毕业设计152辽宁工程技术大学电液伺服跑偏控制系统设计
电液伺服跑偏控制系统设计
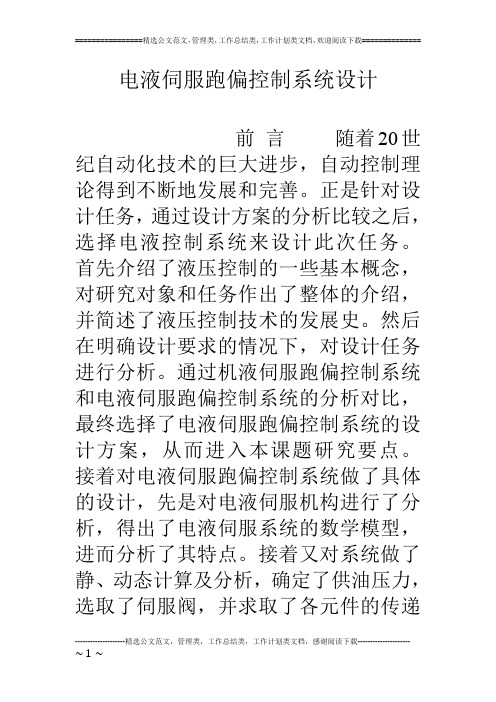
电液伺服跑偏控制系统设计前言随着20世纪自动化技术的巨大进步,自动控制理论得到不断地发展和完善。
正是针对设计任务,通过设计方案的分析比较之后,选择电液控制系统来设计此次任务。
首先介绍了液压控制的一些基本概念,对研究对象和任务作出了整体的介绍,并简述了液压控制技术的发展史。
然后在明确设计要求的情况下,对设计任务进行分析。
通过机液伺服跑偏控制系统和电液伺服跑偏控制系统的分析对比,最终选择了电液伺服跑偏控制系统的设计方案,从而进入本课题研究要点。
接着对电液伺服跑偏控制系统做了具体的设计,先是对电液伺服机构进行了分析,得出了电液伺服系统的数学模型,进而分析了其特点。
接着又对系统做了静、动态计算及分析,确定了供油压力,选取了伺服阀,并求取了各元件的传递函数,绘制了系统方块图,得出系统的各个参数。
然后还要对系统进行校正,得到更为优良的设计参数,使系统更加完善,以进一步提高系统的性能。
最后利用了先进电脑仿真技术MATLAB 对所做的系统进行仿真,通过改变系统的各个参数进行分析、比较,从而可看出系统的各个参数对系统的响应速度和稳定性的影响,本论文在王慧老师的悉心教导之下,通过研读各著作期刊,经过多次的修改。
于作者水平有限,论文中难免出现点差错,恳请读者指正。
1 1 绪论液压伺服控制系统是以液压动力元件作驱动装置所组成的反馈控制系统。
在这种系统中,输出量能够自动地、快速而准确地复现输入量的变化规律。
与此同时,还对输入信号进行功率放大,因此也是一个功率放大装置。
液压伺服控制系统是以液体压力能为动力的机械量自动控制系统。
按系统中实现信号传输和控制方式不同分为机液伺服系统和电液伺服系统两种。
机液伺服系统的典型实例是飞机、汽车和工程机械主离合器操纵装置上常用的液压助力器,机床上液压仿形刀架和汽车与工程机械上的液压动力转向机构等。
电液伺服控制系统是以液压为动力,采用电气方式实现信号传输和控制的机械量自动控制系统。
按系统被控机械量的不同,它又可以分为电液位置伺服系统、电液速度伺服控制系统和电液力控制系统三种。
电液位置控制系统设计
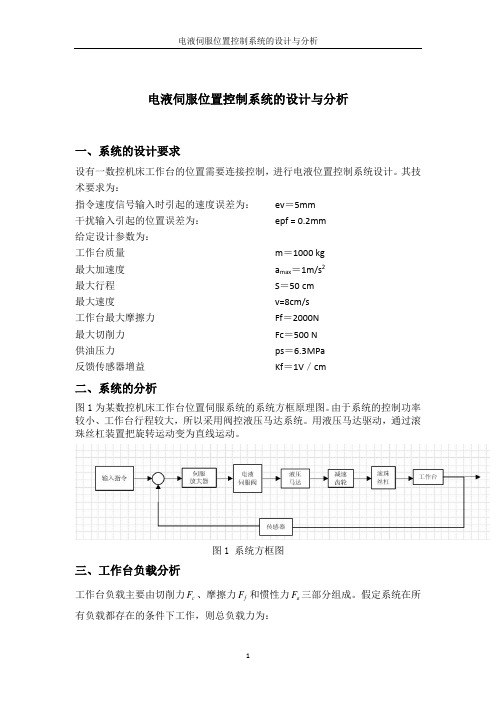
电液伺服位置控制系统的设计与分析一、系统的设计要求设有一数控机床工作台的位置需要连接控制,进行电液位置控制系统设计。
其技术要求为:指令速度信号输入时引起的速度误差为: ev =5mm 干扰输入引起的位置误差为: epf = 0.2mm 给定设计参数为: 工作台质量 m =1000 kg 最大加速度 a max =1m/s 2 最大行程 S =50 cm 最大速度 v=8cm/s 工作台最大摩擦力 Ff =2000N最大切削力 Fc =500 N 供油压力ps =6.3MPa 反馈传感器增益Kf =1V /cm二、系统的分析图1为某数控机床工作台位置伺服系统的系统方框原理图。
由于系统的控制功率较小、工作台行程较大,所以采用阀控液压马达系统。
用液压马达驱动,通过滚珠丝杠装置把旋转运动变为直线运动。
图1 系统方框图三、工作台负载分析工作台负载主要由切削力c F 、摩擦力f F 和惯性力a F 三部分组成。
