烧结厂设计说明书
年产200吨YG类硬质合金的烧结车间设计说明书
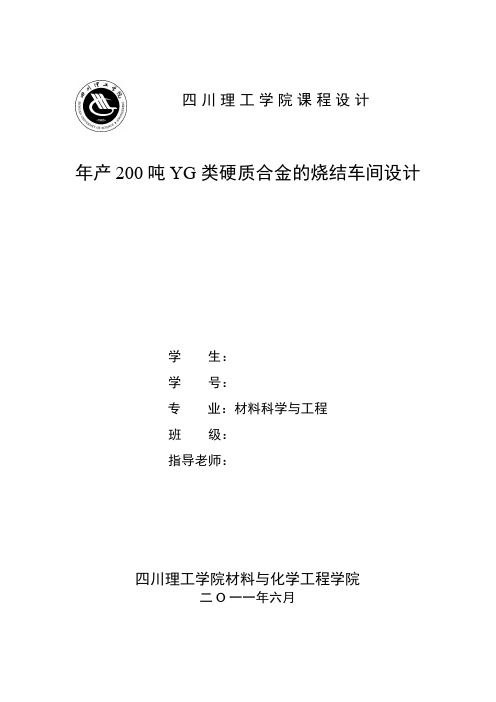
四川理工学院课程设计年产200吨YG类硬质合金的烧结车间设计学生:学号:专业:材料科学与工程班级:指导老师:四川理工学院材料与化学工程学院二O一一年六月摘要本文进行了年产200吨YG类硬质合金烧结车间的设计,介绍了WC-Co硬质合金的力学性能、应用、发展前景和常规制备方法等。
根据设计任务书的要求和相关粉末冶金车间设计规则制定了WC-Co硬质合金的工艺流程。
另外,主要针对球磨、压制和烧结三大工序进行了物料衡算,查阅资料对当前国内的相关设备进行了搜集整理,根据物料衡算和设备参数对球磨机、成型压力机、真空烧结炉等基本设备进行了选型和台数的合理选取,并进行了工作制度的合理性制定、设备的合理化布置及车间平面和厂区平面的布置。
最后,根据国家相关制图标准绘制了WC-Co硬质合金生产的工艺流程图、厂区平面布置图、烧结车间平面布置图和烧结车间的剖面图。
关键词:WC-Co硬质合金;物料衡算;设备选型;车间设计;烧结AbstractThe sintering workshop in where WC-Co hard alloys are produced for200tons per year has been designed in this paper.The mechanical properties of WC-Co hard alloy’s,its applications and prospects for development and the conventional preparation method were introduced.According to the design assignment and the correlative powder metallurgy workshop design practice,the WC-Co hard alloy technical process was developed.In addition,mainly for ball milling,pressing and sintering processes three primary working procedures were calculated material balance.Accessing to information on the current domestic related equipment were collected more,the ball mill,molding presses,vacuum sintering furnace and other basic equipment for the selection of a reasonable selection and number of units were carried out.The rationality of the working system formulated,equipments rationalization arrangement and workshop plane and factory plane layout were also carried out.Finally,the author has drawn the chart of the WC-Co hard alloy production flow,the floor-plans of the factory area and the sintering workshop,and the Sintering workshop sectional drawing according to the interrelated national charting standard.Key words:WC-Co hard alloy;material balance;equipment selection;workshop design;Sintering目录摘要 (I)Abstract (II)第一章绪论 (1)第二章概述 (3)2.1设计依据 (3)2.2设计原则 (3)2.3设计范围 (3)2.4原料及组成 (3)第三章WC—Co硬质合金生产的工艺过程 (4)3.1混合料的制备 (4)3.2干燥、筛分 (4)3.3掺胶制粒 (4)3.4成形 (5)3.5烧结 (5)3.5.1烧结过程 (5)3.5.2真空烧结 (6)第四章工厂工艺计算 (7)4.1工艺流程 (7)4.2物料衡算 (7)4.2.1物料平衡计算的方法和步骤 (7)4.2.2物料平衡的计算 (8)4.3工艺设备选型和计算 (11)4.3.1生产车间及设备简述 (11)4.3.2球磨机 (12)4.3.3振动过筛机 (14)4.3.4干燥柜 (14)4.3.5掺胶混合机 (15)4.3.6成型压力机 (16)4.3.7真空烧结炉 (17)4.3.8喷砂机 (19)第五章环境保护 (20)5.1粉尘污染 (20)5.2噪声污染 (21)第六章总结 (22)参考文献 (23)致谢 (24)附录 (24)第一章绪论硬质合金(Cemented carbide)是以难熔金属碳化物(WC、TiC等)为基体,铁族金属(Co、Fe、Ni等)作粘结剂,用粉末冶金方法制造的一种多相组合材料。
烧结设计手册
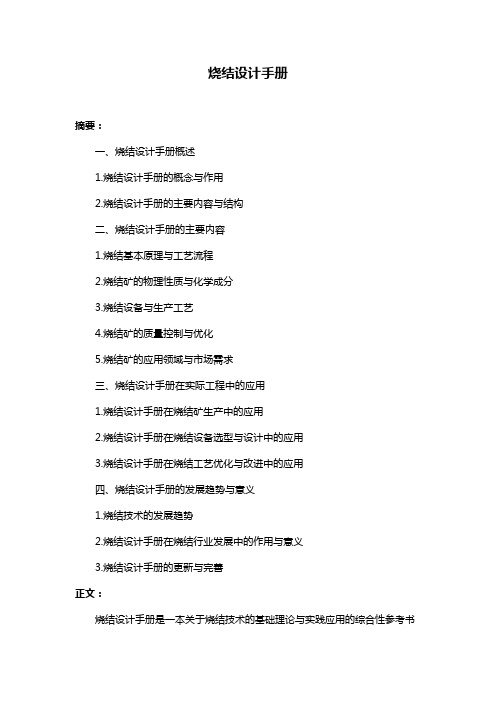
烧结设计手册摘要:一、烧结设计手册概述1.烧结设计手册的概念与作用2.烧结设计手册的主要内容与结构二、烧结设计手册的主要内容1.烧结基本原理与工艺流程2.烧结矿的物理性质与化学成分3.烧结设备与生产工艺4.烧结矿的质量控制与优化5.烧结矿的应用领域与市场需求三、烧结设计手册在实际工程中的应用1.烧结设计手册在烧结矿生产中的应用2.烧结设计手册在烧结设备选型与设计中的应用3.烧结设计手册在烧结工艺优化与改进中的应用四、烧结设计手册的发展趋势与意义1.烧结技术的发展趋势2.烧结设计手册在烧结行业发展中的作用与意义3.烧结设计手册的更新与完善正文:烧结设计手册是一本关于烧结技术的基础理论与实践应用的综合性参考书籍,旨在为烧结行业从业人员提供烧结工艺设计、设备选型、生产管理等方面的技术支持与指导。
本文将从以下几个方面对烧结设计手册进行详细介绍。
一、烧结设计手册概述烧结设计手册主要涵盖了烧结基本原理、工艺流程、设备选型、生产管理等方面的内容,为烧结行业从业人员提供了一套全面、系统的技术参考依据。
烧结设计手册不仅有助于提高烧结矿的生产质量和效率,还能推动烧结行业的技术进步与创新。
二、烧结设计手册的主要内容1.烧结基本原理与工艺流程烧结设计手册详细阐述了烧结的基本原理,包括物料混合、加热、烧结矿固结等过程。
同时,手册还介绍了烧结工艺流程,包括原料准备、配料、混合、烧结、破碎、筛选等环节。
2.烧结矿的物理性质与化学成分烧结设计手册对烧结矿的物理性质(如粒度、密度、强度等)和化学成分(如FeO、Fe2O3、SiO2等)进行了详细分析,以便为烧结矿的质量控制提供依据。
3.烧结设备与生产工艺烧结设计手册对烧结过程中的主要设备(如混合机、烧结机、破碎机、筛选机等)进行了详细介绍,包括设备类型、结构、工作原理等。
同时,手册还阐述了烧结生产工艺,如烧结矿的加热方式、烧结气氛、烧结速度等。
4.烧结矿的质量控制与优化烧结设计手册从原料准备、配料、混合、烧结等环节,详细介绍了烧结矿质量控制的方法与措施。
庚辰钢铁180m2烧结机委托设计说明书..
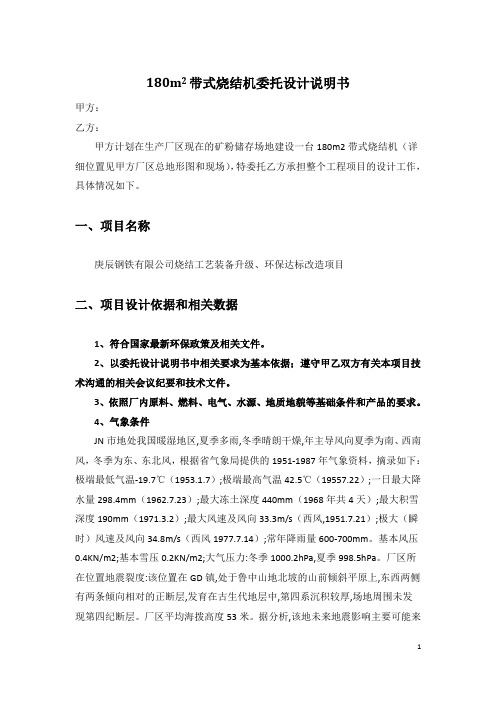
180m2带式烧结机委托设计说明书甲方:乙方:甲方计划在生产厂区现在的矿粉储存场地建设一台180m2带式烧结机(详细位置见甲方厂区总地形图和现场),特委托乙方承担整个工程项目的设计工作,具体情况如下。
一、项目名称庚辰钢铁有限公司烧结工艺装备升级、环保达标改造项目二、项目设计依据和相关数据1、符合国家最新环保政策及相关文件。
2、以委托设计说明书中相关要求为基本依据;遵守甲乙双方有关本项目技术沟通的相关会议纪要和技术文件。
3、依照厂内原料、燃料、电气、水源、地质地貌等基础条件和产品的要求。
4、气象条件JN市地处我国暖湿地区,夏季多雨,冬季晴朗干燥,年主导风向夏季为南、西南风,冬季为东、东北风,根据省气象局提供的1951-1987年气象资料,摘录如下:极端最低气温-19.7℃(1953.1.7);极端最高气温42.5℃(19557.22);一日最大降水量298.4mm(1962.7.23);最大冻土深度440mm(1968年共4天);最大积雪深度190mm(1971.3.2);最大风速及风向33.3m/s(西风,1951.7.21);极大(瞬时)风速及风向34.8m/s(西风1977.7.14);常年降雨量600-700mm。
基本风压0.4KN/m2;基本雪压0.2KN/m2;大气压力:冬季1000.2hPa,夏季998.5hPa。
厂区所在位置地震裂度:该位置在GD镇,处于鲁中山地北坡的山前倾斜平原上,东西两侧有两条倾向相对的正断层,发育在古生代地层中,第四系沉积较厚,场地周围未发现第四纪断层。
厂区平均海拨高度53米。
据分析,该地未来地震影响主要可能来自在鲁西南发生的强地震,该处影响烈度在Ⅵ-Ⅶ度间,基本定在Ⅵ度。
5、原料、燃料指标1) 精矿粉(常用有5种):TFe61~63%,其中含S≤0.2,P≤0.016;因业主方产品要求,烧结配料中精矿粉比例约占60~65%。
主抽风机及脱硫系统的设计需考虑配料的透气性、硫含量。
烧结设计手册

烧结设计手册(原创实用版)目录1.烧结设计手册概述2.烧结设计的基本原则3.烧结设计的具体步骤4.烧结设计的实例分析5.烧结设计手册的应用和意义正文烧结设计手册是一种为烧结过程提供指导的技术文档,旨在帮助工程师和研究人员进行烧结设计,以达到最佳的烧结效果。
本文将从烧结设计手册的概述、基本原则、具体步骤、实例分析以及应用和意义五个方面进行详细阐述。
