气动系统的设计计算
我的气动系统设计
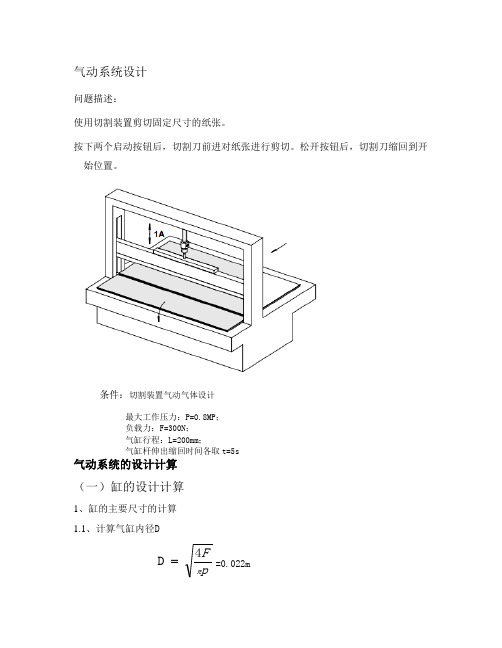
气动系统设计问题描述:使用切割装置剪切固定尺寸的纸张。
按下两个启动按钮后,切割刀前进对纸张进行剪切。
松开按钮后,切割刀缩回到开始位置。
条件:切割装置气动气体设计最大工作压力:P=0.8MP ;负载力:F=300N ;气缸行程:L=200mm ;气缸杆伸出缩回时间各取t=5s气动系统的设计计算(一)缸的设计计算1、缸的主要尺寸的计算1.1、计算气缸内径Dp Fπ4D ==0.022m式中:F---液压缸上的最大外负载;p---液压缸的工作压力;D---缸内径;圆整为标准直径取值:D =25mm1.2、计算活塞杆直径dd=0.707D=17.7圆整为标准直径取值:d =12mmφ---气缸的往复速度比;由表4.4得φ=1.33D---缸内径;d---活塞杆直径;2、气缸的耗气量计算2.1、活塞杆外伸行程的耗气量1qa a 121p p p t L 4D q +=πp---气缸的工作压力;D---缸内径;L---气缸行程;1t ---缸外伸行程的时间;a p ---气缸行程;2.2、活塞杆外伸行程的耗气量2q()a a 2222p p p t L 4d -D q +=πd---活塞杆的直径;2t ---杆内缩行程时间;3、缸的强度计算与校核3.1、缸筒壁厚δ的计算缸筒是液压缸和气压缸中最重要的零件,他承受液体或气体作用的压力,其壁厚须进行计算。
活塞杆受到轴向压缩负载时,为避免发生轴向弯曲,还应进行压杆稳定性验算。
中、高缸一般用无缝缸做缸筒,大多属薄壁筒,即D/d ≥10时,其最薄处的壁厚用材料力学薄壁圆筒公式计算,即:[]σδ2pD ≥ []σ---缸筒材料的许用应力p---气缸的工作压力;δ---薄壁缸筒厚;圆整为标准壁厚取值:δ=5mm ;3.2、活塞杆的稳定性缸保持稳定的条件为:crcr n F F ≤ F---液压缸上的最大外负载;cr F ---活塞杆不产生弯曲变形的临界力;cr n ---稳定性安全系数,一般取cr n =2~6; 由于细长比i m >kl 22cr l i F EJ π≤l---安装长度,其值与安装形式有关,见表4.6;k---活塞杆最小截面的惯性半径,Al k =; m---柔性系数,对钢取m=85;i---由缸支承方式决定的末端系数,其值见表4.6; E---活塞杆材料的弹性模量,对钢取E=a 11p 102.06⨯; J---活塞杆最小截面的惯性矩;A---活塞杆最小截面的截面积;由以上数据得有关公式计算:N 105.020********.062l i F 52411222cr⨯=⨯⨯⨯⨯⨯==πππEJ N 300N 108.36105.0n F F 45cr cr 1>⨯=⨯== 所以稳定性符合要求。
气动系统设计步骤
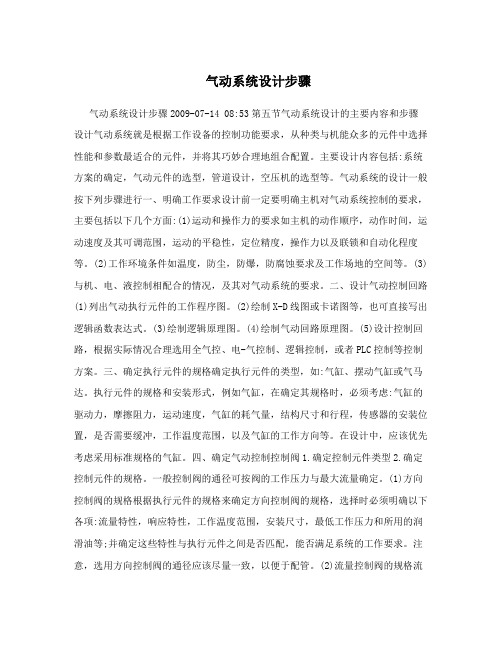
气动系统设计步骤气动系统设计步骤2009-07-14 08:53第五节气动系统设计的主要内容和步骤设计气动系统就是根据工作设备的控制功能要求,从种类与机能众多的元件中选择性能和参数最适合的元件,并将其巧妙合理地组合配置。
主要设计内容包括:系统方案的确定,气动元件的选型,管道设计,空压机的选型等。
气动系统的设计一般按下列步骤进行一、明确工作要求设计前一定要明确主机对气动系统控制的要求,主要包括以下几个方面:(1)运动和操作力的要求如主机的动作顺序,动作时间,运动速度及其可调范围,运动的平稳性,定位精度,操作力以及联锁和自动化程度等。
(2)工作环境条件如温度,防尘,防爆,防腐蚀要求及工作场地的空间等。
