FANUC系统加工中心编程详解
FANUC系统加工中心的11种孔加工固定循环指令
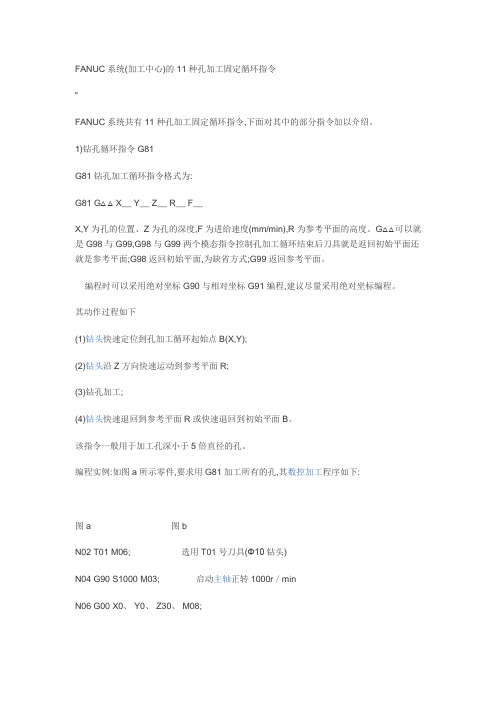
FANUC系统(加工中心)的11种孔加工固定循环指令”FANUC系统共有11种孔加工固定循环指令,下面对其中的部分指令加以介绍。
1)钻孔循环指令G81G81钻孔加工循环指令格式为:G81 G△△ X__ Y__ Z__ R__ F__X,Y为孔的位置、Z为孔的深度,F为进给速度(mm/min),R为参考平面的高度。
G△△可以就是G98与G99,G98与G99两个模态指令控制孔加工循环结束后刀具就是返回初始平面还就是参考平面;G98返回初始平面,为缺省方式;G99返回参考平面。
编程时可以采用绝对坐标G90与相对坐标G91编程,建议尽量采用绝对坐标编程。
其动作过程如下(1)钻头快速定位到孔加工循环起始点B(X,Y);(2)钻头沿Z方向快速运动到参考平面R;(3)钻孔加工;(4)钻头快速退回到参考平面R或快速退回到初始平面B。
该指令一般用于加工孔深小于5倍直径的孔。
编程实例:如图a所示零件,要求用G81加工所有的孔,其数控加工程序如下:图a 图bN02 T01 M06; 选用T01号刀具(Φ10钻头)N04 G90 S1000 M03; 启动主轴正转1000r/minN06 G00 X0、 Y0、 Z30、 M08;N08 G81 G99 X10、 Y10、 Z-15、 R5 F20; 在(10,10)位置钻孔,孔的深度为15mm,参考平面高度为5mm,钻孔加工循环结束返回参考平面N10 X50; 在(50,10)位置钻孔(G81为模态指令,直到G80取消为止) N12 Y30; 在(50,30)位置钻孔N14 X10; 在(10,30)位置钻孔N16 G80; 取消钻孔循环N18 G00 Z30N20 M302)钻孔循环指令G82G82钻孔加工循环指令格式为:G82 G△△ X__ Y__ Z__ R__ P__ F__在指令中P为钻头在孔底的暂停时间,单位为ms(毫秒),其余各参数的意义同G81。
FANUC加工中心编程指令介绍

FANUC 0iMD基本编程指令
数控铣床编程指令分为两大类:
第1类指令称为准备功能指令,即G指令,用来实现刀具轨迹控制、刀具补偿、尺寸单位设定、坐标系原点设定等;如下表1。
第2类指令称为辅助功能指令,用来实现机床的辅助功能,如主轴启停、切削液开关、自动换刀等等。
其中,S指令用来指定主轴转速,F指令用来指定进给速度,T指令用来指定所换刀具,其余辅助控制指令由M指令实现。
如下表2。
表1 准备功能G指令
从上表1可以看到,G指令划分为不同的组别,同一组别的G指令是不相容的。
如01组的G00、G01、G02、G03,如程序指令当前为G01,当使用G02并起作用时,G01自然失去作用。
程序G指令有模态指令与非模态指令之分,模态指令不仅在当前的程序段起作用,而且在后续的程序段中一直起作用,直到被另一个同组别的G指令代替为止;非模态指令指指在它所在的程序段中起作用的G指令,如暂停指令G04。
表2 辅助功能M指令
主轴功能S指令,用来指定主轴的转速,如S3000,表示主轴转速为3000r/min;进给功能F指令,用来指定进给速度,如F1000,表示刀具的进给速度为1000mm/min;刀具选择功能T指令,如T04 M06,表示将刀库中的4号刀具交换到主轴。
发那科加工中心编程

意义 程序号 顺序号 指定移动方式 坐标轴移动指令 圆弧半径 圆弧起点到圆弧中心的距离
进给速度
F
每分钟进给速度、每转进给速度
主轴功能 刀具功能 辅助功能 偏置号 暂停 程序号指定 重复次数 参数
S T M D、H P、X P L、P、K P、Q、R
主轴转速 刀号 机床上各种开关的控制 刀具补偿 暂停时间 子程序号 子程序重复次数 固定循环参数
◤
G01
G02
G03
G04
G05.1
G07.1(G107)
G08
G09
G10
G11 ◤ G15