一、烧结设计手册概述烧结设计手册包含了烧结过程中需要考虑的各种因素,如烧结材料的选择、烧结工艺的设定、烧结设备的选用等。
同时,它还提供了烧结过程中的各种计算公式和数据,以便工程师在进行烧结设计时能够有据可依。
二、烧结设计的基本原则在进行烧结设计时,需要遵循以下几个基本原则:1.确保烧结体的密度:烧结体的密度是评价烧结质量的重要指标,需要在设计过程中充分考虑。
2.控制烧结体的显微结构:烧结体的显微结构对材料的性能有着重要影响,需要通过合理的设计来控制。
3.优化烧结能耗:在保证烧结质量的前提下,尽可能降低烧结过程中的能耗,提高生产效率。
三、烧结设计的具体步骤烧结设计的具体步骤如下:1.确定烧结目标:明确烧结体的性能指标、尺寸和形状等要求。
2.选择烧结材料:根据烧结目标,选择合适的烧结材料,并进行材料性能分析。
3.设计烧结工艺:根据烧结材料的性能,设定烧结温度、保温时间等工艺参数。
4.选择烧结设备:根据烧结工艺要求,选择合适的烧结设备。
5.进行烧结试验:按照设计方案进行烧结试验,验证设计效果,并根据试验结果进行优化。
四、烧结设计的实例分析以烧结锌铁氧体为例,首先需要确定锌铁氧体的性能指标,如磁导率、矫顽力等。
然后根据这些指标,选择合适的锌铁氧体材料,并分析其烧结性能。
接着,设计烧结工艺,如烧结温度、保温时间等。
最后,选择合适的烧结设备进行烧结试验,并根据试验结果对设计进行优化。
五、烧结设计手册的应用和意义烧结设计手册在实际应用中具有重要意义,它可以帮助工程师和研究人员快速、准确地进行烧结设计,提高烧结质量,降低生产成本。
关于450m2烧结机料场设计说明10.22

关于450m2烧结机料场堆料方案
1、烧结机利用系数 1.5t/(m2.h),作业率95%,日产入炉烧结矿12500吨,含铁原料消耗12500吨/日(湿基)。
2、料场储存的物料品种及数量如下:
3、原料场地堆料布局
1)三条线堆料布局
料场设计长度560m,堆料机堆高10m,堆料宽度30m,矿粉堆密度2.2t/m3,所有物料堆间距3m。
2)两条线堆料布局
料场设计长度560m,堆料机堆高10m,堆料宽度45m,矿粉堆密度2.2t/m3,所有物料堆间距3m。
说明:
1、三条料线堆料时,由于料条过细,堆料量减少,堆料宽度按30m 计算,每条线预留6m宽的车道,所以料场宽度为:30×3+4×5+3×6=128m,所以需将料场宽度增加为128m。
2、由于冬季生产矿粉冻块较多,上表中冬季生产的冻块占用场地未进行计算。
冬季生产时尘泥、氧化铁皮等不能消耗完,需占用料场的量未计算。
3、理论计算时,料场堆料满足烧结机生产55天。
4、由于450m2烧结机料场宽度减小,原设计每日解冻117车/天,
而烧结正常生产时,每日需解冻库解冻208车(60吨/车)含铁原料,故解冻库翻车能力需要加大。
北营炼铁厂
二〇一二年五月五日。
烧结厂设计说明书

1 Introduction1.1 OutlineThe design reference Baosteel sintering plant, according to the design requirements of the mission statement, the design production capacity of 300 tons, the sintering plant products of high quality for blast furnace sinter.Because annular cooler temperature exhaust gas discharged with the airflow and fine dust released into the air, allowing more serious environmental pollution, while a large number of hot exhaust gas into the atmosphere, waste heat, dust and heat in order to reduce emissions, reduce pollution of the environment, the design of the ring after a hot exhaust gas cooler dust stove and holding furnace used for point after.The design of the sintering engineering technology, equipment level and the degree of automation and, basically, Baosteel sintering plant rather, is the world's advanced level, the design of a complete process: thick material layer sintering, centralized dust removal system, dual diagonal band spot stove, the addition of a ring cooler holding furnace and hot exhaust gas emissions as a promoter, these are the sintering process technology and equipment constitute the main content, but also an important indicator of the level of today's world.1.2 Design basis and design principles1.2.1 Design basisThis design is the Central South University of Resources Processing and Bioengineering pellets Professional 2013 session of the graduate design task, entitled "Design sinter plant of an annual output of 3 million tons of sinter" which combined in Baosteel graduation internship process field data collected and the master site processes and equipment prepared on the basis of.1.2.1 Design principlesIn order to do this sinter plant design, intended to the following design principles:1) According to today's world sintering technology, combined with the actual situation of Baosteel, determine the design process technology and equipment level.2) reasonably compact device configuration, production workshop has sufficient operating area to ensure smooth material transport facilities.3) selection of equipment, construction to achieve standardization and universal.4) Take effective measures to reduce the sinter plant dust pollution.5) Consider the possibility of future expansion.1.3 Design rangeThe design of the sintering project include the following:1) coke crushing and screening system.2) ingredients mixed system.3) sintering and cooling system.4) the main electrical room.5) finished crushing and screening system.6) the dust handling system.2 Iron-containing materials, flux, fuel2.1 iron-containing materialsThe design of the sintering plant iron raw materials including imported iron ore , national concentrates.Imported iron ore is a high iron low silicon raw materials, mainly from India, Brazil, Australia and other importing countries. Imported Materials ore from the steamer pier, transported by belt conveyor to the raw material yard, through Neutralization and mix on the yard, then by belt conveyor to the dosing chamber, Sintering plant mainly recyclable materials is iron by the belt conveyor to the field and mixed with other Materials Materials , to pre-dosing effect. Iron-containing materials in the yard after mixing , directly to the dosing chamber.2.1.1 Chemical composition of iron-containing materialsThe chemical composition of iron-containing materials into the plant in Table 2-1.2.1.2 The requirements Size and grade1) the size requirements: Fines <8mm.