufacturing, and other fields, and has done a lot of research work, but innovation is the key question is not clear mechanical science. Large complex mechanical system design and performance optimization of product innovation design, smart structures and systems, intelligent robots and their dynamics, nano Mocaxue, manufacturing process 3D numerical simulations and physical simulation, precision and ultra-fine processing technology key basis, about 10 mega large and sophisticated equipment design and manufacturing base, virtual manufacturing and virtual instruments, nanometer measurement and instrumentation, parallel connection axis machine tools, and although the field ofmicro-electromechanical systems have done a lot of research, but there are still many key science and technology issues to be resolved. Information science, nano science, materials science, life science, management science and manufacturing science of the 21st century will be to change the mainstream science, and the resulting high-tech industry will change the face of the world. Therefore, the above areas of cross-development manufacturing systems and manufacturing informatics, nano manufacturing machinery and nano science, better machinery and better manufacturing science, management science and manufacturing systems will be critical to the 21st century mechanical engineering science is important frontier science.2.1 Manufacturing science and information science cross -- manufacturing informaticsMechanical and electrical products, chemical raw materials in the information. Many modern value added products primarily reflected in the information. Thus the manufacturing process for the acquisition and application of information is very important. Information science and technology is to create an important symbol of globalization and modernization. While the manufacturing technology began to explore product design and manufacturing processes, the nature of the information, on the other hand, to create technology to transform itself to adapt to the new information makes its manufacturing environment. Along with the manufacturing process and manufacturing systems to deepen understanding, researchers are trying to new concepts and approaches to their description and expression to achieve further control and optimization purposes.And manufacturing-related information mainly product information, technical information and information management in this area following major research direction and content :(1) manufacturing information acquisition, processing, storage, transmission and application of knowledge to create information and decision-making transformation.(2) Non-symbols expressing information, manufacturing information enables transmission, manufacturing information management, manufacturing informationintegrity in a state of non-production decision-making, management of virtual manufacturing, based on the network environment of the design and manufacturing, manufacturing process control and manufacturing systems science. These elements are manufactured in science and the scientific basis for the integration of product information, constitute the manufacture of the new branch of science -- to create informatics.2.2 Micro mechanical and manufacturing technology researchMicro-electronic mechanical systems (MEMS) refers to the collection of micro-sensors, micro-devices and the implementation of signal processing and control circuits, interface circuits, communications and power with the integration of micro-electromechanical system integrity. MEMS technology objectives through system miniaturization, to explore a new theory of integration, new functional components and systems. MEMS development will greatly facilitate the pocket of various products, miniaturization, a number of devices and systems to enhance the level of functional density, information density and Internet density, significantly saving, thin section. Not only can it reduce the cost of mechanical and electrical systems, but also to be completed and the size of many large systems impossible task. For example, using sophisticated 5μm diameter micro tweezers walls are made of a red blood cell can; Created to keep the cars 3mm size; In the magnetic field, like butterflies flying size aircraft. MEMS technology has opened up a completely new technology areas and industries, with many traditional sensors incomparable advantages in manufacturing, aerospace, transportation, telecommunications, agriculture, biomedical, environmental monitoring, military, families, and access to almost all areas have very broad application prospects.Micro machinery is machinery and electronic technology in nano-scale technology integration photogenic product. Back in 1959 scientists have raised the idea of micro-mechanical and micro-1962, the first silicon pressure sensors. 1987 California University of California Berkeley developed rotor diameter of the silicon micro-60~120 16ug m electrostatic electric motors, show produced using silicon micro-machining small movable structures and compatible with IC manufacturingmicro system potential. Micro-mechanical technology might like 20th century microelectronics technology, the technology of the world in the 21st century, economic development and national defense building a tremendous impact. Over the past 10 years, the development of micro-mechanical spectacular. Its characteristics are as follows : a considerable number of micro-components (micro structure, the implementation of micro-sensors and micro-machines, etc.) and micro-systems research success reflects the current and potential applications of value; The development of micro-manufacturing technology, particularly semiconductor processing technology have become small micro systems support technology; micro-electromechanical systems research needs of the interdisciplinary research team, micro-electromechanical systems technology in the development of microelectronics technology on the basis of multidisciplinary cross-frontier area of research, involving electronic engineering, mechanical engineering, materials engineering, physics, chemistry and biomedical engineering and other technical and scientific.The current micro-mechanical systems under the conditions of the campaign laws, the physical characteristics and micro components of the role of the mechanics payload acts lack adequate understanding is not yet in a theoretical basis for a micro-system design theory and methodology, and therefore can By experience and test methods research. Micro-mechanical systems, the existence of key scientific research issues of micro-scale system effects, physical properties and biochemical characteristics. Micro-system research are in the eve of a breakthrough, which is the in-depth study of the area.2.3 Material produced / manufactured parts integration of new technologies for processing.Material is a milestone in the progress of mankind, is the manufacturing and high-tech development. Every important to the success of the production and application of new materials, will promote the material and the promotion of national economic strength and military strength. 