汽车平衡悬架的设计要点
汽车平衡悬架的设计要点(转)
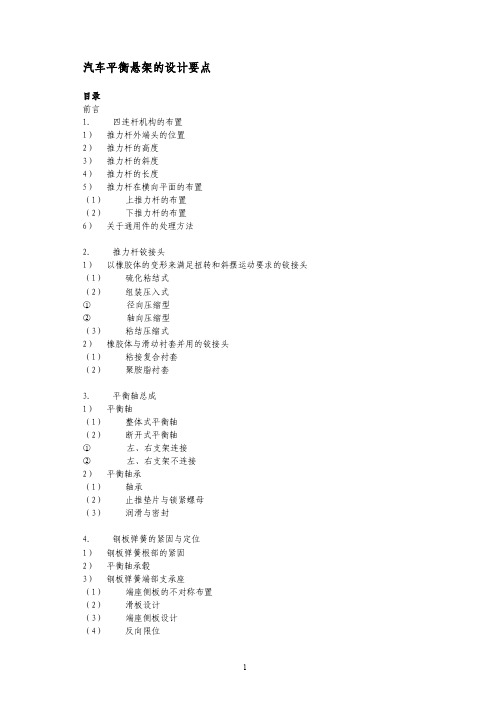
要求对称于平衡轴: 1 2 要求对中、后桥相关位臵相同: 1 2 从图中可知:
2 2 (1) 1 1 (2) 2 1 , 代入式(1),得 将 2 1 , 1 1 , 1 1 , 代入式(2),得 1 1 2 1 ,
a 布臵下推力杆位臵,并核对离地间隙是否满足要求。 2
对于一根上杆、两根下杆的常规设计,这种布臵使上、下杆受力基本相同。 3) 推力杆的斜度 (1)下推力杆斜角 2 决定轴转向效应,即 ε tan 2 式中ε
d 为轴转向效应系数,而 为轴转向角, 为侧倾角。 d
一般纵臵的中、后桥布臵,稳态转向特性往往具有偏大的不足转应效应。将 2 设计成如图 1 所示的布臵,可减小不足转向,使转向灵活些,减少轮胎磨损,同时, 簧载质体的离地间隙也高一些。 (2)上推力杆斜角 1 的布臵,应结合 2 的状态,决定中、后桥的瞬时转动中心位臵和 倾角变化。 若 1 < 2 ,即上、下推力杆延线交点(瞬心)在平衡轴中心线一侧,这样当车 桥跳动时,中、后桥间的那根传动轴的运动干涉(花键窜动量和夹角变化)会比较 小。反之, 1 > 2 ,则对中桥前的那一根传动轴的干涉较有利。因为一般设计,中、 后桥间传动轴较短,所以较常采用 1 < 2 。若采用 1 = 2 ,为平行四连杆机构, 中、后桥作平移运动,跳动时无倾角变化。 4) 推力杆的长度 在平衡轴支架及横梁结构允许条件下,推力杆应尽量选长一些,这样可减小车 轮跳动时的纵向窜动量。最好选取优先数作为长度值。 除非结构布臵上的原因,绝大多数设计都选取上、下杆等长。不等长上、下杆 往往造成中、后桥跳动时有倾角变化。纵臵四连杆机构不像双横臂独立悬架,一般不 采用不等长上、下臂结构。但是,国外也有少数厂家采用上短下长的推力杆,以适度 的倾角变化来换取轮胎接地点在纵向的移动量(轴距变化)达到最小,减少了轮胎磨 损量。 推力杆在横向平面的布臵
汽车悬架系统设计要点
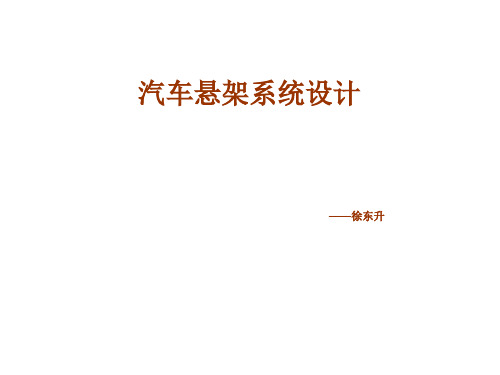
汽车悬架系统设计
——徐东升
汽车悬架的主要功用
汽车悬架是将车架(或车身)与车轴(或直接与车 轮)弹性联接的部件。其主要功用如下: (1)缓和,抑制由于不平路面所引起的振动或冲击以保 证汽车具有良好的平顺性。 (2)迅速衰减车身和车桥(或车轮)的振动。 (3)传递作用在车轮和车架(车身)之间的各种力(垂 直力,纵向力,横向力)和力矩(制动力矩和反作用力 矩)。 (4)保证汽车行驶所必要的稳定性。
阿克曼偏差
o
修改以达到不同的方向盘转角
t
q
t
轿车转向系统角传动比一般为15-17
2
1
在作加长车时 要考虑这个值
p
某些参考车型前轴的阿克曼角实例
阿克曼偏差 (o)
A B
方向盘转角 (o)
方向盘转角和转向角的关系
25
20
车轮转角 (o)
15
10
5
0 -400 -300 -200 -100 0 100 200 300 400
定义车轮中心处的主销偏置距
Braccio trasversale a centro ruota (mm)
汽车底盘悬架类型与设计的要点