(3)与机、电、液控制相配合的情况,及其对气动系统的要求。
二、设计气动控制回路(1)列出气动执行元件的工作程序图。
(2)绘制X-D线图或卡诺图等,也可直接写出逻辑函数表达式。
(3)绘制逻辑原理图。
(4)绘制气动回路原理图。
(5)设计控制回路,根据实际情况合理选用全气控、电-气控制、逻辑控制,或者PLC控制等控制方案。
三、确定执行元件的规格确定执行元件的类型,如:气缸、摆动气缸或气马达。
执行元件的规格和安装形式,例如气缸,在确定其规格时,必须考虑:气缸的驱动力,摩擦阻力,运动速度,气缸的耗气量,结构尺寸和行程,传感器的安装位置,是否需要缓冲,工作温度范围,以及气缸的工作方向等。
在设计中,应该优先考虑采用标准规格的气缸。
四、确定气动控制控制阀1.确定控制元件类型2.确定控制元件的规格。
一般控制阀的通径可按阀的工作压力与最大流量确定。
(1)方向控制阀的规格根据执行元件的规格来确定方向控制阀的规格,选择时必须明确以下各项:流量特性,响应特性,工作温度范围,安装尺寸,最低工作压力和所用的润滑油等;并确定这些特性与执行元件之间是否匹配,能否满足系统的工作要求。
注意,选用方向控制阀的通径应该尽量一致,以便于配管。
(2)流量控制阀的规格流量控制阀包括节流阀和缓冲阀等,其性能对气缸运动的平稳性具有很大的影响。
航空器气动设计的最新计算方法

航空器气动设计的最新计算方法在航空领域,航空器的气动设计一直是至关重要的环节。
随着科学技术的不断进步,新的计算方法层出不穷,为航空器的设计带来了更高的精度和效率。
传统的气动设计方法主要依赖于风洞试验和经验公式。
风洞试验虽然能够提供较为准确的结果,但成本高昂、周期长,而且对于复杂的气动外形,试验结果的准确性也会受到一定的限制。
经验公式则往往基于有限的试验数据和简化的理论模型,适用范围有限。
近年来,计算流体力学(CFD)方法在航空器气动设计中得到了广泛的应用。
CFD 通过数值求解流体流动的控制方程,能够模拟复杂的流场结构和气动现象。
其中,基于雷诺平均NavierStokes(RANS)方程的CFD方法是目前工程应用中最为常见的。
然而,RANS方法在处理一些复杂的流动现象,如大分离流动、湍流过渡等方面仍存在一定的局限性。
为了克服这些局限性,一些新的计算方法应运而生。
其中,脱体涡模拟(DES)和大涡模拟(LES)方法受到了广泛的关注。
DES方法结合了RANS和LES的优点,在近壁面区域采用RANS 模型,而在远离壁面的区域采用LES模型。
这样既能保持RANS方法在近壁面计算的高效性,又能在远离壁面的区域捕捉到大规模的涡结构,提高对分离流动的预测能力。
然而,DES方法在网格分辨率和模型切换等方面仍存在一些问题需要进一步研究和解决。
LES方法直接求解大尺度的涡结构,对湍流的模拟更加准确。
但由于其计算量巨大,目前在全机规模的气动设计中应用还比较有限。
为了提高LES方法的实用性,一些基于LES的混合方法,如分离涡模拟(DVS)和尺度自适应模拟(SAS)等被提出。
除了上述基于湍流模拟的方法,基于优化算法的气动设计方法也取得了重要的进展。
多目标优化算法、遗传算法等被广泛应用于航空器的气动外形优化设计。
这些算法能够在给定的设计空间内自动搜索最优的气动外形,大大提高了设计效率。
在优化过程中,伴随方法的应用也显著提高了计算效率。
气动输送系统设计计算

孙广明①S U N Gu a n g — mi n g ; 付志茹①F U Z h i — r u ; 谢刚①XI E Ga n g ; 张韦①Z HANG We i ; 杨华①Y A N G Hu a ; 李 秀民②L I X i u — m i n ; 李 文雯①L I We n — w e n ; 苗家禄①MI A O J i a — l u