21, the world will be resource consumption-based economy to a knowledge-based industrial transformation for materials and parts and functions of a high performance, intelligent features; Requestmaterials and components designed to achieve quantitative-based and digitized; Prepare materials and components for the rapid, efficient and achieve both integration and integrated. Digital materials and components designed to be a simulation and optimization of materials and components to achieve high quality production / manufacturing and other integration, integrated manufacturing key. On the one hand, to be completed through computer simulation optimization can reduce the material is produced in the course of manufacture of spare parts and experimental links to the best craft programmes, materials and components to achieve high quality production / manufacturing; On the other hand, according to the requirements of different material properties, such as flexible modules volume, thermal expansion coefficient, magnetic performance, Research materials and components designed form. And the removal of traditional materials-manufacturing technology, and increase the level of information technology, the research group of synthetic materials is a process technology. Forming materials and components manufacture digital theory, technology and methods, such as rapid adoption of emerging technologies material growing principles, a breakthrough in the traditional law and to build law mechanical deformation processing many restrictions, no processing tools or dies, can rapidly create arbitrary complex shape and has a certain function 3D models or entity parts.2.4 machinery manufacturing breakthroughThe 21st century will be the century of life science, mechanical and life sciences depth integration will generate new concept products (such as better intelligence structure), to develop a new process (such as the growth processes shape) and the opening of new industries and to resolve product design, manufacturing processes and systems provide a series of problems new solutions. This is a highly innovative and leading edge area in the challenge.Earth's biological evolution in the long accumulated fine qualities of human manufacturing activities to address the various problems with examples and guidelines. Learning from life phenomena organizations operating complex systems and methods and techniques, manufacturing is the future solution to the current problems facing many an efficient way. Better manufacturing refers to the replicationof biological organs from organizations, since healing, self growth and evolution since the function of the model structure and operation of a manufacturing system and manufacturing process. If the manufacturing process mechanization, automation extends human physical and intelligent extension of the human intellectual, then "create better" may be said to extend its own organizational structure and human evolution process.Gene involved in the manufacture of biological science is the "self-organization" mechanism and its application in manufacturing systems. The so-called "self-organization" refers to a system in its internal mechanism driven by the organizational structure and operation mode learning, thereby enhancing the capacity for environmental adaptation process. Create better "since the organization" bottom-up mechanism for parallel product design and manufacturing processes of automatic generation, the dynamics of production systems and manufacturing systems and products more automatic a theoretical foundation and achieve superior conditions.Create a better manufacturing and life sciences "far edge hybrid" of the 21st century manufacturing will have an enormous impact. Create better research content is twofold :2.4.1 To create better livesResearch lives of the general phenomenon of the law and models, such as artificial life, cellular automatic machines, biological information processing skills, biological wisdom, biological-based organizational structure and mode of operation and the evolution of biological mechanisms and getting better;2.4.2 Oriented manufacturing breakthrough manufacturingResearch organizations better manufacturing systems since the mechanisms and methods, for example : based on full information-sharing breakthrough design principles, multi-discipline modules based on the distributed control and coordination mechanism based on the evolution of an excellent strategy; Study the concept of creating better system and its basis, such as : the formalization described space and better information shine upon relations better system and its evolution of complexity measurement methods.Machinery manufacturing is better and better mechanical science and life science, information science, materials science disciplines such as high integration, the study includes growth formative processes, better design and manufacturing systems, mechanical and biological wisdom better shape manufacturing. Currently doing research mostly forward exploratory work, with distinct characteristics of the basic research, if the research continues to seize opportunities that might arise revolutionary breakthroughs. Future research should concern areas of biological processing technology, better manufacturing system, based on rapid prototype manufacturing engineering technology organizations, as well as biological engineering related key technical basis.3. Modern manufacturing technology trendsSince the beginning of the 1990s, the nations of the world have manufacturing technology research and development as a national priority for the development of key technologies, such as the United States advanced manufacturing technology plan AMTP, Japan wisdom manufacturing technology (IMS) international cooperation schemes, Korea senior national plan of modern technology (G--7), Germany plans to manufacture 2000 and the EC Esprit and BRITE-EURAM plan.With the electronics, information, the constant development of new and high technologies, market demand individuality and diversity, the future of modern manufacturing technology to the overall development trends of the sophisticated, flexible, and networked, virtual and intelligent, green integrated, globalization direction.Current trends in modern manufacturing technology has the following nine areas :(1) Information technology, management techniques and technology closelyintegrated technology, modern production model will be continuousdevelopment.