精益生产宣传看板(高清大图)Lean Production
合集下载
精益生产管理ppt课件
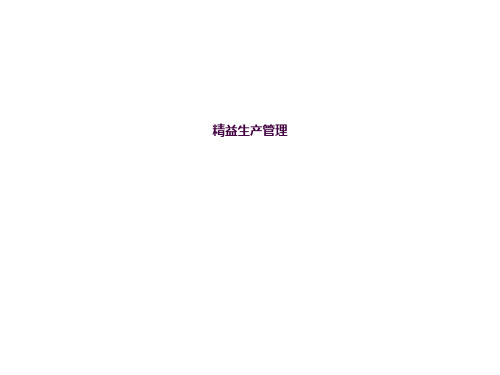
提高质量 环境保护
产品开发流程 市场 策划
开发周期 L/T ↓
直材成本↓
开发
生产周期 L/T ↓
设计 准备
制造成本↓ 生产效率↑
客户 订单执行流程
销售
计划
采购
生产 审查
物流
客户
市场
5、生产运作管理的目标 Just In Time
适品 ·适量 ·适时
逐步消除库存 逐步根绝浪费
利润最大化
流线化生产 安定化生产 平稳化生产 适时化生产
功能 转化
·资源组织 ·功能转化
发现需求 · 发掘需求 · 联络顾客 · 送达需求 ·
市场 客户 需求
生产
营销
财务
·筹措资金 ·运用资金 ·有效合理 ·流动增值
社会 资源
不同职能的价值增值作用——
物流
空间效用 时间效用
营销 占有效用
生产 形式效用
形式效用 通过生产或加工 过程增加产品价值。
时间效用 在特定时间的某 一需求点拥有产品或 服务,使之增加时间 效用或经济价值。
关键业务流程
从本质上说,企业作为一个投入产出的载体,是通过内部运作即流 程来实现价值增值的,企业战略目标确定后,驱动战略目标实现的往往 是几个关键业务流程,对于制造型企业来说,订单执行流程和产品开发 流程就是关键业务流程,这些流程的运作周期、流程质量、成本能力、 增值能力和运行效率从根本上决定了企业绩效。
6、利润与KPI关联图 Q′
P P′
S
C
D
Q
7、供应链管理
企业管理模式的变迁
纵向 一体化
小而全、大而全的管理模式,只 考虑本企业内部资源的最优利用。
横向 一体化
精益生产之看板管理ppt课件

返回3.4
21
4、生产线操作人员工作流程 ① 在拿取零件箱内第一个零件时,将工序内看板取下; ② 确认零件与看板是否相符; ③ 将工序内领取看板放置在看板回收盒内。
22
3.4 信号看板
一、信号看板定义
定义:在批量生产工序内(如冲压工序和锻造工序)使用的看板。 类型:三角看板和材料领取看板。
23
3.4 信号看板
下图为总装车间使用的一种领取看板实例。
18
1、看板回收操作人员工作流程
① 收到生产线播报发 件信息;
② 将工序内领取看板 发放至物流零件货 架的看板回收盒内;
③ 到生产线零件货架 的回收工序内领取 看板;
④ 按看板回收路线回 收看板后,回到起 始位置等待下次生 产线播报信息。
19
2、物流配货操作人员工作流程 ① 从看板回收盒内领取看板; ② 根据工序内领取看板上的零件代码和盛装数量、平板车
5
出厂。
27
28
一般生产线与零部件存放区的距离较远,从零部件送人生产 线并要求外协厂家供应原材料需要经历7个阶段:
1
生产线上的作业人员如果发现材料箱空了,就按生产线旁的按钮。
2
设置在材料存放区域旁的材料呼叫指示灯牌动作,指示这种材料的 指示牌下面的灯点亮。
3
材料存放区域的红灯同时点亮。
4
存放区域中的物料配送人员看到材料呼出指示灯牌,确认是哪个指 示牌下面的呼叫灯亮了。
物流与信息流示意图
3
推式生产分析: ➢ 推式生产的物流和信息流基本上是分离的。 ➢ 中间库存的增加导致库存和设备增加,进而占用资金、增加利息
支付;信息不畅也导致失去了“不断改进的机会”,从而隐藏了 各种浪费。
超产, 好啊!
