《机械加工过程检验作业指导书》
机械加工通用作业指导书【范本模板】
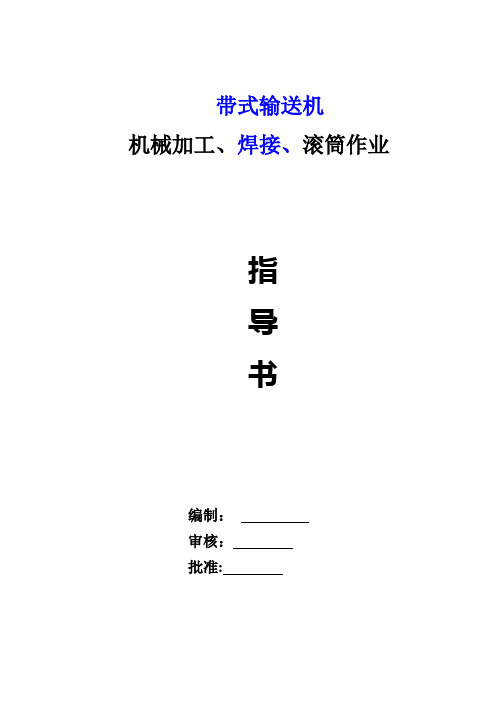
带式输送机机械加工、焊接、滚筒作业指导书编制:审核:批准:山西交城县兴星冶金设备厂机械加工通用作业指导书1、操作者应仔细看清图纸和工艺文件的各项说明,保持图纸和工艺文件的清洁与完整,并应严格按设计图纸、工艺规程和技术标准进行零部件的加工,不得随意自行更改.2、操作者按照工艺要求查看借用的工、夹、量、刀具是否符合工艺及使用要求,若有疑问,应立即与组长或车间生产管理者联系。
3、操作者应将工、夹、量、刀具分别整齐地放置在工具箱上或其它适当的地方,但不准直接放在机床上,并应妥善保管好,不得任意拆卸而改变原来尺寸或形状.4、在加工前,操作者首先应检查、抽查毛坯或经由上道工序加工并和本工序有关的尺寸,以确定余量是否符合工艺要求。
5、操作者应按照工艺规定的定位基面安装零件。
工艺未规定定位基面的,允许操作者自行选择定位基面和装夹方法,但是必须保证加工出来的工件符合图纸和工艺上的尺寸和精度要求。
在装夹工具前,应将夹具和工件清理干净,在定位基面上不得有铁屑、毛刺、污物及磕碰现象。
6、预压紧工件后,应按工艺要求进行工件的校正,若工艺未作出规定时,可按下列方法校正工件:6.1、当在本工序或本工步中加工到成品尺寸,且以后该加工面不再加工,装配时也不再调整或刮研时,可以按定位基面到加工面技术要求的1/3值校正,最后加工完成后应保证图纸中的技术要求。
6.2、在本工序或本工步中加工的加工面以后尚需加工或刮研,则按该加工面下道工序余量的1/3值校正,加工后要按此检验。
6.3、在本工序或本工步中加工的加工面到成品尺寸,以后该加工面不再加工,且图纸、工艺卡片内对该加工面与定位面无任何要求时,加工后应达到通用技术标准。
7、按工艺要求进行压紧,如工艺上无要求,零件压紧时注意压紧力的位置、大小和方向,并允许自加各种辅助支承,以增强刚性。
压紧前与压紧后都要测量,防止变形和磕碰。
8、凡加工面末到成品尺寸而工艺卡片又未规定工序的粗糙度时,粗车、粗铣、粗刨、粗镗和粗插的表面粗糙度应为Ra6.3(△4),磨削前的各种表面粗糙Z应为Rd3.2(△5),粗磨时外围的表面粗糙度应为Ra0.8(△7),平面、轴、孔互为Ral.6(△6);刮研前的加工面应为Ra3.2~Ral.6(△5~△6)。
机械加工与装配作业指导书

机械加工与装配作业指导书第1章机械加工基础知识 (4)1.1 金属切削原理 (4)1.1.1 金属切削概述 (4)1.1.2 切削用量 (4)1.1.3 切削力 (4)1.1.4 刀具材料与结构 (4)1.2 机械加工工艺规程 (4)1.2.1 工艺规程概述 (4)1.2.2 工艺路线的制定 (5)1.2.3 工序内容的制定 (5)1.2.4 切削参数的确定 (5)1.3 机械加工精度与表面质量 (5)1.3.1 机械加工精度 (5)1.3.2 表面质量 (5)1.3.3 提高加工精度和表面质量的方法 (5)1.3.4 加工误差及其控制 (5)第2章常用机械加工方法 (5)2.1 车削加工 (5)2.2 铣削加工 (5)2.3 钻削加工 (6)2.4 镗削加工 (6)第3章数控加工技术 (6)3.1 数控编程基础 (6)3.1.1 数控编程基本概念 (6)3.1.2 编程语言 (6)3.1.3 编程步骤 (6)3.2 数控车削加工 (6)3.2.1 基本原理 (7)3.2.2 工艺参数 (7)3.2.3 编程方法 (7)3.3 数控铣削加工 (7)3.3.1 基本原理 (7)3.3.2 工艺参数 (7)3.3.3 编程方法 (7)第4章特种加工技术 (7)4.1 电火花加工 (7)4.1.1 概述 (7)4.1.2 电火花加工设备 (7)4.1.3 电火花加工工艺 (8)4.1.4 电火花加工应用 (8)4.2 激光加工 (8)4.2.2 激光加工设备 (8)4.2.3 激光加工工艺 (8)4.2.4 激光加工应用 (8)4.3 电子束加工 (8)4.3.1 概述 (8)4.3.2 电子束加工设备 (8)4.3.3 电子束加工工艺 (9)4.3.4 电子束加工应用 (9)第5章零件加工工艺分析 (9)5.1 零件结构工艺性分析 (9)5.1.1 零件结构特点 (9)5.1.2 零件材料 (9)5.1.3 零件加工难度及质量要求 (9)5.2 零件加工工艺路线设计 (9)5.2.1 工艺流程规划 (9)5.2.2 工艺参数设定 (10)5.3 工艺参数选择与计算 (10)5.3.1 切削速度 (10)5.3.2 进给量 (10)5.3.3 切削深度 (10)5.3.4 磨削用量 (10)第6章机械装配基础知识 (11)6.1 装配精度与工艺 (11)6.1.1 装配精度的定义与分类 (11)6.1.2 影响应装配精度的因素 (11)6.1.3 提高装配精度的措施 (11)6.2 装配方法与工具 (11)6.2.1 装配方法的分类与选用 (11)6.2.2 常用装配工具及设备 (12)6.3 装配前的准备工作 (12)6.3.1 零部件检查 (12)6.3.2 装配前的准备工作 (12)6.3.3 装配前的技术准备 (12)第7章常见机械装配工艺 (12)7.1 螺纹连接装配 (12)7.1.1 螺纹连接概述 (12)7.1.2 螺纹连接装配工艺 (13)7.2 键、销连接装配 (13)7.2.1 键、销连接概述 (13)7.2.2 键、销连接装配工艺 (13)7.3 过盈连接装配 (13)7.3.1 过盈连接概述 (13)7.3.2 过盈连接装配工艺 (13)7.4.1 滚动轴承概述 (14)7.4.2 滚动轴承装配工艺 (14)第8章装配质量控制与检验 (14)8.1 装配质量控制措施 (14)8.1.1 建立完善的质量管理体系,保证装配过程遵循相关标准和规范。
(完整版)检验作业指导书

检验作业指导书1.进料检验1.1 定义进料检验又称来料检验,是制止不良物料进入生产环节的首要控制点。
进料检验由IQC执行。
1.2 检测要项IQC在对来货检验前,首先应清楚该批货物的品质检测要项,不明之处要向本部门主管问询,直到清楚明了为止。
在必要时,IQC验货员可从来货中随机抽取两件来货样,交IQC主管签发来货检验临时样品,并附相应的品质检测说明,不得在不明来货检验与验证项目、方法和品质允收标准的情况下进行验收。
1.3 检验项目与方法1.3.1 外观检测一般用目视、手感、限度样品进行验证。
1.3.2 尺寸检测一般用卡尺、千分尺、塞规等量具验证。
1.3.3 结构检测一般用拉力器、扭力器、压力器验证。
1.3.4 特性检测如电气的、物理的、化学的、机械的特性一般采用检测仪器和特定方法来验证。