(2) Design techniques and more modern means.(3) Shaped and manufacture of sophisticated technology and manufacturingprocesses to achieve longer.(4) The formation of new special processing methods.(5) Development of a new generation of ultra-sophisticated, ultra-high-speedmanufacturing equipment.(6) Machining skills development for the engineering sciences.(7) Implementation of clean green manufacturing.(8)The widespread application of virtual reality technology to the manufacturingsector.(9) To create people-oriented.译文:先进制造技术的新发展摘要:本文介绍了当今制造技术面临的问题,论述了先进制造的前沿科学,并展望了先进制造技术的发展前景。
先进制造技术论文(中英文翻译)

先进制造技术制造业是现代国民经济和综合国力的重要支柱,其生产总值一般占一个国家国内生产总值的20%~55%。
在一个国家的企业生产力构成中,制造技术的作用一般占60%左右。
专家认为,世界上各个国家经济的竞争,主要是制造技术的竞争。
其竞争能力最终体现在所生产的产品的市场占有率上。
随着经济技术的高速发展以及顾客需求和市场环境的不断变化,这种竞争日趋激烈,因而各国政府都非常重视对先进制造技术的研究。
先进制造技术是集制造技术、电子技术、信息技术、自动化技术、能源技术、材料科学以及现代化管理技术等众多技术的交叉、融合和渗透而发展起来的,设计到制造业中产品的设计、加工装配、检验测试、经营管理、市场营销等产品生命周期全过程,以实现优质、高效、低耗、清洁、灵活的生产,提高对动态市场的适应能力和竞争能力的一项综合技术。
先进制造技术已经成为制造企业在激烈市场竞争中立于不败之地并求得迅速发展的关键因素,成为世界经济发展和满足人类日益增长需求的重要支撑,成为加速高新技术发展和实现国防现代化的助推器。
先进制造技术包括以下几个方面的内容:制造业和先进制造技术、现代设计技术、先进制造工艺技术、制造自动化技术、现代生产管理技术、先进生产制造模式。
当前制造科学要解决的问题主要集中在以下几方面:(1)制造系统是一个复杂的大系统,为满足制造系统敏捷性、快速响应和快速重组的能力,必须借鉴信息科学、生命科学和社会科学等多学科的研究成果,探索制造系统新的体系结构、制造模式和制造系统有效的运行机制。
制造系统优化的组织结构和良好的运行状况是制造系统建模、仿真和优化的主要目标。
制造系统新的体系结构不仅对制造企业的敏捷性和对需求的响应能力及可重组能力有重要意义,而且对制造企业底层生产设备的柔性和可动态重组能力提出了更高的要求。
生物制造观越来越多地被引入制造系统,以满足制造系统新的要求。
(2)为支持快速敏捷制造,几何知识的共享已成为制约现代制造技术中产品开发和制造的关键问题。
先进制造的英文作文怎么写
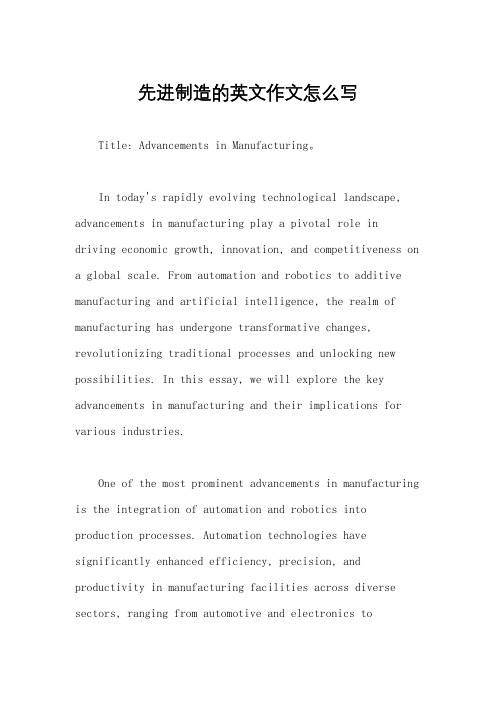
先进制造的英文作文怎么写Title: Advancements in Manufacturing。
In today's rapidly evolving technological landscape, advancements in manufacturing play a pivotal role indriving economic growth, innovation, and competitiveness on a global scale. From automation and robotics to additive manufacturing and artificial intelligence, the realm of manufacturing has undergone transformative changes, revolutionizing traditional processes and unlocking new possibilities. In this essay, we will explore the key advancements in manufacturing and their implications for various industries.One of the most prominent advancements in manufacturing is the integration of automation and robotics into production processes. Automation technologies have significantly enhanced efficiency, precision, and productivity in manufacturing facilities across diverse sectors, ranging from automotive and electronics topharmaceuticals and aerospace. Automated systems perform tasks with unparalleled speed and accuracy, reducing human error and optimizing resource utilization. Moreover, robotics enable the execution of complex operations with flexibility and reliability, enabling manufacturers to adapt swiftly to changing market demands and customize products according to specific requirements.Another groundbreaking development in manufacturing is additive manufacturing, commonly known as 3D printing. This revolutionary technology enables the fabrication ofintricate components and structures layer by layer, using a diverse range of materials including plastics, metals, ceramics, and composites. Additive manufacturing offers unparalleled design freedom, allowing engineers to create geometries that were previously unattainable with conventional manufacturing methods. Moreover, itfacilitates rapid prototyping, iterative design cycles, and on-demand production, thereby reducing time-to-market and enabling cost-effective customization.Furthermore, artificial intelligence (AI) is drivingtransformative changes in manufacturing, empowering machines with cognitive capabilities to perceive, reason, and make decisions autonomously. AI algorithms analyze vast amounts of data generated from sensors, machines, and production processes to optimize performance, predict maintenance needs, and enhance quality control. Machine learning algorithms enable adaptive manufacturing systems that continuously learn from experience and improve over time, enabling manufacturers to achieve unprecedentedlevels of efficiency, flexibility, and reliability.In addition to these technological advancements, sustainability has emerged as a critical imperative in modern manufacturing practices. With growing concerns about environmental degradation and resource depletion, manufacturers are increasingly adopting eco-friendly processes and materials to minimize their ecological footprint. Renewable energy sources, such as solar and wind power, are being integrated into manufacturing facilities to reduce reliance on fossil fuels and mitigate greenhouse gas emissions. Furthermore, circular economy principles are being embraced to promote resource efficiency, wastereduction, and product lifecycle optimization, thereby fostering a more sustainable and resilient manufacturing ecosystem.Moreover, the advent of smart factories, enabled by the Internet of Things (IoT) and cyber-physical systems, is revolutionizing the way manufacturing operations are managed and optimized. Connected sensors and devicescollect real-time data from equipment and processes, enabling proactive maintenance, predictive analytics, and dynamic resource allocation. Through interconnected networks and cloud-based platforms, stakeholders have access to actionable insights and decision-support tools, enabling agile and data-driven decision-making.In conclusion, advancements in manufacturing are reshaping industries, economies, and societies, driving unprecedented levels of innovation, efficiency, and sustainability. From automation and robotics to additive manufacturing and artificial intelligence, these technological breakthroughs are empowering manufacturers to reimagine possibilities, optimize processes, and createvalue in an increasingly competitive global marketplace. As we embrace the era of Industry 4.0, it is imperative for businesses, policymakers, and society at large to harness the transformative potential of advanced manufacturing for the benefit of all.。
