全液压转向器选型计算
液压系统自动计算公式、液压缸选型计算、液压泵和马达选型计算、油箱和散热计算等

↓ 17.78 353.63
油缸强度和刚度校核 缸筒抗拉强度(Mpa) 油缸试验压力(bar) 安全系数 n 壁厚 (mm) 壁厚 (mm)
活塞杆强度校核 活塞杆抗拉强度(Mpa) 安全系数 n 活塞杆直径(mm)
400 100 5 5.00 4.79
→ 壁厚≤缸径/10 → 壁厚>缸径/10
235 5 40.316
350
平衡阀出口背压(bar)
25
活塞伸出 活塞收缩
负负载(Ton) 4.2 7
行程(mm) 605
无杆腔体积 (L) 有杆腔体积 (L) 体积变化 (L)
流量(L/min) 流量(L/min) 全差动流量(L/min)
无杆腔压力(bar) 有杆腔压力(bar)
安装距(mm)
3.04 2.28 0.76
壁厚≤缸径/10 壁厚>缸径/10
Py D 2
D 2
0 .4 Py 1 .3 Py
1
σ=σb/n
σb n=5 Py
系统流量(L/min)
30
系统压力(bar)
80
效率
0.9
系统功率(Kw)
4.4
无杆腔压力(bar) 有杆腔压力(bar) 伸出杆受压力(吨)
17.8 59.8 -1.4
油缸参数 缸径(mm) 80
无杆腔面积 (c㎡) 有杆腔面积 (c㎡) 油缸面积比
伸出速度(M/min) 收缩速度(M/min)
杆径(mm) 40
50.27 37.70 1.33
12 16
伸出阻力 (Ton)
6
收缩拉力 (Ton)
4
回油背压 (bar)
20
SUN平衡阀-油缸
平衡阀先导面积比
收割机液压系统的使用与维护

收割机液压系统的使用与维护【字体:大中小】【关闭】Operation And Maintenance Of The Harvester Hydraulic何培双陈军(天津特精液压股份有限公司300100)摘要:本文介绍了全喂入自走式联合收割机液压系统的原理及各主要液压元件功能结构,并提出了液压系统的使用与维护注意事项。
关键词:液压系统、收割机一、前言以新疆—2.0型为代表的自走式轴流谷物联合收割机占据了我国几乎三分之二的收割机市场,随着市场保有量的不断增大,收割机液压系统的使用与维护问题日益突出,每年都有相当数量的液压元件需进行维修服务。
由于收割机使用所特有的季节性,因维修而耽误麦收市场等问题日益突出,因此,了解收割机液压系统并正确使用与维护,对提高收割机的性能,及时抓住市场有着十分重要的意义。
二、收割机液压系统原理及主要技术指标1.图1为新疆—2.0型液压原理图。
系统由操纵和转向两个系统组成,转向系统用来图1 新疆—2.0收割机液压系统1-油箱2-油泵3-单路稳定阀4-全液压转向器5-转向油缸6-拨禾轮升降油缸7-收割台升降油缸8-行走无级变速油缸9-多路阀10-滤油器控制转向轮转向,操纵系统用来控制收割台和拨禾轮的升降以及联合收割机的行走无级变速。
两个系统共用一个油泵,组成并联系统。
液压油贮存于油箱1内,液压油被齿轮泵2吸入后,从油泵流出的高压油进入单路稳定分流阀,分流阀将高压油分成两路:一路进入操纵系统的多路阀9,按操纵的需要,可分别进入割台升降油缸、拨禾轮升降油缸或行走无级变速油缸,从多路阀流出的低压油经滤油器10流回油箱;另一路进入液压转向器4,按操纵需要进入转向油缸,实现液压转向,从液压转向器回油口流出的低压油也经滤油器10流回油箱,分流阀与多路阀内均装有安全阀,当油路发生意外情况,压力超过额定压力时,安全阀打开,高压油经滤清器直接流回油箱,保护液压元件不受损坏。
2.主要技术指标:油泵型号 CBE-532B-001(或CBE-525B-001)DF3-40B1多路阀额定流量 40L/minDF3-40B1多路阀额定工作压力 16Mpa(安全阀调整压力为10Mpa)FLD-D6单路稳定阀稳定流量6L/min全液压转向器型号 BZZ1-80全液压转向器排量 80ml/r三、主要液压元件结构、功能、及维护1.齿轮泵:①功能、结构:新疆—2.0型收割机采用CBE-532B(CBE-525B)齿轮油泵供油,结构如图2所示。