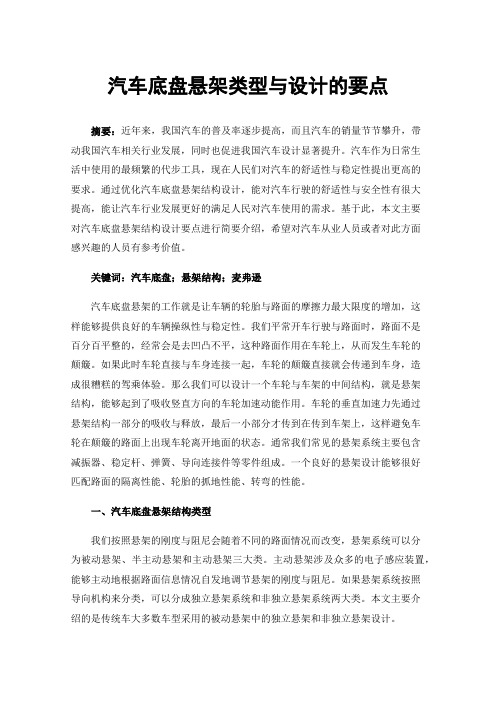
汽车底盘悬架类型与设计的要点摘要:近年来,我国汽车的普及率逐步提高,而且汽车的销量节节攀升,带动我国汽车相关行业发展,同时也促进我国汽车设计显著提升。
汽车作为日常生活中使用的最频繁的代步工具,现在人民们对汽车的舒适性与稳定性提出更高的要求。
通过优化汽车底盘悬架结构设计,能对汽车行驶的舒适性与安全性有很大提高,能让汽车行业发展更好的满足人民对汽车使用的需求。
基于此,本文主要对汽车底盘悬架结构设计要点进行简要介绍,希望对汽车从业人员或者对此方面感兴趣的人员有参考价值。
关键词:汽车底盘;悬架结构;麦弗逊汽车底盘悬架的工作就是让车辆的轮胎与路面的摩擦力最大限度的增加,这样能够提供良好的车辆操纵性与稳定性。
我们平常开车行驶与路面时,路面不是百分百平整的,经常会是去凹凸不平,这种路面作用在车轮上,从而发生车轮的颠簸。
如果此时车轮直接与车身连接一起,车轮的颠簸直接就会传递到车身,造成很糟糕的驾乘体验。
那么我们可以设计一个车轮与车架的中间结构,就是悬架结构,能够起到了吸收竖直方向的车轮加速动能作用。
车轮的垂直加速力先通过悬架结构一部分的吸收与释放,最后一小部分才传到在传到车架上,这样避免车轮在颠簸的路面上出现车轮离开地面的状态。
通常我们常见的悬架系统主要包含减振器、稳定杆、弹簧、导向连接件等零件组成。
一个良好的悬架设计能够很好匹配路面的隔离性能、轮胎的抓地性能、转弯的性能。
一、汽车底盘悬架结构类型我们按照悬架的刚度与阻尼会随着不同的路面情况而改变,悬架系统可以分为被动悬架、半主动悬架和主动悬架三大类。
主动悬架涉及众多的电子感应装置,能够主动地根据路面信息情况自发地调节悬架的刚度与阻尼。
如果悬架系统按照导向机构来分类,可以分成独立悬架系统和非独立悬架系统两大类。
本文主要介绍的是传统车大多数车型采用的被动悬架中的独立悬架和非独立悬架设计。
(一)非独立悬架系统如图1所示,非独立悬架系统简单的理解就是前轮或者后轮的左右两个轮子会相互作用,左边的轮子会受到右边的轮子的影响。
悬架设计 (3)

悬架设计1. 引言悬架系统是汽车工程中非常重要的一个组成部分,它负责连接车辆的车身和车轮,提供悬挂和减震功能,以确保车辆在不平坦的道路上具有良好的稳定性和舒适性。
本文将介绍悬架系统的设计原理、类型以及设计考虑因素。
2. 悬架系统的设计原理悬架系统的设计原理涉及到力学和动力学的基本原理,以及减震器的工作原理。
在悬架系统中,最重要的任务是通过悬架装置将车轮的垂直运动转化为车身的纵向和横向运动,同时提供足够的负载支撑和减震功能。
3. 悬架系统的类型在汽车工程中,主要有几种常见的悬架系统类型,包括独立悬架、非独立悬架和气动悬架。
下面将对这些不同类型的悬架系统进行简要介绍。
3.1 独立悬架独立悬架是最常见的一种悬架系统类型,它将每个车轮都连接到车身的独立悬架装置上。
这种设计可以使每个车轮独立运动,提高车辆的稳定性和操控性能。
独立悬架又可细分为麦弗逊悬架、多连杆悬架和双叉臂悬架等,每种悬架系统在结构和工作原理上都有所不同。
3.2 非独立悬架非独立悬架将两个前轮或后轮连接在一起,通过一个共享的悬架装置来实现。
