乙苯生产工艺
乙苯装置工艺流程及生产原理

乙苯装置工艺流程及生产原理第一节催化干气预处理部分生产原理:乙苯烃化催化剂最怕碱性物质,会造成催化剂失活。
而催化干气多采用乙醇胺等碱性物质脱硫技术脱除硫化氢,因此为了防止碱性物质进入烃化反应系统,催化干气首先要经过水洗。
干气中的丙烯会与苯生成丙苯,同时会增加甲苯的生成量,造成苯耗上升增加产品成本,所以需要通过吸收的办法尽可能降低干气中丙烯的含量。
工艺流程叙述:催化干气进装置后进入催化干气水洗罐(D-101)。
该罐具有两个作用,其一是将催化干气进装置时携带的液体除去,另一作用是用水将携带的MEA 除去。
罐内设填料一段,罐底设水洗循环泵(P-101A/B),水洗用水循环使用。
从催化干气水洗罐(D-101)顶部出来的气体依次进入催化干气换热器(E-101)、催化干气过冷器(E-102)与丙烯吸收塔(C-101)塔顶出来的低温催化干气、冷冻水换热,温度降至15℃,从底部进入丙烯吸收塔(C-101)。
吸收剂从丙烯吸收塔顶部进入与催化干气逆向接触,将催化干气中的丙烯绝大部分除去,从丙烯吸收塔顶部出来的催化干气进入催化干气换热器(E-101)与进塔的催化干气换热回收部分冷量后去反应部分。
吸收了丙烯的吸收剂从塔底出来进入贫液-富液换热器(E-103)与贫液换热后进入解吸塔(C-102)。
解吸塔进料进入解吸塔后,塔顶汽相进入解吸塔顶蒸汽发生器(E-106)冷凝冷却,然后进入解吸塔回流罐(D-102),冷凝下来的液体用解吸塔回流泵(P-103A/B)送至解吸塔顶部,未冷凝的气体从解吸塔回流罐顶部出来后依次进入解吸塔顶冷却器(E-107)解吸塔顶气过冷器(E-108)进一步冷凝冷却,然后进入解吸塔顶分液罐(D-103)进行气液分离,冷凝下来的液体用解吸塔顶凝液泵(P-104A/B)送入解吸塔回流罐(D-102),未冷凝的气体出装置。
解吸塔塔底物料用吸收剂循环泵(P-102A/B/C)加压后依次通过贫液-富液换热器(E-103)、贫液过冷器(E-104)冷却,返回丙烯吸收塔塔顶循环使用。
(整理)年产5万吨乙苯工艺设计28963369

年产15万吨乙苯工艺设计With an Annual Output of 150 Thousand Tons of Ethyl-benzene Technology Design目录摘要 (I)Abstract (II)引言 (1)第一章文献综述 (2)1.1乙苯的性质 (2)1.2产品用途 (2)1.3 乙苯在国民经济中的重要性及市场需求 (2)第二章生产工艺流程设计 (3)2.1 由C8芳烃分离乙苯 (3)2.2 苯的烷基化生产乙苯 (3)2.2.1气液相烷基化法 (3)2.2.2气固相烷基化法 (3)2.2.3莫比尔——巴杰尔法(Mobil—Badger) (4)2.3工艺参数的确定 (4)第三章工艺计算 (5)3.1物料衡算 (5)3.1.1原料乙烯进料量计算 (5)3.1.2原料新鲜苯的计算 (6)3.1.3循环苯的计算 (6)3.1.4络合物计算 (6)3.1.5 尾气量的计算 (7)3.1.6 烷基化液量的计算 (8)3.1.7排出的废络合物 (8)3.1.8 机械损失量 (8)3.2.