精密与特种加工考试试题13级答案
精密与特种加工复习题全解

华航一、单项选择1.对大型轧辊类零件可方便实现磨损及损伤补救的措施是()A.电铸B.涂镀C.电镀D.化学镀2.可提高电解加工电流密度i的措施是()A.加工电压UR↑B.加工间隙Δ0↑C.电导率σ↓D.进给速度v↓3.在电火花加工中存在吸附效应,它主要影响:( )A.工件的可加工性 B. 生产率 C. 加工表面的变质层结构 D. 工具电极的损耗4.刚玉磨料适合于磨削()A.硬质合金B.钢铁C.金刚石D.有色金属5.用电火花进行精加工,采用()A.宽脉冲、正极性加工B.宽脉冲、负极性加工C.窄脉冲、正极性加工D.窄脉冲、负极性加工6.下列电解加工常用电解液配方中,加工精度最好的是()A.10%NaCl B.10%NaNO3C.20%NaClO3D.20%NaCl7.材料平均去除率最高的方法是()A.电火花线切割加工B.激光加工C.电解加工D.离子束加工8.能提高电解加工精度的措施是()A.减小电解加工间隙B.降低进给进度C.增加电解液温度D.增加电解液浓度9.高功率密度的电子束加工适于( )A.钢板上打孔B. 工件表面合金化C. 电子束曝光D.工件高频热处理10.超声加工变幅杆增幅性能最好的是()A.圆锥形B.对数曲线形C.指数曲线形D.圆轴阶梯形11.下列四个选项中,哪个是离子束加工所具有的特点( )A.加工中无机械应力和损伤B.通过离子撞击工件表面将机械能转化成热能,使工件表面熔化而去除工件材料C.工件表面层不产生热量,但有氧化现象D.需要将工件接正电位(相对于离子源)。
12.下列特种加工方法中最易于实现自动控制的是()A.超声加工B.激光加工C.电解加工D.电铸加工13.电火花加工中利用碳黑膜补偿作用降低电极损耗,必须采用()A.负极性加工B.正极性加工C.单极性加工D.多极性加工14.超精密加工技术能够获得()A.极高的加工精度B.微小尺寸零件C.极高的表面粗糙度D.高质量表面15.游离磨料加工可用于()A.砂带磨削B.油石研磨C.精密珩磨D.精密抛光16.超精密加工机床中主轴部件结构应用最广泛的是:( )17.要在金刚石上加工出Ф0.05mm的小孔,可采用的加工方法是()A.电火花加工B.超声加工C.线切割加工D.电解加工18.在电火花加工中,脉冲宽度减小将引起电极相对损耗()A.增加B.先小后大C.不变D.减小19.超声加工下列材料生产率最低的是()A.紫铜板B.工业陶瓷C.淬火钢D.压电陶瓷20.激光打小孔要增加孔深,应该()A.改变发散角B.改变焦点位置C.改变能量分布D.采用激光多次照射21.利用金属离子阴极沉积方法来进行加工的方法是()A.离子束加工B.电解加工C.电铸D.等离子体加工22.在金刚石晶体各晶面中,磨削率的高、低为()A.(111)最高,(110)最低B.(100)最高,(110)最低C.(100)最高,(111)最低D.(110)最高,(111)最低23.一般来说,电解加工时工具电极是:( )A.低损耗B.高损耗C.基本无损耗D负损耗24.金刚石刀具与刀体固定方法中,错误的是()A.机械夹固B.粉末冶金法C.制作金刚石整体刀具D.钎焊25.关于电解加工电解液的流动方式,论点错误的是( )A.正向流动夹具结构较简单,但加工精度较差B.反向流动夹具结构较复杂,但加工精度较好C.反向流动夹具结构较简单,但加工精度较差D.侧向流动适用于薄板类零件的加工二、填空题26.精密和超精密加工机床主轴轴承的常用形式有(液体静压轴承)和(空气静压轴承)。
精密加工与特种加工简答题及答案

三、简答题(30分,每题6分)1、特种加工与传统切削加工方法在加工原理上的主要区别有哪些?(6分)答:1)特种加工是用机械能以外的其他能量去除工件上多余的材料,以达到图样上全部技术要求。
(2分)2)特种加工打破传统的硬刀具加工软材料的规律,刀具硬度可低于被加工材料的硬度。
(2分)3)特种加工过程中,工具与工件不受切削力的作用。
(2分)2、特种加工的本质特点是什么?(6分)答:1)特种加工所使用的工具硬度可以低于被加工材料的硬度;(2分)2)特种加工不依靠机械能,而是主要用其他能量(如电、化学、光、声、热等)去除材料(2分)3)特种加工过程中工具和工件之间不存在显著的机械切削力。