统” 设计 , 实现养 鱼饵料单管道输送作业与远程输送 。 1 环境条件与输送要求 试验地点安排 在本所淡水试验站养殖池塘 ,池塘 为 3 排每排有 2口共计 6口池塘 , 每 口池塘面积约 为 3 . 6亩 , 试 验 区 6口池塘合计面积 为 2 1 . 6 亩。 气 力输送输料管道合计 直线距离 1 4 4米 , 有一处转弯 , 整个管线基本 为水平布置。 本系统通过一 条管道 向 6口池塘输送饲料 , 具体 是在 每 口池塘选定饵料投 喂点设置饵料储存 与投放 设施 , 输料 管道通过饵 料投 喂点时串接三通 分料 阀, 当需要 向某投喂 点输 送饵料 时将分料 阀置于 分料位 置 即可 向该投喂 点输 送饵 料。 因为使用 了“ 干管直通滑块式 阀芯分料 阀” 进行分 料, 串接 的分料 阀在直通状 态B - , t  ̄ t 当于直通 管道 , 不存在 变径和 转向以及 空间的变化问题 。 饵 料的最 大输送量是确定气 力输送 能力的基础数据 , 池塘养殖 生产 规模决定 了饵料 的需求数量 , 由于 在不 同生 产 时期投饵 率不同 , 因此应该按 照饵料需 求量最 大量作 为 输 送 能 力依 据 。池 塘成 鱼 养 殖生 产 水平 每 亩 鱼产 量 在 1 0 0 0 k g 左 右 ,按照 日投饲 率 3 %计 算 , 6口池塘 2 1 . 6亩每 日投放饵 料数量合计 为 6 4 8 k g 。若每 日投饵 3次 , 每次投
气动计算

1 1
0.8536
叶轮机械原理
——轴流压气机气动计算 重热系数的确定(多变压缩功):
lc
* ladk
k
(1 ) H s
z 1 z
叶轮机械原理
——轴流压气机气动计算 各级等熵功分配:
总的等熵功: lc (1 ) H s 252kj/ kg H z
按照功率确定:
ladk
k 1 * k * k RT1 c 1 241.5kJ / kg k 1
若H u 30kJ / kg 则:z 8 ~ 9
叶轮机械原理
——轴流压气机气动计算 2、分配各级的绝热压缩功:
ladk
k 1 * k * k RT1 c 1 241.5kJ / kg k 1
叶轮机械原理
——轴流压气机气动计算 级进口参数确定:
进气道总压损失系数 进口总压 进口密度
P 1 1 RT1
叶轮机械原理
——轴流压气机气动计算 结构参数确定:
由连续方程确定进口面积 确定进口外径 确定平均直径
叶轮机械原理
——轴流压气机气动计算 基元级速度三角形的确定:
确定轴流压气机转速 确定相对进气角 计算出口气流角
叶轮机械原理
——轴流压气机气动计算 其它参数的确定:
计算基元级反动度 校核叶尖速度 计算叶根弯角
叶轮机械原理
——轴流压气机气动计算 计算动叶出口热力学参数:
动叶出口压力 动叶出口温度 动叶出口速度 出口绝对气流角
叶轮机械原理
si
H sm
气动系统管路的设计计算
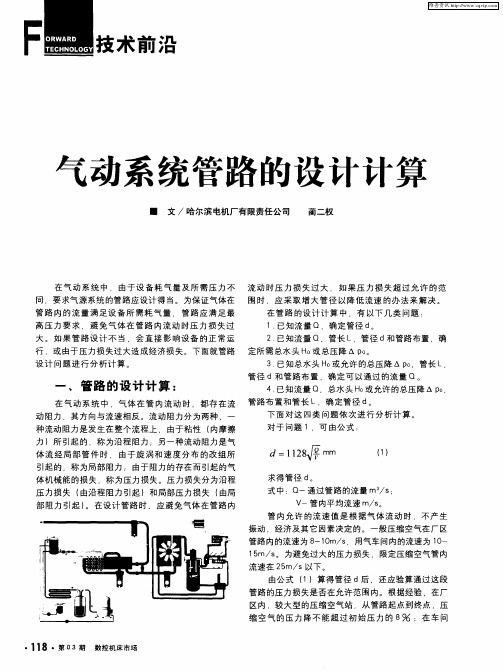
对 于问题 1,可 由公 式 :
体 流经 局部 管件 时 ,由于旋 涡 和速 度 ;由于 阻力的存在而引起的气
d 18 m =1√ m 罟 2
求得管径 d 。
( 1 )
体机械能 的损失 ,称 为压 力损失。压力损失分 为沿程 压 力损 失 ( 由沿程阻力 引起 )和局部 压力损失 ( 由局 部 阻力 引起 ) 。在设计 管路 时 ,应避 免气体在 管路 内
维普资讯
F
.