21
4、生产线操作人员工作流程 ① 在拿取零件箱内第一个零件时,将工序内看板取下; ② 确认零件与看板是否相符; ③ 将工序内领取看板放置在看板回收盒内。
22
3.4 信号看板
一、信号看板定义
定义:在批量生产工序内(如冲压工序和锻造工序)使用的看板。 类型:三角看板和材料领取看板。
23
3.4 信号看板
下图为总装车间使用的一种领取看板实例。
18
1、看板回收操作人员工作流程
① 收到生产线播报发 件信息;
② 将工序内领取看板 发放至物流零件货 架的看板回收盒内;
③ 到生产线零件货架 的回收工序内领取 看板;
④ 按看板回收路线回 收看板后,回到起 始位置等待下次生 产线播报信息。
19
2、物流配货操作人员工作流程 ① 从看板回收盒内领取看板; ② 根据工序内领取看板上的零件代码和盛装数量、平板车
5
出厂。
27
28
一般生产线与零部件存放区的距离较远,从零部件送人生产 线并要求外协厂家供应原材料需要经历7个阶段:
1
生产线上的作业人员如果发现材料箱空了,就按生产线旁的按钮。
2
设置在材料存放区域旁的材料呼叫指示灯牌动作,指示这种材料的 指示牌下面的灯点亮。
3
材料存放区域的红灯同时点亮。
4
存放区域中的物料配送人员看到材料呼出指示灯牌,确认是哪个指 示牌下面的呼叫灯亮了。
物流与信息流示意图
3
推式生产分析: ➢ 推式生产的物流和信息流基本上是分离的。 ➢ 中间库存的增加导致库存和设备增加,进而占用资金、增加利息
支付;信息不畅也导致失去了“不断改进的机会”,从而隐藏了 各种浪费。
超产, 好啊!
LEAN PRODUCTION精益生产( 28)精益思想的基本原则ppt课件

Action Action Action
Action 活动
Action
Action
Action
(3). 流动Flow
理想价值流里的活动——完成一项任务的基本步骤 列队,或关注的对象都是稳定地、连续的流动, 没有批量、排队、等待和干扰。但事实上价值流 经常是受阻和停滞的。
精益思想第“流动”原则是强调价值流要“流动” 起来 。价值流(Stream小溪或江河)是一种物质 的存在,而“流动(Flow)”是流Stream的状态。
客户导演的流动!
原材料
零件
成型 喷漆
组合件 装配
客户
最终产品 配送
(3). 流动的含义和条件
真正建立价值的各个步骤快速的运作
要求增值过程中的每一个步骤都是:
可能Capable
–每一次都是正确的 (6 Sigma) – 经常保持可运作状态 (TPM)
可用Available 充分Adequate
——一种新的企业观
1.精益企业的基本目标 2.精益思想5项基本原则 3.两种对立的企业观
1. 精益企业的基本目标
用尽善尽美的价值创造过程
从概念到投产的设计过程 从定货到送货的信息过程 从原材料到产品的转换过程 全生命周期的支持和服务过程
为用户提供尽善尽美的价值
2. 精益思想5项基本原则
用最终用户的观点确定价值 Value 识别每个产品族的价值流 Value Stream 使产品流动 Flow起来 由客户拉动 Pull企业的行为 整个企业趋于尽善尽美Perfection
(1). 价值Value
精益思想Lean Thinking(LT)的关键出发 点是“价值”。 企业产品(服务)的价值是对客户需求的 满足。价值只能由最终用户来确定,价值 也只有满足特定用户需求才有存在的意义。
Action 活动
Action
Action
Action
(3). 流动Flow
理想价值流里的活动——完成一项任务的基本步骤 列队,或关注的对象都是稳定地、连续的流动, 没有批量、排队、等待和干扰。但事实上价值流 经常是受阻和停滞的。
精益思想第“流动”原则是强调价值流要“流动” 起来 。价值流(Stream小溪或江河)是一种物质 的存在,而“流动(Flow)”是流Stream的状态。
客户导演的流动!