1.4 检验方式的选择1.4.1 全检方式适用于来货数量少、价值高、不允许有不合格品物料或公司指定进行全检的物料。
1.4.2 免检方式适用于低值、辅助性材料或经认定的免检厂来料以及生产急用而特批免检的,对于后者IQC应跟进生产时的品质状况。
1.4.3 抽样检验方式适用于平均数量较多、经常性使用的物料。
样本大小:批量的10%(不少于20件),允收数AC=0,拒收数RE=1。
1.5 检验结果的处理方式1.5.1 允收经IQC验证,不合格品数低于限定的不合格品个数时,则判为该批来货允收。
IQC应在验收单上签名,盖检验合格印章,通知货仓收货。
若不合格品数大于限定的不良品个数,则判定该送检批为拒收。
IQC应及时填制《IQC退货报告》,经相关部门会签后,交仓库、采购办理退货事宜。
同时在该送检批货品外箱标签上盖“退货”字样,并挂“退货”标牌。
1.5.3 特采特采,即进料经IQC检验,品质低于允许水准。
IQC虽提出“退货”的要求,但由于生产的原因,而做出的“特别采用”的要求。
若非迫不得已,公司应尽可能不启用“特采”。
“特采”必须由总经理批准,可行时还必须征得客户的书面许可。
机械行业质量检验试验规程

检验试验规程一、过程检验:(一)、锻造过程检验:1.锻造前进行模具检验:模具检验以泥型检验为准。
泥型应符合毛坯图纸要求。
表明模具合格,挂合格牌标识。
2.检验项目:a)锻造:错箱、塌沿、多肉、缺材、表面粗糙度、毛坯厚度、折叠等。
b)克刺:刺高、克刺表面平整、毛刺等。
c)整形:弯曲。
d)抛丸:外观(表面应无氧化皮、毛刺等)。
e)入库:按《锻坯检查技术条件》进行规定的检验项目验收。
3.检验方案:3.1.锻造、克刺、整形等工序检验:分为首检、巡检。
a)首件:自检,交检查员确认合格后,可以继续加工。
b)巡检:每班巡检3次。
每次检查3件。
每班次加工完毕。
检查员对该班锻造的产品按5%进行抽查,抽查合格挂牌标识,通知操作者转序。
并填写《工序每日巡检记录》。
3.2.抛丸:完工后按10%进行抽检。
抽查合格挂“合格”牌标识,通知操作者转序。
抽查不合格,挂“不合格”牌标识,通知操作者返工。
结果填写《工序每日巡检记录》。
3.3.入库检验:所有工序完成后,按《锻坯检查技术条件》规定进行检查。
检查结果填写《()综合检查记录》。
(二)机械加工工序检验:机加工工序检查员依据《检验作业指导书》进行工序检验,检验结果填写《工序每日巡检记录》;热处理工序检查员依据《零件热处理验收标准》进行检验检验结果填写《工序每日巡检记录》、《()综合检查记录》(三)成品检验:1、成品检验包括:摇臂成品检验、摇臂轴成品检验、摇臂座成品检验。
成品检验员依据《综检检测项目表》(见附录1)规定的项目进行检验。
2、检验方法:参照《检验作业指导书》。
3、抽样方法:依据GB/T282—规定的抽样方法进行抽样。
祥见表一:表一注释:Ac----合格判定树数;Re----不合格判定数。
上表使用说明:连续10批正常检查合格的批次可以转入放宽检查,放宽检查出现1批次不合格转入正常检查。
四、同时依据《包装验收标准》(附录B)对包装质量进行检验。
5.3 产品发出前检验程序:(1)每批次产品发货前3天,由销售公司通知检查员进行检验。
机加工工艺文件和作业指导书的案例
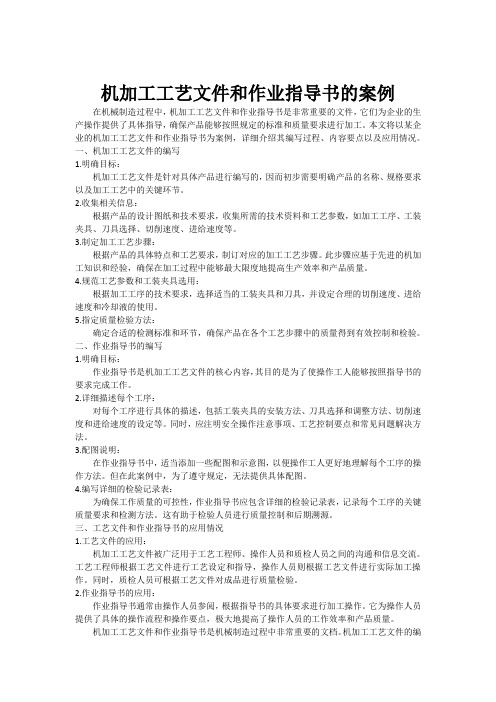