假定系统在所有负载都存在的条件下工作,则总负载力为:max L c f a F F F F =++=3500N (1)四、动力元件参数选择(1) 工作台由液压马达经减速器和滚珠丝杠驱动。
根据力矩平衡方程,减速器输入轴力矩L T :/2L L T F t i π= (2)其中:t 为丝杠导程;i 为减速器传动比 液压马达最大转速max n 为:max max /n iv t = (3)其中:max v 为工作台的最大运动速度。
液压马达所需排量m Q 为6322/510m m L L Q D T p m ππ-===⨯ (4)其中:L p 为液压马达负载压力,一般取L p =23sp ,s p 为液压系统压力,m D 为液压马达弧度排量。
根据条件:i =2,t =1.2×210-m/r ,s p =63×105Pa 由式(2)、式(4)计算得:m D =0.8×610-3m /rad 所以,液压马达负载流量L q 为:536.6710/L q m s -=⨯ (5)伺服阀压降v p 为:max v s L p p p =- (6)考虑泄漏等影响,L q 增大15%, 4.6/min L q L =。
电液位置伺服控制系统实验
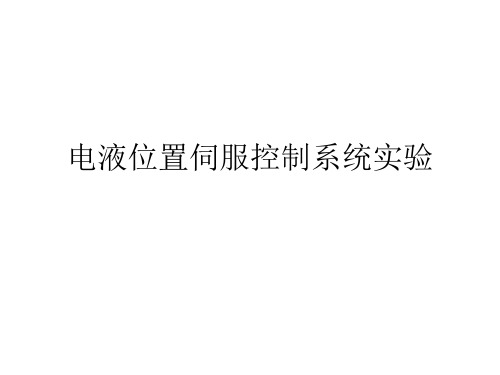
2
s2
2.834 2 0.866 1 2 s s s 1 2 14 .726 14 .726
正常参数时的ωc=2.78, ωh=14.8,Kg=19.1
增大Ki
正常参数
C (s) 4.611 R( s) 1 2 0.866 2 s 14 .726 2 s 14 .726 s 1
斜坡输入1
正弦输入
正弦输入,幅值5,频率1
正弦输入,幅值5,频率2.95
3 液压系统原理
压力传感器2
伺服缸
压力传感器3
平衡阀 电磁换向阀
蓄能器
电液伺服阀 压力传感器1
流量计2
流量计1 精滤器 电磁溢流阀
电机泵组
M
粗滤器 精滤器
4 系统控制原理
数据采集
参考输入
控制器
数模转换
功率放大
伺服阀
伺服缸
K i 73.746 KV 2.834 K d 1 26.022
K d1 h 代入系数得到 K d 1 26 .022 14 .726 h a a 0.12 (b K d 2 ) (b K d 2 ) (0.2 2.861) h h 0.866 2 K d1 a 2 K d 1 a 2 26.022 0.12
mmax 为能量输出单元在线 性范围内的最大值
r0,ml 为输入信号在线性范 围内的最大值
阶跃输入2.5
阶跃输入5
阶跃输入9
阶跃输入12
系统开环传递函数
KV C (s) R(s) 1 2 2 h s 2 s s 1 h h
Ki KV K d1
2)阀控缸微分方程
电液伺服控制系统

组成电液比例控制系统的基本元件: 1)指令元件 2 比较元件 3 电控器 4 比例阀 5 液压执行器 6 检测反馈元件
第6章 电液伺服控制系统
4
6.1 概述
6.1.2 电 液 比 例 控 制 系 统 的 特 点 及 组成
第6章 电液伺服控制系统
5
6.1 概述
电液比例控制的主要优点是: 1)操作方便,容易实现遥控 2 自动化程度高,容易实现编程控制 3 工作平稳,控制精度较高 4 结构简单,使用元件较少,对污染不敏感 5 系统的节能效果好。
6.功率放大级
功率放大级式比例控制放大器的 核心单元。由信号放大和功率驱动电路 组成。