原材料
零件
成型 喷漆
组合件 装配
客户
最终产品 配送
(3). 流动的含义和条件
真正建立价值的各个步骤快速的运作
要求增值过程中的每一个步骤都是:
可能Capable
–每一次都是正确的 (6 Sigma) – 经常保持可运作状态 (TPM)
可用Available 充分Adequate
——一种新的企业观
1.精益企业的基本目标 2.精益思想5项基本原则 3.两种对立的企业观
1. 精益企业的基本目标
用尽善尽美的价值创造过程
从概念到投产的设计过程 从定货到送货的信息过程 从原材料到产品的转换过程 全生命周期的支持和服务过程
为用户提供尽善尽美的价值
2. 精益思想5项基本原则
用最终用户的观点确定价值 Value 识别每个产品族的价值流 Value Stream 使产品流动 Flow起来 由客户拉动 Pull企业的行为 整个企业趋于尽善尽美Perfection
(1). 价值Value
精益思想Lean Thinking(LT)的关键出发 点是“价值”。 企业产品(服务)的价值是对客户需求的 满足。价值只能由最终用户来确定,价值 也只有满足特定用户需求才有存在的意义。
精益生产六西格玛PPT模板
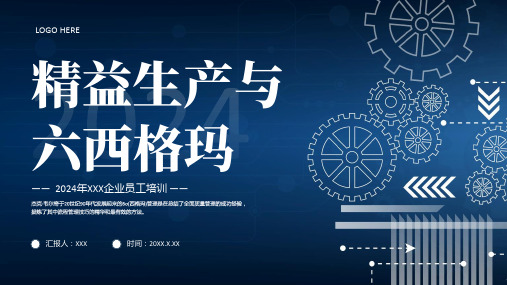
库存
inventory
等待
wait
运输
transport
动作
action
什么是精益生产
PART 01
精益改善工具—— 八大浪费:
价值流图
请在此处添加您的文字说明请在此处添加您的文字说明
线平衡图
请在此处添加您的文字说明请在此处添加您的文字说明
物理流图
请在此处添加您的文字说明请在此处添加您的文字说明
六西格玛思想与精益思想有着许多共通之处,主要表现在如下几个方面:
1.两者都需要高层管理者的支持和授权才能保证成功。
2.两者都不仅用于制造流程,还可以用于非制造流程。
3.两者都属于持续改进的方法。
4.两者都强调降低成本,提高效率,减少浪费。
5.两者都采用团队的方式实施改善。
6.两者都具有显著的财务效果。7.两者都关注顾客的价值和需要。
D
快速改变
请在此处添加您的文字说明请在此处添加您的文字说明
E
看板
请在此处添加您的文字说明请在此处添加您的文字说明
什么是精益生产
PART 01
精益五大原则
站在客户立场思考价值
Thinking about value from the customer's perspective
识别从订单到交付过程一切有价值的活动
精益生产与六西格玛
PART 04
精益生产采用的是拉动式的控制系统,生产计划部门只需要把生产计划下达到最后一道工序,最后一道工序对其上游工序提出所需物料的要求,上游工序根据要求生产,通过这样的拉动一直延续到采购部门。
精益生产的好处就在于真正实现了信息流与物流的结合,而且在整个过程中不会产生多余的中间产品,也不会出现等待、拖延等浪费。因此,精益生产能够真正做到“适时、适量、适物”的生产,节约产品的生产成本,最终产生经济效益。但精益生产是一个复杂的管理系统,它是一种管理思维的集合。
inventory
等待
wait
运输
transport
动作
action
什么是精益生产
PART 01
精益改善工具—— 八大浪费:
价值流图
请在此处添加您的文字说明请在此处添加您的文字说明
线平衡图
请在此处添加您的文字说明请在此处添加您的文字说明
物理流图
请在此处添加您的文字说明请在此处添加您的文字说明
六西格玛思想与精益思想有着许多共通之处,主要表现在如下几个方面:
1.两者都需要高层管理者的支持和授权才能保证成功。
2.两者都不仅用于制造流程,还可以用于非制造流程。
3.两者都属于持续改进的方法。
4.两者都强调降低成本,提高效率,减少浪费。
5.两者都采用团队的方式实施改善。
6.两者都具有显著的财务效果。7.两者都关注顾客的价值和需要。
D
快速改变
请在此处添加您的文字说明请在此处添加您的文字说明
E
看板
请在此处添加您的文字说明请在此处添加您的文字说明
什么是精益生产
PART 01
精益五大原则
站在客户立场思考价值
Thinking about value from the customer's perspective
识别从订单到交付过程一切有价值的活动
精益生产与六西格玛
PART 04
精益生产采用的是拉动式的控制系统,生产计划部门只需要把生产计划下达到最后一道工序,最后一道工序对其上游工序提出所需物料的要求,上游工序根据要求生产,通过这样的拉动一直延续到采购部门。
精益生产的好处就在于真正实现了信息流与物流的结合,而且在整个过程中不会产生多余的中间产品,也不会出现等待、拖延等浪费。因此,精益生产能够真正做到“适时、适量、适物”的生产,节约产品的生产成本,最终产生经济效益。但精益生产是一个复杂的管理系统,它是一种管理思维的集合。
精益求精--看板管理(PPT 39页)
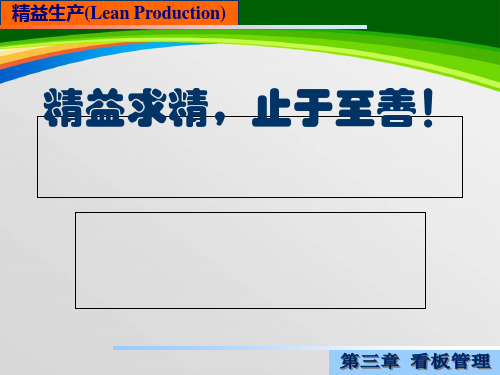
解:C=5件 T=2小时 D=10件/小时 α=0.2
N=10件/小时*2小时*(1+0.2)/5件=4.8(取整为5)
精益生产(Lean Production)
例3:每次向生产线运送4个变速器,运送时间间隔为 1小时。大约每小时有4辆汽车生产出来,管理者确定 保持期望需求的50%作为安全库存。为实现有序生产 ,需要多少看板?
规则2:前工序仅按后工序领取的物品和数量进行生产。
✓ 生产数量不能超过看板规定的数量,没有看板不进行生产。 ✓ 当前工序生产多种零部件时,必须按各看板送达的顺序进行生产。
规则3:不合格品绝对不能送到后工序(100%合格)。 规则4:必需把看板的数量减少到最小程度。 规则5:通过看板对生产进行微调。
精益生产(Lean Production)
表3-1 看板的类型
精益生产(Lean Production)
看板的作用与功能
生产以及搬送的作业指令 防止过量生产和搬送 进行“目视管理”的工具 改善的工具
精益生产(Lean Production)
看板实施的步骤
①进行数据收集:生产流程中的真实数据。 ②计算看板数量:计算需要的缓冲库存的数量。 ③设计看板运行规则:物料控制方式、进度控制负责人等。 ④全面培训 ⑤启动拉动看板(JIT) ⑥监察和维护 ⑦持续改善(CI)
通过外协看板的方式,从最后一道工序慢慢往前拉动, 直至供应商。因此,有时候企业会要求供应商也推行 JIT生产方式。
外协领取看板的数量计算与工序间领取看板数量的计算 方法一致。
精益生产(Lean Production)
外协领取看板数量的计算
ND C(TPTs)
(3-7)
N为外协领取看板的数量;T为订货周期,也称为看板周
N=10件/小时*2小时*(1+0.2)/5件=4.8(取整为5)
精益生产(Lean Production)
例3:每次向生产线运送4个变速器,运送时间间隔为 1小时。大约每小时有4辆汽车生产出来,管理者确定 保持期望需求的50%作为安全库存。为实现有序生产 ,需要多少看板?