G16
◤
G17
◤
G18
◤
G19
G20
G21
◤
G22
G23
G27
G28
G29
G30
组
功能
定位
直线插补 01 圆弧插补(顺时针)
圆弧插补(逆时针)
停刀,暂停
AI先行控制/AI轮廓控制
圆柱插补
00 先行控制
准确停止
设定工件坐标系/最大主轴速度 00
工件坐标系预置
每分钟进给 05 每转进给
13 恒表面速度控制 恒表面速度控制取消
固定循环返回到初始点 10
固定循环返回到R点
20 横向进磨控制取消 横向进磨控制
9
3、常用G代码说明
(1)绝对值编程(G90)和增量值编程(G91) 有两种方法指令刀具的移动:绝对值指令G90和增量值指令G91。 指令格式:G90 X_Y_Z_; G91 X_Y_Z_; 绝对值指令是刀具移动到“距坐标系原点的某一距离”的点; 增量值指令是指刀具从前一个位置移动到下一个位置的位移量。
FANUC系统加工中心编程与操作实例

FANUC系统加工中心编程与操作实例教学要求:1.了解加工中心的分类及特点;掌握机床坐标系和工作坐标系的建立原则和方法。
2.掌握加工中心常用指令(FANUC系统)。
3.掌握固定循环的应用(FANUC系统)。
4.掌握宏程序的格式及应用。
5.掌握加工中心的操作。
6.运用数控编程的知识,进行零件加工工艺分析,完成典型零件的加工程序编制。
2.教学内容:⌝加工中心概述⌝FANUC系统加工中心常用指令⌝常用指令的综合应用⌝典型零件的加工⌝宏程序的应用⌝FANUC系统加工中心的操作第一节加工中心概述一、加工中心种类1.立式加工中心2.卧式加工中心3.立卧加工中心二、数控加工中心工具及辅助设备1.数控回转工作台和数控分度工作台(1)数控回转工作台(2)数控分度工作台2.常用工具。
(1)对刀器(2)找正器(3)光学数显对刀仪三、数控加工中心1.刀柄及刀具系统(1)刀柄(2)刀具系统加工中心常用的铣刀有面铣刀、立铣刀两种,也可用锯片铣刀、三刃面铣刀等2.镗铣加工中心刀库(1)刀库类型加工中心常用的有盘式和链式刀库两种。
(2)选刀方式常用的选刀方式有顺序选刀方式、光电识别选刀方式两种。
第二节FANUC系统加工中心常用指令一、G代码命令1.绝对值坐标指令G90和增量值坐标指令G912.平面选择指令G17、G18、G193.快速点定位G00指令,直线插补G01指令例1使用G00、G01指令,使刀具按如图2-24所示的路径进给。
图2-24 G00、G01指令的使用程序:O0001;G90G54G00X20.0Y20.0;G01Y50.0F50;X50.0;Y20.0;X20.0;G00X0Y0;…4.圆弧插补指令G02、G03例2完成图2-25所示加工路径程序编制(刀具现位于A点上方,只进行轨迹运动)。
图2-25程序:O0002;G90G54G00X0Y25.0;G02X25.0Y0I0J-25.0;A—B点G02X0Y-25.0I-25.0J0;B—C点G02X-25.0Y0I0J25.0;C—D点G02X0Y25.0I25.0J0;D—A点或:G90G54G00X0Y25.0;G02X0Y25.0I0J-25.0;A—A点整圆5.自动原点返回(G28/G30)6.暂停指令G047.刀具半径补偿功能(G40/G41/G42)格式G41G0/G01X_Y_D_;G42G0/G01X_Y_D_;G40G0/G01X_Y_Z_;8.刀具长度补偿实现这种功能的G代码是G43、G44、G49。
实验四: FANUC加工中心编程及仿真加工

数控技术实验指导书郑州科技学院实验中心机械实验室实验四:FANUC加工中心编程及仿真加工一、实验目的(一)熟悉加工中心的外形布局及运动分配。
(二)熟悉加工中心的操作方法。
(三)掌握编制数控加工程序的基本方法及常用指令的使用。
二、实验原理(一)熟悉FANUV加工中心的编程规则,(二)熟悉FANUV加工中心的编程指令,及FANUV加工中心的坐标系输入方法,(三)熟悉掌握FANUV加工中心圆弧的加工指令G02和G03的运用区别。