机加工工艺文件和作业指导书的案例在机械制造过程中,机加工工艺文件和作业指导书是非常重要的文件,它们为企业的生产操作提供了具体指导,确保产品能够按照规定的标准和质量要求进行加工。
本文将以某企业的机加工工艺文件和作业指导书为案例,详细介绍其编写过程、内容要点以及应用情况。
一、机加工工艺文件的编写1.明确目标:机加工工艺文件是针对具体产品进行编写的,因而初步需要明确产品的名称、规格要求以及加工工艺中的关键环节。
2.收集相关信息:根据产品的设计图纸和技术要求,收集所需的技术资料和工艺参数,如加工工序、工装夹具、刀具选择、切削速度、进给速度等。
3.制定加工工艺步骤:根据产品的具体特点和工艺要求,制订对应的加工工艺步骤。
此步骤应基于先进的机加工知识和经验,确保在加工过程中能够最大限度地提高生产效率和产品质量。
4.规范工艺参数和工装夹具选用:根据加工工序的技术要求,选择适当的工装夹具和刀具,并设定合理的切削速度、进给速度和冷却液的使用。
5.指定质量检验方法:确定合适的检测标准和环节,确保产品在各个工艺步骤中的质量得到有效控制和检验。
二、作业指导书的编写1.明确目标:作业指导书是机加工工艺文件的核心内容,其目的是为了使操作工人能够按照指导书的要求完成工作。
2.详细描述每个工序:对每个工序进行具体的描述,包括工装夹具的安装方法、刀具选择和调整方法、切削速度和进给速度的设定等。
同时,应注明安全操作注意事项、工艺控制要点和常见问题解决方法。
3.配图说明:在作业指导书中,适当添加一些配图和示意图,以便操作工人更好地理解每个工序的操作方法。
但在此案例中,为了遵守规定,无法提供具体配图。
4.编写详细的检验记录表:为确保工作质量的可控性,作业指导书应包含详细的检验记录表,记录每个工序的关键质量要求和检测方法。
这有助于检验人员进行质量控制和后期溯源。
三、工艺文件和作业指导书的应用情况1.工艺文件的应用:机加工工艺文件被广泛用于工艺工程师、操作人员和质检人员之间的沟通和信息交流。
机加工作业指导书标准范文
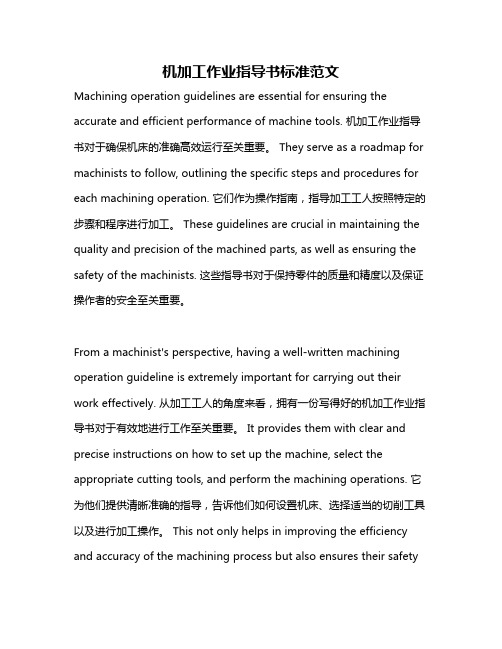
机加工作业指导书标准范文Machining operation guidelines are essential for ensuring the accurate and efficient performance of machine tools. 机加工作业指导书对于确保机床的准确高效运行至关重要。
They serve as a roadmap for machinists to follow, outlining the specific steps and procedures for each machining operation. 它们作为操作指南,指导加工工人按照特定的步骤和程序进行加工。
These guidelines are crucial in maintaining the quality and precision of the machined parts, as well as ensuring the safety of the machinists. 这些指导书对于保持零件的质量和精度以及保证操作者的安全至关重要。