(2分)3、电火花加工必须解决的问题有哪些?(6分)答:1、由于在电火花加工的不同阶段,金属蚀除的速度不同,因此必须具有工具电极的自动进给和调节装置,使工具和工件之间保持合适的放电间隙;(2分)2、火花放电必须是瞬时的、单极性、脉冲放电;(2分)3、火花放电必须在有一定绝缘性能的液体介质中进行。
(2分)4、什么是电火花加工的机理?火花放电过程大致可分为哪四个连续的阶段?(6分)答:电火花加工的机理是指电火花加工的物理本质,即火花放电时,电极表面的金属材料是如何被蚀除下来的这一微观物理过程。
(2分)火花放电过程大致可分为如下四个阶段:1、极间介质的电离、击穿,形成放电通道;(1分)2、介质热分解、电极材料融化、气化,热膨胀;(1分)3、电极材料的抛出;(1分)4、极间介质的消电离;(1分)5、电火花加工的优缺点有哪些?(6分)答:电火花加工的优点主要体现在以下四个方面:1、特别适合任何难以进行切削加工的材料;(1分)2、可以加工特殊或形状复杂的表面和零件;(1分)3、工具与工件不接触,作用力极小;(1分)4、脉冲放电时间短,冷却作用好,加工表面热影响小。
(1分)但存在以下缺陷:1、主要用于加工金属等导电材料;(1分)2、加工速度较慢(需进行预加工,去除大部分余量)且存在一定的电极损耗。
精密与超精密加工试题和答案

1.精密和超精密加工的精度范围分别为多少?超精密加工包括哪些领域?答:精密与超精密加工的精度随着科学技术的发展不断提高,以目前的加工能力而言,精密加工的精度范围是0.1~1μm,加工表面精度Ra在0.02~0.1μm之间。
超精密加工的精度高于0.1μm,加工表面精度Ra小于0.01μm。
超精密加工领域:1)超精密切削,2)超精密磨削,3)超精密研磨和抛光。
2.超精密切削对刀具有什么要求?天然单晶金刚石、人造单晶金刚石、人造聚晶金刚石和立方氮化硼刀具是否适用于超精密切削?答:超精密切削对刀具的要求:1) 刀具刃口锋锐度ρ刀具刃口能磨得极其锋锐,刃口圆弧半径ρ极小,能实现超薄切削厚度,减小切削表面弹性恢复和表面变质层。
ρ与切削刃的加工方位有关,普通刀具5~30μm,金刚石刀具<10nm;从物理学的观点,刃口半径ρ有一极限。
2) 切削刃的粗糙度。
切削时切削刃的粗糙度将决定加工表面的粗糙度。
普通刀刃的粗糙度Ry0.3~5 μm,金刚石刀具刀刃的粗糙度Ry0.1~0.2 μm,特殊情况Ry1nm,很难。
3) 极高的硬度、极高的耐磨性和极高的弹性模量,保证长的刀具寿命。
4) 刀刃无缺陷,足够的强度,耐崩刃性能。
5) 化学亲和性小、与工件材料的抗粘结性好、摩擦系数低,能得到极好的加工表面完整性。
单晶金刚石硬度极高。
自然界最硬的材料,比硬质合金的硬度高5~6倍。
摩擦系数低。
除黑色金属外,与其它物质的亲和力小。
能磨出极锋锐的刀刃。
最小刃口半径1~5nm。
耐磨性好。
比硬质合金高50~100倍。
导热性能好,热膨胀系数小,刀具热变形小。
因此,天然单晶金刚石被一致公认为理想的、不能代替的超精密切削刀具。
人造单晶金刚石已经开始用于超精密切削,但是价格仍然很昂贵。
金刚石刀具不适宜切黑色金属,很脆,要避免振动而且价格昂贵,刃磨困难。
人造聚晶金刚石无法磨出极锋锐的切削刃,切削刃钝圆半径ρ很难达到<1μm,它只能用于有色金属和非金属的精切,很难达到超精密镜面切削。
精密特种加工复习题(新2015)
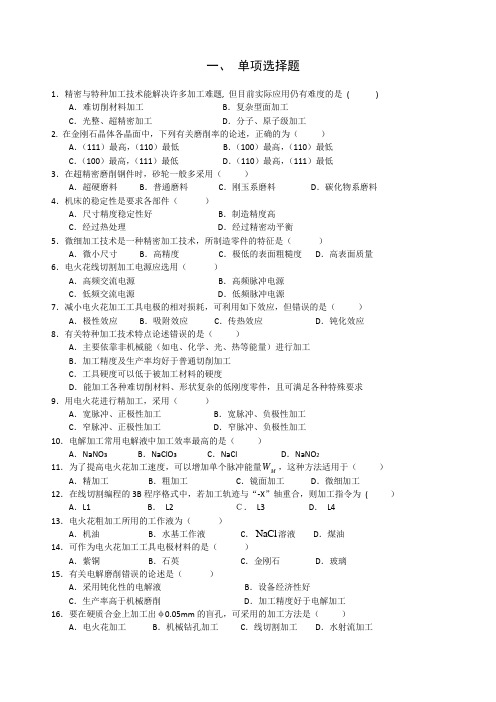
一、单项选择题1.精密与特种加工技术能解决许多加工难题, 但目前实际应用仍有难度的是( ) A.难切削材料加工B.复杂型面加工C.光整、超精密加工D.分子、原子级加工2. 在金刚石晶体各晶面中,下列有关磨削率的论述,正确的为()A.(111)最高,(110)最低B.(100)最高,(110)最低C.(100)最高,(111)最低D.(110)最高,(111)最低3.在超精密磨削钢件时,砂轮一般多采用()A.超硬磨料B.普通磨料C.刚玉系磨料D.碳化物系磨料4.机床的稳定性是要求各部件()A.尺寸精度稳定性好B.制造精度高C.经过热处理D.经过精密动平衡5.微细加工技术是一种精密加工技术,所制造零件的特征是()A.微小尺寸B.高精度C.极低的表面粗糙度D.高表面质量6.电火花线切割加工电源应选用()A.高频交流电源B.高频脉冲电源C.低频交流电源D.低频脉冲电源7.