(四)熟悉掌握FANUV加工中心的钻孔指令G73与G83的运用区别。
(五)熟悉掌握FANUV加工中心的刀偏置G41、G42、G43、G44区别和应用方法。
(六)编制FANUV加工中心零件的加工方法和工艺三、实验环境及操作(一)实验平台:VNUC(数控加工仿真软件):FANUC加工中心(一)机床主要技术参数:X轴行程范围1300~0 mmY轴行程范围:-640~0mmZ轴行程范围:-600~0mm最高主轴转速:9999.r.p.m最大进给速度:24000 mm / min(二)仿真实验环境及操作:仿真操作区机床控制面板主菜单视图操作图1打开VNUCFANUC 系统,进入主界面如图1。
屏幕分为左右两部分,左侧为数控机床仿真操作区,右侧为机床控制面板。
功能简介如下: 1.主菜单:七个主菜单“文件、显示、工艺流程、工具、选项、教学管理、帮助”。
点击主菜单,出现子菜单如图22.机床及加工实体图:可以从不同视角显示机床及加工区实体。
3.视图操作:扩大和缩小图像:按下。
将光标移到机床上任意处。
按下鼠标左键,按住并向上、下方轻轻拖动,即可放大缩小图像。
局部扩大:按下。
将光标移到机床需要放大的部位,按下并拖动鼠标左键,即可局部放大。
旋转图像:按下,将光标移到机床上任意处。
按下鼠标左键,拖动,即可旋转图像。
移动图像:按下图标,将光标移到机床上任意处,按下鼠标左键,向目的方向拖动鼠标,至满意位置时松开即可。
FANUC系统(加工中心)的11种孔加工固定循环指令
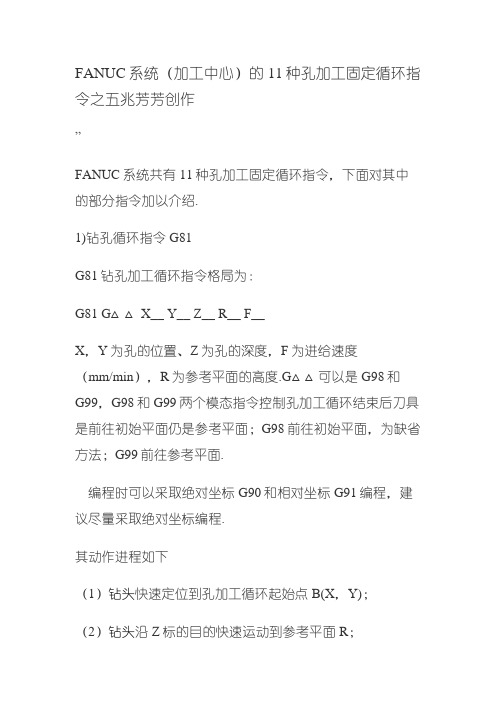
FANUC系统(加工中心)的11种孔加工固定循环指令之五兆芳芳创作”FANUC系统共有11种孔加工固定循环指令,下面对其中的部分指令加以介绍.1)钻孔循环指令G81G81钻孔加工循环指令格局为:G81 G△△ X__ Y__ Z__ R__ F__X,Y为孔的位置、Z为孔的深度,F为进给速度(mm/min),R为参考平面的高度.G△△可以是G98和G99,G98和G99两个模态指令控制孔加工循环结束后刀具是前往初始平面仍是参考平面;G98前往初始平面,为缺省方法;G99前往参考平面.编程时可以采取绝对坐标G90和相对坐标G91编程,建议尽量采取绝对坐标编程.其动作进程如下(1)钻头快速定位到孔加工循环起始点B(X,Y);(2)钻头沿Z标的目的快速运动到参考平面R;(3)钻孔加工;(4)钻头快速退回到参考平面R或快速退回到初始平面B.该指令一般用于加工孔深小于5倍直径的孔.编程实例:如图a所示零件,要求用G81加工所有的孔,其数控加工程序如下:图a 图bN02 T01 M06; 选用T01号刀具(Φ10钻头)N04 G90 S1000 M03; 启动主轴正转1000r/min N06 G00 X0. Y0. Z30. M08;N08 G81 G99 X10. Y10. Z-15. R5 F20; 在(10,10)位置钻孔,孔的深度为15mm,参考平面高度为5mm,钻孔加工循环结束前往参考平面N10 X50; 在(50,10)位置钻孔(G81为模态指令,直到G80取消为止)N12 Y30; 在(50,30)位置钻孔N14 X10; 在(10,30)位置钻孔N16 G80;取消钻孔循环N18 G00 Z30N20 M302)钻孔循环指令G82G82钻孔加工循环指令格局为:G82 G△△ X__ Y__ Z__ R__ P__ F__在指令中P为钻头在孔底的暂停时间,单位为ms(毫秒),其余各参数的意义同G81.该指令在孔底加进给暂停动作,即当钻头加工到孔底位置时,刀具不作进给运动,并保持旋转状态,使孔底更滑腻.G82一般用于扩孔和沉头孔加工.其动作进程如下(1)钻头快速定位到孔加工循环起始点B(X,Y);(2)钻头沿Z标的目的快速运动到参考平面R;(3)钻孔加工;(4)钻头在孔底暂停进给;B.3)高速深孔钻循环指令G73对于孔深大于5倍直径孔的加工由于是深孔加工,倒霉于排屑,故采取间段进给(分多次进给),每次进给深度为Q,最后一次进给深度≤Q,退刀量为d(由系统内部设定),直到孔底为止.