2屈服强度的测定
工字钢屈服强度试验记录

工字钢屈服强度试验记录摘要:一、工字钢屈服强度试验背景二、试验目的与要求三、试验过程及方法四、试验结果与分析五、结论正文:【一、工字钢屈服强度试验背景】在我国,钢结构工程在建筑、桥梁、塔架等领域得到了广泛应用。
为确保钢结构工程的安全性和可靠性,必须对其材料性能进行严格的检测。
其中,工字钢的屈服强度是衡量其承载能力的重要指标。
为了保证工字钢的质量和工程安全,必须对其屈服强度进行试验检测。
【二、试验目的与要求】本次工字钢屈服强度试验的主要目的是检测工字钢的屈服强度是否符合我国相关标准规定,以及验证其材料性能是否满足工程应用需求。
试验要求严格按照试验方法进行,确保试验结果的准确性和可靠性。
【三、试验过程及方法】1.试验样品的选取:从不同生产批次、规格和型号的工字钢中随机抽取一定数量的样品进行试验。
2.试验设备准备:准备屈服强度试验机、千分尺、卡尺等试验设备。
3.试验过程:首先对试验样品进行尺寸测量,然后将样品放置在屈服强度试验机上进行拉伸试验。
在试验过程中,实时记录试验力、应变等数据,直至样品发生屈服现象。
4.数据处理:记录试验过程中的试验力、应变等数据,并计算出屈服强度。
【四、试验结果与分析】1.试验结果显示,所有样品的屈服强度均符合我国相关标准规定,说明产品质量较好。
2.通过对比不同生产批次、规格和型号的工字钢试验结果,发现产品性能存在一定差异。
建议生产厂家在生产过程中加强质量控制,优化工艺参数,以提高产品性能的稳定性和一致性。
【五、结论】本次工字钢屈服强度试验结果表明,所检测的工字钢产品质量较好,性能满足工程应用需求。
但仍需生产厂家进一步加强质量管理和工艺改进,以提高产品性能的稳定性和一致性。
金属材料扭转实验
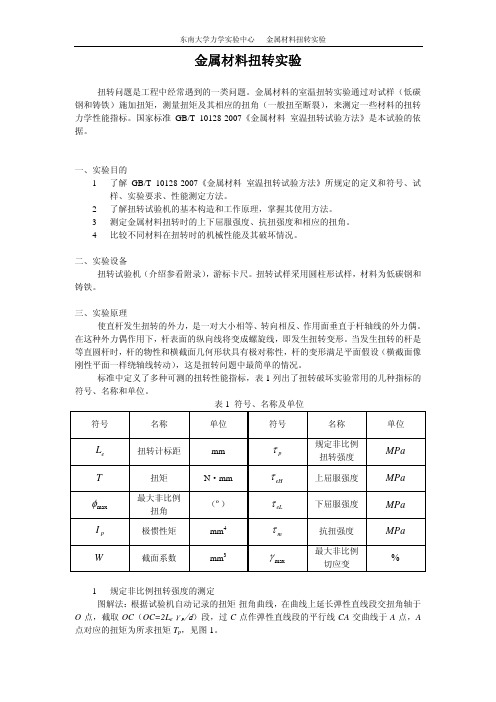
一、实验目的 1 了解 GB/T 10128-2007《金属材料 室温扭转试验方法》所规定的定义和符号、试 样、实验要求、性能测定方法。 2 了解扭转试验机的基本构造和工作原理,掌握其使用方法。 3 测定金属材料扭转时的上下屈服强度、抗扭强度和相应的扭角。 4 比较不同材料在扭转时的机械性能及其破坏情况。
东南大学力学实验中心 金属材料扭转实验
图 8(b)选择需要计算的指标 设置“试验结束条件”,通常设定“断裂百分比”为 40%。点击“下一步”,见图 8(c)。
图 8(c)设置结束条件 选择传感器。然后点击“下一步”,见图 8(d)。
东南大学力学实验中心 金属材料扭转实验
图 8(d)选择传感器 设置坐标轴增量。点击“关闭”,完成参数设置,见图 8(e)。
图 8(e)设置坐标轴增量 3 开始实验,观察加载过程
首先分别对界面中显示的“扭矩”和“转角”进行“清零”,再选择需要绘制的曲线类 型,然后点击“试验开始”,试验机按照前面的设定对试样加载,此时应注意观察试样的变 化情况和控制软件上扭转曲线的绘制情况,见图 9。
东南大学力学实验中心 金属材料扭转实验
东南大学力学实验中心 金属材料扭转实验