减小电火花加工工具电极的相对损耗,可利用如下效应,但错误的是()A.极性效应B.吸附效应C.传热效应D.钝化效应8.有关特种加工技术特点论述错误的是()A.主要依靠非机械能(如电、化学、光、热等能量)进行加工B.加工精度及生产率均好于普通切削加工C.工具硬度可以低于被加工材料的硬度D.能加工各种难切削材料、形状复杂的低刚度零件,且可满足各种特殊要求9.用电火花进行精加工,采用()A.宽脉冲、正极性加工B.宽脉冲、负极性加工C.窄脉冲、正极性加工D.窄脉冲、负极性加工10.电解加工常用电解液中加工效率最高的是()A.NaNO3B.NaClO3C.NaCl D.NaNO2W,这种方法适用于()11.为了提高电火花加工速度,可以增加单个脉冲能量MA.精加工B.粗加工C.镜面加工D.微细加工12.在线切割编程的3B程序格式中,若加工轨迹与“-X”轴重合,则加工指令为( )A.L1 B.L2 C.L3D.L413.电火花粗加工所用的工作液为()A.机油B.水基工作液C.NaCl溶液D.煤油14.可作为电火花加工工具电极材料的是()A.紫铜B.石英C.金刚石D.玻璃15.有关电解磨削错误的论述是()A.采用钝化性的电解液B.设备经济性好C.生产率高于机械磨削D.加工精度好于电解加工16.要在硬质合金上加工出φ0.05mm的盲孔,可采用的加工方法是()A.电火花加工B.机械钻孔加工C.线切割加工D.水射流加工17.以下加工方法中,属于去除材料加工的是( )A.化学镀B.离子注入C.电铸D. 电抛光18. 有关超声加工的特点,错误的是()A.特别适合于硬脆材料 B.生产率较高C.超声机床结构简单 D.加工应力及变形小19.加工透明光亮的玻璃制品,可以采用的工艺是()A.激光B.电解C.电火花D.电子束20.加工弯孔、曲面,可以采用的工艺是()A.激光B.电子束C.等离子体D.超声加工21.有关金刚石刀具特性,错误的是()A.极高的硬度B.极高的耐磨性C.易于重磨D.可超微量切削22.属于固接磨料的磨削方法是()A.精密砂轮磨削B.精密抛光C.精密研磨D.化学抛光23.与弹性变形微量进给装置相比,采用压电和电致伸缩传感器微量进给装置可以()A.提高微进给精度B.实现自动微量进给C.提高进给稳定性D.实现高的重复精度24.超精密切削时用的单晶金刚石刀具,其修光刃做成圆弧刃的目的是()A.易于对刀B.刀具制造简单C.减少表面粗糙度D.增强刀具强度25.下列四个选项中,硬度最高的磨料是()A.白刚玉B.棕刚玉C.金刚石微粉D.碳化硅26.有关特种加工错误的论述是:()A.特种加工可提高材料可加工性B.特种加工能缩短新产品的试制周期C.特种加工可改变零件典型加工路线D.特种加工能取代普通切削加工27.要在金刚石上加工出φ0.05mm的小孔,可采用的加工方法是()A.电火花加工B.激光加工C.线切割加工D.电解加工28.电火花粗加工所用的工作液为()A.机油B.水基工作液C.煤油D.NaCl水溶液29.以下加工方法中,属于复合加工的是( )A.离子镀B.镜面加工C.微细加工D. 电解磨削30.减小电火花加工工具电极的相对损耗,可以采取的措施为()A.增加工件导热系数B.增加脉宽C.采用正极性加工D.增加脉冲间隔W,这种方法适用于()31.为了提高电火花加工速度,可以增加单个脉冲能量MA.精加工B.粗加工C.镜面加工D.微细加工32.在线切割编程的3B程序格式中,若加工轨迹与“-X”轴重合,则加工指令为( )A.L1 B.L2 C.L3D.L433.电火线切割加工所用的工作液为()A.机油B.乳化液C.NaCl溶液D.煤油34.可作为电火花加工工具电极材料的是()A.紫铜B.石英C.金刚石D.玻璃35.有关电解磨削错误的论述是()A.采用钝化性的电解液B.设备经济性好C.生产率高于机械磨削D.加工精度好于电解加工36.要在硬质合金上加工出φ0.05mm的盲小孔,可采用的加工方法是()A.电火花加工B.机械钻孔加工C.线切割加工D.水射流加工37.以下材料比较适合超声加工的是()A.紫铜B.低碳钢C.陶瓷D.合金钢38. 有关超声加工的特点,错误的是()A.特别适合于硬脆材料B.生产率较高C.超声机床结构简单D.加工应力及变形小39.加工金刚石表面小孔,可以采用的工艺是()A.激光B.电解C.电火花D.线切割加工40.