螺纹车削加工讲解
普通车床的螺纹车削加工ppt课件文字可编辑

15
三、典型普通螺纹零件的车削加工
螺纹总背吃刀量ap=h=0.54P=0.81mm
合理分配螺纹加工余量
(一般粗车ap:0.10~0.50;精车ap:0.01~0.10 。)
进刀次数
背吃刀量
加工步骤
加工余量
第一次进刀 第二次进刀 第三次进刀 第四次进刀 第五次进刀 第六次进刀
a =0.50mm p
a =0.15mm p
三、典型普通螺纹零件的车削加工
7. 螺纹车削操作方法与步骤
2)抬闸法 利用开合螺母的压下和抬起来车削螺纹。
控制手柄
正反车车削法
抬闸法
退刀方式 利用丝杆的反转纵向返回起点
手动纵向返回起点
适用范围
适用于任何螺距的加工
只适用于丝杆螺距是工件 螺距整数倍时
13
本标准适用于已投入商业运行的火力 发电厂 纯凝式 汽轮发 电机组 和供热 汽轮发 电机组 的技术 经济指 标的统 计和评 价。燃 机机组 、余热 锅炉以 及联合 循环机 组可参 照本标 准执行 ,并增 补指标 。
二、螺纹的车削加工工艺
2. 普通外螺纹的车削加工工艺流程
车端面 车螺纹大径 车退刀槽 倒角 车螺纹
d<公称直径 <螺纹小径
多刀车削
3
本标准适用于已投入商业运行的火力 发电厂 纯凝式 汽轮发 电机组 和供热 汽轮发 电机组 的技术 经济指 标的统 计和评 价。燃 机机组 、余热 锅炉以 及联合 循环机 组可参 照本标 准执行 ,并增 补指标 。
a =0.10mm p
a =0.03mm p
a =0.02mm p
a =0.01mm p
粗加工 精加工
0.75mm 0.06mm
普通车床螺纹车削加工讲义

3 ) 车螺纹大径φ24
0 -0.23
4 ) 切槽
三.典型普通螺纹零件的车削加工
2. 确定加工步骤
5 ) 倒角
6 ) 车螺纹
三、典型普通螺纹零件的车削加工
3.选择刀具及切削用量
序 号
加工内容
刀具 名称
1 端面 端面刀
2
φ 24、φ 30外 圆
外圆刀
3
退刀槽
4×φ21.5
切槽刀
螺纹
4 M24X1.5— 螺纹刀
合理分配螺纹加工余量
(一般粗车ap:0.10~0.50;精车ap:0.01~0.10 。)
进刀次数 第一次进刀 第二次进刀 第三次进刀 第四次进刀 第五次进刀 第六次进刀
背吃刀量 ap=0.50mm ap=0.15mm ap=0.10mm ap=0.03mm ap=0.02mm ap=0.01mm
加工步骤 粗加工
三、典型普通螺纹零件的车削加工
7. 螺纹车削操作方法与步骤
1)正反车车削法
开车,对刀
合闸,车螺纹
横向退刀,停车, 反转,纵向回起点
快速退出
开车切削 开反车返回
多刀循环加工
进刀
三、典型普通螺纹零件的车削加工
7. 螺纹车削操作方法与步骤
2)抬闸法 利用开合螺母的压下和抬起来车削螺纹。
控制手柄
正反车车削法
车端面 车螺纹大径 车退刀槽 倒角 车螺纹