液压元件的计算与选择

第二节第四节液压元件的计算与选择一、液压泵首先依据初选的系统压力选择液压泵的结构类型,一般P<21MPa,选用齿轮泵和叶片泵;P>21MPa,则选择柱塞泵。
然后确定液压泵的最大工作压力和流量。
液压泵的最大工作压力必须等于或超过液压执行元件最大工作压力及进油路上总压力损失这两者之和,液压执行元件的最大工作压力可以从工况图或表中找到;进油路上总压力损失可以通过估算求得,也可以按经验资料估计,见表10-3。
液压泵的流量必须等于或超过几个同时工作的液压执行元件总流量的最大值以及回路中泄漏量这两者之和。
液压执行元件总流量的最大值可以从工况图或表中找到(当系统中备有蓄能器时,此值应为一个工作循环中液压执行元件的平均流量);而回路中泄漏量则可按总流量最大值的10%-30%估算。
在参照产品样本选取液压泵时,泵的额定压力应选得比上述最大工作压力高20%-60%,以便留有压力储备;额定流量则只需选得能满足上述最大流量需要即可。
液压泵在额定压力和额定流量下工作时,其驱动电机的功率一般可以直接从产品样本上查到。
电机功率也可以根据具体工况计算出来,有关的算式和数据见第三章相关部分或液压工程手册。
二、阀类元件阀类元件的规格按液压系统的最大压力和通过该阀的实际流量从产品样本上选定。
各类液压阀都必须选得使其实际通过流量最多不超过其公称流量的120%,否则会引起发热、噪声和过大的压力损失,使阀的性能下降。
选用液压阀时还应考虑下列问题:阀的结构形式、特性、压力等级、连接方式、集成方式及操纵方式等。
对流量阀应考虑其最小稳定流量;对压力阀应考虑其调压范围;对换向阀应考虑其滑阀机能等。
1.流量阀的选择选择节流阀和调速阀时还要考虑其最小稳定流量是否符合设计要求,一般中、低压流量阀的最小稳定流量为50ml/min~100ml/min;高压流量阀的最小稳定流量为min~20ml/min。
流量阀对流量进行控制,需要一定的压差,高精度流量阀进、出口约需1MPa的压差。
轮式挖掘机电控全液压转向系统设计及应用李耀

轮式挖掘机电控全液压转向系统设计及应用李耀发布时间:2021-07-23T15:37:13.800Z 来源:《建筑模拟》2021年第4期作者:李耀[导读] :针对轮式挖掘机的全液压转向系统在高速行驶时存在方向盘发飘问题,优化设计了电控全液压转向系统,增大车辆高速行驶时方向盘转向操纵力矩,提高了车辆高速行驶稳定性,为高机动轮式工程车辆的电控转向系统设计及应用提供了依据。
徐州徐工挖掘机械有限公司摘要:针对轮式挖掘机的全液压转向系统在高速行驶时存在方向盘发飘问题,优化设计了电控全液压转向系统,增大车辆高速行驶时方向盘转向操纵力矩,提高了车辆高速行驶稳定性,为高机动轮式工程车辆的电控转向系统设计及应用提供了依据。
关键词:轮式挖掘机转向系统电控全液压轮式挖掘机(以下简称轮挖)是以轮胎作为行走部件的挖掘机械,以其机动、灵活、高效等鲜明特点,在社区建设、市政工程等方面应用广泛[1]。
国产轮挖的行驶速度多为20-35 km/h,我司生产的轮挖行驶速度可达60 km/h以上,能够适应高速越野工况,在处置抗险救灾等紧急情况时更加高效灵活。
转向系统是影响轮式机械行驶安全的关键系统之一。
轮式工程机械普遍采用全液压转向系统[2],这种转向系统是在转向盘和转向传动机构之间、利用全液压转向器直接控制转向油缸实现转向,具有布置方便、操作轻便、反应快捷、转向灵活等优点[3]。
但该系统在应用中也可能产生转向轮跑偏、转向轮晃动严重、前轮摆头等问题[4],尤其应用在轮挖上时,在高速行驶状态下易出现方向盘发飘现象,影响车辆高速行驶的稳定性和驾驶员操作手感。
针对上述技术技术问题,本文优化设计了电控全液压转向系统,增大了车辆高速行驶时方向盘正常转向操纵力矩,解决了样机方向盘发飘问题。