加工弯孔、曲面,可以采用的工艺是()A.激光B.电子束C.等离子体D.超声加工41.金刚石晶体的各向异性表现为()A.金刚石晶体的各个晶面的硬度不一样,110晶面的硬度最高B.金刚石晶体的各个晶面的耐磨性不一致,110晶面的磨削率最低,最不容易磨损C.金刚石晶体的各个晶面的面网密度不一样,110晶面的面网密度最小D.金刚石晶体的各个晶面的耐磨性不同,同一个晶面上不同方向上的耐磨性不一样42.下述有关超精密切削对刀具的要求正确的是()A.无需修整B.刃口半径大C.与工件材料抗粘接性好D.刀具为整体结构43.超精密加工机床中采用的T型总体布局为:主轴作Z向运动,进给系统作X向运动,因而其主轴的驱动方式是()A.B与C两种方式都可B.电动机通过柔性联轴器驱动主轴C.采用内装式同轴电动机驱动D.电动机通过带传动驱动44.超硬磨料砂轮目前主要指()A.墨碳化硅砂轮和绿碳化硅砂轮B.白刚玉砂轮C.棕刚玉砂轮D.金刚石砂轮和立方氮化硼砂轮45.精密研磨主要用于()A.减小表面粗糙度B.提高尺寸精度C.减小形状误差D.改善表面性能46.下列加工方法中,材料平均去除率最高的方法是()A. 电火花加工B.超声加工C.电解加工D.电子束加工47.用电火花进行精加工,采用()A.宽脉冲、正极性加工B.宽脉冲、负极性加工C.窄脉冲、正极性加工D.窄脉冲、负极性加工48.可提高电解加工电流密度i的措施是( )∆A.加工电压U↑B.加工间隙↑C.电阻率ρ↑ D. 进给速度v↓49.以下材料最易于电解加工的是()A.聚晶金刚石B.硬质合金C.碳钢D.铸铁50.在电火花加工中,脉冲宽度增加将引起电极相对损耗()A.增加B.先小后大C.不变D.减小51.有关电火花线切割加工的论述错误的是()A.单脉冲能量W M↑,则Ra↑t↑,则加工速度v↑,Ra↑B.脉宽iC.电极丝愈细,则相对损耗愈小D.开路电压U↑,加工间隙Δ↑52.电火花线切割加工电源一般选用()A.高频交流电源B.高频脉冲电源C.低频交流电源D.低频脉冲电源53.下列加工工艺中,利用金属离子阴极沉积方法来进行成形加工的方法是()A.离子束加工B.电解加工C.等离子体加工D.电刷镀54.以下材料最适合超声加工的是()A.铸铁B.高碳钢C.中碳钢D.石英、玻璃55.有关提高电解加工精度的途径错误的是()NaNO等钝化性电解液A.采用小间隙加工B.采用3C.增加电解液浓度D.提高进给速度v56.电解磨削与机械磨削相比较,错误的的观点是()A.可提高加工表面质量B.砂轮磨损量小C.生产率较高D.可取代后者57.加工条件确定后,电解加工蚀除速度与电极间隙之间的比例关系是()A.指数B.双曲线C.直线D.对数曲线58.为了获得较大的振幅,设计制造变幅杆时,应使其长度等于()A.λ2/3 B.2/λC.4/λD.3/λ59.影响超声加工零件表面质量最显著的因素是()A.变幅杆结构B.系统共振频率C.工具进给压力D.磨料粒度60.在下列特种加工方法中,比较易于自动控制的是()A.超声加工B.电解磨削C.电解加工D.电火花加工61.精密与超精密机床主轴的轴承常采用的形式是()A.空气动压轴承B.液体静压轴承C.滚动柱子轴承D.滚动向心球轴承62.以下加工方法中,属于特种加工的是( )A. 精密抛光B. 精密研磨C. 超精密车削D. 离子刻蚀63.以下加工方法中,属于复合加工的是( )A.离子镀B. 电解磨削C.微细加工D. 镜面加工64.精密抛光主要用于()A.减小粗糙度B.改善表面性能C.减小形状误差D.提高尺寸精度65.电火花成形精加工一般所用的工作液为()A.机油B.电解质溶液C.煤油D.蒸馏水66.用电火花进行零件粗加工,须采用()A.宽脉冲、正极性加工B.宽脉冲、负极性加工C.窄脉冲、正极性加工D.窄脉冲、负极性加工67.降低电火花加工工具电极的损耗要充分利用几个效应,但下述的()除外。
精密与特种加工技术试题库及参考答案

精密与特种加工技术试题库及参考答案一、名词解释:1. 极性效应在电火花加工中, 把由于正负极性接法不同而蚀除速度不同的现象叫极性效应。
2. 线性电解液如NaCl电解液, 其电流效率为接近100%的常数, 加工速度v L和与电流密度i的曲线为通过原点的直线(v L=ηωi), 生产率高, 但存在杂散腐蚀, 加工精度差。
