逐板计算法
第五节 理论板数的求法
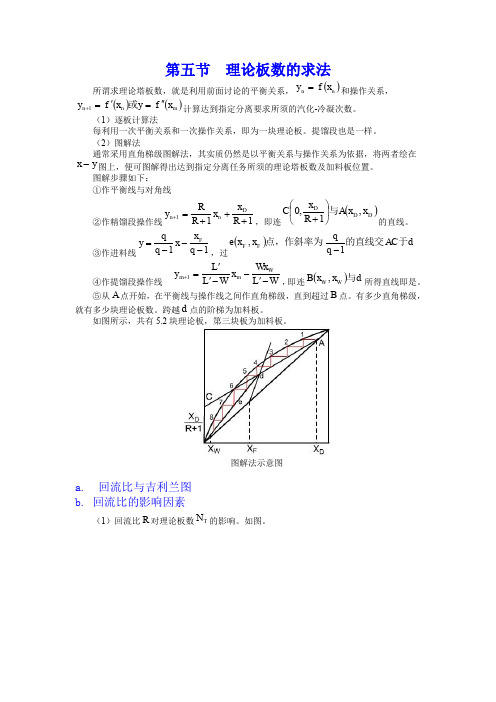
第五节 理论板数的求法所谓求理论塔板数,就是利用前面讨论的平衡关系,()n n x f y =和操作关系,()()m n n x f y x f y ''='=+或1计算达到指定分离要求所须的汽化-冷凝次数。
(1)逐板计算法每利用一次平衡关系和一次操作关系,即为一块理论板。
提馏段也是一样。
(2)图解法通常采用直角梯级图解法,其实质仍然是以平衡关系与操作关系为依据,将两者绘在y x -图上,便可图解得出达到指定分离任务所须的理论塔板数及加料板位置。
图解步骤如下: ①作平衡线与对角线②作精馏段操作线111+++=+R x x R R y D n n ,即连()D D D x x A R x C ,1,0与⎪⎭⎫ ⎝⎛+的直线。
③作进料线11---=q x x q qy F,过()d AC q q x x e F F 于的直线交点,作斜率为1,- ④作提馏段操作线W L Wx x W L L y W m m -'--''=+1,即连()d x x B W W 与,所得直线即是。
⑤从A 点开始,在平衡线与操作线之间作直角梯级,直到超过B 点。
有多少直角梯级,就有多少块理论板数。
跨越d 点的阶梯为加料板。
如图所示,共有5.2块理论板,第三块板为加料板。
图解法示意图a. 回流比与吉利兰图b. 回流比的影响因素(1)回流比R 对理论板数T N 的影响。
如图。
回流比对T N 的影响↑+↓1R x R D ,,操作线靠近平衡线,↑T N 反之,↓+↑1R x R D ,,操作线远离平衡线,↓T N 即 T N 正比于R 1(2)回流比对设备费与操作费的影响 ()D R D L V 1+=+=↑↑V R ,,塔直径↑,冷凝器↑,蒸馏釜↑ 设备费↑↓↑T N R ,,塔高下降,设备费↓↑↑V R ,,冷却水量↑,加热蒸汽量↑, 操作费↑须选一个合适回流比R ,使总费用最省。
理论塔板数的计算(4)

在直角坐标系中绘出y-x图(图略)。
根据精馏段操作线方程式(1),找到 a(0.9,0.9),C(0,0.3)点,联接ac即得到精馏段 操作线。
根据式(2)提馏段操作线,通过 b(0.0667,0.0667),以1.5为斜率作直线bq,即为 提馏段操作线。
从a点开始在平衡线与操作线之间绘直 角梯级,直至
加料过晚
加料过早
q
q
图6-39 加料过晚与加料过早
f e
图6-40 适宜的加料位置
最优加料板位置: x xq
应注意的是:
当某梯级跨越两操作线交点q时(此梯级为 进料板),应及时更换操作线,因为对一定的分 离任务,此时所需的理论板数最少,这时的加料 板为最佳加料板。
加料过早或过晚,都会使某些梯级的增浓程 度减少而使理论板数增加。
解: (1) 根据苯的回收率计算塔顶产品流量:
D F xF 0.9 80 0.4 32kmol / h
xD
0.9
由物料恒算计算塔底产品的流量和组成:
W F D 80 32 48kmol / h
xW
FxF DxD W
80 0.4 32 0.9 48
0.0667
已知回流比R=2,所以精馏段操作线方程为:
2)塔顶全凝器不相当于一块塔板(没有分离; 即进一个汽相出一个液相);塔底为相当于一块 理论板的再沸器(进一个液相出一个液相和一个 汽相);
3)泡点进料(q=1,两操作线交点xq=xF,用来 判别加料板位置。
2、方法: 从塔顶到塔底计算。
精馏段:
xD y1 平衡 x1 操作 y2 平衡 x2 xn xq
f
加料过早
e
图6-38 理论板数图解法示意图
7-4 理论塔板数的计算、进料热状况参数q

L L Hm,V Hm,F
F
Hm,V Hm,L
令q Hm,V Hm,F Hm,V Hm,L