d<公称直径 <螺纹小径
多刀车削
三.典型普通螺纹零件的车削加工
1. 分析零件图
查表或计算 d=φ 24 0 -0.23
d2=d-0.6495P=φ 23.026-00.19
三.典型普通螺纹零件的车削加工
螺纹加工方法详细讲解
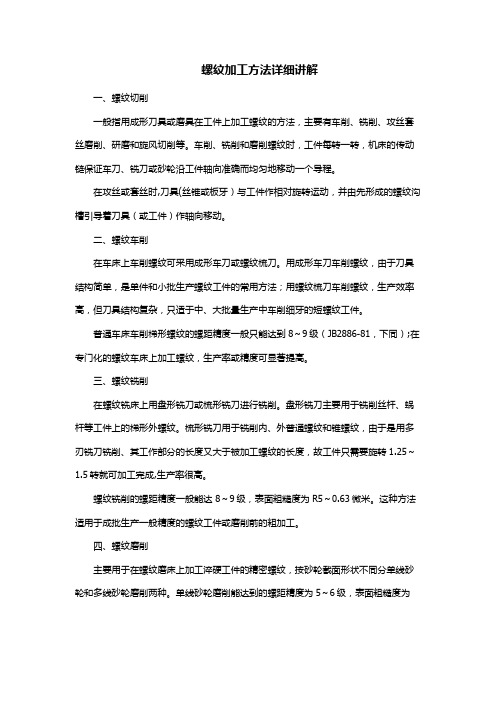
螺纹加工方法详细讲解一、螺纹切削一般指用成形刀具或磨具在工件上加工螺纹的方法,主要有车削、铣削、攻丝套丝磨削、研磨和旋风切削等。
车削、铣削和磨削螺纹时,工件每转一转,机床的传动链保证车刀、铣刀或砂轮沿工件轴向准确而均匀地移动一个导程。
在攻丝或套丝时,刀具(丝锥或板牙)与工件作相对旋转运动,并由先形成的螺纹沟槽引导着刀具(或工件)作轴向移动。
二、螺纹车削在车床上车削螺纹可采用成形车刀或螺纹梳刀。
用成形车刀车削螺纹,由于刀具结构简单,是单件和小批生产螺纹工件的常用方法;用螺纹梳刀车削螺纹,生产效率高,但刀具结构复杂,只适于中、大批量生产中车削细牙的短螺纹工件。
普通车床车削梯形螺纹的螺距精度一般只能达到8~9级(JB2886-81,下同);在专门化的螺纹车床上加工螺纹,生产率或精度可显著提高。
三、螺纹铣削在螺纹铣床上用盘形铣刀或梳形铣刀进行铣削。
盘形铣刀主要用于铣削丝杆、蜗杆等工件上的梯形外螺纹。
梳形铣刀用于铣削内、外普通螺纹和锥螺纹,由于是用多刃铣刀铣削、其工作部分的长度又大于被加工螺纹的长度,故工件只需要旋转1.25~1.5转就可加工完成,生产率很高。
螺纹铣削的螺距精度一般能达 8~9级,表面粗糙度为R5~0.63微米。
这种方法适用于成批生产一般精度的螺纹工件或磨削前的粗加工。
四、螺纹磨削主要用于在螺纹磨床上加工淬硬工件的精密螺纹,按砂轮截面形状不同分单线砂轮和多线砂轮磨削两种。
单线砂轮磨削能达到的螺距精度为5~6级,表面粗糙度为R1.25~0.08微米,砂轮修整较方便。
这种方法适于磨削精密丝杠、螺纹量规、蜗杆、小批量的螺纹工件和铲磨精密滚刀。
多线砂轮磨削又分纵磨法和切入磨法两种。
纵磨法的砂轮宽度小于被磨螺纹长度,砂轮纵向移动一次或数次行程即可把螺纹磨到最后尺寸。
切入磨法的砂轮宽度大于被磨螺纹长度,砂轮径向切入工件表面,工件约转1.25转就可磨好,生产率较高,但精度稍低,砂轮修整比较复杂。
切入磨法适于铲磨批量较大的丝锥和磨削某些紧固用的螺纹。
螺纹车削工艺与技巧

螺纹车削工艺与技巧螺纹车削是常见的一种金属加工方法,广泛应用于制造业中。
它涉及到车床和工具的使用,以切削出各种形状的螺纹。
本文将介绍螺纹车削的基础知识、工艺流程以及一些技巧和注意事项。
一、螺纹车削的基础知识在进行螺纹车削之前,需要了解一些基础知识。
首先是螺纹的类型,常见的螺纹有内螺纹和外螺纹,分别用于孔内和孔外的螺纹制作。
其次是螺纹的参数,如螺距、螺纹角和牙型。
这些参数会直接影响到螺纹的制作和使用,在进行车削时需要选择合适的参数。