3. 平衡间隙(电解加工中)当电解加工一定时间后, 工件的溶解速度vL和阴极的进给速度v相等, 加工过程达到动态平衡, 此时的加工间隙为平衡间隙Δb 。
4. 快速成形技术是一种基于离散堆积成形原理的新型成形技术, 材料在计算机控制下逐渐累加成形, 零件是逐渐生长出来的, 属于“增材法”。
5. 激光束模式激光束经聚焦后光斑内光强的分布形式。
二、判断题:01.实验研究发现, 金刚石刀具的磨损和破损主要是由于111晶面的微观解理所造成的。
(√)02. 电解加工时由于电流的通过, 电极的平衡状态被打破, 使得阳极电位向正方向增大(代数值增大)。
(√)03. 电解磨削时主要靠砂轮的磨削作用来去除金属,电化学作用是为了加速磨削过程。
(×)04. 与电火花加工、电解加工相比, 超声波加工的加工精度高, 加工表面质量好, 但加工金属材料时效率低。
(√)05. 从提高生产率和减小工具损耗角度来看, 极性效应越显著越好, 所以, 电火花加工一般都采用单向脉冲电源。
(√)06. 电火花线切割加工中, 电源可以选用直流脉冲电源或交流电源。
(×)07. 阳极钝化现象的存在, 会使电解加工中阳极溶解速度下降甚至停顿, 所以它是有害的现象,在生产中应尽量避免它。
(×)08. 电子束加工是利用电能使电子加速转换成动能撞击工件, 又转换成热能来蚀除金属的。
(√)09.电火花线切割加工中, 电源可以选用直流脉冲电源或交流电源。
(×)10. 电火花加工是非接触性加工(工具和工件不接触), 所以加工后的工件表面无残余应力。
特种加工考题及标准答案
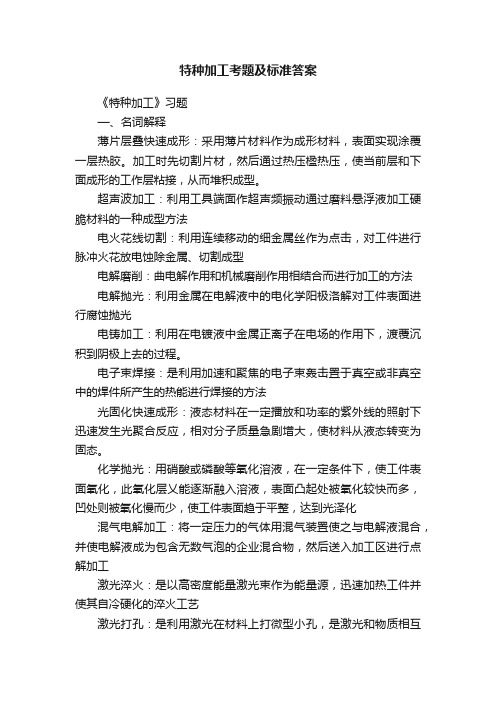
特种加工考题及标准答案《特种加工》习题—、名词解释薄片层叠快速成形:釆用薄片材料作为成形材料,表面实现涂覆一层热胶。
加工时先切割片材,然后通过热压楹热压,使当前层和下面成形的工作层粘接,从而堆积成型。
超声波加工:利用工具端面作超声频振动通过磨料悬浮液加工硬脆材料的一种成型方法电火花线切割:利用连续移动的细金属丝作为点击,对工件进行脉冲火花放电蚀除金属、切割成型电解磨削:曲电解作用和机械磨削作用相结合而进行加工的方法电解抛光:利用金属在电解液中的电化学阳极洛解对工件表面进行腐蚀抛光电铸加工:利用在电镀液中金属正离子在电场的作用下,渡覆沉积到阴极上去的过程。
电子束焊接:是利用加速和聚焦的电子束轰击置于真空或非真空中的焊件所产生的热能进行焊接的方法光固化快速成形:液态材料在一定播放和功率的紫外线的照射下迅速发生光聚合反应,相对分子质量急剧增大,使材料从液态转变为固态。
化学抛光:用硝酸或磷酸等氧化溶液,在一定条件下,使工件表面氧化,此氧化层乂能逐渐融入溶液,表面凸起处被氧化较快而多,凹处则被氧化慢而少,使工件表面趋于平整,达到光泽化混气电解加工:将一定压力的气体用混气装置使之与电解液混合,并使电解液成为包含无数气泡的企业混合物,然后送入加工区进行点解加工激光淬火:是以高密度能量激光束作为能量源,迅速加热工件并使其自冷硬化的淬火工艺激光打孔:是利用激光在材料上打微型小孔,是激光和物质相互作用的热物理过程离子溅射沉积:利用离子溅射使工件表面沉积镀膜的方法离子刻蚀:利用离子轰击作用,对材料表面进行刻蚀的过程铝合金微弧氧化:在电解液中高圧脉冲电场作用下铝合金表面于不同时间段的形成陶瓷层磨料流加工:利用一种含磨料的半流动状态的粘弹性磨料介质在一定压力强迫再被加工表面上流过,由磨料颗粒的刮削作用去除工件表面微观不平材料的工艺方法水射流切割:利用高压高速水流对工件的冲击力作用来去除材料特种加工:泛指用电能、热能、光能、电化学能、化学能、声能及特殊机械能等能量达到出去或增加材料的加工方法涂镀加工:是在金属工件表面局部快速电化学沉积金属的技术二、填空通过从工件上去除材料或向工件表而添加材料,以获得具有要求的(尺寸)(表面质量)(形状)的加工方法,称为加工。
特种加工考试题(附有答案)(修改)

1.试述特种加工的特点及所能解决的主要加工问题,应该如何正确处理传统加工和特种加工工艺之间的关系?答:特点主要有:①不是主要依靠机械能,而是利用其它的能量(如电能、热能、化学能、光能、声能等)去除工件材料;②工具的硬度可以低于被加工工件材料的硬度,有些根本不需要工具;③加工过程中工具和工件之间不存在显著的切削力。