(2) grade requirements: iron grade fluctuation range ±0.5%;FeO fluctuation range ±0.1%;S fluctuation range ±0.08%.2.2 FluxBecause most iron raw materials used is high-speed rail low silicon raw material,in order to improve the quality of sinter and improve the fluidity of slag, this design uses dolomite, limestone and quicklime as flux. Mixture granulated quicklime The quicklime is used to enhance mixture granulation and improve the permeability3.Sintering Process Selection and VerificationAccording to material properties, select the appropriate sintering method, processing procedures and process systems,in order to obtain the desired product. Sintering process designed mainly for the process of analysis and the basic principles for selection process .3.1The meaning and requirements for selecting processProcess is an integrated of certain processes from production process.Sintering process of selection is an important part of the design process. A new sintering plant around all the design elements are determined by the unfolding process. Reasonable production process, equipment capacity is full, rational organization of production, to ensure continuous production, access to advanced technical and economic indicators of important factors. Therefore, the process of selection, must be fully considered, multi-program comparison.Process selection requirement is to ensure the product quality requirements of the premise, to maximize the use of various iron-containing materials, and access to high labor productivity and equipment utilization, conserve energy as much as possible to save production costs for enterprises to seek maximum profit; and to adopt modern means of production, strong labor intensity, improve operational and management level; should consider radical waste pollution, protect the environment and health, protection of workers' health.3.2 Raw materials, flux and fuel3.2.1Raw material preparationThe raw materials used to design the main ore powder, powder ore controls below 8mm size requirements, into the iron-containing raw materials and sintering mix ingredients in order to achieve results. This procedure offers a raw material in thesteel mill plant, mix mine via conveyor belt to produce sinter plant ingredients.Sintered material into the sinter plant conditions:1) bonanza powder particle size should be 8-0mm (also available 6-0mm), ore particle size of more than 10% +8 mm will affect the quality of sinter. Special powder size requirements should be based on experimentally determined. SiO2 content fluctuations should be less than or equal ± 0.2%. Iron grade fluctuations should satisfy the following conditions; large and extra large sinter plant should be less than or equal ± 0.5%; medium-sized sinter plant should be less than equal to ± 0.75%; small sinter plant should be less than equal to ± 1.0%.2) magnetite concentrate moisture should be less than 10%, hematite concentrate moisture should be less than 11%. Concentrate moisture exceeds this requirement, the proportioning accuracy, affecting mixing uniformity.3) Blast should be appropriate wetting dry dust, blast furnace and BOF dust and sludge secondary dust should be dehydrated, so that water is less than 15%.4) Rolling Paper size not greater than 8mm.5) of the iron-containing material harmful impurities should be limited as required.When raw iron grade volatile than <sintering plant design requirements> requirements, should be shot mix stockyard and, if possible together with the steel plant was built in order to achieve sintering, pelletizing plant feed ingredients stable, uniform size. For medium and small sintering plant should also be set up according to the specific conditions of mixing facilities; raw single species, grade fluctuation is small, or not to set mixing facilities. But it should be built by the mining of raw materials warehouse and warehouse and so on. There blending stockyard, the sintering plant should