使原料从进料状况变为 饱和蒸汽的摩尔焓变 原料由饱和液体变为饱 和蒸汽的摩尔焓变
化工原理----精馏
L L Hm,V Hm,F q
作业
化工原理----精馏
x x2 x1 xD 1
化工原理----精馏
讨论(图解法)
♫ 优点:简明清晰,便于分析影响因素 ♫ 缺点:计算不够精确
化工原理----精馏
♫(2)梯级的意义
n-1 Xn-1
n xn
n+1
yn-1 yn yn+1
yn yn+1
Xn+1
xn
Xn-1
梯级跨度越大(操作线与平衡线的偏离程度越大),表 示每块理论板的增浓程度越高,则所需理论板数越少。
F
Hm,V Hm,L
L L qF
由上式和进料板 V V (1 q)F
物料衡算,得
q
液化分数
通式
化工原理----精馏
☼2、各种进料热状况下的q值
♫(1)过冷液体进料 q>1
LV F
♫(2)饱和液体进料 q =1
LV F
L V
过冷液体进料
L V
饱和液体进料
化工原理----精馏
♫(3)汽液混合进料 0<q<1
V
♫(4)饱和蒸汽进料 q=0
F
♫(5)过热蒸汽进料 q<0
L V
过热蒸汽进料
化工原理----精馏
小结
☼ 1、逐板计算法求理论塔板数 ☼ 2、用图解法求理论塔板数
精馏过程工艺参数的确定(理论塔板数计算)
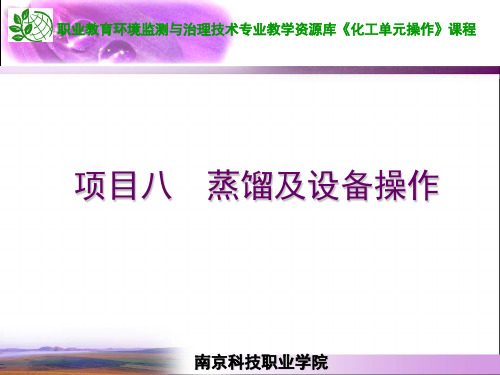
(不包括塔釜) (包括塔釜)
2、图解法 图解法求理论塔板数的基本原
理与逐板计算法相同,所不同的 是用相平衡曲线和操作线分别代 替相平衡方程和操作线方程。用 图解法求理论塔板层数的具体步 骤如下:
(1)绘相平衡曲线 (2)绘操作线 绘出精馏段 操作线和提馏段操作线
(3)绘直角梯级 从(xD,xD)点开始,在精馏段操作线 与平衡线之间绘水平线与垂直线构成直角梯级,当梯级跨 过两段操作线交点d时,则改在提馏段操作线与平衡线之间 作直角梯级,直至梯级的垂线达到或跨过(xW,xW)点为止。 梯级总数即为所需的理论塔板数(包括塔釜)。
职业教育环境监测与治理技术专业教学资源库《化工单元操作》课程
项目八 蒸馏及设备操作
南京科技职业学院
项目八:精馏及设备操作
任务2:精馏过程工艺参数的确定 ---理论塔板数计算 回流比计算
南京科技职业学院 化学工程系
一、理论塔板数计算
(一)理论塔板概念 若汽液两相能在塔板上充分接触,使离
开塔板的汽液两相温度相等,且组成互为平 衡,则称该塔板为理论塔板。
❖ 试用(1)逐板计算法,(2)图解法分别求出所 需的理论板层数及进料板位置。
(三)实际塔板数确定 全塔效率 在指定的分离条件 下,所需的理论塔板 数NT(不包括塔釜) 与实际塔板数N之比 称为全塔效率,用符
号ET表E示T 。N即NT
实际塔板数:
N NT ET
L
泡罩塔塔板效率关系曲线
y3
xn-1
精馏段操作线方程
yn
yn
相平衡方程求
xn≤ xd
直到xn xd(xd为两段操作线交点坐标x数值)时,说明第n 层板为加 料板,该板应属于提馏段。因此精馏段所需理论板数为n -1块。
理论塔板数的计算

理论塔板数的计算一、逐板计算法精馏段操作线方程: 提馏段操作线方程: 相平衡方程: 或第一板:第二板:…… 第m 板:第m+1板: (1)11+++=+R x x R R y D n n w m m x R f x R R f y 1111+--++=+nn n x x y )1(1-+=ααnn n y y x )1(--=ααD, V, L, xD F,xx y m m-逐板计算示意图 111)1(y y x --=ααDx y =11112+++=R x x R R y D 222)1(y y x --=αα111+++=-R x x R R y D m m F m m m x y y x ≤--=)1(αα第m 板为进料111)1(+++--=m m m y y x ααw m m x R f x R R f y 1111+--++=+第N 板:在计算过程中, 每使用一次平衡关系, 表示需要一层理论板. 由于一般再沸器相当于一层理论板.结果: 塔内共有理论板N 块, 第N 板为再沸器, 其中精馏段m-1块, 提馏段N-m+1块 (包括再沸器), 第m 板为进料板。