可以解决:①高硬度、高强度、高韧性、高脆性等各种难加工材料的加工问题;②精密、微细、形状复杂零件的加工问题;③薄壁、弹性等低刚度零件的加工问题。
传统加工是指使用刀具进行的切削加工和磨削加工,是行之有效的实用加工方法,而且今后仍然占主导地位。
但是随着难加工的新材料、复杂表面和有特殊要求的零件越来越多,传统加工工艺必然难以适应。
所以可以认为特种加工工艺是传统加工工艺的补充和发展,特种加工工艺可以在特定的条件下取代一部分传统加工工艺,但不可能取代和排斥主流的传统加工工艺。
2.什么叫电火花加工中的极性效应?如何在生产中利用极性效应?答:在电火花加工中,即使电极材料相同,但正、负电极上的蚀除速度仍是不同的,把由于正负极性接法不同而蚀除速度不同的现象叫极性效应。
在短脉宽的脉冲加工时,电子轰击是主要的,正极蚀除量大于负极;在长脉宽的脉冲加工时,离子轰击是主要的,负极蚀除量大。
从提高生产率和减小工具损耗角度来看,极性效应越显著越好。
如用交变脉冲电流加工时,单个脉冲的极性效应便相互抵消,增加了工具的损耗,因此,电火花加工一般都采用单向脉冲电源。
一般在用短脉宽做精加工时,应将工件接正极,称正极性加工;在用长脉宽做粗加工时,应将工件接负极,称负极性加工。
3.电子束加工、离子束加工和激光加工各自的工作原理和应用范围如何?各有什么优缺点?答:三者都适合于精密、微细加工,但电子束、离子束加工需在真空中进行,因此加工表面不会被氧化、污染,特别适合于“洁净”加工。
电子束加工是基于电能使电子加速转换成动能,在撞击工件时动能转换成热能使材料熔化、气化而被蚀除,主要用于打孔、切割、焊接、热处理等。
特种加工考试题(附有答案)
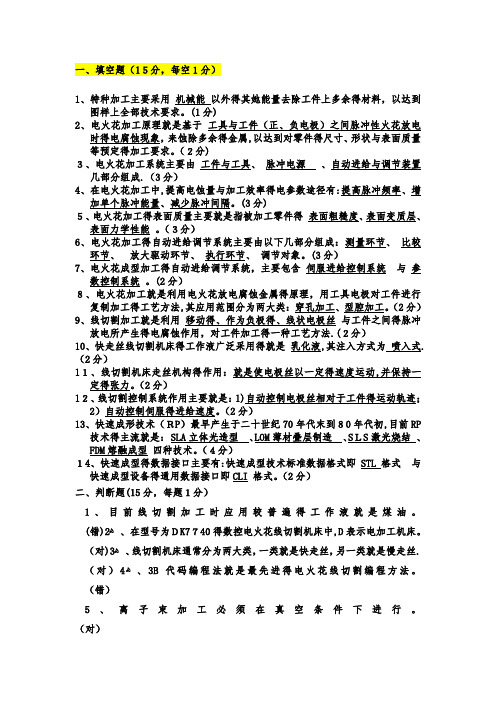
一、填空题(15分,每空1分)1、特种加工主要采用机械能以外得其她能量去除工件上多余得材料,以达到图样上全部技术要求。
(1分)2、电火花加工原理就是基于工具与工件(正、负电极)之间脉冲性火花放电时得电腐蚀现象,来蚀除多余得金属,以达到对零件得尺寸、形状与表面质量等预定得加工要求。
(2分)3、电火花加工系统主要由工件与工具、脉冲电源、自动进给与调节装置几部分组成.(3分)4、在电火花加工中,提高电蚀量与加工效率得电参数途径有:提高脉冲频率、增加单个脉冲能量、减少脉冲间隔。
(3分)5、电火花加工得表面质量主要就是指被加工零件得表面粗糙度、表面变质层、表面力学性能。
(3分)6、电火花加工得自动进给调节系统主要由以下几部分组成:测量环节、比较环节、放大驱动环节、执行环节、调节对象。
(3分)7、电火花成型加工得自动进给调节系统,主要包含伺服进给控制系统与参数控制系统。
(2分)8、电火花加工就是利用电火花放电腐蚀金属得原理,用工具电极对工件进行复制加工得工艺方法,其应用范围分为两大类:穿孔加工、型腔加工。
(2分)9、线切割加工就是利用移动得、作为负极得、线状电极丝与工件之间得脉冲放电所产生得电腐蚀作用,对工件加工得一种工艺方法.(2分)10、快走丝线切割机床得工作液广泛采用得就是乳化液,其注入方式为喷入式.(2分)11、线切割机床走丝机构得作用:就是使电极丝以一定得速度运动,并保持一定得张力。
(2分)12、线切割控制系统作用主要就是:1)自动控制电极丝相对于工件得运动轨迹;2)自动控制伺服得进给速度。
(2分)13、快速成形技术(RP)最早产生于二十世纪70年代末到80年代初,目前RP技术得主流就是: SLA立体光造型、LOM薄材叠层制造、SLS激光烧结、FDM熔融成型四种技术。
(4分)14、快速成型得数据接口主要有:快速成型技术标准数据格式即STL格式与快速成型设备得通用数据接口即CLI 格式。
(2分)二、判断题(15分,每题1分)1、目前线切割加工时应用较普遍得工作液就是煤油。
- 1、下载文档前请自行甄别文档内容的完整性,平台不提供额外的编辑、内容补充、找答案等附加服务。
- 2、"仅部分预览"的文档,不可在线预览部分如存在完整性等问题,可反馈申请退款(可完整预览的文档不适用该条件!)。
- 3、如文档侵犯您的权益,请联系客服反馈,我们会尽快为您处理(人工客服工作时间:9:00-18:30)。
大连理工大学研究生试卷
课程名称:精密与特种加工
学号
姓名:
考试时间:13年11月15日
《精密与加工技术》试题
一.必答题 1. 目前精密和超精密加工的精度范围分别为多少?