From a machinist's perspective, having a well-written machining operation guideline is extremely important for carrying out their work effectively. 从加工工人的角度来看,拥有一份写得好的机加工作业指导书对于有效地进行工作至关重要。
It provides them with clear and precise instructions on how to set up the machine, select the appropriate cutting tools, and perform the machining operations. 它为他们提供清晰准确的指导,告诉他们如何设置机床、选择适当的切削工具以及进行加工操作。
机械加工工艺基础作业指导书

机械加工工艺基础作业指导书第1章机械加工概述 (3)1.1 机械加工的基本概念 (3)1.2 机械加工的分类与工艺过程 (3)第2章机械加工基础知识 (4)2.1 机械加工材料 (4)2.1.1 金属材料的分类及功能 (4)2.1.2 非金属材料的分类及功能 (4)2.2 机械加工工具与设备 (4)2.2.1 刀具 (5)2.2.2 量具 (5)2.2.3 设备 (5)2.3 机械加工精度与表面质量 (5)2.3.1 加工精度 (5)2.3.2 表面质量 (5)第3章车削加工工艺 (5)3.1 车削加工概述 (6)3.2 车削加工设备与工艺参数 (6)3.2.1 车削加工设备 (6)3.2.2 车削加工工艺参数 (6)3.3 车削加工操作要点 (6)3.3.1 工件安装 (6)3.3.2 刀具选择与安装 (6)3.3.3 加工过程控制 (7)3.3.4 安全操作 (7)第4章铣削加工工艺 (7)4.1 铣削加工概述 (7)4.2 铣削加工设备与工艺参数 (7)4.2.1 铣削加工设备 (7)4.2.2 铣削工艺参数 (7)4.3 铣削加工操作要点 (8)4.3.1 工件装夹 (8)4.3.2 铣刀选择与安装 (8)4.3.3 铣削路径规划 (8)4.3.4 铣削参数设置 (8)4.3.5 加工过程监控 (8)4.3.6 切削液使用 (8)4.3.7 安全操作 (8)第5章钻削加工工艺 (8)5.1 钻削加工概述 (8)5.2 钻削加工设备与工艺参数 (8)5.2.1 钻削加工设备 (8)5.3 钻削加工操作要点 (9)第6章镗削加工工艺 (9)6.1 镗削加工概述 (9)6.2 镗削加工设备与工艺参数 (10)6.2.1 镗削加工设备 (10)6.2.2 镗削工艺参数 (10)6.3 镗削加工操作要点 (10)第7章磨削加工工艺 (10)7.1 磨削加工概述 (11)7.2 磨削加工设备与工艺参数 (11)7.2.1 磨削加工设备 (11)7.2.2 磨削工艺参数 (11)7.3 磨削加工操作要点 (11)第8章齿轮加工工艺 (12)8.1 齿轮加工概述 (12)8.2 齿轮加工设备与工艺参数 (12)8.2.1 齿轮加工设备 (12)8.2.2 齿轮加工工艺参数 (12)8.3 齿轮加工操作要点 (12)8.3.1 齿轮加工前的准备 (12)8.3.2 齿轮加工操作要点 (13)第9章特种加工工艺 (13)9.1 特种加工概述 (13)9.2 常见特种加工方法与设备 (13)9.2.1 电火花加工 (13)9.2.2 激光加工 (13)9.2.3 