no longer raw materials warehouse. But in wet areas should be located indoor storage facilities.Medium-sized sinter plant material should be adopted by the dumper. Dumper is a large unloading equipment, which is widely used in large and medium-sized and some large sintering plant sinter plant. It has the unloading of high efficiency, large capacity, suitable for all kinds of bulk material unloading turn. Because high degree of mechanization, is conducive to automated or semi-automated unloading operations.By mine shafts is used only by the material and not for storage facilities. Generally used for steel mills to accept bulk materials and auxiliary materials. By mine chute design should consider the use of mechanized equipment. Small mines can be spiral unloading machine or a chain-head unloading machine to accept raw materials. Most of the raw materials warehouse sintering plant designed to stabilize production, raw materials warehouse storage time of various materials as follows: iron-containing materials, a dedicated transmission line for the five days, no special transport line for the seven days; fuels and solvents , a dedicated conveyor line for the 3-5 days, no special transport line for 7 days. As for the small sinter plant under specific conditions. Freezing cold regions receiving and storage of raw materials should have anti-freeze thawed facilities.3.2.2 Flux preparationSintering production on the granularity of flux, there are strict regulations generally require 3 ~ 0mm content should be greater than 85% while the flux into the plant size is 40 ~ 0mm, so you need to be broken.Flux in the raw material crushing plant is complete. Dolomite, limestone crushing to the required 3 ~ 0mm, via tape machine to the dosing chamber. Lime particle size of 3 ~ 0mm, from the limestone, dolomite roasting plant is provided with a suction pressure tank to the sintering plant dosing chamber, and then compressed into the batching tank.(1) flux crushing and screening process generally has three:1) Open broken rod mill machining processes.2) Closed hammer crusher crushing and screening process flow.3) Impact Crusher closed circuit crushing and screening process flow.Closed flux machining processes are generally used in closed-circuit crushing and screening processing flow, can be divided into two kinds of pre-screening and screening examination. When the flux ore 3-0mm level content more time (generally 30% -40% or more), before use of pre-screening. Otherwise, adopt screening. Check the screening process sieve material for the product, the oversize material back into the crusher heavy breaking. More generally sintering plant using this process.Closed flux machining processes are generally used in closed process, can be divided into pre-screening and pre-screening process closed-circuit crushing and screening checks closed circuit combining two kinds. When the flux ore 3 ~ 0mm level for a long time (generally 30% to 40%), before use of pre-screening. Otherwise, the check screening. Check the screening process under size product for the product, the oversize material back into the crusher broken again. Taking into account the material conditions of this design, the design uses a closed circuit with a screening examination.(2) broken equipmentConsidering the physical properties of raw materials, production capacity and size requirements, the advantages and disadvantages of the crushing equipment discussed below:1) Impact CrusherScope: brittle, medium hard minerals (metallic, C), sintering plant (limestone, dolomite).Advantages: uniform size, over crushed small, light weight, low power consumption, large capacity, large crushing ratio.Disadvantages: vibration, noise, dust, wear big.2) hammer crusher (reversible and irreversible)Scope: brittle, medium-hard, hard and soft minerals (limestone, dolomite and serpentine), the crushing (3 ~ 0mm), rarely used in primary crushing.Pros: large capacity, large crushing ratio; structure is simple, compact, low power consumption and easy maintenance.Disadvantages: wear and high moisture blocking material is easy.3) rod millScope: Baosteel crushing equipment used in the second paragraph of coke.Advantages: too little crush.Disadvantages: high power consumption, low output and heavy equipment.4) four roller crusher (on