答:(1)目前超精密加工技术是指加工尺寸、形状精度达到亚微米级,加工表面粗糙度达到纳米级的加工技术。
在某些领域已经延伸到纳米尺度范围,其加工精度已接近纳米级,表面粗糙度已经达到0.1nm 级,并且正向原子级加工精度逼近。
其中,超精密切削的加工精度高于0.01μm ,表面粗糙度在0.02~0.005μm 之间;超精密磨削的加工精度达到或高于0.1μm ,表面粗糙度在0.025~0.003μm 之间;超精密抛光的加工精度可达数纳米,加工表面粗糙度可达0.1nm 级。
(2)精密加工的加工精度为0.1~1μm ,加工表面粗糙度为0.3~0.03μm ;其中精密磨削的加工精度约为1μm ,表面粗糙度为0.025μm 。
2. 超精密切削对刀具有什么要求?
答:(1)刀具刃口锋锐度ρ小,以实现超薄切削,减小切削刃表面的弹性恢复和表面变质层;
(2)极低的切削刃粗糙度,0.1~0.2y R m μ=,以减少刀具刃口误差复映的影响,获得超光滑表面;
(3)极高的硬度与耐磨性,极高的弹性模量,以保证刀具具有极高的寿命及很高的尺寸耐用度;
(4)足够的强度,刃口无缺陷,耐崩刃,以抵抗切削时晶粒内部强大的分子、原子间结合力;
(5)化学亲和力小,和工件材料的抗粘结性好、摩擦系数低,以得到极好的加工表面完整性。
3. 超精密磨削主要用于加工哪些材料?为什么超精密磨削一般多采用金刚石砂轮?
答:(1)超精密磨削的加工对象有:黑色金属以及陶瓷、玻璃等硬脆材料。
(2)一方面,由于超精密磨削是一种超微量去除加工方式,其切削厚度极薄,磨粒的切削深度甚至小于晶粒的尺寸,使得磨削过程在晶粒内部进行,这就要求磨削力大于晶粒内部极大的原子、分子结合力,这样磨粒所承受的切应力非常大甚至趋近于被磨削材料的剪切强度极限,这就要求磨粒具有较高的抗剪切能力;另一方面,由于磨削过程中所产生的高温、高压作用,又要求磨粒在高温下具有较好的硬度、强度保持性。
对于普通的磨料,在高温、高压与高剪切力作用下,磨粒会迅速磨损或崩裂,加工表面质量严重恶化;相反,由于超硬磨料砂轮具有耐磨性好、寿命高,磨削温度低、散热性能好,加工表面质量好,磨削效率高,热稳定性好、与铁族元素亲和力低、化学稳定性好等优点,可用来加工各种高硬度、高脆性金属与非金属材料。
因此,在超精密磨削中多选用人造金刚石、立方氮化硼等超硬磨料砂轮。
4. 固结磨料加工与游离磨料加工相比有什么特点?
答:(1)游离磨料加工是基于三体摩擦磨损原理,工艺参数多,加工过程不稳定,
磨料运动没有明确轨迹,材料的去除量很难预测;而固结磨料加工是两体摩擦磨损原理,工艺变量少,加工过程相对稳定,具有可重复性,容易实现自动化控制;(2)游离磨料加工时,抛光液中的游离磨料分布在工件与抛光垫之间的所有区域,工件上较低部位也同样受到抛光作用,往往需要较大去除量才能达到全局平坦化;而固结磨料加工只有固结在抛光垫上凸出部位的磨粒才会与工件接触部位发生作用,具有很高的选择性,且由于接触区域小,接触压力大,去除速率增加,只需较小去除量,就可达到平坦化;
(3)游离磨料加工过程中,磨料会堵塞在软质抛光垫内,使其容屑及排屑能力变差,需不断修整湿润抛光垫,此外,抛光后一部分磨料还会镶嵌在薄膜层表面,不易清洗;而固结磨料加工操作过程简单,没有抛光浆料及悬浮微粒的处理问题,也没有更换修整抛光垫的问题,因此,正常加工的时间较长;
(4)游离磨料加工时由于磨料在工件与抛光垫之间不均匀分布,易引起碟形过抛等缺陷;而固结磨料加工具有抛光自停功能,有效地减小各种表面缺陷;(5)固结磨料加工的材料去除率是游离磨料加工的3倍,其平坦化速率高;(6)游离磨料加工过程中磨料、抛光垫磨损严重,成本高;而固结磨料加工的磨损率很低,利用率高,有效减少了杂质微粒对抛光表面的污染,加工表面易清理,废液处理简单,可有效降低成本。
5.简述精密磨削获得高精度和低粗糙度表面的机理。
答:((1)砂轮的选择与修整:精密磨削所选用砂轮主要以容易产生和保持微刃及其等高性为原则,砂轮经过精细修整之后,使其表面磨粒具有等高性及微韧性,因此,磨削之后工件表面留下的磨削痕迹极其微细,且残留高度小;
(2)微刃的微切削作用:采用较小的修整速度与修整深度对砂轮进行修整,易得到高度一致的微切削刃。
这样,无数个微切削刃对砂轮进行微细切削便形成了小粗糙度的表面;
(3)微刃的滑擦、挤压、抛光作用:刚修整完的砂轮表面切削刃较为锋利,切削作用强,随着磨削时间的增加,一方面砂轮表面磨粒变钝,切削作用减弱,挤压,滑擦、抛光作用增强;另一方面,磨削区温度升高,金属表面软化。
因此,切削作用所形成的凸峰就在钝化磨粒的挤压、滑擦作用下被碾平,进一步降低表面粗糙度;
(4)无火花磨削:使磨床各相关部件的弹性变形得以恢复,进一步提高精度、降低工件的表面粗糙度。
6. 超精密加工中为什么需要采用微量进给装置?常用的微量进给装置有哪些类型?