二、图解法图解法求理论板层数的基本原理与逐板计算法的完全相同,只不过是用平衡曲线和操作线分别代替平衡方程和操作线方程,用简便的图解法代替繁杂的计算而已。
1、操作线的作法首先根据相平衡数据, 在直角坐标上绘出待分离混合物的x-y 平衡曲线, 并作出对角线.W NN N x y y x ≤--=)1(ααw N N x R f x R R f y 1111+--++=-在x=xD 处作铅垂线, 与对角线交于点a, 再由精馏段操作线的截距xD /(R+1) 值, 在y 轴上定出点b, 联ab. ab为精馏段操作线.在x=xF 处作铅垂线, 与精馏段操作线ab交于点d.在x=xW 处作铅垂线, 与对角线交于点c, 联cd. cd为提留段操作线.2、求N 的步骤自对角线上a点始, 在平衡线与精馏段操作线间绘出水平线及铅垂线组成的梯级.当梯级跨过两操作线交点d 时, 则改在平衡线与提馏操作线间作梯级, 直至某梯级的垂直线达到或小于xw为止.每一个梯级代表一层理论板. 梯级总数即为所需理论板数.3、梯级含义:如第一梯级:由a点作水平线与平衡线交于点1(y1, x1), 相当于用平衡关系由y1求得x1;再自点1作垂线与精馏段操作线相交, 交点坐标为(y2, x1), 即相当于用操作线关系由x1求得y2。
逐板计算法编程

逐板计算法编程逐板计算法,又称为差分法,是一种常用的算法思想,其通过按照问题的不同板块逐个解决,最终得到整体的解决方案。
在计算机编程领域,逐板计算法可以极大地提高程序的效率和可读性。
首先,我们来看一下逐板计算法的基本原理。
该算法的核心思想是将问题划分为多个板块,逐个计算每个板块的结果,再将这些结果整合起来得到最终答案。
这种分而治之的思想,使得问题的解决变得更加简单和高效。
在实际编程中,逐板计算法的应用非常广泛。
举个例子来说,假设我们要计算一个数列的和。
我们可以将这个数列按照一定的规则分成若干个板块,然后逐个计算每个板块的和,最后将所有板块的和相加即可得到最终结果。
通过逐板计算的方式,我们可以极大地减少计算的复杂度,提高程序的执行效率。
另外,逐板计算法还可以应用于一些复杂的计算问题。
例如,在图像处理中,我们可以将图片分成多个大块,然后再将每个大块分成更小的块。
通过逐个处理每个小块的方式,我们可以有效地处理整个图片,以达到优化处理速度和提高图像质量的目的。
此外,逐板计算法还可以用于解决一些需要动态规划的问题。
在动态规划中,我们通常需要用到已经计算过的子问题的结果来求解当前问题。
逐板计算法提供了一种将复杂问题分解为多个子问题的思路,使得动态规划的实现更加简单和高效。
综上所述,逐板计算法是一种非常实用的算法思想。
通过将问题分解为多个板块,逐个计算并整合结果,我们可以提高程序的效率、可读性和可维护性。
无论是在数学计算、图像处理还是动态规划等领域,逐板计算法都发挥着重要作用。
因此,在编程过程中,我们应当灵活运用逐板计算法,以解决复杂的问题,提升程序的性能和质量。
理论塔板数和回流比
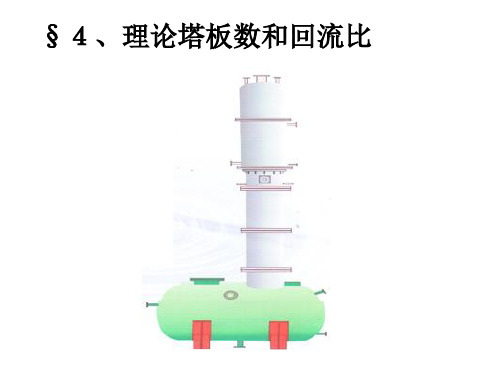
第n 板
∵全回流时操作线与对角线重合,
又∵
R
yn1 xn
∴精馏段操作线方程变成
塔顶采用全凝器,∴
y1 xd
yA xA y x B B d
回 流 比 R 所需理论板数
0.9 25
1.0 22
1.1 19
1.2 18
回流比对理论塔板数影响17
可见:靠近RM时,R↑,N显著↓, 塔高H↓,设备费↓. R 较高时, R 再 ↑ 由 (1.1—1.2) , N↓ 慢, V 显著 ↑ ,塔径 D↑