the roll)Scope of application: Widely used in sinter plant fuel broken.Advantages: can be completed in time, fine, no screening classification, simpleprocess.Cons: roller uneven wear.Common flux crushing equipment crusher and hammer crusher two kinds.Crusher has uniform particle size, over crushed small, light weight, low power consumption, large capacity, large crushing ratio, etc., hammer crusher with high yield, large crushing ratio, low power consumption per unit of product, easy maintenance, etc. advantages in the production of the two devices is different, but the impact crusher vibration, noise, dust capacity, wear and therefore in the design selection hammer crusher. Hammer crusher can be divided into two kinds of reversible and irreversible and reversible hammer crusher hammer function to extend the service life and ensure the crushing efficiency, so the design are made of reversible hammer crusher.(3) screening equipmentSintering plant flux screening equipment is mainly shaker.The design uses a self-centering shakerSelf-centering shaker has the advantage of simple structure, use, operation and replacement of the screen surface is more convenient, strong vibration sieve surface, and the vibration direction perpendicular to the screen surface can reduce the material clogging the sieve of the phenomenon, with high screening efficiency (up to 90 ~ 95%) and production capacity, suitable for medium, fine screening, does not apply to coarse sieve.The disadvantage is that the amplitude of the sieve with the size of the amount to the mine fluctuate, resulting in screening efficiency is not stable enough; sieve in the process of starting and stopping, through resonance, the amplitude increases, a greater impact on the sieve and buildings.11。
2x160m2烧结机项目设计方案说明书
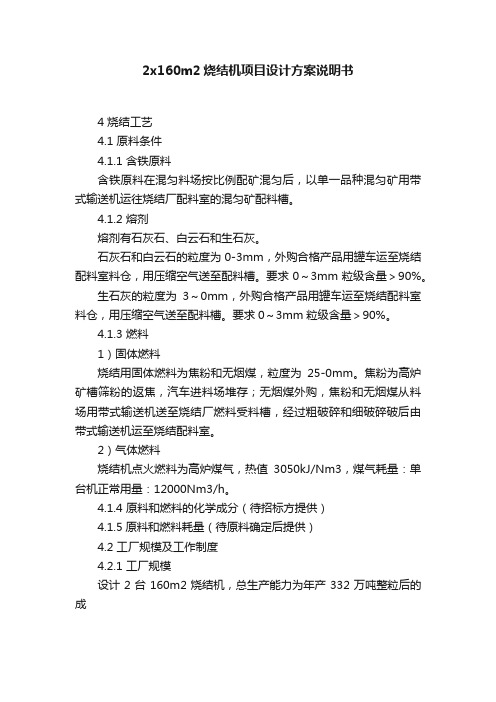
2x160m2烧结机项目设计方案说明书4 烧结工艺4.1 原料条件4.1.1 含铁原料含铁原料在混匀料场按比例配矿混匀后,以单一品种混匀矿用带式输送机运往烧结厂配料室的混匀矿配料槽。
4.1.2 熔剂熔剂有石灰石、白云石和生石灰。
石灰石和白云石的粒度为0-3mm,外购合格产品用罐车运至烧结配料室料仓,用压缩空气送至配料槽。
要求0~3mm粒级含量>90%。
生石灰的粒度为3~0mm,外购合格产品用罐车运至烧结配料室料仓,用压缩空气送至配料槽。
要求0~3mm粒级含量>90%。
4.1.3 燃料1)固体燃料烧结用固体燃料为焦粉和无烟煤,粒度为25-0mm。
焦粉为高炉矿槽筛粉的返焦,汽车进料场堆存;无烟煤外购,焦粉和无烟煤从料场用带式输送机送至烧结厂燃料受料槽,经过粗破碎和细破碎破后由带式输送机运至烧结配料室。
2)气体燃料烧结机点火燃料为高炉煤气,热值3050kJ/Nm3,煤气耗量:单台机正常用量:12000Nm3/h。
4.1.4 原料和燃料的化学成分(待招标方提供)4.1.5原料和燃料耗量(待原料确定后提供)4.2 工厂规模及工作制度4.2.1 工厂规模设计2台160m2烧结机,总生产能力为年产332万吨整粒后的成品烧结矿,分两期建设投产。
4.2.2 工作制度工厂为连续工作制,年工作330天,每天3班,每班8小时,主机业率为90.4%。
4.3 主要参数及产品方案4.3.1 主要参数按照两座高炉主原料采用80%的烧结矿和20%的球团矿的要求,需要烧结矿301.4万吨/年,考虑烧结规模与炼铁要求相比要留有5~10%的富余量,确定本工程烧结机利用系数为1.31t/(m22h),单台烧结机小时产能为209.6 t/h,年产量166万吨。
4.3.2产品方案(初定)烧结厂产品为温度≤120℃的冷烧结矿,出厂烧结矿粒度≥5mm,TFe~57%,碱度1.8。
4.3.3 工艺流程本工程工艺流程是从原料接受到成品烧结矿输出,包括燃料破碎、配料、混合、抽风、烧结、冷却、成品筛分及成品转运的整个工艺过程。
烧结砖厂设计方案
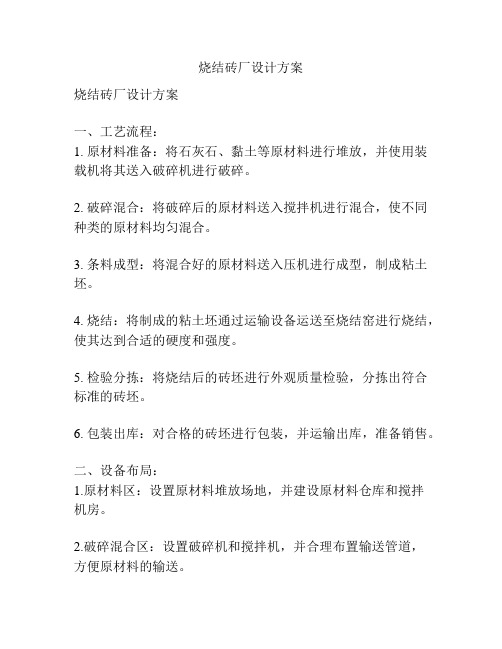
烧结砖厂设计方案烧结砖厂设计方案一、工艺流程:1. 原材料准备:将石灰石、黏土等原材料进行堆放,并使用装载机将其送入破碎机进行破碎。
2. 破碎混合:将破碎后的原材料送入搅拌机进行混合,使不同种类的原材料均匀混合。
3. 条料成型:将混合好的原材料送入压机进行成型,制成粘土坯。
4. 烧结:将制成的粘土坯通过运输设备运送至烧结窑进行烧结,使其达到合适的硬度和强度。
5. 检验分拣:将烧结后的砖坯进行外观质量检验,分拣出符合标准的砖坯。
6. 包装出库:对合格的砖坯进行包装,并运输出库,准备销售。
二、设备布局:1.原材料区:设置原材料堆放场地,并建设原材料仓库和搅拌机房。
2.破碎混合区:设置破碎机和搅拌机,并合理布置输送管道,方便原材料的输送。
3.条料成型区:设置压机和压机房,并建设料斗和输送设备,将混合好的原材料输送到压机进行成型。
4.烧结区:建设烧结窑和烟气处理设备,并设立运输通道,将砖坯送入烧结窑烧结。
5.检验分拣区:设立检验分拣台和分拣设备,对烧结后的砖坯进行质量检验和分拣。
6.包装出库区:设置包装设备和仓库,并设立出库通道,将合格的砖坯进行包装和运输。
三、环境保护:1. 烟气处理:在烧结窑的烟囱上安装烟气处理设备,通过除尘器和脱硫装置等技术手段,将烟气中的颗粒物和硫化物等有害物质净化处理,达到环保排放标准。
2. 噪音控制:在设备运行时,对破碎机、搅拌机等噪音大的设备进行隔音处理,降低噪音污染。
3. 废弃物处理:将生产过程中产生的废弃物进行分类、收集和处理,确保废弃物的无害化处理,并减少对环境的污染。
四、用电和用水:1. 用电:根据各个工艺段的设备功率和运行时间,合理预估用电量,并建设配电室和变压器等设备,确保用电安全。
2. 用水:根据生产工艺流程中的用水需求,合理设计水源设施和供水管道,确保用水的正常供应,同时做好废水处理,减少对水资源的浪费和污染。
以上是烧结砖厂设计方案的简要介绍,方案中考虑了工艺流程、设备布局、环境保护以及用电用水等因素,以确保砖厂的高效运营和环保生产。
- 1、下载文档前请自行甄别文档内容的完整性,平台不提供额外的编辑、内容补充、找答案等附加服务。
- 2、"仅部分预览"的文档,不可在线预览部分如存在完整性等问题,可反馈申请退款(可完整预览的文档不适用该条件!)。
- 3、如文档侵犯您的权益,请联系客服反馈,我们会尽快为您处理(人工客服工作时间:9:00-18:30)。