二、螺纹车削的工艺流程螺纹车削的工艺流程通常包括以下几个步骤:准备工作、装夹工件、选择合适的切削工具、确定切削速度和进给、进行车削操作、检查和修整螺纹。
首先,在进行螺纹车削之前,需要做好准备工作,包括检查车床和刀具的状态,确保其正常工作。
接着,将待加工的工件装夹在车床上,并调整好刀具的位置。
然后,选择适合的切削工具。
常用的切削工具有螺纹刀和攻丝刀,根据加工要求选择合适的刀具。
根据螺纹参数和工件材料,选择合适的刀具材料,例如高速钢、硬质合金等。
确定切削速度和进给是关键步骤之一。
切削速度和进给率的选择要根据刀具和工件材料来确定,一般需参考相关资料或试验确定合适的数值。
切削速度过高可能导致刀具磨损过快,而切削速度过低则可能导致加工效率低下。
进行车削操作时,要注意保持刀具和工件的接触紧密,以减小振动和误差。
通过控制车床的进给和转速,进行螺纹的切削。
在操作过程中,应保持稳定的刀具进给速度和转速,避免过快或过慢。
最后,进行螺纹的检查和修整。
通过螺纹量规等工具进行测量,并进行必要的矫正操作。
确保螺纹的尺寸和质量满足要求。
三、螺纹车削的技巧与注意事项1. 合理选择切削工具:根据螺纹参数和工件材料选择合适的切削工具。
刀具的质量和尺寸对螺纹的加工质量起着重要的影响。
2. 控制进给速度和转速:进给速度和转速的选择要根据刀具和工件材料来确定,保持稳定的切削条件,避免过快或过慢导致的加工问题。
3. 注意工件的固定:工件在车削过程中要牢固固定,以避免振动和位置偏移。
螺纹车削的方法及技巧【详解】
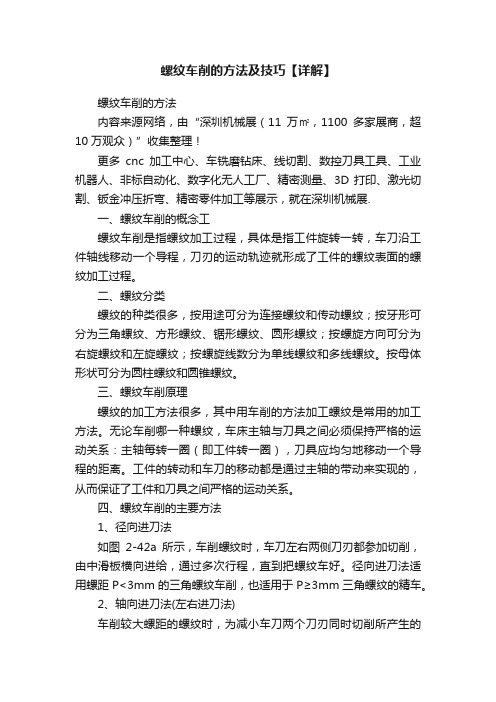
螺纹车削的方法及技巧【详解】螺纹车削的方法内容来源网络,由“深圳机械展(11万㎡,1100多家展商,超10万观众)”收集整理!更多cnc加工中心、车铣磨钻床、线切割、数控刀具工具、工业机器人、非标自动化、数字化无人工厂、精密测量、3D打印、激光切割、钣金冲压折弯、精密零件加工等展示,就在深圳机械展.一、螺纹车削的概念工螺纹车削是指螺纹加工过程,具体是指工件旋转一转,车刀沿工件轴线移动一个导程,刀刃的运动轨迹就形成了工件的螺纹表面的螺纹加工过程。
二、螺纹分类螺纹的种类很多,按用途可分为连接螺纹和传动螺纹;按牙形可分为三角螺纹、方形螺纹、锯形螺纹、圆形螺纹;按螺旋方向可分为右旋螺纹和左旋螺纹;按螺旋线数分为单线螺纹和多线螺纹。
按母体形状可分为圆柱螺纹和圆锥螺纹。
三、螺纹车削原理螺纹的加工方法很多,其中用车削的方法加工螺纹是常用的加工方法。
无论车削哪一种螺纹,车床主轴与刀具之间必须保持严格的运动关系:主轴每转一圈(即工件转一圈),刀具应均匀地移动一个导程的距离。
工件的转动和车刀的移动都是通过主轴的带动来实现的,从而保证了工件和刀具之间严格的运动关系。
四、螺纹车削的主要方法1、径向进刀法如图2-42a所示,车削螺纹时,车刀左右两侧刀刃都参加切削,由中滑板横向进给,通过多次行程,直到把螺纹车好。