见图b所示.G73高速深孔钻循环指令格局为:G73 G△△ X__ Y__ Z__ R__ Q__ F__在指令中Q为每次进给深度为Q,其余各参数的意义同G81.其动作进程如下(1)钻头快速定位到孔加工循环起始点B(X,Y);(2)钻头沿Z标的目的快速运动到参考平面R;(3)钻孔加工,进给深度为Q;(4)退刀,退刀量为d(5)重复(3)、(4),直至要求的加工深度B.4)攻螺纹循环指令G84G84螺纹加工循环指令格局为:G84 G△△ X__ Y__ Z__ R__ F__攻螺纹进程要求主轴转速S与进给速度F成严格的比例关系,因此,编程时要求按照主轴转速计较进给速度,进给速度F=主轴转速×螺纹螺距,其余各参数的意义同G81. 使用G84攻螺纹进给时主轴正转,退出时主轴反转.与钻孔加工不合的是攻螺纹结束后的前往进程不是快速运动,而是以进给速度反转退出.该指令执行前,甚至可以不启动主轴,当执行该指令时,数控系统将自动启动主轴正转.其动作进程如下(1)主轴正转,丝锥快速定位到螺纹加工循环起始点B(X,Y);(2)丝锥沿Z标的目的快速运动到参考平面R;(3)攻丝加工;(4)主轴反转,丝锥以进给速度反转退回到参考平面R;(5)当使用G98指令时,丝锥快速退回到初始平面B.编程实例:对图5-34中的4个孔进行攻螺纹,攻螺纹深度10mm,其数控加工程序为:N02 T01 M06; 选用T02号刀具(Φ10丝锥.螺距为2mm)N04 G90 S150 M03; 启动主轴正转1000r/minN06 G00 X0. Y0. Z30. M08;N08 G84 G99 X10. Y10. Z-10. R5 F300; 在(10,10)位置攻螺纹,螺纹的深度为10mm,参考平面高度为5mm,螺纹加工循环结束前往参考平面,进给速度F=(主轴转速)150×(螺纹螺距)2=300N10 X50; 在(50,10)位置攻螺纹(G84为模态指令,直到G80取消为止)N12 Y30; 在(50,30)位置攻螺纹N14 X10; 在(10,30)位置攻螺纹N16 G80;取消攻螺纹循环N18 G00 Z30N20 M305)左旋攻螺纹循环指令G74G74螺纹加工循环指令格局为:G74 G△△ X__ Y__ Z__ R__ F__与G84的区别是:进给时主轴反转,退出时主轴正转.各参数的意义同G84.其动作进程如下:(1)主轴反转,丝锥快速定位到螺纹加工循环起始点B(X,Y);(2)丝锥沿Z标的目的快速运动到参考平面R;(3)攻丝加工;(4)主轴正转,丝锥以进给速度正转退回到参考平面R;(5)当使用G98指令时,丝锥快速退回到初始平面B. 6)镗孔加工循环指令G85G85镗孔加工循环指令指令格局为:G85 G△△ X__ Y__ Z__ R__ F__各参数的意义同G81.其动作进程如下:(1)镗刀快速定位到镗孔加工循环起始点B(X,Y);(2)镗刀沿Z标的目的快速运动到参考平面R;(3)镗孔加工;(4)镗刀以进给速度退回到参考平面R或初始平面B;7)镗孔加工循环指令G86G86钻孔加工循环指令格局为:G86 G△△ X__ Y__ Z__ R__ F__与G85的区别是:在到达孔底位置后,主轴停止,并快速退出.各参数的意义同G85.其动作进程如下:(1)镗刀快速定位到镗孔加工循环起始点B(X,Y);(2)镗刀沿Z标的目的快速运动到参考平面R;(3)镗孔加工;(4)主轴停,镗刀快速退回到参考平面R或初始平面B;8)镗孔加工循环指令G89G89镗孔加工循环指令格局为:G89G△△ X__ Y__ Z__ R__ P__ F__与G85的区别是:在到达孔底位置后,进给暂停.P为暂停时间(ms),其余参数的意义同G85.