不能超过供气压 力的 5 。如超过 上述数据 .就 % 压力损失可 由公式 ( 求得 : 2)
再由公式 ( )求得压 力损失 △P 2 。
须 增大 管径 。
对于问题 3 ,流速未知 .而在计算沿程 阻力系数
时 .要求知道流速 。这 时 ,可 用迭代 法逐步逼 近需求
A =h=( ∑h k/ ( P ∑h+ g m . )f 2 )
式 中 A P 总压 力损 失 一
值 。先按 已知管径 d的允许流速 ,选取一个流速值 V, 再由公式 ( 5)确定 雷诺数 R .根据 管件确定相对粗 e
糙度 △ / d.由相应 图表 查得 入值 ,根据管件 形式确
由公式 ( )算得 管径 d后 .还 应验算通过这段 1 管路 的压 力损 失是否在允许范围 内。根据经验 在 厂 区内 ,较 大型的压缩空气站 ,从管路起 点到终 点 ,压
缩 空气 的压 力降 不能 超过 初始 压 力的 8% :在车 间
.
1 .第0 期 数控机床市场 8 1 3
管 路 内的 流量 满足 设备 所需 耗 气量 ,管路 应满 足最
高 压 力要 求 .避免 气体 在管 路 内流 动时 压 力损 失过
气动系统设计
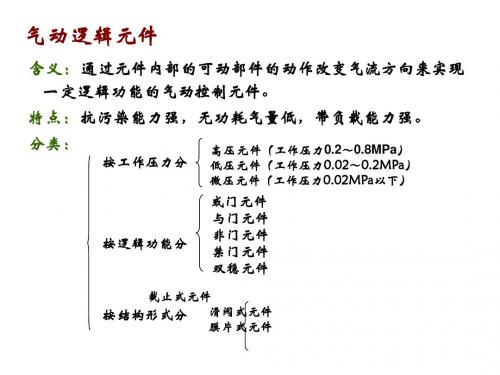
气动回路的设计
1)根据执行元件的数目、动作要求画出方框图或动作
程序,根据工作速度要求确定每个气缸或其它执行元件
双稳元件
原理:有控制
信号a,气源p
从S1输出,撤
除控制信号a, S1保持有输出, 元件记忆了ห้องสมุดไป่ตู้制信号a;当有了控制信号b,则S1关闭,气源 p 从S2输出,撤除控制信号 b ,S2仍保持有输出。
逻辑符号:图b)
气动系统设计
气动基本回路是组成气动控制系统的基本单元,也是设计 气动控制回路的基础气动基本回路分为压力控制、速度控 制和方向控制基本回路。
在一分钟内的动作次数。
2)根据执行元件的动作程序,按本节气动程序控制回 路设计方法设计出气动逻辑原理图,然后进行辅助设计, 此时可参考各种基本回路,设计出气控回路来。 3)使用电磁气阀时,要绘制出电气控制图。
表气动控制方案选择比较
气阀控制 压力(Mpa) 元件响应时间 信号 传递速度 输出功率 流体通道尺寸 耐环境影 响的能力 耐部干扰能力 配管或配线 0.2~0.8 较慢 较慢 大 大 防爆、较耐振、耐灰尘、较耐潮湿 不受辐射、磁力、电场干扰 较麻烦 逻辑元件控制 0.01~0.8 较快 较慢 较大 较大 电--气控制 直动式0~0.8 较慢 最快 大 大 易爆和漏电 受磁场、电场、辐射干扰 容易 先导式0.2~0.8
或门元件 与门元件 非门元件 禁门元件 双稳元件
截止式元件 滑阀式元件 按结构形式分 膜片式元件
气动系统的设计计算

气动系统的设计计算气动系统的设计一般应包括:1)回路设计;2)元件、辅件选用;3)管道选择设计;4)系统压降验算;5)空压机选用;6)经济性与可靠性分析。
以上各项中,回路设计是一个“骨架”基础,本章着重予以说明,然后结合实例对气对系统的设计计算进行综合介绍。
1气动回路1.1气动基本回路气动基本回路是气动回路的基本组成部分,可分为:压力与力控制回路、方向控制(换向)回路、速度控制回路、位置控制回路和基本逻辑回路。