图 7 试样录入 点击“参数设置”,设置实验参数。通常“试验开始扭矩值”设定为 1N·m;“试验速 度”低碳钢试样为 360º/min,铸铁试样为 36º/min。然后点击“下一步”,见图 8(a)。
图 8(a)设定开始扭矩和实验速度 选择需要计算的指标,在前面的复选框内打“√”。点击“下一步”,见图 8(b)。
mm4
W
截面系数Biblioteka mm3τm抗扭强度
MPa
γ max
最大非比例 切应变
%
1 规定非比例扭转强度的测定 图解法:根据试验机自动记录的扭矩-扭角曲线,在曲线上延长弹性直线段交扭角轴于
工程材料第二版习题(1-2)章答案
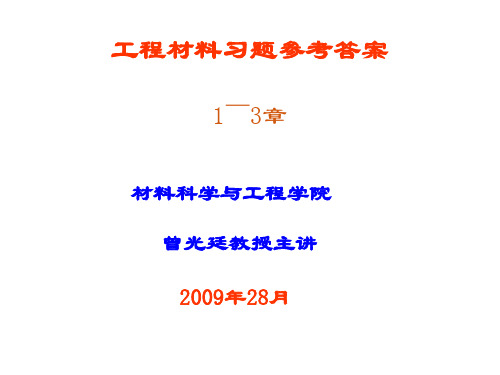
塑性变形的的物理本质: 塑性变形的的物理本质: 滑移和孪生共同产生的塑性变形。 滑移和孪生共同产生的塑性变形。 P24 滑移是晶体的一部分相对另一部分做整 体刚性移动。孪生是在切应力的作用下, 体刚性移动。孪生是在切应力的作用下,晶 体的一部分相对另一部分沿着一定的晶面 孪生面) (孪生面)产生一定角度的切变
2-13、晶粒大小对金属性能有何影响?细化 13、晶粒大小对金属性能有何影响? 晶粒方法有哪些? 晶粒方法有哪些? p17 答: 在一般情况下,晶粒愈小,则金属的强度. 在一般情况下,晶粒愈小,则金属的强度.塑 性和韧性愈好. 性和韧性愈好. 细化晶粒是提高金属性能的重要途径之一, 细化晶粒是提高金属性能的重要途径之一, 晶粒愈细,强度和硬度愈高, 晶粒愈细,强度和硬度愈高,同时塑性韧性 愈好。 愈好。 细化晶粒方法有: 细化晶粒方法有: 增大过冷度; 2.变质处理 变质处理; 3.附加振 增大过冷度; 2.变质处理; 3.附加振 动或搅动等方法; 动或搅动等方法;
5、晶粒 p11 晶粒---每个小晶体具有不规则的颗粒状外形。 ---每个小晶体具有不规则的颗粒状外形 晶粒---每个小晶体具有不规则的颗粒状外形。 何谓空间点阵、晶格、晶体结构和晶胞? 2-2、何谓空间点阵、晶格、晶体结构和晶胞? 常用金属的晶体结构是什么?划出其晶胞, 常用金属的晶体结构是什么?划出其晶胞, 并分别计算起原子半径、配位数和致密度? 并分别计算起原子半径、配位数和致密度? 1、空间点阵 p9 空间点阵-----为了便于分析各种晶体中的原子 空间点阵---为了便于分析各种晶体中的原子 排列及几何形状, 排列及几何形状,通常把晶体中的原子假想为 几何结点,并用直线从其中心连接起来,使之 几何结点,并用直线从其中心连接起来, 构成一个空间格子。 构成一个空间格子。
材料的屈服强度
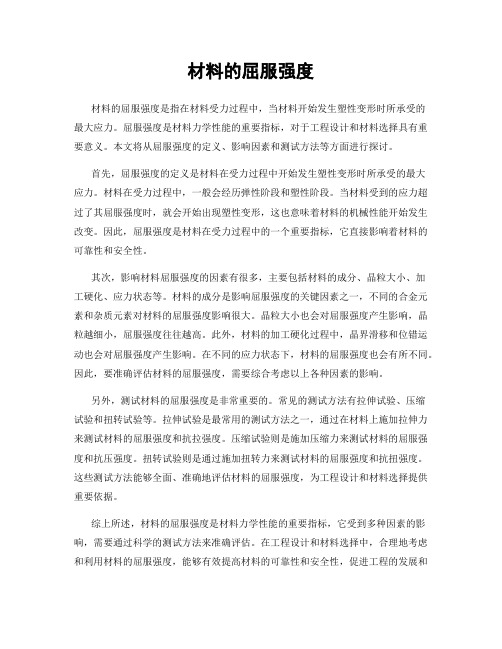
材料的屈服强度材料的屈服强度是指在材料受力过程中,当材料开始发生塑性变形时所承受的最大应力。
屈服强度是材料力学性能的重要指标,对于工程设计和材料选择具有重要意义。
本文将从屈服强度的定义、影响因素和测试方法等方面进行探讨。
首先,屈服强度的定义是材料在受力过程中开始发生塑性变形时所承受的最大应力。
材料在受力过程中,一般会经历弹性阶段和塑性阶段。
当材料受到的应力超过了其屈服强度时,就会开始出现塑性变形,这也意味着材料的机械性能开始发生改变。