根据功率放大级工作原理不同,分 为:模拟式和开关式。
第6章 电液伺服控制系统
29
6.3 电液比例电控技术
(1)模拟式功率放大级
第6章 ห้องสมุดไป่ตู้液伺服控制系统
30
6.3 电液比例电控技术
(2)开关式功率放大级
第6章 电液伺服控制系统
比例放大器根据受控对象、功率级工作原理不同,分为: 1 单路和双路比例控制放大器 2 单通道、双通道和多通道比例控制放大器 3 电反馈和不带电反馈比例控制放大器 4 模拟式和开关式比例控制放大器 5 单向和双向比例控制放大器 6 恒压式和恒流式比例控制放大器
第6章 电液伺服控制系统
16
6.3 电液比例电控技术
第6章 电液伺服控制系统
18
6.3 电液比例电控技术
第6章 电液伺服控制系统
19
6.3 电液比例电控技术
2.输入接口单元 (1)模拟量输入接口
2 数字量输入接口 3 遥控接口
第6章 电液伺服控制系统
20
电液伺服控制系统的设计
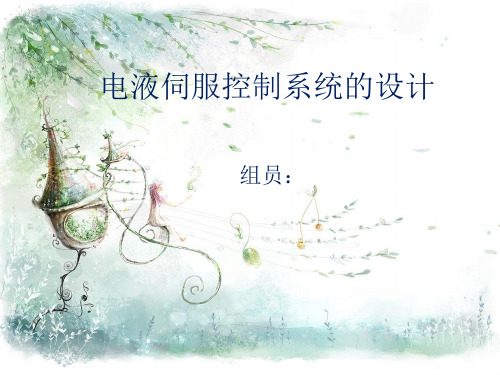
Ap ——液压缸活塞的有效面积;x p ——活塞的位移; 液压缸活塞的有效面积; 活塞的位移; 液压缸活塞的有效面积 活塞的位移 Ctp--总泄漏系数;Vt——液压缸进油腔的容积;βe—— 总泄漏系数; 液压缸进油腔的容积; 总泄漏系数 液压缸进油腔的容积 系统的有效体积弹性模量。 系统的有效体积弹性模量。
电液位置伺服控制系统以液体作为动 电液位置伺服控制系统以液体作为动 力传输和控制介质,利用电信号进行控制 力传输和控制介质, 输入和反馈。 输入和反馈。只要输入某一规律的输入信 执行元件就能启动、 号,执行元件就能启动、快速并准确地复 现输入量的变化规律。 现输入量的变化规律。电液位置伺服控制 系统是最为常见的液压控制系统, 系统是最为常见的液压控制系统,实际的 伺服系统无论多么复杂, 伺服系统无论多么复杂,都是由一些基本 元件组成的。系统的核心是电液伺服阀, 元件组成的。系统的核心是电液伺服阀, 它的性能直接影响甚至决定整个系统的性 功用十分重大。 能,功用十分重大。
系统数学模型的建立
(式中 k1=1/Ap) 计算得到负载扰动引起的稳态 误差为:ess=0.057×10-3(m)
(1)比例阀线性化流量方程 ) Q L = K q xv − K c p L (1) ) 式中K 比例阀流量增益; 比例阀流量- 式中 q——比例阀流量增益;K c ——比例阀流量-压力 比例阀流量增益 比例阀流量 系数; 负载压力; 比例阀阀芯位移。 系数;p L——负载压力;xv——比例阀阀芯位移。 负载压力 比例阀阀芯位移 (2)伺服油缸流量连续性方程 )
系统的阶跃响应曲线
从上两幅图中可以看出, 从上两幅图中可以看出,系统的幅值裕度 与相角稳定裕度均为负值, 与相角稳定裕度均为负值,阶跃响应曲线 为发散振荡,说明系统是不稳定的, 为发散振荡,说明系统是不稳定的,必须 校正。 校正。
电液伺服比例控制实训系统技术方案(纯方案,6页)
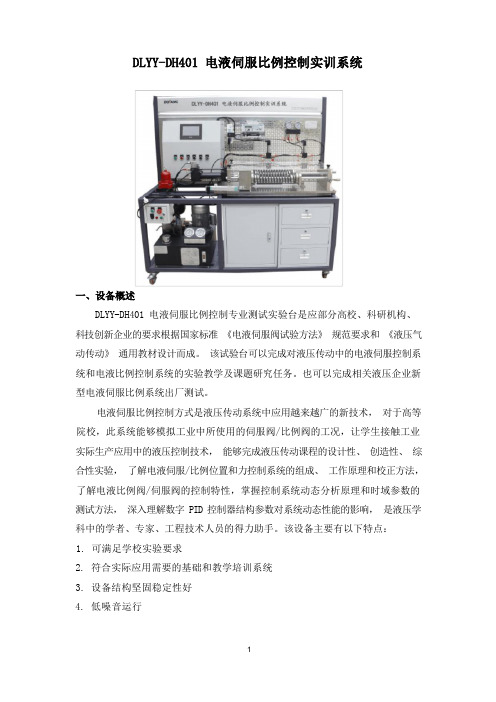
DLYY-DH401 电液伺服比例控制专业测试实验台是应部分高校、科研机构、科技创新企业的要求根据国家标准《电液伺服阀试验方法》规范要求和《液压气动传动》通用教材设计而成。
该试验台可以完成对液压传动中的电液伺服控制系统和电液比例控制系统的实验教学及课题研究任务。