规则2:前工序仅按后工序领取的物品和数量进行生产。
✓ 生产数量不能超过看板规定的数量,没有看板不进行生产。 ✓ 当前工序生产多种零部件时,必须按各看板送达的顺序进行生产。
规则3:不合格品绝对不能送到后工序(100%合格)。 规则4:必需把看板的数量减少到最小程度。 规则5:通过看板对生产进行微调。
精益生产(Lean Production)
表3-1 看板的类型
精益生产(Lean Production)
看板的作用与功能
生产以及搬送的作业指令 防止过量生产和搬送 进行“目视管理”的工具 改善的工具
精益生产(Lean Production)
看板实施的步骤
①进行数据收集:生产流程中的真实数据。 ②计算看板数量:计算需要的缓冲库存的数量。 ③设计看板运行规则:物料控制方式、进度控制负责人等。 ④全面培训 ⑤启动拉动看板(JIT) ⑥监察和维护 ⑦持续改善(CI)
通过外协看板的方式,从最后一道工序慢慢往前拉动, 直至供应商。因此,有时候企业会要求供应商也推行 JIT生产方式。
外协领取看板的数量计算与工序间领取看板数量的计算 方法一致。
精益生产(Lean Production)
外协领取看板数量的计算
ND C(TPTs)
(3-7)
N为外协领取看板的数量;T为订货周期,也称为看板周
LEAN精益生产培训PPT演示课件

• Remove constraints to respond to customer demand through the entire supply pipeline (supplier-customer)
• Capable plants linked to lean concepts
• 改善整个价值链 • 节点上连着精益工
Maintain / improve quality and reduce price 不断改进质量及降低销售价格
Total life cycle of product becoming shorter and shorter 产品的生命周期越来越短
No boundary,business globalize village 无国界,业务“地球村”
LEAN MANUFACTURING TRAINING
精益生产培训
xxxxxxxxxx有限公司
C
1
我们每天坐班的工厂?…
顾客是上帝 额外费用
未预计的订单变化
订单下达到工厂
快!119
Copy Right By LMC
2
What Shall We Talk…? 内容安排
Copy Right By LMC
8
Marketing Competition and Globalization
市场竞争及全球化
Life Cycle in year
Life Cycle Change/产品生命周期
30 25 20 15 10
5 0
化装品
50 年前 现在
玩具 机床 食品 药品
Product Styles In Supermarket ³¬ ¼¶ ÊÐ ³¡ Ö® ÉÌ Æ·Ö Àà
看板管理培训课件(PPT 161页)

20
拉式生产现场
21
第二节
看板概念、类型和功能
22
一、看板概念
看板一词起源于日语,是传递信号控制生 产的工具。
看板类似于工厂内部结算的“现金券”!! 它可以是某种“板”,如:卡片、揭示牌、
电子信息屏等,也可以是能表示某种信息 的任何其他形式,例如:彩色乒乓球、容 器位置、方格标识、信号灯等。
1、推式生产; 2、拉式生产。
5
1、推式生产原理
计划部门根据市场需求,按照产品物料清单计 划出每种零部件的需求量和各生产阶段的提前 期,确定每个零部件的投入产出计划,按照计 划发出生产指令和采购订货指令。
各车间和工序均按计划生产零部件,将实际完 成情况反馈到生产计划部门,并将加工完成的 零部件送到下一道工序或下游生产车间,整个 过程相当于从前工序向后工序推动,故这种生 产方式被称为推式生产。
看板、标签
2 必须的产品
每道工序或每个车间都按照当时的需要 向上一道工序或上游车间提出需求,发 出工作指令,上游工序或车间完全按照 这些指令进行生产。
14
二、拉式生产(2)
这时物流和信息流是结合在一起的,整 个过程相当于从后工序向前工序拉动, 故这种生产方式被称为拉式生产。
从下图可以看出,生产计划部门只制定 最终产品计划,计划下达到最后车间或 工序,其他车间或工序按照下游车间或 后工序的指令来确定生产。
为了能更有效地实施拉动式生产计划,早 期的精益生产先驱者发明了“看板”这一 简单的工具,依据看板作为信息传递的载 体,在各工序、车间、协作厂之间传递生 产指令或搬运指令。
18
2、拉式生产分析
按照拉式生产的原则,每道工序都按下 道工序的要求,在适当的时间,按需要 的品种与数量进行生产,就不会出现计 划产量和实际产量不符的现象,也就不 会出现中间库存。
拉式生产现场
21
第二节
看板概念、类型和功能
22
一、看板概念