热量衡算 (11)3.2.1烃化塔带入热量的计算 (11)3.2.2 物料带出热的计算 (11)3.2.4烷基化反应器冷凝器负荷及冷却水量的计算 (14)3.2.5 烷基化液冷却器及冷却水 (15)3.3乙苯精馏塔衡算 (15)第四章苯精馏塔的设计表 (17)4.1塔体温度的确定 (17)4.1.1塔顶温度 (17)4.1.2塔底温度确定 (18)4.1.3烷基化液进料温度 (18)4.2回流比及实际板数的确定 (19)4.2.1回流比的确定 (19)4.2.2最小理论板数的确定 (19)4.2.3总板效率 (19)4.2.4实际板数确定 (20)4.3进料板位置的确定 (20)4.4气液相负荷及塔径计算 (20)4.5溢流装置的设计 (23)4.5.1溢流堰长 (23)4.5.2溢流堰高 (23)4.6降液管的设计 (23)4.6.1弓形降液管的宽度和横截面积 (23)4.6.3降液管底隙高度 (24)4.7塔板的布置 (24)4.7.1边缘区宽度确定 (24)4.7.2开孔区面积计算 (24)4.7.3浮阀数计算及其排列 (24)第五章塔板流体力学验算 (26)5.1压降计算 (26)5.2塔板负荷性校核 (27)5.2.1极限雾沫夹带线 (27)5.2.2液泛线 (27)5.2.3降液管负荷上限线 (27)5.2.4液相下限线 (28)5.2.5气液负荷下限线 (28)第六章塔高及塔附件的计算及选型 (29)6.1 塔总体高度 (29)6.2塔体壁厚设计 (29)6.3封头设计及人孔选取 (29)6.3.1封头设计 (29)6.3.2人孔及群座的选取 (29)6.4接管计算 (29)6.4.1进料管 (30)6.4.2塔顶蒸汽管 (30)6.4.3回流管径 (30)6.4.4釜底出料管径 (31)6.4.5再沸气管径 (31)结论 (32)致谢 ............................................................................ 错误!未定义书签。
乙苯制苯乙烯工艺技术流程

乙苯制苯乙烯工艺技术流程乙苯制苯乙烯是一种重要的工业化学反应过程,该过程是通过乙苯经过一系列的化学反应,最终生成苯乙烯。
下面将详细介绍乙苯制苯乙烯的工艺技术流程。
1. 原料准备:乙苯是制取苯乙烯的主要原料,其纯度必须高于99%。
乙苯进入工厂之前首先要经过净化处理,去除其中的杂质,以确保反应的高效进行。
2. 加热塔:将净化后的乙苯进入加热塔,加热塔内部有一系列的加热器,将乙苯加热至适宜的反应温度,通常在500-600°C之间。
3. 顶部冷凝器:从加热塔的顶部冷凝器中出来的气体,经过冷凝作用,变为液体,其中含有苯乙烯和乙苯,通过分离装置分离苯乙烯和乙苯。
4. 初级分离器:初级分离器用来分离顶部冷凝器中的液体混合物,主要分离苯乙烯和乙苯。
苯乙烯较轻,因此会被分离出来,进入下一步反应,而乙苯则会在底部得到收集。
5. 深度分离:由于初级分离器无法完全分离出苯乙烯和乙苯的混合物,还需要经过一系列的深度分离过程。
深度分离过程中,会使用一些特殊的分离剂,通过溶剂萃取、蒸馏或分馏来分离苯乙烯和乙苯。
6. 催化剂反应:将得到的苯乙烯和适量的空气一起进入催化剂反应器中,反应过程中,苯乙烯会发生氧化反应,生成苯乙酮。
7. 活性炭吸附:通过活性炭吸附器,将催化剂反应产生的废气中的有害物质吸附,净化废气,保护环境。
8. 蒸馏和分离:通过蒸馏和分离操作,将催化剂反应产生的混合物中的苯乙酮和乙苯分离开来。