也可以完成相关液压企业新型电液伺服比例系统出厂测试。
电液伺服比例控制方式是液压传动系统中应用越来越广的新技术,对于高等院校,此系统能够模拟工业中所使用的伺服阀/比例阀的工况,让学生接触工业实际生产应用中的液压控制技术,能够完成液压传动课程的设计性、创造性、综合性实验,了解电液伺服/比例位置和力控制系统的组成、工作原理和校正方法,了解电液比例阀/伺服阀的控制特性,掌握控制系统动态分析原理和时域参数的测试方法,深入理解数字 PID 控制器结构参数对系统动态性能的影响,是液压学科中的学者、专家、工程技术人员的得力助手。
该设备主要有以下特点:1. 可满足学校实验要求2. 符合实际应用需要的基础和教学培训系统3. 设备结构坚固稳定性好4. 低噪音运行5. 系统配置优化合理,安全性高6. 布局清晰而耐人寻味的设计7. 钢架结构、平台式实验台、基础稳定,刚度大,无变形,无振动。
8. 液压泵站采用内置式低噪音齿轮泵;配高精度滤油器,提供恒压源,恒流源。
9. 伺服阀和比例阀采用品牌工业元件,采用工业化设计,使用整体。
10. 采用触摸屏,带高速运算功能的 PLC 模块。
11. 采用 PID 控制模块,能够是传动系统达到快、准、稳的效果12. 实验台运行可靠、安全。
它由航空铝合金和工业型钢组合而成,由液压系统、实验台面、操控模组三部分组成。
外观设计美观大方。
同时配备喷塑钣金材料做成的橱柜,橱柜分为左右两组,各自有独立的锁闭系统。
可方便各元件的存储。
四个脚轮以便于移动和安装。
该数据采集系统可以同时对液压回路进行压力、位移、等参数进行测量,并通过对应接口上传至人机界面动态显示。
伺服电机控制系统毕业设计
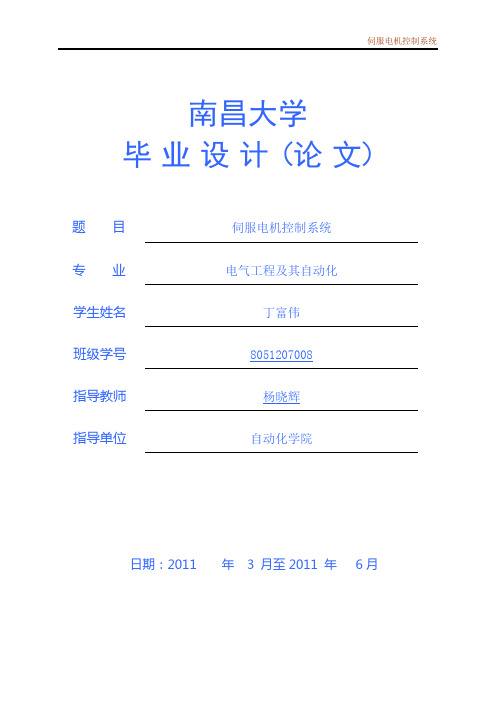
由于直流伺服电动机既具有交流电动机的结构简单、运行可靠、维护方便等一系列优点,又具有直流电动机的运行效率高、无励磁损耗以及调速性能好的特点,故在当今国民经济的各个领域,如医疗器械、仪表仪器、化工、轻纺以及家用电器等方面的应用日益普及。直流伺服电动机的应用主要分为以下几类:
定速驱动机械
一般不需要调速的领域以往大多是采用三相或单相交流异步和同步电机。随着电力电子技术的进步,在功率不大于 且连续运行的情况下,为了减少体积,节省材料,提高效率和降低能耗,越来越多的电机正被直流伺服电动机逐步取代,这类应用:有自动门、电梯、水泵、风机等。而在功率较大的场合,由于一次成本和投资较大,除了永磁电机外还要增加驱动器,因此目前较少有应用。
系统给定转速由键盘输入,并能实时显示转速;功率芯片选用性能价格比较高的快速MOSFET;功率驱动选用带保护电路和过流输出的集成芯片IR2130,可实现电机的高频快速起动;系统还设置了电流采样电路,与速度反馈电路组成双闭环系统,可以实现电机的快速起动并获得良好的带负载性能,达到了设计任务书的要求。
软件方面根据直流伺服电动机的组成、脉宽调制和工作原理,结合80C196MC的硬件部分和软件编程的特点,设计了无刷直流调速系统的软件。系统软件分为主程序和中断程序两大主块,主程序完成系统的初始化, LED显示器扫描和键盘功能处理程序等部分。