1 样机主要参数底盘系统模型,其主要技术参数如表1所示。
2.1 总体方案电控全液压转向系统总体方案如图1所示。
转向管柱下端和角传动器相连实现换向,角传动器与全液压转向器之间设计有电控单元,电控单元与角传动器、全液压转向器之间通过联轴器相连。
基于AMESim的全液压转向系统的仿真分析
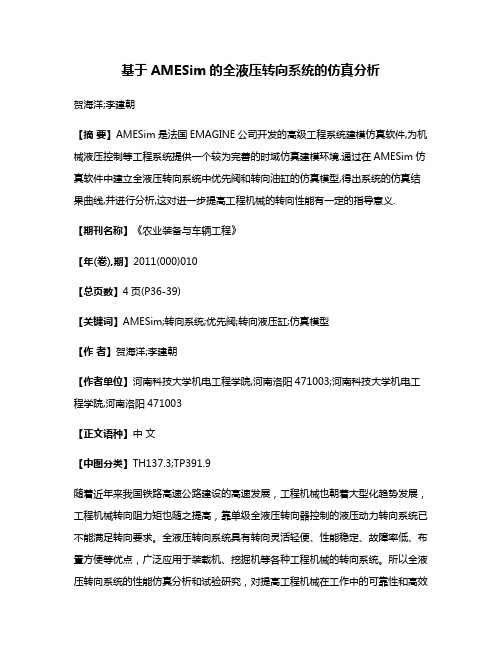
基于AMESim的全液压转向系统的仿真分析贺海洋;李建朝【摘要】AMESim是法国EMAGINE公司开发的高级工程系统建模仿真软件,为机械液压控制等工程系统提供一个较为完善的时域仿真建模环境.通过在AMESim仿真软件中建立全液压转向系统中优先阀和转向油缸的仿真模型,得出系统的仿真结果曲线,并进行分析,这对进一步提高工程机械的转向性能有一定的指导意义.【期刊名称】《农业装备与车辆工程》【年(卷),期】2011(000)010【总页数】4页(P36-39)【关键词】AMESim;转向系统;优先阀;转向液压缸;仿真模型【作者】贺海洋;李建朝【作者单位】河南科技大学机电工程学院,河南洛阳471003;河南科技大学机电工程学院,河南洛阳471003【正文语种】中文【中图分类】TH137.3;TP391.9随着近年来我国铁路高速公路建设的高速发展,工程机械也朝着大型化趋势发展,工程机械转向阻力矩也随之提高,靠单级全液压转向器控制的液压动力转向系统已不能满足转向要求。
全液压转向系统具有转向灵活轻便、性能稳定、故障率低、布置方便等优点,广泛应用于装载机、挖掘机等各种工程机械的转向系统。
所以全液压转向系统的性能仿真分析和试验研究,对提高工程机械在工作中的可靠性和高效性有着非常重要的意义[5]。
由法国EMAGINEG公司开发的AMESim,作为一款优秀的的仿真软件,已成为流体、机械、热分析等复杂系统建模和仿真的优先选择平台[1]。
本论文首先分析了全液压转向系统的工作原理及各部件组成,在此基础上结合转向系统原理,在AMESim平台对系统关键元件建模仿真,研究分析了输入信号下全液压转向系统关键元件的工作特性。
全液压转向系统集转向器和流量放大器于一体,既具有转向器的负荷传感功能,又具有流量放大功能。
在转向油路与工作油路同时工作的情况下,液压转向泵供油优先满足转向油路使用,剩余部分供给工作油路使用。
因此,它既能保证转向油路可靠工作,又减小了液压泵排量,达到节能的目的。
伺服液压系统选型计算说明(1)

伺服液压系统选型及计算说明1、客户提供伺服液压系统工作原理要求如下:电机:15kW ,工作压力15-16-25MPa伺服油缸:D=100㎜ d=70㎜,L=200㎜,压力等级25MPa垂直安装,中间铰接耳轴结构,工作状态为上下举升重物,传感器内置结构,内置传感器误差<0.1㎜,精度0.02%F.S,重复性<0.02%F.S系统要求:(1)整个系统控制8条油缸,两个为一组,分为四组,四组油缸平面布置为平行四边形分布,每组油缸两缸间距可调,调整行程为7米,此调整为机械结构调整,不用液压控制,但调整油缸的油管软管部分使用拖链形式,工作时有时8条油缸同步,有时为一组中的两缸同步,有时为一侧的两组四条缸同步,有时为一端的两组四条缸同步,同步位置高度误差小于0.2㎜。
(2)油缸升降速度可调。
(3)有防重物油缸急降功能。
(4)原理图完备,元器名细表型号完备,拖链型号。
(5) 液压系统阀件、泵为力士乐产品,油缸可选,但必须是知名品牌。