这种设计相对于独立悬架来说比较简单和经济,但在提供悬挂和减震功能方面效果较差。
3.3 气动悬架气动悬架使用气压调节器来控制车身与地面之间的间隙。
通过增加或减少气压,可以实现对车身高度的调节,从而改变车辆的悬挂刚度和行驶舒适性。
气动悬架通常用于高端豪华车辆,以提供更好的悬挂性能和乘坐舒适度。
4. 悬架系统设计的考虑因素在设计悬架系统时,需要考虑以下几个主要因素。
4.1 载荷悬架系统设计必须考虑车辆的预计最大载荷,以确保悬架系统能够承受和支撑所需的重量。
这涉及到选用合适的弹簧和减震器,以及调节悬架刚度和行程长度。
4.2 地面条件不同的地面条件对悬架系统的设计有不同的要求。
在较为平坦的道路上,悬架系统可以设计得较为柔软,以提供更好的乘坐舒适性。
而在崎岖不平的道路上,需要更坚固的悬架系统来保证车辆的稳定性和可靠性。
汽车钢板弹簧悬架设计

汽车钢板弹簧悬架设计1.弹簧选用汽车钢板弹簧主要由弹簧片组成,弹簧片之间通过铆钉连接。
在选用弹簧片时,需要根据车辆的重量和使用环境来确定合适的弹簧片数量和材料。
弹簧片的数量越多,弹簧刚度就越高,对于重负荷的车辆,需要选择刚度较高的弹簧片。
弹簧片的材料可以选择高强度钢板,以提高弹簧的寿命和可靠性。
2.弹簧布局汽车钢板弹簧的布局主要包括前后轴的弹簧组织和布置。
为了保证车辆的稳定性和悬挂的平衡性,前后轴的弹簧刚度需要相对均衡,可以根据车辆设计的重心位置和工况来确定各个轴的刚度比例。
同时,在弹簧的布置上,需要考虑到弹簧的有效作用长度,以及与减震器和车架的配合情况,确保弹簧在工作时能够正常运动。
3.减震器选用汽车钢板弹簧悬架中的减震器起到控制弹簧振动和提高行驶平稳性的作用。
减震器的选用需要根据车辆的重量和行驶条件来确定。
一般而言,重负荷的车辆需要选择刚度较高的减震器,而轻负荷的车辆可以选择较为柔软的减震器。
常见的减震器有液压减震器、气压减震器和双作用减震器等。
在实际应用中,需要根据车辆的需求和预算来选择合适的减震器。
4.悬挂系统调校在汽车钢板弹簧悬架的设计中,调校是一个关键的环节。
通过调整弹簧刚度、减震器阻尼、弹簧预紧力等参数,可以实现悬挂系统的理想性能。
悬挂系统的调校需要根据车辆的用途和乘客的需求来进行,例如,运载车辆和越野车辆需要更硬的悬挂系统来增加稳定性和通过性,而乘用车和豪华车则需要更柔软的悬挂系统来提高乘坐舒适性。
在进行悬挂系统的调校时,需要进行一系列的试验和数据分析,以确定最佳的参数组合。
物理试验和计算机仿真是常用的手段。
通过调整参数和验证,最终确定悬挂系统的设计。
总之,汽车钢板弹簧悬架设计需要考虑弹簧选用、弹簧布局、减震器选用和悬挂系统调校等方面。
通过合理的设计和调校,可以实现符合车辆需求和乘客舒适性要求的悬挂系统。
汽车设计悬架设计(技术分享)

W0≥[FW(L-ks)]/4[σW] 式中,[σW]为许用弯曲应力。 对于55SiMnVB或60Si2Mn等材料,表面经喷丸处理后,推荐[σW]在 下列范围内选取;前弹簧和平衡悬架弹簧为350-450N/mm2;后副簧 为220-250N/mm2。
8
1 非独立悬架
纵置钢板弹簧为弹性元件兼作导向装置
优点
➢结构简单 ➢制造容易 ➢维修方便 ➢工作可靠
缺点
➢汽车平顺性较差 ➢高速行驶时操稳性差 ➢轿车不利于发动机、行李舱的布置