蒸馏可以根据两者的沸点差异,将两种物质分离开来。
9. 后处理和净化:得到的苯乙酮需要经过后处理和净化,去除其中的杂质和有害物质,以提高产品的纯度。
10. 产品收集和储存:经过后处理和净化后,得到的苯乙酮可以直接进行储存或者进行下一步的加工。
以上所述为乙苯制苯乙烯的工艺技术流程。
乙苯制苯乙烯是一个复杂的过程,需要通过多个步骤来完成。
每个步骤都需要严格控制条件,以确保反应的高效和产品的纯度。
同时,化工生产中也需要注重安全和环保,控制废气和废液的排放,以保护环境。
年产8万吨苯烷基化生产乙苯工艺设计范本
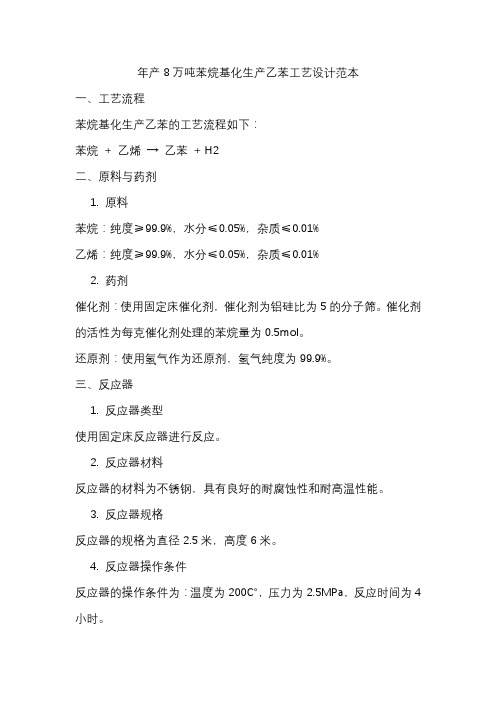
年产8万吨苯烷基化生产乙苯工艺设计范本一、工艺流程苯烷基化生产乙苯的工艺流程如下:苯烷+ 乙烯→ 乙苯+ H2二、原料与药剂1.原料苯烷:纯度≥99.9%,水分≤0.05%,杂质≤0.01%乙烯:纯度≥99.9%,水分≤0.05%,杂质≤0.01%2.药剂催化剂:使用固定床催化剂,催化剂为铝硅比为5的分子筛。
催化剂的活性为每克催化剂处理的苯烷量为0.5mol。
还原剂:使用氢气作为还原剂,氢气纯度为99.9%。
三、反应器1.反应器类型使用固定床反应器进行反应。
2.反应器材料反应器的材料为不锈钢,具有良好的耐腐蚀性和耐高温性能。
3.反应器规格反应器的规格为直径2.5米,高度6米。
4.反应器操作条件反应器的操作条件为:温度为200℃,压力为2.5MPa,反应时间为4小时。
四、分离和纯化反应后得到的产物经过分离和纯化后得到纯乙苯。
1.分离将反应器中的产物进行分离,分离出乙苯和未反应的苯烷。
2.纯化将分离后得到的乙苯进行纯化,纯化过程采用蒸馏法进行,纯度达到99.9%。
五、工艺控制1.反应器温度控制反应器温度采用自动控制系统进行控制,保持温度稳定在200℃。
2.反应器压力控制反应器压力采用自动控制系统进行控制,保持压力稳定在2.5MPa。
3.催化剂活性监测每隔一定时间对催化剂进行检测,确保催化剂的活性保持在标准范围内。
4.产物纯度监测对产物进行定期检测,确保纯度符合标准要求。
六、安全措施1.反应器压力过高时,自动泄压阀会自动开启,确保反应器的安全。
2.反应器温度过高时,自动温度控制系统会自动降低温度,确保反应器的安全。
3.在氢气进入反应器时,必须保证氢气纯度符合要求,以防止发生爆炸事故。
4.在反应过程中,必须保证操作人员的安全,采取必要的防护措施。
乙苯生产工艺流程

乙苯生产工艺流程
《乙苯生产工艺流程》
乙苯是一种重要的有机化合物,广泛用于橡胶、塑料、化妆品等行业。
其生产工艺流程主要分为苯和乙烯的加氢反应,以下是乙苯的生产工艺流程:
1. 原料准备:首先准备苯和乙烯作为生产乙苯的原料,这两种原料通常通过石油提炼或裂解石油得到。
2. 加氢反应:将苯和乙烯送入加氢反应器中,在催化剂的作用下进行加氢反应,生成乙苯。
这个反应需要在一定的温度和压力下进行,控制好反应条件可以提高乙苯的产率。
3. 分离精馏:由于反应生成的产物中可能还含有杂质或未反应的原料,需要进行分离精馏处理。
通过恰当的精馏方法,将乙苯从未反应的原料和其它杂质中分离出来,得到纯净的乙苯产物。
4. 产品脱水:乙苯作为有机溶剂广泛用于化工生产,但其水含量严重影响着产品的质量。