RL
∵
L RD D V L D RD D DR 1
由塔顶开始在平衡曲线和操作线之间作直角阶梯直到最后一个直角阶梯的共有11个直角阶梯即需11块理论塔板包括塔釜跨越两线交点的第六块塔板为加料板与逐板计算的结果完全一致
§4、理论塔板数和回流比
理论塔板(又叫平衡塔板)自该板 升向上一板的蒸气与该板流向下一 板的液体互成平衡。
y* n xn
一、逐板法
逐板计算就是反复地利用物料的气液平衡关系
在y-x图上,对于沸点液体进料,操作线、q线与平衡 线在x = xf处相交,如图。
yd yf C yd ) A ( xd, A B y ) B ( xd , f C(xf,yf)
xW
xf
xd
最小回流比16
由图看出:最小回流比时,精馏段操作线的斜率是:
RM A B xd y f RM 1 B C xd x f
x y 1 1x
当计算到xn≤xf 时(仅指饱和液体进料情况),说 明第 n 板是加料板。由此往下利用操作关系时应 该改用提馏段操作线方程,直至计算到xm ≤ xw为 止。在计算中每使用一次平衡关系,表示通过一 块理论板。 冷料
6.逐板计算法计算理论塔板数

y n1
xD R 2 0.9 xn xn 0.667 xn 0.3 R 1 R 1 2 1 2 1
逐板计算法计算理论塔板数
提馏段操作线方程:
x F xW 0.4 0.0667 ( R q) q (2 1) 1 3 因: R xD xF 0.9 0.4
逐板计算法计算理论塔板数
1
Contents
理论板的假定
目 录
2
逐板计算法
逐板计算法计算理论塔板数
1、 理论板的假定
所谓理论板是指离开该板的汽液两相互成平衡,塔板上各
处的液相组成均匀一致的理想化塔板。
其前提条件是汽液两相皆充分混合、各自组成均匀、塔板 上不存在传热、传质过程的阻力。
逐板计算法计算理论塔板数
逐板计算法计算理论塔板数
再利用相平衡方程由y2’求算x2’,如此重复计算,直至计算到 xm≤xW 为止。 对于间接蒸汽加热,再沸器内汽液两相可视为平衡,再沸器相当于一层 理论板,故提馏段所需理论板层数为(m–1)。 在计算过程中,每使用一次平衡关系,便对应一层理论板。 逐板计算法计算结果准确,概念清晰,但计算过程繁琐,一般适用于 计算机的计算。
有关理论塔板的两点说明
(1)实际上,由于塔板上汽液间的接触面积和接触时间是有限
的,在任何形式的塔板上,汽液两相都难以达到平衡状态,除
非接触时间无限长,因而理论板是不存在的。 (2)理论板作为一种假定,可用作衡量实际板分离效率的依据
和标准。通常,在工程设计中,先求得理论板层数,用塔板效
率予以校正,即可求得实际塔板层数。 总之,引入理论板的概念,可用泡点方程和相平衡方程描述 塔板上的传递过程,对精馏过程的分析和计算是十分有用的。
- 1、下载文档前请自行甄别文档内容的完整性,平台不提供额外的编辑、内容补充、找答案等附加服务。
- 2、"仅部分预览"的文档,不可在线预览部分如存在完整性等问题,可反馈申请退款(可完整预览的文档不适用该条件!)。
- 3、如文档侵犯您的权益,请联系客服反馈,我们会尽快为您处理(人工客服工作时间:9:00-18:30)。
一、概述1.1精馏操作对塔设备的要求和类型1.1.1对塔设备的要求精馏所进行的是气(汽)、液两相之间的传质,而作为气(汽)、液两相传质所用的塔设备,首先必须要能使气(汽)、液两相得到充分的接触,以达到较高的传质效率。
但是,为了满足工业生产和需要,塔设备还得具备下列各种基本要求:⑴气(汽)、液处理量大,即生产能力大时,仍不致发生大量的雾沫夹带、拦液或液泛等破坏操作的现象。
⑵操作稳定,弹性大,即当塔设备的气(汽)、液负荷有较大范围的变动时,仍能在较高的传质效率下进行稳定的操作并应保证长期连续操作所必须具有的可靠性。