应用 :货车、大客车的前、后悬架以及某些轿车的后悬架
建筑分析
9
2 独立悬架
➢簧下质量小;
➢悬架占用的空间小;
优点
➢可以用刚度小的弹簧,改善了汽车行驶平顺性; ➢由于有可能降低发动机的位置高度,使整车的质心高度下
建筑分析
21
§6-3 悬架主要参数的确定
一、前后悬架的静挠度、动挠度的选择
1、概念
1)静挠度
2)动挠度
汽车满载静止时悬架上的载荷Fw与此时 悬架刚度c之比,即fc=Fw/c。
指从满载静平衡位置开始悬架压缩到结 构允许的最大变形(通常指缓冲块压缩 到其自由高度的1/2或2/3)时,车轮 中心相对车回(或车身)的垂直位移
n1 c1 / m1 / 2
n2 c2 / m2 / 2
式中,c1、c2为前、后悬架的刚度(N/cm); m1、m2为前、后悬架的簧上质量(kg)。
建筑分析
23
当采用弹性特性为线性变化的悬架时,前、后悬架的静挠度 可用下式表示
式中,
fc1=m1g/c1 fc2=m2g/c2
g为重力加速度(g=981cm/s2)。
浅谈汽车底盘悬架结构设计要点

浅谈汽车底盘悬架结构设计要点近年来,随着社会的发展,人们的生活水平逐渐的提高,汽车的发展也越来越广泛。
人们对于汽车的需求量也在不断增长,这在加剧汽车行业市场竞争的同时,也对汽车产品的更新产生了一定的推动作用,而底盘作为汽车的重要组成部分,其技术水平会直接影响到汽车的性能。
标签:汽车底盘;悬架结构;设计要点引言汽车底盘作为汽车最具有科技含量的一部分结构,其主要功能在于支撑和安装各种各样的零部件,在接受发动机设备引擎动力的基础上,从而实现发动并行驶的最终目的。
因此,由于汽车底盘的基础作用,做好汽车底盘维修保养工作可以保证汽车安全和汽车的稳定行驶,实现现代汽车工业良好有序发展。
1整车工作原理汽车在平行于地面的平面上行驶,并且轮胎靠着地面放置以确保操作期间的稳定性。
转向力矩电机固定于车架法兰盘上,可以带动上转向臂及其他部件绕电机主轴旋转,理论转角为360°.上转向臂与转向力矩电机采用键连接,通过加紧装置固定,可绕转向电机主轴旋转。
减震器上部与上转向臂的下部、减震器下部与下转向臂上部采用固定连接,随着上转向臂一起转动,可以减小车体的震动。
下转向臂的另一端固定地连接到支撑轴并随减震器一起旋转。
撑轴一端固定在下转向臂,一端安装有轴承,安装有轴承的一端与轮毂连接在一起,使得轮胎随着支撑轴一起旋转,从而实现汽车的转向驱动电机安装在轮毂内,以驱动轮毂绕支撑轴旋转,从而驱动车辆。
2汽车底盘悬架结构设计要点及优化2.1连续控制底盘系统该系统对于马力以及制动力的输出主要是借助车轮速度、方向盘角度以及横向、纵向、倾斜感应器来实现的,通过这些数据,系统可以对悬挂以及动力分布进行适当的调整。
在底盘分布的传感器,能够对车身进行测量,明确车身相对于道路的垂直、横向纵向加速度,之后借助稳定控制系统和防抱死制动器,对方向盘速度边转角、车轮垂直运动、车轮旋转、发动机扭矩等相关数据进行测量。
在整个过程当中,主要是通过传感器对上述数据进行收集并上传,之后再由微处理器,将数据反馈到减震器,每秒会刷新数据约500次左右。
悬架设计总结

悬架是现代汽车上重要总成之一,它把悬架与车轴弹性地连接起来。