因此,通常需要对乙苯进行脱水处理,降低产品中的水含量。
5. 储存包装:最后将经过处理的乙苯产品进行储存和包装,以便运输到使用场所。
这就是乙苯的生产工艺流程,通过严格控制生产过程和加工工
艺可以得到高纯度的乙苯产品,为相关行业的生产提供了稳定的原料支持。
乙苯生产技术

3 乙烯浓度旳影响
由表2可知,乙烯浓度对催化精馏过程有 影响。干气中乙烯浓度提升,乙烯旳转化 率提升,乙苯选择性降低。这是因为在反 应压力一定旳情况下,干气中乙烯浓度增 长,乙烯分压增大,有利于乙烯在液相中 旳溶解吸收,提升了乙烯旳转化率。又因 为乙烯在液相中旳溶解度增长,继续烷基 化反应速率增大,生成更多旳二乙苯和多 烷基苯等,降低了乙苯旳选择性
4 催化剂
该工艺采用ZSM-5沸石催化剂,完全防止了 AlCl3催化剂带来旳一系列问题。但因为 ZSM-5催化剂旳活性温度较高,所以反应要 在较高温度下进行。在较高温度下,烷基化 反应速率较快,该催化剂对苯和乙烯旳烃化 反应及多乙苯与苯旳反烃化反应均具有较 强旳催化剂活性和良好旳选择性,可达 99.5%。此工艺催化剂用量少,轻易结焦而 失活,但轻易再生,使用寿命长,生产中不存 在环境污染和设备腐蚀问题。
任务点05 经典设备旳选择
乙苯单元由烷基化反应、烷基转移反应和乙苯精馏部分 构成。烷基化反应部分旳任务是在分子筛催化剂旳作用 下使乙烯和苯烷基化生成乙苯、多乙苯等物质。烷基转 移反应部分旳任务则是在分子筛催化剂旳作用下使苯、 多乙苯发生烷基转移反应,生成乙苯。烷基化反应和烷 基转移反应部分旳出料中具有乙苯、多乙苯、重质物及 未反应旳原料苯,都被送到乙苯精馏预分馏塔。由预分 馏塔、苯塔、乙苯塔、多乙苯塔、脱非芳塔将反应产物 分离成苯、乙苯、多乙苯和重质物。其中回收旳苯返回 到烷基化反应器和烷基转移反应器,多乙苯返回到烷基 转移反应器。脱非芳塔则用于脱除进料和反应过程中生 成旳轻组分和轻非芳烃
• 用旳比较多旳是磁力泵和屏蔽泵 另外还有大功率离心泵 反烃化反 应进料泵是高速齿轮泵。
任务点06 乙苯生产中安全、环境保护、节能 措施
1.1应严格监视反应器旳温度、压力,进料苯和多乙苯 中旳水含量应不大于10ppm。反应器开停车应严格 控制开、降温速度;反应器系统旳联锁必须正常投 入使用,定时校验联锁并有统计。
11苯烷基化合成乙苯的生产工艺

苯烷基化合成乙苯的生产工艺目前在工业生产中, 除极少数乙苯来源于重整轻油C 8芳烃馏份抽提外, 其余90%以上是在适当催化剂存在下由苯与乙烯烷基化反应来制取。
其生产工艺有以下几种。
一、 AlCl 3 法传统的AlC13液相法使用AlC13-HCl 催化剂, AlC13溶解于苯、乙苯和多乙苯的混合物中, 生成络和物。
该络和物在烷基化反应器中与液态苯形成两相反应体系, 同时通入乙烯气体,常压下发生烷基化反应,生成乙苯和多乙苯, 同时多乙苯和乙苯发生烷基转移反应,反应中苯的烷基化反应和多乙苯的烷基转移反应在一台反应器中完成。
均相AlCl 3法通过控制乙烯的投料, 使Alcl 3催化剂的用量减少到处于溶解度范围内, 使反应可以在均一的液相中进行,烷基化和烷基转移反应在两个反应器中进行,乙苯收率高,副产焦油少,Alcl 3用量少(仅为传统法的1/3)。