径向进刀法适用螺距P<3mm的三角螺纹车削,也适用于P≥3mm三角螺纹的精车。
2、轴向进刀法(左右进刀法)车削较大螺距的螺纹时,为减小车刀两个刀刃同时切削所产生的扎刀现象,可使车刀只用一侧刀刃进行切削。
车削过程中,除了做横向进给外,同时还利用小滑板把车刀向左或向右做微量进给,使车刀只有一侧刀刃进行切削,通过多次行程,直至把螺纹车好。
这种加工方法适用于P≥3mm螺纹的精车等。
3、斜向进刀法如图2-42c所示,车削螺纹时,除中滑板横向进给外,只把小滑板向一个方向做微量进给。
这种方法只适用于粗车。
4、改进型斜向进刀法如图2-42d所示,这种车削方法是两侧刀刃都有切削任务,其中一个刀刃承担主要切削任务,这样可以避免斜向进刀不切削一侧刀刃磨损大和工件表面粗糙度大的问题。
螺纹车削加工基础知识
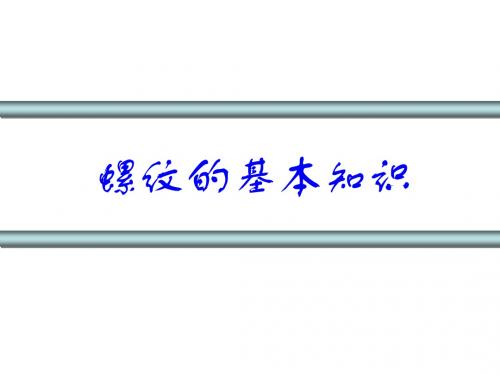
矩形螺纹
内 内 内 螺 螺 螺 纹 纹 纹
60 ° 60 ° 60 °
外 外 外 螺 螺 螺 纹 纹 纹
d d d d 2 d 2 d 2 d 1 d 1 d 1
梯形螺纹
内 内 内 螺 螺 螺 纹 纹 纹
30 °
30 ° 30 ° 30 °
外 外 外 螺 螺 螺 纹 纹 纹
梯形 锯齿形
d d d d 2 d 2 d 2 d 1 d 1 d 1
螺纹的基本知识
螺纹的基本知识
复习提问
• 车削圆锥面常用哪五种方法? • 转动小滑板法、偏移尾座法、仿形法、宽 刃刀车削法、铰内圆锥法。
螺纹的基本知识
联接
紧固
传动
螺纹的基本知识 一、螺纹的形成
螺纹是在圆柱或圆锥表面上,经过机械加工而形成的具有
规定牙型的螺旋线沟槽。在圆柱或圆锥外表面上形成的螺纹称
5、按用途:联接螺纹 传动螺纹
螺纹的基本知识 • 旋向判断方法:
二、 螺纹的分类
1、顺着轴线方向看(轴线垂直放)
右边高—右旋
左边高—左旋
思考:
右旋
左旋
2、根据旋入的方向判断:顺时针旋入为右旋 逆时针旋入为左旋
螺纹的基本知识
三角形(普通)螺纹
内 内 内 螺 螺 螺 纹 纹 纹
二、 螺纹的分类
60 °
螺纹的基本知识
二、 螺纹的分类
螺纹 联接
三角形螺纹 管螺纹 梯形螺纹
传动
矩形螺纹 锯齿形螺纹
螺纹的基本知识
三、螺纹要素
强调:只有螺纹的牙型、直径、线数、螺距、旋向这五要素
完 全相同时,内、外螺纹才能旋合在一起。
螺纹的基本知识
小结:
数控机床车削螺纹的原理
数控机床车削螺纹的原理数控机床是一种高精度、高效率的机床,广泛应用于各个制造行业中。
其中,数控机床的车削螺纹技术是其最为重要的应用之一。
本文将从数控机床车削螺纹的原理、机床结构、刀具选择和切削参数等方面进行详细阐述。
一、数控机床车削螺纹的原理数控机床车削螺纹通过控制工件和刀具在机床上的相对运动来实现。
机床通过数控系统控制刀具对工件进行切削,完成螺纹加工。