⑶流体流动的阻力小,即流体流经塔设备的压力降小,这将大大节省动力消耗,从而降低操作费用。
对于减压精馏操作,过大的压力降还将使整个系统无法维持必要的真空度,最终破坏物系的操作。
⑷结构简单,材料耗用量小,制造和安装容易。
⑸耐腐蚀和不易堵塞,方便操作、调节和检修。
⑹塔内的滞留量要小。
实际上,任何塔设备都难以满足上述所有要求,况且上述要求中有些也是互相矛盾的。
不同的塔型各有某些独特的优点,设计时应根据物系性质和具体要求,抓住主要矛盾,进行选型。
1.1.2 板式塔类型气-液传质设备主要分为板式塔和填料塔两大类。
精馏操作既可采用板式塔,也可采用填料塔,板式塔为逐级接触型气-液传质设备,其种类繁多,根据塔板上气-液接触元件的不同,可分为泡罩塔、浮阀塔、筛板塔、穿流多孔板塔、舌形塔、浮动舌形塔和浮动喷射塔等多种。
板式塔在工业上最早使用的是泡罩塔(1813年)、筛板塔(1832年),其后,特别是在本世纪五十年代以后,随着石油、化学工业生产的迅速发展,相继出现了大批新型塔板,如S型板、浮阀塔板、多降液管筛板、舌形塔板、穿流式波纹塔板、浮动喷射塔板及角钢塔板等。
目前从国内外实际使用情况看,主要的塔板类型为浮阀塔、筛板塔及泡罩塔,而前两者使用尤为广泛。
筛板塔也是传质过程常用的塔设备,它的主要优点有:⑴结构比浮阀塔更简单,易于加工,造价约为泡罩塔的60%,为浮阀塔的80%左右。
⑵处理能力大,比同塔径的泡罩塔可增加10~15%。
⑶塔板效率高,比泡罩塔高15%左右。
⑷压降较低,每板压力比泡罩塔约低30%左右。
筛板塔的缺点是:⑴塔板安装的水平度要求较高,否则气液接触不匀。
⑵操作弹性较小(约2~3)。
⑶小孔筛板容易堵塞。
1.2.精馏塔的设计步骤本设计按以下几个阶段进行:⑴设计方案确定和说明。
根据给定任务,对精馏装置的流程、操作条件、主要设备型式及其材质的选取等进行论述。
⑵蒸馏塔的工艺计算,确定塔高和塔径。
⑶塔板设计:计算塔板各主要工艺尺寸,进行流体力学校核计算。
接管尺寸、泵等,并画出塔的操作性能图。
⑷管路及附属设备的计算与选型,如再沸器、冷凝器。
⑸抄写说明书。
⑹绘制精馏装置工艺流程图和精馏塔的设备图。
本设计任务为分离醇和水的混合物,对于二元混合物的分离,应采用连续常压精馏流程。
设计中采用泡点进料,将原料液通过预热器加热至泡点后送入精馏塔内。
塔顶上升蒸气采用全凝器冷凝,冷凝液在泡点下一部分回流至塔内,其余部分经产品冷凝器冷却后送至贮罐。
该物系属于易分离物系,最小回流比比较小,故操作回流比取最小回流比的1.5倍。
塔底采用间接蒸气加热,塔底产品经冷却后送至贮罐。
二、精馏塔的物料衡算2.1.原料液及其塔顶、塔底产品的摩尔分率乙酸的摩尔质量为:60.05kg/kmol乙酸酐的摩尔质量为: 102.09kg/kmolX F = (0.60/60.05) / ( 0.60/60.05+0.40/102.09)=0.718X D = (0.95/60.05) / (0.95/60.05+0.05/102.09)=0.970X W = (0.05/60.05) / (0.05/60.05+0.95/102.09)=0.08212.2 原料液及其塔顶与塔底产品的平均摩尔质量M F=60.05×0.718+102.09×(1-0.718)=71.91kg/kmolM D=60.05×0.970+102.09×(1-0.970)=61.31kg/kmolM W=60.05×0.0821+102.09×(1-0.0821)=98.64kg/kmol则可知:原料的处理量:F=730/(365×24×71.91)=1.159kmol/h由总物料衡算:1.159=D+W以及: X F×F= X D ×D+W×X W即:0.718×1.159= 0.970×D+W×0.0821容易得出: W=0.329kmol/hD =0.830kmol/h三、精馏塔的工艺条件及有关物性数据数据的计算3.1. 