因此,屈服强度是材料在受力过程中的一个重要指标,它直接影响着材料的可靠性和安全性。
其次,影响材料屈服强度的因素有很多,主要包括材料的成分、晶粒大小、加工硬化、应力状态等。
材料的成分是影响屈服强度的关键因素之一,不同的合金元素和杂质元素对材料的屈服强度影响很大。
晶粒大小也会对屈服强度产生影响,晶粒越细小,屈服强度往往越高。
此外,材料的加工硬化过程中,晶界滑移和位错运动也会对屈服强度产生影响。
在不同的应力状态下,材料的屈服强度也会有所不同。
因此,要准确评估材料的屈服强度,需要综合考虑以上各种因素的影响。
另外,测试材料的屈服强度是非常重要的。
常见的测试方法有拉伸试验、压缩试验和扭转试验等。
拉伸试验是最常用的测试方法之一,通过在材料上施加拉伸力来测试材料的屈服强度和抗拉强度。
压缩试验则是施加压缩力来测试材料的屈服强度和抗压强度。
扭转试验则是通过施加扭转力来测试材料的屈服强度和抗扭强度。
这些测试方法能够全面、准确地评估材料的屈服强度,为工程设计和材料选择提供重要依据。
综上所述,材料的屈服强度是材料力学性能的重要指标,它受到多种因素的影响,需要通过科学的测试方法来准确评估。
在工程设计和材料选择中,合理地考虑和利用材料的屈服强度,能够有效提高材料的可靠性和安全性,促进工程的发展和进步。
因此,对于材料的屈服强度,我们应该深入理解其定义、影响因素和测试方法,从而更好地应用于实际工程中。
2屈服强度的测定

二、屈服强度σ0.2的测定一、概述金属材料的屈服点(屈服强度)是工程实际中广泛应用的一个重要强度性能指标。
对于没有明显屈服现象的金属材料,通常固定以产生0.2%残余应变时的应力(称为规定残余伸长应力)作为这类材料的屈服点,故又称为名义屈服极限、屈服强度等,用σ0.2表示。
二、实验目的:1.学会测定无明显屈服阶段材料的名义屈服极限的原理和方法;2.测定45钢的规定残余伸长应力σ0.2;3.学习试验机和相关仪器的操作使用。
三、实验仪器,材料:电子万能试验机,引伸计,游标卡尺,拉伸试样四、实验原理国标GB228-87《金属拉伸试验方法》规定,σ0.2表征试样卸除拉伸力后,其标距部分的残余伸长达到规定的原始标距长度的0.2%时的应力,简称为规定残余伸长应力。
表达式为:σr0.2=F r0.2A0⁄式中,F r0.2为规定产生0.2%的残余伸长力,A0为试样平行长度部分的原始横截面面积。
金属材料规定残余伸长应力σ0.2和屈服点一样,表征材料开始塑性变形时的应力。
其测试方法可分为图解法和引伸计(卸力)法。
1、图解法测σ0.2时,需要借助试验机上的自动绘图装置做出载荷F与伸长△L的关系曲线图。
如图1所示。
为了确保其测量精度,要求力轴每毫米所代表的应力一般不大于10N/mm2 ,曲线的高度应使F r出于力轴量程的1/2以上。
伸长放大倍数的选择应使图中的OC段的长度不小于5mm。
然后,在绘出的F-△L曲线图上,自弹性直线段与伸长轴的交点O起,在伸长轴上截取一相应于规定非比例伸长的OC段,即OC=L r×K×0.2%=KL rεr其中L r为图1 图解法测定σ0.2引伸计标距,K为引伸计放大倍数,εr为残余伸长应变,即等于0.2%。