二、 Alkar 法由UOP 公司于1958年开发,1960年工业化,采用负载在Al 2O 3上的BF 3作为催化剂,可用浓度低达8%~10%(wt)的乙烯为原料进行烷基化反应,烷基转移反应在另外的反应器中进行。
其工艺流程如图2。
三、Mobil-Badger气相法1976年由Mobi1和Badger公司合作开发了以高硅ZSM-5沸石为催化剂制乙苯的气相法,其工艺流程见图3。
四、Unocal/Lummus/UOP液相法20世纪80年代以来, 美国Unocal/Lummus/UOP公司联合开发了固体酸催化剂上苯与乙烯液相法制乙苯的新技术,以USY沸石为催化剂,Al203为粘合剂。
烷基化反应器分两段床层,苯与乙烯以液相进行烷基化反应,各床层处于绝热状态。
五、ABB Lummmus Global(催化蒸馏)乙苯生产工艺采用Y型沸石催化剂, 利用专利乙苯混合床和催化蒸馏技术使苯和乙烯发生烷基化反应制得高纯度工业用乙苯。
现代催化干气制乙苯技术工艺进展

现代催化干气制乙苯技术工艺进展摘要乙苯作为重要的化工原料之一,主要用途是生产苯乙烯。
全球绝大部分乙苯都是用苯和乙烯通过烃化反应而得,且几乎都是采用纯乙烯作为原料,进而导致了乙烯成本过高。
伴随我国原油消费量逐年增加,年产含有大量乙烯的催化干气却主要作为燃料使用,不仅造成了资源浪费,也对环境造成破坏。
因此,利用催化干气作为原料,使其中的乙烯与苯反应制成乙苯的生产工艺成为迫切需要。
关键词催化干气;稀乙烯;技术工艺;发展前景引言第三代催化干气制乙苯是我国具有自主知识产权的新型工艺,已得到广泛运用。
它是以催化干气中的稀乙烯作为原料,采用气相烷基化和液相烷基转移反应,实现了催化干气中稀乙烯的最大化利用,同时還配套生产国内紧缺的用于合成聚苯乙烯、丁苯橡胶等的苯乙烯产品。
不仅开拓了催化干气利用的新路子,还大大增加了公司的效益,提升公司竞争力[1]。
1 催化干气制乙苯技术工艺过程及发展分析1.1 烃化和反烃化反应原理(1)生成乙苯:C2H4+C6H6=C6H5C2H5在沸石催化剂上存在Lewis酸中心,吸附干气中乙烯分子,再与苯反应生成乙苯。
(2)生成多乙苯:如:C6H5C2H5+ C2H4=C6H4(C2H5)2乙苯进一步烷基化生成二乙苯、三乙苯等。
(3)多乙苯反烃化:C6H4(C2H5)2+ C6H6=2 C6H5C2H5反烃化反应器中,沸石催化剂上存在Lewis酸中心,吸附多乙苯分子,与苯发生烷基转移反应生成乙苯。
(4)生成丙苯和丁苯:C2H6+ C6H6= C6H5C3H7 C4H8+ C6H6=C6H5C4H9干气中含有少量的丙烯和丁烯,在烃化催化剂上与苯发生烷基化反应,生成丙苯和丁苯。
(5)生成甲苯、二甲苯:非芳烃、乙苯和二甲苯生成甲苯;在Lewis酸中心作用下,乙苯能够异构化生成二甲苯。
1.2 工艺发展分析(1)传统A1C13液相法A1C13液相法将A1C13催化剂与苯均成液相反应状态,在反应器中进行烷基化反应,同时二乙苯与苯发生烷基转移反应。
- 1、下载文档前请自行甄别文档内容的完整性,平台不提供额外的编辑、内容补充、找答案等附加服务。
- 2、"仅部分预览"的文档,不可在线预览部分如存在完整性等问题,可反馈申请退款(可完整预览的文档不适用该条件!)。
- 3、如文档侵犯您的权益,请联系客服反馈,我们会尽快为您处理(人工客服工作时间:9:00-18:30)。
以负载在Al2O3上的BF3为催化剂的反应法