答:(1)在超精密机床和超精密加工中,为使机床微位移的分辨力进一步提高;为进行机床和加工误差的在线补偿,以提高加工的形状精度;为进行某些特殊的非轴对称表面的加工,都需要使用微量进给装置。
高精度微量进给装置现在已成为超精密机床的一个重要的关键装置,重要的机床附件。
(2)现在用的微量进给装置有多种结构形式,多种工作原理,归纳起来有下面6种类型:机械传动或液压传动式,弹性变形式,热应变式,流体膜变形式,磁致伸缩式,电致伸缩式。
根据精密和超精密微量进给装置的要求,上述6种类型中,仅有弹性变形式和电致伸缩式微量机构比较适用,并比较成熟。
尤其是电致伸缩微量进给装置,可以进行自动化控制,有较好的动态特性,可以用于误差在线补偿。
二.选答题
14. 论述磨料射流加工技术的原理和特点,结合实例分析其在精密加工领域的应用。
答:(1)原理:磨料射流加工是以一定的压力,强迫含有磨料的介质通过被加工表面,利用黏弹性介质中的磨粒的切削作用,有控制的去除工件材料,实现对工件表面光整精加工的目的。
磨料射流加工过程相当于用软砂轮紧密的贴合在零件表面上移动,在强制移动中切削被流动的粘性磨料包容带走。
图为磨料射流加工原理图,工件安装在夹具内,夹具夹持在上下对置的上下两个磨料室之间。
工作时,填满在下磨料室内的粘性磨料在活塞的挤压下,被迫流过工件的通道而进入上磨料室,然后由上磨料室的活塞向下挤压,使磨料介质从工件的通道从新返回下磨料室内。
这样循环往复,具有一定的流量,流速和压力的磨料对工件表面和边角不断进行磨削,以达到加工的目的。
特点:○1适用范围由于粘性磨料是一种具有半固态流动性的物体,具有可塑性,又具有弹性,它可以适应各种复杂表面的抛光和去毛刺,如各种型孔,型面,齿轮,交叉孔,喷嘴小孔,液压部件,各种磨具等,所以它的适用范围是很广的,几乎能加工所有的金属材料,也能加工陶瓷,硬质塑料等。
○2加工效率与传统作业相比磨料射流加工效率高,可以同时加工多个孔道,缝隙,或边,对一些小型零件,可以多件同时加工,效率可以大大提高。
○3表面质量加工后的表面粗糙度与原始状态和磨料粒度有关,一般可以降低为加工前的1/10,最低的粗糙度Ra可以达到0.025微米的镜面。
磨料流动加工可以去除在0.025mm深度的表面残余应力,可以去除前面工序(如电火花加
工,激光加工)形成的表面变质层和其他的表面缺陷。
○4加工精度磨料射流加工不能修正零件的形状误差。
切削均匀性可以保持在被切削量的10%以内,不会破坏零件原有的形状精度。
由于去除量很少,可以达到较高的尺寸精度。
(2)磨料射流加工可用于边缘光整,倒圆角,去毛刺,抛光和少量的表面材料去除,特别适合用于难以加工的内部通道的抛光和去毛刺,从软的铝到韧性的镍合金材料均可以进行磨料射流加工。
磨料射流加工已经用于硬质合金拉丝模,挤压模,拉伸摸,粉末冶金模,叶轮,齿轮,燃料旋流器等的抛光和去毛刺,还用于去除电火花加工,激光加工或者渗氮处理这类热能加工产生的不希望有的变质层。
实例分析:磨料射流与超声波加工复合形成超声流动抛光。
黏弹性磨料在作超声振动的工具中心受挤压并从口中流出,其流动受到工具和工件的限制,流动与振动的复合运动使磨粒划擦工件表面而产生抛光作用。
通过与CNC装置相结合,该方法可以抛光复杂的三维型腔,仅适用于敞开型的表面。
参考文献:
[1] Chu Xiangfeng. Investigation on the electrochemical-mechanical polishing of NiP substrate of hard disk. Rare Metal Materials and Engineering.V ol.40.No.11.2011.
[2] 杨清文,廖振方,刘本立,磨料射流切割技术及其应用展望,机械制造,No.1,1997.
[3] 薛胜雄等,高压水射流技术与应用,北京:机械工业出版社,1998.
[4] 王银珍. 蓝宝石衬底的化学机械抛光技术的研究. 人工晶体学报.Vol.33.No.3.2004.
[5] 储向峰. 化学机械抛光在光学晶体加工中的应用. 金刚石与磨料磨具工程.Vol.32.No.1.2012.
[6] 余剑锋. 新型化学机械抛光垫和抛光液的研究. 华南理工大学.2010.
[7] 宋拥军,温效康,梁志强,磨料水射流切割与激光等离子切割的比较分析,高压水射流,l994年合刊,总第49期.
[8] 杨清文,淹没和非淹没下前混合磨料射流的动力特性及切割特性[博士论文],中国重庆,1998.。