其主要任务是传递作用在车轮与车架之间的一切力与力矩,并且缓和路面传给车架的冲击载荷,衰减由此引起的承载系统的振动,保证汽车的行驶平顺性,保证车轮在路面不平和载荷变化时有理想的运动特性,保证汽车的操纵稳定性,使汽车获得高速行驶能力。
为满足上述功能,悬架系统设计需满足下述要求:1) 保证汽车有良好的行驶平顺性。
2) 具有合适的衰减振动能力。
3) 保证汽车具有良好的操纵稳定性。
4) 汽车制动或加速时要保证车身稳定,减少车身纵倾,转弯时车身侧倾角要合适。
5) 结构紧凑、占用空间尺寸小。
6) 可靠地传递车身与车轮之间的各种力和力矩,在满足零部件质量要小的同时,还要保证有足够的强度和寿命。
上述六点对悬架系统设计要求,都需先对悬架系统运动进行分析,了解在各种载荷状态及不同工况下悬架系统运动状态。
问题解决过程:我公司生产HFJ6350、HFJ6351B 、HFJ6370、HFJ6380车前悬架为麦弗逊式独立悬架,后悬架为纵置板簧式非独立悬架。
这是一种典型的组合之一。
麦弗逊式悬架的特点是减振器兼作转向主销,可在工作站上建立运动模型,运用运动模块,通过两端凑的方法,求出各种载荷状态下悬架姿态。
钢板弹簧在整车上的布置情况,不仅影响整车的平顺性,而且也影响其操纵稳定性。
以下用三种方法对比分析了钢板弹簧系统关键点轨迹和关键角的变化。
一、 计算方法(附程序)如图1所示,假定主片长度L 在钢板弹簧运动中不变,即长度L 以外部分不参与变形;长度L 段的变形是纯圆弧型的,不考虑钢板弹簧悬架系统中橡胶件变形的影响。
而弧高Ha 和角θ间的关系(参见图2)为:Ha=R[cos (θ/2-α)-cos (θ/2)]式中 R= ⌒ PS /θ α=⌒ PQ / ⌒ PS ×θ所以Ha= ⌒ PS /θ×{cos[(1/2-⌒ PQ / ⌒ PS )×θ]-cos (θ/2)}由于 ⌒ PS 、⌒ PQ 为已知,所以每给定一个Ha 值,都有一个θ值与之对应,解此方程可用牛顿迭代法。
- 1、下载文档前请自行甄别文档内容的完整性,平台不提供额外的编辑、内容补充、找答案等附加服务。
- 2、"仅部分预览"的文档,不可在线预览部分如存在完整性等问题,可反馈申请退款(可完整预览的文档不适用该条件!)。
- 3、如文档侵犯您的权益,请联系客服反馈,我们会尽快为您处理(人工客服工作时间:9:00-18:30)。
汽车平衡悬架的设计要点东风汽车工程研究院陈耀明二00四年十一月目录前言1.四连杆机构的布置1)推力杆外端头的位置2)推力杆的高度3)推力杆的斜度4)推力杆的长度5)推力杆在横向平面的布置(1)上推力杆的布置(2)下推力杆的布置6)关于通用件的处理方法2.推力杆铰接头1)以橡胶体的变形来满足扭转和斜摆运动要求的铰接头(1)硫化粘结式(2)组装压入式①径向压缩型②轴向压缩型(3)粘结压缩式2)橡胶体与滑动衬套并用的铰接头(1)粘接复合衬套(2)聚胺脂衬套3.平衡轴总成1)平衡轴(1)整体式平衡轴(2)断开式平衡轴①左、右支架连接②左、右支架不连接2)平衡轴承(1)轴承(2)止推垫片与锁紧螺母(3)润滑与密封4.钢板弹簧的紧固与定位1)钢板弹簧根部的紧固2)平衡轴承毂3)钢板弹簧端部支承座(1)端座侧板的不对称布置(2)滑板设计(3)端座侧板设计(4)反向限位前言采用倒置半椭圆钢板弹簧做为弹性元件、纵置四连杆机构做为导向杆系的平衡悬架,因其结构简单、可靠,性能良好,长期以来成为6×6越野汽车、6×4自卸汽车和牵引汽车后悬架的传统结构。