该法以负载在Al2O3上的BF3为催化剂,可用浓度低达8%~10%(质量分数)的 乙烯为原料进行烷基化反应,因此可以用处理后的FCC干气或焦炉尾气为原 料。该反应在100~150°C和2.5~3.5MPa下进行,乙烯和苯的摩尔比控制在 0.15~0.2之间。烷基转移反应在另外的反应器中进行温度为180~230°C。 从两个反应器出来的物料合并后进入提纯系统。 优点:成品的乙苯纯度可达99.9%。该方法主要优点是催化剂活性高、寿 命长、乙苯选择性好、无腐蚀无污染、流程简短、能耗小,可用于低浓度 乙烯的综合利用。 缺点:催化剂制备条件苛刻,费用也较贵,并容易中毒失活。原料在反应前 必须净化,要求H2S、CO2和H2O等杂质的含量小于1×10-6。
生产方法比较分析
乙苯是生产苯乙烯的中间产品,少量的乙苯也用于溶剂、稀释剂以及生 产二乙基苯等。目前在工业生产中,90%以上是在适当催化剂存在下由 苯与乙烯烷基化反应来制取乙苯。
苯和乙烯烷基化是在酸性催化剂存在下进行,若以所用催化剂分类, 可分为三氯化铝(AlCl3)法、BF3—Al2O3法和固体酸法等。液相三 氯化铝法又可分为传统的两相烷基化工艺和单相高温烷基工艺。 AICI3催化剂液相反应法 传统的AlCl3法反应器内反应物和催化剂形成三相,液态芳烃、气态乙 烯和液态的催化剂配合物。催化剂配合物呈红色,与液态芳烃不互溶, 反应时乙烯鼓泡进入含有两个液相的的反应器内,使它们分散混合。 乙烯与苯的摩尔比为0.3~0.35,反应在低于130°C以下及常压进行。
2 乙烯浓度的影响
由表2可知,乙烯浓度对催化精馏过程有影响。干气 中乙烯浓度提高,乙烯的转化率提高,乙苯选择性降低 。这是由于在反应压力一定的情况下,干气中乙烯浓 度增加,乙烯分压增大,有利于乙烯在液相中的溶解吸 收,提高了乙烯的转化率。又由于乙烯在液相中的溶 解度增加,继续烷基化反应速率增大,生成更多的二乙 苯和多烷基苯等,降低了乙苯的选择性
气相法
以高硅ZSM-5沸石为催化剂制乙苯的气相法,对苯和乙烯的烷基化反应及二乙苯
和苯的烷基转移反应均具有较强的活性和良好的选择性。烷基化反应在高温、 中压的气相条件下进行,反应温度370~430°C,反应压力1.42~2.84 MPa,乙烯质量 空速3~5/h。 优点: 该工艺可以用浓乙烯为原料,也可用稀乙烯混合气体为原料,该工艺采用 ZSM-5沸石催化剂,完全避免了AlCl3催化剂带来的一系列问题。该催化剂对苯和
A0202:乙苯生产工艺条件影响因素分析
影响苯与乙烯烷基化反应的因素很多,其中主要有温度、原料组成与配 比、催化剂等。工业上最佳操作点应当是使乙苯收率尽可能大、苯的循 环量和多乙苯的生成量尽可能少。
1.反应温度
由反应原理可知,苯烷基化是放热反应。 从热力学方面分析,在较低温度下有较好的平衡收率,随着温度的
5、催化剂用量
乙基化反应对AlCl3催化剂的纯度要求在97.5~ 98.5%以上,
而且必须无水。
*工艺选择
该工艺采用ZSM-5沸石催化剂,完全避免了AlCl3催化剂 带来的一系列问题。但由于ZSM-5催化剂的活性温度 较高,因此反应要在较高温度下进行。在较高温度下, 烷基化反应速率较快,该催化剂对苯和乙烯的烃化反 应及多乙苯与苯的反烃化反应均具有较强的催化剂 活性和良好的选择性,可达99.5%。此工艺催化剂用量 少,容易结焦而失活,但容易再生,使用寿命长,生产中 不存在环境污染和设备腐蚀问题。