表42.6-1气动压力与力控制回路及特点说明简图说明1.压力控制回路一次压控制回路主要控制气罐,使其压力不超过规定压力。
常采用外控式溢流阀1来控制,也可用带电触点的压力表1′,代替溢流阀1来控制压缩机电动机的启、停,从而使气罐内压力保持在规定压力范围内。
采用溢流阀结构简单、工作可靠,但无功耗气量大;后者对电动机及其控制要求较高二次压控制回路二次压控制主要控制气动控制系统的气源压力,其原理是利用溢流式减压阀1以实现定压控制高低压控制回路气源供给某一压力,经二个调压阀(减压阀)分别调到要求的压力图a 利用换向阀进行高、低压切换图b 同时分别输出高低压的情况差压回路此回路适用于双作用缸单向受载荷的情况,可节省耗气量图a 为一般差压回路图b 在活塞杆回程时,排气通过溢流阀1,它与定压减压阀2相配合,控制气缸保持一定推力2.力控制回路串联气缸增力回路三段活塞缸串联。
工作行程(杆推出)时,操纵电磁换向阀使活塞杆增力推出。
复位时,右端的两位四通阀进气,把杆拉回增力倍数与串联的缸段数成正比气液增压缸增力回路利用气液压缸1,把压力较低的气压变为压力较高的液压,以提高气液缸2的输出力。
应注意活塞与缸筒间的密封,以防空气混入油中1.1.1压力与力控制回路(见表42.6-1)1.1.2换向回路(见表42.6-2)表42.6-2气动换向回路及特点说明简图说明1.单作用气缸换向回路二位三通电磁阀控制回路图a 为常断二位三通电磁阀控制回路。
- 1、下载文档前请自行甄别文档内容的完整性,平台不提供额外的编辑、内容补充、找答案等附加服务。
- 2、"仅部分预览"的文档,不可在线预览部分如存在完整性等问题,可反馈申请退款(可完整预览的文档不适用该条件!)。
- 3、如文档侵犯您的权益,请联系客服反馈,我们会尽快为您处理(人工客服工作时间:9:00-18:30)。
气动系统的设计计算
浏览字体设置:
+
10pt
放入我的网络收藏夹
气动系统的设计计算
气动系统的设计一般应包括: 1)回路设计;
2)元件、辅件选用; 3)管道选择设计; 4)系统压降验算; 5)空压机选用;
6)经济性与可靠性分析。
以上各项中,回路设计是一个“骨架”基础,本章着重予以说明,然后结合实例对气对系统的设计计算进行综合介绍。
1 气动回路
1.1 气动基本回路
气动基本回路是气动回路的基本组成部分,可分为:压力与力控制回路、方向控制(换向)回路、速度控制回路、位置控制回路和基本逻辑回路。
1.1.2换向回路(见表4
2.6-2)
表42.6-2 气动换向回路及特点说明
1.1.3速度控制回路(见表4
2.6-3)
位置停止)
表42.6-4 气动位置控制回路及特点说明
1.1.5 基本逻辑回路(见表4
2.6-5)
实际应用中经常遇到的典型回路简称常用回路。
1.2.1 安全保护回路(见表42.6-6)
1.2.2往复动作回路(见表42.6-7、8)
表42.6-6 气动安全保护回路及特点说明
1.2.3程序动作控制回路
程序动作控制回路(表42.6-8)在实际中应用广、类型多。
下面仅举一个双缸程序动作(A1-B1-B0-A0)为例(表42.6-8)说明。
而不同执行缸以及各种不同程序动作的回路,将在本章第2节中介绍其基本设计方法。
1.2.4同步动作控制回路(见表42.6-9)
表42.6-9 气动同步动作控制回路及特点说明。