1 Introduction1.1 OutlineThe design reference Baosteel sintering plant, according to the design requirements of the mission statement, the design production capacity of 300 tons, the sintering plant products of high quality for blast furnace sinter.Because annular cooler temperature exhaust gas discharged with the airflow and fine dust released into the air, allowing more serious environmental pollution, while a large number of hot exhaust gas into the atmosphere, waste heat, dust and heat in order to reduce emissions, reduce pollution of the environment, the design of the ring after a hot exhaust gas cooler dust stove and holding furnace used for point after.The design of the sintering engineering technology, equipment level and the degree of automation and, basically, Baosteel sintering plant rather, is the world's advanced level, the design of a complete process: thick material layer sintering, centralized dust removal system, dual diagonal band spot stove, the addition of a ring cooler holding furnace and hot exhaust gas emissions as a promoter, these are the sintering process technology and equipment constitute the main content, but also an important indicator of the level of today's world.1.2 Design basis and design principles1.2.1 Design basisThis design is the Central South University of Resources Processing and Bioengineering pellets Professional 2013 session of the graduate design task, entitled "Design sinter plant of an annual output of 3 million tons of sinter" which combined in Baosteel graduation internship process field data collected and the master site processes and equipment prepared on the basis of.1.2.1 Design principlesIn order to do this sinter plant design, intended to the following design principles:1) According to today's world sintering technology, combined with the actual situation of Baosteel, determine the design process technology and equipment level.2) reasonably compact device configuration, production workshop has sufficient operating area to ensure smooth material transport facilities.3) selection of equipment, construction to achieve standardization and universal.4) Take effective measures to reduce the sinter plant dust pollution.5) Consider the possibility of future expansion.1.3 Design rangeThe design of the sintering project include the following:1) coke crushing and screening system.2) ingredients mixed system.3) sintering and cooling system.4) the main electrical room.5) finished crushing and screening system.6) the dust handling system.2 Iron-containing materials, flux, fuel2.1 iron-containing materialsThe design of the sintering plant iron raw materials including imported iron ore , national concentrates.Imported iron ore is a high iron low silicon raw materials, mainly from India, Brazil, Australia and other importing countries. Imported Materials ore from the steamer pier, transported by belt conveyor to the raw material yard, through Neutralization and mix on the yard, then by belt conveyor to the dosing chamber, Sintering plant mainly recyclable materials is iron by the belt conveyor to the field and mixed with other Materials Materials , to pre-dosing effect. Iron-containing materials in the yard after mixing , directly to the dosing chamber.2.1.1 Chemical composition of iron-containing materialsThe chemical composition of iron-containing materials into the plant in Table 2-1.2.1.2 The requirements Size and grade1) the size requirements: Fines <8mm.(2) grade requirements: iron grade fluctuation range ±0.5%;FeO fluctuation range ±0.1%;S fluctuation range ±0.08%.2.2 FluxBecause most iron raw materials used is high-speed rail low silicon raw material,in order to improve the quality of sinter and improve the fluidity of slag, this design uses dolomite, limestone and quicklime as flux. Mixture granulated quicklime The quicklime is used to enhance mixture granulation and improve the permeability3.Sintering Process Selection and VerificationAccording to material properties, select the appropriate sintering method, processing procedures and process systems,in order to obtain the desired product. Sintering process designed mainly for the process of analysis and the basic principles for selection process .3.1The meaning and requirements for selecting processProcess is an integrated of certain processes from production process.Sintering process of selection is an important part of the design process. A new sintering plant around all the design elements are determined by the unfolding process. Reasonable production process, equipment capacity is full, rational organization of production, to ensure continuous production, access to advanced technical and economic indicators of important factors. Therefore, the process of selection, must be fully considered, multi-program comparison.Process selection requirement is to ensure the product quality