液相法
固体酸催化剂上苯与乙烯液相法制乙苯的新技术,以USY沸石为催化 剂,Al2O3为粘合剂。在232~316°C和2.79~6.99MPa下进行反应,苯的质量空 速2~10/h,苯/乙烯摩尔比4~10。 优点:该法不产生污染环境的废料,反应温度低(一般不超过300°C),乙苯中 二甲苯杂质含量仅为20~40×10-6,远远少于气相法。催化剂的运转周期可 长达一年,对原料纯度要求不高。使用后的催化剂可以进行器外再生,再生条 件缓和,使用寿命可达3年。 缺点:但该法只能用于浓乙烯的烷基化反应,而不适合FCC干气或焦炉尾气 原料。空速低,催化剂用量大,反应压力较高,使能耗增加,设备和操作复杂,。 若以反应状态分类,可分为液相法和气相法两种。
均相AlCl3法
由于传统的法存在着污染腐蚀严重及反应器内两个 液相等问题,1974年Monsanto/ Lummus公司提出了均 相法。该工艺通过控制乙烯的投料,使催化剂的用量 减少到处于溶解度范围内,使反应可以在均一的液相 中进行,提高了乙苯的产率。反应温度为160~180℃, 压力0.6~0.8MPa ,乙烯与苯的摩尔比为0.8。均相法 进料乙烯浓度范围可为15%~100%。当用稀乙烯为 原料时,原料气中C和O均需净化至质量分数约为 5×10-6以下
由于传统的A1Cl3法存在着污染腐蚀严重及反应器内两个液相等 问题,l由于该法在降低成本上有较明显的效果,不少传统的AlCl3 法的装置进行了改造和扩建。
该工艺特点是,烷基化和烷基转移反应在两个反应器中进行,乙 苯收率高,副产焦油少,Alcl3用量少(仅为传统法的1/3)。
但这种方法也只是使设备腐蚀及环境污染问题有所缓解,并未从 根本上得到解决。
催化剂
芳烃烷基化可使用的催化剂种类较多,但它们均属于 酸性催化剂,可以将其大体可分为以下三类: (1)酸性卤化物类 主要有AlBr3、AlCl3、FeCl3、BF3、ZnCl2等。 目前普遍采用的是氯化铝催化剂,并加少量氯化氢以促进反应。 氯化铝催化剂活性很高,可在较低温度(90~100℃)、较低压力 下进行反应,在烷基化反应的同时可使副产的多烷基苯进行脱烷 基反应。氯化铝催化剂的主要缺点是对设备有较强腐蚀性,催化 剂的消耗量较大,原料中水分要求严格。但是,因其价廉易得, 催化活性高,仍被广泛使用。 (2)质子酸类 主要有H2SO4、H3PO4、HF等。最常采用的是磷 酸-硅藻土固体催化剂,具有选择性高、腐蚀性小及三废排放量小 的优点。其缺点是反应温度和压力较高,多烷基苯不能在烷基化 条件下进行脱烷基反应。
四、 生产中安全、环保、节能措施----从物料MSDS数据,分析生产 中可能存在的燃烧爆炸、中毒危险,从而提出相应安全措施;从工 艺角度提出可能解决环保的措施;从系统热平衡分析提出能量回收 利用措施;
A0201 生产工艺路线选择
乙苯性质:
1、理化特性 外观与性状: 无色液体,有芳香气味。 熔点(℃): -94.9 沸点(℃): 136.2 相对密度(水=1): 0.87 相对蒸气密度(空气=1): 3.66 饱和蒸气压(kPa): 1.33(25.9℃)
A0204:乙苯生产中安全、环保、节能措施
烷基化反应系统:
1. 应严格监视反应器的温度、压力,进料苯和多乙苯中的 水含量应小于10ppm。反应器开停车应严格控制开、降温速 度;反应器系统的联锁必须正常投入使用,定期校验联锁 并有记录。
2. 岗位巡检时,应加强对反应器的监视。定期用特殊的红 外测温仪测定反应器有无过热点,发现过热点必须立即紧 急处理;反应器降温用的喷淋水必须保持随时可用,至少 每月试验一次。
升高,乙苯的收率反而下降。同时,在非均相烷基化过程中,温度过高, 不利于乙烯的吸收,催化配合物容易树脂化而遭破坏。
从动力学方面分析,反应温度低,反应速度低,对反应进行不利。 适宜的温度随所用催化剂不同而不同。我组选用ZSM-5催化剂,反应温 度主要满足催化剂发挥催化活性和延长使用寿命的需要,一般为440~ 445℃,过高的反应温度同样会发生生成焦油等副反应,结果导致催化剂因 表面结炭而失活
催化剂络合物配制系统:
1.应保持多乙苯和苯中含水小于10ppm,氯化氢含水小 于50PPppm。
2.受潮分解结块的三氯化铝禁止再用于生产。
3.催化剂配制开车时,尾气吸收系应保持正常开车。
3.脱氢反应系统:
1. 严格控制反应器入口温度。进料蒸汽:乙苯不得低于1.3:1。乙 苯中二乙苯含量小于10ppm,尽量减少开、停车次数,防止催化剂 破碎。反应器最初开车应首先用氮气加热升温,床层温度达200℃以 上时方可通入蒸气。尾气压缩机入口压力应保持为0.0276MPa。反应 器、蒸汽过热炉、尾气压缩机的联锁系统必须正常投用,并定期校 验和记录。 2. 安全阀应每年定压一次,防爆膜应每年检查一次,发现问题要及 时更换或修理。 3. 尾气系统三台在线氧分析器都应正常投用,当有两台指示值超过 1%时联锁应动作,使系统升为正压操作。尾气在负压操作时需排入 火炬系统,不准排入大气。
乙烯的烃化反应及多乙苯与苯的反烃化反应均具有较强的催化剂活性和良好的 选择性,可达99.5%。 此工艺催化剂用量少,容易结焦而失活,但容易再生,使用寿命长,生产中不存在环 境污染和设备腐蚀问题。此外,系统排放的废气和残液均可为装置提供25%的燃 料,输入系统的热量和反应生成的热量中95%可回收。因此,物耗、能耗低。 缺点:在处理FCC干气或焦炉尾气原料时,为了延长催化剂单程寿命,需对原料进 行严格精制(原料气中丙烯、H2S、O2和H2O等杂质均需净化至质量分数均为l0-5 以下)。且该工艺装置投资和能耗相对较高(苯单耗0.749t/t乙苯,乙烯0.168t/t乙 苯)。产物中二甲苯含量较高(约2×10-3)[13,14],影响产品的品质。
闪点(℃): 15 引燃温度(℃): 432 爆炸上限%(V/V): 6.7 爆炸下限%(V/V): 1.0 溶解性: 不溶于水,可混溶于乙醇、醚等多数有 机溶剂。
2、主要用途:
用于有机合成和用作溶剂。主要用于生产苯乙烯, 进而生产苯乙烯均聚物以及以苯乙烯为主要成分的 共聚物(ABS,AS等)。乙苯少量用于有机合成工业, 例如生产苯乙酮、乙基蒽醌、对硝基苯乙酮、甲基 苯基甲酮等中间体。在医药上用作合霉素和氯霉素 的中间体。也用于香料。此外,还可作溶剂使用。
3 压力
由表3可以看出,压力对反应的影响十分显著,即随反应压 力的增加,乙烯转化率明显增加。反应压力增加有利于乙烯 在液相中的溶解吸收,而乙烯在液相中的溶解吸收是整个过 程的控制步骤,所以烷基化反应相应加快,乙烯转化率提高