其动作进程如下:(1)镗刀快速定位到镗孔加工循环起始点B(X,Y);(2)镗刀沿Z标的目的快速运动到参考平面R;(3)镗孔加工;(4)进给暂停;(5)镗刀以进给速度退回到参考平面R或初始平面B;9)精镗循环指令G76G76镗孔加工循环指令格局为:G76 G△△ X__ Y__ Z__ R__ P__ Q__ F__与G85的区别是:G76在孔底有三个动作:进给暂停、主轴准停(定向停止)、刀具沿刀尖的反向偏移Q值,然后快速退出.这样包管刀具不划伤孔的概略.P为暂停时间(ms),Q 为偏移值,其余各参数的意义同G85.其动作进程如下:(1)镗刀快速定位到镗孔加工循环起始点B(X,Y);(2)镗刀沿Z标的目的快速运动到参考平面R;(3)镗孔加工;(4)进给暂停、主轴准停、刀具沿刀尖的反向偏移;(5)镗刀快速退出到参考平面R或初始平面B;10)背镗循环指令G87G87背镗加工循环指令指令格局为:G87 G△△ X__ Y__ Z__ R__ Q__ F__各参数的意义同G76.其动作进程如下:(1)镗刀快速定位到镗孔加工循环起始点B(X,Y);(2)主轴准停、刀具沿刀尖的反标的目的偏移;(3)快速运动到孔底位置;(4)刀尖正标的目的偏移回加工位置,主轴正转;(5)刀具向上进给,到参考平面R;(6)主轴准停,刀具沿刀尖的反标的目的偏移Q值;(7)镗刀快速退出到初始平面B;(8)沿刀尖正标的目的偏移;11)取消孔加工循环指令G80。
1加工中心-宏程序编程讲解

• G1 Z[#3] F1000
• G41 G1 X[#1] Y0 D01 左刀补,刀补号位1
• G03 I[-#1] J0 Z[#3+1.5]; 一定要用G03逆时针编程
• #3=#3+1.5;
螺纹的螺距1.5递增
• ENDW;
首先调用#3的程序返回
• G40 G1 X0 Y0
• #1=#1+0.3;
• N8 #5= [#4-#3]*COS[#1*PI/180]; 圆球起点X轴点的坐标计算
• #6= [#4-#3]*SIN[#1*PI/180]; 圆球起点Z轴点的坐标计算
• G01 X[-#5] Y0 Z[-#6-#3] F1000; 进给至圆球面的X、Y、Z、轴起点位置
• G03 I[#5];
整圆铣削加工
• #1=#1+3;
Z轴每次增加量,增加量为每次3度
• IF[#1LE#2] GOTO8; 当角度未到90度时,转移到N8程序段
• G0 Z100;
• M30;
【华中系统编程】 铣螺纹
铣削M36*1.5-6G的螺纹,【Φ17mm的内螺纹刀、螺纹刀片为M1.5】:
• 1. 洗M36*1.5-6G的螺纹,【Φ17mm的内螺纹刀、螺纹刀片为M1.5】:
• 4.【凹球】铣SR20半球体(凹球),Φ10球刀:(角度编程)
• O0001:
• G54 G17 G40 G69 G80 G49 G90;
• M03 S1500 G00 X0 Y0 Z100;
• Z0;
• #1=0; 起始角
• #2=90; 终止角
• #3=5; 球刀半径
• #4=20; 圆球半径
• 2. 铣SR28圆弧,Φ16立铣刀:(步距编程)
发那科数控系统的编程与操作
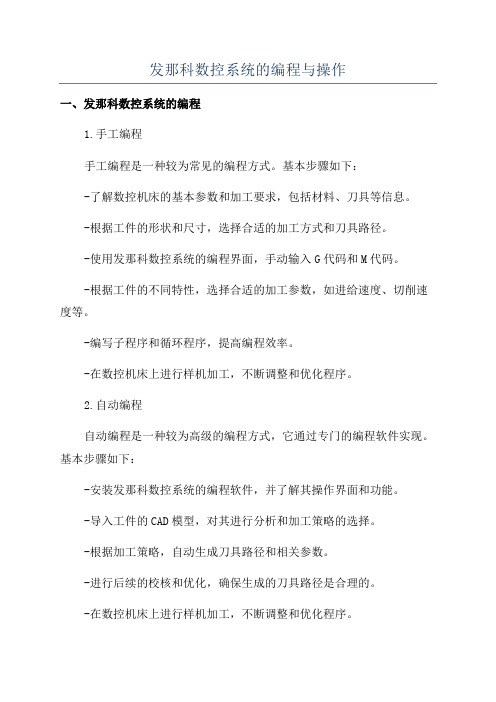
发那科数控系统的编程与操作一、发那科数控系统的编程1.手工编程手工编程是一种较为常见的编程方式。
基本步骤如下:-了解数控机床的基本参数和加工要求,包括材料、刀具等信息。
-根据工件的形状和尺寸,选择合适的加工方式和刀具路径。
-使用发那科数控系统的编程界面,手动输入G代码和M代码。
-根据工件的不同特性,选择合适的加工参数,如进给速度、切削速度等。
-编写子程序和循环程序,提高编程效率。
-在数控机床上进行样机加工,不断调整和优化程序。
2.自动编程自动编程是一种较为高级的编程方式,它通过专门的编程软件实现。
基本步骤如下:-安装发那科数控系统的编程软件,并了解其操作界面和功能。
-导入工件的CAD模型,对其进行分析和加工策略的选择。
-根据加工策略,自动生成刀具路径和相关参数。
-进行后续的校核和优化,确保生成的刀具路径是合理的。
-在数控机床上进行样机加工,不断调整和优化程序。