其工作原理如下:1. 设置螺纹参数:在数控系统中,需要设置螺纹的参数,包括螺纹的直径、螺距、螺纹类型等。
这些参数的设置将直接影响到刀具的运动轨迹和加工结果。
2. 运动轨迹计算:根据螺纹参数,数控系统会计算出刀具在车削过程中的运动轨迹。
这些轨迹会与工件表面上的螺纹轮廓相匹配,实现精确的螺纹加工。
3. 控制切削路径:数控系统会发送指令控制刀具的运动路径。
这些指令可以实现刀具的进给、回程和切削等动作。
通过合理的路径规划,可以确保刀具在车削过程中的尺寸和形状精度。
4. 刀具运动控制:根据数控系统发送的指令,伺服系统会控制主轴和刀架的运动,实现刀具的加工动作。
通过合理的速度和加减速控制,可以保证刀具的切削效果和加工质量。
5. 实时监控和修正:在整个车削过程中,数控系统会实时监控刀具和工件的位置、速度和加工状态。
一旦出现偏差,系统会自动进行修正,以保证加工的准确性和稳定性。
二、数控机床车削螺纹的机床结构数控机床车削螺纹通常采用的是数控车床或数控铣床。
这些机床具有不同的结构和功能,但都可以用于车削螺纹加工。
1. 数控车床:数控车床是一种专门用于车削零件的机床。
它由工件夹持装置、主轴、进给系统、切削工具和数控系统等组成。
通过控制数控系统,可以实现刀具的运动轨迹和加工参数的精确控制。
2. 数控铣床:数控铣床是一种专门用于铣削零件的机床。
它由工作台、主轴、进给系统、刀具和数控系统等组成。
通过控制数控系统,可以实现刀具在工作台上的运动轨迹和加工参数的精确控制。
三、刀具选择和切削参数在数控机床车削螺纹时,刀具的选择和切削参数的设置对加工效果和加工质量具有重要影响。
数控车削编程螺纹加工(“螺纹”文档)共45张
项
程序如表5.5所示。
目
表5.5复合螺纹切削循环指令编程
五
程序
…
螺
M03S800
纹
T0404
的
G00X32Z2
加
G76P010160Q50R0.5
工
G76X27.4Z-27.5P1300Q450F2
…
相关知识
例:试用复合螺纹切削循环指令G76编写图5.9所示的梯形螺纹加工程序。
项 目 五
螺
纹
的
加
图5.10 梯形螺纹编程
数控车削编程与加工
工程五 螺纹的加工
项 目 五
螺 纹 的 加 工
工程义务
粗精加工如图5.1所示螺纹套零件,零件资料为45钢。
项 目 五 螺 纹 的 加 工
图5.1螺纹套
相关知识
一、螺纹的根本要素和加工工艺
项 目
1.普通螺纹的根本要素
〔1〕牙型
沿螺纹轴线剖切时,螺纹牙齿轮廓的剖面外形称为牙型。螺纹的牙型
纹
确后,方可加工,防止出现不测事故。
的
加
4.螺纹切入切出量确实定
工
为保证螺纹加工质量,螺纹切削时在两端设置足够的切入切出量。因此,
实践螺纹的加工长度为:W=L(螺纹实际长度)+δ1+δ2
相关知识
式中:δ1——切入量,普通取2-5;
项
δ2——切出量,普通取0.5δ1左右;
目
五பைடு நூலகம்
螺 纹 的 加 工