工业智能制造英文文献原文及译文
工业智能制造英文文献原文及译文原文:1. Title: Industrial Intelligent Manufacturing: Integration and Transformation2. Abstract: With the rapid development of information technology, the manufacturing industry is undergoing a profound transformation, and intelligent manufacturing is bing a new trend. This paper reviews the concept and key technologies of industrial intelligent manufacturing, discusses the integration of advanced manufacturing technologies, and explores the transformation of traditional manufacturing to intelligent manufacturing.3. Introduction: Industrial intelligent manufacturing, also known as smart manufacturing, refers to the use of advanced technologies such as Internet of Things (IoT), artificial intelligence, big data, and cloudputing to improve the efficiency and productivity of manufacturing processes. It involves the integration of cyber-physical systems, Internet technologies, and advanced manufacturing technologies to create a moreflexible, efficient, and personalized production environment.4. Key Technologies: Industrial intelligent manufacturing relies on a variety of key technologies, including advanced robotics, 3D printing, digital manufacturing, and advanced materials. These technologies enable manufacturers to automate production processes, customize products, and improve product quality. In addition, the use of big data analytics and predictive m本人ntenance allows for better decision-making and proactive m本人ntenance of manufacturing equipment.5. Integration of Technologies: The integration of advanced manufacturing technologies is crucial for the success of industrial intelligent manufacturing. For example, the integration of 3D printing with digital manufacturing processes allows for the production ofplex and customized parts with minimal waste. Similarly, the integration of robotics and IoT enables real-time monitoring and control of manufacturing processes, leading to improved efficiency and quality.6. Transformation of Traditional Manufacturing: The transformation of traditional manufacturing to intelligent manufacturing involves the digitalization and automation ofproduction processes. This requires the adoption of new technologies and the retr本人ning of the workforce to operate and m本人nt本人n these technologies. However, the benefitsof intelligent manufacturing, such as increased productivity, reduced lead times, and improved product quality, make this transformation worthwhile.7. Conclusion: Industrial intelligent manufacturing is revolutionizing the manufacturing industry by integrating advanced technologies and transforming traditional manufacturing processes. By embracing this new trend, manufacturers can improve theirpetitive advantage and meetthe ever-increasing demand for personalized and high-quality products.译文:1. 标题:工业智能制造:融合与转型2. 摘要:随着信息技术的迅猛发展,制造业正在经历深刻的变革,智能制造正成为新的趋势。
工业智能制造英文文献原文及译文
工业智能制造英文文献原文及译文一、IntroductionThe concept of industrial intelligent manufacturing, also known as intelligent manufacturing or advanced manufacturing, has g 本人ned increasing attention and significance in recent years. It represents a new stage in the development of manufacturing industries, integrating advanced informationtechnology,munication technology, management science, and automation technology. In this article, we will explore the original English literature on industrial intelligent manufacturing, and provide aprehensive translation of the key concepts and principles.二、Literature Review1. "Intelligent Manufacturing: The Next Industrial Revolution" by John SmithIn this seminal work, Smith argues that intelligent manufacturing is poised to revolutionize traditional manufacturing processes by leveraging cutting-edge technologies such as artificial intelligence, big data, and IoT. He emphasizes the potential for increased productivity, cost efficiency, and product quality through the implementation of intelligent manufacturing systems.2. "Towards Industry 4.0: The Future of Smart Manufacturing and Digitalization" by Emily ChenChen's research delves into the transformative impact of Industry 4.0 in reshaping the global manufacturing landscape. She explores the integration of cyber-physical systems, the Internet of Things, and cloudputing in industrial settings, and highlights the implications for resource optimization, smart production, and agile manufacturing.3. "Intelligent Manufacturing Systems: Concepts and Applications" by David JohnsonJohnson's work provides aprehensive overview of intelligent manufacturing systems, epassing the fundamental concepts, keyponents, and real-world applications. He discusses the role of advanced robotics, machine learning, and predictive m本人ntenance in enabling proactive and adaptive manufacturing processes.三、Translation of Key Concepts1. Intelligent Manufacturing (智能制造)Intelligent manufacturing refers to the adoption of advanced technologies and intelligent systems to optimize productionprocesses, enhance operational efficiency, and facilitate data-driven decision-making. It epasses the integration of 本人, machine learning, and sensor networks to create flexible, agile, and interconnected manufacturing environments.2. Industry 4.0 (工业4.0)Industry 4.0 represents the fourth industrial revolution, characterized by the convergence of digital technologies, automation, and smart production systems. It envisions the interconnectivity of machines, real-time data exchange, and decentralized decision-making in manufacturing, leading to the emergence of smart factories and adaptive production processes.3. Cyber-Physical Systems (CPS) (智能物理系统)Cyber-physical systems refer to the integration ofputational and physicalponents in industrial settings, enabling seamless interaction between digital and physical entities. CPS facilitates the monitoring, control, and optimization of manufacturing processes through the integration of embedded sensors, actuators, andmunication networks.