二、发那科数控系统的操作1.打开数控机床的电源,启动发那科数控系统。
2.选择合适的工作模式,如手动模式、自动模式等。
3.进入编程界面,输入相应的指令和参数。
4.根据加工要求,选择合适的刀具和刀具路径。
5.设置加工参数,如切削速度、进给速度等。
6.进行刀具的预调和工件的定位,确保加工的精度。
7.启动数控机床,进行加工操作。
8.监控加工过程,及时调整参数和纠正错误。
9.加工完成后,关闭数控机床和发那科数控系统。
发那科数控系统的编程与操作需要熟悉一定的机械加工知识和对数控系统的理解。
在实际操作中,需要根据具体的加工要求和工件特性进行合理的选择和设置。
同时,还需要不断学习和积累经验,不断提高编程和操作的技术水平。
只有这样,才能更好地应用发那科数控系统,提高生产效率和产品质量。
- 1、下载文档前请自行甄别文档内容的完整性,平台不提供额外的编辑、内容补充、找答案等附加服务。
- 2、"仅部分预览"的文档,不可在线预览部分如存在完整性等问题,可反馈申请退款(可完整预览的文档不适用该条件!)。
- 3、如文档侵犯您的权益,请联系客服反馈,我们会尽快为您处理(人工客服工作时间:9:00-18:30)。
F A N U C系统加工中心编程详解Company number:【0089WT-8898YT-W8CCB-BUUT-202108】FANUC-Oi-MD系统数控编程常用编程指令一:准备功能(G功能)准备功能G代码用来规定刀具和工件的相对运动轨迹、机床坐标系、坐标平面、刀具补偿、坐标偏置等多种加工操作。
数控加工常用的G功能代码见表4-1.表4-1二:辅助功能(M代码)辅助功能代码用于指令数控机床辅助装置的接同和关断,如主轴转/停、切削液开/关,卡盘夹紧/松开、刀具更换等动作。
常用M代码见表如下:M05主轴停止用于主轴停止转动M06换刀用于加工中心的自动换刀M08切削液开用于切削液开M09切削液关用于切削液关M98调用子程序用于子程序M99子程序结束用于子程序结束并返回主程序坐标系编程指令一、有关坐标和坐标系的指令(1)、工件坐标系设定G92格式:G92 X_ Y_ Z_X、Y、Z、为当前刀位点在工件坐标系中的坐标。
1、G92指令通过设定刀具起点相对于要建立的工件坐标原点的位置建立坐标系。
2、此坐标系一旦建立起来,后序的绝对值指令坐标位置都是此工件坐标系中的坐标值。
例:G92 X20 Y10 Z10其确立的加工原点在距离刀具起始点X=-20,Y=-10,Z=-10的位置上,如图a所示。
(2)、绝对值编程G90与增量值编程G91格式: G90 G00/G01 X— Y — Z —G91 G00/G01 X— Y— Z—注意:铣床编程中增量编程不能用U、W,如果用,就表示为U轴、W轴.例:刀具由原点按顺序向1、2、3点移动时用G90、G91指令编程。
注意:铣床中X轴不再是直径.(3)、工件坐标系选择 G54-G59说明:1、G54~G59是系统预置的六个坐标系,可根据需要选用。
2、该指令执行后,所有坐标值指定的坐标尺寸都是选定的工件加工坐标系中的位置。
1~6号工件加工坐标系是通过CRT/MDI方式设置的。
3、G54~G59预置建立的工件坐标原点在机床坐标系中的坐标值可用MDI方式输入,系统自动记忆。
4、使用该组指令前,必须先回参考点。
5、G54~G59为模态指令,可相互注销。
选择机床坐标系:(4)、G53 --选择机床坐标系编程格式:G53 G90 X~ Y~ Z~;➢G53 指令使刀具快速定位到机床坐标系中的指定位置上,式中X、Y、Z后的值为机床坐标系中的坐标值。
➢例:G53 X-100 Y-100 Z-20➢G53为非模态指令,只在当前程序段有效.(5)、G52 –局部坐标系设定编程格式:G52 X~ Y~ Z~;式中X、Y、Z后的值为局部原点相对工件原点的坐标值。