尽管近年来为了提高平顺性和解决门对门运输中保持车高不变的问题,一些重型牵引汽车采用了空气悬架,但使用在路面条件苛刻的军用车辆和自卸汽车,这种平衡悬架仍有明显的优势和强大生命力。
我国从上世纪60年代就自主研发了具有独立自主产权的板簧平衡悬架,并且生产了三十几年。
与国外车型对比,我们也有许多独有的设计经验和优势。
撰写本文的目的就是为了总结这些设计经验,供有关的悬架设计师参考借鉴。
1. 四连杆机构的布置1) 推力杆外端头的位置要求对平衡轴对称,对中、后桥相关点位置相同,见图1。
要求对称于平衡轴:21δδ=要求对中、后桥相关位置相同:21γγ=从图中可知: 22δγβ+= (1)11δγα-= (2)将12γγ= , 12δδ= , 代入式(1),得11δγβ+= , 11γβδ-= , 代入式(2),得 βγγβγα-=+-=1112 ,∴221βαγγ+==2221αββαβδδ-=+-==式中 α、β为中、后桥倾角(设αβ>)。
1γ、2γ为端头连线与中、后桥中垂线的夹角1δ、2δ为端头连线与车架垂线的夹角2) 推力杆的高度推力杆在中、后桥上的外端头高低,按下列步骤布置: (1) 根据桥壳琵琶圆的大小,确定上推力杆端头位置,则确定了其离地高度a ,见图1; (2) 按b ≈2a 布置下推力杆位置,并核对离地间隙是否满足要求。
对于一根上杆、两根下杆的常规设计,这种布置使上、下杆受力基本相同。
3) 推力杆的斜度(1)下推力杆斜角2θ决定轴转向效应,即ε2tan θ=式中εφψd d =为轴转向效应系数,而ψ为轴转向角,φ为侧倾角。
一般纵置的中、后桥布置,稳态转向特性往往具有偏大的不足转应效应。
将2θ设计成如图1所示的布置,可减小不足转向,使转向灵活些,减少轮胎磨损,同时,簧载质体的离地间隙也高一些。
(2)上推力杆斜角1θ的布置,应结合2θ的状态,决定中、后桥的瞬时转动中心位置和倾角变化。
若1θ<2θ,即上、下推力杆延线交点(瞬心)在平衡轴中心线一侧,这样当车桥跳动时,中、后桥间的那根传动轴的运动干涉(花键窜动量和夹角变化)会比较小。
反之,1θ>2θ,则对中桥前的那一根传动轴的干涉较有利。
因为一般设计,中、后桥间传动轴较短,所以较常采用1θ<2θ。
若采用1θ=2θ,为平行四连杆机构,中、后桥作平移运动,跳动时无倾角变化。
4) 推力杆的长度在平衡轴支架及横梁结构允许条件下,推力杆应尽量选长一些,这样可减小车轮跳动时的纵向窜动量。
最好选取优先数作为长度值。
除非结构布置上的原因,绝大多数设计都选取上、下杆等长。
不等长上、下杆往往造成中、后桥跳动时有倾角变化。
纵置四连杆机构不像双横臂独立悬架,一般不采用不等长上、下臂结构。
但是,国外也有少数厂家采用上短下长的推力杆,以适度的倾角变化来换取轮胎接地点在纵向的移动量(轴距变化)达到最小,减少了轮胎磨损量。
5) 推力杆在横向平面的布置(1) 上推力杆的布置上推力杆的布置往往与中、后桥壳中心线对汽车中心线的偏置量1c 、2c 有关,一般有两种布置方案: ① 令上推力杆尽量靠近纵梁,使横梁受力分散,如图2中1A 、1B 所示。