进入90年代以来,随着电力电子工业的飞速发展,许多高性能半导体功率器件,如GTR、MOSFET、IGBT、MCT等相继问世,以及微处理器、大规模集成电路技术的发展,逆变装置也发生了根本性的变化。这些开关器件本身向着高频化、大容量、智能化方向发展,并出现集半导体开关、信号处理、自我保护等功能为一体的智能功率模块(正M)和大功率集成电路,使直流伺服电动机的关键部件之一―逆变器的成本降低,且向高频化、小型化发展。同时,永磁材料的性能不断提高和完善,特别是钕、铁、硼永磁材体的热稳定性和耐腐蚀性的改善,加上永磁电机研究和开发经验的逐步成熟,稀土永磁直流伺服电动机的应用和开发进入一个新阶段,目前正朝着超高速、高转矩,高功能化、微型化方向发展[3]。
电液伺服系统的建模与控制

电液伺服系统的建模与控制1. 引言电液伺服系统是一种广泛应用于工业控制领域的系统,它可以通过控制液压执行器的输出来实现对机械运动的精确控制。
本文将介绍电液伺服系统的建模与控制方法,以帮助读者更好地了解和应用这一技术。
2. 电液伺服系统的概述电液伺服系统由液压执行器、电液伺服阀、传感器和控制器等组成。
液压执行器负责将液压能转化为机械能,电液伺服阀负责控制液压执行器的动作,传感器用于反馈系统状态信息,控制器根据传感器的反馈信息对电液伺服阀进行控制。
3. 电液伺服系统的建模建模是控制系统设计的第一步,对于电液伺服系统也是不可或缺的。
电液伺服系统的建模既可以基于理论模型,也可以基于实验数据进行。
3.1 理论模型在理论模型建模中,我们需要考虑液压执行器、电液伺服阀和控制器的动态特性。
液压执行器的动态特性可以用惯性、摩擦、密封等参数来描述。
电液伺服阀的动态特性可以用阀门的流量-压力特性和阀门饱和现象来描述。
控制器的动态特性通常可以用传统的PID控制算法进行建模。
3.2 实验模型在实验模型建模中,我们需要通过实验得到系统的频率响应和传递函数,并将其转化为数学模型。
这种方法对于实际系统的建模更加准确,但也需要大量的实验数据和较高的技术要求。
4. 电液伺服系统的控制控制是电液伺服系统中最关键的环节之一。
常用的电液伺服系统控制方法有位置控制、速度控制和力控制等。
4.1 位置控制位置控制是电液伺服系统中最基本的控制方法之一。
通过控制电液伺服阀的输出来控制液压执行器的位置。
传感器将执行器的位置信息反馈给控制器,控制器根据反馈信息进行调节,使得系统实现期望的位置跟踪。
4.2 速度控制速度控制是电液伺服系统中常用的控制方法之一。
通过控制电液伺服阀的输出来控制液压执行器的速度。
传感器将执行器的速度信息反馈给控制器,控制器根据反馈信息进行调节,使得系统实现期望的速度跟踪。
4.3 力控制力控制是电液伺服系统中一种高级的控制方法。
- 1、下载文档前请自行甄别文档内容的完整性,平台不提供额外的编辑、内容补充、找答案等附加服务。
- 2、"仅部分预览"的文档,不可在线预览部分如存在完整性等问题,可反馈申请退款(可完整预览的文档不适用该条件!)。
- 3、如文档侵犯您的权益,请联系客服反馈,我们会尽快为您处理(人工客服工作时间:9:00-18:30)。
前言随着20世纪自动化技术的巨大进步,自动控制理论得到不断地发展和完善。
本文正是针对设计任务,通过设计方案的分析比较之后,选择电液控制系统来设计此次任务。
本文首先介绍了液压控制的一些基本概念,对研究对象和任务作出了整体的介绍,并简述了液压控制技术的发展史。
然后在明确设计要求的情况下,对设计任务进行分析。
通过机液伺服跑偏控制系统和电液伺服跑偏控制系统的分析对比,最终选择了电液伺服跑偏控制系统的设计方案,从而进入本课题研究要点。