几个坐标系指令应用举例ZYW XX XY X 5454Y 机机9292Y G G 92543040AX Y 59593030G 59B45152035G 523535CDXY 机床原点M Z 2X2工件原点M机床原点X1Z 1Y2Y1如图所示从A-B-C-D 行走路线 编程如下N01G54 G00 G90 快速移到G54中的A 点N02 G59 将G59置为当前工件坐标系 N03 G00 移到G59中的B 点N04 G52 在当前工件坐标系G59中建立局部坐标系G52 N05 G00 G90 移到G52中的C 点N06 G53 移到G53(机械坐标系)中的D 点 ……二、坐标平面选定坐标平面选择 G17,G18,G19G17 XY 平面 刀具长度补偿值为Z 平面 G18 XZ 平面 刀具长度补偿值为Y 平面 G19 YZ 平面 刀具长度补偿值为X 平面1、坐标平面选择指令是用来选择圆弧插补的平面和刀具补偿平面的。
2、G17、G18、G19为模态功能,可相互注销,G17为缺省值。
直线插补编程1、快速定位指令G00格式:G00 X_Y_Z_其中,X、Y、Z、为快速定位终点,在G90时为终点在工件坐标系中的坐标;在G91时为终点相对于起点的位移量。
(空间折线移动)说明:(1)、G00 一般用于加工前快速定位或加工后快速退刀。
(2)、为避免干涉,通常的做法是:不轻易三轴联动。
一般先移动一个轴,再在其它两轴构成的面内联动。
如:进刀时,先在安全高度Z上,移动(联动)X、Y轴,再下移Z轴到工件附近。
退刀时,先抬Z轴,再移动X-Y轴。
2、直线进给指令G01格式: G01 X _Y_ Z_ F_其中,X、Y、Z为终点坐标,F为进给速度,在G90时为终点在工件坐标系中的坐标;在G91时为终点相对于起点的位移量。
说明:(1) G01指令刀具从当前位置以联动的方式,按程序段中F指令规定的合成进给速度,按合成的直线轨迹移动到程序段所指定的终点。
(2)实际进给速度等于指令速度F与进给速度修调倍率的乘积。
(3)G01和F都是模态代码,如果后续的程序段不改变加工的线型和进给速度,可以不再书写这些代码。
(4)G01可由G00、G02、G03或G33功能注销。
3、例子O1234:G17 G90; (初始化)G54 G00 X0 Y0; (设定工件坐标系)M03 S1000; (主轴正转)G00 Z100.; (刀具下刀)Z5.; (下刀R点)G01 Z-5. F100; (下刀切削深度)G01 X5. Y10.; (原点→A点)G01 X5. Y35.; (A点→B点)G01 X35. Y35.; (B点→C点)G01 X35. Y10.; (C点→D点)G01 X5. Y10.; (D点→A点)G00 X0 Y0; (快速回到原点)G00 Z100.; (快速抬刀)M05; (主轴停止)M30; (程序结束)圆弧插补编程圆弧进给指令 G02 :顺时针圆弧插补G03 :逆时针圆弧插补指令格式:G17 G02 ( G03 ) G90 ( G91 ) X_Y_I_ J_ F_或G17 G02 ( G03 ) G90 ( G91 ) X_Y_ R_ F_G18 G02 ( G03 ) G90 ( G91 ) X_Z_I_ K_ F_或G18 G02 ( G03 ) G90 ( G91 ) X_Z_ R_ F_O ZXG03G02O Y ZG03G02O XYG03G02XZYG19 G02 ( G03 ) G90 ( G91 ) Y_Z_J_ K_ F_或 G19 G02 ( G03 ) G90 ( G91 ) Y_Z_ R_ F_(一)、注明:1、I 指圆弧起点指向圆心的连线在X 轴上的投影矢量与X 轴方向一致为正,相反为负。
2、J 指圆弧起点指向圆心的连线在Y 轴上的投影矢量与Y 轴方向一致为正,相反为负。
3、K 指圆弧起点指向圆心的连线在Z 轴上的投影矢量与Z 轴方向一致为正,相反为负。
4、整圆不能用R 编程,只能用I 、J 、K :a≤1800 R 取正值;a>1800 R 取负值 (二)、指令参数说明:1、圆弧插补只能在某平面内进行。