requirements of the premise, to maximize the use of various iron-containing materials, and access to high labor productivity and equipment utilization, conserve energy as much as possible to save production costs for enterprises to seek maximum profit; and to adopt modern means of production, strong labor intensity, improve operational and management level; should consider radical waste pollution, protect the environment and health, protection of workers' health.3.2 Raw materials, flux and fuel3.2.1Raw material preparationThe raw materials used to design the main ore powder, powder ore controls below 8mm size requirements, into the iron-containing raw materials and sintering mix ingredients in order to achieve results. This procedure offers a raw material in thesteel mill plant, mix mine via conveyor belt to produce sinter plant ingredients.Sintered material into the sinter plant conditions:1) bonanza powder particle size should be 8-0mm (also available 6-0mm), ore particle size of more than 10% +8 mm will affect the quality of sinter. Special powder size requirements should be based on experimentally determined. SiO2 content fluctuations should be less than or equal ± 0.2%. Iron grade fluctuations should satisfy the following conditions; large and extra large sinter plant should be less than or equal ± 0.5%; medium-sized sinter plant should be less than equal to ± 0.75%; small sinter plant should be less than equal to ± 1.0%.2) magnetite concentrate moisture should be less than 10%, hematite concentrate moisture should be less than 11%. Concentrate moisture exceeds this requirement, the proportioning accuracy, affecting mixing uniformity.3) Blast should be appropriate wetting dry dust, blast furnace and BOF dust and sludge secondary dust should be dehydrated, so that water is less than 15%.4) Rolling Paper size not greater than 8mm.5) of the iron-containing material harmful impurities should be limited as required.When raw iron grade volatile than <sintering plant design requirements> requirements, should be shot mix stockyard and, if possible together with the steel plant was built in order to achieve sintering, pelletizing plant feed ingredients stable, uniform size. For medium and small sintering plant should also be set up according to the specific conditions of mixing facilities; raw single species, grade fluctuation is small, or not to set mixing facilities. But it should be built by the mining of raw materials warehouse and warehouse and so on. There blending stockyard, the sintering plant should no longer raw materials warehouse. But in wet areas should be located indoor storage facilities.Medium-sized sinter plant material should be adopted by the dumper. Dumper is a large unloading equipment, which is widely used in large and medium-sized and some large sintering plant sinter plant. It has the unloading of high efficiency, large capacity, suitable for all kinds of bulk material unloading turn. Because high degree of mechanization, is conducive to automated or semi-automated unloading operations.By mine shafts is used only by the material and not for storage facilities. Generally used for steel mills to accept bulk materials and auxiliary materials. By mine chute design should consider the use of mechanized equipment. Small mines can be spiral unloading machine or a chain-head unloading machine to accept raw materials. Most of the raw materials warehouse sintering plant designed to stabilize production, raw materials warehouse storage time of various materials as follows: iron-containing materials, a dedicated transmission line for the five days, no special transport line for the seven days; fuels and solvents , a dedicated conveyor line for the 3-5 days, no special transport line for 7 days. As for the small sinter plant under specific conditions. Freezing cold regions receiving and storage of raw materials should have anti-freeze thawed facilities.3.2.2 Flux preparationSintering production on the granularity of flux, there are strict regulations generally require 3 ~ 0mm content should be greater than 85% while the flux into the plant size is 40 ~ 0mm, so you need to be broken.Flux in the raw material crushing plant is complete. Dolomite, limestone crushing to the required 3 ~ 0mm, via tape machine to the dosing chamber. Lime particle size of 3 ~ 0mm, from the limestone, dolomite roasting plant is provided with a suction pressure tank to the sintering plant dosing chamber, and then compressed into the batching tank.