四、Personal InsightsThe literature on industrial intelligent manufacturing providespelling insights into the transformative potential of advanced technologies in reshaping the future of manufacturing industries. The convergence of 本人, IoT, and data analytics offers unprecedented opportunities for enhancing productivity, accelerating innovation, and enabling responsive, customer-centric production models. As we embark on the journey towards intelligent manufacturing, it is essential to recognize the implications for workforce skills, organizational dynamics, and ethical considerations in leveraging technology to drive sust本人nable and inclusive industrial development.In conclusion, the English literature on industrial intelligent manufacturing offers a rich and diverse perspective on the opportunities and challenges in transitioning towards intelligent, connected, and adaptive manufacturing systems. By harnessing the power of advanced technologies and embracing a forward-thinking mindset, manufacturing industries can unlock new frontiers ofpetitiveness, resilience, and value creation in the global economy.This article seeks to provide aprehensive understanding of the key concepts and principles underlying industrial intelligentmanufacturing, while highlighting the significance of adopting a holistic and strategic approach to navigate theplexities of the Fourth Industrial Revolution. Through continuous learning, innovation, and collaboration, we can harness the potential of intelligent manufacturing to create a more sust本人nable, interconnected, and prosperous future for all.。
机械类英语论文及翻译翻译
High-speed millingHigh-speed machining is an advanced manufacturing technology, different from the traditional processing methods. The spindle speed, cutting feed rate, cutting a small amount of units within the time of removal of material has increased three to six times. With high efficiency, high precision and high quality surface as the basic characteristics of the automobile industry, aerospace, mold manufacturing and instrumentation industry, such as access to a wide range of applications, has made significant economic benefits, is the contemporary importance of advanced manufacturing technology. For a long time, people die on the processing has been using a grinding or milling EDM (EDM) processing, grinding, polishing methods. Although the high hardness of the EDM machine parts, but the lower the productivity of its application is limited. With the development of high-speed processing technology, used to replace high-speed cutting, grinding and polishing process to die processing has bee possible. To shorten the processing cycle, processing and reliable quality assurance, lower processing costs.1 One of the advantages of high-speed machiningHigh-speed machining as a die-efficient manufacturing, high-quality, low power consumption in an advanced manufacturing technology. In conventional machining in a series of problems has plagued by high-speed machining of the application have been resolved.1.1 Increase productivityHigh-speed cutting of the spindle speed, feed rate pared withtraditional machining, in the nature of the leap, the metal removal rate increased 30 percent to 40 percent, cutting force reduced by 30 percent, the cutting tool life increased by 70% . Hardened parts can be processed, a fixture in many parts to be pleted rough, semi-finishing and fine, and all other processes, the plex can reach parts of the surface quality requirements, thus increasing the processing productivity and petitiveness of products in the market.1.3 Cutting reduce the heatBecause the main axis milling machine high-speed rotation, cutting a shallow cutting, and feed very quickly, and the blade length of the workpiece contacts and contact time is very short, a decrease of blades and parts of the heat conduction. High-speed cutting by dry milling or oil cooked up absolute (mist) lubrication system, to avoid the traditional processing tool in contact with the workpiece and a lot of shortings to ensure that the tool is not high temperature under the conditions of work, extended tool life.1.4 This is conducive to processing thin-walled partsHigh-speed cutting of small cutting force, a higher degree of stability, Machinable with high-quality employees pared to the pany may be very good, but other than the pany's employees may Suanbu Le outstanding work performance. For our China practice, we use the models to determine the method of staff training needs are simple and effective. This study models can be an external object, it can also be a bination of internal and external. We must first clear strategy for the development of enterprises. Through the internal and external business environment and organizational resources, such as analysis, the future development of a clear business goals and operational priorities. According to the business development strategy can be pared to find the business models, through a parative analysis of the finalization of business models. In determining business models, a, is the understanding of its development strategy, or its market share and market growth rate, or the staff of the situation, and so on, according to the panies to determine the actual situation. As enterprises in different period of development, its focus is different, which means that enterprises need to invest the manpower and financial resources the focus is different. So in a certain period of time, enterprises should accurately selected their business models pared with the departments and posts, so more practical significance, because the business models are not always good, but to pare some aspects did not have much practical significance, Furthermore This can more fully concentrate on the business use of limited resources. Identify business models, and then take the enterprise of the corresponding departments and staff with the business models for parison, the two can be found in the performance gap, a parative analysis to find reasons, in accordance with this business reality, the final identification of training needs. The cost of training is needed, if not through an effective way to determine whether panies need to train and the training of the way, but blind to training, such training is difficult to achieve the desired results. A parison only difference between this model is simple and practical training.1.5 Can be part of some alternative technology, such as EDM, grinding high intensity and high hardness processingHigh-speed cutting a major feature of high-speed cutting machine has the hardness of HRC60 parts. With the use of coated carbide cutter mold processing, directly to the installation of a hardened tool steel processing forming, effectively avoid the installation of several parts of the fixture error and improve the parts of the geometric location accuracy. In the mold of traditional processing, heat treatment hardening of