接着本文对电液伺服跑偏控制系统做了具体的设计,先是对电液伺服机构进行了分析,得出了电液伺服系统的数学模型,进而分析了其特点。
接着又对系统做了静、动态计算及分析,确定了供油压力,选取了伺服阀,并求取了各元件的传递函数,绘制了系统方块图,得出系统的各个参数。
然后还要对系统进行校正,得到更为优良的设计参数,使系统更加完善,以进一步提高系统的性能。
最后利用了先进电脑仿真技术MATLAB对所做的系统进行仿真,通过改变系统的各个参数进行分析、比较,从而可看出系统的各个参数对系统的响应速度和稳定性的影响。
本论文在王慧老师的悉心教导之下,通过研读各著作期刊,经过多次的修改。
由于作者水平有限,论文中难免出现点差错,恳请读者指正。
1 绪论液压伺服控制系统是以液压动力元件作驱动装置所组成的反馈控制系统。
在这种系统中,输出量(位移、速度、力等)能够自动地、快速而准确地复现输入量的变化规律。
与此同时,还对输入信号进行功率放大,因此也是一个功率放大装置。
液压伺服控制系统是以液体压力能为动力的机械量(位移、速度和力)自动控制系统。
按系统中实现信号传输和控制方式不同分为机液伺服系统和电液伺服系统两种。
机液伺服系统的典型实例是飞机、汽车和工程机械主离合器操纵装置上常用的液压助力器,机床上液压仿形刀架和汽车与工程机械上的液压动力转向机构等。
电液伺服控制系统是以液压为动力,采用电气方式实现信号传输和控制的机械量自动控制系统。
按系统被控机械量的不同,它又可以分为电液位置伺服系统、电液速度伺服控制系统和电液力控制系统三种。
电液位置伺服控制系统适合于负载惯性大的高速、大功率对象的控制,它已在飞行器的姿态控制、飞机发动机的转速控制、雷达天线的方位控制、机器人关节控制、带材跑偏、张力控制、材料试验机和加载装置等中得到应用。
1.1 液压伺服控制系统的组成液压伺服控制系统不管多么复杂,都是由以下一些基本元件组成的,如图1-1所示:图1-1 电液伺服控制系统Fig.1-1 electro-hydraulic servo system1)输入元件——也称指令元件,它给出输入信号(指令信号)加于系统的输入端。
该元件可以是机械的、电气的、气动的等。
如靠模、指令电位器或计算机等。
2)反馈测量元件——测量系统的输出并转换为反馈信号。
这类元件也是多种形式的。
各种传感器常作为反馈测量元件。
如测速机、阀套,以及其它类型传感器。
3)比较元件——相当于偏差检测器,它的输出等于系统输入和反馈信号之差,如加法器、阀芯与阀套组件等。
4)液压放大与转换元件——接受偏差信号,通过放大、转换与运算(电液、机液、气液转换),产生所需要的液压控制信号(流量、压力),控制执行机构的运动,如放大器、伺服阀、滑阀等。
5)液压执行元件——产生调节动作加于控制对象上,实现调节任务。
如液压缸和液压马达等。
6)控制对象——被控制的机器设备或物体,即负载。
此外,系统中还可能有各种校正装置,以及不包含在控制回路内的能源设备和其它辅助装置等。
液压控制元件、执行元件和负载在系统中是密切相关的,把三者的组合称之为液压动力机构。
凡包含有液压动力机构的反馈控制系统统称为液压控制系统。
1.2 液压伺服控制的分类液压伺服控制系统可按下列不同的原则进行分类,每一种分类的方法都代表系统一定的特点。