图5.2螺纹的切入切出量
单一螺纹切削循环 …
G92X42.2Z-41R-14.5
X41.6
X41.2
注释 …
ap =0.8
螺纹车削教学实例
bm同螺钉, 由被联接件的 材料决定。
33
0.25d
⒋ 紧定螺钉联接装配图的比例画法
紧定螺钉分锥端、 Ⅰ 柱端、平端三种。
Ⅰ 2.5:1
0.2d
锥端紧定螺钉靠
端部锥面顶入机件上
d
的小锥坑起定位、固
定作用。
0.4d
柱端紧定螺钉利 用端部小圆柱插入机
Ⅱ
Ⅱ 2.5:1
件上的小孔或环槽起
定位、固定作用。
平端紧定螺钉靠 其端平面与击机件的 摩擦力起定位作用。
代号 轴承类型
0 双列角接触轴承 1 调心球轴承 2 调心滚子轴承和推力调心滚子轴承 3 圆锥滚子轴承 4 双列深沟球轴承 5 推力球轴承 6 深沟球轴承 7 角接触轴承 8 推力圆柱滚子轴承 N 圆柱滚子轴承 U 外球面球轴承 QJ 四点接触球轴承
54
★第二位数字是尺寸系列代号。 尺寸系列是指同一内径的轴承具有不同的
★在非圆投影的剖视图 中,两轮节线重合, 画点划线。齿根线画 粗实线。齿顶线画法 为一个轮齿为可见, 画粗实线,一个轮齿 被遮住,画虚线。
★在投影为圆的视图中, 两轮节圆相切,齿顶 圆画粗实线,齿根圆 画细实线或省略不画。
(注:标准齿轮的节圆=分度圆。) 49
⑶ 齿轮和齿条啮合的画法
齿轮直径无限大时,齿顶圆、齿根圆、分度 圆和齿廓都变成直线,齿轮成为齿条。
外径和宽度,因而有不同的承载能力。 ★右边的两位数字是内径代号。
当内径尺寸在20-480mm范围内时, 内径尺寸=内径代号5 。 如:轴承代号 6204
6—类型代号(深沟球轴承)。 2—尺寸系列(02)代号。 04—内径代号(内径尺寸=045=20mm)。
55
二、滚动轴承的画法
车削普通螺纹操作方法
车削普通螺纹操作方法
车削普通螺纹的操作方法如下:
1.固定工件:将需要车削螺纹的工件固定在车床的头座上,确保工件稳定不会滑动。
2.调整车刀:选择合适的车刀,并将其夹紧在主轴的前层和后层上。
调整刀具的高度和角度以确保切削力和切削效果都能得到最佳结果。
3.设定进给和转速:根据螺纹的规格和工件材料,设定合适的进给速度和转速。
进给速度应根据螺纹的进给系数和纵向进给速度计算得出,而转速则取决于工件材料的硬度和刀具的材质和尺寸。
4.开始车削:打开主轴,启动车床,并将工件带动起来。
通过调节主轴、进给和纵向进给,使车刀在工件上匀速切削。
5.检查螺纹质量:在车削过程中,不断检查螺纹的质量,确保尺寸和表面光洁度满足要求。
如有必要,可以调整进给和刀具的位置以改善螺纹的质量。
6.完成车削:当螺纹车削完成后,将车床停止,并移除工件。
清理工件和车床上的切屑和废料。
以上是车削普通螺纹的基本操作方法。
根据实际情况和不同的工件要求,可能还需要做一些调整和优化。
在操作过程中,务必注意安全,遵循操作规程,并遵循车床操作的基本原则。