操作温度的计算t x y t x y 139.493 0.000 0.000 121.006 0.550 0.682135.286 0.050 0.160 120.454 0.600 0.712132.157 0.100 0.272 119.959 0.650 0.742129.756 0.150 0.355 119.518 0.700 0.773127.864 0.200 0.419 119.128 0.750 0.830126.337 0.250 0.472 118.788 0.800 0.880125.077 0.300 0.516 118.502 0.850 0.920124.016 0.350 0.555 118.273 0.900 0.956123.108 0.400 0.590 118.106 0.950 0.988122.319 0.450 0.622 118.009 1.000 1.000121.624 0.500 0.653表一、常压下乙酸-乙酸酐的气液平衡组成与温度关系由于泡点进料q=1,由气液平衡数据,用内插法求温度(0.750-0.700)/(119.128-119.518)=(0.718-0.700)/(t F-119.518)所以,进料板温度 t F =119.378℃同理可得塔釜温度 t W=133.277℃塔顶温度 t D=118.067℃精馏段平均温度 t m=(119.378+118.067)/2=118.723(℃)提馏段平均温度 t’m=(119.378+133.277)=126.328(℃)3.2平均粘度的计算液体黏度μL液相平均粘度依下式计算即lgμLm=∑x i lgμi纯组分的粘度温度(℃)100 110 120 130 1400.4583 0.4174 0.382 0.351 0.324乙酸,mPa.s乙酸酐,0.3763 0.3465 0.3204 0.2976 0.2775 mPa.s3.2.1进料板液相平均粘度的计算由t F=119.378℃,同理用内插法求μA、μB(0.382-0.4174)/(120-110)=(0.382-μA) / (120-119.378)解得μA=0.388 mPa.s(0.3204-0.3465)/(120-110)=( 0.3204-μB) / (120-119.378)解得μB =0.325 mPa.slgμLDm=0.718lg0.388+(1-0.718)lg 0.325=-0.433μLDm=0.369mPa.s3.2.2塔顶平均粘度的计算由t D=118.067℃,同理可得μA=0.3888mPa.s μB=0.3254mPa.slgμLFm=0.970lg0.3888+(1-0.970)lg0.3254=-0.4126μLFm=0.3867mPa.s精馏段平均粘度μLm=(0.369+0.3867)/2=0.379mPa.s3.2.3塔底液相平均粘度的计算由t W=133.277℃,同理可得μA=0.3422mPa.s μB=0.2910mPa.slgμLWm=0.0821g0.3422+(1-0.0821)lg0.2910=-0.5303μLWm=0.2949mPa.s提馏段平均粘度μL’m=(0. 369+0. 2949)/2=0.332mPa.s四、塔板数的确定以及操作压力和平均密度的计算4.1.