2、G17代码进行XY 平面的指定,省略时就被默认为是G173、当在ZX (G18)和YZ (G19)平面上编程时,平面指定代码不能省略 (三)G02/G03判断:G02为顺时针方向圆弧插补,G03为逆时针方向圆弧插补。
顺时针或逆时针是从垂直于圆弧加工平面的第三轴的正方向看到的回转方向。
平面圆弧插补(四)编制圆弧程序段例1: 1、大圆弧AB每段圆弧可有四个程序段表示G17 G90 G03 X0 Y25 R-25 F80G17 G90 G03 X0 Y25 I0 J25 F80G17 G91 G03 X-25 Y25 R-25 F80G17 G91 G03 X-25 Y25 I0 J25 F802、小圆弧ABG17 G90 G03 X0 Y25 R25 F80G17 G90 G03 X0 Y25 I-25 J0 F80G17 G91 G03 X-25 Y25 R25 F80G17 G91 G03 X-25 Y25 I-25 J0 F80例2:整圆编程要求由A点开始,实现逆时针圆弧插补并返回A点。
G90 G03 X30 Y0 I-40 J0 F80G91 G03 X0 Y0 I-40 J0 F80例3:O1234:G17 G90; (初始化)G54 G00 X-30. Y-50.;(设定工件坐标系)M03 S1000; (主轴正转)G00 Z100.; (刀具下刀)Z5.; (下刀R点)G01 Z-5. F100; (下刀切削深度)G01 X-30. Y0.; (下刀点→A点)G02 X30. Y0. R30.; (A点→C点)G01 X30. Y-15.; (C点→D点)G03 X15. Y-30. R15;(D点→E点)G01 X-20. Y-30.; (E点→G点)G02 X-30. Y-20. R10.;(G点→H点)G03 X-42. Y-20. R6.; (圆弧切出)G01 X-45.;G00 Z100.; (快速抬刀)G00 X0 Y0; (快速回到原点)M05; (主轴停止)M30; (程序结束)刀具半径补偿功能编程G41:刀具半径补偿左偏置 G42:刀具半径补偿右偏置G40:取消刀具半径补偿格式:G41/G42 G01/G00 X Y D ;G40 G01/G00 X Y ;G41:左刀补(在刀具前进方向左侧补偿),如图 (a);G42:右刀补(在刀具前进方向右侧补偿),如图 (b);X, Y, Z:G00/G01的参数,即刀补建立或取消的终点(注:投影到补偿平面上的刀具轨迹受到补偿);D:G41/G42的参数,即刀补号码,它代表了刀补表中对应的半径补偿值。
G40、G41、G42都是模态代码,可相互注销。
注意:(1)刀具半径补偿平面的切换必须在补偿取消方式下进行(2)刀具半径补偿的建立与取消只能用G00或G01指令,不得是G02或G03刀具长度补偿功能编程格式:G43/G44 G01/G00 Z H ;G49 G01/G00 Z ;G43:刀具长度正补偿G44:刀具长度负补偿G49:取消刀具长度补偿Z:G00/G01的参数,即刀补建立或取消的终点H:刀具长度偏置号例子:O1234;G17 G40 G49 G80 G90;G54 G00 X0 Y0;M03 S1000;G00 X-65. Y-60.;G43 G00 ;Z5.;G01 Z-10. F100;G01 X-65. Y30.;G02 X-55. Y40. R10.;G01 X45. Y40.;G01 Y-20.;G02 X-55. Y-40.;G02 X-65. Y-30. R10.;G03 X-77. Y-30. R6.;G01 X-80.;G40 G00 X-85.;G49 G00 Z100.;X0 Y0;M05;M30;子程序编程(M98、M99)把一个程序中按某一固定顺序重复出现的内容抽出并按一定格式编写,则称为子程序,子程序由主程序或子程序调用指令调出执行,调用子程序的格式如下:M98Pxxxx Lxxxx子程序号调用次数(1-9999)如果省略了重复次数,则认为重复次数为一次。