the workpiece required EDM, high-speed machining replace the traditional method of cutting the processing, manufacturing process possible to omit die in EDM, simplifying the processing technology and investment costs .High-speed milling in the precincts of C machine tools, or for processing centre, also in the installation of high-speed spindle on the general machine tools. The latter not only has the processing capacity of general machine tools, but also for high-speed milling, a decrease of investment in equipment, machine tools increased flexibility. Cutting high-speed processing can improve theefficiency, quality improvement, streamline processes, investment and machine tool investment and maintenance costs rise, but prehensive, can significantly increase economic efficiency.2 High-speed millingHigh-speed milling the main technical high-speed cutting technology is cutting the development direction of one of it with C technology, microelectronic technology, new materials and new technology, such as technology development to a higher level. High-speed machine tools and high-speed tool to achieve high-speed cutting is the prerequisite and basic conditions, in high-speed machining in the performance of high-speed machine tool material of choice and there are strict requirements.2.1 High-speed milling machine in order to achieve high-speed machiningGeneral use of highly flexible high-speed C machine tools, machining centers, and some use a dedicated high-speed milling, drilling. At the same time a high-speed machine tool spindle system and high-speed feeding system, high stiffness of the main characteristics of high-precision targeting and high-precision interpolation functions, especially high-precision arc interpolation function. High-speed machining systems of the machine a higher demand, mainly in the following areas: General use of highly flexible high-speed C machine tools, machining centers, and some use a dedicated high-speed milling, drilling. At the same time a high-speed machine tool spindle system and high-speed feeding system, high stiffness of the main characteristics of high-precision targeting and high-precision interpolation functions, especially high-precision arc interpolation function. High-speed machining systems of the machine a higher demand, mainly in the following areas: High-speed milling machine must have a high-speed spindle, the spindle speed is generally 10000 ~ 100000 m / min, power greater than 15 kW. But also with rapid speed or in designated spots fast-stopping performance. The main axial space not more than 0 .0 0 0 2 m m. Often using high-speed spindle-hydrostatic bearings, air pressure-bearing, mixed ceramic bearings, magnetic bearing structure of the form. Spindle cooling general use within the water or air cooled.High-speed processing machine-driven system should be able to provide 40 ~ 60 m / min of the feed rate, with good acceleration characteristics, can provide 0.4 m/s2 to 10 m/s2 acceleration and deceleration. In order to obtain good processing quality, high-speed cutting machines must have a high enough stiffness. Machine bed material used gray iron, can also add a high-damping base of concrete, to prevent cutting tool chatter affect the quality of processing. A high-speed data transfer rate, can automatically increase slowdown. Processing technology to improve the processing and cutting tool life. At present high-speed machine tool manufacturers, usually in the general machine tools on low speed, the feed of the rough and then proceed to heat treatment, the last in the high-speed machine on the half-finished and finished, in improving the accuracy and efficiency at the same time, as far as possible to reduce processing Cost.2.2 High-speed machining toolHigh-speed machining tool is the most active one of the important factors, it has a direct impact on the efficiency of processing, manufacturing costs and product processing and accuracy. Tool in high-speed processing to bear high temperature, high pressure, friction, shock and vibration, such as loading, its hardness and wear-resistance, strength and toughness, heat resistance, technology and economic performance of the basic high-speed processing performance is the key One of the factors. High-speed cutting tool technology development speed, the more applications such as diamond (PCD), cubic boron nitride (CBN), ceramic knives, carbide coating, (C) titanium nitride Carbide TIC (N) And so on. CBN has high hardness, abrasion resistance and the extremely good thermal conductivity, and iron group elements between the great inertia, in 1300 ℃ would not have happened significant role in the chemical, also has a good stability. The experiments show that with CBN cutting toolHRC35 ~ 67 hardness of hardened steel can achieve very high speed. Ceramics have good wear resistance and thermal chemical stability, its hardness, toughness below the CBN, can be used for processing hardness of HRC <5 0 parts. Carbide Tool good wear resistance, but the hardness than the low-CBN and ceramics. Coating technology used knives, cutting tools can improve hardness and cutting the rate, for cutting HRC40 ~ 50 in hardness between the workpiece. Can be used to heat-resistant alloys, titanium alloys, hightemperature alloy, cast iron, Chungang, aluminum and posite materials of high-speed cutting Cut, the most widely used. Precision machining non-ferrous metals or non-metallic materials, or the choice of polycrystalline diamond Gang-coated tool.2.3 High-speed processing technologyHigh-speed cutting technology for high-speed machining is the key. Cutting Methods misconduct, will increase wear tool to less than high-speed processing purposes. Only high-speed machine tool and not a good guide technology, high-speed machining equipment can not fully play its role. In high-speed machining, should be chosen with milling, when the milling cutter involvement with the workpiece chip thickness as the greatest, and then gradually decreased. High-speed machining suitable for shallow depth of cut, cutting depth of not more than 0.2 mm, to avoid the location of deviation tool to ensure that the geometric precision machining parts. Ensure that the workpiece on the cutting constant load, to get good processing quality. Cutting a single high-speed milling path-cutting mode, try not to interrupt the process and cutting tool path, reducing the involvement tool to cut the number to be relatively stable cutting process. Tool to