2、计算选型说明(1)系统额定流量的确定由电机功率15KW ,工作压力按照25MPa ,根据公式p=60Q P ⨯得出系统的额定流量不大于 Q=P p 60⨯=256015⨯=36L/min ,取总效率为0.8,则系统额定流量不大于36×0.8=28.8L/min ;(2)泵的选取按照上述计算的流量参数,选取力士乐排量为28ml/r 的恒压变量柱塞泵,采用6级电机,得额定流量为Q=1000min /r 960r /ml 28⨯=26L/min ; 油泵型号:A10VSO28DR/31R-PPA12NOO(3)计算油缸的速度按照8条油缸同时动作算得单只油缸通过的流量为:Q1=26/8=3.25L/min ,取3L/min 按照无杆腔计算,由公式Q=vA 算得油缸的速度: V=A Q =10104/10003⨯⨯⨯π=38.2cm/min=6.36mm/s ;取6mm/s ; (4)同步位置误差小于0.2mm 的时间要求同步位置控制精度0.2mm ,油缸以6mm/s 的速度运动,运行0.2mm 的时间为: t=0.2/6=0.03s=30ms ;此计算的数据30ms 即是该系统保证同步误差小于0.2mm 的总响应时间,这其中包括泵从零压到100%压力建立起来、阀的响应、位移检测的响应、控制系统的响应等因素在内。
全液压转向器选型计算
1.4、所需流量计算
4、所需流量的选择计算: Q=q0 x N/1000 式中: N为转向器输入的转速,流量的选择应保证在车辆的各种工况下转向器 能获得足够的流量,进而使转向器能够获得足够的转向速度。 转向器 转速参考: 50 mL/r ~250 mL/r 315 mL/r ~400 mL/r 500 mL/r ~1000 mL/r 100rpm 75rpm 60rpm
• 油缸的行程S(cm) 转向油缸的行程由转向臂的尺寸 及转角范围所决定。
1.3、转向器选择与计算
油缸通过大行程所需要的油的体积 V(ml) V=0.01 x S x A 转向器排量的计算q (mL/r) q=V/n 其中: n为转向轮从一个极限位置转到另一个极限位置时方向盘转过的圈数 ,用户应根据 需要选择,一般应为2.5~5.5圈 计算得到排量值后,应从本样本中查找最相近排量的转向器,如查到的排量为q0, 则转 向器的实际的圈数应为:n=V/q0
1.2、转向油缸的选择与计算
. 油缸的计算
• 油缸需要的推力: F=K2T/r 式中: F —油缸需要的力(N); T —见前步计算; r —最小力臂 (mm); K2 —系数1000; • 油缸的工作面积: A=10F/P 式中: A —油缸工作面积(mm²) P —油缸工作压力(Bar) * 在转向系统很少超载的车辆中,P值 为转向系统溢流阀设定压力的80%; 可 能严重超载的车辆, P值为转向系统溢 流阀设定压力的30%。 D—油缸内径mm d —活塞杆直径mm 1、 对等面积油缸: D=√4A/π+d² 2、 对并联油缸: D=√2A/π+d²/2 3、 对不等面积油缸: D=√4A/π+d² (d/D)²≤0.15
转向系统选型计算
全液压转向器应用基础知识
(4)在动力转向状态下,转向器的操作扭矩取决于弹簧 片的弹力。
1.5 BZZ1型全液压转向器的结构
1.5.1 常识资料: BZZ1型(开心无反应)转向器在中间位置时,转
开芯无反应、开芯有反应、闭芯无反应、闭芯有反应 (实际运用中,没有人使用)、负荷传感(和不同的 优先阀分别可以构成:静态系统、动态系统)、同轴 流量放大,等几类。
1.1、 镇江液压件厂有限责任公司全液压转向器产品分类情况:
BZZ系列:
BZZ1 -E50~1000(开芯无反应型) BZZ1 –E1000~2500(特大排量,开芯无反应型) BZZ2 -E50~1000 (开芯有反应型) BZZ3 -E50~1000 (闭芯无反应型) BZZ3–E1000~2500(特大排量,闭芯无反应型) BZZ5 -E50~1000(负荷传感型)
实现运动的目的:
1、通过另一侧排油腔容积腔的变化(容积腔的缩小)将经过计 量的油液排入转向器的左或右转向油口(A口或B口)。从而使 进入转向油缸的压力油与计量马达的排量建立起比例关系。
2、利用该转子的同向自转运动(与阀芯的转动方向相同)通过 齿轮联轴器的运动传递,将该同向转动运动反馈至起配油机构作 用的阀套上,使阀套与阀芯的转动实现随动,即:当方向盘带动 阀芯的转动一旦停止,在转子的自转运动带动下,阀套就会自动 将与阀芯间的配油槽关闭,使转向器进油口(P口)的压力油无 法进入转向器内部,转向器便立即处于中位状态,从而使进入转 向油缸的压力油容积与方向盘的转速建立起联系。