1.2.1按系统输入信号的变化规律分类液压伺服控制系统按输入信号的变化规律不同可分为:定值控制系统、程序控制系统和伺服控制系统。
1) 定值控制系统——当系统输入信号为定值时,称为定值控制系统。
对定值控制系统,基本任务是提高系统的抗干扰性,将系统的实际输出量保持在希望值上。
2) 程序控制系统——当系统的输入信号按预先给定的规律变化时,称为程序控制系统。
输入量总在频繁的变化,系统的输出量能够以一定的准确度跟随输入量的变化而变化。
3) 伺服控制系统——也称随动系统,其输入信号是时间的未知函数,而输入量能够准确、快速地复现输入量的变化规律。
对伺服系统来说,能否获得快速响应往往是它的主要矛盾。
1.2.2按被控物理量的名称分类1) 位置伺服控制系统;2) 速度伺服控制系统;3) 加速度伺服控制系统;3) 力控制系统;4) 其它物理量的控制系统;1.2.3 按液压动力元件的控制方式分类1) 节流式控制(阀控式)系统——用伺服阀按节流原理来控制流入执行机构的流量或压力的系统。
2) 容积式控制(变量泵控制或变量马达控制)系统——利用伺服变量泵或变量马达改变排量的办法控制流入执行机构的流量和压力系统。
又可分为伺服变量泵系统和伺服变量马达系统两种。
1.2.4 按信号传递介质的形式分类1) 机械液压伺服系统;2) 电气液压伺服系统;3) 气动液压伺服系统;除以上几种分类方法外,还可将系统分为数字控制系统和连续时间控制系统,线性或非线性控制系统等。
1.3 液压伺服控制的优缺点1.3.1 液压伺服控制的优点液压伺服系统与其它类型的伺服系统相比,具有以下的优点:1) 液压元件的功率—重量比和力矩—惯量比大, 功率传递密度高, 可组成结构紧凑、体积小、重量轻、加速性好的伺服系统。
对于中、大功率的伺服系统,这一优点尤为突出。
2) 液压动力元件快速性好,系统响应快。
由于液压动力元件的力矩—惯量比(或力—质量比)大,所以加速能力强,能高速起动、制动与反向。
3) 液压伺服系统抗负载的刚度大,即输出位移受负载变化的影响小,定位准确,控制精度高。
4) 液压执行元件速度快, 在伺服控制中采用液压执行元件可以使回路增益提高、频宽高。
5) 液压控制系统可以实现频繁的带载起动和制动, 可以方便地实现正反向直线或回转运动和动力控制, 调速范围广、低速稳定性好、能量贮存和动力传输方便。
此外,液压伺服控制系统还有一些优点。
如液压元件的润滑性好,液压元件寿命长(与气动相比);调速范围宽、低速稳定性好;借助油管动力传输比较方便;借助蓄能器,能量储存比较方便;液压执行元件有直线位移式和旋转式两种,增加它的适应性;过载保护容易;解决系统温升问题比较方便;易于采取节能措施等1.3.2 液压伺服控制的缺点液压控制系统因有上述突出优点,使它获得广泛的应用。
但它还存在不少缺点,因而又使它的应用受到某些限制。
其主要缺点有:1) 液压元件,特别是精密的液压控制元件(如电液伺服阀)抗污染能力差,对工作油液的清洁度要求高。
污染的油液会使阀磨损而降低其性能,甚至被堵塞而不能正常工作。
这是液压伺服系统发生故障的主要原因。
因此液压伺服系统必须采用精过滤器。
2) 油液的体积弹性模量随油温和混入油中的空气含量而变化。
油液的黏度也随油温的变化而变化。
因此油温的变化对系统的性能有很大的影响。
3) 当液压元件的密封装置设计、制造或使用维护不当时,容易引起漏油,污染环境。
采用石油基液压油,在某些场合有引起火灾的危险。