然后过C点做弹性直线段的平行线CA交曲线于A点,则A点对应的拉力F r即为所测规定残余伸长相对应的F r0.2。
根据F r0.2可计算出规定残余伸长应力σ0.2。
此法是一次加载后,即可求出σ0.2,但要求有高精度的自动测绘设备,例如电子万能试验机(力传感器、位移传感器及记录绘图装置等)才能保证其测量精度要求。
屈服强度测试标准
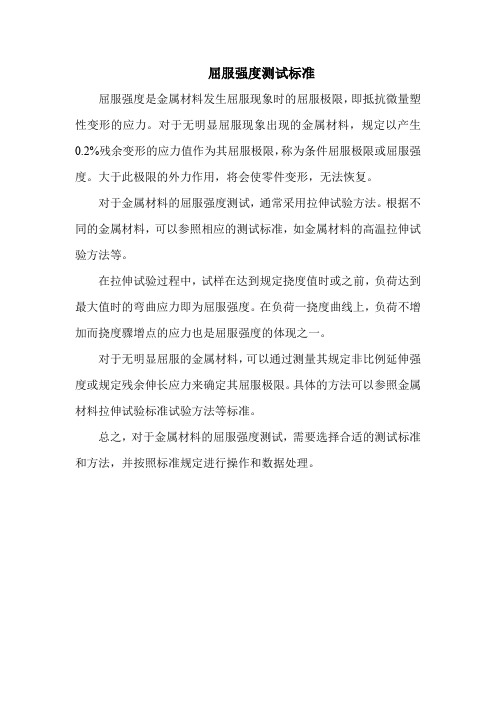
屈服强度测试标准
屈服强度是金属材料发生屈服现象时的屈服极限,即抵抗微量塑性变形的应力。
对于无明显屈服现象出现的金属材料,规定以产生0.2%残余变形的应力值作为其屈服极限,称为条件屈服极限或屈服强度。
大于此极限的外力作用,将会使零件变形,无法恢复。
对于金属材料的屈服强度测试,通常采用拉伸试验方法。
根据不同的金属材料,可以参照相应的测试标准,如金属材料的高温拉伸试验方法等。
在拉伸试验过程中,试样在达到规定挠度值时或之前,负荷达到最大值时的弯曲应力即为屈服强度。
在负荷一挠度曲线上,负荷不增加而挠度骤增点的应力也是屈服强度的体现之一。
对于无明显屈服的金属材料,可以通过测量其规定非比例延伸强度或规定残余伸长应力来确定其屈服极限。
具体的方法可以参照金属材料拉伸试验标准试验方法等标准。
总之,对于金属材料的屈服强度测试,需要选择合适的测试标准和方法,并按照标准规定进行操作和数据处理。
b19屈服强度

b19屈服强度
摘要:
一、概念解释
二、屈服强度的测定
三、屈服强度在材料应用中的重要性
四、提高屈服强度的方法
五、结论
正文:
一、概念解释
屈服强度,又称屈服极限,英文Yield Strength,常用符号s,是材料屈服的临界应力值。
它表示材料在受到外力作用时,发生塑性变形前的最大应力值。
当外力超过材料的屈服强度,材料将发生永久性变形,失去原有的功能。
二、屈服强度的测定
对于屈服现象明显的材料,屈服强度就是屈服点的应力。
对于屈服现象不明显的材料,则规定应变值为0.2%所对应的应力值为其屈服极限,称为条件屈服强度。
三、屈服强度在材料应用中的重要性
屈服强度是评价材料力学性能的重要指标,它在工程设计、建筑结构等领域具有重要作用。
建筑钢材以屈服强度作为设计应力的依据。
因为当应力超过材料的屈服强度,材料将发生永久性变形,失去原有的功能。
四、提高屈服强度的方法
提高屈服强度的方法主要有:合金元素调控、热处理控制、微观组织调控等。
通过这些方法,可以提高材料的屈服强度,从而提高其使用寿命和性能。
五、结论
总之,屈服强度是材料的重要性能指标,它在材料的研发、设计和应用中起着关键作用。
了解屈服强度的概念、测定方法和应用,对于材料科学和工程领域的研究人员具有很大的实际意义。
2系铝合金屈服强度表

2系铝合金屈服强度表铝合金是一种常用的金属材料,具有轻质、强度高、导热性好等优点,在工业生产和日常生活中被广泛应用。
2系铝合金是铝合金中一种重要的系列,其强度表现出色。
本文将就2系铝合金的屈服强度进行详细介绍。
屈服强度是指材料在受力过程中开始产生塑性变形的临界点。
对于2系铝合金来说,它们的屈服强度一般较高,能够承受较大的外力而不发生塑性变形。