(1) flux crushing and screening process generally has three:1) Open broken rod mill machining processes.2) Closed hammer crusher crushing and screening process flow.3) Impact Crusher closed circuit crushing and screening process flow.Closed flux machining processes are generally used in closed-circuit crushing and screening processing flow, can be divided into two kinds of pre-screening and screening examination. When the flux ore 3-0mm level content more time (generally 30% -40% or more), before use of pre-screening. Otherwise, adopt screening. Check the screening process sieve material for the product, the oversize material back into the crusher heavy breaking. More generally sintering plant using this process.Closed flux machining processes are generally used in closed process, can be divided into pre-screening and pre-screening process closed-circuit crushing and screening checks closed circuit combining two kinds. When the flux ore 3 ~ 0mm level for a long time (generally 30% to 40%), before use of pre-screening. Otherwise, the check screening. Check the screening process under size product for the product, the oversize material back into the crusher broken again. Taking into account the material conditions of this design, the design uses a closed circuit with a screening examination.(2) broken equipmentConsidering the physical properties of raw materials, production capacity and size requirements, the advantages and disadvantages of the crushing equipment discussed below:1) Impact CrusherScope: brittle, medium hard minerals (metallic, C), sintering plant (limestone, dolomite).Advantages: uniform size, over crushed small, light weight, low power consumption, large capacity, large crushing ratio.Disadvantages: vibration, noise, dust, wear big.2) hammer crusher (reversible and irreversible)Scope: brittle, medium-hard, hard and soft minerals (limestone, dolomite and serpentine), the crushing (3 ~ 0mm), rarely used in primary crushing.Pros: large capacity, large crushing ratio; structure is simple, compact, low power consumption and easy maintenance.Disadvantages: wear and high moisture blocking material is easy.3) rod millScope: Baosteel crushing equipment used in the second paragraph of coke.Advantages: too little crush.Disadvantages: high power consumption, low output and heavy equipment.4) four roller crusher (on the roll)Scope of application: Widely used in sinter plant fuel broken.Advantages: can be completed in time, fine, no screening classification, simpleprocess.Cons: roller uneven wear.Common flux crushing equipment crusher and hammer crusher two kinds.Crusher has uniform particle size, over crushed small, light weight, low power consumption, large capacity, large crushing ratio, etc., hammer crusher with high yield, large crushing ratio, low power consumption per unit of product, easy maintenance, etc. advantages in the production of the two devices is different, but the impact crusher vibration, noise, dust capacity, wear and therefore in the design selection hammer crusher. Hammer crusher can be divided into two kinds of reversible and irreversible and reversible hammer crusher hammer function to extend the service life and ensure the crushing efficiency, so the design are made of reversible hammer crusher.(3) screening equipmentSintering plant flux screening equipment is mainly shaker.The design uses a self-centering shakerSelf-centering shaker has the advantage of simple structure, use, operation and replacement of the screen surface is more convenient, strong vibration sieve surface, and the vibration direction perpendicular to the screen surface can reduce the material clogging the sieve of the phenomenon, with high screening efficiency (up to 90 ~ 95%) and production capacity, suitable for medium, fine screening, does not apply to coarse sieve.The disadvantage is that the amplitude of the sieve with the size of the amount to the mine fluctuate, resulting in screening efficiency is not stable enough; sieve in the process of starting and stopping, through resonance, the amplitude increases, a greater impact on the sieve and buildings.11。