采用抗燃液压油可使这种危险减小。
4) 液压元件加工精度要求高,成本高,价格贵。
5) 液压能源的获得、储存和远距离输送不如电气系统方便。
1.4 电液伺服控制系统的发展概况电液伺服控制技术最先产生于美国的MIT,后因其响应快、精度高,很快在工业界得到了普及。
电液伺服系统是一种以液压动力元件作为执行机构,根据负反馈原理,使系统的输出跟踪给定信号的控制系统。
它不仅能自动、准确、快速地复现输入信号的变化规律,而且可对输入量进行变换与放大。
作为控制领域的一个重要研究对象,电液伺服系统的设计理论和方法一直受到控制学科的指导和启发,经历了从线性到非线性智能控制的发展历程。
自从20世纪50年代麻省理工学院开始研究电液伺服系统的控制至以后的几十年中,电液伺服控制设计基本上是采用基于工作点附近的增量线性化模型对系统进行综合与分析。
PID 控制也因其控制律简单和易于理解,受到工程界的普遍欢迎。
然而,随着人们对控制品质要求的不断提高,电液伺服系统中PID 控制的地位发生了动摇。
这主要是由电液伺服系统的特性所决定的。
首先,电液伺服系统是一个严重不确定非线性系统,环境和任务复杂,普遍存在参数变化、外干扰和交叉耦合干扰;其次,电液伺服系统对频带和跟踪精度都有很高的要求。
如航空航天领域的系统频宽可达100Hz,已接近甚至超过液压动力机构的固有频率;另外,在高精度快速跟踪条件下,电液伺服系统中的非线性作用已不容忽视。
因此,可以说电液伺服系统是一类典型的未知不确定非线性系统。
这类系统扰动大、工作范围宽、时变参量多、难以精确建模。
这些特点对系统的稳定性、动态特性和精度都将产生严重的影响,特别是控制精度受负载特性的影响而难以预测。
例如,在材料试验机上,一般的动态加载多采用PID方式,对不同的试件,必须更改不同的PID参数,尤其是在材料变形的塑性区域,PID控制更加难以满足人们日益精细的控制要求。
70年代末至80年代初,计算机技术的发展为电子技术和液压技术的结合奠定了基础。
随后计算机控制在电液伺服系统中得到应用,使复杂控制策略的实现成为可能。
自适应控制的引入在一定程度上提高了系统的鲁棒性和控制精度,并在解决许多工程问题上发挥了积极的作用。
但在大扰动或系统存在严重不确定性时,自适应算法将趋向复杂,造成实现上的困难。
此外,它对非线性因素的处理能力也不尽人意。
近年来,控制学科的发展推动了电液伺服系统智能控制的研究。
对非对称缸系统,国内早期在WE试验机上有过研究;国外也进行了非对称缸系统建模和Robust控制的研究,如使用双函数边界法,将阀口流量、缸体运动的非线性用线性不确定方程来描述,将非线性问题转化为参数摄动问题进行处理。
此外,模糊控制、神经网络控制等非线性控制技术也都在电液伺服系统中取得了一席用武之地。
尤其是在模糊控制方面,经过多年的研究与实践,已由最初的技术应用研究,逐步形成了系统化的模糊控制设计理论和方法,并在电液伺服系统中取得成功的应用。
由此可见,电液伺服系统非线性智能控制研究的前景是十分广阔的。
然而,目前仍存在许多问题。
比如,应用方面的非线性系统理论的不完备,对诸如控制策略设计、稳定性分析以及非线性和智能控制理论方法在实际应用中存在的局限性缺乏有针对性的研究等。
此外,值得指出的是,虽然电液伺服系统中的非线性因素会对控制系统的设计产生一定的影响,但是这些非线性因素的影响在多数条件下远不如负载干扰的影响大。