103S系列: 103S-1- 50~400-* 型 (小体积含集成阀,开芯无反应型)
叉车转向系统
叉车转向系统Steering System of Forklift Truck2010.10.目录第一节叉车转向系统概述 (1)1.1 叉车转向系统的定义、作用及叉车转向的特点 (1)1.2 与整车机动性有关的主要考核指标 (1)1.3 叉车转向系统的要求 (4)1.4 叉车转向系统的组成 (4)1.5 叉车转向系统的类型 (5)第二节全液压转向系统 (7)2.1 全液压转向系统的工作原理 (7)2.2 全液压转向系统的组成 (8)2.3 转向器的工作原理 (11)第三节叉车转向原理 (11)3.1 叉车转向原理 (11)3.2 车辆转向方式 (13)3.3 叉车在行驶中转向的基本条件 (15)第四节转向桥 (16)4.1叉车转向桥概述 (16)4.1.1 叉车转向桥的类型 (16)4.1.2 横置油缸转向桥的构造 (19)4.1.3 叉车转向桥的作用 (21)4.2 1-1.8t焊接转向桥结构 (22)4.3 转向桥安装及车轮定位型式 (25)4.3.1 转向桥的安装方式 (25)4.3.2 转向轮的定位 (25)4.3.3 叉车转向轮的定位方式 (27)第五节叉车转向系统的设计 (29)5.1 转向系统的设计方法 (29)5.2 横置油缸式转向梯形的优化设计 (30)5.2.1 转向梯形的类型 (30)5.2.2 曲柄滑块式转向梯形的优化设计 (32)5.3 转向传动机构的设计计算 (35)5.3.1 转向阻力矩的计算 (35)5.3.2 转向传动机构的受力计算 (38)5.4 转向桥的设计计算 (39)5.4.1 转向桥的受力分析 (39)5.4.2 转向桥强度计算 (40)5.5 衡量叉车转向操纵轻便性的主要指标 (41)5.5.1 方向盘最大作用力确定 (42)5.5.2 方向盘回转圈数 (43)5.6 全液压转向器的选择 (43)第六节叉车转向系统的试验 (45)6.1转向性能试验 (45)6.1转向桥的疲劳试验 (48)6.1.1 转向桥体疲劳试验台简介 (48)6.1.2 转向桥体的疲劳试验 (49)6.3 整车强化试验 (51)第七节转向系统的安装调试及维护保养 (51)7.1转向桥安装注意事项 (51)7.2转向桥的调整 (52)7.3转向系统的维护保养 (53)第八节转向系统的主要故障及排除 (53)8.1转向系统重装后检查 (53)8.2转向系统故障排除 (54)8.3 叉车的蛇行现象 (54)第一节 叉车转向系统概述叉车主要用于货场仓库的装卸或短途运输,工作场地较小,转向频繁,常需要原地转向。
YZC2.5液压转向系统设计选型
YZC2.5双钢轮振动压路机液压转向系统的设计梁勇1周细威2霍恒玉 3摘要:本文对YZC2.5型双钢轮振动压路机的全液压转向系统进行了参数计算和型号选定。
关键词:全液压;油缸;参数中图分类号:文献标识码:文章编号:现在,小型双钢轮振动压路机被广泛应用于市政、桥梁、公路建设中,具有广阔的市场前景。
由于该类型压路机,行驶速度一般不高,低于20km/h,因此多采用全液压转向方案。
下面对一种YZC2.5双钢轮振动压路机的全液压转向系统进行方案设计。
1、压路机基本参数工作质量: 2500Kg前轮分配质量: 1300Kg后轮分配质量: 1200Kg前轮静线载荷: 108N/cm后轮静线载荷: 100N/cm速度范围: 0—7Km/h理论爬坡能力: 30%转向角:±30°振动轮宽度: 1200mm振动轮直径:φ675mm2、 油缸参数确定:(双作用单活塞杆)⑴油缸行程:由结构设计确定L=125mm 。