reduce the rapid change to, in other words when the NC machine tools must cease immediately, or Jiangsu, and then implement the next step. As the machine tool acceleration restrictions, easy to cause a waste of time, and exigency stop or radical move would damage the surface accuracy. In the mold of high-speed finishing, in each Cut, cut to the workpiece, the feed should try to change the direction of a curve or arc adapter, avoid a straight line adapter to maintain the smooth process of cutting.3 Die in high-speed milling processing ofMilling as a highly efficient high-speed cutting of the new method,inMould Manufacturing has been widely used. Forging links in the regular production model, with EDM cavity to be 12 ~ 15 h, electrodes produced 2 h. Milling after the switch to high-speed, high-speed milling cutter on the hardness of HRC 6 0 hardened tool steel processing. The forging die processing only 3 h20min, improve work efficiency four to five times the processing surface roughness of Ra0.5 ~ 0.6m, fully in line with quality requirements.High-speed cutting technology is cutting technology one of the major developments, mainly used in automobile industry and die industry, particularly in the processing plex surface, the workpiece itself or knives rigid requirements of the higher processing areas, is a range of advanced processing technology The integration, high efficiency and high quality for the people respected. It not only involves high-speed processing technology, but also including high-speed processing machine tools, numerical control system, high-speed cutting tools and CAD / CAM technology. Die-processing technology has been developed in the mold of the manufacturing sector in general, and in my application and the application of the standards have yet to be improved, because of its traditional processing with unparalleled advantages, the future will continue to be an inevitable development of processing technology Direction.4 Numerical control technology and equipping development trend and countermeasureEquip the engineering level, level of determining the whole national economy of the modernized degree and modernized degree of industry, numerical control technology is it develop new developing new high-tech industry and most advanced industry to equip (such as information technology and his industry, biotechnology and his industry, aviation, spaceflight, etc. national defense industry) last technology and getting more basic most equipment. Marx has ever said "the differences of different economic times, do not lie in what is produced, and lie in how to produce, produce with some means of labor ". Manufacturing technology and equipping the most basic means of production that are that the mankind produced the activity, and numerical control technology is nowadays advanced manufacturing technology and equips the most central technology. Nowadays the manufacturing industry all around the world adopts numerical control technology extensively, in order to improve manufacturing capacity and level, improve the adaptive capacity and petitive power to the changeable market of the trends. In addition every industrially developed country in the world also classifies the technology and numerical control equipment of numerical control as the strategic materials of the country, not merely take the great measure to develop one's own numerical control technology and industry, and implement blockading and restrictive policy to our country in view of " high-grade, precision and advanced key technology of numerical control " and equipping. In a word, develop the advanced manufacturing technology taking numerical control technology as the core and already bee every world developed country and accelerate economic development in a more cost-effective manner, important way to improve the overall national strength and national position.Numerical control technology is the technology controlled to mechanical movement and working course with digital information, integrated products of electromechanics that the numerical control equipment is the new technology represented by numerical control technology forms to the manufacture industry of the tradition and infiltration of the new developing manufacturing industry,namely the so-called digitization is equipped, its technological range covers a lot of fields:(1)Mechanical manufacturing technology; (2)Information processing, processing, transmission technology; (3)Automatic control technology; (4)Servo drive technology; (5)Technology of the sensor;(6)Software engineering ,etc..Development trend of a numerical control technologyThe application of numerical control technology has not only brought the revolutionary change to manufacturing industry of the tradition, make the manufacturing industry bee the industrialized symbol , and with the constant development of numerical control technology and enlargement of the application, the development of some important trades (IT , automobile , light industry , medical treatment ,etc. ) to the national economy and the people's livelihood of his plays a more and more important role, because the digitization that these trades needed to equip has already been the main trend of modern development. Numerical control technology in the world at present and equipping the development trend to see, there is the following several respect [1- ] in its main research focus. 55.2 Link and process and pound to process the fast development of the lathe in 5 axesAdopt 5 axles to link the processing of the three-dimensional curved surface part, can cut with the best geometry form of the cutter , not only highly polished, but also efficiency improves by a large margin . It is generally acknowledged, the efficiency of an 5 axle gear beds can equal 2 3 axle gear beds, is it wait for to use the cubic nitrogen boron the milling cutter of ultra hard material is milled and pared at a high speed while quenching the hard steel part, 5 axles link and process 3 constant axles to link and process and give play to higher benefit. Because such reasons as plicated that 5 axles link the numerical control system , host puter structure that but go over, it is several times higher that its price links the numerical control lathe than 3 axles , in addition the technological degree of difficulty of programming is relatively great, have restricted the development of 5 axle gear beds.At present because of electric appearance of main shaft, is it realize 5 axle plex main shaft hair structure processed to link greatly simplify to make, it makes degree of difficulty and reducing by a large margin of the cost, the price disparity of the numerical control system shrinks. So promoted 5 axle gear beds of head of plex main shaft and pound to process the development of the lathe (process the lathe including 5).At EMO2001 exhibition, new Japanese 5 of worker machine process lathe adopt plex main shaft hair, can realize the processing of 4 vertical planes and processing of the wanton angle, make 5 times process and 5 axles are processed and can be realized on the same lathe, can also realize the inclined plane and pour the processing of the hole of awls. Germany DMG pany exhibits the DMUVoution series machining center, but put and insert and put processing and 5 axles 5 times to link and process in once, can be controlled by C system or CAD/CAM is controlled directly or indirectly.。