下面是一些常见的2系铝合金及其典型的屈服强度数值表:1. 2011铝合金:该合金主要含有铜和铅等元素,具有良好的加工性能和耐腐蚀性。
其屈服强度通常在120-150 MPa之间。
2. 2024铝合金:该合金含有铜、镁和锌等元素,具有良好的强度和韧性。
其屈服强度约为280-420 MPa。
3. 2219铝合金:该合金含有铜、铁和硅等元素,具有高强度和耐腐蚀性。
其屈服强度通常在310-370 MPa之间。
4. 2618铝合金:该合金含有铜、镍和钛等元素,具有优异的高温强度和耐蚀性。
其屈服强度约为310-350 MPa。
5. 2017铝合金:该合金含有铜和镁等元素,具有良好的耐磨性和抗蚀性。
其屈服强度通常在150-220 MPa之间。
需要注意的是,上述数值仅为常见2系铝合金的典型屈服强度范围,具体数值还会受到合金配比、热处理和工艺等因素的影响。
在实际应用中,根据不同的需求和工程要求,可以选择合适的铝合金材料以满足特定的强度要求。
除了屈服强度,2系铝合金还具有其他优良的性能。
例如,它们具有一定的耐腐蚀性,能够在潮湿和腐蚀环境中保持较好的稳定性。
同时,2系铝合金还具有良好的可焊性和可加工性,能够满足复杂零件的制造需求。
在实际应用中,选择合适的2系铝合金材料需要综合考虑材料的强度、韧性、耐腐蚀性、可加工性等因素。
在设计和工程中,还需要根据具体的应用环境和要求,对铝合金进行适当的热处理和加工工艺,以提高材料的性能和强度。
2系铝合金是一类优质的金属材料,具有较高的屈服强度。
通过合理选择合金配比和进行适当的热处理,可以进一步提高2系铝合金的强度和性能。
- 1、下载文档前请自行甄别文档内容的完整性,平台不提供额外的编辑、内容补充、找答案等附加服务。
- 2、"仅部分预览"的文档,不可在线预览部分如存在完整性等问题,可反馈申请退款(可完整预览的文档不适用该条件!)。
- 3、如文档侵犯您的权益,请联系客服反馈,我们会尽快为您处理(人工客服工作时间:9:00-18:30)。
二、屈服强度σ0.2的测定
一、概述
金属材料的屈服点(屈服强度)是工程实际中广泛应用的一个重要强度性能指标。
对于没有明显屈服现象的金属材料,通常固定以产生0.2%残余应变时的应力(称为规定残余伸长应力)作为这类材料的屈服点,故又称为名义屈服极限、屈服强度等,用σ0.2表示。
二、实验目的:
1.学会测定无明显屈服阶段材料的名义屈服极限的原理和方法;
2.测定45钢的规定残余伸长应力σ0.2;
3.学习试验机和相关仪器的操作使用。
三、实验仪器,材料:
电子万能试验机,引伸计,游标卡尺,拉伸试样
四、实验原理
国标GB228-87《金属拉伸试验方法》规定,σ0.2表征试样卸除拉伸力后,其标距部分的残余伸长达到规定的原始标距长度的0.2%时的应力,简称为规定残余伸长应力。
表达式为:
σr0.2=F r0.2A0
⁄
式中,F r0.2为规定产生0.2%的残余伸长力,
A0为试样平行长度部分的原始横截面面积。
金属材料规定残余伸长应力σ0.2和屈服点一样,表征材料开始塑性变形时的应力。
其测试方法可分为图解法和引伸计(卸力)法。
1、图解法测σ0.2时,需要借助试验机上的自动绘图装置做出载荷F与伸长△L的关系曲线图。