⑵油缸推力转向时所需操纵力矩()()N y M F m N M gux m M M M kgm Bom ag m m l X M M M X g m M M L L L L H v H V L H V 30153130.039203920108004.081.925002122500,4.0,80012003232,23===⋅=⨯⨯⨯⨯⨯===+===⨯====+-油缸推力取整机重量取钢轮与地面附着系数公司量力臂经验公式来自钢轮压路机铰接转向当后轮力矩前轮力矩μμ⑶油缸内径确定:油缸推力:F L =30153N (见4.4部分计算)取活塞杆直径d=φ28mm 内径其中(42d pF D +=πp=100bar) mm 8.62)1028(1010053.304235=⨯+⨯⨯⨯=-π 圆整:D=63mm3、 转向泵参数确定:⑴全偏角所需流量:rcm Q t st t L D Q V v/10295.04/12563495.0442/4322=⨯⨯⨯==-==πηηπ效率取秒取全偏角所需时间 ⑵泵排量:r cm q r n n Q q p s p /2.1060060102min)/600(3=⨯==为发动机怠速时转速其中 圆整:发动机只能带BCN-E310泵,故取r cm q p /103=4、 全液压转向器选取全液压转向器采用BZZ1系列(无反应内反馈)据统计驾驶员方向盘最大转速是1~1.5r/s ,一般情况下方向盘总圈数2—4转。
- 1、下载文档前请自行甄别文档内容的完整性,平台不提供额外的编辑、内容补充、找答案等附加服务。
- 2、"仅部分预览"的文档,不可在线预览部分如存在完整性等问题,可反馈申请退款(可完整预览的文档不适用该条件!)。
- 3、如文档侵犯您的权益,请联系客服反馈,我们会尽快为您处理(人工客服工作时间:9:00-18:30)。
• 油缸的行程S(cm) 转向油缸的行程由转向臂的尺寸 及转角范围所决定。
1.3、转向器选择与计算
油缸通过大行程所需要的油的体积 V(ml) V=0.01 x S x A 转向器排量的计算q (mL/r) q=V/n 其中: n为转向轮从一个极限位置转到另一个极限位置时方向盘转过的圈数 ,用户应根据 需要选择,一般应为2.5~5.5圈 计算得到排量值后,应从本样本中查找最相近排பைடு நூலகம்的转向器,如查到的排量为q0, 则转 向器的实际的圈数应为:n=V/q0
1.4、所需流量计算
4、所需流量的选择计算: Q=q0 x N/1000 式中: N为转向器输入的转速,流量的选择应保证在车辆的各种工况下转向器 能获得足够的流量,进而使转向器能够获得足够的转向速度。 转向器 转速参考: 50 mL/r ~250 mL/r 315 mL/r ~400 mL/r 500 mL/r ~1000 mL/r 100rpm 75rpm 60rpm
转向系统选型计算
1.1、转动转向轮系总力矩的计算
(下面提供的选择计算方法仅供参考) 轮式杠杆型转向系统见右简图,其液压转 向器的选择计算如下:
1. 转动转向轮系所需要的总力矩 T=Wf · √B²/8+E² ·K1
式中: T —转动转向轮所需要的总矩(NM); W—转向桥所承受的重量(Kg); f —轮胎与地面的摩擦系数,见右图 B —轮胎的名义宽度(mm); E —偏心距(mm),见右图 K1 —系数0.01
1.2、转向油缸的选择与计算
. 油缸的计算
• 油缸需要的推力: F=K2T/r 式中: F —油缸需要的力(N); T —见前步计算; r —最小力臂 (mm); K2 —系数1000; • 油缸的工作面积: A=10F/P 式中: A —油缸工作面积(mm²) P —油缸工作压力(Bar) * 在转向系统很少超载的车辆中,P值 为转向系统溢流阀设定压力的80%; 可 能严重超载的车辆, P值为转向系统溢 流阀设定压力的30%。 D—油缸内径mm d —活塞杆直径mm 1、 对等面积油缸: D=√4A/π+d² 2、 对并联油缸: D=√2A/π+d²/2 3、 对不等面积油缸: D=√4A/π+d² (d/D)²≤0.15