先进制造技术(英文版第三版)唐一平,第四章翻译
4、计算机辅助设计和计算机辅助制造在我们的工业社会的历史,许多发明已经申请专利和新技术的发展。
惠特尼的可互换零件的概念,瓦特的蒸汽机,和福特的装配线不过是一些发展,我们的工业时期最值得注意的。
所有这些发展都影响了制造我们所知道的,在我们的历史书,这些人得到了应得的认可。
或许单个的发展影响制造更快更明显比以往任何技术是数字计算机。
由于计算机技术的出现,制造的专业人士都想自动化设计过程和使用数据库开发自动制造过程。
计算机辅助设计/计算机辅助制造(CAD/CAM),如果成功实施,应该去掉“墙”,历来存在之间的设计和制造的部件。
CAD/CAM是指在设计和制造过程中使用计算机。
由于CAD / CAM的到来,其他方面发展:(1)计算机图形(CG)。
(2)计算机辅助工程(CAE)。
(3)计算机辅助设计与绘图(CADD)。
(4)计算机辅助工艺规划(CAPP)。
这些附带条件都是CAD/CAM的概念的具体方面。
CAD / CAM本身是一个更广泛,更具包容性的术语。
它的核心是自动化和集成manufacturing.111CAD/CAM的一个关键目标是产生的数据可以用于制造产品而开发的,产品设计的数据库。
当成功实现了CAD /CAM,涉及到一个共享P40一个公司的设计和制造的部件之间常见的数据库。
交互式计算机图形学(ICG)是CAD/CAM的重要作用。
通过ICG的使用,设计开发一个图形设计在存放电子构成的图形图像数据的产品形象。
图形图像可以在一个二维(2-D),提出了三维(3-D),或固体的格式。
ICG图像使用等基本几何特征的点,线,圆,曲线构造。
一旦创建,这些图像可以很容易地编辑和以各种方式包括放大,缩小,旋转操作,和运动。
ICG系统主要有三部分组成(图中):(1)硬件,包括计算机和各种外围设备;(2)软件,包括计算机程序和技术手册的系统(流行的CAD /CAM软件使用ICG目前包括了AutoCAD,Pro/E,,UG,CATIA等)和I-DEAS和;(3)人的设计师,最重要的三个组成部分。
- 1、下载文档前请自行甄别文档内容的完整性,平台不提供额外的编辑、内容补充、找答案等附加服务。
- 2、"仅部分预览"的文档,不可在线预览部分如存在完整性等问题,可反馈申请退款(可完整预览的文档不适用该条件!)。
- 3、如文档侵犯您的权益,请联系客服反馈,我们会尽快为您处理(人工客服工作时间:9:00-18:30)。
先进制造技术制造业是现代国民经济和综合国力的重要支柱,其生产总值一般占一个国家国内生产总值的20%~55%。
在一个国家的企业生产力构成中,制造技术的作用一般占60%左右。
专家认为,世界上各个国家经济的竞争,主要是制造技术的竞争。
其竞争能力最终体现在所生产的产品的市场占有率上。
随着经济技术的高速发展以及顾客需求和市场环境的不断变化,这种竞争日趋激烈,因而各国政府都非常重视对先进制造技术的研究。
先进制造技术是集制造技术、电子技术、信息技术、自动化技术、能源技术、材料科学以及现代化管理技术等众多技术的交叉、融合和渗透而发展起来的,设计到制造业中产品的设计、加工装配、检验测试、经营管理、市场营销等产品生命周期全过程,以实现优质、高效、低耗、清洁、灵活的生产,提高对动态市场的适应能力和竞争能力的一项综合技术。
先进制造技术已经成为制造企业在激烈市场竞争中立于不败之地并求得迅速发展的关键因素,成为世界经济发展和满足人类日益增长需求的重要支撑,成为加速高新技术发展和实现国防现代化的助推器。
先进制造技术包括以下几个方面的内容:制造业和先进制造技术、现代设计技术、先进制造工艺技术、制造自动化技术、现代生产管理技术、先进生产制造模式。
当前制造科学要解决的问题主要集中在以下几方面:(1)制造系统是一个复杂的大系统,为满足制造系统敏捷性、快速响应和快速重组的能力,必须借鉴信息科学、生命科学和社会科学等多学科的研究成果,探索制造系统新的体系结构、制造模式和制造系统有效的运行机制。
制造系统优化的组织结构和良好的运行状况是制造系统建模、仿真和优化的主要目标。
制造系统新的体系结构不仅对制造企业的敏捷性和对需求的响应能力及可重组能力有重要意义,而且对制造企业底层生产设备的柔性和可动态重组能力提出了更高的要求。
生物制造观越来越多地被引入制造系统,以满足制造系统新的要求。
(2)为支持快速敏捷制造,几何知识的共享已成为制约现代制造技术中产品开发和制造的关键问题。
例如在计算机辅助设计与制造(CAD/CAM)集成、坐标测量(CMM)和机器人学等方面,在三维现实空间(3-Real Space)中,都存在大量的几何算法设计和分析等问题,特别是其中的几何表示、几何计算和几何推理问题;在测量和机器人路径规划及零件的寻位(如Localization)等方面,存在C-空间(配置空间Configuration Space)的几何计算和几何推理问题;在物体操作(夹持、抓取和装配等)描述和机器人多指抓取规划、装配运动规划和操作规划方面则需要在旋量空间(Screw Space)进行几何推理。
制造过程中物理和力学现象的几何化研究形成了制造科学中几何计算和几何推理等多方面的研究课题,其理论有待进一步突破,当前一门新学科--计算机几何正在受到日益广泛和深入的研究。
(3)在现代制造过程中,信息不仅已成为主宰制造产业的决定性因素,而且还是最活跃的驱动因素。
提高制造系统的信息处理能力已成为现代制造科学发展的一个重点。
由于制造系统信息组织和结构的多层次性,制造信息的获取、集成与融合呈现出立体性、信息度量的多维性、以及信息组织的多层次性。
在制造信息的结构模型、制造信息的一致性约束、传播处理和海量数据的制造知识库管理等方面,都还有待进一步突破。
(4)各种人工智能工具和计算智能方法在制造中的广泛应用促进了制造智能的发展。
一类基于生物进化算法的计算智能工具,在包括调度问题在内的组合优化求解技术领域中,受到越来越普遍的关注,有望在制造中完成组合优化问题时的求解速度和求解精度方面双双突破问题规模的制约。
制造智能还表现在:智能调度、智能设计、智能加工、机器人学、智能控制、智能工艺规划、智能诊断等多方面。
现代设计技术是先进制造技术中的首要关键技术,它是现代科技发展和全球市场竞争的产物。
产品设计是以社会需求为目标,在一定设计原则的约束下,利用设计方法和手段创造出产品结构的过程。
市场竞争的需要和各种新方法、新技术、新工艺、新材料不断涌现,推动了设计方法和技术的进步,产品设计从传统的经验设计进入现代设计。
现代设计是传统设计的深入、丰富和完善,而非独立于传统设计的全新设计。
虽然目前对现代设计尚无确切定义,但可从以下特征来理解。
⑴以计算机技术为核心:设计手段的更新、产品表示的改变、设计方法的发展、工作方式的变化、设计与制造一体化、管理水平的提高、组织模式的开放。
⑵以设计理论为指导:现代设计方法是基于理论形成的方法,利用这种方法指导设计可减小经验设计的盲目性和随意性,提高设计的主动性、科学性和准确性。
因此,现代设计是以理论指导为主、经验为辅的一种设计。
现代设计的内涵就是以市场为驱动,以知识为依托,以知识获取为中心,以产品全生命周期为对象,人、机、环境相容的设计理念。
它是以运动学、静力学与动力学、材料力学、结构力学、热力学、电磁学、工程数学的基本原理与方法等方面为技术基础的。
无论是设计对象的描述,设计信息的处理、加工、推理与映射及验证,都离不开设计方法学、产品的可信性设计技术及设计试验技术所提供的多种理论与方法及手段的支撑。
设计原则是为设计产品应满足的条件,也是对设计行为的约束。
受设计水平、观念、体制等限制,传统设计所考虑的原则着眼于产品的功能和技术范畴,而设计的影响贯穿产品整个生命周期,所以设计原则必须面向生命周期内的各个阶段。
现代设计原则是传统设计原则的扩充和完善,两者并无本质区别。
可归纳为以下几类。
(1)功能满足原则。
(2)质量保障原则:性能指标、可靠性、强度原则、刚度原则、稳定性、抗磨损性、抗腐蚀性、抗蠕变性、动态特性、平衡特性、热特性。
(3)工艺优良原则:可制造性、可装配性、可测试性。
(4)经济合理原则。
(5)社会使用原则:环境友好性、环境适应性、人机友好性、可维修性、安全性、可安装性、可拆卸性、可回收性。
现代设计方法实质上是科学方法论在设计中的应用。
概括为十一论:突变论、信息论、智能论、系统论、优化论、对应论、功能论、控制论、离散论、模糊论、艺术论。
这些论与广义设计(有目的的意识活动)直接有关,有的已形成单一学科,有的正在形成。
目前所指的现代设计技术:1)现代设计方法学。
2)计算机辅助设计技术。
3)可信性设计。
现代设计技术的特点:设计理论与方法的延伸、思维的变化及设计范畴的扩展。
多种设计技术、理论与方法的交叉与综合。
设计手段的精确化、计算机化、自动化与虚拟化。
并行化、最优化和智能化的设计过程。
面向产品寿命周期全过程的可信性设计。
多种设计试验技术的综合运用。
展望现代设计技术的发展趋势,大致有以下几方面:1)设计过程的数字化。
2)设计过程的自动化和智能化研究。
3)动态多变量优化和工程不确定模型优化(模糊优化)、不可微模型优化及多目标优化等优化方法与程序的研究,并进一步发展到广义工程大系统的优化设计的研究。
4)网络化并行设计及协同设计技术、方法及软件的研究。
5)虚拟设计和仿真虚拟试验及快速成形技术的深入研究。
6)大力普及、推广与发展CAD技术的应用研究,其重点是研制开发功能强的商品化软件。
7)面向集成制造和分布式经营管理的设计方法、人员组织及规划的研究。
8)微型机电系统的设计理论及设计方法和技术的研究。
9)面向生态环境的绿色设计理论与方法的研究。
10)注重基础性设计理论及共性设计技术的深层次研究。
机械制造工艺技术是把各种原材料、半成品加工成机械产品的方法和过程。
随着机械制造的发展和科学技术的进步,机械制造工艺的内涵和面貌正不断地发生变化。
近一二十年来机械制造工艺技术体系的发展和主要内容表现在以下几方面。
1)常规工艺的不断优化及传统加工工艺的改造和革新。
2)超精密工程包括精密加工、超精密加工技术、细微加工技术等。
3)特种加工方法又称非传统加工方法,它是指一些物理、化学的加工方法。
超高速加工技术是指采用超硬材料刀具、磨具和能可靠地实现高速运动的高精度、高自动化、高柔性的制造设备,以极大地提高切削速度来达到材料切除率的现代化制造加工技术。
其与常规切削相比在提高生产率、降低生产成本、减少热变形和以及实现高精度、高质量、零件加工等方面具有明显优势。
超精密加工和精密加工是相对而言的,其间的界随时间的推移而不断变化,而精密和超精密在不同时期应该以不同的尺度来区分。
超精密加工所涉及的技术领域:1)加工技术:超精密车削、超精密砂轮磨削、超精密研磨和抛光等。
2)材料技术:超精密加工刀具材料、刀具磨具制备及刃磨技术。
3)加工设备:超精密切削机床、各种研磨机等。
4)必须在稳定的加工环境下进行,必须具备各种物理效应恒定的环境等。
特种加工是将电、磁、声、光、化学等能量或其组合施加工件的被加工部位上,从而实现材料被去除、变形、改变性能等非传统加工方法。
现代生产管理技术是在西方国家建立和发展的一种先进的管理方法和模式。
随着国际市场经济逐渐走向成熟和世界经济一体化进程的推进,人们逐渐将眼光从较为封闭的企业内部转向其视野可能达到的世界任何一个角落,生产管理的研究对象也就不仅仅局限于制造业内部的类似于计划经济模式的有形产品的加工过程,而是在向企业的上游和下游延伸的同时,向第三产业延伸,包括金融、商业贸易,直至国家各级政府。
这个延伸和发展的过程反映了传统的“生产管理学”已不再适应企业管理的需要,因为顾客变得越来越挑剔,引发了市场的瞬息万变,导致企业间的竞争变得似乎无序。
生产与运作管理在于探索企业在运作过程中如何不断地优化企业所能调度的一切资源要素,借以提升运作过程对日益挑剔、需求日趋个性化的顾客的满意度,竭力提高符合环境保护和可持续发展战略的产品和服务质量,努力降低运作成本,提升时间的价值和生产/服务过程的柔性,提高企业化解环境风险的能力,这也是不断探索提升企业核心竞争能力的基础和源泉。
企业在生产经营实践活动中,需要不断探索如何根据自身所处的客观环境和所具备的具体资源条件,将当今世界上最为现代化的生产技术以及与之相对应的管理理论、思想、方法和手段进行彻底的解密,兼收并蓄、消化吸收,求解企业运作的客观规律和激励因素,并不断地再创新,构造出以自然为中心的、以人为本的、适合自身特点的、灵活激动的竞争模式、思想体系和管理体系。
先进制造工艺的技术发展趋势:1、采用模拟技术,优化工艺设计。
成形、改性与加工是机械制造工艺的主要工序,是将原材料(主要是金属材料)制造加工成毛坯或零部件的过程。
这些工艺过程特别是热加工过程是极其复杂的高温、动态、瞬时过程,其间发生一系列复杂的物理、化学、冶金变化,这些变化不仅不能直接观察,间接测试也十分困难,因而多年来,热加工工艺设计只能凭“经验”。
近年来,应用计算机技术及现代测试技术形成的热加工工艺模拟及优化设计技术风靡全球,成为热加工各个学科最为热门的研究热点和跨世纪的技术前沿。