看板一词起源于日语,是传递信号控制生 产的工具。
看板类似于工厂内部结算的“现金券”!! 它可以是某种“板”,如:卡片、揭示牌、
电子信息屏等,也可以是能表示某种信息 的任何其他形式,例如:彩色乒乓球、容 器位置、方格标识、信号灯等。
1、推式生产; 2、拉式生产。
5
1、推式生产原理
计划部门根据市场需求,按照产品物料清单计 划出每种零部件的需求量和各生产阶段的提前 期,确定每个零部件的投入产出计划,按照计 划发出生产指令和采购订货指令。
各车间和工序均按计划生产零部件,将实际完 成情况反馈到生产计划部门,并将加工完成的 零部件送到下一道工序或下游生产车间,整个 过程相当于从前工序向后工序推动,故这种生 产方式被称为推式生产。
看板、标签
2 必须的产品
每道工序或每个车间都按照当时的需要 向上一道工序或上游车间提出需求,发 出工作指令,上游工序或车间完全按照 这些指令进行生产。
14
二、拉式生产(2)
这时物流和信息流是结合在一起的,整 个过程相当于从后工序向前工序拉动, 故这种生产方式被称为拉式生产。
从下图可以看出,生产计划部门只制定 最终产品计划,计划下达到最后车间或 工序,其他车间或工序按照下游车间或 后工序的指令来确定生产。
为了能更有效地实施拉动式生产计划,早 期的精益生产先驱者发明了“看板”这一 简单的工具,依据看板作为信息传递的载 体,在各工序、车间、协作厂之间传递生 产指令或搬运指令。
18
2、拉式生产分析
按照拉式生产的原则,每道工序都按下 道工序的要求,在适当的时间,按需要 的品种与数量进行生产,就不会出现计 划产量和实际产量不符的现象,也就不 会出现中间库存。
003丰田精益生产PPT113页(1)

精益思想与精益生产体制
Lean Thinking & Lean Production System
思索:
企业的目标:做大?做强? 狼来了!来自何方? 核心课题(Toyota成功的启示):生产何等品质的产 品?以何等成本生产同等品质的产品?(迎接“同质化”、 “微利时代”的挑战) 路在何方? 制造的固有技术(工艺技术):自主创新、核心技术 制造的链接技术(管理技术):精益体制
管理理念一:简捷、简捷、再简捷 !→→ 准确实现、避免偏 差
管理体系流程化 管理标准显在化 管理方法可视化
管理理念二:以人为本、共同实现!→→集思广益、荣辱以共
全员参与 自主管理
Topdown与Downtop并行
维护部门生产保养
全公司生产保养 1968年Nippon Denso 首次创立日本特色的 全员生产性保全体制 ,80%~90%员工参 与
福特T型车的成功启示:流水线生产方式(Line Production) 流水线生产方式的挑战:多品种、小批量 Toyota的生产方式革命:流线化、批量细分化、单件流(One Piece Flow) 现代开发新产品的“并行工程”
突破库存瓶颈:流线化生产 流线化生产的核心含义:细胞化
工序1 工序4 1
易
缺
难
足
1、标准作业
标准作业
有规律的重复 性作业,如:组装工 序的螺栓紧固。
非标准作业
没有规律的非 重复性作业,如:补 充螺栓。
如果操作者在作业中同时需要进行 标准作业和非标准作业,必然造成生产动 作的停顿,从而使生产不稳定。
标准作业
为达到人员的安定,首先要分离标 准作业和非标准作业。
标准作业
Lean Thinking & Lean Production System
思索:
企业的目标:做大?做强? 狼来了!来自何方? 核心课题(Toyota成功的启示):生产何等品质的产 品?以何等成本生产同等品质的产品?(迎接“同质化”、 “微利时代”的挑战) 路在何方? 制造的固有技术(工艺技术):自主创新、核心技术 制造的链接技术(管理技术):精益体制
管理理念一:简捷、简捷、再简捷 !→→ 准确实现、避免偏 差
管理体系流程化 管理标准显在化 管理方法可视化
管理理念二:以人为本、共同实现!→→集思广益、荣辱以共
全员参与 自主管理
Topdown与Downtop并行
维护部门生产保养
全公司生产保养 1968年Nippon Denso 首次创立日本特色的 全员生产性保全体制 ,80%~90%员工参 与
福特T型车的成功启示:流水线生产方式(Line Production) 流水线生产方式的挑战:多品种、小批量 Toyota的生产方式革命:流线化、批量细分化、单件流(One Piece Flow) 现代开发新产品的“并行工程”
突破库存瓶颈:流线化生产 流线化生产的核心含义:细胞化
工序1 工序4 1
易
缺
难
足
1、标准作业
标准作业
有规律的重复 性作业,如:组装工 序的螺栓紧固。
非标准作业
没有规律的非 重复性作业,如:补 充螺栓。
如果操作者在作业中同时需要进行 标准作业和非标准作业,必然造成生产动 作的停顿,从而使生产不稳定。
标准作业
为达到人员的安定,首先要分离标 准作业和非标准作业。
标准作业