这时应令21e e =,则桥壳上的支座成为对称件,横梁上支座可以是通用件。
因两支座分置,在其横梁背面应贴加强板。
② 令中、后桥上推力杆摆在一条直线上,如图2中2A 、2B 所示,这时221df f ==,d 为中、后桥中心线的偏距。
这种布置横梁受力集中,支座可通用且对置固定,桥上支座仍为对称件。
这种布置的优点仅是给车架内侧让出一些空间。
当然,也可以采用1A 、2B 或2A 、1B 的布置,视总体布置对空间的要求来确定,这时桥壳上支座可以是通用件。
当设计成通用件或对称件时,支座与销轴的定位搭接相关面应同向。
有些贯通桥往往使中、后桥壳中心线对齐,即o d =。
这时仍可以按上述两种方案中的一种来布置,也就是,分散布置(对称)或集中布置(通用)。
(2) 下推力杆的布置一般布置在中、后桥两侧尽量宽的位置,应注意到与轮胎(考虑装防滑链),制动气室等之间要留有间隙。
6) 关于通用件的处理方法按照上述方法来布置四连杆机构,其重要目的之一是可以将中、后桥对应的推力杆上、下支座设计成通用件。
这对于允许同轴扭转的球头销和带有滑动衬套的橡胶铰接头是毫无问题的,但对于不产生相对滑动的粘结式或压入式橡胶铰接头,若要求在设计位置橡胶处于自由状态,则各个铰接头芯轴定位平面互不相同,零件就不是完全通用的。
从图1可见,若1θ≠2θ,且内端头芯轴定位平面垂直于推力杆向,则上、下支座螺孔要倾斜且不等斜。
反之,若芯轴定位平面平行于支座底面,则它对于推力杆而言要偏转1θ和2θ。
对于外端头:在中桥上,其上推力杆芯轴定位面对桥垂线偏斜1θα+,其下推力杆芯轴定位面偏斜2θα+;在后桥上,其上推力杆芯轴定位面偏斜1θβ-,而下杆偏斜2θβ-。
当然,如果令11θβθα-=+ ,112δαβθ=-=,则上推力杆在中、后桥的支座完全通用;同理,令22θβθα-=+ ,122θαβθ=-=,下杆的支座也可通用。
这就是说,只要选择上、下推力杆互相平行,而且都垂直于外端头连线,则上、下支座均可制成通用件。
然而,如上文已述,推力杆倾斜角的选择有其他考虑因素,不一定能满足这个条件,那么,处理这个问题的比较好的方法可以有: (1) 如果设计时选择的相关角度,α、β、1θ、2θ都不大,即可令芯轴定位平面垂直于推力杆,而上、下支座的定位面都选择与其底面平行或垂直,这样的零件既通用,工艺性又好。
虽然在设计位置上,橡胶铰接头有预扭,但只要在极限跳动时,扭转角不超过许用值,则是好设计。
(2)如果超过许用值,就应选取在设计位置上没有预扭角,处理的方法有两种:①将支座设计成通用件,橡胶铰接头压入推力杆头时偏转一个角度。
这样,推力杆成为非通用件,但其基本元件仍是通用件。
应注意对推力杆要加注标记,以免装错。
②将推力杆设计成通用件,一般是令芯轴定位平面垂直于杆向,而支座的相关定位面按上述公式倾斜,这样的支座就不通用,但仅是局部不通用。
2.推力杆铰接头推力杆做为平衡悬架的导向机构,除了起到导向作用外,还要承受很大的杆向力。
而且,当车桥垂直跳动时,铰接头要发生同轴扭转;当车桥相对车身侧向倾斜时,要发生斜摆。
所以,推力杆铰接头的功能是承受沿杆向的径向负荷,同时,要允许有扭转和斜摆两个自由度的运动,见图3。