电子束加工 (13)9.2.4 离子束加工 (14)9.2.5 超声波加工 (14)9.2.6 水射流加工 (14)9.3 特种加工操作要点 (14)9.3.1 电火花加工操作要点 (14)9.3.2 激光加工操作要点 (14)9.3.3 电子束加工操作要点 (14)9.3.4 离子束加工操作要点 (14)9.3.5 超声波加工操作要点 (14)9.3.6 水射流加工操作要点 (15)第10章机械加工工艺规程制定 (15)10.1 工艺规程的基本概念 (15)10.2 工艺规程的制定步骤与方法 (15)10.2.1 制定工艺路线 (15)10.2.2 确定工序内容 (15)10.2.3 选择工艺参数 (15)10.2.5 制定检验标准 (16)10.3 工艺规程的实施与优化 (16)10.3.1 工艺规程的实施 (16)10.3.2 工艺规程的优化 (16)第1章机械加工概述1.1 机械加工的基本概念机械加工是指利用机械力对工件进行切削、塑性变形或组合等加工过程,以达到工件形状、尺寸、表面质量及功能等方面要求的一门技术。
机械加工通用作业指导书(1)word版本

带式输送机机械加工、焊接、滚筒作业指导书编制:审核:批准:山西交城县兴星冶金设备厂机械加工通用作业指导书1、操作者应仔细看清图纸和工艺文件的各项说明,保持图纸和工艺文件的清洁与完整,并应严格按设计图纸、工艺规程和技术标准进行零部件的加工,不得随意自行更改。
2、操作者按照工艺要求查看借用的工、夹、量、刀具是否符合工艺及使用要求,若有疑问,应立即与组长或车间生产管理者联系。
3、操作者应将工、夹、量、刀具分别整齐地放置在工具箱上或其它适当的地方,但不准直接放在机床上,并应妥善保管好,不得任意拆卸而改变原来尺寸或形状。
4、在加工前,操作者首先应检查、抽查毛坯或经由上道工序加工并和本工序有关的尺寸,以确定余量是否符合工艺要求。
5、操作者应按照工艺规定的定位基面安装零件。
工艺未规定定位基面的,允许操作者自行选择定位基面和装夹方法,但是必须保证加工出来的工件符合图纸和工艺上的尺寸和精度要求。
在装夹工具前,应将夹具和工件清理干净,在定位基面上不得有铁屑、毛刺、污物及磕碰现象。
6、预压紧工件后,应按工艺要求进行工件的校正,若工艺未作出规定时,可按下列方法校正工件:6.1、当在本工序或本工步中加工到成品尺寸,且以后该加工面不再加工,装配时也不再调整或刮研时,可以按定位基面到加工面技术要求的1/3值校正,最后加工完成后应保证图纸中的技术要求。
6.2、在本工序或本工步中加工的加工面以后尚需加工或刮研,则按该加工面下道工序余量的1/3值校正,加工后要按此检验。
6.3、在本工序或本工步中加工的加工面到成品尺寸,以后该加工面不再加工,且图纸、工艺卡片内对该加工面与定位面无任何要求时,加工后应达到通用技术标准。
7、按工艺要求进行压紧,如工艺上无要求,零件压紧时注意压紧力的位置、大小和方向,并允许自加各种辅助支承,以增强刚性。
压紧前与压紧后都要测量,防止变形和磕碰。
8、凡加工面末到成品尺寸而工艺卡片又未规定工序的粗糙度时,粗车、粗铣、粗刨、粗镗和粗插的表面粗糙度应为Ra6.3(△4),磨削前的各种表面粗糙Z应为Rd3.2(△5),粗磨时外围的表面粗糙度应为Ra0.8(△7),平面、轴、孔互为Ral.6(△6);刮研前的加工面应为Ra3.2~Ral.6(△5~△6)。