如图1所示。
为了确保其测量精度,要求力轴每毫米所代表的应力一般不大于10N/mm2 ,曲线的高度应使F r出于力轴量程的1/2以上。
伸长放大倍数的选择应使图中的OC段的长度不小于5mm。
然后,在绘出的F-△L曲线图上,自弹性直线段与伸长轴的交点O起,在伸长轴上截取一相应于规定非比例伸长的OC段,即
OC=L r×K×0.2%=KL rεr其中L r为
图1 图解法测定σ0.2
引伸计标距,K为引伸计放大倍数,εr为残余伸长应变,即等于0.2%。
然后过C点做弹性直线段的平行线CA交曲线于A点,则A点对应的拉力F r即为所测规定残余伸长相对应的F r0.2。
根据F r0.2可计算出规定残余伸长应力σ0.2。
此法是一次加载后,即可求出σ0.2,但要求有高精度的自动测绘设备,例如电子万能试验机(力传感器、位移传感器及记录绘图装置等)才能保证其测量精度要求。
所以在一般情况下不采用此法。
常采用引伸计(卸力)法来测量金属材料的σ0.2。
2、采用引伸计(卸力)法σ0.2时,其具体步骤为:
(1)根据前面拉伸实验做好准备工作,如测量直径,安装试样及调整引伸计等。
(2)计算引伸计标距L r内产生0.2%的残余变形所对应的规定残余伸长值
(0.2%L r)及其在引伸计上的飞个数A,
即规定残余伸长值在引伸计上的分个数A=规定残余伸长值
引伸计每分格值。
(3)加初始载荷F0。
即相当于预计规定残余伸长应力的10%的力。
安装好引伸计。
继续加力至2F0后再卸力到F0,调整引伸计的零点或引伸计的条件零点为1分格(分格数的初读数)
(4)从F0开始加载,第一次施力致使试样在引伸计标距内产生的总伸长为
K×L r×εr+(1~2)分格,即A+(1~2)格。
式中第一项为规定残余伸长,
第二项为弹性伸长。
然后卸载至F0,在引伸计上读出首次卸力的残余伸长。
以后每次施力应使试样产生总伸长为其前一次的总伸长加上规定残余伸长与二次残余伸长(卸至F0)之差,再加上1~2分格的弹性伸长增量。
实验直至实测的残余伸长值等于或稍大于规定残余伸长值为止,如图2所示。
(5)的分格数计入附表中,然后计算其残余伸长值并与规定残余伸长应力σ0.2所要求的残余伸长比较。
最后用内插法计算出相当于规定残余伸长时所对应的力F r0.2。
图2 引伸计(卸力)法测定σ0.2
五、实验步骤:
1.测量直径d。
用千分尺测量试样工作长度内两端及中央三处的直径,每处应在
两个相互垂直的方向各测量一次,取平均值。
2.用分度机对试样进行分度,将试样的工作长度分为十等分,每等分间距10mm。
3.安装引伸计,装夹试样到试验机上,开启油泵,对试样进行加载。
4.加载时注意记录屈服载荷P s及最大载荷P b。
5.取下试样,用游标卡尺测量断裂后的总长度L k和颈缩处的最小直径d k。
六、实验报告要求
1.简述实验名称、目的要求、设备仪器及实验过程。
2.给出材料的σ0.2的值(包含记录原始数据表格)。
3.分析实验误差及其原因。
七、思考题
1.测定材料的规定残余伸长应力σ0.2有何实际意义?
2.用引伸计(卸力)法来测量金属材料的σ0.2时为什么要反复加、卸载?初始
载荷F0是否影响测量结果?。