理论板层数N T的求取附:汽液平衡数据t x y t x y 139.493 0.000 0.000 121.006 0.550 0.682 135.286 0.050 0.160 120.454 0.600 0.712 132.157 0.100 0.272 119.959 0.650 0.742 129.756 0.150 0.355 119.518 0.700 0.773 127.864 0.200 0.419 119.128 0.750 0.830 126.337 0.250 0.472 118.788 0.800 0.880 125.077 0.300 0.516 118.502 0.850 0.920 124.016 0.350 0.555 118.273 0.900 0.956 123.108 0.400 0.590 118.106 0.950 0.988 122.319 0.450 0.622 118.0091.000 1.000 121.6240.5000.6534.1.1气相组成的计算由t D =118.067℃,用内插法求y D(118.106-118.009)/(0.988-1.00)=(118.106-118.067) / (0.988-y D ) 解得: y D =0.933同理,由t F =119.378℃,得y F =0.792 t W =133.277℃, 得y W =0.2324.1.2相对挥发度的计算由 X F =0.718,y F =0.792,得()()[]F F FFF x y x y -÷-÷=11α,带入数据得: =F α 1.50 同理,由X D =0.970,y D =0.933,得=D α 4.39 X W =0.0821,y W =0.232,得=W α 3.38 精馏段的平均相对挥发度:=1α(1.50+4.39)/2=2.95 提馏段的平均相对挥发度:=2α(1.50+3.38)/2=2.444.1.3.精馏塔的气、液相负荷Rmin=(x D -y q )/(y q -x q )由前面计算,我们可以知道y q =0.792,同时又是泡点进料,有x q =x F ,故Rmin =(0.970-0.792)/(0.792-0.0.718) =2.405取操作回流比为:R=1.5Rmin=1.5×2.405=3.61L=R ×D =3.61×0.830=3.00kmol/h V=(R+1)×D =4.61×0.830=3.83kmol/h L ’=L+F =3.00+1.159=4.159kmol/h V ’=V =3.83kmol/h4.1.4.精馏段、提馏段操作线及平衡方程精馏段操作线:y =R ×x /(R+1)+ X D /( R+1)=3.61x/(3.61+1)+0.970/(3.61+1)=0.783x+0.210 (1) 提馏段操作线:y’=L’/V’×x’-W × X W /V’=4.159x’/3.83-0.329×0.0821/3.83=1.09x ’-0.0071 (2) 精馏段平衡线:x=y/[y+(1-y)α⨯]=y/[y+(1-y)×2.95] (3) 同理有:提馏段平衡线:x=y/[y+(1-y)×2.44] (4)4.1.5.逐板计算法求理论塔板层数 x=y/[y+(1-y)×2.44]y 1=x D =0.970,带入(3),得x 1=0.916 将x 1=0.916 带入(1),得y 2=0.927将y 2=0.927 带入(3), 得x 1=0.811,如此重复,直到x n <=x q ,算的x 3=0.649<x q列表,精馏段有将x 3=0.649 带入(2),得y 4=0.700将y 4=0.700 带入(4), 得x 4=0.489,如此重复,直到x m <=x w ,算的x 7=0.0815<x w 列表,精馏段有y 1=0.970 y 2=0.927 y 3=0.845 x 1=0.916 x 2=0.811x 3=0.649y 4=0.700 y 5=0.526 y 6=0.334 y 7=0.178x4=0.489 x5=0.313 x6=0.170 x7=0.0815从表中可知,总理论塔板数N T为6块(不包括再沸器),其中精馏段2块,提馏段4块。