早期的铰接头多数采用球头球销结构,除了球碗采用聚胺脂橡胶、并有较好的密封措施的,可以获得较长的使用寿命外,其余如金属球碗、聚甲醛球碗等,可靠性和寿命都不理想。
近代的推力杆,多数采用橡胶铰接头结构,销轴也从悬臂锥销改为贯通两点固定(简支梁)。
橡胶铰接头的结构型式很多,大体可以分为两大类:1)以橡胶体的变形来满足扭转和斜摆运动要求的铰接头具体结构有下列3种:(1)硫化粘结式橡胶硫化后直接与内、外圈金属件的贴合面粘结在一起,见图4。
这种结构的最大缺点是粘结后在橡胶体内产生收缩应力(拉应力),对于自由面远比约束面小很多的衬套,收缩应力很大。
当铰接头承受负荷产生径向拉压,或扭转、斜摆角度很大时,衬套内的工作拉应力叠加收缩应力,使衬套工况更恶劣,缩短其使用寿命。
此外,一旦出现疲劳起因点(裂纹),由于一直存在拉应力,就促使裂纹迅速扩展,导致迅速损坏。
当然,若技术上可以达到高粘接强度,又有低收缩率和高强度的橡胶,这种结构也是可以使用的。
(2)组装压入式为了消除收缩拉应力,而且改变成为压应力,可以将橡胶体压入内、外圈之中,借助橡胶的回弹力,在橡胶与金属表面之间产生很大摩擦力,以阻止相对滑动。
由于一直存在残余压应力,可大大减低合成工作应力,且延长裂纹扩展时间。
组装压入式橡胶铰接头有两种结构:①径向压缩型制成的橡胶圈的内、外径与金属芯轴、外套均有一定过盈量(预压量),利用一套专用工具把橡胶圈挤入芯轴与外套之间。
根据铰接头受力情况,可以设计成单胶圈压入式或双胶圈压入式,见图5与图6。
后者的优点是在扭转和斜摆刚度相同的条件下,可增大径向刚度,从而降低了承受径向载荷时的应力,提高使用寿命。
采用拔细工艺,也可以达到径向压缩的目的。
即,制成的橡胶圈内、外径相对芯轴或套管,外圈皆无过盈量。
外圈的半成品为一根钢管,先将橡胶圈套在芯轴或套管上,再成串地装入钢管内,然后用拔丝机把钢管拔细,形成了对橡胶的压缩,最后在车床上切割就得到成品。
采用内套管可避免浪费外圈钢管。
径向压缩型铰接头的要害问题是胶圈的不稳定性,也就是说,铰接头工作时,受到径向拉压,或同轴扭转,或斜摆,当载荷去掉后,不能恢复到原来状态。
稳定性问题主要取决于橡胶圈的厚宽比。
由于推力杆铰接头工作时扭转和斜摆角比较大,胶圈的厚宽比一般都大于0.25。
在这种条件下,经多次试验证明,推力杆铰接头的胶圈不能维持稳定,工作后不能复原甚至脱落。
结论是径向压缩型橡胶圈不能用于推力杆铰接头,只能用于厚宽比很小的零部件,例如,钢板弹簧销的橡胶衬套。
②轴向压缩型将推力杆头的内圆加工成相对的两个锥孔,橡胶圈也制成两个锥圈,装入后靠端面挡板压紧,并用螺栓紧固,见图7。
也可以采用相反的结构,芯轴中部制成球形,外圈为柱形,两半胶圈制成相似形状,装入后用挡板压紧,然后用挡圈或螺栓固定。
这种结构简单可靠,但若推力杆扭转角很大,往往其压缩后的摩擦力不足以防止滑转。
所以,这种结构较多用在扭转角较小的部件,如减振器吊环。
(3)粘结压缩式单纯的硫化粘结式和组装压入式都有其致命的弱点,所以近年来人们广泛采用两者结合的方法,即,芯轴部分(扭转应力高,容易滑转)采用硫化粘接,外圈不粘接,套入之后靠端面挡板压缩,产生很大压应力和表面摩擦力,阻止外圈滑转,最后用挡圈或螺栓固紧。